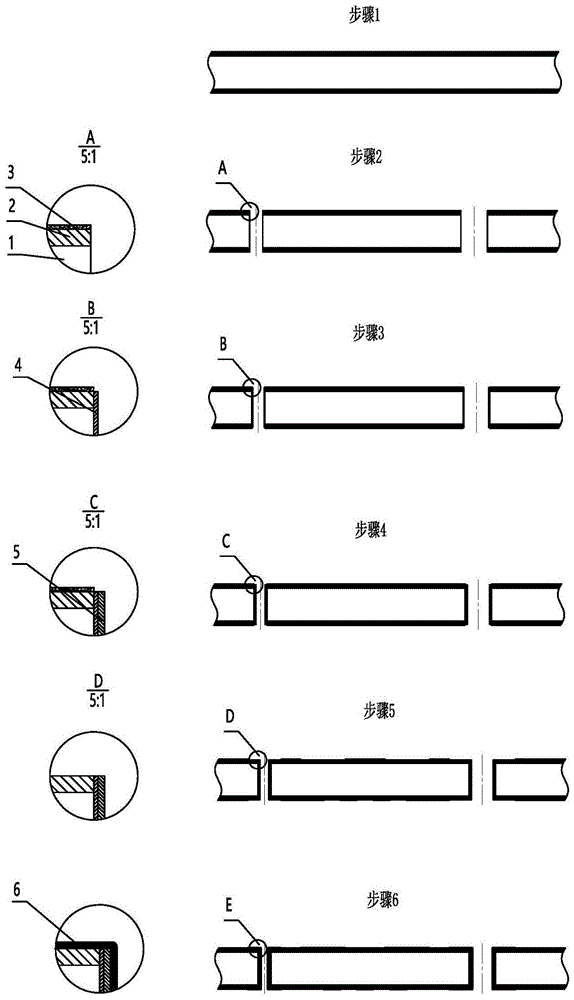
本发明属于电路制作
技术领域:
,涉及激光加工技术,尤其是一种只电镀孔后激光制抗镀图案和导电图案的制电路板方法。
背景技术:
本发明利用激光加工技术,用同一表面疏化学镀活性种子的有机材料作为掩敝层,只电镀孔壁,用激光去除线路、焊盘上掩蔽材料,同时电镀孔壁、焊盘和线路,能分别控制孔壁铜厚和线路铜厚,用激光去除非线路铜箔制导电图案,能更好地满足对电子产品对电路板的电气要求,特别适合制造厚铜导电图案,也适合各种电路板大批量,小批量、多品种以及样品生产。其制造流程是:在双面覆铜箔板,或完成内层制作叠加外层的多层电路板表面上涂覆有机掩蔽材料→钻孔→孔导电化→电镀铜加厚孔壁→激光去除高聚物膜露出焊盘和线路铜→电镀铜加厚→激光去膜露出非线路区域铜→激光去除非线路区域铜箔制出导电图案→贴阻焊膜→组装现场用激光制阻焊图案并对焊接区进行可焊性处理→漏印焊膏,进行元件安装,焊接。电子产品从概念到成品一般要经历设计、备料和组装三个阶段。物理设计结束后,就要进行物料准备,包括选择和定制各种元器件、接插件、显示模块以及其它功能模块等等。其中,最重要的物料之一就是裸电路板,因为裸电路板用来支承元器件并起着元器件管脚间的电气互联作用,是影响电子产品的质量、可靠性以及整个制造过程的难易程度、成本高低、速度的快慢的关键因素,必须按照设计要求和产品的属性定制。裸电路板,简称裸板,指尚未安装元器件的电路板,也称印制电路板、印刷电路板、印刷线路板、印制板、电路板、线路板、印刷板。裸板一般由专业制造印制电路板的厂家按需定制。以多层电路板为例,裸板制造的工艺流程大致为:制造内层导电图案—黑化/棕化及层压—在多层覆铜箔绝缘基板上钻孔—进行孔金属化—制作外层导电图案并退除金属抗蚀膜或有机抗蚀膜—涂覆阻焊剂—制作阻焊图案及生成焊接区—对焊接区表面进行可焊性涂覆处理—制作标记符号—出货给组装阶段的厂家。电子产品的组装,即把各种物料装、配、组合在一起,并通过钎焊、紧固、粘接等连接手段实现物料之间位置的固定和对应的电气连接和功能的配合。狭义上,常将把元器件安装及焊接到电路板上的组装过程称作装联。装联元器件之后的产品,一般称为组装板。在不需要区分的场合,裸电路板和组装板通称为电路板。以前的装联技术,以通孔插装方法为主,即把各种元器件、接插件、功能模块等的管脚插入到裸板的安装孔中,再用焊料把这些管脚与孔壁和焊盘钎焊在一起,从而把元器件固定在电路板上,并通过电路板上的焊盘、互连线、中继孔实现元器件管脚间的电气互连。目前的电子产品,更多地采用表面安装技术进行装联,即,先在电路板连接盘-即焊盘上涂覆焊锡膏,然后把各种元器件、接插件、功能模块等的管脚对应放置在连接盘的焊锡膏层之上,最后再对电路板进行加热,使焊锡膏中的粉状或颗粒状的固体金属锡/锡合金熔化,熔化的焊料浸润元器件的端电极/管脚和电路板焊盘,冷却成固体金属时把元器件的端电极与连接盘钎焊在一起,从而把元器件贴装固定于电路板表面,并通过电路板上的焊盘、导线、孔构成的导电通道,实现元器件间的电气互连。电路板的组装或在专业组装厂家进行,或由电子产品开发机构自行完成。以SMT技术为例,电路板的装联工艺流程大致为:来自裸板制造厂的电路板—往焊接盘上漏印焊锡膏—拾取元器件并将其贴覆于电路板表面—加热使焊锡膏重熔回流实现管脚与焊盘的钎焊。整体考虑电路板的裸板制造和元器件组装过程,可以看出,裸电路板制造的关键是导电图形制作、层压、钻孔及孔金属化、阻焊图案制作及可焊性涂覆等过程,而涂覆焊锡膏、贴插元器件、焊接则是装联生产阶关键流程。再进一步分析,可以知道,这些过程本质上都是为了实现元器件的安装固定和元器件之间的电气互连两个目的。其中,导电图案制造关乎电路板线路的精细程度和电气性能;阻焊图案的制造、可焊性涂覆虽然是在裸板阶段完成,但却是装联阶段生产的基础;而钻孔及孔金属化则一方面影响着电路板的连接密度、机械性能、应用环境,及插装件的安装固定时的匹配度,另一方面决定着电路板各个水平导电层间Z方向互连的电气性能以及可靠性高低,并且,还直接影响着电路板的水平方向电气连接导电图案制造过程的难易程度。随着社会经济的进步,对电子产品的要求越来越高,元件越来越小,功能越来越强,管脚数越来越多,对导电图案、阻焊图案的要求越来越精细、准确,对孔的要求也越来越小、越深,不论是在裸板制造阶段,还是元器件组装阶段,各个制程问题又互相影响,使得电路板制造的技术难度越来越大。比如,目前的孔金属化制程,为了满足Z向电气互连物理载体达到最低可靠性和电气要求,即孔壁导电层达到最低厚度,必须用电镀技术往孔壁上沉积金属铜,而电镀过程需要导电通道,现有的技术,不论是图形电镀、全板电镀蚀刻制导电图形法,还是激光选择性去除铜箔制导电图案法,都不得不用基材上原有的铜箔作为孔壁上镀铜的电源线,在电镀铜加厚孔壁导电层过程同时,板面固有铜箔基础上,必定会与孔壁同步增加导电层厚度,而且,由于电力线分步的因素,还由于电镀过程的深度能力和均镀能力限制,使得最终板面沉积层的厚度会大于孔壁沉积层。IPC标准IPC-6012中,,对金属化孔壁厚有明确的要求,至少为20μm。现在的电路板制程,深镀能力有限,当孔壁铜厚达到20μm时,板面增加的铜厚度超出孔壁铜厚,与材料原有铜箔厚度18um相加后,总铜厚超过40μm。然而,这种电镀加厚孔必须同步加厚板面原始铜箔技术,并没有因为消耗了铜资源而增强电路板的性能,并没有降低后续制程的难度,恰恰相反,这样的制程在以下几个方面,对电路板性能和制程有负面影响:第一,孔壁导电层厚度比板面导电层厚度小,造成Z向导电链路与X、Y平面导电链路电性能不一致。第二,电路板电镀孔壁工序产生的导电层,成了未来导电图形导电层的顶层,在趋肤效应的作用下,是频率较高的电信号传输的主要介质,而电路板生产中用电镀技术沉积出铜层的质量,比材料原有的用电铸或压延技术制造出的铜箔的纯度略低,晶体略粗糙,电气和机械性能质量略差,因此,导电层厚度的增加反而不利于信号高速、高频传输。第三,铜箔厚度的增加及其导致的侧向蚀刻是一种制约导电图案精细度的因素,用化学蚀刻技术制造导电图案过程中,蚀刻液与铜箔接触进行蚀刻,蚀刻除了垂直向铜箔深度进行,由于蚀刻液与导线两侧面接触,使得蚀刻同时也在导线的两个侧向进行,被蚀刻的铜层越厚,时间越长,侧向蚀刻现象越严重,侧向蚀刻不仅减小了导线宽度,严重时还会产生断线。第四,铜箔厚而不匀,是用激光制导电图案技术广泛应用的瓶颈,显然,铜箔越厚,需要的激光能量就越大,需要加工的遍数就越多,加工过程会越慢;铜箔厚度越不均匀,光蚀过程越难,要么是铜箔厚度较大区域出现施加激光功率过小,去铜不净,残留铜影响绝缘性能现象,要么是铜箔厚度较小区域出现施加激光功率过大,烧蚀铜箔下面的绝缘材料,影响电路板质量现象。现有的技术,导电图案制造过程的问题在于,传统蚀刻方法过程复杂,需要先用图形转移过程制造抗蚀掩膜,图形转移过程又需要使用光敏材料,还需要先制造用于选择性曝光用的掩膜版,且蚀刻制出导电图形后需要将抗蚀掩膜去除,伴随蚀刻出现的欠蚀刻、过蚀刻、侧蚀刻、蚀刻不匀现象常常使得质量控制各因素间顾此失彼,问题重重;而激光直接去除有机材料制抗蚀刻掩膜、抗电镀掩膜、阻焊掩膜,以及直接去除导电铜箔方法制导电图形过程虽然简单,但因为激光光斑直径小,需要逐点逐线加工,速度慢,效率低。此外,在激光直接去除导电铜箔方法制导电图形加工中,因为基板上的铜箔层在孔金属化后厚度变得更厚、厚度更不均匀,激光能量很难实时做相应变化,难以保证去除质量。阻焊图案制作以及可焊性涂覆的问题在于,和制造导电图形一样,传统技术制阻焊图案,是一个图形转移过程,需要使用光敏材料,还需要先制造用于选择性曝光的掩膜版,烘烤、曝光效果相互干涉,使得质量控制左右为难,阻焊剂上焊盘一类的缺陷频频出现。而无论是用热风整平、还是用化学镍金技术进行可焊性涂覆都存在着成份复杂,过程繁琐,会带来焊接机理不清而影响可靠性的困惑。综上所述,不难看到,当前的电路板制造技术中包含着一系列的间接加工、化学处理、湿法制造流程。这些单功能流程各有各的固有技术局限,而且,它们之间相互牵制,互为结果,是限制更高质量、更高效率、更加环境友好的根本原因,既需要对各个单功能流程进行改进、更新,还需要在整体上综合优化,升级。技术实现要素:针对现有技术不能分别电镀加厚孔和线路的不足,本发明一种只电镀孔后激光制抗镀图案和导电图案的制电路板方法,能有区别地电镀孔壁,焊盘和线路,用表面疏化学镀活性种子的高聚物薄膜掩蔽板面,钻孔后只电镀孔壁至厚度满足要求后,再用激光直接去除材料,制作电镀孔壁和线路的图案,直接用激光去除非线路铜箔制造导电图案,最后,用激光直接去除材料制造阻焊图案。加工步骤如下:(1)往内部没有或含有一层及以上导电图形的双面覆有铜箔的工件表面上涂覆有机掩蔽材料;(2)按设计要求钻孔;(3)孔导电化;(4)电镀,在孔壁上沉积铜加厚导电层至需要的厚度;(5)用激光去除焊盘和线路区域上的掩蔽材料;(6)电镀,往焊盘、线路和孔壁上沉积铜加厚;(7)用激光去除非线路区域上的掩蔽层;(8)用激光去除非线路区域的铜箔层;(9)全板涂覆并一次性固化阻焊材料;(10)在组装现场用激光去除焊接区表面上的阻焊材料,制造阻焊图案,并对焊接区表面进行清洁及可焊性处理;(11)向连接盘上添加焊料,进行元件贴装、插装,进行重熔焊接及或波峰焊接。其中,步骤(1),在双面覆铜板或已经完成内层线路制作的多层覆铜箔板上覆高聚物薄膜。现有技术一般采用光致干膜作为抗电镀掩膜,光致干膜为三层结构,光敏胶涂层在载膜和保护膜之间,由胶粘剂和光聚合单体等组成,形成图案过程较复杂,要经过光绘制版、贴膜、曝光、显影工序;而且,价格贵,强度不高且厚度较大,一般在20μm以上,分辨率受限,掩蔽效果较差。本发明的掩蔽膜不需要具备光敏感性能,但其表面需具有疏化学镀活性种子状态,并且具有抗电镀、抗蚀刻性质;包括由单一组分、多组分、复合的热固、光固、可热压合附着的,非光敏和光敏的材料制造的干性PET、PI、RPP、BOPET、BOPP、PA、PPE、派瑞林等高聚物薄膜,以及单体的、预聚合的、或已完成聚合的液态、膏状或其它形态的材料;材料的涂覆方法包括滚压、热压、印刷、镀覆、喷涂、帘涂等方法或方法相结合的加工;材料的厚度厚度大于线路上增厚的总金属厚度,范围在2μm-3000μm,优选20μm-1000μm。事实上,一般的预涂覆压敏涂层膜、热敏涂层的高聚物薄膜,经过疏化学镀活性种子处理后即可满足要求。例如,热压贴厚度为200μm热敏PET、BOPET膜作为抗电镀掩膜。其中,步骤(2),按照设计要求钻孔。被钻孔材料是导电铜箔和绝缘材料交替叠层而成的复合材料,与传统技术不同,本发明所钻材料增加了贴在板面上的高聚物掩蔽膜。钻孔工具既可以是机械钻头,也可以是聚焦激光光束。如果采用机械钻头钻孔,在孔壁上可能出现环氧钻污,在进行孔导电化前,应该用不伤害上述高聚物薄膜的药液或过程将环氧钻污去除掉,以保证孔金属化质量。其中,步骤(3),孔导电化。本步骤的目的是在孔壁上沉积起始导电层,为下一步电镀孔壁打底。传统的化学沉铜工艺,是先在孔壁上先沉积具有活性的贵金属粒子,然后再沉积铜孔金属实现孔壁表面导电的,因此孔导电化即是现行电路板制造技术中的孔金属化过程;而对于直接电镀工艺,特别是其中的碳膜法、高分子膜法,实现孔壁导电的物质不是金属,因此用孔金属化描述形成起始导电层的过程并不准确。本发明中,涉及现行技术时仍用孔金属化进行描述,涉及本发明的过程时用孔导电化描述,孔导电化既包括用金属实现的孔导电过程,也包括用非金属材料实现孔导电的过程。实现本步骤的目标有两种方法,一种是直接电镀方法,例如,用碳膜法对孔进行黑孔化,经过“前处理→黑孔”步骤后形成起始导电层;另一种是传统化学沉铜工艺,经过“镀前处理→活化处理→化学镀铜”后形成起始导电层。其中,化学镀铜的厚度达到保证过程可靠的下限即可,比如1μm。本步骤中,因为板面覆有高聚物薄膜,且该薄膜表面外表面具有疏化学镀活性种子性能,掩蔽了板面,所有在直接电镀方法的黑孔步骤后,或在化学沉铜方法的活化处理后,板面不会有导电的炭黑、石墨等物质,也不会附着具有催化作用的金属钯活性粒子以及化学沉积的铜等物质。这样,就能维持板面与覆铜箔导电层处于电气绝缘状态,在后续电镀时,就不会有金属铜在板面上沉积,从而达到只在孔壁上电镀铜导电层的目的。其中,步骤(4),电镀铜,在孔壁上沉积铜加厚孔壁。为了解决电镀孔壁时,总面积过小,电力线分步不均,电流密度不容易控制等问题,可以在工件上制造有助于改善质量的电镀平衡块。方法为:在进行步骤(1)之后,在进行步骤(2)、(3)之前或之后,在进行步骤(4)之前,用激光去除非线路且与线路间隔大于30μm以上,优选间隔大于50μm的无电气功能的死铜区域,或其导电层需要去除且不对后续去除过程产生负面影响的区域,或铜厚不影响其功能的区域,或增加铜厚对功能有正面影响的区域上的抗电镀薄膜掩蔽层,露出其下的铜箔面,形成有利于电镀孔壁时电镀电流平衡分布的分散图案。制造电镀平衡块,仅需去除对应部位铜箔表面的有机材料。此时,所用聚焦激光光斑光功率密度须大于去除有机材料所需的最低功率密度,并且低于或接近于去除其下所覆盖的金属层所需最低光功率密度。优选大于去有机材料所需最低光功率密度的1.2倍。步骤(4)的控制点是电镀时间。此时,板面上除孔壁和电镀平衡块以外,全部区域上都有掩膜覆盖,掩膜是绝缘材料,虽然与电镀药液接触,但表面上沉积不上铜,因此,只有孔壁和平衡块在电镀过程中能沉积铜,电镀时间足够,就能在孔壁上获得足够厚度的铜沉积层,达到了选择性控制孔壁铜厚的目的。其中,步骤(5),激光去除焊盘和线路上的高聚物薄膜掩蔽层。加工目的是露出焊盘和线路的铜表面,以便在焊盘、线路和孔壁上再电镀金属铜加厚,以及在铜表面再电镀镍、金或锡等金属作为抗蚀刻的保护层。不同的电路板,不同的线路,需要去除的区域宽窄不一。如果去除区域宽度与光束直径或其倍数不相符合,会降低去除速度,还会产生搭接,搭接时罗叠区域被激光加工两遍,造成与非罗叠区域加工效果不一致。本发明根据去除的区域形状和尺寸改变聚焦激光光束直径,使聚焦光束直径或其倍数恰等于需要去除区域的宽度,以降低或去除激光加工区域的搭接,提高加工效率。本步骤与制造电镀平衡块过程一样,仅需去除对应部位铜箔表面的有机材料。此时,所用聚焦激光光斑光功率密度须大于去除有机材料所需的最低功率密度,且低于或接近于去除其下所覆盖的金属层所需最低光功率密度。优选大于去有机材料所需最低光功率密度的1.2倍。其中,步骤(6),电镀,往焊盘、线路和孔壁上沉积铜加厚。目的是得到足够厚度的导电层,以满足电路板设计的电气要求。本步骤的控制点是电镀时间。电镀时间足够,就能在孔壁、焊盘和线路上获得足够厚度的铜沉积层,能达到选择性控制电路板导电图案的导电层厚度的目的。现在的电路板制造技术,一般采用光致干膜作为抗电镀掩膜,材料多为紫外光固型,其所形成的掩蔽图案厚度在一定的范围内,既不能太薄,也不能过厚。因为材料是在热压贴膜、紫外曝光后才交联聚合,成为掩膜,后续还要能比较容易地被去膜化学药液分解,如此的后续技术要求造成的掩膜在某种程度上只能是一种不完美的亚固体。太厚,分辨率低,需要的曝光量大,会出现一方面靠近光源的薄层过曝光,另一方面远离光源的薄层欠曝光现象;如果太薄,本来就脆弱的亚固体材料,就更达不到掩蔽需要的机械强度,可能导致渗镀。本发明用激光直接去除制造抗镀掩蔽图形,使用的是非光敏材料,材料本身是聚合完全的固体,无论薄厚,都有足够的掩蔽能力,即使电镀时间较长,也不会脱落、溶解。对于要求线路铜厚度大的电路板,可以在步骤(1)选择较厚的材料,例如,选择厚度为300μm的掩膜,用激光去除需要线路表面上的掩膜材料后,控制电镀时间,直到金属层厚度接近或达到300μm为止。其中,步骤(7),激光去除非线路区域高聚物薄膜掩蔽层。目的是露出非线路区域铜箔表面,以便下一步骤蚀刻去除。和步骤(5)一样,此步骤,需要去除对应部位铜箔表面的有机材料层。此时,所用聚焦激光光斑光功率密度须大于去除有机材料所需的最低功率密度,且低于或接近于去除其下所覆盖的金属层所需最低光功率密度。优选大于去有机材料所需最低光功率密度的1.2倍。去除铜箔表面的高分子聚合物,可以选择以CO2激光器为光源的设备加工。CO2激光器发出的激光,波长为10μm左右,处于远红外波段。铜对这个波段的激光吸收系数低,但这个波段的激光与大多数高聚物耦合性好。因此,去除掉高聚物又不伤铜的激光参数范围宽。选择CO2激光,可以使用大直径光斑,去除效率高,成本低,性价比高,而且不伤铜。除了CO2激光外,波长在1μm左右的脉冲光纤激光,性能稳定,使用方便且成本低,也适合去除高聚物材料,制造抗蚀图案。其中,步骤(8),激光去除非线路区域上的铜箔层。非线路区域上的铜箔层被去除后,没有铜箔的区域在绝缘基板上形成了绝缘图案,孔、焊盘、线路区域上的导电层在绝缘基板上形成了导电图案。因为本发明能够选择性地电镀孔、焊盘和线路,所以用激光去除非线路区域的导电材料的技术更容易实施。现在通用的制造电路板技术,在孔金属化电镀过程之后,由于孔化系统均镀能力的限制,在同一块基板材料上的不同区域,铜的沉积速度不同,导致总导电层厚度出现较大差异。这样,用激光光蚀去除非线路部分的导电层时,如果激光参数不随铜厚变化,要么导致总铜厚度大的部位去铜不净,残留铜影响绝缘性能,要么导致对总铜厚度小的部位施加能量过大,烧蚀绝缘材料问题。实施本发明选择性电镀的技术方案,可以不在非线路区域,特别是可以不在激光光蚀去除路径上沉积铜,保持激光光蚀路径下导电层为原始铜箔,厚度均匀,降低激光加工难度。本发明采用德中技术的分条与剥离法/Striping&Stripping,先用激光光蚀,逐点、逐层地将导电材料汽化,形成封闭的分隔线,把需要去除的导电层区域细分为相互绝热的面积在某确定范围内的小片,称为分条/Striping;然后,再用激光去加热小片,降低小片与基板的结合力,使其成片脱离基板,称为剥离/Stripping。分条与剥离法的加工步骤依次为:先逐点投照光蚀激光,汽化去除各个导电图案包络线下的导电材料,以轮廓线为界,制出闭合的绝缘沟道;再逐点投照光蚀激光,汽化去除分隔线下的导电材料,将需要去除的大块导电材料细分为互相绝热的小片;然后依次向小片上投射加热激光,降低其与基材的结合力并变形,在辅助气的共同作用下,使之脱离工件,被转移收集。进行分条与剥离加工时,当两导体间绝缘间距S较宽,数值满足S>2dmax时,加工方案为nd (n-1)D,即n个光束直径为d的光蚀汽化去除和(n-1)个光束直径为D的加热剥离去除,其中n≥2,且优选n值最小;当两导体间导电层宽度S满足2dmax≥S≥dmax时,S=d1 d2,即选用光蚀直径为d1和d2的两个光蚀激光束去除两导体间的导电材料,其中,d1和d2可以相同,也可以不同;当两导体间绝缘间距S小于光蚀加工该任务的束腰直径最大值,即dmax≥S时,加工方案为S=d,即选择光束直径,使得恰好只用一个光束直径为d的光蚀激光束去除两导体间的导电材料。其中,S为两导体间绝缘间距,即需要去除的导电层的宽度,d为光蚀激光光束直径,D为加热激光光束直径,n为1、2、3、4等整数。实施激光分条与剥离技术,并不一定先去掉非线路区域的抗电镀掩蔽膜-高聚物薄膜,例如,用紫外波段激光加工,或皮秒激光在分条时,可将掩蔽膜和其下的铜箔层一起用激光光蚀汽化,直至绝缘基材层止,形成绝热沟道;剥离时,对掩蔽膜和其下的铜箔层一起加热,通过热变形和与绝缘基材的结合力的降低,成块剥离。为了适合激光加工,抗电镀掩蔽膜可以选择有颜色的材料,以产生更好的吸收效果。其中,步骤(9),全板涂覆并一次性固化阻焊材料。现有技术一般采用液体光敏油墨作为阻焊剂,阻焊剂中含有胶粘剂和光聚合单体,形成图案过程非常复杂,除了要光绘底版外,还要经过涂覆、预烘、曝光、显影、固化等多道工序;而且,价格贵,分辨率不高,在细节距连接盘之间常有漏涂阻焊或阻焊溢流上焊盘现象,涂覆质量很难保证。本发明的阻焊剂不需要具备光敏感性能,一般的预涂覆压敏涂层膜、热敏涂层膜即可满足要求,价格便宜,分辨率高,可以制作精细的图案结构。此外,本发明采用热压涂覆,不需要额外的固化过程,阻焊图案留待元件组装前现场用激光制作,流程简单。例如,热压贴厚度为5μm-300μm,或者更进一步,30μm-100μm热敏PI、PVC、PC、PET、PP、RPP、BOPET、BOPP、PA、PPE、派瑞林膜作为阻焊剂。对于导电图案厚度较大,超出高聚物薄膜包覆能力的电路板,应该选择液体阻焊涂料,尽量在吸真空条件下涂覆,以使阻焊剂除了覆盖导电图案的顶面,也能覆盖导电图案的侧壁。因为本发明用激光直接去除,制造阻焊图案,液体阻焊涂料,也不需要具备光敏性能,应该满板涂覆,一次性固化。其中,步骤(10),在组装现场用激光去除焊接区表面高聚物薄膜层,制造阻焊图案,并对焊接区表面进行清洁及可焊性处理。本步骤的要点是在组装现场制造阻焊图案,指一旦阻焊图案制作完毕,裸露出新鲜的铜箔,应立即进行往焊盘表面涂覆焊料,贴片,焊接过程,或插件、焊接过程。本步骤中的激光加工既有选择性去除阻焊材料,制阻焊图案作用;又有清洁焊接区,对焊接表面进行可焊性处理的作用。用激光制造阻焊图案的技术要点在于:图案尺寸准确、光滑,无毛刺;去除干净,阻焊剂无残留、无碳化;保持焊接区金属性能,不伤金属、无重熔、变色;不影响焊盘与基材的附着力,无过热,焊盘不起翘,附着力不降低。阻焊剂一般是高分子聚合物,物理上、化学上与金属差异大,用激光加工去除,找到符合技术要求的窗口比较容易,可以用一种波长激光在同一设备一步完成,也可以在不同设备上分两步进行。纳秒紫外激光,皮秒、飞秒激光,既能被高聚物吸收,起去除作用;也能被铜金属较好地吸收,起到清洁其表面的作用。特别是皮秒、飞秒激光,单脉冲能量较小,但光的强度,即单位面积上的激光功率大,能够仅仅去除微量物质,但改变材料表面性能,是对裸铜表面进行可焊性处理的较好选择。本步骤,可以选择这样的激光加工系统,用同一设备,一步或分步完成制阻焊图案并对焊接区进行可焊性处理加工。CO2激光、光纤激光与高聚物作用,吸收率高,而与铜作用,吸收率低。一般而言,这类激光,不能兼顾去除铜箔上的高聚物制阻焊图案与对焊接区进行清洁和可焊性处理功能。因此,本步骤的另外一种选择,是用两类激光光源分两步进行:选择大光斑CO2激光,高效去除高聚物制出图案;再用纳秒UV脉冲激光,或皮秒、飞秒激光再去除阻焊剂残余物。第一步:制作阻焊图案,生成焊接区:用波长较长的CO2激光器发出的大直径激光光斑,选择性光蚀去除掉焊接区上的阻焊剂涂覆层,去除可能进入孔内的阻焊剂,制作出阻焊图案,生成焊接区。第二步,对焊接区表面进行清洁及可焊性处理,用波长较短的UV波段,或者光强度较大的皮秒、飞秒脉冲激光,去除焊接区表面的阻焊剂残存物,并轻微光蚀焊接区金属表面层,去除金属氧化物,露出新鲜的金属表面,产生容易被熔融的焊料浸润的可焊性。其中,步骤(11),向连接盘上添加焊料,进行元件贴装、插装,进行重熔焊接及或波峰焊接。本发明的方法,因为用激光处理过的新鲜铜表面替代焊接区的可焊性涂覆层,因此,结束步骤(10)之后,应该在尽可能短的时间内进行步骤(11),以避免连接盘表面氧化,在激光处理后可焊性优良的状况下,完成元器件装联,包括,进行元器件插装,并直接向激光处理过的焊接区施加焊料,完成元器件焊接;或直接在向激光处理过的焊接区漏印焊锡膏,然后进行元器件贴装和回流焊接;或依照其它技术进行元器件组装。在本发明中,激光加工既用于钻孔,还用于去除铜箔层上的高聚物薄膜。所用激光加工设备由一套或者多套数据获取与处理系统、设备操作系统、激光光源、光束整形及传输系统、激光聚焦系统、工件夹持及自动和手动上料与下料系统,工件定位及与光束间的运动与控制系统,视觉检测以及激光功率监测及补偿系统,清洁、恒温系统,激光及设备安全使用系统等组成;激光去除高聚物薄膜或激光去除非线路区域上的铜箔时,能根据被加工区域的形状和尺寸,以单位面积上能量和功率为恒量,以与材料相互作用的光斑直径为变量,以加工速度快、加工路径搭接时无罗叠或有一定量的罗叠、脉冲间有一定罗叠量或间距量之一或其组合为优先,生成激光参数和加工数据;在加工中能针对被加工图形的结构,按预定的激光参数、加工路径要求,在线变换光斑直径。本发明的优点和效果是:1、本发明可以只电镀加厚孔壁,容易控制镀层厚度,能解决孔壁镀层厚度偏薄问题。2、本发明使用非光敏材料作为抗电镀材料,降低成本,而且耐电镀性能好,可以制造具有孔壁和线路金属铜层更厚的导电图案。3、本发明使用激光直接去除方法制造抗电镀图案、阻焊图案,不用图形转移,减少步骤和相关材料、设备,降低成本,可以制造精细的导电图案和阻焊图案。4、本发明技术方案只电镀孔和线路,不增加非线路部分导电层厚度,使蚀刻更容易,有利于制造更精细的导电图案。5、本发明的激光制造图案过程中,根据去除的区域形状和尺寸改变聚焦激光光束直径,使聚焦光束直径或其倍数恰等于需要去除区域的宽度,能降低或去除激光加工区域的搭接,提高加工效率。6、本发明一次性固化阻焊材料,在组装现场制造阻焊图案,不需要可焊性涂覆步骤、材料、设备,大幅度降低成本,降低制造难度。7、本发明用非光敏材料作为阻焊剂,分别用不同波长、脉冲宽度、功率密度的激光制造阻焊图案和进行焊接区清洁以及可焊性处理,效率更高,处理的效果更好。附图说明图1a为本发明的工艺流程图(步骤1-6);图1b为本发明的工艺流程图(步骤7-11);图中:1、绝缘基板;2、覆铜板铜层;3、有机掩蔽材料层;4、起始导电层;5、电镀铜层;6、沉积加厚铜层;7、阻焊材料层;8、可焊性处理表面;9、焊料;10、元件。具体实施方式以下将结合实施实例,对本发明做进一步的说明。下述的实施实例是说明性的,不是限定性的,不能以下述实施实例来限定本发明的保护范围。电子工业中常用覆铜板为基础材料制作电路板,覆铜板包括绝缘基板1和覆铜板铜层2。实施例1(1)往内部无图形的Fr4覆铜板上双面热压单面覆胶BOPP膜,形成有机掩蔽材料层3.使用德中DCT-BR300型号刷板机对1.5H/H覆铜板进行双面刷板(进板速度1.2mm/min;摆动频率70次/min),压缩空气吹净板面水分,微热烘干或自然干燥。进行叠片/叠层,把覆铜板正反两面分别和尺寸相同的BOPP膜贴合(覆胶面紧贴铜箔),并用橡胶辊轮轻微辊压,排出贴合面之间的空气,使其紧密贴合,以保证在后续操作中不产生相对滑动。使用德中DCT-LA400热压合设备对双面覆BOPP膜板进行压合(15千克力,100℃,走板速度100mm/min)。(2)按照设计要求钻孔使用德中DCT-DM350设备按照设计要求钻孔。将设计好的数据导入德中CircuitCAM软件,经此软件处理之后,生成设备可用的打孔数据,并导入DM350设备,将压合之后的板子至于设备平台,CCD定位,进行全自动打孔加工,根据孔径不同,具体钻孔参数也有所不同,其主要参数范围如下:钻头转速45000转/min-100000转/min,进刀速度15mm/s-30mm/s,退刀速度25mm/s-40mm/s。(3)活化及化学沉铜,形成起始导电层4.使用碱性除油剂进行除油(50-60℃,5-8min);稀盐酸溶液预浸(室温,1-2min);钯盐溶液活化(25-30℃,3-5min);解胶溶液处理(45-50℃,5-8min);碱性沉铜溶液进行沉铜(40-45℃,60-80min)。本步骤中,只有孔壁部分能与药液接触,其余板面全部被膜所覆盖。此BOPP膜表面具有疏化学活化特性,因此不能形成化学沉铜层,而孔壁的表面会形成一层较薄的化学沉铜层。(4)电镀(加厚孔壁铜层),形成电镀铜层5.使用德中DCT-TP300孔化设备进行孔壁铜层的加厚电镀。采用小电流、长时间(0.2安培-0.25安培,20min)的方式增加孔壁镀层的均匀性。为了进一步提高均镀、深镀能力,DCT-TP300孔化设备还配备了药液射流循环结构、脉冲直流电镀功能及反脉冲电镀功能。本步骤中,因为BOPP膜表面并无导电能力,因此电镀只是针对孔壁进行。(5)激光去除焊盘和线路表面覆盖的BOPP膜将数据导入德中CircuitCAM软件,经过软件处理、计算,生成激光去焊盘和线路表面覆盖的BOPP膜的路径;将路径数据导入DreamCreaTor设备操作软件中,板子置于设备平台,CCD自动对位后,激光自动去除焊盘和线路表面覆盖的BOPP膜。本步骤采用德中DCT-U5设备,涉及的关键激光加工参数如下:波长脉宽光斑直径平均功率脉冲频率加工速度加工次数355nm100ns20um8100kHz800mm/s2次(6)电镀(加厚焊盘、线路和孔壁上的铜层),沉积加厚铜层6使用德中DCT-TP300孔化设备进行加厚电镀。电镀参数为:2安培,30min。(7)激光去除非线路表面覆盖的BOPP膜本步骤采用德中CO2激光设备,涉及的关键激光加工参数如下:波长脉宽光斑直径焦点偏移平均功率脉冲频率加工速度加工次数10600nm--250um0mm2520kHz800mm/s1次(8)激光去除非线路区域上的铜箔层根据数据图形和加工中所涉及的材料,优选德中纳秒紫外激光设备U5作为加工设备;依据线路图形,使用德中CircuitCAM软件计算出线路绝缘包络线路径、非线路区域(即需去掉的铜箔区域)的分条分片路径、加热剥离去除路径。首先,用光蚀激光加工线路区域的绝缘包络线。根据计算出的线路绝缘包络线路径,向导电材料投射激光,光蚀,逐点汽化去除导电材料至绝缘材料表面,在要保留的导电材料周围制作闭合的绝缘包络沟道。然后,用光蚀激光进行分条分片加工。向导电材料投射激光,光蚀,逐点汽化去除导电材料至绝缘材料表面,将需要去除的大片导电材料细分为互相绝热的小条或小片。最后,用加热激光进行剥离加工,依次向各个互相绝热的小条或小片上投射激光,使其受热,发生变形,降低其与绝缘材料的结合力,在辅助气体的共同作用下,使小条或小片与绝缘材料分开,脱离绝缘材料表面,被转移,被收集,逐条或逐片地从绝缘材料上被剥离去除。本实施例中激光去除区域的导电层为原始铜箔,厚度均匀,大大降低了激光加工难度。加工参数如下:(9)双面层压PI膜作为阻焊膜(满板层压),形成阻焊材料层7.使用德中DCT-MP300层压机对完成叠片的双面板及PI膜进行层压,层压时为缓冲压力及平衡热量在板面平面上的分布,使用了硅橡胶垫作为热压合衬垫。依据材料特性,热压合分五步进行:step1常温低压(5min;25℃;24N/cm2);step2中温中压(30min;140℃;94N/cm2);step3高温高压(60min;220℃;188N/cm2);step4保压冷却(45min;----;188N/cm2)。本实例采用的干膜为50um杜邦KaptonHN膜。(10)组装现场激光去除焊接区(焊盘及部分插件孔)表面覆盖的PI膜,制造阻焊图案,并对焊接区表面清洁及可焊性处理,形成可焊性处理表面8.本步骤采用集成双激光头的德中DCT-3000P设备,两种激光器光源分别为:波长1064nm纳秒激光器;波长355nm皮秒激光器。本步骤细分为三步:a、用355nm皮秒激光,采用聚焦方式,沿需要去除表面PI覆盖膜的孔边缘和焊盘边缘加工轮廓线,保证将PI膜切割透而尽量不伤底层的铜箔,孔正上方上覆盖的PI膜因其下层没有与任何其他层接触,会自动脱落,随后被在线真空集尘装置吸走,而焊盘表面的覆盖的PI膜则被分割成孤立的区域;b、用1064纳米纳秒激光将焊盘表面覆盖并被分割成孤立区域的PI膜进行去除;c、再次用355nm皮秒激光,采用离焦的方式,清除焊盘表面残余物并对铜面进一步清理,达到直接可焊接的程度。本步骤亦采用德中CircuitCAM软件对加工数据进行处理并计算,生成相应的激光加工路径,再导入DCT-3000P的DreamCreaTor设备操作软件,将覆PI膜的线路板置于加工台,CCD自动定位,开始自动加工。其中光源的切换、光斑直径变换等均是在线自动执行的。本步骤涉及的关键激光加工参数如下:(11)向连接盘上添加焊料9,进行元件10贴装、插装,进行重熔焊接及或波峰焊接.向焊盘等焊接区添加固体导电膏,进行元器件装联,过回流焊进行终固化。实施例2(1)往内部已完成2层图形制做、表面已层压铜箔但未进行线路制作的板子热压PET膜使用德中DCT-BR300型号刷板机进行双面刷板(进板速度1.2mm/min;摆动频率70次/min),压缩空气吹净板面水分,微热烘干或自然干燥。使用德中DCT-LA400热压贴膜设备对完成叠片的双面板及PET膜进行热压合。(12千克力,100℃-105℃,走板速度200mm/min)。本实例采用的初始板材,即内部包含两层导电图形,外部压合了两层铜箔的四层板,为后续表述清晰,将四层导电层按剖面结构从上到下依次称顶层、次顶层、次底层和底层,中间三层介质层亦按照此种方式称为介一层、介二层和介三层。(2)激光钻孔使用德中DCT-D6(飞秒紫外)激光设备按照设计要求打孔。将设计好的数据导入德中CircuitCAM软件,经此软件处理之后,生成设备可用的打孔数据,并导入D6设备操作软件DreamCreaTor,将压合之后的板子至于设备平台,CCD定位,进行全自动打孔加工。激光钻孔关键参数:波长脉宽光斑直径平均功率脉冲频率加工速度加工次数355nm600fs20um12.5W1200kHz800mm/s12次(3)向孔内灌注导电银浆使孔导电化用碱性除胶剂清除孔内壁残余胶渣(50℃,40min,加摆动);清水冲洗板面及孔壁(2min),去除残存除胶剂;压缩空气将板面及孔内水分吹干后,热风再次干燥板面及孔壁,尤其要保证孔壁干燥无水气;将板子至于德中DCT-VT300真空灌孔设备平台上,沿孔口向孔内加注银浆(盛田801)至完全覆盖孔口,开启真空泵抽真空,孔顶部银浆将沿孔壁流至孔底部,使孔内壁附着一层导电银江,为使此附着导电层更均匀,将板子翻转,重复此步操作;用无尘布清洁板面,擦拭去除板面上孔口周围附着的浆料;板子至于烘箱,使孔壁附着的导电银浆固化(125℃,30min),形成起始导电层。(4)电流平衡区/陪镀区制作按照线路设计要求,去除板子上符合电流平衡区/陪镀区定义区域表面的PET膜,露出其下层铜箔,以做电镀孔壁时平衡电流只用。具体方法,将数据导入德中CircuitCAM软件,经过软件处理、计算,生成激光去除电流平衡区/陪镀区表面PET膜的路径;将路径数据导入德中DCT-U5设备的DreamCreaTor设备操作软件中,板子至于设备平台,CCD自动对位后,激光自动去除电流平衡区/陪镀区表面PET膜,主要加工参数如下:(5)电镀铜使用德中DCT-TP300孔化设备进行电镀镀铜(1.25安培,20min-30min,此为考虑了电流平衡区/陪镀区的影响,经优化后的电镀参数),使得在孔壁表面形成的均匀银质起始导电层的表面智商,形成一层较厚的电镀铜层。(6)激光去除焊盘和线路表面上的PET膜将数据导入德中CircuitCAM软件,经软件处理,生成激光去除焊盘和线路表面PET膜的路径;将路径数据导入德中DCT-U5设备的DreamCreaTor设备操作软件中,板子至于设备平台,CCD自动对位后,激光自动去除,主要加工参数同本实施例步骤(4)。(7)电镀(加厚焊盘、线路和孔壁上的铜层)使用德中DCT-TP300孔化设备进行电镀电镀参数:5安培,45min。(8)激光去除非线路区域的铜箔及其上面覆盖的PET膜使用德中CircuitCAM软件计算出线路绝缘包络线路径、非线路区域(即需去掉的铜箔区域,包括铜箔及铜箔上覆盖的PET膜)的分条分片路径、加热剥离去除路径(铜箔和PET膜的去除路径)。路径数据导入德中DCT-S5设备的DreamCreaTor设备操作软件中,板子至于设备平台,CCD自动对位后,激光自动加工,主要加工参数如下:(9)双面涂覆阻焊油墨并进行完全固化使用丝网印刷设备,双面印刷太阳PSR-400系列G23KHP型阻焊油墨,于烘箱中120℃烘烤60min,进行完全固化处理。(10)激光去除焊接区(焊盘及部分插件孔)表面阻焊油墨将阻焊数据导入德中CircuitCAM软件,经过软件处理、计算,生成激光去除焊接区域表面阻焊油墨的路径;将路径数据导入德中DCT-U5设备的DreamCreaTor设备操作软件中,板子至于设备平台,CCD自动对位后,激光自动去除阻焊材料。(11)添加焊料,装联元器件向焊盘等焊接区添加固体导电膏,进行元器件装联,过回流焊进行终固化。在专利说明中应该强调,基于本发明任何一步,都可以继续用传统方法制造电路板;在本发明的步骤中,可以插入传统电路板制程,比如通断检查,比如印制标记符号;可以适合双面、多层以及各种基板材料。以上所述的仅是本发明的优选实施方式,应当指出,对于本领域的普通技术人员来说,在不脱离发明构思的前提下,还可以做出若干变形和改进,这些都属于本发明的保护范围。当前第1页12
再多了解一些
本文用于企业家、创业者技术爱好者查询,结果仅供参考。