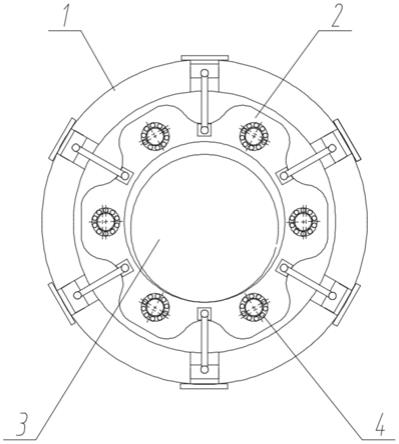
1.本发明涉及平动马达及减速机技术领域,涉及一种由平动运动直驱少齿差传动的宽速谱大扭矩马达,具体为一种由液压或电磁力直接驱动少齿差传动中行星内齿圈作行星运动的“宽速谱大扭矩马达”。
背景技术:
2.目前,生产应用中,大多数传动方案都是用高速回转马达通过减速器减速,增大输出转矩驱动工作机工作,其中还有一些是由制造厂将马达与少齿差减速机组合在一起的“减速电机”,售给用户直接使用,因该传动系统有结构紧凑、体积小、重量轻、减速比大等优点而广泛应用于各个领域。然而,该型式传动存在很大缺陷。因行星轮外周有齿隙,内孔有轴承游隙(间隙虽小,但必然存在,几何关系不变),当行星轮受到作用力时,能在这两个极小的间隙范围内任意移动和转动,在消除间隙后必然产生反作用力,其方向变化范围竞达180
°
,方向和大小的变化极其复杂且很不稳定,致使转臂轴承寿命较短,存在结构零件破坏的严重后果。
3.经对行星齿轮啮合受力分析发现,针摆减速机是由电动机输入转矩m,再经过转臂轴承(即曲轴增力机构)转换成径向力f驱动行星轮运动,其公式如下:
[0004][0005]
其中,e为行星齿轮中心与减速机针轮的几何中心之间的中心距;
[0006]
α是f与坐标轴y的夹角。
[0007]
α的余弦计算公式如下:
[0008][0009]
其中,δ2是在工作状态时,行星齿轮内孔与转臂轴承外圆(或滚子的包络线)在y坐标轴上的极小间隙;δ
e
为摆线行星齿轮移动量。
[0010]
由此可见,因少齿差传动的e很小,所以f必然很大,又是在高转速状态下工作,轴承寿命较短是必然现象,并且当δ2为零时,作用力方向α为零,即使输入很小的转矩m,径向力f也趋于无穷大,这是有关零件破坏的根本原因。
技术实现要素:
[0011]
本发明提供一种由平动运动直驱少齿差传动的宽速谱大扭矩马达,结构简单紧凑,不仅省去传动机构,而且实现大扭矩、宽速谱输出,性能更稳定,有效提高产品寿命;
[0012]
为实现上述目的,本一种由平动运动直驱少齿差传动的宽速谱大扭矩马达,包括内齿圈、中心齿轮和驱动组件;
[0013]
本发明选用的少齿差传动是,内齿圈为主动,作行星运动,中心齿轮为被动,只能自转并输出的传动形式;在平动导轨作用下,多组驱动组件直接将力作用在内齿圈上,使内
齿圈作平动运动,内齿依次地与中心齿轮的外齿啮合,驱动中心齿轮旋转。
[0014]
一种方案,每组驱动组件包括活塞和活塞杆;
[0015]
活塞径向滑动安装在齿轮箱体上的腔孔内,腔孔的一端通过端盖密封并形成密闭的油腔;
[0016]
配油装置将压力油通入油腔内为活塞提供动力;
[0017]
所述活塞杆的两端分别球铰接安装在活塞上、槽孔i内。
[0018]
一种方案,每组驱动组件包括双柱头叶片;
[0019]
双柱头叶片的两端头分别活动并密封设置在槽孔ii、槽孔i内;
[0020]
多个双柱头叶片的中部将内齿圈与齿轮箱体之间的内腔分为多个密封腔体,配油装置为每个密封腔体提供压力油,并驱动内齿圈动作。
[0021]
一种方案,每组驱动组件包括设置在齿轮箱体上的衔铁,衔铁靠近内齿圈的一端设有滚子,绕组绕设在衔铁上并引出至外侧与相应通电组件连接;多组通电组件分别与控制器连接,控制器控制其相应的通断电。
[0022]
进一步的,所述内齿圈上设有多个以内齿圈的轴线圆周均匀布置的通孔;
[0023]
所述平动导轨为多组、并以中心齿轮的轴线圆周均匀布置;每组平动导轨包括曲轴,曲轴的两端同轴并转动安装在齿轮箱体上,中部偏心并转动安装装在通孔内;
[0024]
曲轴的偏心距与少齿差传动中心距相等。
[0025]
一种并联组合的宽速谱大扭矩马达传动系统,包括多个由平动运动直驱少齿差传动的宽速谱大扭矩马达,其并联设置在同一根输出轴上。
[0026]
与现有技术相比,本一种由平动运动直驱少齿差传动的宽速谱大扭矩马达具有以下优点:
[0027]
由于采用液压或者电磁力的驱动方式,直接将力作用在内齿圈上,直接驱动内齿圈做平动运动与中心齿轮啮合,由中心齿轮输出回转运动和转矩,这种传动方案一方面取代传统的回转电机,而且还省去所有中间传动机构和零件,另一方面在整个传动链中,没有高速转轴,运动更加平稳,零件寿命更长;由于设置平动导轨,可提高平动运动精度,而且设置多组平动导轨,还能防止行星内齿圈产生自转,又可省去防止产生自转的机构,内齿圈仅作平动运动,受力状态稳定性能更优;
[0028]
由于可将本装置多组并排设置,依次套装在同一输出轴上,可实现同一输出轴上的更大扭矩输出,且组数不限,扭矩可无限增大,还可完全消除“力偶矩”,运动更加平稳,使用范围更广,更加灵活。另外该并联方案的轴向尺寸与径向尺寸没有关联,用户选用时可依据不同的要求,分别进行设计,极为方便灵活。由于油腔位置固定不动,为选用简单的脉冲数字控制提供了方便条件,而且输出轴的转数和转角没有积累误差。
附图说明
[0029]
图1是本发明中的驱动组件实施例1主视图;
[0030]
图2是本发明中的驱动组件实施例1局部放大图;
[0031]
图3是本发明中的驱动组件实施例2主视图;
[0032]
图4是将多组本发明并联连接在输出轴的左视图;
[0033]
图5是本发明的配油装置的第一方案简图;
[0034]
图6是本发明的配油装置的第二方案简图;
[0035]
图7是本发明的配油装置的第三方案简图;
[0036]
图中:1、齿轮箱体,11、腔孔,2、内齿圈,3、中心齿轮,31、输出轴,4、平动导轨,41、曲轴,51、活塞,52、活塞杆,53、端盖,54、槽孔i,55、双柱头叶片,56、槽孔ii,61、进油管路,62、出油管路,63、给油管路,71、阀体,72、阀芯,73、接油孔,74、进出油孔,81、固定圆盘,82、旋转圆盘,83、油腔孔。
具体实施方式
[0037]
下面结合附图对本发明作进一步说明。
[0038]
如图1所示,本一种由平动运动直驱少齿差传动的宽速谱大扭矩马达,包括内齿圈2、中心齿轮3和驱动组件;
[0039]
内齿圈2的轴线与中心齿轮3轴线平行,内齿圈2的轴线绕中心齿轮3的轴线公转,中心齿轮3的轴线固定;在平动导轨4作用下,多组驱动组件直接将力作用在内齿圈2上,使内齿圈2作平动运动,内齿依次地与中心齿轮3的外齿啮合,驱动中心齿轮3旋转。
[0040]
如图1、图2所示,进一步的,每组驱动组件包括活塞51和活塞杆52;
[0041]
活塞51径向滑动安装在齿轮箱体1上的腔孔11内,腔孔11的一端通过端盖53密封并形成密闭的油腔;
[0042]
配油装置将压力油通入油腔内为活塞51提供动力;
[0043]
所述活塞杆52的两端分别球铰接安装在活塞51上、槽孔i54内。
[0044]
如图3所示,进一步的,每组驱动组件包括双柱头叶片55;
[0045]
双柱头叶片55的两端头分别活动并密封设置在槽孔ii56、槽孔i54内,多个双柱头叶片55的中部将内齿圈2与齿轮箱体1之间的内腔分为多个密封腔体,配油装置为每个密封腔体提供压力油,并驱动内齿圈2动作。
[0046]
进一步的,每组驱动组件包括设置在齿轮箱体1上的衔铁,衔铁靠近内齿圈2的一端设有滚子,绕组绕设在衔铁上并引出至外侧与相应通电组件连接;多组通电组件分别与控制器连接,控制器控制其相应的通断电。
[0047]
进一步的,所述内齿圈2上设有多个以内齿圈2的轴线圆周均匀布置的通孔;
[0048]
所述平动导轨4为多组、并以中心齿轮3的轴线圆周均匀布置;每组平动导轨4包括曲轴41,曲轴41的两端同轴并转动安装在齿轮箱体1上,中部偏心并转动安装装在通孔内;
[0049]
曲轴41的偏心距与少齿差传动中心距相等。
[0050]
进一步的,将多个本马达并联设置在同一根输出轴31,并联数量不限,形成一种并联组合的宽速谱大扭矩马达传动系统,即每个中心齿轮3的中部轴向限位套装在输出轴31上。
[0051]
本一种由平动运动直驱少齿差传动的宽速谱大扭矩马达,主要特点在于:
[0052]
少齿差传动。该传动方案中的少齿传动部分,选用的是内齿圈2为主动件作平动运动,再通过中心齿轮3输出的少齿差传动。
[0053]
平动马达。驱动组件是输出为平动运动的“平动马达”,就是用一个断面为矩形的圆环(内齿圈2),在有平动导轨4约束的条件下,绕圆环外周依次给圆环施加径向力,此时圆环能输出平面平行运动,该平动马达取代了传统的回转马达,直接提供平行运动。
[0054]
平动运动导轨。平动运动物体上每一个质点都是以e为半径,绕自己的回转中心作圆周运动,与曲轴41中的曲拐运动完全一样,所以这个物体的任意位置都可安装这样的曲轴41,在被动状态下,平动导轨4主要包括曲轴41,能有效的约束平动运动。
[0055]
开环控制组件。固定圆盘81上设有油腔孔83,油腔孔83的孔数和活塞51油腔数相同并连通;旋转圆盘82上加工两段对称布置的圆弧槽,两槽端的距离与固定圆盘81上的油腔孔83直径相等,两段圆弧槽分别与进油管路61和回油管路连通(图中未表示),当控制组件的马达带动旋转圆盘82转动时,即可依序给油腔供油驱动宽速谱大扭矩马达作相同转速的转动。
[0056]
并联传动方案。如图4所示,本发明还提供一种将上述马达并联组合的传动方案。由于该马达是径向布局的外驱动形式,所有传动件都在同一个平面上,整体外形也是很薄的矩形断面圆环,因此我们可以把它看作是一个“部件”,然后把同一规格参数(注:传动比i为双数)的“圆盘形部件”转180度,并排安装到与它配套的输出轴31上。因为这些“部件”都是独立工作,互不干扰;所以并联数量不受限制,输出功率和扭矩也不受限制,这种模块化设计,积木式组合方案对大型、特大型设备有重要意义。用户选择功率扭矩和外形尺寸可根据需要灵活搭配,也基本不受限制。由于马达每个环节都不自锁,所以并联组合传动也是安全的。
[0057]
本一种由平动运动直驱少齿差传动的宽速谱大扭矩马达使用时,根据实际使用来进行选择驱动组件的数量,比如可为6、8、10等,多个驱动组件圆周分布在内齿圈2外侧,驱动组件开始动作,在平动导轨4作用下,驱动组件将力作用在内齿圈2上,使其绕设中心齿轮3进行公转(平动),并且内齿圈2不发生自转,内齿圈2平动时始终与中心齿轮3保持啮合,内齿圈2与中心齿轮3的啮合点为齿轮、齿条啮合关系,因此实现大扭矩、大速比输出;本装置直接将力作用在内齿圈2上,通过内齿圈2公转,与中心齿轮3啮合输出扭矩,实现动力输出,比传统采用双偏心套带动摆线齿轮和输出轴31的方式更加简单紧凑,节省零部件。
[0058]
实施例1
[0059]
如图1、图2所示,当驱动组件可包括活塞51和活塞杆52时,首先在齿轮箱体1上径向开设有与驱动组件数量一致的腔孔11,腔孔11外侧通过端盖53进行密封,活塞51滑动安装在腔孔11内,并与腔孔11形成密闭油腔,配油装置将压力油通入油腔内为活塞51提供动力;活塞杆52的两端分别活动安装在活塞51上、槽孔i54内,优选的,这种活动安装为球铰接连接方式;
[0060]
当配油装置将压力油注入油腔内带动活塞51移动,不同位置油腔内的油压不同,使得活塞杆52对内齿圈2不同的作用力,一方面,驱动组件越多时,作用在内齿圈2上的作用力更平衡,使内齿圈2平动运动更加稳定,另一方面,内齿圈2在平动导轨4作用下进行平动,与中心齿轮3啮合实现中心齿轮3的自转。
[0061]
这种方式可增加活塞51的数量和有效面积,增大中心齿轮3每转排量,但可能存在对内齿圈2外圆面积利用率低的情况,造成减速机尺寸不够合理,因此适用于大型大扭矩减速器的使用;
[0062]
作为一种方案,可将塑胶皮囊放置在油腔内,通过塑胶皮囊的弹性压缩带动活塞杆52将力作用在内齿圈2上,因此这种塑胶皮囊的方式不再产生任何泄漏,成为零泄漏的液压驱动装置。
[0063]
实施例2
[0064]
如图3所示,当驱动组件为双柱头叶片55,双柱头叶片55两端头分别密封活动设置在槽孔ii56、槽孔i54内,多个双柱头叶片55的中部叶片将内齿圈2与齿轮箱体1之间的内腔分为多个密封腔体,配油装置为每个密封腔体提供压力油,因此多个密封腔体内的压力油在密封腔体内对内齿圈2作用,使内齿圈2与中心齿轮3啮合力更加均匀,当内齿圈2在平动导轨4作用下进行平动时,双柱头叶片55的两端分别在相应的槽孔i54、槽孔ii56内活动,实现中心齿轮3的自转,保障大扭矩动力输出;
[0065]
用双柱头叶片55围成的封闭腔体能够充分利用内齿圈2外圆面积,利用率可达百分之百,其主要依据平动运动特点,由于内齿圈2平动时没有自转,公转半径较小,相应每个质点的运动速度和距离都很小,完全可以用双柱头叶片55的摆动以及在槽孔i54、槽孔ii56内的径向滑动,满足平动运动在坐标轴x、y方向的动作;这种双柱头叶片55方式没有高速滑动、受力状态较好,并且采用封闭腔体的方式是的整体结构尺寸较小,工艺性也很好,适合小型大扭矩减速器的使用;
[0066]
实施例1和实施例2是采用平动马达方式的驱动,此时内齿圈2为主动件,直接驱动中心齿轮3,省掉传统的中间传动机构,主要通过配油装置依次注入压力油,内齿圈2只有公转没有自转的平面平行运动;
[0067]
如图5所示,作为配油装置的一种方案,每个驱动组件对应设有一个进油管路61、出油管路62和给油管路63,即给油管路63安装在内齿圈2上并随其平动进行移动,进油管路61、出油管路62靠近平动轨道,给油管路63为相应的油腔或者封闭腔体提供压力油,当内齿圈2做平动运动时,可通过给油管路63与进油管路61连接进行进油,给油管路63与出油管路62连接进行出油,因此实现随着内齿圈2平动运动提供相应的压力油;
[0068]
如图6所示,作为配油装置的第二种方案,每个驱动组件对应设有阀体71,阀体71上设有接油孔73和进出油孔74,内设有阀芯72,阀芯72的输出端可与内齿圈2外侧径向接触,当内齿圈2做平动运动时,将带动阀芯72在阀体71内移动,压力油通过液压马达从进出油孔74进行进出,并随着阀芯72在阀体71内移动,阀芯72内腔体的压力油从接油孔73为相应的油腔或者封闭腔体提供压力油,因此可随着内齿圈2的平动,相应阀芯72进行调整,并驱动组件提供不同的作用力;
[0069]
如图7所示,作为配油装置的第三种方案,包括固定圆盘81和旋转圆盘82,固定圆盘81上设有与齿轮箱体1上腔孔11一致的油腔孔83,即多个油腔孔83对应与齿轮箱体1上的腔孔11连通,旋转圆盘82上设有两段可覆盖在全部油腔孔83上的圆弧槽,优选的,圆弧槽的槽宽与油腔孔83的一致,两段圆弧槽分别与进油管路61和回油管路连通,当控制组件的马达带动旋转圆盘82转动时,压力油从相应油腔孔83进入腔孔11内为驱动组件提供动力,即可依序给腔孔11供油驱动宽速谱大扭矩马达作相同转速的转动,比如驱动组件为12个,相应的油腔孔83为12个,而旋转圆盘82上的圆弧槽为一对,每个油槽的大小可包括六个油腔孔83,控制组件的马达带动旋转圆盘82转动,根据内齿圈2的运动情况,其中一个圆弧槽进行进油处理,;另一个圆弧槽进行回油处理,这种开环方式有效实现内齿圈2的平动,精度更高。
[0070]
实施例3
[0071]
每组驱动组件包括设置在齿轮箱体1上的衔铁,衔铁靠近内齿圈2的一端设有滚
子,绕组绕设在衔铁上并引出至外侧与相应通电组件连接,因此控制器控制相应绕组通电,衔铁对内齿圈2外侧进行磁性作用力,使内齿圈2在平动导轨4作用下进行平动,并带动中心齿轮3的自转,保障大扭矩动力输出;
[0072]
本装置的平动导轨4是保障内齿圈2在平动的过程中不发生自转,优选的,曲轴41的两端通过轴承转动安装在齿轮箱体1内,中部偏心距与内齿圈2公转半径一致,并可通过轴承套装在内齿圈2上,曲轴41对内齿圈2进行限位,使内齿圈2在运动过程中只做平动运动,而无法进行自转。
[0073]
内齿圈2和中心齿轮3上齿形可采用渐开线齿,也可采用摆线齿形;如图4所示,本装置外形结构为扁圆结构,整体紧凑,可以多组进行并联设置,形成一个并联组合的宽速谱大扭矩马达传动系统,即每个中心齿轮3的中部可为花键槽或者平键槽结构,可将多个本装置通过花键或者平键的方式套装在输出轴31上,多个本装置进行并联设置,可实现同一输出轴31上的更大扭矩输出,使用范围更广,更加灵活。
[0074]
本由平动运动直驱少齿差传动的宽速谱大扭矩马达采用液压或者电磁力的驱动方式,直接将力作用在内齿圈2上,这种直接驱动使得内齿圈2做平动运动带动中心齿轮3转动,不仅节省传动机构,避免传统采用双偏心套带动行星齿轮进行驱动的方式,使得整体结构更加简单紧凑,而且保障中心齿轮3大扭矩的转矩输出;并且设置平动导轨4,用于约束内齿圈2平动运动以提高精度,而且防止其自转。
再多了解一些
本文用于企业家、创业者技术爱好者查询,结果仅供参考。