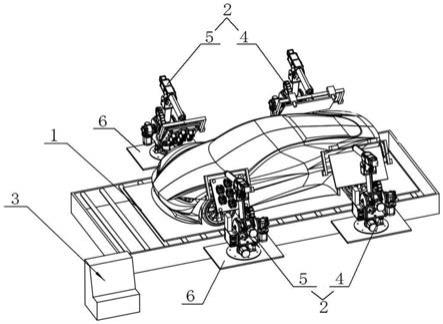
1.本发明涉及一种用于汽车修复的生产线,特别涉及一种整车制造及修配环节的车身覆盖件漆面缺陷的光学自动检测与智能修复的生产线。
背景技术:
2.汽车的整车制造涉及冲压、焊接、涂装、总装四大工艺,其中涂装工艺的主要作用是为车身喷涂油漆,在提高车身防锈、耐腐蚀性能的同时,增加车身的美观程度,汽车车身在涂装和总装工艺过程中,由于操作不当、运输磕碰等会在车身覆盖件表面形成漆面缺陷,漆面缺陷不仅影响车身的美观、防锈、耐腐蚀性能,而且会对整车的售价产生较大的影响,因此整车在制造过程中和出厂前会对车身的漆面缺陷进行检测与修复。现阶段,汽车车身漆面缺陷的检测与修复工作一般由人工完成,工人在平行光条件下通过目视检测和触摸检测的方法确定漆面缺陷的种类、特征、尺寸及位置,通过手持修复工具对缺陷进行打磨、抛光、喷涂等修复操作。人工检测及修复的缺点在于,经验依存度高、检测准确率不稳定、检测效率低、检测周期长、工序繁琐复杂、劳动强度大、修复质量不稳定、容易对漆面造成附加损伤、单点修复效率低、人工成本高、修复周期长等。综上,伴随先进检测技术和智能制造技术的发展,开发一款应用于整车制造及修复领域,具备汽车漆面缺陷检测与缺陷修复的一体化智能装备线成为提升整车制造水平的一条路径,通过设计光学检测系统,对车身漆面缺陷进行检测、分类、测量、定位,通过数字理论对缺陷信息进行求解,形成修复工艺参数矩阵,通过工艺修复参数矩阵驱动修复装置,完成对漆面缺陷的自动化智能修复。
技术实现要素:
3.为了解决上述技术问题,本发明提供一种汽车车身漆面缺陷智能检测与修复生产线,包括运载定位系统、检修系统和主控制系统,所述的运载定位系统包括运输滑道和载物台,所述的运输滑道自带驱动电机,载物台设在运输滑道上,载物台上设有轮胎固定器和定位传感器,驱动电机和定位传感器分别通过线路与主控制系统相连;检修系统设在运输滑道的两侧,所述的检修系统包括检测系统和修复系统,检测系统和修复系统沿运输滑道运行的方向先后布置;检测系统和修复系统通过连接平台与生产车间平台相连接,运载定位系统、检测系统和修复系统分别通过线路与主控制系统相连。
4.所述的检测系统包括检测系统机械臂、检测系统搭载框架、检测系统步进电机、工业相机、投影屏幕和检测系统控制器,检测系统机械臂与检测系统搭载框架的顶部相连,所述的检测系统搭载框架为c型框,检测系统搭载框架的两末端设有检测系统步进电机,投影屏幕的两侧分别设有转轴,投影屏幕两侧的转轴分别与检测系统搭载框架两端的检测系统步进电机输出轴相连;所述的工业相机设在检测系统搭载框架的顶部;所述的检测系统控制器设在检测系统机械臂上,通过线路与主控制系统相连。
5.所述的修复系统包括修复系统机械臂、修复系统搭载框架、矩阵框架、修复单元、连接组件和修复系统控制器,修复系统机械臂与修复系统搭载框架的顶部相连,所述的修
复系统搭载框架为c型框,修复系统搭载框架的两末端设有修复系统步进电机,矩阵框架的两侧分别设有转轴,矩阵框架两侧的转轴分别与修复系统搭载框架两端的修复系统步进电机输出轴相连;所述的矩阵框架上设有数个矩阵式排布的安装槽孔,每个安装槽孔内设有一个修复单元,所述的修复单元通过连接组件与安装槽孔连接;所述的修复系统控制器设在修复系统机械臂上,通过线路与主控制系统相连。
6.所述的矩阵框架包括矩阵框架底板和矩阵框架盖板,矩阵框架底板上设有数个矩阵式排布的安装槽孔;矩阵框架盖板上设有与矩阵框架底板的安装槽孔对应的通孔;矩阵框架盖板扣合在矩阵框架底板上。
7.所述的修复单元包括风道装置、主壳体、磨抛喷涂仓和涡轮磨抛装置,所述的风道装置设在主壳体上部,磨抛喷涂仓设在主壳体的下部,风道装置、主壳体与磨抛喷涂仓内部贯通;风道装置上部设有进风通道,进风通道上设有流量控制阀,流量控制阀通过线路与修复系统控制器相连;主壳体的上端设有支撑格栅,支撑格栅中间设有上轴孔,主壳体与磨抛喷涂仓之间设有隔离格栅,隔离格栅中间设有下轴孔;所述的涡轮磨抛装置包括中心轴、涡轮和磨抛盘,中心轴上下两端分别通过支撑轴承枢接在上轴孔和下轴孔内,涡轮设在中心轴下部,位于主壳体内,中心轴下端与磨抛盘相连,磨抛盘位于磨抛喷涂仓内;磨抛喷涂仓内设有喷头和负压吸头,喷头通过管路与喷漆泵相连,负压吸头通过管路与负压泵相连;所述的主壳体的内壁设有高热反射率涂层,主壳体内设有等间距圆周分布的加热器,加热器通过线路与修复系统控制器相连;主壳体内还设有温度传感器,温度传感器通过线路与修复系统控制器相连;修复系统控制器通过线路与喷漆泵和负压泵相连。
8.进一步的,所述的风道装置包括整流仓、集气仓和加速导流板,整流仓为喇叭形结构,进风通道设在整流仓上部,整流仓下端与集气仓螺纹连接;所述的集气仓为圆柱体结构,加速导流板设在集气仓的底部,加速导流板与集气仓螺纹连接;所述的加速导流板中部开设有向下凸出的渐缩式导气孔,加速导流板上开设有数个围绕渐缩式导气孔圆周方向等间距分布的渐缩式导气小孔;整流仓内设有压力传感器,压力传感器通过线路与修复系统控制器相连。
9.进一步的,所述的磨抛喷涂仓为圆台型中空结构,磨抛喷涂仓的下边缘设有周向分布的软体刷,磨抛盘的磨抛面低于磨抛喷涂仓的下边缘,高于软体刷的下边缘;磨抛喷涂仓内还设有喷涂传感器和浓度传感器,喷涂传感器和浓度传感器通过线路与修复系统控制器相连。
10.所述的连接组件包括固定框架和连接支架,所述的固定框架中间设有修复单元连接孔,修复单元设在修复单元连接孔内;固定框架的外圈对称设有燕尾型凸台,燕尾型凸台上设有弹簧孔,弹簧孔内设有弹簧,自然状态下弹簧高于弹簧孔深度;固定框架的下部周圈均匀设有弹簧片;所述的连接支架包括连接支架底板和连接支架盖板,连接支架底板上设有固定框架安装孔,固定框架安装孔的底部周圈设有支撑凸台,固定框架安装孔的侧边设有与固定框架的燕尾型凸台对应的燕尾型凹槽;固定框架设在固定框架安装孔内,支撑凸台对固定框架起支撑作用;所述的连接支架盖板上设有与固定框架安装孔相对应的通孔,连接支架盖板扣合在连接支架底板上;连接支架固定设在矩阵框架的安装槽孔内。
11.进一步的,所述的固定框架为矩形框,固定框架相对的两条边外侧对称设有两个燕尾型凸台,固定框架的每条边下部分别设有两个弹簧片;所述的连接支架为六边形;连接
支架盖板上设有与固定框架的燕尾型凸台对应的燕尾槽,燕尾槽内设有与燕尾型凸台上的弹簧对应的弹簧限位孔,弹簧的顶端卡接在弹簧限位孔内;固定框架安装孔为与固定框架相应的矩形槽孔,固定框架安装孔的支撑凸台上设有与固定框架底部的弹簧片对应的弹簧片限位槽,固定框架底部的弹簧片卡接在弹簧片限位槽内。
12.进一步的,所述的修复单元连接孔的内圈由数个弧形凸台组成,每个弧形凸台的弧面设有内螺纹,修复单元的外壁设有相应的外螺纹,修复单元与修复单元连接孔通过螺纹连接。
13.本发明的工作原理:
14.首先将待检测车辆通过轮胎固定器固定在载物台上,定位传感器定位车辆位置信息并传输给主控制系统,主控制系统控制运输滑道带动载物台向前运动,当车身前半部分接近检测系统时,运输滑道减速至精确停止,使待检测车辆的前半部分进入检测系统的工作区内,主控制系统控制运输滑道及载物台在检测过程中保持静止,主控制系统控制运输滑道两侧的检测系统对待测车辆前半部分车身的漆面缺陷进行检测、分类、测量,并结合定位传感器对缺陷相对位置进行定位后,将相关缺陷及缺陷位置信息传输给主控制系统,由主控制系统完成缺陷信息的计算、整理、工艺修复参数的生成;完成车身前半部分漆面缺陷检测后,主控制系统控制运输滑道继续向前运动,将刚完成漆面缺陷检测的待测车辆前半部分运输到修复系统的工作区内,此时,待检测车辆的后半部分车身位于检测系统的工作区内,主控制系统控制检测系统完成对待检测车辆后半车身的漆面缺陷检测工作,控制修复系统对已经检测完毕的前半部分漆面缺陷进行自动修复;如此往复,形成流水线,实现车辆漆面缺陷的先检测后修复工作。
15.检测系统依据结构光相位偏折术理论进行搭建,利用结构光相移条纹照射车身表面后发射条纹的相位变化,经过计算实现漆面缺陷的相关测量等工作。投影屏幕的主要作用是显示由主控制系统所生成的编码条纹并将其投射到待检测的车身表面,投影屏幕可以选用商用的lcd显示器,也可以依据实际应用情况进行定制,投影屏幕与检测系统搭载框架进行连接,工业相机的主要作用是拍摄经待测车身漆面调制并反射回来的条纹信息,工业相机被固定在检测系统搭载框架上,在应用过程中,投影屏幕和工业相机两者之间的相对位置关系必须是固定的,可以通过位于检测系统搭载框架两侧的检测系统步进电机调整投影屏幕的转角进而确定两者的相对位置关系,投影屏幕与工业相机之间的具体位置关系由标定过程来确定,位置关系的具体数值导入到主控制系统中,实现检测系统的标定。检测系统机械臂可以带动检测系统搭载框架进行位姿的改变,以实现大面域范围内复杂几何面型背景下车身漆面缺陷的精确检测。
16.所述的运输滑道为现有的流水线滑道设备,用于搭载载物台运输待检测车辆;所述的轮胎固定器为现有设备,用于将待检测汽车固定在载物台上,所述的定位传感器也为现有设备,用于确定车辆在运载定位系统笛卡尔坐标系下的坐标,为检测与修复功能的实现提供精确的参考位置信息;所述的主控制系统的主要作用是对整个缺陷检测与修复过程进行控制,主要控制内容包括但不限于结构光条纹的投影编码生成、投射,工业相机的图像捕捉,检测系统机械臂、检测系统搭载框架位姿改变,缺陷的定位、分类、特征、尺寸计算,缺陷工艺修复参数的确定,修复系统机械臂、修复系统搭载框架、修复单元等修复工作操作的实现,运载定位系统的运动速度、位置的控制,检测与修复工作生产节拍的控制等。
17.漆面缺陷自动修复过程如下:将修复系统中的每个修复单元的流量控制阀分别与空气压缩泵相连,修复系统控制器控制启动修复系统机械臂,通过修复系统机械臂和修复系统搭载框架带动矩阵框架多位置、多角度转动,至修复单元的磨抛喷涂仓下部扣在待磨抛喷涂的车辆漆面缺陷处,使磨抛盘与漆面接触。
18.由于每个修复单元均通过连接组件与矩阵框架相连,连接组件中固定框架安装在连接支架的固定框架安装孔内,固定框架安装孔的尺寸略大于固定框架,固定框架的燕尾型凸台嵌入燕尾型凹槽内,燕尾型凹槽的尺寸略大于燕尾型凸台,固定框架上部设置的弹簧和下部设置的弹簧片对固定框架起到纵向支撑作用,当修复单元受到不同角度的压力时,压缩相应角度的弹簧或弹簧片,使固定框架能够在固定框架安装孔内发生小角度的升降或摆动;由于汽车覆盖件表面形状不规则,有一定的弧度或坡度,因此当修复单元底面接触汽车漆面时会发生适应性偏转,使修复单元底面对于汽车覆盖件表面更加贴合,提升修复单元的面型适应柔性。修复系统机械臂能够带动修复系统搭载框架多自由度转动,修复系统搭载框架上的修复系统步进电机能够带动矩阵框架沿转轴发生翻转,最终使矩阵框架带动修复单元多自由度多角度转动,同时每个修复单元可以根据漆面形状独立进行小角度贴合调整,数个修复单元矩阵式排布能够增加修复面积,同时对不规则汽车漆面最大限度贴合。
19.矩阵式排布的修复单元与漆面贴合后,启动空气压缩泵,向修复单元内输送压力气流,气流从风道装置的进风通道进入整流仓,整流仓依据流体力学的基本原理,平滑气流,使压力气流流速降低,压力提升,气流经过整流仓整流后,在集气仓内富集和稳压,消除气流中的一些湍流,稳压后的气流经过加速导流板上的渐缩式导气孔加速导出,流进主壳体内,渐缩式导气小孔起到辅助作用,增大气流的导出效率。整流仓上部的压力传感器对风道装置内的气体压力进行监控,并实时将压力信号传输给控制系统,由控制系统控制流量控制阀的开度进而控制进入装置内的气体流量。气流经过风道装置消湍、稳流、增速后进入主壳体内,主壳体内的加热器通电升温对气流进行加热,加热后的气流沿着加热器之间形成的导流通道向下流通,高热反射率涂层用以降低热辐射的扩散,保持腔室内的温度,提升气体加热效率;温度传感器实时监测加热器温度和气流温度,并将数据传输给控制系统,进而由控制系统调节施加在加热器中的电功率,达到气体温度的有效控制。加热后的气流继续向下流通,流经涡轮磨抛装置时,高温、高压气流驱动涡轮磨抛装置的涡轮转动,涡轮带动中心轴在支撑轴承内旋转,进而带动中心轴下端的磨抛盘旋转,实现对漆面的磨抛操作;高温气流同时具有提升涡轮转速和软化漆面的作用。
20.在进行磨抛作业时负压泵启动,磨抛喷涂仓内的负压吸头将流进磨抛喷涂仓内的气流以及磨抛产生的碎屑粉尘一并吸出,以保证磨抛喷涂仓的环境清洁度,避免废弃物附着在作业面上造成漆面的损伤,提升打磨喷涂效果。磨抛后启动喷漆泵,对磨抛后的漆面进行喷涂修复,负压吸头同时将喷涂作业时所产生的粉尘、气溶胶等废弃物进行清吸,直到完成修复。
21.本发明的有益效果:
22.本发明能够智能化、自动、高效的进行汽车车身漆面缺陷的检测、定位、修复工艺方案的确定和修复等工作,实现了检测
‑
修复一体化操作。通过将结构光相位偏折原理引入车身漆面检测环节,构建了以结构光为基础的光学漆面缺陷检测系统来代替传统的平行光
条件下的人工目视及触摸检测,结构光漆面检测系统通过反射光条纹的相位变化,实现漆面缺陷的识别、测量、定位,结合图像处理技术等实现缺陷的分类,实现汽车车身漆面缺陷的高精度、高准确率、高效率、非接触的准确检测与定位,克服了传统人工检测方法在检测效率、检测精度、可靠性、成本等方面不足;通过结合依据漆面缺陷特征的修复工艺参数智能推导算法,实现了修复工艺参数的智能化、专家化解决方案,在最佳修复工艺参数确定后,修复工艺参数以矩阵的形式呈现,并用于驱动矩阵式漆面缺陷自动修复系统,该系统具有大面域、复杂几何形貌的漆面缺陷修复能力,通过控制系统传输过来的位置信息、修复工艺参数信息,实现漆面缺陷的自动修复,克服了传统人工缺陷修复的相关不足。所构建的汽车漆面缺陷智能检测与修复生产线,作为整车制造及修复领域的一款智能装备,具备完全替代人工进行漆面缺陷检测与修复的相关工作,在降低劳动成本、提高生产效率、可靠性和稳定性等方面发挥作用,将极大的提升汽车制造领域的自动化、智能化生产水平,提高汽车漆面缺陷检测与修复的一致性和可靠性。
附图说明
23.图1为本发明整体结构示意图;
24.图2为本发明运载定位系统结构示意图;
25.图3为本发明检测系统整体结构示意图;
26.图4为本发明检测系统局部结构示意图;
27.图5为本发明修复系统整体结构示意图;
28.图6为本发明矩阵框架结构示意图;
29.图7为本发明矩阵框架底板结构示意图;
30.图8为本发明矩阵框架盖板结构示意图;
31.图9为本发明修复单元整体结构示意图;
32.图10为本发明修复单元结构示意图;
33.图11为本发明修复单元涡轮磨抛装置结构示意图;
34.图12为本发明修复单元风道装置结构示意图;
35.图13为本发明修复单元主壳体结构示意图;
36.图14为本发明固定框架结构示意图;
37.图15为本发明连接支架结构示意图;
38.图16为本发明连接支架底板结构示意图;
39.图17为本发明连接支架盖板结构示意图;
40.图18为本发明固定框架与修复单元结构示意图;
41.1.运载定位系统2.检修系统3.主控制系统4.检测系统5.修复系统
42.6.连接平台101.运输滑道102.载物台103.轮胎固定器
43.401.检测系统机械臂402.检测系统搭载框架403.检测系统步进电机
44.404.工业相机405.投影屏幕406.检测系统控制器501.修复系统机械臂
45.502.修复系统搭载框架503.矩阵框架504.修复单元505.连接组件
46.506.修复系统控制器507.修复系统步进电机508.矩阵框架底板
47.509.矩阵框架盖板510.安装槽孔511.风道装置512.主壳体
48.513.磨抛喷涂仓514.涡轮磨抛装置515.进风通道516.流量控制阀
49.517.支撑格栅518.隔离格栅519.中心轴520.涡轮521.磨抛盘
50.522.喷头523.负压吸头524.管路525.加热器526.整流仓
51.527.集气仓528.加速导流板529.渐缩式导气孔530.渐缩式导气小孔
52.531.压力传感器532.软体刷533.固定框架534.连接支架
53.535.燕尾型凸台536.弹簧537.弹簧片538.连接支架底板
54.539.连接支架盖板540.固定框架安装孔541.支撑凸台542.燕尾型凹槽
55.543.弹簧限位孔544.弹簧片限位槽545.弧形凸台
具体实施方式
56.请参阅图1
‑
18所示:
57.本发明提供一种汽车车身漆面缺陷智能检测与修复生产线,包括运载定位系统1、检修系统2和主控制系统3,所述的运载定位系统1包括运输滑道101和载物台102,所述的运输滑道101自带驱动电机,载物台102设在运输滑道101上,载物台102上设有轮胎固定器103和定位传感器,驱动电机和定位传感器分别通过线路与主控制系统3相连;检修系统2设在运输滑道101的两侧,所述的检修系统2包括检测系统4和修复系统5,检测系统4和修复系统5沿运输滑道101运行的方向先后布置;检测系统4和修复系统5通过连接平台6与生产车间平台相连接,保证检测系统4和修复系统5的水平性、稳定性及可靠性;运载定位系统1、检测系统4和修复系统5分别通过线路与主控制系统3相连。
58.所述的检测系统4包括检测系统机械臂401、检测系统搭载框架402、检测系统步进电机403、工业相机404、投影屏幕405和检测系统控制器406,检测系统机械臂401与检测系统搭载框架402的顶部相连,所述的检测系统搭载框架402为c型框,检测系统搭载框架402的两末端设有检测系统步进电机403,投影屏幕405的两侧分别设有转轴,投影屏幕405两侧的转轴分别与检测系统搭载框架402两端的检测系统步进电机403输出轴相连;所述的工业相机404至少两部,分别设在检测系统搭载框架402的顶部左右两侧;所述的检测系统控制器406设在检测系统机械臂401上,通过线路与主控制系统3相连。
59.所述的修复系统5包括修复系统机械臂501、修复系统搭载框架502、矩阵框架503、修复单元504、连接组件505和修复系统控制器506,修复系统机械臂501与修复系统搭载框架502的顶部相连,所述的修复系统搭载框架502为c型框,修复系统搭载框架502的两末端设有修复系统步进电机507,矩阵框架503的两侧分别设有转轴,矩阵框架503两侧的转轴分别与修复系统搭载框架502两端的修复系统步进电机507输出轴相连;所述的矩阵框架503上设有数个矩阵式排布的安装槽孔510,每个安装槽孔510内设有一个修复单元504,所述的修复单元504通过连接组件505与安装槽孔510连接;所述的修复系统控制器506设在修复系统机械臂501上,通过线路与主控制系统3相连。
60.所述的矩阵框架503包括矩阵框架底板508和矩阵框架盖板509,矩阵框架底板508上设有数个矩阵式排布的安装槽孔510;矩阵框架盖板509上设有与矩阵框架底板508的安装槽孔510对应的通孔;矩阵框架盖板509扣合在矩阵框架底板508上。
61.所述的修复单元504包括风道装置511、主壳体512、磨抛喷涂仓513和涡轮磨抛装置514,所述的风道装置511设在主壳体512上部,磨抛喷涂仓513设在主壳体512的下部,风
道装置511、主壳体512与磨抛喷涂仓513内部贯通;风道装置511上部设有进风通道515,进风通道515上设有流量控制阀516,流量控制阀516通过线路与修复系统控制器506相连;主壳体512的上端设有支撑格栅517,支撑格栅517中间设有上轴孔,主壳体512与磨抛喷涂仓513之间设有隔离格栅518,隔离格栅518中间设有下轴孔;所述的涡轮磨抛装置514包括中心轴519、涡轮520和磨抛盘521,中心轴519上下两端分别通过支撑轴承枢接在上轴孔和下轴孔内,涡轮520设在中心轴519下部,位于主壳体512内,中心轴519下端与磨抛盘521相连,磨抛盘521位于磨抛喷涂仓513内;磨抛喷涂仓513内设有喷头522和负压吸头523,喷头522通过管路524与喷漆泵相连,负压吸头523通过管路524与负压泵相连,管路524设在主壳体512外部;所述的主壳体512的内壁设有高热反射率涂层,主壳体512内设有等间距圆周分布的加热器525,加热器525通过线路与修复系统控制器506相连;主壳体512内还设有温度传感器,温度传感器通过线路与修复系统控制器506相连;修复系统控制器506通过线路与喷漆泵和负压泵相连。
62.进一步的,所述的风道装置511包括整流仓526、集气仓527和加速导流板528,整流仓526为喇叭形结构,进风通道515设在整流仓526上部,整流仓526下端与集气仓527螺纹连接;所述的集气仓527为圆柱体结构,加速导流板528设在集气仓527的底部,加速导流板528与集气仓527螺纹连接;所述的加速导流板528中部开设有向下凸出的渐缩式导气孔529,加速导流板528上开设有数个围绕渐缩式导气孔529圆周方向等间距分布的渐缩式导气小孔530;整流仓526内设有压力传感器531,压力传感器531通过线路与修复系统控制器506相连。
63.进一步的,所述的磨抛喷涂仓513为圆台型中空结构,磨抛喷涂仓513的下边缘设有周向分布的软体刷532,磨抛盘521的磨抛面低于磨抛喷涂仓513的下边缘,高于软体刷532的下边缘;磨抛喷涂仓513内还设有喷涂传感器和浓度传感器,喷涂传感器和浓度传感器通过线路与修复系统控制器506相连;所述的喷涂传感器为气体压力传感器和流量传感器等,喷涂传感器用于控制喷涂量,浓度传感器用于检测磨抛喷涂仓513内的气体压力、气溶胶浓度等。
64.所述的连接组件505包括固定框架533和连接支架534,所述的固定框架533中间设有修复单元连接孔,修复单元504设在修复单元连接孔内;固定框架533的外圈对称设有两个燕尾型凸台535,燕尾型凸台535上设有弹簧孔,弹簧孔内设有弹簧536,自然状态下弹簧536高于弹簧孔深度;固定框架533的下部周圈均匀设有弹簧片537;所述的连接支架534包括连接支架底板538和连接支架盖板539,连接支架底板538上设有固定框架安装孔540,固定框架安装孔540的底部周圈设有支撑凸台541,固定框架安装孔540的侧边设有与固定框架533的燕尾型凸台535对应的燕尾型凹槽542;固定框架533设在固定框架安装孔540内,支撑凸台541对固定框架533起支撑作用;所述的连接支架534盖板539上设有与固定框架安装孔540相对应的通孔,连接支架534盖板539扣合在连接支架底板538上;连接支架534固定设在矩阵框架503的安装槽孔510内。
65.进一步的,所述的固定框架533为矩形框,固定框架533相对的两条边外侧对称设有两个燕尾型凸台535,固定框架533的每条边下部分别设有两个弹簧片537;所述的连接支架534为六边形;连接支架534盖板539上设有与固定框架533的燕尾型凸台535对应的燕尾槽,燕尾槽内设有与燕尾型凸台535上的弹簧536对应的弹簧限位孔543,弹簧536的顶端卡
接在弹簧限位孔543内;固定框架安装孔540为与固定框架533相应的矩形槽孔,固定框架安装孔540的支撑凸台541上设有与固定框架533底部的弹簧片537对应的弹簧片限位槽544,固定框架533底部的弹簧片537卡接在弹簧片限位槽544内。
66.进一步的,所述的修复单元连接孔的内圈由四个弧形凸台545组成,每个弧形凸台545的弧面设有内螺纹,修复单元504的外壁设有相应的外螺纹,修复单元504与修复单元连接孔通过螺纹连接。
67.本发明的工作原理:
68.首先将待检测车辆通过轮胎固定器103固定在载物台102上,定位传感器定位车辆位置信息并传输给主控制系统3,主控制系统3控制运输滑道101带动载物台102向前运动,当车身前半部分接近检测系统4时,运输滑道101减速至精确停止,使待检测车辆的前半部分进入检测系统4的工作区内,主控制系统3控制运输滑道101及载物台102在检测过程中保持静止,主控制系统3控制运输滑道101两侧的检测系统4对待测车辆前半部分车身的漆面缺陷进行检测、分类、测量,并结合定位传感器对缺陷相对位置进行定位后,将相关缺陷及缺陷位置信息传输给主控制系统3,由主控制系统3完成缺陷信息的计算、整理、工艺修复参数的生成;完成车身前半部分漆面缺陷检测后,主控制系统3控制运输滑道101继续向前运动,将刚完成漆面缺陷检测的待测车辆前半部分运输到修复系统5的工作区内,此时,待检测车辆的后半部分车身位于检测系统4的工作区内,主控制系统3控制检测系统4完成对待检测车辆后半车身的漆面缺陷检测工作,控制修复系统5对已经检测完毕的前半部分漆面缺陷进行自动修复;如此往复,形成流水线,实现车辆漆面缺陷的先检测后修复工作。
69.检测系统4依据结构光相位偏折术理论进行搭建,利用结构光相移条纹照射车身表面后发射条纹的相位变化,经过计算实现漆面缺陷的相关测量等工作。投影屏幕405的主要作用是显示由主控制系统3所生成的编码条纹并将其投射到待检测的车身表面,投影屏幕405可以选用商用的lcd显示器,也可以依据实际应用情况进行定制,投影屏幕405与检测系统搭载框架402进行连接,工业相机404的主要作用是拍摄经待测车身漆面调制并反射回来的条纹信息,工业相机404被固定在检测系统搭载框架402上,在应用过程中,投影屏幕405和工业相机404两者之间的相对位置关系必须是固定的,可以通过位于检测系统搭载框架402两侧的检测系统步进电机403调整投影屏幕405的转角进而确定两者的相对位置关系,投影屏幕405与工业相机404之间的具体位置关系由标定过程来确定,位置关系的具体数值导入到主控制系统3中,实现检测系统4的标定。检测系统机械臂401可以带动检测系统搭载框架402进行位姿的改变,以实现大面域范围内复杂几何面型背景下车身漆面缺陷的精确检测。
70.所述的运输滑道101为现有的流水线滑道设备,用于搭载载物台102运输待检测车辆;所述的轮胎固定器103为现有设备,用于将待检测汽车固定在载物台102上,所述的定位传感器也为现有设备,用于确定车辆在运载定位系统1笛卡尔坐标系下的坐标,为检测与修复功能的实现提供精确的参考位置信息;所述的主控制系统3的主要作用是对整个缺陷检测与修复过程进行控制,主要控制内容包括但不限于结构光条纹的投影编码生成、投射,工业相机404的图像捕捉,检测系统机械臂401、检测系统搭载框架402位姿改变,缺陷的定位、分类、特征、尺寸计算,缺陷工艺修复参数的确定,修复系统机械臂501、修复系统搭载框架502、修复单元504等修复工作操作的实现,运载定位系统1的运动速度、位置的控制,检测与
修复工作生产节拍的控制等。
71.漆面缺陷自动修复过程如下:将修复系统5中的每个修复单元504的流量控制阀516分别与空气压缩泵相连,修复系统控制器506控制启动修复系统机械臂501,通过修复系统机械臂501和修复系统搭载框架502带动矩阵框架503多位置、多角度转动,至修复单元504的磨抛喷涂仓513下部扣在待磨抛喷涂的车辆漆面缺陷处,使磨抛盘521与漆面接触。
72.由于每个修复单元504均通过连接组件505与矩阵框架503相连,连接组件505中固定框架533安装在连接支架534的固定框架安装孔540内,固定框架安装孔540的尺寸略大于固定框架533,固定框架533的燕尾型凸台535嵌入燕尾型凹槽542内,燕尾型凹槽542的尺寸略大于燕尾型凸台535,固定框架533上部设置的弹簧和下部设置的弹簧片537对固定框架533起到纵向支撑作用,当修复单元504受到不同角度的压力时,压缩相应角度的弹簧或弹簧片537,使固定框架533能够在固定框架安装孔540内发生小角度的升降或摆动;由于汽车覆盖件表面形状不规则,有一定的弧度或坡度,因此当修复单元504底面接触汽车漆面时会发生适应性偏转,使修复单元504底面对于汽车覆盖件表面更加贴合,提升修复单元504的面型适应柔性。修复系统机械臂501能够带动修复系统搭载框架502多自由度转动,修复系统搭载框架502上的修复系统步进电机507能够带动矩阵框架503沿转轴发生翻转,最终使矩阵框架503带动修复单元504多自由度多角度转动,同时每个修复单元504可以根据漆面形状独立进行小角度贴合调整,数个修复单元504矩阵式排布能够增加修复面积,同时对不规则汽车漆面最大限度贴合。
73.矩阵式排布的修复单元504与漆面贴合后,启动空气压缩泵,向修复单元504内输送压力气流,气流从风道装置511的进风通道515进入整流仓526,整流仓526依据流体力学的基本原理,平滑气流,使压力气流流速降低,压力提升,气流经过整流仓526整流后,在集气仓527内富集和稳压,消除气流中的一些湍流,稳压后的气流经过加速导流板528上的渐缩式导气孔529加速导出,流进主壳体512内,渐缩式导气小孔530起到辅助作用,增大气流的导出效率。整流仓526上部的压力传感器531对风道装置511内的气体压力进行监控,并实时将压力信号传输给控制系统,由控制系统控制流量控制阀516的开度进而控制进入装置内的气体流量。气流经过风道装置511消湍、稳流、增速后进入主壳体512内,主壳体512内的加热器525通电升温对气流进行加热,加热后的气流沿着加热器525之间形成的导流通道向下流通,高热反射率涂层用以降低热辐射的扩散,保持腔室内的温度,提升气体加热效率;温度传感器实时监测加热器525温度和气流温度,并将数据传输给控制系统,进而由控制系统调节施加在加热器525中的电功率,达到气体温度的有效控制。加热后的气流继续向下流通,流经涡轮磨抛装置514时,高温、高压气流驱动涡轮磨抛装置514的涡轮520转动,涡轮520带动中心轴519在支撑轴承内旋转,进而带动中心轴519下端的磨抛盘521旋转,实现对漆面的磨抛操作;高温气流同时具有提升涡轮520转速和软化漆面的作用。
74.在进行磨抛作业时负压泵启动,磨抛喷涂仓513内的负压吸头523将流进磨抛喷涂仓513内的气流以及磨抛产生的碎屑粉尘一并吸出,以保证磨抛喷涂仓513的环境清洁度,避免废弃物附着在作业面上造成漆面的损伤,提升打磨喷涂效果。磨抛后启动喷漆泵,对磨抛后的漆面进行喷涂修复,负压吸头523同时将喷涂作业时所产生的粉尘、气溶胶等废弃物进行清吸,直到完成修复。
再多了解一些
本文用于企业家、创业者技术爱好者查询,结果仅供参考。