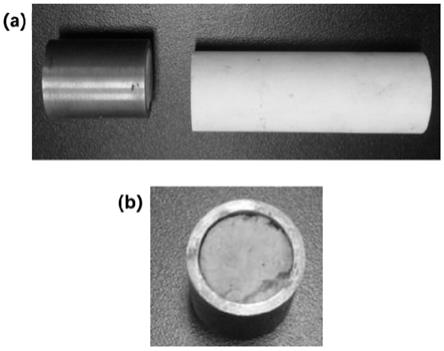
1.本发明涉及一种暂堵材料,尤其涉及一种压裂酸化用暂堵材料及其制备方法。
背景技术:
2.在对长井段油气储层进行压裂酸化时,笼统改造效果不够理想,机械工具分层分段改造存在风险大、费用高等问题。面对这种现状,一般采用暂堵材料。暂堵材料是一种能够能暂时降低地层渗透性或暂时封堵高渗透油气层的物质,与传统压裂酸化工作液混合后注人井内,在压差的作用下能够迅速形成致密的油气层暂堵带,经过一定时间后可自行解堵。
3.堵剂材料根据其用途不同满足两大类技术需求:第一类是承压强度高,承压能力和幅度时间可调等要求;第二类是在压裂酸化工作液中具有溶解性,有利于压后生产作业。第一类技术需求要求提高暂堵材料的分子量,但是分子量太大易造成难溶解,粘度大,难返排;第二类技术需求要求降低暂堵材料的分子量,但是降低分子量易造成暂堵材料的强度降低。可见,这两大类技术需求是一对矛盾体。
4.在《油气田环境保护》2009年第19卷第2期公开的《水溶性暂堵剂hd的研制与评价》论文提到,该暂堵剂采用无机盐类和有机酸类(有机酸与有机酸盐的混合物,软化点较高,溶解度随温度变化较小)及其他添加剂(包括水溶性高分子聚合物聚丙烯酰胺,表面活性剂月桂酸单酯,交联剂和固体颗粒)来研制水溶性暂堵剂。该暂堵剂水溶性较好,可用于高含水油井。但是该暂堵剂不能溶于酸,且与酸不反应,对于碳酸盐岩油气藏,很难达到酸压后溶解的目的,反而容易造成储层二次伤害。
5.200410009408.1公开一种水溶性压裂酸化用暂堵材料,该暂堵剂由骨胶、磺化沥青和胍胶三种成分组成;cn91101010.6公开了一种水溶性暂堵材料,由骨胶,田菁粉(或羟甲基淀粉)、磺化沥青组成。这两种暂堵材料均存在对碳酸盐岩油气藏酸压后不能溶解进而不能自动解堵的问题。201110330609.1提供了一种酸压暂堵材料,由树脂,地蜡,碳酸钙,碳酸镁,氯化钾,氯化铵组合而成,适用地层温度可达100℃,封堵率在96%,酸溶率在98%以上,封堵强度>50mpa,可以满足碳酸盐岩储层长井段酸压暂堵需求。cn 103806889a公开了一种变粘暂堵液,由1-5%的水溶性聚乙烯醇、1-3%的二甲基双丙烯酰胺、0.005-0.02%的n’n-亚甲基双丙烯酰胺,0.005-0.2%的偶氮类引发剂、0.1-0.5%的有机硼交联剂、0.5-5%的过硫酸铵胶囊和余量水组成,但是未公布适用的地层温度、可承受的压力等适用条件。
6.近年来,随着勘探开发向深层领域进军,地层温度越来越高,地层压力越来越高,适用于150℃以上地层温度和承压60mpa以上的压裂酸化用暂堵材料还未见报道。
技术实现要素:
7.为了解决上述问题,本发明的目的在于提供一种压裂酸化用暂堵材料及其制备方法,该制备方法制备得到的压裂酸化用暂堵材料的耐受温度能够达到160℃以上,暂堵强度
达到60mpa以上。
8.为了达到上述目的,本发明提供了一种压裂酸化用暂堵材料的制备方法,其包括以下步骤:
9.(1)在n2和/或惰性气体气氛下,使1,1'-((3-氟丙烷-1,1-二基)双(氧基))双(丁-3-烯-2-醇),三氯甲烷和苯亚甲基-1,3-双(2,4,6-三甲苯基)-2-(咪唑啉卡宾)(三环己基磷)二氯化钌进行反应,得到中间产物;
10.(2)将中间产物与丙酮、二水合锇酸钾和n-甲基吗啉氧化物在去离子水和有机溶剂中进行反应,得到混合溶液;
11.(3)向步骤(2)的混合溶液中加入饱和亚硫酸钠溶液进行反应,后处理后得到所述压裂酸化用暂堵材料。
12.在上述制备方法中,优选地,所述1,1'-((3-氟丙烷-1,1-二基)双(氧基))双(丁-3-烯-2-醇)的体积与苯亚甲基-1,3-双(2,4,6-三甲苯基)-2-(咪唑啉卡宾)(三环己基磷)二氯化钌的摩尔量的比为(150-210)ml:1mol。
13.在上述制备方法中,优选地,所述1,1'-((3-氟丙烷-1,1-二基)双(氧基))双(丁-3-烯-2-醇)的体积与三氯甲烷的摩尔量的比为(10-15)ml:1mol。
14.在上述制备方法中,优选地,所述中间产物与二水合锇酸钾的质量比为(5:1)-(15:1)。
15.在上述制备方法中,优选地,所述中间产物与n-甲基吗啉氧化物的质量比为(1:2)-(2:1)。
16.在上述制备方法中,优选地,所述中间产物与丙酮的质量比为(1:15)-(1:30)。
17.在上述制备方法中,优选地,所述中间产物与去离子水的质量比为(1:10)-(5:10)。
18.在上述制备方法中,优选地,所述有机溶剂包括二氯甲烷,更优选地,所述丙酮与二氯甲烷的体积比为(3:1)-(1:1)。
19.在上述制备方法中,优选地,所述丙酮与饱和亚硫酸钠溶液的体积比为(1:2)-(2:1)。
20.在上述制备方法中,优选地,步骤(1)中,所述反应的温度为30-80℃,时间为2-8h。
21.根据本发明的实施方案,步骤(1)所使用的反应容器的体积与三氯甲烷的体积比可以控制为(3:1)-(50:1),步骤(1)的反应容器可以选用不锈钢罐式反应器。
22.根据本发明的实施方案,步骤(1)还可以包括将1,1'-((3-氟丙烷-1,1-二基)双(氧基))双(丁-3-烯-2-醇)、三氯甲烷与苯亚甲基-1,3-双(2,4,6-三甲苯基)-2-(咪唑啉卡宾)(三环己基磷)二氯化钌的反应产物倒入正己烷、得到沉淀、将沉淀分离,得到中间产物的操作。在一些具体实施方案中,对沉淀分离的过程可以包括对沉淀进行离心、过滤、干燥的操作,例如在倒入正己烷后进行离心、过滤、干燥的操作;干燥的温度优选为50-200℃(更优选为50-150℃),干燥的时间优选为0.5-2h。
23.在上述制备方法中,优选地,步骤(1)中,所述反应容器和正己烷的体积比为(2:1)-(3:1)。
24.在上述制备方法中,优选地,步骤(2)中,所述反应的时间为2-10h。
25.根据本发明的具体实施方案,步骤(2)可以采用边搅拌边反应的方式进行,搅拌的
速度可以控制为50-200rpm(优选为50-150rpm)。
26.根据本发明的实施方案,步骤(2)的反应容器与丙酮的体积比可以控制为(10:1)-(3:1),步骤(2)的反应容器可以选用圆底烧瓶。
27.在上述制备方法中,优选地,步骤(3)中,所述反应的时间为1-3h。
28.根据本发明的具体实施方案,步骤(3)中,可以采用边搅拌边反应的方式,搅拌的速度可以控制为50-200rpm(优选为50-150rpm)。
29.根据本发明的具体实施方案,步骤(3)中,所述后处理包括:将步骤(3)反应后的体系进行有机相和水相的分离,然后将有机相干燥,选择蒸发三氯甲烷后得到粗品,再将粗品沉淀,得到压裂酸化用暂堵材料,该压裂酸化用暂堵材料通常为白色。
30.在上述制备方法中,优选地,干燥有机相采用无水硫酸钠,更优选地,无水硫酸钠与去离子水的质量比为(4:1)-(2:5)。
31.在上述制备方法中,优选地,在进行后处理时,沉淀粗品采用加入乙醚的方式,更优选地,乙醚与去离子水的体积比为(2:1)-(1:2)。
32.根据本发明的具体实施方案,制备得到的压裂酸化用暂堵材料可以经过粉碎和过筛的得到5-200目颗粒,也可以按照业内常规方法压塑成特定尺寸的球状材料。
33.根据本发明的具体实施方案,压裂酸化用暂堵材料的制备方法可以包括以下步骤:
34.(1)在容积为1-5l的不锈钢管式反应器的空气全部置换为n2,加入15-80g的1,1'-((3-氟丙烷-1,1-二基)双(氧基))双(丁-3-烯-2-醇)、100-400ml三氯甲烷和65-300mg苯亚甲基-1,3-双(2,4,6-三甲苯基)-2-(咪唑啉卡宾)(三环己基磷)二氯化钌,加热至30-80℃反应2-8h后,自然冷却至室温;然后将反应器中的反应产物倒入0.5-2l的正己烷中得到沉淀,再通过对沉淀离心、过滤、50-200℃干燥0.5-2h,得到15-62g中间产物;
35.(2)将15-62g中间产物加入2-10l的圆底烧瓶,再加入0.5-2l丙酮、0.3-1.2l二氯甲烷、1.2-5g二水合锇酸钾、100-450ml去离子水和15-70g n-甲基吗啉氧化物,以50-200rpm速度搅拌2-10h,得到混合溶液;
36.(3)向混合溶液中加入300-1200ml的饱和亚硫酸钠溶液,以50-200rpm速度搅拌反应1-3h,将反应后的体系进行有机相与水相的分离,将有机相用50-200g无水硫酸钠干燥,选择蒸发氯仿得到粗品,再将粗品加入100-500ml的乙醚中沉淀,得到10-40g压裂酸化用暂堵材料。
37.本发明还提供了一种压裂酸化用暂堵材料,其是由上述制备方法制备得到的。
38.本发明提供的有益效果包括:
39.本发明提供的压裂酸化用暂堵材料的耐受温度>160℃,暂堵强度>60mpa,暂堵时间>10h,5%盐酸溶解率>99%,5%盐酸溶解所需时间>32h。
附图说明
40.图1为暂堵实验所用的环形充填容器的照片。a图为环形充填容器照片,b图为进行暂堵实验时暂堵剂颗粒在该容器中的充填方式。
41.图2为暂堵实验用流动实验装置的照片。
具体实施方式
42.为了对本发明的技术特征、目的和有益效果有更加清楚的理解,现对本发明的技术方案进行以下详细说明,但不能理解为对本发明的可实施范围的限定。
43.以下实施例中所用试剂均从sigma-aldrich公司购得,所用的1,1'-((3-氟丙烷-1,1-二基)双(氧基))双(丁-3-烯-2-醇)的相对分子量为234.12、密度为1.12g/cm3,所用的苯亚甲基-1,3-双(2,4,6-三甲苯基)-2-(咪唑啉卡宾)(三环己基磷)二氯化钌的相对分子量为822.96。
44.实施例1
45.本实施例提供了一种压裂酸化用暂堵材料的制备方法,包括以下步骤:
46.(1)在容积为2.5l的不锈钢管式反应器的空气全部置换为n2,加入35.1g的1,1'-((3-氟丙烷-1,1-二基)双(氧基))双(丁-3-烯-2-醇)、200ml三氯甲烷和126.8mg苯亚甲基-1,3-双(2,4,6-三甲苯基)-2-(咪唑啉卡宾)(三环己基磷)二氯化钌,加热至60℃反应4h后,自然冷却至室温;然后将反应器中的反应产物倒入1l的正己烷中沉淀,再通过离心、过滤、100℃干燥1h,得到30.2g中间产物;
47.(2)将30.2g中间产物加入5l的圆底烧瓶,再加入1l丙酮、0.6l二氯甲烷、2.4g二水合锇酸钾、200ml去离子水和33.5gn-甲基吗啉氧化物,以100rpm速度搅拌5h,得到混合溶液;
48.(3)向混合溶液中加入600ml的饱和亚硫酸钠溶液,以100rpm速度搅拌反应2h,将反应后的体系进行有机相与水相的分离,将有机相用100g无水硫酸钠干燥,选择蒸发氯仿得到粗品,再将粗品加入200ml的乙醚中沉淀,得到20.1g压裂酸化用暂堵材料。
49.实施例2
50.本实施例提供了一种压裂酸化用暂堵材料的制备方法,包括以下步骤:
51.(1)在容积为5l的不锈钢管式反应器的空气全部置换为n2,加入80g的1,1'-((3-氟丙烷-1,1-二基)双(氧基))双(丁-3-烯-2-醇)、400ml三氯甲烷和300mg苯亚甲基-1,3-双(2,4,6-三甲苯基)-2-(咪唑啉卡宾)(三环己基磷)二氯化钌,加热至60℃反应5h后,自然冷却至室温;然后将反应器中的反应产物倒入2l的正己烷中沉淀,再通过离心、过滤、110℃干燥2h,得到62g中间产物;
52.(2)将62g中间产物加入10l的圆底烧瓶,再加入2l丙酮、1l二氯甲烷、5g二水合锇酸钾、450ml去离子水和70g n-甲基吗啉氧化物,以100rpm速度搅拌6h,得到混合溶液;
53.(3)向混合溶液中加入1l的饱和亚硫酸钠溶液,以100rpm速度搅拌反应3h,将反应后的体系进行有机相与水相的分离,将有机相用200g无水硫酸钠干燥,选择蒸发氯仿得到粗品,再将粗品加入500ml的乙醚中沉淀,得到45g压裂酸化用暂堵材料。
54.实施例3
55.本实施例提供了一种压裂酸化用暂堵材料的制备方法,包括以下步骤:
56.(1)在容积为1l的不锈钢管式反应器的空气全部置换为n2,加入15g的1,1'-((3-氟丙烷-1,1-二基)双(氧基))双(丁-3-烯-2-醇)、100ml三氯甲烷和70mg苯亚甲基-1,3-双(2,4,6-三甲苯基)-2-(咪唑啉卡宾)(三环己基磷)二氯化钌,加热至80℃反应4h后,自然冷却至室温;然后将反应器中的反应产物倒入0.5l的正己烷中沉淀,再通过离心、过滤、100℃干燥1h,得到16g中间产物;
57.(2)将16g中间产物加入2.5l的圆底烧瓶,再加入0.6l丙酮、0.3l二氯甲烷、1.5g二水合锇酸钾、100ml去离子水和20g n-甲基吗啉氧化物,以100rpm速度搅拌4h,得到混合溶液;
58.(3)向混合溶液中加入600ml的饱和亚硫酸钠溶液,以100rpm速度搅拌反应2h,将反应后的体系进行有机相与水相的分离,将有机相用60g无水硫酸钠干燥,选择蒸发氯仿得到粗品,再将粗品加入100ml的乙醚中沉淀,得到11g压裂酸化用暂堵材料。
59.测试例1
60.测试实施例1-3制备的压裂酸化用暂堵材料的耐受温度、暂堵强度、暂堵时间、5%盐酸溶解率、5%盐酸溶解所需时间,并以两种现有商业暂堵材料(上海利民公司的中温型产品lm12和高温型产品lm15)作为对比例,测试结果总结在表1中。
61.耐受温度、暂堵强度、暂堵时间测试采用自制暂堵材料评价装置,其为内径为一英寸环形填充容器(如图1中的a图和b图所示)。暂堵实验在图2的暂堵实验用流动实验装置中进行,具体过程为:
62.按照图1中的b图的方式,将测试样品填充于该环形容器中,流动后方连接高渗透人造岩心,再放入暂堵实验用流动实验装置中进行测试。将岩心夹持器的温度升高到实验温度,并开泵注入5%的盐酸。暂堵材料的颗粒暂堵剂在实验温度下发生玻璃化转化形成暂堵,注入压力会急剧上升。将注入压力稳定在实验压力,保持实验温度,观察并记录耐受温度、暂堵强度和暂堵时间。
63.将10g暂堵剂和200ml残酸置于高压釜中放于加热至实验温度的烘箱中降解,一段时间后过滤、干燥、称得剩余暂堵剂质量wd。记录暂堵材料在5%盐酸溶解率和溶解所需时间,并通过以下公式计算降解率:
64.降解率=(10-wd)/10
×
100%。
65.表1
[0066][0067]
从表1中的结果可以看出,本发明提供的压裂酸化用暂堵材料的耐受温度>160℃,暂堵强度>60mpa,暂堵时间>10h,5%盐酸溶解率>99%,5%盐酸溶解所需时间>32h,各项暂堵能力明显高于现有商业暂堵材料。
再多了解一些
本文用于企业家、创业者技术爱好者查询,结果仅供参考。