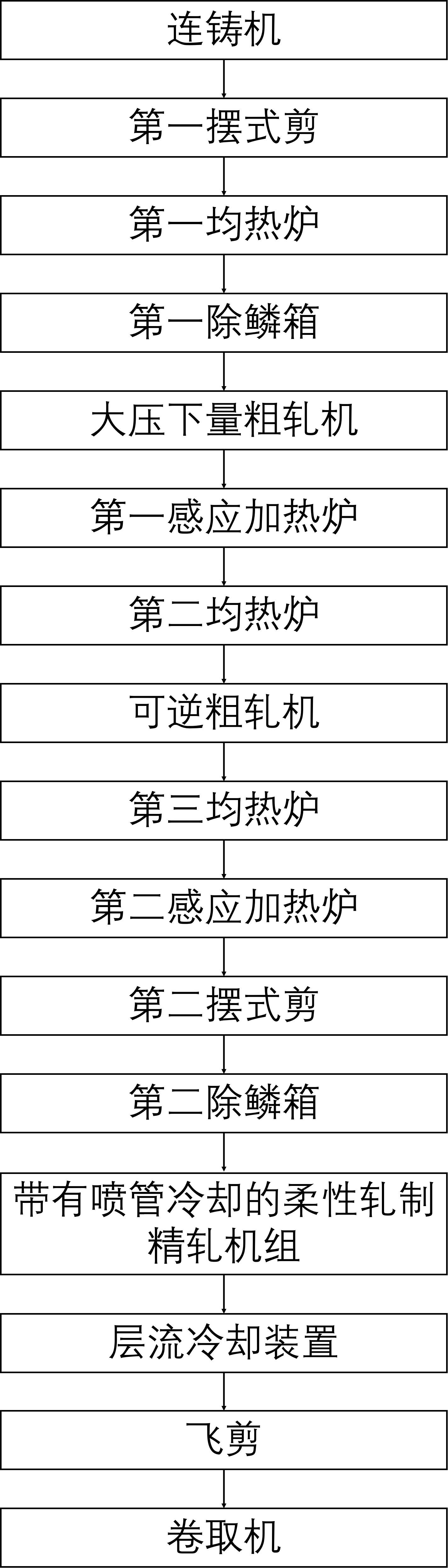
1.本发明涉及钢铁冶金领域,特别涉及一种板带宏微观形性一体化控制柔性轧制方法。
背景技术:
2.薄板坯连铸连轧技术将传统钢铁制造流程中的连铸、加热、轧制、冷却等一系列独立工序融为一体的钢铁近终形生产流程。薄板坯连铸连轧技术具有投资少,占地少,能耗低,成材率高,运行成本低,可生产传统热轧工艺无法生产的薄材、极薄材,实现部分品种规格的“以热代冷”显著优势,近终形工艺流程符合当今世界对环保、清洁生产和节能的要求,是未来钢铁冶金发展趋势。柔性轧制技术是在薄板坯连铸连轧技术精轧工序基础上增设一架备用轧机,基于动态变规程理论实现零停机时间连铸连轧生产工业应用。
3.传统柔性轧制技术粗轧工序采用粗轧机三机架连续布置形式,高度追求近终形生产,粗轧大压下过程心表温度不均匀现象具有遗传效应,任一机架出现表面质量问题难以通过下一机架进行消除,无法为后续工序提供合格来料,导致板带成品宏观尺寸与微观组织性能无法满足交货要求。三机架连轧每一道次温度逐渐降低导致粗轧末机架轧机负荷增加,粗轧各机架轧辊,尤其是第三机架轧辊磨损严重,轧机振动剧烈,影响轧制稳定性与中间坯板形质量。柔性轧制技术使得轧制时间与轧制里程大幅度增加,轧制过程中高温板带的热量和形变产生的热量使得精轧机组轧辊受热温度升高,与空气介质换热程度不同导致轧辊温度沿辊身长度分布不均,呈现中部温度高、两端边部低状态,中部与边部温差导致轧辊产生热凸度,严重影响薄规格产品板形质量。
技术实现要素:
4.为了解决上述技术问题,本发明提供了一种板带宏微观形性一体化控制柔性轧制方法。
5.本发明的技术方案如下:本发明提供一种板带宏微观形性一体化控制柔性轧制方法,板带轧制过程中装备布局方式如下:连铸机
→
第一摆式剪
→
第一均热炉
→
第一除鳞箱
→
大压下量粗轧机
→
第一感应加热炉
→
第二均热炉
→
可逆粗轧机
→
第三均热炉
→
第二感应加热炉
→
第二摆式剪
→
第二除鳞箱
→
带有喷管冷却的柔性轧制精轧机组
→
层流冷却装置
→
飞剪
→
卷取机。
6.s1、利用连铸机进行板带铸造,连铸机采取弧形结晶器,利用液芯压下及动态轻压下技术提高拉带速度,保证连铸通钢量,改善铸带中心处偏析与疏松缺陷;s2、利用第一摆式剪对板带进行剪切,实现生产线具备板带不同长度尺寸灵活分割能力,实现一机多任务连续排程不停机生产,减少非计划过渡材损耗;s3、利用双蓄热式均热炉对板带进行加热,降低板带长度与宽度温差,充分利用在炉时间实现板带奥氏体均匀化,确保板带内部晶粒度均匀一致性,提高板带进入粗轧入口
温度,降低板带屈服强度,减少第一粗轧机大压下能耗;s4、粗轧前利用第一除鳞箱对板带喷射高压水,在板带进行粗轧前清除板带表面氧化铁皮,提高板带进入粗轧机表面质量;s5、利用大压下量粗轧机对板带进行粗轧:大压下量粗轧机采用单机架布置,大压下量粗轧机为四辊轧机;s6、利用第一感应加热炉对板带进行加热补温:感应加热采用纵磁加热方式,进一步保证板带横向温度分布均匀程度,利用集肤效应消除大压下量粗轧机大压下量导致板带厚度方向温度不均匀程度,补充板带温度,减少可逆粗轧机大压下能耗;s7、利用第二均热炉对板带进行保温加热:对来自大压下量粗轧机轧制完成的板带进行保温,对经过可逆粗轧机往复轧制的板带进行补热,减少可逆粗轧机大压下能耗,确保板带整体范围心表温度均匀,消除温度梯度,依靠可逆粗轧机agc系统可以针对性对下一道次轧制参数进行有效调整,消除轧制过程中镰刀弯、跑偏、浪形缺陷,提高板形控制精度和轧制设备稳定性;s8、利用可逆粗轧机对板带进行粗轧:可逆粗轧机为四辊轧机并采用单机架布置,通过agc系统与主传动系统自动调节实现往复可逆轧制,并控制板形;无头轧制生产过程切换成单向轧制模式;s9、利用第三均热炉补偿板带经可逆粗轧机轧制损失的热量,减少可逆粗轧机往复轧制能耗,确保板带整体范围心表温度均匀,消除温度梯度;无头轧制生产过程起到保温作用;s10、利用第二感应加热炉对板带进行加热补温:感应加热采先横后纵磁结合加热方式,确保板带横向纵向温度分布,并利用其加热效率高优点,补充精轧入口板带温度,保证板带温度进入精轧机组为设定温度;s11、当多规格板带生产规程切换时,利用第二摆式剪对粗轧完成的板带头尾进行剪切;s12、精轧前利用第二除鳞箱对板带喷射高压水,在板带进行精轧前清除板带表面氧化铁皮,提高板带进入带有喷管冷却的柔性轧制精轧机组表面质量;s13、利用带有喷管冷却的柔性轧制精轧机组对板带进行精轧:柔性轧制精轧机组包括五台工作精轧机和一台备用精轧机,各轧机间布置喷管冷却装置实现生产线不停机生产;喷管冷却装置动态定量向各轧机轧辊喷淋冷却水,消除连续轧制生产轧辊辊身长度温度分布不均现象,消除轧辊热凸度,提高轧制板形质量;s14、利用层流冷却装置对板带进行冷却降温;s15、利用飞剪在无头轧制生产模式下,对板带进行剪切分卷;s16、通过卷取机对板带进行卷取。
7.板带经过连铸处理后板带温度为1450℃
±
20℃,经过双蓄热式均热炉后起到目标温度保温的作用,并且在炉内温度实现温度一致性、均匀性控制,温度为1350℃,经过大压下量粗轧机大压下粗轧后,温度降为1200
±
30℃,经过第一感应加热炉后温度升至1250
±
20℃,经过第二均热炉1250℃保温后,心表温差缩减为10℃,经过可逆粗轧机前利用机架侧导板进行板坯对中,粗轧后进入第三均热炉温度补偿至1200
±
20℃,利用agc系统控制操作
侧和传动侧压下辊缝与轧制力实现镰刀弯、翘扣头缺陷消除,根据产品规格需要制订往复轧制次数,粗轧完成板坯经过横纵磁感应加热后温度升至1200
±
15℃,经过柔性轧制精轧机组精轧后温度降为950
±
20℃,经过层流冷却装置后,温度降为630
±
20℃,随后进行卷取。
8.优选地,板带在大压下量粗轧机粗轧、可逆粗轧机粗轧和带有喷管冷却的柔性轧制精轧机组精轧阶段,微观组织为奥氏体,经过层流冷却,微观组织转变为铁素体和珠光体。
9.优选地,粗轧板带浪形最大高度小于5mm,翘扣头最大高度小于15mm,中心线偏移量控制在100mm以内,带有喷管冷却的柔性轧制精轧机组轧辊热凸度控制在0.05mm以内,精轧板带厚度为0.6~8mm。
10.优选地,所述喷管冷却装置为中间密集、两侧分散布置方式,喷管最大水压为40mpa。
11.本发明与现有技术相比具有如下优点:(1)本发明通过改进粗轧机布置形式,采用单机架大压下粗轧机、可逆粗轧机布置形式,针对大批量定制生产需求时,可逆粗轧机采用单向轧制模式,实现无头轧制连续生产,依靠感应加热升高板坯温度,降低轧机负荷,针对高质量钢种定制化要求,可逆粗轧机采用可逆往复轧制模式,依靠均热炉和agc系统与主传动系统,消除每道次轧制出现的板形问题。
12.(2)本发明通过增设大压下粗轧机后纵向感应加热装置,利用集肤效应消除大压下后板带厚度方向温度梯度分布,并利用均热炉对板带宽度厚度方向均匀补热,确保板带进入下一工序前温度均匀一致。
13.(3)本发明在柔性轧制精轧机组内增设喷管冷却装置,喷管冷却装置为中间密集、两侧分散布置方式,减小轧辊辊身长度方向温差,消除柔性轧制轧制时间与轧制里程大幅度增加导致精轧机组轧辊受热温度升高,与空气介质换热程度不同导致轧辊出现热凸度现象,确保长度方向轧制均匀性,提高板带表面质量,减小成品长度方向表面质量离散度。
14.(4)本发明配备摆式剪、双蓄热式均热炉,结合柔性轧制机组实现生产线具备板带不同长度尺寸灵活分割能力,实现一机多任务连续排程不停机生产,减少非计划过渡材损耗,提高能源利用率。
15.(5)本发明提供了一种板带宏微观形性一体化控制柔性轧制方法,通过对传统柔性轧制生产工艺路径与装备布局方式流程再造,充分发挥双蓄热式均热炉、可逆粗轧机组、感应加热装置、喷管冷却装置的物理冶金特征和装备潜能,确保柔性轧制生产过程轧辊中边部温度、板带宽厚方向温度均匀一致,实现板带宏观板形微观组织精细化控制,确保柔性轧制不停机高效生产基础上,提升成品综合性能,解决传统柔性轧制高度牺牲产品质量追求近终形制造带来的问题,充分利用最新工艺装备发挥各工序特性,实现全流程板带形性一体化控制,突破传统柔性轧制生产品种制约,实现高性能品种钢稳定生产,满足钢铁产业生产高质量高性能钢材迫切需要,该工艺方法在钢铁产业流程再造、节能减排、品规拓展、自主创新等方面具有重要意义。
附图说明
16.图1是本发明一种板带宏微观形性一体化控制柔性轧制方法工艺流程图。
17.图2是传统柔性轧制方法装备布置示意图。
18.图3是本发明一种板带宏微观形性一体化控制柔性轧制方法装备布置示意图。
19.图4是本发明柔性轧制精轧机组喷管冷却装置主视图。
20.图5是本发明柔性轧制精轧机组喷管冷却装置侧视图。
21.附图标号:1-连铸机;2-第一摆式剪;3-第一均热炉;4-第一除鳞箱;5-大压下量粗轧机;6-第一感应加热炉;7-第二均热炉;8-可逆粗轧机;9-第三均热炉;10-第二感应加热炉;11-第二摆式剪;12-第二除鳞箱;13-带有喷管冷却的柔性轧制精轧机组;14-层流冷却装置;15-飞剪;16-卷取机;17-粗轧机组;18-摆式剪;19-加热炉;20-精轧机组;21-轧辊;22-喷管冷却装置;23-板带。
具体实施方式
22.以下,参照附图对本发明的实施方式进行说明。
23.参考图1、图3、图4和图5,板带23经过连铸处理后板带温度为1450℃
±
20℃,经过双蓄热式均热炉后起到目标温度保温的作用,并且在炉内温度实现温度一致性、均匀性控制,温度为1350℃,经过大压下量粗轧机5大压下粗轧后,温度降为1200
±
30℃,经过第一感应加热炉6后温度升至1250
±
20℃,经过第二均热炉7进行1250℃保温后,心表温差缩减为10℃,经过可逆粗轧机8前利用机架侧导板进行板坯对中,粗轧后进入第三均热炉9温度补偿至1200
±
20℃,利用agc系统控制操作侧和传动侧压下辊缝与轧制力实现镰刀弯、翘扣头缺陷消除,根据产品规格需要制订往复轧制次数,粗轧完成板坯经过横纵磁感应加热后温度升至1200
±
15℃,经过柔性轧制精轧机组精轧后温度降为950
±
20℃,经过层流冷却装置14后,温度降为630
±
20℃,随后进行卷取。
24.参考图2,传统柔性轧制方法装备布局方式如下:连铸机1
→
粗轧机组17
→
摆式剪18
→
加热炉19
→
精轧机组20
→
层流冷却装置14
→
飞剪15
→
卷取机16。
25.实施例1参考图1、图3、图4和图5,本实施例在柔性轧制生产过程中,经连铸机1处理后板带温度为1450℃,经过双蓄热式均热炉,温度为1350℃,炉内采用上下双烧嘴布置形式,能够有效减少板带长度温差和断面温差,解决板带边部温度缺陷,提高成品板卷表面质量。第一摆式剪2可以在需要切换板带生产规程时,剪切并剔除连铸带头尾,实现进入柔性轧机生产超薄规格板带与粗轧机生产中厚板生产模式进行切换,实现一条产线同时生产不同规程板带,充分挖掘产线装备潜能,优化生产排程,提高生产效率,减少停机切换能源损耗。
26.经过大压下量粗轧机5轧制后,温度降为1150℃,第一感应加热炉6将板带温度升至1230℃,采用纵磁模式感应加热布置对板带23进行均匀加热,利用集肤效应消除粗轧大压下量产生厚向温度不均影响,第二均热炉温度保持在1250℃,经过可逆粗轧机8前利用机架侧导板进行板坯对中,粗轧后进入第三均热炉温度补偿至1200℃,利用agc系统控制操作侧和传动侧两侧辊缝与轧制力,实现往复轧制过板带浪形最大高度为5mm,翘扣头最大高度为10mm,中心线偏移量控制为80mm,粗轧完成板坯经过横纵磁感应加热后温度升至1200℃,实现进入带有喷管冷却的柔性轧制精轧机组13前板带宽厚方向始终保持温度均匀一致性;第二摆式剪11用于剪切半无头轧制生产过程中板带头尾。
27.经过带有喷管冷却的柔性轧制精轧机组13精轧后温度降为950℃,带有喷管冷却
的柔性轧制精轧机组13精轧过程轧辊表面温度经分段冷却后保持在60℃,轧辊热凸度为0.05mm,经过层流冷却装置14后,温度降为630℃,随后进行卷取;经过层流冷却后,微观组织转变为铁素体和珠光体,通过飞剪剪切成预设尺寸,最终通过卷取机16对成品进行卷取。
28.经过上述工艺过程,确保柔性轧制过程中轧辊中边部温度、板带宽厚方向温度均匀一致,实现板带宏观板形微观组织精细化控制,减小产品宏微观表面完整性离散程度,提高产品成材率,并为企业多任务不停机生产同时,多规格生产排程稳定切换提供基础。
29.实施例2参考图1、图3、图4和图5,本实施例在柔性轧制生产过程中,经过大压下量粗轧机5轧制后,温度降为1180℃,第一感应加热炉6将板带温度升至1240℃,采用纵磁模式感应加热布置对板带23进行均匀加热,利用集肤效应消除粗轧大压下量产生厚向温度不均影响,第二均热炉温度保持在1250℃,经过可逆粗轧机8前利用机架侧导板进行板坯对中,粗轧后进入第三均热炉温度补偿至1200℃,利用agc系统控制操作侧和传动侧两侧辊缝与轧制力,浪形最大高度小于3mm,翘扣头最大高度小于15mm,中心线偏移量控制在60mm以内,粗轧完成板坯经过横纵磁感应加热后温度升至1200℃,实现进入精轧机组前板带宽厚方向始终保持温度均匀一致性;第二摆式剪11用于剪切半无头轧制生产过程中板带头尾。
30.经过带有喷管冷却的柔性轧制精轧机组13精轧后温度降为950℃,带有喷管冷却的柔性轧制精轧机组13精轧过程轧辊21表面温度经分段冷却后保持在75℃,轧辊热凸度为0.03mm,经过层流冷装置后,温度降为630℃,随后进行卷取;层流冷却后,微观组织转变为铁素体和珠光体,通过飞剪15剪切成预设尺寸,最终通过卷取机16对成品进行卷取。
31.经过上述工艺过程,确保柔性轧制过程中轧辊中边部温度、板带宽厚方向温度均匀一致,实现板带宏观板形微观组织精细化控制,减小产品宏微观表面完整性离散程度,提高产品成材率,并为企业多任务不停机生产同时,多规格生产排程稳定切换提供基础。
32.实施例3参考图1、图3、图4和图5,本实施例在柔性轧制生产过程中,经过大压下量粗轧机5轧制后,温度降为1130℃,第一感应加热炉6将板带温度升至1225℃,采用纵磁模式感应加热布置对板带23进行均匀加热,利用集肤效应消除粗轧大压下量产生厚向温度不均影响,第二均热炉7温度保持在1250℃,经过可逆粗轧机8前利用机架侧导板进行板坯对中,粗轧后进入第三均热炉9温度补偿至1200℃,利用agc系统控制操作侧和传动侧两侧辊缝与轧制力,浪形最大高度小于5mm,翘扣头最大高度小于8mm,中心线偏移量控制在90mm以内,粗轧完成板坯经过横纵磁感应加热后温度升至1200℃,实现进入精轧机组前板带宽厚方向始终保持温度均匀一致性;第二摆式剪11用于剪切半无头轧制生产过程中板带头尾。
33.经过带有喷管冷却的柔性轧制精轧机组13精轧后温度降为950℃,带有喷管冷却的柔性轧制精轧机组13精轧过程轧辊21表面温度经分段冷却后保持在65℃,轧辊热凸度为0.04mm,经过层流冷却装置14后,温度降为630℃,随后进行卷取;经过层流冷却后,微观组织转变为铁素体和珠光体,通过飞剪15剪切成预设尺寸,最终通过卷取机16对成品进行卷取。
34.经过上述工艺过程,确保柔性轧制过程中轧辊中边部温度、板带宽厚方向温度均匀一致,实现板带宏观板形微观组织精细化控制,减小产品宏微观表面完整性离散程度,提高产品成材率,并为企业多任务不停机生产同时,多规格生产排程稳定切换提供基础。
35.以上所述的实施例仅是对本发明的优选实施方式进行描述,并非对本发明的范围进行限定,在不脱离本发明设计精神的前提下,本领域普通技术人员对本发明的技术方案
做出的各种变形和改进,均应落入本发明权利要求书确定的保护范围内。
再多了解一些
本文用于创业者技术爱好者查询,仅供学习研究,如用于商业用途,请联系技术所有人。