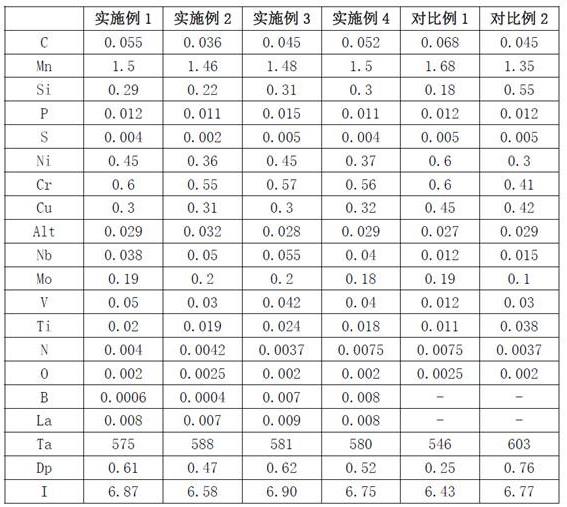
一种耐大热输入焊接的nb-v-ti-b系q500qenhw耐候桥梁钢
技术领域
1.本发明属于耐候钢材技术领域,特别涉及一种耐大热输入焊接的nb-v-ti-b系q500qenhw耐候桥梁钢,其不仅具有优异的强韧性匹配,而且在大热输入焊接条件下焊接热影响区还具有优良的-40℃低温韧性。
背景技术:
2.目前,我国大力推进川藏铁路、滇藏铁路等国家重点铁路工程建设,沿线多穿越高山峡谷,拟建造千米级超大跨度免涂装耐候钢桥梁近百座。桥位多处高寒缺氧、冻土滑坡、地震频发等严苛的地质条件,生态环境脆弱,但气候条件较为适宜,适宜建造耐候桥梁钢。另外桥梁制造工期紧,且焊接制造多采用高强钢、厚规格(最大厚度可达80mm)钢板。为此材料须满足高负荷、防脆断、高效制造和绿色环保的设计要求。
3.现有成熟的345-420mpa级耐候桥梁钢强度偏度,无法满足超大跨度桥梁结构中关键承重构件高负荷的使用要求。国内相关团队针对500mpa级高强度耐候桥梁钢也做了大量研究,虽然钢板的强韧性、耐候性和焊接性达到了500mpa级耐候钢相关标准要求,但只能满足常规的单丝气保护焊接和埋弧自动焊形式的焊接制造,无法满足双丝大热输入埋弧自动焊接制造,焊接效率低,工期长,无法满足工程技术要求。此外,国内关于耐热输入焊接制造的桥梁钢仅仅适用于非耐候的普通桥梁钢,不能够无涂装使用。因此,开发出高强韧性、高耐候性且耐大热输入焊接的高性能q500qenhw耐候桥梁钢极为迫切。但500mpa级耐候桥梁钢在这种环境下高强度、耐候性与易焊性之间存在匹配矛盾,如何实现高强韧性、高耐候性和耐大热输入焊接性的优良匹配是这类耐候钢材设计与制造技术领域亟待突破的关键技术问题。
4.为了解决上述问题,众多学者在这类钢的综合性能调控方面,已进行了如下有益探索。
5.授权公告号为cn101876032a的发明专利“一种耐候桥梁钢用高强度钢板及其生产方法”,采用低碳当量,mn-ni-cr-cu-nb-v-ti系回火索氏体钢,通过低碳当量设计和控轧控冷 调质工艺,生产出的耐候桥梁钢具有高强度、良好的焊接性、抗层状撕裂性能等特点,但其冲击温度要求为-23℃,不能满足-40℃低温韧性的要求。
6.授权公告号为cn108342662a的发明专利“一种屈服强度550mpa级高强度耐候钢”,通过优化成分设计,不添加铌、钒,降低了生产成本,并严格控制了钢中n的含量,并采用控轧控冷工艺,生产出机械性能稳定及冷弯性能良好的高强度耐候钢。但是,耐候钢的-40℃冲击吸收功akv仅不低于38j,低温韧性富余量不足。
7.授权公告号为cn103451537a的发明专利“一种高焊接性能的低温耐候钢板及其生产方法”,控制较低的si、mn、cr含量(《0.15%、0.40~0.80%、未加入),可望使m-a组元脆性组织减少,使得钢板及大热输入下焊接热影响区具有优良的低温韧性,但也导致此钢强度不足、未达到500mpa级,且耐典型大气腐蚀性能不足。此外,添加有害元素sn(0.001~0.004%),虽然可弥补耐候性不足,但易导致焊缝裂纹倾向,恶化了钢板的焊接性能。
8.公开号为cn107326304a的发明专利“一种tmcp型屈服500mpa级桥梁钢板及生产方法”,通过低碳、nb-v微合金化控制技术,细化了组织,使得钢板屈服强度提高,改善了钢板的强韧性,此外钢板中mn、cr含量(1.45-1.55%、0.20-0.25%)较低,减少了m-a组元脆性组织、改善了焊接热影响区的低温韧性,但是导致该钢耐腐蚀性元素加入量严重不足,不具备耐典型大气腐蚀性能。
9.公开号为cn109609845a的发明专利“一种500mpa级耐候桥梁钢及其制造方法”,控制较高的si、cr含量(0.10-0.50%、0.30-1.25%),获得了较好的耐大气腐蚀性能(i≥6.5),但也易导致m-a组元脆性组织增多、焊接热影响区低温韧性不足。另外 mn含量(0.80-1.20%)较低,导致钢板的抗拉强度偏低(≤640mpa),进而屈强比较高(0.85-0.89),不利于结构安全性。
10.授权公告号为cn103451561b的发明专利“一种可大热输入量焊接的耐候钢板及其生产方法”,采用低碳低硅低锰c、si、mn(0.02~0.06、《0.10%、0.40~0.80%)成分设计,控制钢中的氧含量,进行热机械控制轧制和控制冷却,减少了钢板中m-a组元脆性组织,提高了焊接热影响区低温韧性,但也导致屈服强度偏低、未达到500mpa级。同时该发明只提供了焊接热影响区-20 ℃冲击值,尚不确定是否达到了-40 ℃冲击性能要求。且耐大气腐蚀指数i仅6.10,耐候性也显不足。因此,此钢在综合性能调控方面仍有待改进。
11.授权公告号为cn103451561b的发明专利“一种可大热输入量焊接的耐候钢板及其生产方法”,将si、mn(《0.10%、0.40~0.80%)控制在较低水平,也可以使m-a组元脆性组织减少,有利于提高焊接热影响区低温韧性,但也导致屈服强度偏低、未达到500mpa级。同时该发明只提供了焊接热影响区-20 ℃冲击值,尚不确定是否达到了-40 ℃冲击性能要求。且耐大气腐蚀指数i仅6.10,耐候性也显不足。因此,此钢在综合性能调控方面仍有待改进。
12.由此可见,目前现有500mpa级耐候桥梁钢及同类材料技术,对合金化成分设计及调控的研究还不够深入,未能实现500mpa级高强耐候桥梁钢高强韧性、高耐候性和耐大热输入焊接性的综合控制。
技术实现要素:
13.本发明要解决的问题是提供一种耐大热输入焊接的nb-v-ti-b系q500qenhw耐候桥梁钢,其厚度范围为32-80mm,屈服强度500mpa级,兼具高强韧性和高耐候性,在单/双丝埋弧自动焊大热输入范围15-75kj/cm条件下,焊接热影响区-40℃冲击功不低于60j,可应用于超大跨度免涂装耐候钢桥梁的建造。
14.为解决上述技术问题,本发明采用的技术方案是:一种耐大热输入焊接的nb-v-ti-b系q500qenhw耐候桥梁钢,其化学成分按重量百分数计为:c 0.035-0.055、si 0.20-0.40、mn 1.45-1.55、cr 0.42-0.60、ni0.35-0.45、cu 0.30-0.55、mo 0.17-0.20、nb 0.032-0.058、v 0.030-0.060、ti 0.018-0.025、b 0.0004-0.0008、al 0.015-0.034、n 0.0040-0.0080、o 0.0015-0.0025、la 0.0070-0.0090、p ≤0.015、s ≤0.005,余量为fe及不可避免杂质;上述化学成分按重量百分数计满足:570≤ta≤590,0.47≤dp≤0.68,且耐大气腐蚀指数i≥6.5,其中,
ta =729-394c-68.3mn 24.5si-36.1ni-24.8cr-20.5cu,dp = 15.32ti 5.79v 0.08b 0.18c 0.15n,i=26.01cu 3.88ni 1.20cr 1.49si 17.28p-7.29cu*ni-9.10ni*p-33.39cu2。
15.进一步的,所述耐候桥梁钢的焊接热影响区内对奥氏体晶粒长大具有抑制作用的尺寸为20~80nm的(ti,b,v)(c,n)复合析出粒子数量占85~95%,数量密度在9.10
×
105个/mm3~9.75
×
105个/mm3之间。
16.进一步的,所述耐候桥梁钢的焊接热影响区内可促进晶内铁素体异质形核的尺寸为0.5~1.5μm的 (ti,b,v)(c,n)析出粒子占90~95%,数量密度在8.14
×
104个/mm3~8.95
×
104个/mm3。
17.进一步的,采用单/双丝埋弧自动焊大热输入范围15-75kj/cm时,焊接热影响区满足-40℃kv2≥60j。
18.进一步的,所述耐候桥梁钢的屈服强度rel≥500mpa、抗拉强度rm≥630mpa。
19.进一步的,所述耐候桥梁钢焊接热影响区的组织由针状铁素体、粒状贝氏体铁素体和m-a组元构成,其中,针状铁素体的面积占比不低于30%,m-a组元的面积占例不多于10%。
20.进一步的,所述耐候桥梁钢的制备方法包括如下步骤:1)冶炼:钢坯料装炉,加热至熔化,浇注成钢锭,所述钢坯料的化学成分以质量百分比计为: c 0.035-0.055、si 0.20-0.40、mn 1.45-1.55、cr 0.42-0.60、ni 0.35-0.45、cu 0.30-0.55、mo0.17-0.20、nb 0.032-0.058、v 0.030-0.060、ti 0.018-0.025、b0.0004-0.0008、al 0.015-0.034、n 0.0040-0.0080、o 0.0015-0.0025、la 0.0070-0.0090、p ≤0.015、s ≤0.005,余量为fe及不可避免杂质;2)热机械轧制:将钢坯加热至温度1200~1280℃;粗轧开轧温度1100~1190℃,粗轧终轧温度1020~1080℃;精轧开轧温度900~960℃,精轧终轧温度730~850℃;控制冷却阶段开冷温度720~780℃,终冷温度500~580℃;3)钢板回火处理:回火温度550~660℃,回火时间2.0~3.0min/mm
ꢀ×
板厚(mm)。
21.本发明的技术方案是通过如下原理及方式来实现上述目的。
22.1)本发明的耐候桥梁钢,需要在准确理解高强易焊耐候钢c、si-mn、cr-ni-cu、nb-v-ti-b-la多元合金化及n、o气体元素含量控制原理的基础上,合理设计和控制如下化学成分(按重量百分数计)。
23.c:适量的c是可显著提高钢材强度,有利于本发明钢保证较高强度和较低屈强比。但过高的c会提高焊接裂纹敏感性,增加焊接热影响区的m-a组元脆性相含量,恶化焊接性能。因此,本发明钢中c的含量控制在0.035-0.055%。
24.si:适量的si可以提高耐候钢的强度、耐蚀性。但是当si含量过高时,会使焊接热影响区硬相m-a组元含量增加、低温韧性恶化。为此,本发明钢的si含量控制在0.20-0.40%。
25.mn:mn是固溶强化元素,可通过固溶强化显著提高强度。但是,mn含量过高会增加母材焊接裂纹敏感性。因此,本发明钢的mn含量控制在1.45-1.55%之间。
26.cu与cr、ni:cu与cr、ni复合添加,以确保钢的耐候性能,但是添加过多,会恶化焊接热影响区低温韧性。因此,本发明钢控制cu含量为0.30-0.55%,cr含量为0.42-0.60%,ni含量为0.35-0.45%。
27.mo:适量的mo既显著提高耐候性及母材和焊接热影响区的强韧性。但是,过多的mo会增加生产成本,且损害焊接热影响区低温韧性。因此,本发明钢将mo含量控制在0.17-0.20%。
28.nb:适量的nb元素可通过轧制形变诱导析出,细化晶粒,从而提高母材强韧性,但过多的nb增加成本,且不利于形成(ti,b,v)(c,n)析出粒子,影响焊接性能。因此,本发明钢控制nb:0.032-0.058%。
29.v-ti-b: v、ti、b复合添加,可在大热输入焊接热循环过程中,形成(ti,b,v)(c,n)粒子钉扎奥氏体晶界,抑制奥氏体晶粒长大;还可促进晶内铁素体异质形核,细化铁素体晶粒以及后续生成的脆硬相m/a组元。因此,本发明钢控制nb:0.032-0.058%、v:0.030-0.060%、ti:0.018-0.025%、b:0.0004-0.0008%。
30.n:适量增n,可以促进(ti,b,v)(c,n)粒子的析出。但是,过多的n易产生应变时效脆化问题。因此,本发明钢的n控制在0.0040-0.0080%。
31.la:适量添加稀土元素la,可富集在(ti,b,v)(c,n)粒子上,提高该析出粒子的形核率,但是过高的la会增加成本,以及增大析出粒子尺寸,降低形核效果。因此,控制la含量为0.0070-0.0090%。
32.al:al作为主要脱氧剂,主要在炼钢过程中起到脱氧作用,过多的al会促进有害链状b类夹杂物形成,不利于发挥氮化钛和氮化钒的作用。因此,本发明钢控制al含量 0.015-0.034%。
33.p:p 在钢中有严重的偏析倾向,加入过多,会恶化钢的力学性能和焊接性能,因此,本发明的钢限制p含量在0.015%以下。
34.s:s 是作为杂质混入的不可避免元素,s含量过高会生成粗大的夹杂物,降低钢板力学性能和焊接性能,故本发明钢将s 含量控制在低于0.005%。
35.2)准确调控一部分关键元素之间的相对添加量,以发挥这些元素对本发明钢耐大热输入焊接性能、力学性能与耐候性等综合性能的关键调控作用。
36.(1)通过调控关系式570≤ta≤590,要求将由c、mn、si、ni、cr、cu等六种主元成分按ta =729-394c-68.3mn 24.5si-36.1ni-24.8cr-20.5cu确定的双丝埋弧焊、气电立焊等焊接方法使得热输入75kj/cm焊接热影响区的奥氏体向铁素体转变开始温度ar3控制在570~590℃,以抑制粗大的粒状贝氏体与侧板条铁素体在原奥晶界形核生长,为细小晶内针状铁素体组织转变、韧性改善创造动力学条件;过高的ta值使侧板条铁素体组织较多,过低的ta值使粗大的粒状贝氏体或魏氏体组织较多,均不利于焊接热影响区组织细化与低温韧性。
37.(2)通过调控关系式0.47≤dp≤0.68,要求将由ti、v、b、n、c等五种关键微合金化元素成分按dp=15.32ti 5.79v 0.08b 0.18c 0.15n确定的关系式控制在0.47~0.68之间,使得焊接热影响区内形成20~80 nm的纳米级尺度(ti,b,v)(c,n)复合析出粒子数量占85~95%,数量密度在9.10
×
105个/mm3~9.75
×
105个/mm3之间;形成0.5~1.5 μm的微米级尺度(ti,b,v)(c,n)析出粒子占90~95%,数量密度在8.14
×
104个/mm3~8.95
×
104个/mm3。形成的微米级尺度(ti,b,v)(c,n)析出粒子可抑制焊接热循环过程中焊接热影响区奥氏体晶粒长大粗化,而形成的纳米级尺度(ti,b,v)(c,n)析出粒子可促进焊接热循环过程中焊接热影响区晶内形成针状铁素体,二者共同作用,可有效细化焊接热影响区组织,提高低温韧性。
过高的dp值使(v,ti,b)(c,n) 粒子尺寸偏小,无法起到抑制奥氏体晶粒长大粗化的作用,而过低的dp值使(v,ti,b)(c,n)亚微粒子数量偏少,促进针状铁素体异质形核作用能力不足,均不利于细化焊接热影响区组织与提高焊接热影响区低温韧性。
38.(3)通过调控关系式i≥6.5,要求将由cu、ni、cr、si四种主元成分(脆性元素p以外)按i=26.01(%cu) 3.88(%ni) 1.20(%cr) 1.49(%si) 17.28(%p)-7.29(%cu)(%ni)-9.10(%ni)(%p)-33.39 (%cu)2确定的耐候性指数下限值控制在≥6.5的范围,以确保本发明钢在气候温和的典型大气条件下的百年寿命周期腐蚀减薄量不超过1mm。过低的i值使耐候性不足,过高的i值反而损害综合性能且成本增加。
39.3)限定了热机械轧制与回火的关键工艺参数,包括适当的钢坯料加热温度、粗轧温度、精轧温度、开冷温度、终冷温度、回火温度与时间,其目的,一是母材形成适度细化的多相复合组织,以获得高塑韧性力学性能;二是母材形成适度尺寸数量分布的纳米级粒子与亚微米级粒子,使其在焊接热影响区发挥细化组织、提高韧性的作用。
40.本发明的有益效果是:1、在热输入量75kj/cm焊接条件下,本发明钢的焊接热影响区的组织由针状铁素体、粒状贝氏体铁素体和m-a组元构成,其中,针状铁素体的面积占比不低于30%,m-a组元的面积占例不多于10%,进而使得焊接热影响区的-40℃冲击功不低于60j;2、组织主要为针状铁素体和粒状贝氏体,屈服强度≥532mpa,抗拉强度≥657mpa, 屈强比0.80-0.82,-40℃夏比v型缺口冲击功≥250j;3、耐大气腐蚀指数i≥6.5,经过五个周期(216h)周期浸润加速腐蚀试验腐蚀速率趋于稳定时,腐蚀速率为1.25g/m3•
h,是普通c-mn钢的2倍左右;4、实现了500mpa级高强耐候钢的高强、耐大热输入焊接与耐候性的优良匹配,方案容易实施,生产工艺易控,能够实现低成本稳定批量工业化生产,可广泛用于大跨度、全焊接结构、免涂装桥梁建设。
41.下面结合附图对本发明进行详细说明。
附图说明
42.图1为本发明钢实施例1的母材显微组织图;图2为本发明钢实施例1在焊接热输入75kj/cm的焊接热影响区显微组织;图3为对比钢1在焊接热输入75kj/cm的焊接热影响区显微组织。
具体实施方式
43.本发明了一种耐大热输入焊接的nb-v-ti-b系q500qenhw耐候桥梁钢,化学成分按重量百分数计为:c 0.035-0.055、si 0.20-0.40、mn 1.45-1.55、cr 0.42-0.60、ni0.35-0.45、cu 0.30-0.55、mo 0.17-0.20、nb 0.032-0.058、v 0.030-0.060、ti 0.018-0.025、b 0.0004-0.0008、al 0.015-0.034、n 0.0040-0.0080、o 0.0015-0.0025、la 0.0070-0.0090、p ≤0.015、s ≤0.005,余量为fe及不可避免杂质。
44.上述化学成分按重量百分数计满足:570≤ta≤590,0.47≤dp≤0.68,且耐大气腐蚀指数i≥6.5,其中,ta =729-394c-68.3mn 24.5si-36.1ni-24.8cr-20.5cu,
dp = 15.32ti 5.79v 0.08b 0.18c 0.15n,i=26.01(%cu) 3.88(%ni) 1.20(%cr) 1.49(%si) 17.28(%p)
‑ꢀ
7.29(%cu)(%ni)-9.10(%ni)(%p)
ꢀ‑
33.39 (%cu)2。
45.上述耐候桥梁钢板制造方法步骤包括:准备钢坯料-轧制-冷却-回火处理。热轧阶段所需加热温度1200-1240℃,粗轧阶段控制粗轧终轧温度1020-1080℃,精轧阶段控制开轧温度900-960℃,精轧终轧温度730-850℃。精轧终轧后经层流水冷却,控制开冷温度为720-780℃, 500-580℃停止冷却空冷至室温,然后进行回火处理,控制回火温度为550-660℃,回火时间为2.0-3.0t(t为板厚)即可获得钢板成品。
46.实施例和对比例成分见表1中所示。
47.表1 实施例及对比例钢成分。
48.以下结合附图及具体实施方式对本发明的技术方案作进一步说明。
49.采用75kg真空炉按照实施例1-4以及对比例1-2的成分炼制6炉试验钢并按本发明所述的耐候桥梁钢板制造方法制得耐候桥梁钢板,具体步骤如下:1)冶炼:准备钢坯料,按照表1中所示成分准备各炉中钢坯料。钢坯料装炉,抽真空至 1 帕斯卡,加热钢水至熔化,高温高真空精炼钢水10 分钟,充保护气氩气,加合金,调整温度,分别浇注成型材,本发明中的型材为方块钢锭。
50.2)热机械轧制:首先将方块钢锭以10℃/s的速度加热到完全奥氏体化温度1200-1280℃,保温3小时以上,然后依次进行粗轧、精轧,即奥氏体再结晶区和奥氏体未再结晶区两阶段轧制工艺,采用大压下量进行轧制,粗轧控制终轧温度见表2所示,粗轧总压下率不
低于50%;精轧阶段控制开轧温度900-960℃,终轧温度730-850℃;分别参见表2 所示,精轧后制成厚度50mm 的钢板。
51.3)然后进入快速冷却装置进行冷却,开冷温度、冷却速率及终冷温度见表2。
52.4)最后进行回火处理,回火工艺(时间和温度)见表2所示,得到耐候桥梁钢板成品。
53.表2耐候桥梁钢板轧制工艺。
54.对上述方法制得的钢板分别进行力学性能检测,结果如表3所示,屈服强度均大于500mpa,抗拉大于630mpa,延伸率大于20%,屈强比小于0.85,-40℃冲击功均在254j以上。
55.表3耐候桥梁钢板力学性能。
56.从精轧后厚度 50mm 的钢板中切取10.5*10.5*80mm 的gleeble 热模拟试验样,以100℃/s 的升温速度加热到1350℃,停留1-3s 后,在以150s 的t8/5冷却时间,模拟埋弧焊焊典型热输入75kj/cm 的焊接。随后将热模拟试验样加工成10*10*55mm 的标准冲击试样,在500kj 的冲击试验机上进行-40℃冲击性能检验。
57.其中实施例1钢板母材金相组织如附图1所示,为细化的粒状贝氏体 针状铁素体复相组织,有利于获得优异强韧性。在模拟焊接热输入为75kj/cm 时,热影响区金相组织见附图2,对比例1 钢板在模拟焊接热输入为75kj/cm 时,热影响区组织见附图3。可以看出本发明的耐候桥梁钢板热影响区主要为针状铁素体(af) 粒状贝氏体铁素体(gb) m/a组元多相复合组织,其中针状铁素体组织比例约50%,针状铁素体占比较高,m-a组元占比8%,尺寸较细小,该组织使其热影响具有良好的低温韧性。而对比钢2,其化学成分含量和配比不在本发明中限定的创新设计技术范围内,得到的组织为粗大的粒状贝氏体 板条贝氏体,无细
化的针状铁素体组织,且脆硬的m/a组元比例约为30%,这种粗大的硬相m-a组元在承受冲击载荷时,容易萌生微裂纹而导致脆性断裂,使其焊接热影响区低温韧性较差。低温冲击韧性实验结果如表4所示。
58.表4 钢板典型热输入下热影响区冲击功。
59.上述结果表明:本发明各实施例钢模拟典型热输入条件下焊接热影响区-40℃冲击功均大于100j,低温韧性优良。而对比钢1-2的焊接热影响区-40℃冲击功均低于60j,低温韧性较差。
60.从表1可知,本发明耐候钢实施例1-8耐大气腐蚀指数i>6.5,从实施例1及对比例1成品钢板切取40*60*4mm腐蚀样,进行5个周期共216h的模拟工业大气环境周期浸润加速腐蚀试验,针对每个周期取样进行称重,测得失重量,计算得到本发明钢平均腐蚀失重率为1.25g
·
(m2·
h)-1
,而对比钢1的平均腐蚀失重率为2.51 g
·
(m2·
h)-1
。本发明钢板耐候性能约为对比钢的2倍,具有良好的耐大气腐蚀性能。
61.综上,在本发明组成范围及制备工艺条件下,所得钢板的力学性能、腐蚀性能和耐大热输入焊接性能均显著优于对比钢材。
62.最后应当说明的是:以上实施例仅用以说明本发明的技术方案而非对其限制;尽管参照较佳实施例对本发明进行了详细的说明,所属领域的普通技术人员应当理解:依然可以对本发明的具体实施方式进行修改或者对部分技术特征进行等同替换;而不脱离本发明技术方案的精神,其均应涵盖在本发明请求保护的技术方案范围当中。
再多了解一些
本文用于创业者技术爱好者查询,仅供学习研究,如用于商业用途,请联系技术所有人。