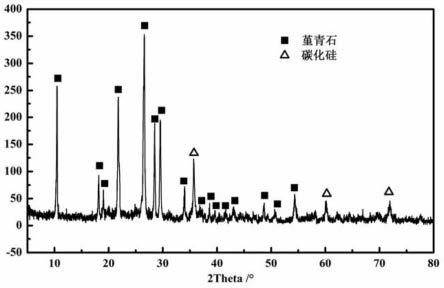
1.本发明涉及陶瓷材料技术领域,尤其涉及一种碳化硅晶须涂层表面改性堇青石蜂窝陶瓷的低温原位合成方法及其制得的产品。
背景技术:
2.堇青石质蜂窝陶瓷是一种广泛用于工业余热回收、汽车尾气净化、工业废气处理等领域的环保陶瓷材料,具有耐热冲击、重量轻、比表面积大、通流面积大、阻力损失小等优点,并具有高效节能和降低有害气体排放的双重优越性。
3.表面改性是有效提高蜂窝陶瓷比表面积的方法,而现阶段主要采取腐蚀法和涂层法。如采用多种酸对堇青石蜂窝陶瓷进行腐蚀处理,但是机械强度严重下降;采用碱腐蚀法对堇青石蜂窝陶瓷的表面进行改性,但是显著地损坏了堇青石陶瓷的结构完整性,容易导致材料的强度降低。而涂层法不仅可以提高陶瓷的比表面积,还可以提高蜂窝陶瓷的强度,赋予其更高的比表面积,因此成为了最常用的表面改性手段。目前研究最多的是涂覆大比表面积的γ-al2o3。然而,γ-al2o3涂层普遍存在着传热性能差、耐久性差、易发生相转变等缺点。而且γ-al2o3涂层具有高热膨胀系数,与堇青石陶瓷载体普遍存在严重的热膨胀失配,反复冷热交换容易导致涂层剥离。因此,亟待开发一种传热性强、耐久性好、性质稳定的表面改性涂层。
4.目前制备蜂窝陶瓷表面涂层的方法通常为浸渍法,即将蜂窝陶瓷浸入制好的料桨中,然后再进行热处理,造成了额外的燃耗,而且涂层与蜂窝陶瓷基体的结合性差。因此,如何简化涂层的制备工艺,并赋予涂层与蜂窝陶瓷基体良好的结合性仍是亟待解决的问题。
技术实现要素:
5.本发明的目的在于克服现有技术的不足,提供一种碳化硅晶须涂层表面改性堇青石蜂窝陶瓷的低温原位合成方法,采用低温原位合成的方式在烧制堇青石蜂窝陶瓷的同时原位生长出sic晶须涂层,使其由蜂窝陶瓷基体的内部到外部协同生长,再辅以晶种和催化剂降低晶须的起始合成温度,以便与堇青石蜂窝陶瓷的低温烧结制度相适应,从而形成传热性强、耐久性好、性质稳定、原位合成的表面改性涂层,获得高比表面积、高抗热震性、高强度的堇青石蜂窝陶瓷。本发明的另一目的在于利用上述碳化硅晶须涂层表面改性堇青石蜂窝陶瓷的低温原位合成方法制得的产品。
6.本发明的目的通过以下技术方案予以实现:
7.本发明提供的一种碳化硅晶须涂层表面改性堇青石蜂窝陶瓷的低温原位合成方法,以基料、结合剂、润滑剂、垫烧辅料为原料;
8.所述基料的组成为粘土类矿物30~50wt%、镁质矿物30~40wt%、铝质原料10~15%、金属铝质原料2~10wt%、金属硅质原料2~7wt%、碳质原料5~10wt%、晶种0.1~1wt%、催化剂0.1~1wt%,其中,镁质矿物为菱镁矿,或菱镁矿和烧滑石;
9.所述结合剂的用量为基料的3~5wt%,润滑剂的用量为基料的3~5wt%;
10.所述垫烧辅料的组成为硅质原料20~50wt%、碳质原料50~80wt%、金属铝质原料0~10wt%、金属硅质原料0~10wt%;
11.制备方法为:将所述基料混合后,加入结合剂混合均匀,再加入润滑剂和相对于基料用量为15~16wt%的水进行拌料、练泥、挤出成型、二次微波干燥后得到生坯,其中,第一次微波干燥至生坯的水分含量为5~8%,静置10~12h后,进行第二次微波干燥,至最终生坯的水分含量为<1%;然后将所述生坯进行埋石墨粉烧结,即将生坯置于匣钵中由所述垫烧辅料铺设的料床上,生坯通孔垂直于水平方向,将匣钵盖上盖板后再埋石墨粉烧结,升温时在150℃、660℃分别保温0.5~1h,烧结温度为1200~1300℃,烧成时间为1~3h,得到碳化硅晶须涂层表面改性堇青石蜂窝陶瓷。
12.进一步地,本发明所述粘土类矿物为高岭土、球土、膨润土中的一种、二种或三种组合;铝质原料为al(oh)3和/或γ-al2o3;金属铝质原料为金属铝粉和/或铝屑;金属硅质原料为金属硅粉、多晶硅废料、单晶硅废料中的一种或其组合;碳质原料为石墨粉、炭粉、碳黑中的一种或其组合;晶种为纳米β-sic粉;催化剂为过渡金属fe、co、ni粉中的一种或其组合。
13.进一步地,本发明所述粘土类矿物的粒度为80~700目;镁质矿物的粒度为80~325目;铝质原料的粒度为80~325目;金属铝质原料的粒度为80~180目;金属硅质原料的粒度为80~700目;碳质原料的粒度为325~1000目;晶种的粒度为50~100纳米;催化剂的粒度为700~1000目。
14.上述方案中,本发明所述硅质原料为稻壳粉、石英粉、粘土尾矿中的一种或其组合,其粒度为180~700目。所述结合剂为羧甲基纤维素(cmc)和/或羟丙基甲基纤维素(hpmc);润滑剂为食用油。
15.利用上述碳化硅晶须涂层表面改性堇青石蜂窝陶瓷的低温原位合成方法制得的产品,其气孔率≥50%、比表面积≥40m2/g、抗折强度≥50mpa、室温~800℃热震循环30次不开裂。
16.本发明具有以下有益效果:
17.(1)本发明采用梯级分段造孔的方案,用于提高堇青石蜂窝陶瓷基体的气孔率与比表面积,并以这些气孔为晶须生长创造空间,即室温下利用烧滑石或菱镁矿与水的作用,提高水的ph值呈弱碱性,碱性水与金属铝反应产生少量气体起到造孔作用,形成产物al(oh)3;150℃左右利用al(oh)3的分解产生水汽进行二次造孔,利用菱镁矿在660℃分解产生co2进行三次造孔,利用烧成温度下含sio2的矿物与金属铝、金属硅、碳质原料的“铝热还原反应”、“硅热还原反应”和“碳热还原反应”生成sio与co气体进行四次造小孔。利用不同温度梯度下四次造孔的工艺,可使大中小三种气孔均匀地分布在蜂窝陶瓷中,有效地提高了气孔率与比表面积,为烧成温度下合成晶须的气体逸出至表面创造了通道,也为晶须在陶瓷内部的生长创造了空间,提高了晶须的数量。
18.(2)本发明为降低sic晶须涂层的合成温度,采用了晶种 催化剂的组合,其中,纳米β-sic粉体作为晶种,有助于sio、co的沉积,促进sic晶须生长;fe、co、ni过渡金属粉烧成温度下熔融成液相,可作为催化剂促进β-sic晶种、sio、si、c的溶解与析出。晶种 催化剂的组合一方面降低了sic晶须的起始合成温度(现有技术为1300℃以上)至1200℃,另一方面
通过促进各类还原反应,进一步提高了晶须的数量(sic含量>20wt%)。
19.(3)本发明采用辅料垫烧的方式,使能合成sic晶须的气体(sio、co)由下至上流过蜂窝陶瓷的通孔中,补充了蜂窝陶瓷可能由于高气孔率导致的气体逸出流失部分,也提高了蜂窝陶瓷表面sic晶须涂层的数量及其比表面积。
20.(4)本发明在蜂窝陶瓷的内部与表面协同生长sic晶须及其涂层,其中,内部的sic晶须有助于提高材料的力学强度、传热性与抗热震性,表面生长的sic晶须涂层则有助于提高材料的比表面积,由蜂窝陶瓷内部气孔生长至其表面的sic晶须在气孔内部进行交织,起到自我锚定的作用,从而与陶瓷基体的结合性优良。
21.(5)本发明采用低温原位合成的方式生长sic晶须及其涂层,即在烧制堇青石蜂窝陶瓷的同时原位生长出sic晶须涂层,一次烧制即可获得蜂窝陶瓷基体 涂层,避免了传统的涂覆方法需要的第二步热处理,减少了燃耗。
22.(6)本发明采用梯级造孔工艺,设计气氛组成,辅以晶种与催化剂,通过蜂窝陶瓷内外协同生长的方式原位合成碳化硅晶须涂层,用来提高蜂窝陶瓷的比表面积与气孔率。本发明的晶须涂层可以很好地锚定在蜂窝陶瓷的孔洞,并有效解决了现有技术碳化硅晶须涂层合成温度过高的问题,提高了堇青石蜂窝陶瓷的性能。本发明合成温度低、产品性能优异,对于提高堇青石蜂窝陶瓷的品质具有重要意义,有利于推广应用和行业技术的进步与发展。
附图说明
23.下面将结合实施例和附图对本发明作进一步的详细描述:
24.图1是本发明制得的碳化硅晶须涂层表面改性堇青石蜂窝陶瓷的x射线衍射图谱;
25.图2是本发明实施例制得的碳化硅晶须涂层表面改性堇青石蜂窝陶瓷的二次电子像;
26.图3为本发明实施例中埋粉烧结与垫烧的示意图。
具体实施方式
27.实施例一:
28.本实施例一种碳化硅晶须涂层表面改性堇青石蜂窝陶瓷的低温原位合成方法,以基料、结合剂、润滑剂、垫烧辅料为原料;
29.基料的组成为高岭土(80目)20wt%、球土(325目)10wt%、烧滑石(325目)20wt%、菱镁矿(325目)20wt%、γ-al2o3(180目)5wt%、al(oh)3(80目)5wt%、金属铝粉(180目)5wt%、铝屑(180目)4wt%、金属硅粉(700目)5wt%、石墨粉(325目)5wt%、纳米β-sic粉(50纳米)0.5wt%、fe粉(700目)0.5wt%;
30.结合剂为cmc,其用量为基料的5wt%;润滑剂为食用油,其用量为基料的3wt%;
31.垫烧辅料的组成为稻壳粉(325目)20wt%、粘土尾矿(325目)10wt%、石墨粉(325目)50wt%、铝屑(180目)10wt%、多晶硅废料(180目)10wt%;
32.制备方法为:将上述基料混合后,加入结合剂混合均匀,再加入润滑剂和相对于基料用量为15wt%的水进行拌料、练泥、挤出成型、二次微波干燥后得到生坯,其中,第一次微波干燥至生坯的含水量为5%,静置12h后,进行第二次微波干燥,至最终生坯的水分含量为
<1%;然后将生坯进行埋石墨粉烧结,如图3所示,将生坯置于匣钵中由上述垫烧辅料铺设的料床上,生坯通孔垂直于水平方向,将匣钵盖上盖板后再埋石墨粉烧结,升温时在150℃、660℃分别保温0.5h,烧结温度为1200℃,烧成时间为3h,得到碳化硅晶须涂层表面改性堇青石蜂窝陶瓷。
33.实施例二:
34.本实施例一种碳化硅晶须涂层表面改性堇青石蜂窝陶瓷的低温原位合成方法,以基料、结合剂、润滑剂、垫烧辅料为原料;
35.基料的组成为高岭土(80目)20wt%、膨润土(325目)10wt%、球土(700目)10wt%、烧滑石(180目)20wt%、菱镁矿(80目)10wt%、γ-al2o3(325目)10wt%、金属铝粉(80目)5wt%、多晶硅废料(80目)5wt%、石墨粉(500目)8wt%、纳米β-sic粉(100纳米)1wt%、fe粉(700目)0.5wt%、co粉(800目)0.5wt%;
36.结合剂为hpmc,其用量为基料的3wt%;润滑剂为食用油,其用量为基料的5wt%;
37.垫烧辅料的组成为石英粉(325目)20wt%、石墨粉(500目)80wt%;
38.制备方法为:将上述基料混合后,加入结合剂混合均匀,再加入润滑剂和相对于基料用量为16wt%的水进行拌料、练泥、挤出成型、二次微波干燥后得到生坯,其中,第一次微波干燥至生坯的含水量为7%,静置11h后,进行第二次微波干燥,至最终生坯的水分含量为<1%;然后将生坯进行埋石墨粉烧结,如图3所示,将生坯置于匣钵中由上述垫烧辅料铺设的料床上,生坯通孔垂直于水平方向,将匣钵盖上盖板后再埋石墨粉烧结,升温时在150℃、660℃分别保温1h,烧结温度为1250℃,烧成时间为2h,得到碳化硅晶须涂层表面改性堇青石蜂窝陶瓷。
39.实施例三:
40.本实施例一种碳化硅晶须涂层表面改性堇青石蜂窝陶瓷的低温原位合成方法,以基料、结合剂、润滑剂、垫烧辅料为原料;
41.基料的组成为高岭土(500目)50wt%、烧滑石(180目)10wt%、菱镁矿(180目)20wt%、al(oh)3(180目)10wt%、金属铝粉(150目)2wt%、金属硅粉(325目)2wt%、石墨粉(400目)5.8wt%、纳米β-sic粉(50纳米)0.1wt%、ni粉(900目)0.1wt%;
42.结合剂为hpmc,其用量为基料的3wt%;润滑剂为食用油,其用量为基料的5wt%;
43.垫烧辅料的组成为石英粉(700目)50wt%、碳黑(1000目)50wt%;
44.制备方法为:将上述基料混合后,加入结合剂混合均匀,再加入润滑剂和相对于基料用量为15.5wt%的水进行拌料、练泥、挤出成型、二次微波干燥后得到生坯,其中,第一次微波干燥至生坯的含水量为8%,静置10h后,进行第二次微波干燥,至最终生坯的水分含量为<1%;然后将生坯进行埋石墨粉烧结,如图3所示,将生坯置于匣钵中由上述垫烧辅料铺设的料床上,生坯通孔垂直于水平方向,将匣钵盖上盖板后再埋石墨粉烧结,升温时在150℃、660℃分别保温1h,烧结温度为1300℃,烧成时间为1h,得到碳化硅晶须涂层表面改性堇青石蜂窝陶瓷。
45.实施例四:
46.本实施例一种碳化硅晶须涂层表面改性堇青石蜂窝陶瓷的低温原位合成方法,以基料、结合剂、润滑剂、垫烧辅料为原料;
47.基料的组成为高岭土(325目)30wt%、烧滑石(325目)15wt%、菱镁矿(180目)
15wt%、al(oh)3(325目)15wt%、金属铝粉(150目)10wt%、多晶硅废料(80目)5wt%、单晶硅废料(325目)2wt%、石墨粉7wt%(325目)、纳米β-sic粉(50纳米)0.5wt%、co粉(1000目)0.5wt%;
48.结合剂为cmc和hpmc,用量分别为基料的2wt%、3wt%;润滑剂为食用油,其用量为基料的4wt%;
49.垫烧辅料的组成为稻壳粉(325目)10wt%、石英粉(700目)10wt%、粘土尾矿(180目)10wt%、石墨粉(325目)20wt%、炭粉(500目)20wt%、碳黑(1000目)10wt%、金属铝粉(120目)5wt%、铝屑(80目)5wt%、多晶硅废料(325目)4wt%、单晶硅废料(80目)3wt%、金属硅粉(700目)3wt%;
50.制备方法为:将上述基料混合后,加入结合剂混合均匀,再加入润滑剂和相对于基料用量为15wt%的水进行拌料、练泥、挤出成型、二次微波干燥后得到生坯,其中,第一次微波干燥至生坯的含水量为6%,静置10h后,进行第二次微波干燥,至最终生坯的水分含量为<1%;然后将生坯进行埋石墨粉烧结,如图3所示,将生坯置于匣钵中由上述垫烧辅料铺设的料床上,生坯通孔垂直于水平方向,将匣钵盖上盖板后再埋石墨粉烧结,升温时在150℃、660℃分别保温0.5h,烧结温度为1240℃,烧成时间为2h,得到碳化硅晶须涂层表面改性堇青石蜂窝陶瓷。
51.实施例五:
52.本实施例一种碳化硅晶须涂层表面改性堇青石蜂窝陶瓷的低温原位合成方法,以基料、结合剂、润滑剂、垫烧辅料为原料;
53.基料的组成为高岭土(325目)20wt%、球土(700目)10wt%、菱镁矿(325目)30wt%、al(oh)3(150目)15wt%、金属铝粉(180目)7wt%、多晶硅废料(240目)2wt%、单晶硅废料(325目)3wt%、金属硅粉(700目)2wt%、石墨粉(325目)4wt%、炭粉(325目)3wt%、碳黑(1000目)3wt%、纳米β-sic粉(50纳米)0.5wt%、co粉(700目)0.2wt%、fe粉(1000目)0.2wt%、ni粉(700目)0.1wt%;
54.结合剂为cmc和hpmc,用量分别为基料的3wt%、2wt%;润滑剂为食用油,其用量为基料的5wt%;
55.垫烧辅料的组成为稻壳粉(325目)20wt%、石英粉(700目)20wt%、石墨粉(325目)20wt%、炭粉(700目)30wt%、金属铝粉(180目)2wt%、铝屑(180目)3wt%、多晶硅废料(325目)2wt%、单晶硅废料(500目)3wt%;
56.制备方法为:将上述基料混合后,加入结合剂混合均匀,再加入润滑剂和相对于基料用量为15wt%的水进行拌料、练泥、挤出成型、二次微波干燥后得到生坯,其中,第一次微波干燥至生坯的含水量为6%,静置11h后,进行第二次微波干燥,至最终生坯的水分含量为<1%;然后将生坯进行埋石墨粉烧结,如图3所示,将生坯置于匣钵中由上述垫烧辅料铺设的料床上,生坯通孔垂直于水平方向,将匣钵盖上盖板后再埋石墨粉烧结,升温时在150℃、660℃分别保温0.5h,烧结温度为1260℃,烧成时间为3h,得到碳化硅晶须涂层表面改性堇青石蜂窝陶瓷。
57.分别以未采用辅料垫烧(即放入空匣钵中)、未加入纳米sic晶种、未加入过渡金属催化剂(其他条件均与实施例一相同)为对比例一、对比例二、对比例三;以未采用二次微波干燥工艺和静置10~12h的处理,一次微波干燥至最终生坯的水分含量为<1%(其他条件
均与实施例二相同)为对比例四;以未使用菱镁矿为原料,仅以烧滑石为镁源(其他条件均与实施例三相同)为对比例五。本发明实施例与对比例制得的堇青石蜂窝陶瓷的各项性能与sic含量如表1所示。
58.表1本发明实施例与对比例制得的堇青石蜂窝陶瓷的性能与sic含量
[0059][0060]
其中,sic的含量采用k值法进行检测,以刚玉为参照物。
[0061]
从表1可以看出,本发明实施例制得的碳化硅晶须涂层表面改性堇青石蜂窝陶瓷均获得了高气孔率与高比表面积。
[0062]
对比实施例一与对比例一的数据可知,未采用本发明的垫烧辅料进行垫烧,对比例一所得样品的sic含量下降,因为蜂窝陶瓷的高气孔率导致内部的sio、co等合成sic晶须的气体会流失一部分,因此需要通过垫烧辅料补充流失的部分;对比实施例一与对比例二、对比例三的数据可知,单独使用sic晶种或催化剂,促进sic合成的效果不如复合使用,因此使用晶种 催化剂的组合十分有必要;对比实施例二与对比例四的数据可知,如果没有干燥后剩余的碱性水与金属铝反应释放气体和生成mg(oh)2、al(oh)3,气孔率、比表面积与sic含量等指标均不如进行静置反应处理的样品;对比实施例三与对比例五的数据可知,仅以烧滑石为镁质原料,缺少了菱镁矿660℃左右的分解,同样降低了样品的气孔率、比表面积与sic含量。
[0063]
本发明实施例制得的碳化硅晶须涂层表面改性堇青石蜂窝陶瓷,如图1所示,晶相只有sic和堇青石两种;如图2所示,大量sic晶须分布在堇青石蜂窝陶瓷基体内部与表面,内部的晶须(图2上半部分)起到提高热导率、抗折强度和抗热震性能的作用,表面的晶须涂层(图2下半部分)起到提高比表面积的作用,且性质稳定、传热性好。
再多了解一些
本文用于创业者技术爱好者查询,仅供学习研究,如用于商业用途,请联系技术所有人。