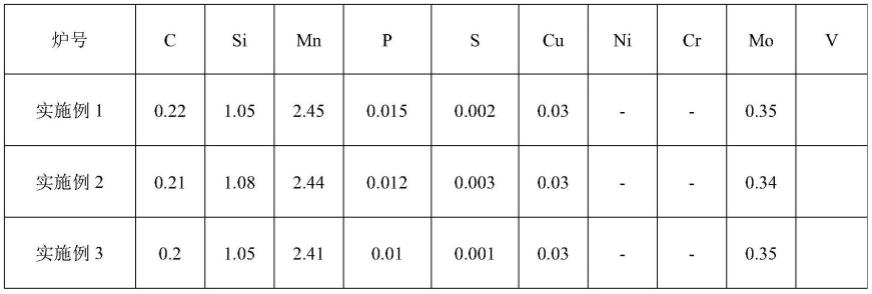
1.本技术涉及冶金技术领域,具体而言,涉及钎具钢及其制备方法。
背景技术:
2.凿岩钎具是矿山开采、隧道等基本建设的钻爆作业中所需的工具消耗品,钎具工作时,钎头和钎杆连接,钎头直接与岩石接触,承受着2000~9000次/min左右的高频冲击,每次的冲击能量25-500j,钎具工作时的失效形式有杆体磨损、变形、断裂失效及钎头硬质合金的脱落,塑性变形、应力疲劳腐蚀断裂等。钎具用钢要求有较高的强度、高的韧性、耐磨损、耐腐蚀及高的冲击疲劳性能。但现有的钎具用钢需要使用nb、v等贵重金属来保持其性能,导致生产成本较高。
3.鉴于此,特提出本技术。
技术实现要素:
4.本技术的目的在于提供钎具钢及其制备方法,不需要添加nb、v等贵重金属,能够兼顾成本和性能。
5.本技术是这样实现的:
6.第一方面,本技术提供一种钎具钢,钎具钢的化学成分按重量百分比计,包含c:0.17%~0.23%,si:0.90%~1.2%,mn:2.2%~2.6%,mo:0.30%~0.4%,s≤0.005%,p≤0.020%,cu≤0.20%,al:0.010%~0.025%,o≤0.0015%,n<0.0050%,h≤0.0001%,其余为fe和不可避免的杂质。
7.在可选的实施方式中,钎具钢的化学成分按重量百分比计,包含0.01%≤cu≤0.20%,0.01%≤p≤0.02%。
8.在可选的实施方式中,钎具钢的化学成分按重量百分比计,包含si:1.0%~1.1%,mn:2.35%~2.48%。
9.第二方面,本技术提供一种如前述实施方式中任一项的钎具钢的制备方法,包括按照钎具钢的化学成分依次进行钢水冶炼、精炼、连铸和轧制。
10.在可选的实施方式中,钢水冶炼步骤包括:
11.使用转炉对铁水进行冶炼,控制铁水进入转炉时s≤0.050%,as≤0.035%,冶炼终点时控制钢水中c含量为0.08%~0.12%,控制p含量≤0.018%。
12.在可选的实施方式中,转炉在出钢过程中加入硅铁、低碳锰铁、硅锰以及铝铁。
13.在可选的实施方式中,精炼步骤包括依次进行lf精炼和rh精炼;
14.lf精炼步骤中加入钼铁,lf精炼持续时长为60~80min;
15.rh精炼的真空处理时间大于18min,并且采用氩气进行软吹,使用碳化稻壳覆盖于炉渣表面。
16.在可选的实施方式中,开浇炉的钢水在lf精炼结束后温度为1605
±
10℃,到达rh精炼的工位时的温度为1595
±
10℃;连浇炉的钢水在lf精炼结束后温度为1599
±
10℃,到
达rh精炼的工位时的温度为1589
±
10℃。
17.在可选的实施方式中,连铸步骤包括使用中间包、结晶器连续铸造形成连铸坯,并使连铸坯在二冷段内进行二次冷却;
18.沿连铸坯输送方向,二冷段包括依次连接的一区、二区、三区和四区,二次冷却用水量的分配比例为:一区28~30%,二区34~37%,三区19~22%,四区13~15%。
19.在可选的实施方式中,在轧制步骤之后,钎具钢的制备方法还包括对轧制成型的钢材进行热处理,热处理步骤包括:
20.将钢材在885℃
±
10℃下进行油淬冷却;在250
±
10℃回火,保温150min;空冷至室温。
21.本技术具有以下有益效果:
22.本技术实施例提供的钎具钢的化学成分按重量百分比计,包含c:0.17%~0.23%,si:0.90%~1.2%,mn:2.2%~2.6%,mo:0.30%~0.4%,s≤0.005%,p≤0.020%,cu≤0.20%,al:0.010%~0.025%,o≤0.0015%,n<0.0050%,h≤0.0001%,其余为fe和不可避免的杂质。本技术实施例提供的钎具钢为低成本si-mn-mo系钎具钢,无需添加nb、v贵重金属,而通过添加廉价的al(0.010%~0.025%),能够获得较低的成本,且具有较佳强度、韧性的钎具钢,能够满足钎具的使用需求。本技术实施例提供的钎具钢的制备方法用于制作上述的钎具钢。
具体实施方式
23.目前传统的凿岩钎具一般采用simnmo、simn、crmo、crnimo等牌号的钢种。凿岩钎具大多使用中高碳钢,锻造性能较差,造成凿岩钎具冲击韧性较低,使用寿命较短,而性能优良的凿岩钎具的用钢使用大量的贵重合金nb、ni、v,成本较高。因此迫切需要一种低成本、洁净、高强高韧的凿岩钎具用钢。本技术提供的钎具钢属于一种低成本si-mn-mo系钎具用钢,不添加nb、v贵重金属,仅添加廉价的al,配合合理的制作工艺,制得一种低成本高强高韧洁净钎具钢。
24.为使本技术实施例的目的、技术方案和优点更加清楚,下面将对本技术实施例中的技术方案进行清楚、完整地描述。实施例中未注明具体条件者,按照常规条件或制造商建议的条件进行。所用试剂或仪器未注明生产厂商者,均为可以通过市售购买获得的常规产品。
25.以下结合实施例对本技术的特征和性能作进一步的详细描述。
26.本技术提供的一种钎具钢,其化学成分按重量百分比计,包含c:0.17%~0.23%,si:0.90%~1.2%,mn:2.2%~2.6%,mo:0.30%~0.4%,s≤0.005%,p≤0.020%,cu≤0.20%,al:0.010%~0.025%,o≤0.0015%,n<0.0050%,h≤0.0001%,其余为fe和不可避免的杂质。n含量过高,会对钢材表面质量产生负面影响,研究表明,n含量超过0.0070%会增加钢材裂纹敏感性。由于氧含量过高会导致钢材使用疲劳寿命降低,因此控制o≤0.0010%来保障钢材使用疲劳寿命。由于该钎具钢中si、mn含量较高,氢脆敏感性强,严格控制氢含量能保证产品质量,因此控制h≤0.0001%。al除了具有脱氧和细化晶粒作用外,还能抑制低碳钎具钢的时效,提高钢在低温下的韧性,进一步的,可控制al在0.015%~0.025%。
27.进一步的,钎具钢的化学成分按重量百分比计,包含0.01%≤cu≤0.20%,0.01%≤p≤0.02%。铜和磷过高,易导致钎具钢在热加工过程中产生热脆和冷脆,降低力学性能。但少量的铜加入钢中可以提高钎具钢抗大气腐蚀性,特别与磷配合使用时,能提高钎具钢的强度,而对钢焊接性能无影响。因此,本实施例中对铜、磷的上限和下限均做出了限定,来使钎具钢具有较佳的抗腐蚀性和力学性能。
28.进一步的,钎具钢的化学成分按重量百分比计,包含si:1.0%~1.1%,mn:2.35%~2.48%。
29.下面介绍本技术提供的钎具钢的制备方法。
30.本技术实施例提供的钎具钢的制备方法包括钢水冶炼、精炼、连铸和轧制等步骤,在轧制之后,还可以对轧制得到的钢材进行热处理以提高性能。下面对各个步骤分别进行介绍。
31.一、钢水冶炼
32.该步骤目的是将炼钢原料冶炼为适合后续精炼的钢水。在本实施例中,钢水冶炼步骤所使用的原料是高炉铁水,即矿料经高炉冶炼得到的铁水。本技术实施例中,可采用转炉进行钢水冶炼,确保铁水进入转炉时s≤0.050%,as≤0.035%。可选的,铁水可按照110吨控制;优选的,禁止铁包加废钢。冶炼终点时控制钢水中c含量为0.08%~0.12%,控制p含量≤0.018%;进一步的,可控制p含量≤0.015%。在本技术实施例中,如未特别说明,各元素含量百分比均为重量百分比。
33.可选的,转炉在出钢过程中加入硅铁、低碳锰铁、硅锰以及铝铁。具体的,钢水出钢到1/3开始,可从高位料仓加入900
±
15kg的硅铁,加入低碳锰铁1200
±
20kg,加入硅锰2500
±
20kg,加入铝铁200
±
10kg。转炉总合金加入量控制在4800
±
50kg,转炉出钢温度确保≥1610℃。转炉铁水及合金装入量按130吨左右控制,采用留钢操作,出钢量控制在110吨左右。
34.应理解,在可选的其他实施例中,也可以采用电炉冶炼合适的钢水,作为后续精炼的原料;铁水、硅铁、低碳锰铁、硅锰以及铝铁的装入量可以根据需要进行调整。
35.二、精炼
36.精炼步骤的目的是为了进一步除杂、除气以及合金化(即将钢水的元素成分调至最终钢中所需要的比例),精炼所使用的原料即为钢水冶炼步骤中得到的钢水。在本技术实施例中,精炼步骤包括依次进行lf精炼和rh精炼,分别使用了lf炉和rh真空精炼炉。
37.(1)lf精炼
38.lf精炼的目的是脱硫、脱氧以及去除夹杂。可选的,要求到站温度≥1520℃,取样温度确保≥1540℃。脱氧要求:渣料加完化开后逐步加入铝球渣150~200kg,碳化硅进行扩散脱氧,保证初样前黄白渣,精炼中后期加入碳化硅(过程中如果碳高可使用硅铁粉)对炉渣进行维护。造渣要求:加入400
±
20kg石灰,到站炉渣化好后分2~4批加入。通过石灰与萤石来调整渣的流动性。lf精炼过程中吹氩器,前期化渣、增碳加合金时氩气按25~45m3/h控制。lf精炼步骤中加入钼铁,可选的,lf精炼开始处理后60~90min加入钼铁500
±
10kg(以110吨铁水为基础),后续根据试样分析结果逐步调整至目标值。lf精炼时间≥55min,为避免长时间精炼导致钢水与空气中的氮气接触造成n含量增加,优选地,lf精炼时间控制在60min~80min。
39.lf精炼结束后出站温度需要进行控制,具体的,开浇炉的钢水在lf精炼结束后温度为1605
±
10℃,连浇炉的钢水在lf精炼结束后温度为1599
±
10℃。应理解,开浇炉是指一个浇次中的第一个炉次,连浇炉是指开一个浇次中开浇炉之后的炉次。由于lf精炼工序之后的rh和连铸工序均无加热设备。在后续rh精炼过程及钢包调运过程会存在一定温降。若温度过低,到连铸中间包会堵水口,易使浇注中断。温度过高会引起水口失控,坯壳减薄造成漏钢。而开浇炉是一个浇次中的首个炉次,后续面对的中间包的温度相对较低,中间包会吸收一定的热量,因此需要提高首个浇次(即开浇炉)的钢水温度。
40.可选的,在lf精炼过程中,可根据第一个采样结果补喂铝线,调整钢水中al为0.03%,出站前4min调整al满足成分控制要求。
41.(2)rh精炼
42.可选的,开浇炉钢水到达rh精炼的工位时的温度为1595
±
10℃;连浇炉钢水到达rh精炼的工位时的温度为1589
±
10℃。rh精炼对钢水进行真空脱气处理,可选的,真空度≤266pa,真空处理时间大于18min。可选的,高真空时间≥15min,纯脱气时间≥8min。环流气体采用ar环流,开抽阶段流量控制在40~60nm3/h,稳定后流量控制在60~80nm3/h。采用ar软吹,软吹流量控制在1~30nm3/h,开浇炉软吹时间≥15min,连浇炉软吹时间≥10min。可选的,软吹控制以不吹破渣面且渣面略微波动为准,确保钢中的大尺寸夹杂物上浮排除,软吹过程中禁止钢水裸露。破真空后喂钙铁线,即,软吹镇静前喂纯钙线,比如喂钙线80米。钙处理后(软吹前)投入碳化稻壳保温,保证碳化稻壳均匀铺盖于炉渣表面。可选的,该钎具钢精炼过程中禁止ob升温,成分微调在前中期完成;处理过程禁止使用冷钢降温。
43.三、连铸
44.经过精炼步骤处理完的钢水中的合金元素已经调整到钎具钢所需的含量,温度也达到了可浇注的状态。连铸步骤主要目的是通过浇注的方式将钢水冷却形成铸坯,在浇注过程中也伴随着夹杂物的上浮,因此也具有一定的去除夹杂的作用。在本技术实施例中,连铸步骤包括使用中间包、结晶器连续铸造形成连铸坯,并使所述连铸坯在二冷段内进行二次冷却。连铸过程中,在中间包的上游有大包,钢水通过大包注入到中间包中。中间包的作用在于将钢液分配给各个结晶器,并一定程度吸收钢水中上浮的夹杂物。
45.可选的,采用5机5流生产大方坯连铸坯,铸坯尺寸可选为280
×
280mm大方坯。连铸过程中间包过热度控制需要符合要求,比如开浇炉的过热度≤40℃,连浇炉的过热度≤35℃,以增大铸坯细等轴晶区,减小成分偏析。开浇炉在调运至连铸机平台时,钢包内钢水温度要求控制为1543
±
5℃,连浇炉中间包目标温度为1515
±
10℃。连铸过程中,大包至中间包采用长水口加ar气保护浇注,同时采用浸入式水口保护浇注,防止钢液二次氧化。大包的长水口插入深度≥200mm,中间包至结晶器的水口插入深度120
±
20mm。确保稳定拉速、稳定中包液位在最高位,保证结晶器液面的稳定,杜绝人为扰动结晶器液面,避免卷渣出现(保护渣卷入钢水中影响钢水质量)。连铸过程中,用中包覆盖剂、结晶器保护渣等措施对钢水进行全程保护浇注,中包覆盖剂和结晶器保护渣能够隔离钢水与空气,避免钢水氧化,同时也能够一定程度吸收上浮夹杂。浇铸时还可采用结晶器电磁搅拌技术和末端电磁搅拌技术,均匀钢水成分,降低偏析值。其中,结晶器水量控制在2400
±
60l/min,结晶器电磁搅拌电流按100
±
30a控制,频率2.5hz。末端电磁搅拌电流按600a控制,频率4hz。电磁搅拌采用交替方式搅拌,具体交替时间:15s/10s/15s。由于本实施例中铸坯为大断面铸坯,为保证连
铸坯质量及连铸过程顺利,各流拉速控制在0.9m/min。本技术实施例的钎具钢可能存在裂纹敏感性强的问题,因此比水量采用弱冷,按0.30l/kg~0.40l/kg设置。另外,弱冷可以抑制柱状晶生长,增大截面上等轴晶面积比。
46.二冷段位于结晶器的下游,铸坯从结晶器拉出时中心部位温度较高而呈液态,需要在后续的二冷段中进行二次冷却(结晶器中的冷却相当于首次冷却)。可选的,二冷段包括依次连接的一区、二区、三区和四区,二次冷却用水量的分配比例为:一区28~30%,二区34~37%,三区19~22%,四区13~15%。在一个具体的实施例中,可设置水量分配为:一区29%,二区36%,三区21%,四区14%。连铸二冷水的控制是生产的关键,会直接影响铸坯的表面质量。本实施例中,二冷段的冷却水前区强后区弱,前区强(一区、二区)使铸坯形成一定厚度坯壳,保证配合拉速进行稳定浇注,避免漏钢。后区(三区、四区)采用弱冷,保证冷却均衡,铸坯表面温度逐步下降,使钢坯内部同表面温度减的梯度大小均衡,保证钢坯内外温度降温均衡,避免钢坯产生裂纹。
47.在二次冷却进行完毕后,铸坯进入缓冷阶段。由于钎具钢中硅锰含量高,裂纹敏感性较强,连铸坯切割后,铸坯表面和内部冷速差别大,易导致因应力作用而造成裂纹和开裂的风险。所以铸坯需采用合适的缓冷,消除表面应力裂纹。可选的,连铸坯分段后铸坯温度为500℃~720℃时,将铸坯送入不带加热功能的坑缓冷,铸坯缓冷至温度≤200℃可以出坑。缓冷入坑温度过高,缓冷过程温降慢,缓冷时间需要的长,影响生产效率。缓冷入坑温度过低意味着缓冷之前的冷却过程(比如二次冷却)强度过大,易造应力裂纹。而出坑温度过高则可能产生组织相变,导致体积膨胀,引起组织应力而形成铸坯的脆性,易造成铸坯开裂或断裂。
48.四、轧制
49.对铸坯进行轧制,一方面是为了使钢坯变为需要的形状,另一方面,可改善钢材的性能。在本技术实施例中,会对经过缓冷后的铸坯进行加热轧制。
50.可选的,采用步进梁式连续加热炉加热,由于钎具钢合金含量高,导热性较差,且存在较强的裂纹敏感性,铸坯进炉在无烧嘴的预热段温度需确保≤700℃(比如选择为494~649℃),缓慢预热,预热段时间≥110min。加热炉沿长度方向上还包括三段:即一加热段、二加热段和均热段。铸坯可先后在一加热段、二加热段进行加热,然后进入均热段。可选的,进入一加热段后加热温度控制在750~1000℃,一加热热段时间确保≥60min。二加热段温度控制在1050~1200℃,均热段控制为1140~1180℃,加热温度严格控制不超过1200℃。含硅钢的除鳞困难是由于在较高温度(1200℃以上)下形成feo-sio2氧化物共晶产物(铁橄榄石)有关,这种液态的氧化铁皮渣钢的界面具有很强湿润性,促进了界面的强附着力,从而阻碍了氧化铁皮的去除,影响钢材表面质量。二加热段和均热段为高温加热段,控制总时间110min~150min,主要目的为保障钢烧透,加热总时间确保≥280min。钢坯入炉时在保障预热段加热时间的基础上,钢坯在预热段均衡步进,冷坯步进速度≥0.11m/min,温坯步进速度≥0.13m/min。均热段实际空燃比按≤1.8控制,比如选择空燃比为1.4~1.8。通过对煤气和空气流量、炉膛压力等控制,使得被加热钢坯在达到轧制工艺要求的温度分布的同时,实现了最小的加热炉能耗。二加热段实际空燃比根据热值进行调整保证残氧量在1~1.5%。通过残氧量能够判断空气在燃烧过程中是否过剩,从而确保空燃比处于较佳值。
51.轧制圆钢的开轧温度控制在1020~1100℃,终轧温度控制在≥900℃。圆钢轧制结
束后采用堆冷即可。即,不额外增加退火或入坑缓冷工序。圆钢定尺分段后确保温度≥350℃下线进行避风堆冷时效,可完成去应力和去氢处理,轧制工序不增加退火或缓冷设备,能够降低生产成本。钢材后续经过探伤精整后打包入库。
52.五、热处理
53.在轧制步骤之后,钎具钢的制备方法还可以包括对轧制成型的钢材进行热处理,以提高钎具钢的性能。可选的,热处理包括将钢材加热到885℃
±
10℃,保温40min,再进行油淬冷却;此后在250
±
10℃回火,保温150min;空冷至室温。具体的,可使用柴油进行油淬。淬火温度过高,得到的马氏体形态会变粗,抗拉强度变低;同时因奥氏体晶粒长大,淬火后的马氏体组织也粗大,增加了钢的脆性。淬火温度越低,则马氏体板条越细小。但淬火温度过低,则达不到相变温度,则不能完成淬火要求,再好的冷却也不能使材料淬硬。由于马氏体的板条细化和板条内较高的位错密度是提高钢强度重要因素,因此为了获得较高的抗拉强度,应当在适当的温度区间选择较低的淬火温度。本实施例中将淬火加热温度选择在885
±
10℃,组织中马氏体的板条细小,从而获得高强度高韧性的力学性能。
54.回火温度应当结合具体的钢材成分来选定,针对本技术实施例提供的钎具钢,回火温度采用低温回火,并控制温度在250
±
10℃,能获得较好的强韧性能。若回火温度过高,容易发生马氏体分解和残留奥氏体转变,组织由回火马氏体转变为索氏体、屈氏体,导致强度降低。若回火温度过低,会导致,会导致材料强度较高,但韧性较差,容易出现脆性断裂。
55.通过上述步骤制备得到的钎具钢具有高强度高韧性的特点,抗拉强度达到1504~1568mpa,屈服强度达到1202~1288mpa,冲击功达到86~115j。并且,在上述工艺下,该钎具钢纯净度好,【o】控制在9ppm以下,【n】含量控制在50ppm以下,【h】控制在1ppm以下,钢中有害残余元素含量较低。采用合理的铸坯缓冷、加热工艺及轧制工艺保证了钢表面和内部质量。本技术实施例提供的钎具钢,硅锰含量高,裂纹敏感性和氢致缺陷敏感强,而采用“热轧 堆冷”替代“热轧 去应力退火”和“热轧 缓冷”状态交货,能够降低工序成本。
56.下面结合本技术各个实施例以及对比例,对本技术提供的钎具钢及其制备方法的有益效果进行说明。
57.各实施例和对比例的成分见表1和表2。
58.表1:
59.[0060][0061]
表2:
[0062]
炉号alassnsbpbbio/ppmn/ppmh/ppm实施例10.0180.0040.0040.00040.00090.00056.138.40.4实施例20.0190.0040.0030.00040.00070.00055.936.70.7实施例30.020.0030.0020.00040.00080.00056.240.40.3对比例10.010
‑‑‑‑‑‑
50-对比例20.020
‑‑‑‑‑‑
76-对比例30.032
‑‑‑‑‑‑
72-对比例40.0180.0090.0070.00040.0010.0031165-[0063]
上述表格中数据,如非特别说明,单位为wt.%。
[0064]
以下对各个实施例以及对比例的工艺参数进行介绍。
[0065]
实施例1
[0066]
(1)钢水冶炼
[0067]
采用容量130吨转炉,终点c:0.093%,终点出钢下渣控制良好,终点p:0.011%。
[0068]
(2)精炼
[0069]
使用容量130吨的lf炉,到站钢水温度1526℃,出站温度1610℃;lf精炼时间113min。使用容量130吨rh炉进行rh精炼,rh精炼温度控制为1597℃,高真空时间为19min。
[0070]
(3)连铸
[0071]
过热度34℃,拉速0.9m/min;结晶器电磁搅拌100a/2.5hz,末端电磁搅拌600a/4hz。铸坯为280mm大方坯。二次冷却中各区配水为:一区29%,二区35%,三区21%,四区15%。冷却至615℃进入缓冷坑。
[0072]
(4)轧制
[0073]
预热段温度546℃,均热段温度1185℃,高温段时间180min,加热总时间345min。开轧温度为1045℃,终轧温度为940℃。圆钢离线堆冷温度为425℃。
[0074]
(5)热处理
[0075]
对钢材毛坯样进行884℃油淬,保温40min,柴油冷却;淬火后在250℃回火,保温150min,再进行空冷。
[0076]
实施例2
[0077]
(1)钢水冶炼
[0078]
采用容量130吨转炉,终点c:0.12%,终点出钢下渣控制良好,终点p:0.010。
[0079]
(2)精炼
[0080]
使用容量130吨的lf炉,到站钢水温度1513℃,出站温度1603℃;lf精炼时间112min。使用容量130吨rh炉进行rh精炼,rh精炼温度控制为1594℃,高真空时间为18min。
[0081]
(3)连铸
[0082]
过热度27℃,拉速0.9m/min;结晶器电磁搅拌100a/2.5hz,末端电磁搅拌600a/4hz。铸坯为280mm大方坯。二次冷却中各区配水为:一区30%,二区34%,三区22%,四区14%。冷却至625℃进入缓冷坑。
[0083]
(4)轧制
[0084]
预热段温度620℃,均热段温度1188℃,高温段时间165min,加热总时间330min。开轧温度为1035℃,终轧温度为918℃。圆钢离线堆冷温度为410℃。
[0085]
(5)热处理
[0086]
对钢材毛坯样进行885℃油淬,保温40min,柴油冷却;淬火后在250℃回火,保温150min,再进行空冷。
[0087]
实施例3
[0088]
(1)钢水冶炼
[0089]
采用容量130吨转炉,终点c≥0.09~0.12%,终点出钢下渣控制良好,终点p:0.014%。
[0090]
(2)精炼
[0091]
使用容量130吨的lf炉,到站钢水温度1577℃,出站温度1597℃;lf精炼时间97min。使用容量130吨rh炉进行rh精炼,rh精炼温度控制为1590℃,高真空时间为21min。
[0092]
(3)连铸
[0093]
过热度30℃,拉速0.9m/min;结晶器电磁搅拌100a/2.5hz,末端电磁搅拌600a/4hz。铸坯为280mm大方坯。二次冷却中各区配水为:一区30%,二区36%,三区21%,四区13%。冷却至618℃进入缓冷坑。
[0094]
(4)轧制
[0095]
预热段温度520℃,均热段温度1165℃,高温段时间195min,加热总时间375min。开轧温度为1030℃,终轧温度为934℃。圆钢离线堆冷温度为405℃。
[0096]
(5)热处理
[0097]
对钢材毛坯样进行887℃油淬,保温40min,柴油冷却;淬火后在250℃回火,保温150min,再进行空冷。
[0098]
对比例1
[0099]
采用现有转炉炼钢工艺,采用vd炉精炼。在轧制步骤中,加热温度为1120℃,保温时间3.1h,开轧温度为1083℃,终轧温度为943℃,空冷至417℃后入缓冷坑缓冷。
[0100]
对比例2
[0101]
与对比例1的区别在于,在轧制步骤中,加热温度为1210℃,保温时间3h,开轧温度为1097℃,终轧温度为943℃,空冷至434℃后入缓冷坑缓冷。
[0102]
对比例3
[0103]
与对比例1的区别在于,在轧制步骤中,加热温度为1180℃,保温时间3.3h,开轧温
度为1060℃,终轧温度为920℃,空冷至446℃后入缓冷坑缓冷。
[0104]
对比例4
[0105]
与上述对比例1的区别在于,精炼采用rh精炼工序。连铸步骤的二次冷却中各区配水为:一区25%,二区40%,三区19%,四区16%。在轧制步骤中,空冷至165℃下线堆冷。热处理步骤中,对钢材毛坯样进行900℃油淬,保温40min,柴油冷却;淬火后在200℃回火,保温150min,再进行空冷。性能结果伸长率和面缩率偏低不合格。
[0106]
实施例1~3以及对比例1~4的力学性能测试结果如表3所示。其中,拉伸性能和冲击性能的测试均保留了两个测试结果。
[0107]
表3:
[0108][0109]
实施例1~3的低倍、高倍性能情况如表4所示。
[0110]
表4:
[0111][0112]
通过上述测试结果比较可知,相较于现有的钎具钢及其工艺,本技术实施例提供的钎具钢为低成本si-mn-mo系钎具钢,无需添加nb、v贵重金属,而通过添加廉价的al(0.010%~0.025%),能够获得较低的成本。与对比例4比较可知,通过对二次冷却中各区配水量的优化及热处理工艺的优化,使得本技术提供的工艺所制备的钎具钢具有更高的屈服强度,更高的断后伸长率和断面收缩率。总体来看,结合本技术实施例提供的制备工艺,能够制得具有较佳强度、韧性的钎具钢。并且,本技术实施例制备得到的钎具钢偏析程度
低,夹杂少,晶粒细化,能够较好地满足钎具的使用需求。
[0113]
以上所述仅为本技术的优选实施例而已,并不用于限制本技术,对于本领域的技术人员来说,本技术可以有各种更改和变化。凡在本技术的精神和原则之内,所作的任何修改、等同替换、改进等,均应包含在本技术的保护范围之内。
再多了解一些
本文用于创业者技术爱好者查询,仅供学习研究,如用于商业用途,请联系技术所有人。