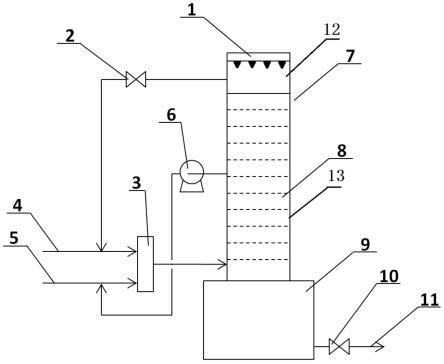
1.本发明涉及重整催化剂领域,尤其涉及一种连续重整催化剂的制备方法。
背景技术:
2.催化重整是石油加工的重要生产工艺之一,其主要目的是生产高辛烷值汽油、btx芳烃及廉价的氢气。随着汽油质量升级、加氢技术快速发展以及炼化一体化项目的加快进行,催化重整在炼油化工行业中的地位越来越重要。目前,催化重整工艺的发展趋势是向热力学有利的方向发展。但是操作苛刻度的提高使催化剂积碳速率加快。为了保持催化剂的活性,必须缩短催化剂的再生周期,频繁的再生导致催化剂载体的微孔结构改变,比表面积下降,pt晶粒烧结,cl流失。因此,高苛刻度连续重整工艺条件对催化剂的催化性能(活性、选择性、稳定性)及物理性能(水热稳定性、持氯能力、强度)提出了新的要求。
3.针对连续重整工艺技术进步,现有技术通过对催化剂进行改性来提高催化剂性能。
4.cn1535176a公开了一种含pt、sn的多金属重整催化剂,该催化剂用于石脑油催化重整反应,具有较好的活性和选择性,且积碳速率较低。
5.cn1384175a公开了一种稀土(ce和eu)改性的铂锡重整催化剂,该催化剂具有好的活性稳定性和高的选择性(液收增加、抗积碳能力增强)。
6.cn105561991a公开了一种pt-sn双金属催化剂,催化剂外壳区域(边缘向中心方向厚度为0.25mm的区域)平均sn浓度为中心区域的1.3~1.8倍。锡在催化剂外壳区域的富集,抑制了催化剂外壳区域的积碳速率,并提高到了催化剂的活性和芳烃产率。
7.cn103316675公开了一种pt-sn重整催化剂的制备方法,该方法用干燥的含sn氧化铝载体吸附适量水(孔体积的3~30%),用含乙酰丙酮铂的c7~c9烷烃浸渍,干燥、水氯活化、还原。该法解决了pt在小孔的负载可能由于传质受限、积碳、烧结等原因而无法发挥催化功能的问题,利用水的毛细管凝聚作用先占据小孔,在用乙酰丙酮铂实现铂在较大孔中的定向负载,(乙酰丙酮铂不溶于水,之前吸附的水被烷烃封堵在小孔内)具有较高的活性、选择性和稳定性,为进一步降低铂的用量提供的可能。
8.us6059960公开了一种含稀土的pt-sn多金属重整催化剂,其引入的镧系组元为eu、yb、sm或者eu和yb的混合物,并且在催化剂中50%以上的镧系金属以euo存在。当催化剂pt-sn-eu组分时,只有eu/pt原子比为1.3~2.0时,相对活性和选择性均较好,比值小于1.3时,催化剂的选择性降低,比值大于2.0时,催化活性明显下降。
9.cn1234455公开了一种含pt、sn的多金属重整催化剂及其制备与应用,其引入的镧系组元为eu和ce。该催化剂用于石脑油催化重整反应,具有较高的活性和选择性,积碳速率较低,寿命长。
10.cn1384175公开了一种pt-sn-稀土的连续重整催化剂及其制备方法,该催化剂用混合稀土及ib族元素改性提高催化剂的选择性和抗积碳能力,增加水热稳定性及机械强度,能够满足连续重整工艺频繁再生的要求。
技术实现要素:
11.基于以上所述,本发明的目的是提供一种连续重整催化剂的制备方法,该制备方法制备连续重整催化剂的氧化铝载体时,采用拟均相成型的方法,所得催化剂进行重整反应,得到的反应产物液收增加,同时能够降低积碳,延长催化剂寿命。同时,该催化剂具有较高的活性,较高的选择性和良好的活性稳定性,较好的水热稳定性及机械强度。
12.为此,本发明提供一种连续重整催化剂的制备方法,该连续重整催化剂的氧化铝载体采用拟均相成型方法制备,包括以下步骤:
13.将氧化铝溶胶滴入与所述拟均相成型方法配套的成型装置,在所述成型装置的拟均相有相中氧化铝溶胶成型为球形颗粒,所述球形颗粒浸渍活性组分后得到连续重整催化剂;
14.其中,所述拟均相有相由氨气和油相混合形成。
15.本发明所述的连续重整催化剂的制备方法,其中优选的是,所述成型装置包括依次连接的滴球盘、成球柱和干燥器,所述成球柱内由储存氨气的上层和储存拟均相有机相的下层组成,所述上层与氨气管线连接,所述下层与预混装置连接。
16.本发明所述的连续重整催化剂的制备方法,其中优选的是,所述预混装置包括氨气管线、油相管线和分散器,所述氨气管线和所述油相管线通过微量调节器并联至所述分散器,所述分散器与所述下层连接,所述氨气和拟均相有机相通过球阀和泵在所述分散器和所述成球柱之间循环。
17.本发明所述的连续重整催化剂的制备方法,其中优选的是,所述油相选自庚烷、辛烷、壬烷、汽油、煤油、石蜡油、矿物油、石油醚中的至少一种。
18.本发明所述的连续重整催化剂的制备方法,其中优选的是,所述氧化铝载体选自γ-al2o3、η-al2o3、θ-al2o3中的至少一种,进一步优选γ-al2o3或η-al2o3,更进一步优选γ-al2o3;所述氧化铝载体为球形,且其直径为1~3mm,进一步优选1.4~2.0mm,球形度大于0.90;所述氧化铝载体的表观堆密度为0.5~0.9g/cm3,平均孔径为4~12nm,进一步优选1.4~2.0mm,孔体积为0.3~1.4ml/g,比表面积为120~1400m2/g。
19.本发明所述的连续重整催化剂的制备方法,其中优选的是,所述氧化铝溶胶是由水合氧化铝与去离子水混合得到的氧化铝悬浮液经过搅拌后加入酸溶液胶溶得到的,所述氧化铝悬浮液中固含量以氧化铝计为10~30wt%。
20.本发明所述的连续重整催化剂的制备方法,其中优选的是,所述酸溶液为硝酸、盐酸、甲酸、乙酸和高氯酸中的至少一种,进一步优选硝酸和/或盐酸;所述酸溶液的质量浓度为5~50wt%;所述酸溶液的用量满足所述氧化铝溶胶中的h
/al
3
摩尔比为0.04~0.1。
21.本发明所述的连续重整催化剂的制备方法,其中优选的是,所述水合氧化铝为薄水铝石、拟薄水铝石或两者的混合物。进一步优选醇铝水解法制备的具有大比表面积、大孔体积的高纯氧化铝粉末。
22.本发明所述的连续重整催化剂的制备方法,其中优选的是,所述成型还包括将球形颗粒取出所述成型装置后进行老化、干燥和焙烧,所述老化的条件为:在氨水溶液中,氨水溶液的浓度为6~10wt%,老化时间1~12h,老化温度20~40℃;所述干燥的温度为60~120℃,时间为6~24h;所述焙烧的温度为400~1100℃,时间为2~12h。
23.本发明所述的连续重整催化剂的制备方法,其中优选的是,均以元素计,所述连续
重整催化剂由0.1~2.0wt%的ⅳa族金属组分,0.01~1.0wt%的
ⅷ
族金属组分,优选0.01~0.5wt%的
ⅷ
族金属组分,0.01~3.0wt%稀土组分和0.2~3.0wt%卤素组分和余量氧化铝载体组成。
24.本发明所述的连续重整催化剂的制备方法,其中优选的是,所述ⅳa族金属组分选自ge或sn,优选sn;所述
ⅷ
族金属组分选自pt、pd、ru、rh、ir、os中的至少一种,优选pt;所述稀土组分选自镧系稀土中的至少一种,优选la、ce、pr、nd、pm和eu中的至少一种,更优选ce;所述卤素组分为cl。
25.具体的,ⅳa族金属组分在催化剂中的存在形态可为金属元素,也可为化合物,如:氧化物、硫化物、卤化物、氧卤化物等,也可以与载体和催化剂中的其他组分以物理或化学的结合方式存在。成品催化剂中,ⅳa族金属优选以氧化态形式存在。
26.本发明所述的连续重整催化剂的制备方法,其中优选的是,所述浸渍活性组分的过程为:将ⅳa族金属组分、稀土组分分别或同时引入氧化铝载体,再引入
ⅷ
族金属组分,每引入一次活性组分均需干燥、焙烧;然后进行水热活化、水氯老化和还原;优选的,所述水热活化、水氯老化和还原包括以下步骤:(1)催化剂在流动的空气中焙烧,流动的空气中h2o:cl2:hcl的摩尔比为20~80:1:1,焙烧温度为370~700℃,焙烧时间为2~4h;(2)催化剂在干燥氢气氛围下还原,干燥氢气中水含量小于20ppm,还原温度为400~600℃,还原时间为1~2h。
27.本发明所述的连续重整催化剂的制备方法,其中优选的是,所述干燥温度为25~300℃,所述焙烧温度为370~700℃,进一步优选550~650℃,所述焙烧时间为0.5~10h,所述焙烧过程在含氧气氛中进行,进一步优选含氧气氛为空气。
28.本发明所述的连续重整催化剂的制备方法,其中优选的是,所述浸渍活性组分采用共浸渍法或连续分浸渍法,进一步优选的,所述浸渍活性组分采用共浸渍法或连续分浸渍法引入
ⅷ
族金属。
29.本发明所述的连续重整催化剂的制备方法,其中优选的是,所述氧化铝溶胶中含有胶体稳定剂,进一步优选的,所述胶体稳定剂为尿素。
30.本发明所述的连续重整催化剂的制备方法,其中优选的是,将ⅳa族金属、稀土分别或同时引入氧化铝载体,再引入pt,引入的pt采用共浸渍法。
31.具体的,在催化剂制备中,首先应引入的元素为ⅳa族金属、稀土元素。它们的引入顺序可以是任意的,可先将ⅳa族金属引入载体,再引入稀土,也可以是相反,还可以是同时引入ⅳa族金属和稀土。引入ⅳa族金属及稀土操作后,最好进行焙烧,以确保引入组元与载体牢固结合。
32.本发明所述的连续重整催化剂的制备方法,其中优选的是,ⅳa族金属组分可在球形氧化铝载体成型时引入,也可以在球形氧化铝载体成型后通过浸渍法引入。适宜的ⅳa族金属可溶性化合物为其氧化物、氯化物、硝酸盐或醇盐,如:氯化亚锡、四氯化锡;二氧化锗、锗的四乙醇盐、四氯化锗;硝酸铅、乙酸铅或氯酸铅。优化四氧化锡、四氯化锗或氯酸铅。
33.本发明所述的连续重整催化剂的制备方法,其中优选的是,稀土可在球形氧化铝载体成型时引入,也可以再球形氧化铝载体成型后通过浸渍法引入。稀土可以与ⅳa族金属组分同时引入载体,也可以再引入ⅳa族金属组分之前或者之后引入。所用的稀土选自其金属盐、化合物或配合物,如硝酸盐、碳酸盐、硫酸盐、氯化物、氟化物、氢氧化物、氧化物。
34.本发明所述的连续重整催化剂的制备方法,其中优选的是,催化剂中的pt可采用沉淀、离子交换或浸渍等方法引入载体。优选浸渍法向在途引入pt金属化合物。可采用pt金属的水溶性化合物或配合物的非限制性例子有:氯铂酸、溴铂酸、三氯化铂、四氯化铂水合物、硝酸四氨化铂、二硝基二氨化铂。优选pt的含氯化合物,如氯铂酸的水合物。为使pt在载体中分布均匀并向载体中引入卤素,可在浸渍液中加入家兔含卤素的无机酸或有机酸,如:盐酸、氢氟酸、一氯乙酸、三氯乙酸等。此外,再载体中浸渍pt金属之后最好进行焙烧,以减少pt金属在其他的浸渍过程中被洗脱的危险。
35.具体的,上述引入金属组分的各步操作,在引入金属元素后都要进行干燥、焙烧。干燥温度为25~300℃,焙烧温度为370~700℃,优选550~650℃,焙烧时间优选0.5~10h。所述的焙烧过程在含氧气氛中进行,优选的含氧气氛为空气。
36.为保证催化剂具有适宜的酸性并使金属组元更好分散,在其制备中还包括卤素调节步骤。用于引入卤素的化合物优选cl2、hcl或能分解出氯的有机化合物,如二氯甲烷、三氯甲烷、四氯化碳。卤素调节的温度为370~700℃,时间为0.5~5.0h或更长。在此过程中,应有适量的水,水:cl2:hcl=(20~80):1:1(摩尔比)。卤素调节步骤可与催化剂焙烧同时进行,也可在焙烧之前或之后进行。成品催化剂中卤素的含量优选0.2~3.0wt%。
37.催化剂活化完成后进行催化剂的还原,还原步骤需要在基本无水的环境中进行,还原气中的水含量要小于20ppm,优选的还原气为氢气,也可采用co等其他的还原性气体对催化剂进行还原。还原温度为400~600℃,优选的还原时间为0.5~10.0h。
38.本发明催化剂适用于石脑油的连续重整过程,生产高辛烷值汽油调和组分或芳烃。所述的石脑油富含环烷烃和链烷烃,选自按astm d-86方法测定,初馏点为40~80℃、终馏点为160~220℃的全馏程汽油,馏程为60~150℃的轻石脑油,或馏程为100~200℃的重石脑油。适用的重整原料为直馏汽油、加氢裂化重石脑油、热裂化或催化裂化的汽油馏分以及费托合成汽油。
39.本发明催化剂用于催化重整反应过程所采用的绝对压力为100kpa~7mpa,优选0.35~2.5mpa;反应温度为315~600℃,优选425~565℃;氢气/烃摩尔比为1~20,优选2~10;液时空速(lhsv)为0.1~5h-1
,优选1~3h-1
。重整过程在基本无水的条件下进行。原料在进入转化区时含水量应小于50ppm,最好小于20ppm。重整原料中的水可通过常规的吸附剂,如分子筛进行干燥,也可以通过分馏装置进行适当的汽提操作来调节,也可将吸附干燥和汽提干燥结合,来排除原料中的水。
40.本发明的有益效果如下:
41.(1)本发明方法制备的载体在球形度、磨耗指数上优于油氨柱法,在孔径、堆密度和比表面积与油氨柱法相似。
42.(2)本发明方法制备的催化剂具有较高的活性,较高的选择性,良好的活性稳定性,能够提高液收,降低积碳。
43.(3)与采用油氨方法制备载体以及催化剂g、h和i相比,本发明催化剂采用分散器拟均相混合的方法制备催化剂,可以显著提高催化剂的水热稳定性,从而满足频繁再生对催化剂稳定性的要求,实现连续重整装置长周期稳定运行。
附图说明
44.图1为本发明催化剂的球型载体成型装置的结构示意图。
45.图中,1、滴球盘,2、球阀,3、分散器,4氨气管线,5油相管线,6、泵,7、成球柱,8、拟均相有机相,9、干燥器,10、球阀,11、排污管线,12、上层,13,下层。
具体实施方式
46.以下对本发明的实施例作详细说明:本实施例在以本发明技术方案为前提下进行实施,给出了详细的实施方式和过程,但本发明的保护范围不限于下述的实施例,下列实施例中未注明具体条件的实验方法,通常按照常规条件。
47.本文中披露的所有范围都包含端点并且是可独立结合的。本文中所披露的范围的端点和任何值都不限于该精确的范围或值,这些范围或值应当理解为包含接近这些范围或值的值。
48.测试方法
49.表1中各参数测试方法如下:
50.(1)、球形度a:随机取10g载体,用球形度测量仪拍摄载体自有落体时没粒载体的投影,测量其投影周长p和投影面积a,根据公式(1)分别计算每粒载体的球形度(sp),根据公式(2)计算出载体的球形度,n为测试样品中总得颗粒度。
[0051][0052][0053]
(2)、磨损指数b:取约100g球形载体,在马弗炉中300℃焙烧2h,放入干燥器冷却至室温。取25
±
0.05g样品放入磨耗仪磨管中,转动1h,转速25转/min。测试结束,样品过1毫米筛,称重。
[0054]
磨损指数b:式中p1为测试前样品质量,p2为测试后样品质量。
[0055]
表2中各参数测试方法如下:
[0056]
(1)、比表面积损失率a=(s
1-s2)/s1×
100%
[0057]
其中,s1为老化前催化剂的比表面积;s2为老化后催化剂的比表面积。
[0058]
(2)、压碎强度b:随机取50粒催化剂,逐一在智能颗粒强度仪上测试,取平均值。测试时加力速度为2n/s直至颗粒破碎。
[0059]
参见图1所示,图1为本发明催化剂的球型载体成型装置的结构示意图。本发明的氧化铝载体通过图1的成型装置进行成型,将制备好的氧化铝溶胶倒入成型装置中,形成球形凝胶颗粒,取出后在氨水溶液中老化一段时间,经干燥、焙烧后得到球形氧化铝载体。
[0060]
该载体成型装置包括由上至下依次连接的滴球盘1、成球柱7和干燥器9。干燥器9的底部的排污口(未图示)连接有排污管线11,成球柱7内由储存氨气的上层12和储存拟均相有机相8的下层13组成,成球柱7与预混装置连接。预混装置包括氨气管线4、油相管线5和
分散器3,氨气管线4和油相管线5通过微量调节器(未图示)并联至分散器3。成球柱7的上层12与氨气管线4连接,下层13与分散器3连接,氨气和拟均相有机相(氨气和油相的拟均相状态)通过球阀2和泵6在分散器3和成球柱7之间循环。生产设备形成闭环循环,密封良好,无液体或气体泄漏,环保效果良好。
[0061]
在一些实施例中,分散器3的材质优选为陶瓷、金属或膜材料。
[0062]
在一些实施例中,泵6优选为隔膜泵、泥浆泵、柱塞泵或水泵。
[0063]
在一些实施例中,排污管线11上优选设有球阀10。
[0064]
本发明将制备好的氧化铝溶胶由滴球盘1倒入成球柱7的过程即滴球过程,滴球过程为连续操作。首先,氧化铝溶胶通过滴球盘1形成液滴,滴球速度为1~2kg/h(以拟薄水铝石质量计),液滴通过重力作用进入成球柱内的不溶于水的拟均相有机相中,在表面张力的作用下收缩成球,同时与拟均相有机相中溶解的nh3发生中和反应使液滴固化为凝胶小球。
[0065]
滴球过程中,拟均相有机相通过泵6循环至分散器中与nh3进行再混,循环比为0~0.2(回流量/成型柱中拟均相有机相的摩尔量),循环量视滴球速度、酸铝比、不同溶剂对nh3的溶解度而定。打开氨气管线4以补充系统损失的nh3,氨气流量为20~50l/h。
[0066]
成型后的凝胶小球取出后,放置在氨水溶液中老化,氨水浓度优选6~10wt%,老化时间优选1~12h。
[0067]
所述成型过程的干燥温度为60~120℃,时间6~24h;所述焙烧温度为400~1100℃,时间2~12h,焙烧介质可以是干空气,也可以是含微量水(5wt%以下)的湿空气。
[0068]
实施例1
[0069]
制备载体
[0070]
(1)取拟薄水铝石粉体1kg(氧化铝干基含量75wt%),加入2.35kg去离子水室温搅拌30min浆化,加入173g,37.5wt%的硝酸溶液,2.25g,0.3wt%的氯化亚锡的盐酸溶液(60g,h
/al
3
(干基)质量比0.08),酸化2h使之胶溶,在溶胶中加入225g尿素作为胶体稳定剂,得到氧化铝固含量为20wt%,h
/al
3
摩尔比为0.07的氧化铝溶胶。
[0071]
采用本发明图1所示的新型催化剂球型载体成型装置,选用正庚烷作为成型所需要的有机溶剂,将氨气和正庚烷的输入流量分别为15l/min和800g/min,在分散器进行充分混合后形成拟均相有机相作为溶剂进入成型柱7中,待成型柱中的溶剂填充至80~90%后开始进行氧化铝溶胶滴球。滴球速度为1kg/h(以拟薄水铝石粉质量计),滴球过程中打开阀2和泵6使成型柱中的上层氨气和下层正庚烷循环至分散器中再混,同时打开氨气输入管线以补充系统中损失的氨。正庚烷循环比(回流量/成型柱中有机相的量)为0.08,氨气输入流量为23l/h。滴球完成后在干燥器9中得到成型的凝胶颗粒。将成型后的凝胶颗粒取出后置于氨水中老化10h,80℃下干燥12h,650℃下焙烧4h,得到氧化铝固体小球。控制成型装置的滴球针孔的孔直径,得到1号载体的孔径为8.5nm,其性质详见表1所示。
[0072]
实施例2
[0073]
与实施例1的区别在于,控制成型装置的滴球针孔的孔直径,得到2号载体的孔径为7.0nm,其性质详见表1所示。
[0074]
对比例1
[0075]
取1kg拟薄水铝石和适量去离子水,室温搅拌浆化0.5h。然后加入12ml,30wt%硝酸,2.25g,0.3wt%的氯化亚锡的盐酸溶液(60g,h
/al
3
(干基)质量比0.08),,酸化2h。然后
在油氨柱内滴球成型,其中油柱为航空煤油,湿球在氨水柱中固化2h,然后过滤,用去离子水洗涤三次,60℃干燥6h,120℃干燥2h,在流动空气中650℃焙烧4h。所制备3号载体的性质见表1所示。
[0076]
实施例3
[0077]
制备载体
[0078]
按照实施例1的方法制备氧化铝载体,不同的是加入预定量氯化亚锡的盐酸溶液后,还加入预定量氯化铈溶液,最终得到氧化铝固含量为20wt%,h
/al
3
摩尔比为0.07的氧化铝溶胶。
[0079]
采用本发明图1所示的新型催化剂球型载体成型装置,选用正庚烷作为成型所需要的有机溶剂,将氨气和正庚烷的输入流量分别为15l/min和800g/min,在分散器进行充分混合后形成拟均相有机相作为溶剂进入成型柱7中,待成型柱中的溶剂填充至80~90%后开始进行氧化铝溶胶滴球。滴球速度为1kg/h(以拟薄水铝石粉质量计),滴球过程中打开阀2和泵6使成型柱中的上层氨气和下层正庚烷循环至分散器中再混,同时打开氨气输入管线以补充系统中损失的氨。正庚烷循环比(回流量/成型柱中有机相的量)为0.08,氨气输入流量为23l/h。滴球完成后在干燥器9中得到成型的凝胶颗粒。将成型后的凝胶颗粒取出后置于氨水中老化10h,80℃下干燥12h,650℃下焙烧4h,得到氧化铝固体小球,即4号载体。控制成型装置的滴球针孔的孔直径,得到4号载体的孔径为7.0nm,其性质见表1所示。
[0080]
实施例4
[0081]
与实施例3的区别在于,控制成型装置的滴球针孔的孔直径,得到5号载体的孔径为8.5nm,其性质详见表1所示。
[0082]
对比例2
[0083]
按照对比例1方法制备球形氧化铝载体。不同的是加入2.25g,0.3wt%的氯化亚锡的盐酸溶液(60g,h
/al
3
(干基)质量比0.08),,及0.75g,0.1wt%的氯化铈溶液,酸化2h。然后在油氨柱内滴球成型,其中油柱为航空煤油,湿球在氨水柱中固化2h,然后过滤,用去离子水洗涤三次,60℃干燥6h,120℃干燥2h,在流动空气中650℃焙烧4h。所制备6号载体的性质见表1所示。
[0084]
表1载体性质
[0085][0086]
表1中,1号和2号载体由实施例1和2采用本发明的成型方法和装置制备,3号载体
由对比例1按照油氨柱方法制备载体。由比较结果可知,本发明方法制备的载体在球形度、磨耗指数上优于油氨柱法,在孔径、堆密度和比表面积与油氨柱法相似。
[0087]
表1中,4号和5号载体由实施例3和4采用本发明的成型方法和装置制备,6号载体由对比例2按照油氨柱方法制备载体。由比较结果可知,本发明方法制备的载体在球形度、磨耗指数上优于油氨柱法,在孔径、堆密度和比表面积与油氨柱法相似。
[0088]
实施例1和2与实施例3和4的区别在于,用装置制备载体时,实施例1和2只加预定量的含氯化亚锡的盐酸溶液,实施例3和4在加入预定量的含氯化亚锡的盐酸溶液后还加入了预定量氯化铈溶液。
[0089]
实施例5
[0090]
取100g 1号载体,用硝酸铈溶液浸渍,浸渍液中ce含量相对于干基氧化铝质量为0.20%,浸渍液与载体的液/固比为1.1,浸渍0.5h,60℃蒸干浸渍液,120℃干燥4h,然后在650℃焙烧4h,得到含sn和ce载体。
[0091]
用按预定量配制的氯铂酸的盐酸溶液浸渍,浸渍液中pt含量和盐酸含量相对干基氧化铝质量分别为0.3%和1.8%,浸渍液与载体的液/固比为1.5,浸渍时间4h,在真空条件下70℃将多余的浸渍液蒸干后,120℃干燥12h。实验后的催化剂在480℃,h2o:cl2:hcl的摩尔比=60:1:1条件下,于空气中活化处理6h,在480℃用纯氢还原后制得催化剂a,催化剂a的组成见表2。催化剂中pt、sn、ce的含量用xrf法测定,氯含量用电极法测定。
[0092]
实施例6
[0093]
按实施例5的方法制备催化剂b,不同的是浸渍液中ce含量相对干基氧化铝质量为0.45%,氢气还原后得到的催化剂b组成见表2。
[0094]
对比例3
[0095]
取100g 3号载体,按实施例5的方法制备催化剂c,不同的是浸渍液中ce含量相对干基氧化铝质量为0.45%,氢气还原后得到的催化剂c组成见表2。
[0096]
实施例7
[0097]
取100g 2号载体,用预定量硝酸铈溶液和氯铂酸的盐酸溶液共同浸渍向载体引入ce和pt,浸渍液中ce和pt含量相对于干基氧化铝质量为0.3%和0.3%,浸渍液与载体的液/固比为1.6,浸渍时间4h,在真空条件下70℃将多余的浸渍液蒸干后,120℃干燥12h。实验后的催化剂在560℃,h2o:cl2:hcl的摩尔比=30:1:1条件下,于空气中活化处理6h,在560℃用纯氢还原后制得催化剂d,d的组成见表2。
[0098]
实施例8
[0099]
按实施例7的方法制备催化剂e,不同的是浸渍液中ce和pt含量相对干基氧化铝质量为0.45%和0.3%,氢气还原后得到的催化剂e组成见表2。
[0100]
对比例4
[0101]
取100g 3号载体,按实施例7的方法制备催化剂f,不同的是浸渍液中ce和pt含量相对干基氧化铝质量为0.45%和0.3%,氢气还原后得到的催化剂f组成见表2。
[0102]
实施例9
[0103]
取100g 4号载体,用预定量硝酸铈溶液浸渍,浸渍液中ce含量相对于干基氧化铝质量为0.20%,浸渍液与载体的液/固比为1,浸渍0.5h,60℃蒸干浸渍液,120℃干燥4h,然后在650℃焙烧4h,得到含sn和ce载体。
[0104]
用按预定量配制的氯铂酸的盐酸溶液浸渍,浸渍液中pt含量和盐酸含量相对干基氧化铝质量分别为0.3%和1.8%,浸渍液与载体的液/固比为1.5,浸渍时间4h,在真空条件下70℃将多余的浸渍液蒸干后,120℃干燥12h。干燥后的催化剂前体在520℃,h2o:cl2:hcl的摩尔比=50:1:1条件下,于空气中活化处理6h,在480℃用纯氢还原后制得催化剂g,g的组成见表2。
[0105]
实施例10
[0106]
按实施例7的方法制备催化剂h,不同的是取100g 5号载体,浸渍液中ce含量相对干基氧化铝质量为0.35%,氢气还原后得到的催化剂h组成见表2。
[0107]
对比例5
[0108]
取100g 6号载体,按实施例7的方法制备催化剂i,不同的是浸渍液中ce含量相对干基氧化铝质量为0.35%,氢气还原后得到的催化剂i组成见表2。
[0109]
将本发明实施例及对比例中制备的催化剂在在常压550℃,含水10%的空气气氛下老化处理210小时,记录老化前及老化后催化剂的比表面积。
[0110]
表2
[0111][0112][0113]
从表2数据可以看出,与采用油氨方法制备载体的对比催化剂g、h和i相比,本发明催化剂采用分散器拟均相混合的方法制备催化剂,可以显著提高催化剂的水热稳定性,从而满足频繁再生对催化剂稳定性的要求,实现连续重整装置长周期稳定运行。实施例9
[0114]
本实施例对本发明催化剂的选择性进行评价。
[0115]
在100ml装置上中,装入50g催化剂,以80~165℃的直馏石脑油为原料,原料油的性质见表3。评价条件为:反应压力0.34mpa,反应温度为500℃,液体进料体积空速2h-,氢油体积比1000:1。评价结果见表4。
[0116]
表3原料油性质
[0117][0118]
表4
[0119][0120][0121]
由表4可知,在催化剂ce含量相同时,本发明催化剂b、e和h与油氨柱法成型催化剂c、f和i相比,反应产物c
5
收率和芳产均提高,表明本发明催化剂具有更优异的选择性。
[0122]
当然,本发明还可有其它多种实施例,在不背离本发明精神及其实质的情况下,熟悉本领域的技术人员可根据本发明作出各种相应的改变和变形,但这些相应的改变和变形都应属于本发明的保护范围。
再多了解一些
本文用于创业者技术爱好者查询,仅供学习研究,如用于商业用途,请联系技术所有人。