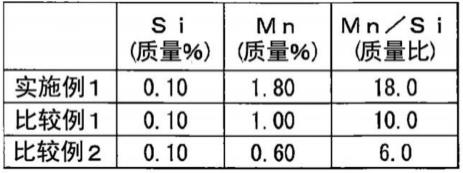
1.本发明涉及换热器用铝合金挤出多孔管及其制造方法。
背景技术:
2.蒸发器、冷凝器等汽车用铝合金制换热器中,作为流体的通路材料,使用具有由多个分区划分的多个中空部的铝合金挤出多孔管。近年来,为了汽车的轻量化,正在进行对汽车上搭载的换热器的轻量化,要求将换热器用铝合金材料进一步薄壁化。
3.为了薄壁化,需要使坯料的强度提高。进而,在汽车用换热器中,为了接合各构件而进行硬钎焊,因此不仅是坯料的强度,硬钎焊后也需要具有高强度。
4.另一方面,铝合金制挤出多孔管中,由于挤出比(挤出容器的截面积/挤出材料的截面积)会达到几百~几千,因此若仅单纯地使铝合金制挤出多孔管的强度提高,则挤出时的压力会过度上升、材料制造的难易度会增加,生产率会大幅降低。因此,寻求不仅是硬钎焊后的强度提高、同时也使挤出性提高的材料。
5.为了得到高强度铝合金材料,通常有效的是添加si、fe、cu、mn、mg等合金元素。但是,对于mg,在目前铝合金制换热器的组装中,进行作为硬钎焊法的主流的使用氟化物系助焊剂的非活性气体气氛硬钎焊时,氟化物系助焊剂会与材料中的mg反应,助焊剂的活性度会降低,硬钎焊性会降低,因此不优选积极地进行添加。进而,mg会提高挤出时的压力,因此还有制造性显著降低的问题。对于cu,根据换热器的工作环境,材料中含有cu时,有晶间腐蚀敏感性增大的担忧。
6.基于上述理由,尝试了通过在挤出多孔管中添加si、fe、mn来提高强度的操作。例如,专利文献1中,公开了通过同时添加mn、si来使作为挤出管的强度提高的方法。然而,公开的方法仅为成分的调整,涉及具体的制造方法的记载不充分。另外,专利文献2中公开了通过均质化处理来控制添加的mn的固溶/析出状态的方法。另一方面,未记载制造该挤出管时所担忧的生产率的问题。
7.现有技术文献
8.专利文献
9.专利文献1:日本特开2006-316294号公报
10.专利文献2:日本特开2008-121108号公报
技术实现要素:
11.发明要解决的问题
12.上述添加元素之中,mn、si是可以容易地实现高强度化的元素,但用通常的方法以高浓度添加这些元素时,铝的母相中固溶的mn、si会使热过程中的变形阻力增加,挤出性极差。
13.对此,可想到尝试通过进行高温的均质化处理和低温的均质化处理来使母相中的溶质元素的固溶量减少,使变形阻力降低,但对于挤出性而言,难以说得到充分确保。
14.另外,虽然fe对于强度提高具有一定的效果,但铸造时容易形成粗大的alfemn系化合物,这可能成为加快挤出工具的磨损的原因,因此不优选积极地添加。
15.如此,为了制造高强度的挤出多孔管,需要通过mn、si的添加使强度提高,并且使挤出性进一步提高。
16.因此,本发明的目的在于,提供挤出性优异且硬钎焊后具有高强度的换热器用铝合金挤出多孔管及其制造方法。
17.用于解决问题的方案
18.本发明人等在添加有mn、si的挤出多孔管用合金中以进一步改良挤出性为目的反复进行了研究,结果发现:通过限定mn、si的含有范围及两元素的含有比,进而利用适当的均质化处理使微细的almnsi化合物析出,可以降低挤出前的固溶量而使挤出性提高,进而,通过之后在硬钎焊加热时使前述almnsi化合物再次固溶,可以使硬钎焊后的强度提高,从而完成了本发明。
19.即,本发明(1)提供一种换热器用铝合金挤出多孔管,其特征在于,由铝合金形成,所述铝合金含有0.60~1.80质量%的mn和大于0.00质量%且小于0.20质量%的si、余量为al和不可避免的杂质,且mn含量相对于si含量之比(mn/si)为15.0以上,
20.所述换热器用铝合金挤出多孔管在600℃
±
10℃、3分钟的加热试验中的强度变化(加热试验后的铝合金的拉伸强度(a)-加热试验前的铝合金的拉伸强度(b))为-5mpa以上。
21.另外,本发明(2)提供(1)的换热器用铝合金挤出多孔管,其特征在于,还含有0.10质量%以下(包括0.00质量%。)的ti和0.05质量以下(包括0.00质量%。)的cu之中的1种或2种。
22.另外,本发明(3)提供(1)或(2)的换热器用铝合金挤出多孔管,其特征在于,前述加热试验中的强度变化为-5~ 10mpa。
23.另外,本发明(4)提供一种换热器用铝合金挤出多孔管的制造方法,其特征在于,具备:
24.2阶段均质化处理,对于由含有0.60~1.80质量%的mn和大于0.00质量%且小于0.20质量%的si、余量为al和不可避免的杂质的铝合金形成、且mn含量相对于si含量之比(mn/si)为15.0以上的铸锭,进行以550~650℃的加热温度加热2小时以上的第一均质化处理,之后,进行以450~540℃的加热温度加热3小时以上的第二均质化处理,由此使2阶段均质化处理前后的铸锭的电导率变化(第二均质化处理后的铸锭的电导率(c)-第一均质化处理前的铸锭的电导率(d))为20%iacs以上;和
25.热挤出工序,在热挤出时的加热温度与该第二均质化处理的加热温度之差(热挤出时的加热温度-第二均质化处理的加热温度)的绝对值成为50℃以下的加热温度下,对该2阶段均质化处理的处理物进行热挤出加工。
26.另外,本发明(5)提供(4)的换热器用铝合金挤出多孔管的制造方法,其特征在于,前述铸锭的铝合金还含有0.10质量%以下(包括0.00质量%。)的ti和0.05质量以下(包括0.00质量%。)的cu之中的1种或2种。
27.另外,本发明(6)提供(4)或(5)的换热器用铝合金挤出多孔管的制造方法,其特征在于,前述2阶段均质化处理中,在前述第一均质化处理之后,连续地以平均降温速度20~60℃/小时降温至前述第二均质处理的加热温度,连续地实施前述第二均质化处理。
28.另外,本发明(7)提供(4)或(5)的换热器用铝合金挤出多孔管的制造方法,其特征在于,前述2阶段均质化处理中,在前述第一均质化处理之后,先冷却至常温,之后以平均升温速度20~60℃/小时升温至前述第二均质化处理的加热温度,连续地实施前述第二均质化处理。
29.发明的效果
30.通过本发明,可以提供挤出性优异且硬钎焊后具有高强度的换热器用铝合金挤出多孔管及其制造方法。
附图说明
31.图1为实施例及比较例中制作的铝合金挤出多孔管的剖视示意图。
具体实施方式
32.本发明的换热器用铝合金挤出多孔管的特征在于,由铝合金形成,所述铝合含有0.60~1.80质量%的mn和大于0.00质量%且小于0.20质量%的si、余量为al和不可避免的杂质,且mn含量相对于si含量之比(mn/si)为15.0以上,
33.所述换热器用铝合金挤出多孔管在600℃
±
10℃、3分钟的加热试验中的强度变化(加热试验后的铝合金的拉伸强度(a)-加热试验前的铝合金的拉伸强度(b))为-5mpa以上。
34.本发明的换热器用铝合金挤出多孔管由含有0.60~1.80质量%的mn和大于0.00质量%且小于0.20质量%的si、余量为al和不可避免的杂质、且mn含量相对于si含量之比(mn/si)为15.0以上的铝合金形成。换言之,本发明的换热器用铝合金挤出多孔管是如下铝合金的挤出成型体:含有0.60~1.80质量%的mn和大于0.00质量%且小于0.20质量%的si、余量为al和不可避免的杂质,且mn含量相对于si含量之比(mn/si)为15.0以上。
35.本发明的换热器用铝合金挤出多孔管的铝合金含有mn。mn在硬钎焊加热中固溶于母相中,提高强度。铝合金中的mn含量为0.60~1.80质量%,优选为1.00~1.80质量%。通过使铝合金中的mn含量处于上述范围,挤出成型性优异且硬钎焊加热后的强度提高。另一方面,铝合金中的mn含量小于上述范围时,无法实现作为换热器用管所需的强度,另外,大于上述范围时,与强度提高效果相比,会明显地显现出挤出性的降低。
36.本发明的换热器用铝合金挤出多孔管的铝合金含有si。si在硬钎焊加热中固溶于母相中,提高强度。铝合金中的si含量大于0.00质量%且小于0.20质量%,优选为0.05~0.15质量%。通过使铝合金中的si含量处于上述范围,挤出成型性优异且硬钎焊加热后的强度提高。另一方面,铝合金中的si含量小于上述范围时,无法实现作为换热器用管所需的强度,另外,大于上述范围时,与强度提高效果相比,会明显地显现出挤出性的降低。
37.本发明的换热器用铝合金挤出多孔管的铝合金中,铝合金中的mn含量相对于si含量之比(mn/si)为15.0以上,优选为16.0~40.0。在将铝合金中的mn个si的含量限定为上述范围的基础上,通过将mn含量相对于si含量之比(mn/si)设为上述范围并进一步实施后述的2阶段均质化处理,会成为挤出性优异的铝合金。另一方面,铝合金中的mn/si比小于上述范围时,有时无法得到作为换热器的期望的强度。
38.本发明的换热器用铝合金挤出多孔管的铝合金可以含有ti。ti为了使耐腐蚀性进一步提高并适当控制铸造时的组织而添加至铝合金中。铝合金中的ti含量为0.10质量%以
下,优选大于0%且为0.06质量%以下。ti在铝合金中会形成高浓度的区域和低浓度的区域,这些区域在材料的壁厚方向交替地分布为层状,ti的低浓度区域与高浓度区域相比会优先发生腐蚀,因此腐蚀方式呈层状,因此,壁厚方向上的腐蚀的进展被抑制,耐孔蚀性及耐晶界腐蚀性提高。铝合金的ti含量大于上述范围时,铸造时会生成粗大的化合物,有挤出性受损的担忧。
39.本发明的换热器用铝合金挤出多孔管的铝合金可以含有cu。cu具有利用硬钎焊时的热输入而固溶从而提高强度的效果。铝合金中的cu含量为0.05质量%以下。铝合金的cu含量大于上述范围时,在作为汽车用换热器预想的腐蚀环境下使用时,容易发生晶界腐蚀,耐腐蚀性降低。
40.需要说明的是,本发明的换热器用铝合金挤出多孔管的铝合金在不损害本发明的效果的范围内,也可含有0.10质量%以下的b,另外,cr、zn、zr等杂质的含有以总量计若为0.25质量%以下的范围则可以接受。
41.本发明的铝合金挤出多孔管在600℃
±
10℃、3分钟的加热试验中的强度变化(加热试验后的铝合金的拉伸强度(a)-加热试验前的铝合金的拉伸强度(b))为-5mpa以上,优选为-5~ 10mpa,特别优选为-5~ 5mpa。通过使铝合金挤出多孔管的上述加热试验中的强度变化处于上述范围,硬钎焊加热后的管的强度提高,或者不会由于硬钎焊加热导致管的强度过度降低。上述加热试验中的强度变化如下求出:首先,测定加热试验前的管的拉伸强度(a),然后,以600℃
±
10℃加热管3分钟后,测定加热试验后的管的拉伸强度(b),根据得到试验结果,利用公式“加热试验后的铝合金的拉伸强度(a)-加热试验前的铝合金的拉伸强度(b)”计算加热试验中的强度变化。需要说明的是,加热试验中的强度变化为-5mpa以上是指“加热试验后的铝合金的拉伸强度(a)-加热试验前的铝合金的拉伸强度(b)”的值》-5mp,是指(i)拉伸强度(a)与拉伸强度(b)相同、(ii)拉伸强度(a)比拉伸强度(b)大、以及(iii)拉伸强度(a)比拉伸强度(b)小但其差的绝对值为5mpa以内,即是指(i)(a)-(b)=0mpa、(ii)(a)-(b)》0mpa、以及(iii)-5mpa《(a)-(b)《0mpa之中的任一者。
42.本发明的铝合金挤出多孔管的mn的含量、si的含量及它们的含量比(mn/si)在本发明规定的范围内,且在600℃
±
10℃、3分钟的加热试验中的强度变化为成为本发明规定的范围内的mn与si的固溶状态及almnsi析出物的析出状态,因此热挤出时的加工性高且硬钎焊加热下强度不降低或强度降低小。
43.本发明的铝合金挤出多孔管利用以下所述的本发明的铝合金挤出多孔管的制造方法适宜地制造。
44.本发明的铝合金挤出多孔管的制造方法的特征在于,具备:
45.2阶段均质化处理,对于由含有0.60~1.80质量%的mn和大于0.00质量%且小于0.20质量%的si、余量为al和不可避免的杂质的铝合金形成、且mn含量相对于si含量之比(mn/si)为15.0以上的铸锭,进行以550~650℃的加热温度加热2小时以上的第一均质化处理,之后,进行以450~540℃的加热温度加热的3小时以上第二均质化处理,由此使2阶段均质化处理前后的铸锭的电导率变化(第二均质化处理后的铸锭的电导率(c)-第一均质化处理前的铸锭的电导率(d))为20%iacs以上;和
46.热挤出工序,在热挤出时的加热温度与该第二均质化处理的加热温度之差(热挤出时的加热温度-第二均质化处理的加热温度)的绝对值成为50℃以下的加热温度下,对该
2阶段均质化处理的处理物进行热挤出加工。
47.本发明的铝合金挤出多孔管的制造方法至少具备:铸造工序、均质化处理、和热轧工序。
48.本发明的铝合金挤出多孔管的制造方法的铸造工序为熔解前述组成的铝合金,以半连续铸造等通常的方法进行铸造,从而得到挤出用的毛坯的工序。
49.铸锭由铝合金形成,且mn含量相对于si含量之比(mn/si)为15.0以上、优选为16.0~40.0,所述铝合金含有0.60~1.80质量%的mn、优选含有1.00~1.80质量%,含有大于0.00质量%且小于0.20质量%的si、优选含有0.05~0.15质量%,ti含量为0.10质量%以下、优选大于0%且为0.06质量%以下,cu含量为0.05质量%以下,余量为al和不可避免的杂质。
50.本发明的铝合金挤出多孔管的制造方法的2阶段均质化处理是对进行铸造工序得到的铸锭(挤出用毛坯)首先进行第一均质化处理,之后进行第二均质化处理的2阶段的均质化处理。
51.第一均质化处理中,对进行铸造工序得到的铸锭以加热温度550~650℃加热2小时以上。另外,第二均质化处理中,对进行了第一均质化处理的处理物以加热温度450~540℃加热3小时以上。于是,在2阶段均质化处理中,通过进行第一均质化处理及第二均质化处理,使2阶段均质化处理前后的铸锭的电导率变化(第二均质化处理后的铸锭的电导率(c)-第一均质化处理前的铸锭的电导率(d))为20%iacs以上。
52.在第一均质化处理中,将铸造凝固时形成的粗大的结晶物分解,使其粒状化或再固溶。第一均质化处中的加热温度为550~650℃、优选为580~620℃。第一均质化处中的加热温度通过处于上述范围,可以将铸造凝固时形成的粗大的结晶物分解,使其粒状化或再固溶。另一方面,如果第一均质化处理的加热温度小于上述温度,则其效果不充分,另外,虽然加热温度越高其效果越大,但超出上述范围时,会超过固相线温度,有毛坯部分熔融的担忧。第一均质化处理中的加热时间为2小时以上,由于加热时间长会推进反应,因此处理时间优选为10小时以上。但是,如果第一均质化处理的加热时间大于24小时,则效果饱和,即使大于24小时地进行处理也无法期待其以上的效果,从经济性的方面来看不优选。第一均质化处理中的加热时间更优选为10~24小时。
53.第一均质化处理中,将铸造凝固时形成的粗大的结晶物分解,使其粒状化或再固溶。另外,第一均质化处理中,作为溶质元素的mn、si向母相中的固溶也同时得到促进,但溶质元素向母相的固溶度高时,母相中的位错的运动速度会降低,变形阻力会增大。因此,作为均质化处理,如果仅进行第一均质化处理并对得到的处理物进行热挤出加工,则挤出性会变低。
54.因此,在进行第一均质化处理后,通过进行第二均质化处理,母相中固溶的mn、si析出,可以使mn、si的固溶度降低,因此可以使之后的热挤出加工中的变形阻力降低、使挤出性提高。第二均质化处理中的加热温度为450~540℃、优选为480~520℃。通过使第二均质化处理中的加热温度处于上述范围,母相中固溶的mn、si析出,可以使mn、si的固溶度降低,因此可以使之后的热挤出加工中的变形阻力降低、使挤出性提高。另一方面,第二均质化处理的加热温度小于上述温度时,其效果不充分,另外,大于上述范围时,难以发生析出,效果变得不充分。第二均质化处理中的加热时间为3小时以上,由于加热时间长会推进反
应,因此处理时间优选为5小时以上。但是,如果第二均质化处理的加热时间大于24小时,则效果饱和,即使大于24小时地进行处理也无法期待其以上的效果,从经济性的方面来看不优选。第二均质化处理中的加热时间更优选为5~15小时。
55.本发明的铝合金挤出多孔管的制造方法中,通过对铸锭(毛坯)进行第一均质化处理及之后的第二均质化处理,使溶质元素在母相中的固溶度降低,从而使挤出性提高。此时,铸锭的电导率成为溶质元素的固溶度的指标,固溶度升高时电导率降低,析出进行而固溶度降低时,电导率增高。于是,为了得到良好的挤出性,挤出前事先降低固溶度,即,使2阶段均质化处理前后的电导率变化设为20%iacs以上,优选设为25%iacs以上。由此,可以使挤出性可靠地提高。进而,如后所述,挤出前事先将铸锭的电导率降低还有助于抑制硬钎焊后的强度降低。2阶段均质化处理前后的铸锭的电导率变化小于上述范围时,挤出前的固溶度高,因此热变形阻力增高,挤出性受损,另外,由于硬钎焊中添加元素的析出被推进,因此硬钎焊后的强度会降低。2阶段均质化处理前后的铸锭的电导率之差越大则越优选,但作为上限,例如为35%iacs。需要说明的是,本发明中,2阶段均质化处理前后的铸锭的电导率变化是指通过“进行第二均质化处理后的铸锭的电导率(c)-进行第一均质化处理前的铸锭的电导率(d)”求出的值。
56.2阶段均质化处理中,可以在以第一均质化处理的加热温度进行第一均质化处理后,连续地以平均降温速度20~60℃/小时降温至第二均质处理的加热温度,连续地以第二均质化处理的加热温度实施第二均质化处理。
57.另外,2阶段均质化处理中,可以在以第一均质化处理的加热温度进行第一均质化处理后,先冷却至常温,例如冷却至200℃以下,之后以平均升温速度20~60℃/小时升温至第二均质化处理的加热温度,连续地以第二均质化处理的加热温度实施第二均质化处理。
58.2阶段均质化处理中,通过进行上述的第一均质化处理和第二均质化处理,可以使2阶段均质化处理前后的铸锭的电导率变化为20%iacs以上、优选为25%iacs以上。
59.本发明的换热器用铝合金挤出多孔管的制造方法的热挤出工序为对2阶段均质化处理的处理物进行热挤出加工,从而得到挤出多孔管的工序。热挤出工序中,热挤出时的加热温度为热挤出时的加热温度与第二均质化处理的加热温度之差(热挤出时的加热温度-第二均质化处理的加热温度)的绝对值成为50℃以下、优选成为30℃以下的温度。即,热挤出工序中的热挤出时的加热温度与第二均质化处理的加热温度的温度差为
±
50℃以内、优选为
±
30℃以内。热挤出中,通过将挤出前的毛坯加热温度设为与第二均质化处理温度之差(热挤出时的加热温度-第二均质化处理的加热温度)的绝对值成为50℃以下、优选成为30℃以下的温度,可以抑制热挤出加工中的溶质元素的再固溶。即,本发明的换热器用铝合金挤出多孔管的制造方法的热挤出工序中,可以将添加的mn、si以第二均质化处理中析出的微细的almnsi析出物的形式保留。然后,热挤出加工中得到的铝合金挤出多孔管通过硬钎焊安装于换热器,被硬钎焊接合,但此时,前述的微细的almnsi析出物再固溶于母相中,因此硬钎焊后也可以维持高强度。另一方面,热挤出中,以热挤出时的加热温度与第二均质化处理的加热温度之差的绝对值大于上述范围的加热温度进行热挤出时,在挤出温度高的情况下,almnsi析出物会在挤出前或挤出中再固溶,因此挤出性降低,另外,在挤出温度低的情况下,热变形阻力变大,因此挤出性降低。
60.本发明的换热器用铝合金挤出多孔管的制造方法中,进行热挤出工序后,根据需
要,也可进行用于提高涂装、耐腐蚀性的锌喷镀等。
61.如此,本发明的换热器用铝合金挤出多孔管的制造方法中,将铸锭中的mn的含量、si的含量及它们的含量比(mn/si)设为本发明规定的范围,且进行换热器用铝合金挤出多孔管的制造方法所涉及的2阶段均质化处理,由此提高热挤出加工中的挤出性,进而,将铸锭中的mn的含量、si的含量及它们的含量比(mn/si)设为本发明规定的范围,且进行换热器用铝合金挤出多孔管的制造方法所涉及的热挤出加工,由此可以得到硬钎焊加热中强度不会降低、或即使强度降低、强度的降低也小的换热器用铝合金挤出多孔管。
62.本发明的换热器用铝合金挤出多孔管是进行上述本发明的换热器用铝合金挤出多孔管的制造方法得到的换热器用铝合金挤出多孔管。即,本发明的换热器用铝合金挤出多孔管是进行上述本发明的换热器用铝合金挤出多孔管的制造方法所涉及的2阶段均质化处理和热挤出工序而得到的换热器用铝合金挤出多孔管。
63.本发明的换热器用铝合金挤出多孔管以及进行上述本发明的换热器用铝合金挤出多孔管的制造方法而得到的换热器用铝合金挤出多孔管与顶盖、翅片等构件一同安装,例如以590~610℃、优选595~605℃在例如氮气等非活性气体气氛中进行例如1~5分钟、优选为2~4分钟的硬钎焊加热,供于换热器的制造。
64.以下,示出实施例对发明进行具体说明,但本发明并不限定于以下示出的实施例。
65.实施例
66.将具有表1的组成的铝合金铸锭成挤出用毛坯,对得到的毛坯,进行在600℃下保持10小时的第一均质化处理、和接着在500℃下保持10小时的第二均质化处理,然后,在500℃下热挤出加工成图1所示的截面形状,得到挤出扁平多孔管。需要说明的是,图1为示意图,具体的尺寸设为:挤出扁平多孔管的宽度为14.0mm、高度为2.5mm、外周壁厚为0.4mm、内柱壁厚为0.4mm、孔数为19孔。
67.用以下的方法评价,第一均质化处理前及第二均质化处理后的毛坯的电导率、将该毛坯热挤出加工为管时的临界挤出速度、挤出扁平多孔管的加热试验前后的强度变化。
68.《电导率》
69.利用sigma tester,测定第一均质化处理前及第二均质化处理后的毛坯的电导率。比较第一均质化处理前和第二均质化处理后的电导率,将两者之差为25%以上者评价为
◎
、将20%以上且小于25%者评价为
○
、将小于20%者评价为
×
。
70.《临界挤出速度》
71.以在纯铝中仅添加有mn的现有合金的临界挤出速度(m/分钟)为基准,以相对于其之比的形式进行评价(将现有合金的临界挤出速度设为1.0),将临界挤出速度为0.9~1.0者记作
◎
,将0.8以上且小于0.9者记作
○
,将0.7以上且小于0.8者记作
△
,将小于0.7者记作
×
。
72.《加热试验》
73.对试验材料在600
±
10℃下进行3分钟的加热试验,采集拉伸试验片进行拉伸试验。加热试验前也同样实施拉伸试验,评价加热试验前后的拉伸强度的变化。将加热试验前后的拉伸强度的变化为0mpa以上的强度未降低者以及即使强度降低强度变化也为-5mpa以上且小于0mpa者记作
○
,将强度因加热试验而降低、且强度变化小于-5mpa(强度变化的绝对值大于5mpa)者记作
×
。
74.(评价结果)
75.表2中示出结果。表中示出的实施例1~4在2阶段均质化处理前后的电导率变化均为20%以上,挤出临界速度为与现有合金等同或不损害生产率水平的值,且加热试验的强度变化为-5mpa以上,在全部项目中均合格。
76.另一方面,比较例1虽然2阶段均质化处理前后的电导率变化为20%以上,加热试验的强度变化为-5mpa以上,但mn/si比大于4.0,因此挤出临界速度比现有合金低,不合格。
77.[表1]
[0078][0079]
[表2]
[0080]
再多了解一些
本文用于创业者技术爱好者查询,仅供学习研究,如用于商业用途,请联系技术所有人。