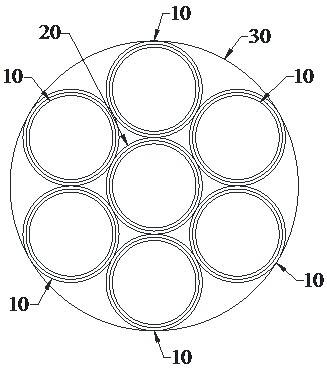
1.本发明涉及硫铁矿尾矿在矿山修复中的应用及矿山采空区的充填方法,属于硫铁矿技术领域。
背景技术:
2.硫铁矿,别名黄铁矿、磁黄铁矿、白铁矿,分子式为fes2,分子量为120。硫铁矿是一种重要的化学矿物原料,主要用于制造硫酸。
3.为了有效地利用硫铁矿尾矿矿渣,可以将该矿渣与盐酸溶液相互反应,将矿渣中残留的铁离子与氯离子结合得到一种高效的净水剂。或者是将矿渣与硫酸铵和氢氧化钠溶液进行反应,进而制备氧化铝和铁红等物质,或者是将这种尾矿矿渣作为制备导电材料的原材料。或者将其与粘结剂和填充剂等物质混合作为一种新型的涂料。而硫铁矿尾矿矿渣中含有二氧化硅和三氧化二铝等物质,将其作为制备混凝土的原材料,不仅解决了矿渣的堆放和污染环境的问题,也可充当混凝土的原材料;如果将矿渣替代一部分天然河砂和石子,也减少了天然河砂和石子的用量,但是,矿渣在混凝土中的力学性能仍比不上天然河砂和石子,故需要寻找其他手段弥补。
4.在混凝土领域中,现有研究:在等稠条件下,粉煤灰掺量依次为铁尾矿利用,铁尾矿加工烧制胶凝材料用量的0%、10%、15%、20%、25%、30%而增加,用水量随之有小幅的增加,但是分层度稍有降低,堆积密度7d和28d强度递减。当取代率超过30%时,砂浆3d、7d、28d强度有大幅降低,因此粉煤灰取代水泥率以不超过30%为宜。在砂浆稠度大致相同的条件下,砂浆的用水量与粉煤灰掺量的关系如下:当粉煤灰掺量在小于20%时,砂浆用水量与基准砂浆用水量变化不大,而当粉煤灰掺量大于25%时,用水量大幅增加,增加率大致为5%左右。
5.这种变化趋势主要原因如下:1)、当粉煤灰等量替代水泥后,由于形态效应,使得砂浆的工作性改善,不同颗粒大小的组合使其与水分子接触面减小,实际表现为用水量减少。
6.2)、粉煤灰作为一种活性材料加入水泥砂浆,会导致胶凝材料的总量增加,而胶凝材料的水化需要和水分子结合,因而实际表现为用水量的增加。
7.所以当砂浆的组成材料需水量大于减水量时,即表现出砂浆用水量的增加,反之则表现为用水量的减少。
8.综上分析,粉煤灰等量取代水泥配制混合砂浆和易性变化不大,但是砂浆早期强度测试结果显示较低,中后龄期强度继续保持增长,但是均不能满足基准砂浆强度的要求,相比较有降低。所以根据《用于水泥和混凝土中的粉煤灰》(gb/t 1596
‑‑
2005),通过多次试验,确定掺入粉煤灰的用量。
9.以nacl、cacl2、na2so4作早强剂间接激发粉煤灰活性,用nacl、cacl2作粉煤灰硅酸盐制品的早强剂,能不同程度地提高制品的强度,但其作用并不是在粉煤灰颗粒本身发生,而是通过加快石灰消解和增加石灰在水中的溶解度。食盐不仅具有上述作用,还能大大加
快形成硫铝酸盐的过程。
10.作为对矿山地下采空区进行充填,为保证强度以及质量,在一些区域如管桩、基桩、狭长裂缝区等,可使用c70混凝土来进行填充。但是,现有常规c70混凝土在试压强度、轴压强度、收缩值、碳化深度等方面不如c80混凝土,但是c80混凝土的成本较高。尤其是,对于c80混凝土来说,我公司经过大量的试验,如果掺入硫铁矿尾矿的矿粉,对性能影响很大。再加上c70混凝土、c80混凝土如果在抗渗性上能进一步提高,其在矿山地下采空区的应用前景会更广。
11.基于此,提出本发明。
技术实现要素:
12.本发明针对现有技术存在的不足,提供了硫铁矿尾矿在矿山修复中的应用及矿山采空区的充填方法,具体技术方案如下:矿山采空区的充填方法,将硫铁矿尾矿制备成矿浆,将矿浆与混凝土砂浆按照6:1的体积比同时并同步地输送至矿山地下采空区进行充填,养护3~28天后,再进行修整、维护作业。
13.上述技术方案的进一步优化,使用混凝土泵一对矿浆进行输送,采用六根软管一与混凝土泵一的输出端连通;使用混凝土泵二对混凝土砂浆进行输送,采用一根软管二与混凝土泵二的输出端连通;将软管一的末端按照中心对称的方式排列在软管二末端的外周,软管二的末端位于中央区域,在六根软管一的末端外部采用绑带进行绑扎;六根软管一和一根软管二构成输浆管。
14.上述技术方案的进一步优化,所述矿浆包括以下质量份组分:水
ꢀꢀꢀꢀꢀꢀꢀꢀꢀꢀꢀꢀꢀꢀꢀꢀꢀꢀꢀꢀ
150~200份;水泥
ꢀꢀꢀꢀꢀꢀꢀꢀꢀꢀꢀꢀꢀꢀꢀꢀꢀꢀ
350~400份;硫铁矿尾矿活化粉
ꢀꢀꢀꢀꢀꢀ
275~300份;中砂
ꢀꢀꢀꢀꢀꢀꢀꢀꢀꢀꢀꢀꢀꢀꢀꢀꢀꢀ
800~900份;碎石
ꢀꢀꢀꢀꢀꢀꢀꢀꢀꢀꢀꢀꢀꢀꢀꢀꢀꢀ
900~1000份;聚羧酸减水剂
ꢀꢀꢀꢀꢀꢀꢀꢀꢀꢀ
6.5~10份;活化膏
ꢀꢀꢀꢀꢀꢀꢀꢀꢀꢀꢀꢀꢀꢀꢀꢀ
5~6份。
15.上述技术方案的进一步优化,所述混凝土砂浆包括以下质量份组分:水
ꢀꢀꢀꢀꢀꢀꢀꢀꢀꢀꢀꢀꢀꢀ
150~160份;水泥
ꢀꢀꢀꢀꢀꢀꢀꢀꢀꢀꢀꢀ
350~400份;矿粉
ꢀꢀꢀꢀꢀꢀꢀꢀꢀꢀꢀꢀ
220~250份;中砂
ꢀꢀꢀꢀꢀꢀꢀꢀꢀꢀꢀꢀ
850~950份;碎石
ꢀꢀꢀꢀꢀꢀꢀꢀꢀꢀꢀꢀ
900~1000份;聚羧酸减水剂
ꢀꢀꢀꢀ
8.5~10份。
16.上述技术方案的进一步优化,所述活化膏的制备方法包括以下步骤:步骤p1、取香蒲的花序和苞片,将其晒干,得到干香蒲,干香蒲的水分含量小于或等于7%;步骤p2、将干香蒲先浸渍在澄清石灰水中最少3h,然后再将其浸渍在质量分数为
40
±
1%的硅酸钠溶液中最少3h,晾干,得到浸渍香蒲;步骤p3、将浸渍香蒲在无氧环境下于560~590℃下热裂解,收集冷凝后的液体与热裂解后剩余的固体并将二者混合均匀得到裂解混合物,向裂解混合物中加入2-磺基苯甲酸酐和氢氧化钠,搅拌反应最少5h,之后再球磨最少1h,得到活化膏。
17.上述技术方案的进一步优化,所述硫铁矿尾矿活化粉的制备方法,包括以下步骤:步骤s1、将硫铁矿尾矿球磨成粒径为0.5~1mm的硫铁矿尾矿粉;步骤s2、将凹凸棒土球磨成粒径为0.5~1mm的凹凸棒土粉;步骤s3、将硫铁矿尾矿粉、凹凸棒土粉、硅微粉混合搅拌均匀后,以水为润湿剂,使用湿法造粒机进行造粒,得到粒径为5~7mm的湿颗粒,采用流化床烘干,得到干颗粒;将干颗粒在470~490℃煅烧,得到烧结粒;步骤s4、将烧结粒浸入到三氟甲磺酸溶液中,浸泡时间为20~30min,之后捞出沥干,干燥后得到超强酸化粒;步骤s5、将超强酸化粒粉碎成粒径小于0.15mm的粉体,即得到硫铁矿尾矿活化粉。
18.上述技术方案的进一步优化,在步骤s3中,湿颗粒在流化床烘干的温度为110~120℃;干颗粒的水分含量为小于或等于1%。
19.上述技术方案的进一步优化,在步骤s4中,烧结粒与三氟甲磺酸溶液的质量比为1:100;三氟甲磺酸溶液的质量分数为0.00016%。
20.上述技术方案的进一步优化,硫铁矿尾矿在矿山修复中的应用,将硫铁矿尾矿制备成矿浆并与混凝土砂浆配合用于对矿山的修复。
21.上述技术方案的进一步优化,所述矿浆按照如权利要求3所述的矿山采空区的充填方法中的配比制成,所述混凝土砂浆按照如权利要求4所述的矿山采空区的充填方法中的配比制成。
22.本发明的有益效果:1、通过对硫铁矿尾矿回收利用,将其制成性能更优异的硫铁矿尾矿活化粉;硫铁矿尾矿活化粉与活化膏联合使用并参与反应;最终本发明所述矿浆所填充得到的区域,其试压强度(抗压强度)不但在早期有提升,养护完全后,性能更优异,稳定性好,抗渗性好,实现了矿山地下采空区的快速充填固化。
23.2、混凝土砂浆与矿浆搭配使用并按照特定的方式对矿山地下采空区进行充填,不但有助于降低成本,而且,还能够提高抗压强度等性能。
24.3、本发明中使用的硫铁矿尾矿活化粉、活化膏,其原材料中有一部分为工业固废、农业固废等,原材料成本低,获取方便。
25.4、本发明解决了硫铁矿尾矿(如矿渣)的堆积的问题,有效降低矿山地下采空区的安全隐患,并降低了矿山尾矿充填的成本。
附图说明
26.图1为本发明所述输浆管的结构示意图。
具体实施方式
27.为了使本发明的目的、技术方案及优点更加清楚明白,以下结合附图及实施例,对
本发明进行进一步详细说明。应当理解,此处所描述的具体实施例仅仅用以解释本发明,并不用于限定本发明。
28.实施例1矿山采空区的充填方法,具体为:将硫铁矿尾矿制备成矿浆,将矿浆与混凝土砂浆按照6:1的体积比同时并同步地输送至矿山地下采空区进行充填,养护3~28天后,再进行修整、维护作业。
29.实施例2基于实施例1,矿浆与混凝土砂浆按照6:1的体积比同时并同步地输送至矿山地下采空区进行充填的方法如下:使用混凝土泵一对矿浆进行输送,采用六根软管一10与混凝土泵一的输出端连通;使用混凝土泵二对混凝土砂浆进行输送,采用一根软管二20与混凝土泵二的输出端连通;将软管一10的末端按照中心对称的方式排列在软管二20末端的外周,软管二20的末端位于中央区域,在六根软管一10的末端外部采用绑带30进行绑扎;六根软管一10和一根软管二20构成输浆管,如图1所示。
30.绑带30优选钢带。软管一10和软管二20均采用在具有弹性的管体内嵌入螺旋弹簧状的钢丝来增强其抗压强度和抗拉强度。
31.采用该种特制结构,很容易做到将矿浆与混凝土砂浆按照6:1的体积比同时并同步地输送至矿山地下采空区,在泵入时,只需将输浆管的末端插入到对应的矿山地下采空区即可。
32.另外,该种独特结构,使得软管二20所泵出的混凝土砂浆形成一根混凝土柱;软管一10所泵出的矿浆形成一根矿浆柱;六根矿浆柱正好将其内的混凝土柱给围住,使得相邻两根混凝土砂浆之间相互独立,从而有效发挥出混凝土柱的独特性。
33.实施例3所述矿浆的原料组成见配方1,配方1如下:水
ꢀꢀꢀꢀꢀꢀꢀꢀꢀꢀꢀꢀꢀꢀꢀꢀꢀꢀꢀꢀ
150 kg;水泥
ꢀꢀꢀꢀꢀꢀꢀꢀꢀꢀꢀꢀꢀꢀꢀꢀꢀꢀ
350 kg;硫铁矿尾矿活化粉
ꢀꢀꢀꢀꢀꢀ
275 kg;中砂
ꢀꢀꢀꢀꢀꢀꢀꢀꢀꢀꢀꢀꢀꢀꢀꢀꢀꢀ
800 kg;碎石
ꢀꢀꢀꢀꢀꢀꢀꢀꢀꢀꢀꢀꢀꢀꢀꢀꢀꢀ
900 kg;聚羧酸减水剂
ꢀꢀꢀꢀꢀꢀꢀꢀꢀꢀ
6.5 kg;活化膏
ꢀꢀꢀꢀꢀꢀꢀꢀꢀꢀꢀꢀꢀꢀꢀꢀ
5 kg。
34.所述混凝土砂浆的原料组成见配方2,配方2如下:水
ꢀꢀꢀꢀꢀꢀꢀꢀꢀꢀꢀꢀꢀꢀ
150 kg;水泥
ꢀꢀꢀꢀꢀꢀꢀꢀꢀꢀꢀꢀ
350 kg;矿粉
ꢀꢀꢀꢀꢀꢀꢀꢀꢀꢀꢀꢀ
220 kg;中砂
ꢀꢀꢀꢀꢀꢀꢀꢀꢀꢀꢀꢀ
850 kg;碎石
ꢀꢀꢀꢀꢀꢀꢀꢀꢀꢀꢀꢀ
900 kg;聚羧酸减水剂
ꢀꢀꢀꢀ
8.5 kg。
35.所述活化膏的制备方法如下:
步骤p1、取香蒲的花序和苞片,将其晒干,得到干香蒲,干香蒲的水分含量小于或等于7%;步骤p2、将干香蒲先浸渍在澄清石灰水中3h,然后再将其浸渍在质量分数为40
±
1%的硅酸钠溶液中3h,晾干,得到浸渍香蒲;步骤p3、将浸渍香蒲在无氧环境下于570
±
5℃下热裂解,收集冷凝后的液体与热裂解后剩余的固体并将二者混合均匀得到裂解混合物,向裂解混合物中加入2-磺基苯甲酸酐和氢氧化钠,搅拌反应5h,之后再球磨1h,得到活化膏。
36.硫铁矿尾矿的主要成分为:al2o3,17wt%;sio2,34wt%;cao,2.6wt%;tio2,1.2wt%;so3,2.1wt%;fe2o3,43.1%。
37.所述硫铁矿尾矿活化粉的制备方法如下:步骤s1、将硫铁矿尾矿球磨成粒径为0.5~1mm的硫铁矿尾矿粉;步骤s2、将凹凸棒土球磨成粒径为0.5~1mm的凹凸棒土粉;步骤s3、将硫铁矿尾矿粉、凹凸棒土粉、硅微粉混合搅拌均匀后,以水为润湿剂,使用湿法造粒机进行造粒,得到粒径为5~7mm的湿颗粒,采用流化床烘干,流化床烘干的温度为110℃,得到干颗粒,干颗粒的水分含量为小于或等于1%。将干颗粒在480
±
3℃煅烧,得到烧结粒;步骤s4、将烧结粒浸入到三氟甲磺酸溶液中,烧结粒与三氟甲磺酸溶液的质量比为1:100,三氟甲磺酸溶液的质量分数为0.00016%;浸泡时间为20min,之后捞出沥干,干燥后得到超强酸化粒;步骤s5、将超强酸化粒粉碎成粒径小于0.15mm的粉体,即得到硫铁矿尾矿活化粉。
38.本发明采用容量法测量粉体比表面积。硫铁矿尾矿活化粉的比表面积为689m2/g。
39.本发明所述矿浆(对应配方1)所得到的试件,其试压强度(抗压强度)在7d为78.2mpa,28d为89.8mpa;28d的轴压强度为78.3mpa;28d的收缩值为130μm;碳化深度为1.9mm;28d时的氯离子扩散系数为11.19
×
10-14
m2/s,1年时的氯离子扩散系数在8.9
×
10-14
m2/s。矿浆所得到的试件的渗透性很低,并且随着时间的延长,试件的渗透性会变得更低。
40.矿浆所得到的试件,从试压强度、轴压强度来看,接近c80混凝土。
41.本发明所述混凝土砂浆是对现有c70混凝土的配方优化后的结果,该混凝土砂浆(对应配方2)所得到的试件,其试压强度(抗压强度)在7d为62.1mpa,28d为75.2mpa;28d的收缩值为250μm;碳化深度为4.3mm;1年时的氯离子扩散系数在228.2
×
10-14
m2/s。
42.通过对比混凝土砂浆与矿浆可知,矿浆的性能更优异。虽然矿浆中引入硫铁矿尾矿,但是本发明将硫铁矿尾矿制备成硫铁矿尾矿活化粉,再通过特制的活化膏来激发,反而使其性能有明显提升。
43.但是,矿浆的成本要比混凝土砂浆要高一些。硫铁矿尾矿活化粉虽然主材来源于废弃物硫铁矿尾矿,但是在加上其制作工艺以及材料,最终成本反而要比矿粉高一些。活化膏的成本也比矿粉高一些,但是其用量少;最终矿浆的成本要比混凝土砂浆高8~10%。目前的市场价,c80混凝土要比c70混凝土贵17%左右。
44.因此,如果只采用矿浆对矿山地下采空区进行充填,相对于只采用混凝土砂浆来说,成本更高。综合考虑成本、性能等因素,需要对混凝土砂浆与矿浆进行搭配使用。
45.对照例1
对照混凝土砂浆1的原料组成件配方3,配方3如下:水
ꢀꢀꢀꢀꢀꢀꢀꢀꢀꢀꢀꢀꢀꢀ
150 kg;水泥
ꢀꢀꢀꢀꢀꢀꢀꢀꢀꢀꢀꢀ
350 kg;矿粉
ꢀꢀꢀꢀꢀꢀꢀꢀꢀꢀꢀꢀ
130 kg;粉煤灰
ꢀꢀꢀꢀꢀꢀꢀꢀꢀꢀ
75 kg;中砂
ꢀꢀꢀꢀꢀꢀꢀꢀꢀꢀꢀꢀ
850 kg;碎石
ꢀꢀꢀꢀꢀꢀꢀꢀꢀꢀꢀꢀ
900 kg;聚羧酸减水剂
ꢀꢀꢀꢀ
8.5 kg。
46.本例中,采用对照混凝土砂浆1替代实施例3中的混凝土砂浆,其余条件不变。
47.本例是现有常规c70混凝土的一种配方。该混凝土砂浆(对应配方3)所得到的试件,其试压强度(抗压强度)在28d为70.3mpa;28d的收缩值为300μm;碳化深度为5.7mm;1年时的氯离子扩散系数在375.1
×
10-14
m2/s。
48.如果在c70混凝土中掺入一定量的粉煤灰取代矿粉,但是还会导致试压强度下降,碳化深度变深,抗渗性下降。
49.对照例2对照的矿浆的原料组成见配方4,配方4如下:水
ꢀꢀꢀꢀꢀꢀꢀꢀꢀꢀꢀꢀꢀꢀꢀꢀꢀꢀꢀꢀ
150 kg;水泥
ꢀꢀꢀꢀꢀꢀꢀꢀꢀꢀꢀꢀꢀꢀꢀꢀꢀꢀ
350 kg;硫铁矿尾矿粉
ꢀꢀꢀꢀꢀꢀꢀꢀꢀꢀ
275 kg;中砂
ꢀꢀꢀꢀꢀꢀꢀꢀꢀꢀꢀꢀꢀꢀꢀꢀꢀꢀ
800 kg;碎石
ꢀꢀꢀꢀꢀꢀꢀꢀꢀꢀꢀꢀꢀꢀꢀꢀꢀꢀ
900 kg;聚羧酸减水剂
ꢀꢀꢀꢀꢀꢀꢀꢀꢀꢀ
6.5 kg;活化膏
ꢀꢀꢀꢀꢀꢀꢀꢀꢀꢀꢀꢀꢀꢀꢀꢀ
5 kg。
50.其中,将硫铁矿尾矿球磨成粒径小于0.15mm的硫铁矿尾矿粉。
51.该对照的矿浆(对应配方4)所得到的试件,其试压强度(抗压强度)在28d为69.1mpa,28d的收缩值为530μm。
52.与实施例3中的配方1相比,如果没有将硫铁矿尾矿制成硫铁矿尾矿活化粉,而是直接粉碎制成硫铁矿尾矿粉,直接导致试压强度和收缩值显著降低,甚至不如对照例1。说明,硫铁矿尾矿不能直接磨成粉加入到c70混凝土体系中,否则,可能对其造成负面作用。
53.对照例3对照的矿浆的原料组成见配方5,配方5如下:水
ꢀꢀꢀꢀꢀꢀꢀꢀꢀꢀꢀꢀꢀꢀꢀꢀꢀꢀꢀꢀ
150 kg;水泥
ꢀꢀꢀꢀꢀꢀꢀꢀꢀꢀꢀꢀꢀꢀꢀꢀꢀꢀ
350 kg;硫铁矿尾矿粉
ꢀꢀꢀꢀꢀꢀꢀꢀꢀꢀ
280 kg;中砂
ꢀꢀꢀꢀꢀꢀꢀꢀꢀꢀꢀꢀꢀꢀꢀꢀꢀꢀ
800 kg;碎石
ꢀꢀꢀꢀꢀꢀꢀꢀꢀꢀꢀꢀꢀꢀꢀꢀꢀꢀ
900 kg;聚羧酸减水剂
ꢀꢀꢀꢀꢀꢀꢀꢀꢀꢀ
6.5 kg。
54.其中,将硫铁矿尾矿球磨成粒径小于0.15mm的硫铁矿尾矿粉。
55.该对照的矿浆(对应配方5)所得到的试件,其试压强度(抗压强度)在28d为
69.3mpa,28d的收缩值为510μm。
56.与对照例2相比,活化膏无法激发硫铁矿尾矿粉。
57.对照例4所述矿浆的原料组成见配方6,配方6如下:水
ꢀꢀꢀꢀꢀꢀꢀꢀꢀꢀꢀꢀꢀꢀꢀꢀꢀꢀꢀꢀ
150 kg;水泥
ꢀꢀꢀꢀꢀꢀꢀꢀꢀꢀꢀꢀꢀꢀꢀꢀꢀꢀ
350 kg;硫铁矿尾矿活化粉
ꢀꢀꢀꢀꢀꢀ
220 kg;中砂
ꢀꢀꢀꢀꢀꢀꢀꢀꢀꢀꢀꢀꢀꢀꢀꢀꢀꢀ
850 kg;碎石
ꢀꢀꢀꢀꢀꢀꢀꢀꢀꢀꢀꢀꢀꢀꢀꢀꢀꢀ
900 kg;聚羧酸减水剂
ꢀꢀꢀꢀꢀꢀꢀꢀꢀꢀ
8.5 kg。
58.该对照的矿浆(对应配方6)所得到的试件,其试压强度(抗压强度)在28d为76.6mpa,28d的收缩值为210μm。
59.配方2与配方6相比,如果不加活化膏,则无法激发硫铁矿尾矿活化粉;硫铁矿尾矿活化粉与矿粉的性能相差不大,只是略微好点。
60.配方2与配方6相比以及配方4与配方5相比,如果不加活化膏,则无法激发硫铁矿尾矿活化粉;另外,活化膏无法激发硫铁矿尾矿粉;说明,硫铁矿尾矿活化粉只能依靠活化膏激发,聚羧酸减水剂也无法激发。
61.对照例5本例与实施例的区别仅在于:不采用实施例2特制的输浆管进行输送矿浆与混凝土砂浆,而是将矿浆与混凝土砂浆先混合均匀后,采用混凝土泵三直接泵入到指定位置,养护28天后,随机取样50个,按照《抗压强度测试》测量抗压强度。对测量的50组抗压强度组,计算方差,方差(σ2)≥33.7。
62.而对实施例3中六根矿浆柱与其内混凝土柱之间交界处的区域随机取样50个,按照《抗压强度测试》测量抗压强度。对测量的50组抗压强度组,计算方差,方差(σ2)≤6.8。
63.由此可知,如果按照本实施例中这种直混的方式,所得到的试件,其均匀性非常差,不同区域之间的性能指标差异较大。以抗压强度为例,本例所得到的方差非常大。
64.而实施例3中,由于采用这种特殊工艺,使得六根矿浆柱与其内混凝土柱之间交界处的均匀性非常好;以抗压强度为例,实施例3所得到的方差较小。
65.对照例6本例与实施例的区别仅在于:更改实施例2中软管一10的内径,将其缩小5/6;最终使得矿浆与混凝土砂浆按照1:1的体积比同步地输送至矿山地下采空区进行充填,得到六根矿浆柱与一根混凝土柱合并一起的联合柱。该联合柱28d的轴压强度为66.8mpa.而实施例3中对应的联合柱,其轴压强度为75.6mpa。由此可知,联合柱的轴压强度下降了11.6%。
66.经过多次试验,矿浆与混凝土砂浆之间的体积比为6:1。
67.对照例7本例与实施例3中的唯一区别仅在于,在制备硫铁矿尾矿活化粉时,本例使用质量分数为50%的硫酸溶液;而实施例3中使用的是质量分数为0.00016%的三氟甲磺酸溶液。
68.本例中,所制成的对照硫铁矿尾矿活化粉的比表面积为397m2/g。
69.在本例中,对应试件的碳化深度为8.3mm;1年时的氯离子扩散系数在438.1
×
10-14
m2/s。
70.对照例8本例与实施例3中的唯一区别仅在于,在制备硫铁矿尾矿活化粉时,本例使用质量分数为85%的硫酸溶液;而实施例3中使用的是质量分数为0.00016%的三氟甲磺酸溶液。
71.在本例中,所制成的对照硫铁矿尾矿活化粉的比表面积为195m2/g。
72.通过对比对照例7和对照例8可知,使用常规酸性溶液(如硫酸)对硫铁矿尾矿粉、凹凸棒土粉、硅微粉等改性,如果酸性的浓度/酸度过高,反而还会使得内部结构坍塌,从而造成比表面积下降。
73.在本例中,对应试件的碳化深度为10.3mm;1年时的氯离子扩散系数在531.5
×
10-14
m2/s。
74.对照例9本例与实施例3中的唯一区别仅在于,在制备硫铁矿尾矿活化粉时,本例使用的三氟甲磺酸溶液的质量分数为0.0016%;而实施例3中使用的是质量分数为0.00016%的三氟甲磺酸溶液。
75.三氟甲磺酸溶液的酸度非常大,当其浓度较高时,会导致硫铁矿尾矿粉、凹凸棒土粉、硅微粉等内部结构迅速完全坍塌,从而破坏其本身性质。
76.在本例中,对应试件的碳化深度为50.9mm;1年时的氯离子扩散系数在1019.9
×
10-14
m2/s。
77.对照例10本例与实施例3中的唯一区别仅在于,在制备硫铁矿尾矿活化粉时,本例使用的三氟甲磺酸溶液的质量分数为0.00001%;而实施例3中使用的是质量分数为0.00016%的三氟甲磺酸溶液。
78.三氟甲磺酸溶液的酸度非常大,虽然其浓度较小时,也可以对硫铁矿尾矿粉、凹凸棒土粉、硅微粉等进行改性。在本例中,所制成的对照硫铁矿尾矿活化粉的比表面积为437m2/g。
79.在一些实施例中,如果烧结粒与三氟甲磺酸溶液的质量比过大(如10:100),会导致合格率小于73%。
80.而实施例3中,所制备的硫铁矿尾矿活化粉,其合格率超过98.6%。
81.合格率是指经过检测,比表面积达不到设计值90%的产品判定为不合格。
82.在一些实施例中,烧结粒与三氟甲磺酸溶液的质量比如果过小(如0.1:100),首先,浸泡时间需超过20min,同时,还会导致粉末内部的结构无法进一步更深层次的扩张,合格率会显著下降。
83.对照例11本例与实施例3中的唯一区别仅在于,在制备活化膏时,本例使用的是茅草;而实施例3中使用的是香蒲。
84.在本例中,对应试件1年时的氯离子扩散系数在625.9
×
10-14
m2/s。
85.香蒲对澄清石灰水的吸附以及作为载体与其余物质之间的反应,有效提高反应转化率以及效率。而同样作为碳源的茅草对应的效果则差得多。
86.香蒲作为生物质材料,在热裂解后,使用2-磺基苯甲酸酐和氢氧化钠进行激发并再次反应,最终得到的活化膏。活化膏参与水化反应,从而使得硫铁矿尾矿活化粉形成具有一定致密性的材料;热裂解冷凝后的液体能够进一步促进水化反应的完全反应,香蒲热裂解后剩余的固体还能增加浆体的流动性。
87.对照例12活化膏如果不采用在无氧环境下热裂解,而是在有氧环境下煅烧,所对应的对照活化膏无法对硫铁矿尾矿活化粉进行激发,其在矿浆中相当于杂质,反而其性能略有不如对照例4。
88.在本例中,对应试件1年时的氯离子扩散系数在812.3
×
10-14
m2/s。
89.在上述实施例中,硫铁矿尾矿的主要成分为:al2o3,16~20wt%;sio2,33~38wt%;cao,1~5wt%;tio2,1~3wt%;so3,1~3wt%;其余为fe2o3。只要满足上述范围均可。实施例中的硫铁矿尾矿的主要成分的具体值,只是其中一个实施例。
90.在上述实施例中,粉煤灰的粒径在30~100μm。水泥采用pii52.5水泥。碎石选用5~20mm的碎石。矿粉选用灵寿县展星矿产品有限公司发s95级矿粉,比表面积为430m2/kg。
91.《抗压强度测试》以混凝土砂浆为例,将混凝土砂浆制成70mm
×
70mm
×
70mm的试块,在温度为20
±
2℃、相对湿度为95%的环境中养护条件下养护28天,并分别测定试块3天、7天、28天的抗压强度。
92.《碳化深度测试》碳化深度是在二氧化碳浓度为(20
±
3)%,温度为(20
±
5)℃,湿度为(70
±
5)%的条件下碳化28d后所测得。在该条件下碳化28d即相当于在自然条件下碳化50年。抗渗性能试验是从0.1mpa开始,以后每隔8h增加0.1mpa,一直加压到5mpa,在5mpa的恒压条件下恒压8h后停止,把试件分开,即可测量碳化深度。
93.《氯离子扩散系数测定》设备:氯离子扩散系数测定仪,真空干燥箱。
94.试剂:阴极溶液采用质量分数为10%的nacl溶液,阳极溶液采用0.3mol/l的naoh溶液,ca(oh)2浸泡溶液,显色指示剂为硝酸银溶液。
95.测试样品规格:直径为100
±
1mm,高度为50
±
2mm的圆柱体试件。
96.测试步骤如下:1)、先将养护到规定龄期的圆柱体试件干燥,以硅胶涂刷圆柱体试件的圆柱表面至其完全密封。
97.2)、将圆柱体试件放入真空干燥箱中,抽真空使得真空干燥箱内的负压保持在1~5kpa并维持3h,之后注入蒸馏水将圆柱体试件完全淹没,淹没1h后恢复常压,再继续浸泡18
±
1h。
98.3)、将圆柱体试件固定安装在容器内,向容器内注入测试溶液,连接氯离子扩散系数测定仪,开机进行电迁移实验。
99.4)、将电迁移后的圆柱体试件沿轴向劈开,在开的表面上喷涂硝酸银溶液,确定扩散深度。将所测得数据输入氯离子扩散系数测定仪,自动计算该通道的扩散系数。
100.常规c70混凝土在1年时的氯离子扩散系数在(100~500)
×
10-14
m2/s之间。氯离子
扩散系数越小,对应的渗透性就低,也就表明混凝土的抗渗性越好。
101.以上所述仅为本发明的较佳实施例而已,并不用以限制本发明,凡在本发明的精神和原则之内所作的任何修改、等同替换和改进等,均应包含在本发明的保护范围之内。
再多了解一些
本文用于创业者技术爱好者查询,仅供学习研究,如用于商业用途,请联系技术所有人。