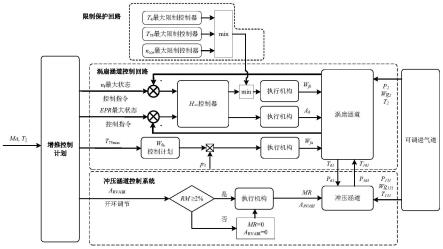
串联式tbcc发动机的模态转换控制方法
技术领域
1.本发明涉及一种串联式涡轮基组合循环(tbcc)发动机的模态转换控制方法,属于航空宇航推进系统控制技术领域。
背景技术:
2.涡轮基组合循环(tbcc)发动机作为高超声速飞行器的核心部件,一直是组合动力领域关注和研究的热点。对于并联式涡轮基组合循环(tbcc)发动机,作为加速器的低速通道发动机需要在传统马赫数2一级涡轮发动机的基础上,进一步扩展飞行包线至马赫数4以上,以适应高速通道双模态冲压发动机的起动范围。低速通道发动机应在整个工作过程中以及工作模式的转换过程中具有足够的推力以维持整个推进系统的推力连续。随着飞行马赫数的增加,传统马赫数2一级涡轮发动机由于进口总温的增加导致高/低压转子相对换算转速下降,在低速-高速通道模态转换点附近已接近风车状态,共同工作点远离设计点,发动机推力极低[haney j w.highly reusable space transportation system study[c]//aip conference proceedings.american institute of physics,1997,387(1):1277-1284.]。在这个过程中,极有可能出现发动机安装推力小于飞行器阻力(推阻不平衡)的情况导致飞行器持续减速,无法为高速通道发动机正常起动提供合适的来流条件,或者即使高速通道发动机能够起动但仍旧无法实现推阻平衡而导致模态转换失败。这类由于推阻不平衡导致飞行器无法完成低速通道向高速通道模态转换的问题被称为并联式tbcc发动机的推力陷阱问题[郑日恒,陈操斌.涡轮基组合循环发动机推力陷阱问题解决方案[j].火箭推进,2021,47(06):21-32.],如图1所示。
[0003]
目前对串联式tbcc发动机模态转换控制方法的研究以定点式模态转换控制为主,即在某一恒定的飞行马赫数和飞行高度条件(称为模态转换设计点)下完成模态转换,保持模态转换过程中发动机总推力恒定[chen m,tang h,zhang k,et al.turbine-based combined cycle propulsion system integration concept design[j].proceedings of the institution of mechanical engineers,part g:journal of aerospace engineering,2013,227(7):1068-1089.]。然而,定点式模态转换控制下,由于串联式tbcc发动机的亚燃模态最低工作马赫数的限制,模态转换设计点仍然处于涡轮发动机工作马赫数的上限,虽然相较并联式tbcc发动机的低速-高速通道模态转换马赫数有所降低,但此时涡轮发动机仍处于推力较低的工作区间,仍容易陷入推力陷阱。另一种可取的模态转换控制方式是区间式模态转换控制,即在某一较低的飞行马赫数下开始模态转换,随着马赫数的增加,当达到亚燃模态的最低工作马赫数时,完成模态转换。日本hypr90-c发动机在2.5~3ma之间进行模态转换,马赫数3以上时冲压发动机单独工作[soga y,kurosaki m,tsuzuki y,et al.control of hypr demonstrator engine[c]//34th aiaa/asme/sae/asee joint propulsion conference and exhibit.1998:3283.]。黄红超[黄红超,王占学,蔡元虎.基于推力连续准则的小型涡轮冲压组合发动机模态转换过程分析[j].航空动力学报,2009,24(12):2756-2762.doi:10.13224/j.cnki.jasp.2009.12.020.]分析了不同
的流量调节阀开度对模态转换过程参数变化的影响,按照推力连续的准则,确定了模态转换过程流量调节阀开度随马赫数的变化规律。相较定点式模态转换,区间式模态转换控制方式由于在较低的马赫数区间打开冲压通道,转换过程中可以获得更大的发动机的推力,为解决推力陷阱问题提供了可能性。然而,目前针对区间式模态转换的研究较少,且公开文献中研究的侧重点大多集中在模态转换前后发动机推力和空气流量光滑衔接和平稳过渡上,尚未深入研究以解决推力陷阱,增加推力为目标的模态转换控制方案,同时,缺乏区间式模态转换方式增加推力的原理分析。对于作为并联式tbcc发动机低速通道加速器使用的串联式tbcc发动机,为避免推力陷阱,同时实现高加速性,亟需以实现高推力性能为目标来制定串联式tbcc发动机的模态转换控制方案。
技术实现要素:
[0004]
本发明所要及解决的技术问题在于克服现有技术不足,提供一种串联式tbcc发动机的模态转换控制方法,对于作为并联式tbcc发动机低速通道加速器使用的串联式tbcc发动机,可有效避免推力陷阱,同时实现高加速性。
[0005]
本发明具体采用以下技术方案解决上述技术问题:
[0006]
一种串联式tbcc发动机的模态转换控制方法,所述串联式tbcc发动机作为并联式tbcc发动机低速通道加速器使用;对串联式tbcc发动机的模态转换进行以下分区控制:
[0007]
在来流马赫数为0~第一马赫数区间内,控制所述串联式tbcc发动机以涡扇模态最大状态工作,所述第一马赫数为发动机工作在最大状态下时,冲压涵道的回流裕度为2%时的马赫数,p
131
为进气道出口总压,p
s61
为一级混合室出口静压;
[0008]
在来流马赫数为第一马赫数~第二马赫数区间内,打开低速通道冲压涵道,并令低速通道冲压涵道开度大于0且低于或等于临界开度;所述临界开度是指在当前来流马赫数下令冲压涵道气流流量与涡轮通道气流流量的合流量等于进气道所能提供的最大进气量的冲压涵道开度,所述第二马赫数为满足低速通道冲压发动机单独工作的最小马赫数;
[0009]
在来流马赫数为第二马赫数~4.0区间内,控制所述串联式tbcc发动机以完全冲压模态工作。
[0010]
优选地,在来流马赫数为第一马赫数~第二马赫数区间内,令低速通道冲压涵道开度始终等于临界开度。
[0011]
优选地,对涡扇涵道进行h
∞
闭环控制。
[0012]
优选地,对低速通道冲压涵道开度进行开环控制。
[0013]
相比现有技术,本发明技术方案具有以下有益效果:
[0014]
本发明从原理角度分析并设计了以实现高推力为目标的作为并联式tbcc发动机低速通道的串联式tbcc发动机模态转换控制方案,可以在保持涡扇各部件工作在最大状态的同时,开启冲压涵道,通过增加发动机的进气流通能力,同时降低发动机溢流阻力的方式,提高发动机最大安装推力性能并实现更好的进气道-发动机匹配工作,从而有效解决并联式tbcc发动机的推力陷阱问题;本发明还进一步提出了最优的冲压涵道开度调节方案,可最大程度地提升模态转换过程中发动机的推力,实现进气道进气量的最佳有效利用。
附图说明
[0015]
图1为并联式tbcc发动机的推力陷阱问题示意图;
[0016]
图2为动压为34.29kpa的飞行轨迹;
[0017]
图3为常规定点式模态转换控制计划下的发动机推力f与ma之间的关系示意图;
[0018]
图4为涡扇模态下发动机关键参数随马赫数变化情况示意图;
[0019]
图5为回流裕度rm随ma的变化示意图;
[0020]
图6为本发明所提出的增推控制结构示意图;
[0021]
图7为h∞鲁棒控制的结构原理示意图;
[0022]
图8为ma=2.5时rvabi开度对发动机特性的影响;
[0023]
图9为不同来流马赫数条件下,rvabi开度对发动机特性的影响;
[0024]
图10为rvabi开度最优调节规律;
[0025]
图11为外并联增推式tbcc发动机部件级模型结构原理示意图;
[0026]
图12为飞行轨迹及模态划分示意图;
[0027]
图13为并联式tbcc发动机采用不同模态转换控制方案的仿真对比结果。
具体实施方式
[0028]
作为并联式tbcc发动机低速通道加速器使用的串联式tbcc发动机,其任务是将并联式tbcc发动机加速至高速通道双模态超燃冲压发动机最小起动马赫数ma=4,在此过程中提供足够的推力避免产生推力陷阱;针对这一问题,本发明的解决思路是采用分区间的模态转换控制方案,具体如下:
[0029]
对串联式tbcc发动机的模态转换进行以下分区控制:
[0030]
在来流马赫数为0~第一马赫数区间内,控制所述串联式tbcc发动机以涡扇模态最大状态工作,所述第一马赫数为发动机工作在最大状态下时,冲压涵道的回流裕度为2%时的马赫数,p
131
为进气道出口总压,p
s61
为一级混合室出口静压;
[0031]
在来流马赫数为第一马赫数~第二马赫数区间内,打开低速通道冲压涵道,并令低速通道冲压涵道开度大于0且低于或等于临界开度;所述临界开度是指在当前来流马赫数下令冲压涵道气流流量与涡轮通道气流流量的合流量等于进气道所能提供的最大进气量的冲压涵道开度,所述第二马赫数为满足低速通道冲压发动机单独工作的最小马赫数;
[0032]
在来流马赫数为第二马赫数~4.0区间内,控制所述串联式tbcc发动机以完全冲压模态工作。
[0033]
优选地,在来流马赫数为第一马赫数~第二马赫数区间内,令低速通道冲压涵道开度始终等于临界开度。
[0034]
优选地,对涡扇涵道进行h
∞
闭环控制。
[0035]
优选地,对低速通道冲压涵道开度进行开环控制。
[0036]
为了便于公众理解,下面结合附图对本发明的技术方案进行详细说明:
[0037]
以tbcc推进系统为动力的高超声速飞行器一般是沿着等动压线进行加速爬升。starrunner概念机飞行轨迹的动压约为95kpa,hypr计划中飞行轨迹的动压约为20kpa,提高飞行器的动压可以对其性能进行充分的开发,但是动压的上升也会使得飞行器所承受的
机械负荷以及温度载荷的上升,所以飞行器必须在合适的最大动压下进行爬升。动压q0定义如式(1)所示。
[0038][0039]
式中,ρ0和v0分别表示自由来流的密度和速度,k0为自由来流的绝热指数,p0为自由来流的静压,由飞行高度h确定,ma为飞行马赫数,在飞行轨迹动压已知的情况下,飞行马赫数ma和高度h是一一对应的。
[0040]
以高超声速飞行器沿动压值q0=34.29kpa(h=24km,ma=4)的飞行轨迹运行为例,ma≤4为串联式tbcc发动机工作区间,其任务是将并联式tbcc发动机加速至高速通道双模态超燃冲压发动机最小起动马赫数ma=4,ma≥4为双模态超燃冲压发动机工作区间,如图2所示。
[0041]
在追求发动机高推力的同时必须考虑发动机状态参数限制,串联式tbcc发动机工作过程中的主要限制包括最大机械/气动负荷限制、最大热负荷限制以及气动稳定性限制。基于现有发动机水平,须满足的限制参数值如表2所示。
[0042]
表2发动机状态参数限制
[0043][0044][0045]
沿上述q0=34.29kpa等动压工作线,仿真了常规定点式模态转换控制计划下,串联式tbcc发动机工作参数随来流马赫数ma的变化。已知串联式tbcc发动机冲压模态单独工作的最小马赫数为ma=3,按照常规模态转换控制方法,选取飞行轨迹上马赫数ma=3,飞行高度h=20km工作点为模态转换点进行模态转换,在ma≤3区间,以涡扇模态最大状态工作,在3≤ma≤4区间以冲压模态单独工作。
[0046]
沿飞行轨迹,发动机推力变化如图3所示:
[0047]
如图3所示,随着马赫数的增加,涡扇模态下发动机推力显著减小,在模态转换点(ma=3,h=20km),涡扇发动机最大推力仅为地面状态的41%。ma》3后进入到冲压模态,发动机推力重新上升。整个过程中,在模态转换点附近推力下降严重,极易出现推阻不平衡现象。
[0048]
高马赫数条件下涡扇模态推力不足的原因主要包括两个方面:一方面,随着飞行马赫数ma增加,来流空气总温t2大幅升高,由式(2)可知,随着t2的增加,风扇相对换算转速n
fcor
及压气机相对换算转速n
ccor
迅速减小(参见图4中的(a))。由风扇及压气机特性图上的共同工作线可知(参见图4中的(b)、(c)),在低折合转速大流量条件下,风扇增压比πf和压气机增压比πc均较小,发动机可用增压比(π=πf×
πc)下降导致发动机做功能力降低,从而导致总推力下降。另一方面,随着飞行马赫数ma的增加,发动机需求流量w
a2
急剧下降,进气道进口可用气流w
a1max
大于发动机需求流量w
a2
,产生溢流阻力(见图4中的(e)),此时通常需要调节进气道几何型面,否则将导致发动机安装推力大幅度下降。
[0049][0050]
式中,nf,nc分别为风扇及压气机物理转速,下标“des”代表各参数在标准状态下参数值。
[0051]
由以上分析可知,串联式tbcc发动机工作过程中,在模态转换点附近发动机总推力出现明显下降,且进气道工作在亚临界状态,溢流阻力较大,导致发动机安装推力下降严重,极易出现推阻不平衡现象。因此,极有必要在高马赫数条件下开展增推控制方案研究工作。
[0052]
对于一定高度和马赫数的飞行状态,串联式tbcc发动机推力公式可表示为:
[0053]
f=w
g9
·v9-(w
a2
w
a131
)
·
v0 (p
s9-p
s0
)
·
a9ꢀꢀꢀ
(3)
[0054]
式中w
g9
为发动机喷管出口燃气流量;w
a2
为发动机风扇进口空气流量;w
a131
为冲压涵道进口空气流量;v0为飞行速度;排气速度v9=ma9·
c9;p
s9
为喷管出口静压;p
s0
为大气背压;a9为喷管出口截面面积。
[0055]
由温度,压力的静参数与迟滞参数关系式公式(4),可得喷管出口马赫数ma9计算公式如式(5)所示。
[0056][0057][0058]
喷管出口截面当地声速式中,k为比热比;r为气体常数,t
s9
,t9分别为喷管出口静温、总温,p9为喷管出口总压。
[0059][0060]
忽略燃气流量与空气流量的差别,则有:
[0061][0062]
当喷管扩张段为全管超声速流时,喷管出口仅可能出现三种状态:出口斜激波、设
计状态、出口膨胀波,而这三种状态对应的喷管出口静压p
s9
均为特征压力p
b1
。推力公式可进一步改写为:
[0063][0064]
进一步假设喷管与外界无热交换。则有t
75
=t8=t9。推力公式可进一步简化为:
[0065][0066]
式中,σ7为加力燃烧室总压恢复系数,σ8为喷管进口至喉道总压恢复系数,σ9为喷管扩张段总压恢复系数。
[0067]
由公式(9)可知,如果在涡扇模态高马赫数推力不足的工作区间打开冲压涵道,同时保证风扇进口流量w
a2
,冲压混合室出口总压p6不变,加力燃烧室出口总温t
75
=t
75max
,则随着冲压涵道流通面积a
rvabi
的增加,进气流量w
a131
不断增加,发动机需求总流量w
a2
′
=w
a2
w
a131
增加,发动机推力f也会随之增加。同时,发动机需求总流量的增加可以减小高马赫数区间工作时进气道的溢流流量,从而减小发动机溢流阻力,进一步提高安装推力。
[0068]
基于以上原理分析,为得到最大输出推力,需保证风扇进口流量w
a2
,冲压混合室出口总压p6不变,同时,保持加力燃烧室出口总温t
75
保持为最大值。然而,空气流量w
a2
和加力燃烧室出口总温t
75
无法基于传感器精确测量,因此在实际控制中通常是通过间接参数表征。在相同的风扇进口条件下,保证低压转子转速指令n
fref
不变使得低压转子相对换算转速n
fcor
不变,由部件特性公式(10)可知,可以基本保证风扇进口换算流量w
a22c
不变,如式(11)所示,一定程度上实现对风扇进口流量w
a2
的控制。
[0069]wa22c
=f(n
fcor
,πf)
ꢀꢀꢀ
(10)
[0070][0071]
另外,在一定的飞行条件下,风扇进口总压p2不变,因此保证发动机总压比epr=p6/p2不变可保证冲压混合室出口总压p6不变;加力燃烧室出口总温t
75
可通过复合参数w
fa
/p3表征。因此,设计发动机增推控制方案如式(12)所示:
[0072][0073]
如式(12)所示,通过闭环控制w
fb
,a8,w
fa
,保持涡轮各部件以允许的最大负荷工作,同时开环调节后可变面积涵道引射器出口面积a
rvabi
来改变冲压涵道流量w
a131
,从而达到增加发动机推力的目的。
[0074]
为了保证增推控制过程平稳,安全进行,增推控制的适用条件除了需要满足发动机最大机械/气动负荷限制、最大热负荷限制以及气动稳定性限制(见表2)外,还需要满足以下三个条件:
[0075]
1)冲压涵道气流不倒流(若涡轮后的高温燃气经过冲压涵道回流到风扇进口,即
形成了燃气倒流现象,将造成发动机风扇超温损坏)。2)转换过程中加力/冲压燃烧室燃烧稳定。3)流入发动机的总流量w
a2
′
=w
a2
w
a131
不应大于进气道所能提供的最大进气流量w
a1max
。如果流入发动机的总流量大于进气道所能提供的最大进气流量,进气道将工作在超临界状态,进气道总压恢复系数下降,进而导致发动机推力下降,耗油率大幅上升。
[0076]
不倒流是增推控制过程中打开冲压涵道的基本要求,定义冲压涵道的回流裕度rm如式(13)所示。为了保证不倒流,需要保证进气道出口总压p
131
大于一级混合室出口静压p
s61
,因此,增推控制过程中需满足rm》0,考虑到发动机运行过程中的测量误差,在增推控制过程中,保证回流裕度rm≥2%。
[0077][0078]
回流裕度rm主要受发动机工作状态和飞行马赫数ma的影响,当发动机工作在最大状态时,rm的大小主要由飞行马赫数决定;不同马赫数下发动机rm如图5所示。
[0079]
由图5可以看出,当飞行马赫数小于2.2,回流裕度rm《2%,此时若打开冲压涵道会发生燃气倒流现象;当飞行马赫数大于2.2时,rm≥2%,此时满足打开冲压涵道的条件。随着飞行马赫数的增加,rm不断增加,说明飞行马赫数越高,冲压涵道越不容易产生回流。
[0080]
为了实现上述增推控制方案,在满足增推控制方案适用条件的工作区间,设计了如图6所示的增推控制结构。该增推控制结构分为两部分,包括涡扇涵道的h
∞
闭环控制和冲压涵道后可变面积涵道引射器开环控制。
[0081]h∞
鲁棒控制具有很强的鲁棒性和抗干扰性,可以保证发动机闭环系统的稳定性。其原理如图7所示。
[0082]
其中,ω是扰动信号,需要设计合适的控制器k(s)抑制其对输出y的影响,保证被控对象p(s)稳定。为了实现无静差跟踪,w1(s)需包含一个积分环节,且当ω
→
0时,‖w1‖
∞
>>‖w2‖
∞
。同时当ω
→
∞时,需满足‖w2‖
∞
>>‖w1‖
∞
,以增强抗噪声能力。
[0083]
为了保证发动机全程安全稳定运行,控制结构中加入了发动机限制保护回路,包括n
cor
最大限制控制器、t4最大限制控制器和t
75
最大限制控制器(n
cor
≤100%,t4≤1800k,t
75
≤2400k)。采用高低选择器来选择满足所有约束条件的控制变量。在此基础上,增加了冲压涵道增推控制系统,若冲压涵道回流裕度rm≥2%,则通过改变冲压涵道引射器出口面积a
rvabi
调节冲压涵道进口流量w
a131
,从而增加发动机总推力。若rm《2%,保持冲压涵道关闭状态:mr=0,a
rvabi
=0。
[0084]
采用图6所示增推控制结构,在等动压线上不同来流马赫数时,仿真后可变面积涵道引射器(rvabi)不同开度下对发动机性能的影响,rvabi开度α定义如式(14)所示。
[0085][0086]
其中,a
rvabi,max
为rvabi面积的最大值,α=0代表冲压涵道完全关闭,α=100%代表冲压涵道完全打开。
[0087]
首先选取ma=2.5飞行条件,仿真rvabi不同开度下对发动机性能参数的影响,如图8所示。随着α的放大,冲压涵道空气流量w
a131
不断增加,发动机推力f不断增加,同时耗油率s
fc
不断下降,当α增加至α=α0=66%时,冲压涵道气流流量与涡轮通道气流流量的合流量w
a2
′
=w
a2
w
a131
等于进气道所能提供的最大进气量w
a1max
,定义此时rvabi的开度为临界开
度α0,如式(15)所示:
[0088]
α=α0(when:w
a1max
=w
a2
′
=w
a2
w
a131
)
ꢀꢀꢀ
(15)
[0089]
此时继续增大α,将导致涡扇发动机空气流量下降,进气道工作在超临界状态,总压恢复系数σ下降,进而导致推力f下降,耗油率s
fc
大幅度上升,如图8所示。
[0090]
图9仿真了不同来流马赫数条件下,rvabi开度对发动机特性的影响。如图9所示,在不同的来流马赫数下,本发明提出的增推控制方案均可以增大发动机推力f,同时,降低耗油率s
fc
,推力的最大增幅约为35.7%,耗油率约降低0.13%,回流裕度rm随来流马赫数ma的增加逐渐增加,说明马赫数愈大则愈不容易发生燃气回流现象。
[0091]
由图9中的(b)、(c)可以看出,不同飞行马赫数下均存在一个rvabi的临界开度α0,在该开度下,进气道工作在临界状态,进气道进口气流全部用来做功,无溢流流量及溢流阻力,发动机安装推力f也达到最大值。此开度即为当前马赫数下rvabi的最优开度。不同马赫数下的最优开度如图10所示。因此,图10中α0随来流马赫数ma的变化曲线即为冲压涵道出口面积a
rbabi
的最优调节规律。
[0092][0093]
以上述的串联式tbcc发动机作为低速通道加速器,进一步开发了并联式tbcc发动机部件级模型,如图11所示。
[0094]
低速通道采用上文建立的串联式tbcc发动机模型,高速通道为双模态超燃冲压发动机,高速通道亚燃模态下需满足公式(17)尾喷管流量平衡方程;动态过程中,需满足燃烧室容积动力学方程,如公式(18)所示。超燃模态下由于高速通道内气流全程超声速,上游气流不会受到下游气流条件的影响,因此不需要迭代计算。
[0095][0096][0097]
式中,下标“s”指双模态超燃冲压发动机截面参数,w
g8cs
,v
nets
分别为尾喷管允许通过的燃气流量和燃烧室控制体体积。
[0098]
沿等动压线飞行轨迹,外并联增推式tbcc发动机的工作模态划分如图12所示。低速通道串联式tbcc发动机向高速通道双模态超燃冲压发动机转换的马赫数为ma=4。工作模态随着来流马赫数提高可分为以下几个阶段:(1)ma=0~2.2区间内,处于涡扇模态,以涡扇模态最大状态工作;(2)ma=2.2~3.0区间内,打开低速通道冲压涵道,定义此模态为增推模态,低速通道冲压涵道开度按图10的最优调节规律变化;(3)ma3.0~4.0区间内,满足低速通道冲压发动机单独工作来流条件,串联式tbcc发动机进入完全冲压模态;(4)ma4.0以上,串联式tbcc发动机停止工作,进入高速通道双模态超燃冲压工作模态。
[0099]
沿上述飞行轨迹,针对并联式tbcc发动机,分别采用低速通道的常规控制方案和本发明控制方案,推力、空气流量、耗油率变化的对比如图13所示:
[0100]
由图13中的(a)可以看出,采用常规的控制方案,当飞行马赫数ma》2.7时,由于发动机安装推力小于飞行器阻力,出现推阻不平衡现象致使飞行器持续减速,无法为冲压发
动机正常起动提供合适的来流条件,陷入推力陷阱。当采用增推控制计划后,发动机推力最大增加量δf
max
约为7.036kn(增幅为29.8%),且沿飞行轨迹全程推力大于飞行器阻力,有效地避免了推力陷阱现象的产生。从图13中的(b)可以看出,增推控制可有效利用发动机进气道的最大进气量,采用所设计的最优冲压涵道面积调节规律,可使原本的溢流空气几乎全部进入串联式tbcc发动机冲压涵道做功,发动机需求总流量w
a2
′
=w
a2
w
a131
与进气道最大进气量w
a1max
相等,从而最大程度地提高发动机的安装推力。同时,由图13中的(c)可以看出,采用增推控制后,发动机的耗油率也有一定程度的下降,对发动机的经济性得到小幅度提升。
再多了解一些
本文用于创业者技术爱好者查询,仅供学习研究,如用于商业用途,请联系技术所有人。