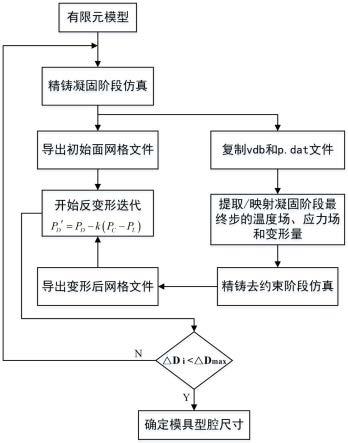
1.本发明涉及涡轮叶片尺寸控制方法领域,尤其涉及一种基于网格节点的涡轮叶片精铸全过程反变形方法。
背景技术:
2.航空发动机是装备制造领域的最高端产品,代表着一个国家的科技水平和综合国力,而涡轮叶片是决定航空发动机性能、可靠性和安全性的核心热端部件,航空制造强国对其关键技术严密封锁。以某型空心涡轮叶片为例,即使在尺寸精度让步接收条件下,叶片尺寸超差依然在50%以上,为了提高涡轮叶片合格率,首先需要具有精确尺寸的模具,通过该模具可以在一定程度上实现涡轮叶片控形。“试错法”制造模具是非常昂贵的,因此需要借助有限元软件分析涡轮叶片在精密铸造过程中作用尺寸变化。
3.目前,大多数学者考虑涡轮叶片在凝固阶段的尺寸变化,忽视了凝固阶段后去约束对叶片尺寸带来的影响,例如去除模壳、工艺筋、延长段和陶芯等约束。在公开专利基于去约束的精铸建模仿真方法(cn202210019676.x)和论文《涡轮叶片精铸脱壳芯过程仿真及对铸件应力/尺寸影响规律》中,证明去约束过程中应力的释放对精铸涡轮叶片精度的影响不可忽视。因此,需要同时考虑涡轮叶片精铸全过程,即凝固阶段和去约束阶段,通过反变形迭代确定模具型腔尺寸,从而控制涡轮叶片在精铸全过程中的变形量,提高叶片合格率。
技术实现要素:
4.为了控制涡轮叶片在精铸全过程中的变形量,保证叶片尺寸满足设计要求,本发明提出一种基于网格节点的涡轮叶片精铸全过程反变形方法。对涡轮叶片精铸全过程进行数值模拟,在保证网格节点序号不变的前提下,将凝固阶段和去约束阶段串联,实现凝固 去约束阶段的直接反变形,通过多次精铸全过程迭代,有效控制涡轮叶片在精铸全过程中的尺寸变化。
5.本发明实现上述目的技术解决方案包括以下步骤:
6.步骤1:
7.将设计模型根据工厂实际工艺划分并转为有限元模型,其目的是为准确模拟去约束过程建立基础,方法为:
8.[1]通过三维软件ug打开设计模型,通过拆分体、合并等操作,分别导出叶片、延长段、浇道、冷铜和炉体等多个prt文件。
[0009]
[2]将[1]中多个prt文件一起导入hypermesh,对互相接触的体进行布尔操作,使其接触面共节点,例如叶片和陶芯、浇道和冷铜等,然后通过隐藏命令对每个体进行网格划分,根据结构不同调整网格尺寸,网格划分完成后导出out文件。
[0010]
[3]将[2]生成的out网格文件通过visual-cast模块导入铸造专用有限元软件procast,将炉体通过convert to enclosure命令转换为辐射区域,切换visual-mesh模块修复网格、生成模壳shelling和体网格等,然后设置重力方向、材料参数、换热系数和边界
条件等参数,最终提交计算,完成精铸过程凝固阶段仿真。
[0011]
步骤2:
[0012]
根据实际工艺对步骤1完成的凝固模拟铸件进行去约束操作,更加符合实际生产中叶片去约束工艺,方法为:
[0013]
[1]将步骤1生成的*vdb和*p.dat文件拷贝至新文件夹,为了实现凝固 去约束阶段反变形,需要保证两阶段中网格节点的一致性,通过设置vacant模拟实际生产中约束去除。
[0014]
[2]建立新的边界条件。采用“四点法”约束叶片在空间位置,在叶片上选定point 1点,约束其xyz方向均为0,沿该点x方向选定point 2点,约束其y方向为0,沿该点y方向选定point 3点,约束其z方向为0,沿该点z方向选定point 4点,约束其x方向为0。
[0015]
[3]提交计算,完成精铸过程去约束阶段仿真。
[0016]
步骤3:
[0017]
步骤1完成凝固阶段模拟,步骤2完成去约束阶段模拟,实现涡轮叶片精铸全过程仿真,最后利用步骤1和2的结果文件进行反变形的,得到符合设计要求的模具型腔,方法为:
[0018]
[1]反变形迭代公式为pd′
=p
d-k(p
c-p
l
),其中pd,pc,p
l
分别为模具型腔、铸件和理论模型的对应点,k为松弛因子,k=1时表示型腔在经过铸件反变形后可以达到理论模型。
[0019]
[2]导出步骤1凝固阶段的面网格文件,该文件包含模型网格的初始节点p
l
(x,y,z)坐标,导出步骤2去约束阶段的后处理网格文件,该文件包含模型在经历凝固阶段 去约束阶段变形后的网格节点pc(x,y,z)坐标。
[0020]
[3]将[2]导出的p
l
(x,y,z)和pc(x,y,z)离散点数据代入反变形迭代公式,得到反变形模型。为了验证该模型的准确性,需要对该模型进行相同工艺条件下的精铸全过程仿真,判断所有离散点的变形量
△di
是否小于设计要求
△dmax
,i为离散点总数量。
[0021]
步骤4:
[0022]
若步骤3中反变形模型精铸仿真后离散点
△di
》
△dmax
,则不满足设计要求,需要在相同仿真参数下重复步骤1、步骤2和步骤3,直至符合设计要求
△di
≤
△dmax
,得到的pd′
即为模具型腔数据,该模具可有效控制涡轮叶片在精铸全过程中的尺寸变化。
[0023]
本发明的有益效果是:同时考虑涡轮叶片在凝固阶段和去约束阶段的尺寸变化,更加符合叶片实际铸造工艺,为了保证两阶段中网格节点的一致性,通过设置vacant模拟实际生产中约束去除,通过对三维网格节点进行反变形迭代确定模具型腔尺寸,使其在该模具下精铸仿真后离散点
△di
》
△dmax
,满足设计要求,从而有效控制涡轮叶片在精铸全过程中的变形量,提高叶片合格率。
附图说明
[0024]
图1是本发明一种基于网格节点的涡轮叶片精铸全过程反变形方法流程图;
[0025]
图2是本发明的一种实施方式的涡轮叶片精铸有限元模型图;
[0026]
图3是本发明的一种实施方式去约束阶段提取映射温度场图;
[0027]
图4是本发明的一种实施方式去约束阶段的部分约束模型图;
[0028]
图5是本发明的一种实施方式的涡轮叶片精铸全过程反变形优化系统图;
[0029]
图6是本发明的一种实施方式的通过反变形系统优化后的模型图。
具体实施方式
[0030]
为了更清楚地说明本发明的具体实施方案,结合附图和具体实施方式对本发明进行详细说明。但本发明的保护范围不限于下述的实施例。显而易见地,下面描述中的附图仅仅是本发明的部分实施方式,对于本领域普通研究人员而言,在不付出创造性劳动的前提下,还可以根据本发明得到其他附图。
[0031]
以某型号简化航空涡轮叶片为例,本发明的具体实施流程如图1所示:
[0032]
步骤1
[0033]
将设计模型根据工厂实际工艺划分并转为有限元模型,通过三维软件ug打开设计模型,通过拆分体、合并等操作,分别导出叶片、延长段、浇道、冷铜和炉体等多个prt文件。然后将这些prt文件一起导入hypermesh,对互相接触的体进行布尔操作,使其接触面共节点,例如叶片和陶芯、浇道和冷铜等,然后通过隐藏命令对每个体进行网格划分,根据结构不同调整网格尺寸,网格划分完成后导出所有体为out文件。
[0034]
图2是涡轮叶片精铸有限元模型图;
[0035]
步骤2
[0036]
根据实际工艺需要对步骤1完成的凝固模拟的铸件进行去约束操作,更加符合实际生产中叶片去约束工艺,将步骤1生成的*vdb和*p.dat文件拷贝至新文件夹,提取映射凝固阶段最终步的温度场和应力场,为了实现凝固 去约束阶段反变形,需要保证两阶段中网格节点的一致性,通过设置vacant模拟实际生产中约束去除。建立新的边界条件和运行参数,提交计算,完成精铸过程去约束阶段仿真。
[0037]
图3是去约束阶段提取映射温度场图;
[0038]
图4是去约束阶段部分约束模型图;
[0039]
步骤3:
[0040]
步骤1完成凝固阶段模拟,步骤2完成去约束阶段模拟,实现涡轮叶片精铸过程仿真,最后利用步骤1和2的结果文件进行反变形的,得到符合设计要求的模具型腔,导出步骤1凝固阶段的面网格文件,该文件包含模型网格的初始节点坐标,导出步骤2去约束阶段的后处理网格文件,该文件包含模型在经历凝固阶段 去约束阶段变形后的网格节点坐标。
[0041]
图5是涡轮叶片精铸全过程反变形优化系统图;
[0042]
步骤4:
[0043]
若步骤3中反变形模型精铸仿真后离散点,则不满足设计要求,需要在相同仿真参数下重复步骤1、步骤2和步骤3,直至符合设计要求。
[0044]
图6是通过反变形系统优化后的模型图。
再多了解一些
本文用于创业者技术爱好者查询,仅供学习研究,如用于商业用途,请联系技术所有人。