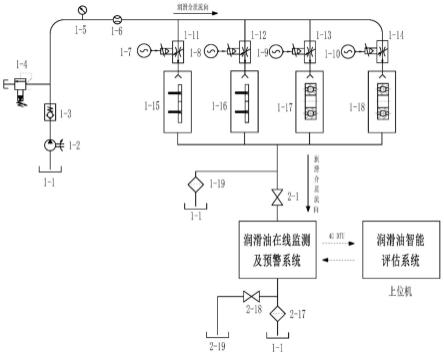
1.本发明涉及润滑油状态监测技术领域,特别是涉及一种可实现油液参数在线监测与智能评估的新型润滑系统。
背景技术:
2.润滑是降低零件表面磨损,预防设备故障最主要的方式。润滑系统具有润滑效率高、可靠性好的特点得到广泛应用,其原理为通过油泵将油箱里的润滑油泵送至机器的各个润滑点后,通过设计管路使得油液在重力作用下回流到油箱,形成多点式循环系统,在该系统中润滑油可以循环利用,在实现高效润滑的同时不会造成润滑油的大量浪费。但传统的润滑系统无法实现溢流保护、流量控制、按需供油等功能,一方面存在安全隐患,在系统管路堵塞时管路内压力急剧增大,引起设备故障,另一方面润滑油的过度使用使得润滑油氧化加剧,杂质颗粒浓度异常增加,大幅降低油品润滑性能与使用寿命。
3.润滑系统的润滑效率与润滑油的健康状态息息相关,失效后的润滑油无法满足润滑需求,其粘度、颗粒浓度等指标异常会导致各润滑点磨损、振动加剧,特别是对于精密机器,异常的磨损与振动会导致极大的误差,无法满足生产需求,并会导致机器使用寿命降低,带来极大的经济损失。目前,离线检测是判定润滑油健康状态最主要的方式,进行润滑油现场采样后将油液样本在实验室内利用相关分析设备进行离线检测,如检测润滑油的粘度、水分、杂质颗粒浓度等指标是否正常,但该方式存在严重的信息滞后性,无法快速发现润滑油存在的健康问题。
技术实现要素:
4.针对上述问题,本发明实施例提供了一种可实现油液参数在线监测与智能评估的新型润滑系统。
5.本发明实施的一方面,提供了一种可实现油液参数在线监测与智能评估的新型润滑系统,包括润滑油循环回路、润滑油在线监测及预警系统、上位机;
6.润滑油循环回路包括油箱,与油箱连接的润滑油管,在润滑油管上依次设置的定量泵、溢流阀、压力计、流量计、电控节流阀、油液喷嘴及第一过滤器;电控节流阀实现至各润滑点的润滑油流量控制,润滑油管中经过第一过滤器后回流至油箱的回油管段中并联接入润滑油在线监测及预警系统;
7.润滑油在线监测及预警系统由下位机、接入回油管段的旁路管道、dtu无线传输模块组成,旁路管道上依次设置有旁路开关阀、油液增压泵、粘度传感器、水分传感器、颗粒度传感器以及第二过滤器;下位机与粘度传感器、水分传感器以及颗粒度传感器通信连接,下位机与上位机通过dtu无线传输模块通信连接;
8.旁路开关阀打开后润滑油循环回路中的润滑油进入旁路管道,依次流经粘度传感器、水分传感器以及颗粒度传感器,最后经第二过滤器后回流至油箱中;
9.粘度传感器检测润滑油的粘度数据并将检测到的粘度数据发送至下位机,水分传
感器检测润滑油的水分数据并将检测到的水分数据发送至下位机,颗粒度传感器检测润滑油的大颗粒浓度数据和小颗粒浓度数据并将所检测到的大颗粒浓度数据和小颗粒浓度数据发送至下位机;
10.下位机接收各个传感器发送的粘度数据、水分数据、大颗粒浓度数据和小颗粒浓度数据后进行实时显示,并进行数据阈值判定,超出设定阈值时系统报警,同时将所接收到的各个数据发送至上位机;
11.上位机中内置有油液剩余使用寿命预估模型与油液健康状态智能评估模型;
12.上位机接收到下位机发送的数据后,针对接收到的粘度数据、水分数据、大颗粒浓度数据和小颗粒浓度数据中的每一个数据通过以下步骤s1-s3计算每一个数据对应的超出时间:
13.s1,确定n个数据,n个数据包括当前时间步t接收到的数据以及当前时间步t之前连续接收到的n-1个数据,将所确定的n个数据输入至预训练的油液剩余使用寿命预估模型,得到时间步t 1对应的预估数据;
14.s2,利用所得到的时间步t 1对应的预估数据更新确定的n个数据,并将更新后的数据输入至预训练的油液剩余使用寿命预估模型,得到时间步t 2对应的预估数据;
15.s3,参照s2进行迭代计算得到数据值大小超出设定阈值的时间步t m对应的预估数据,并根据时间步的步长和时间步t m计算预估数据的数值大小超出设定阈值的超出时间;
16.上位机计算每一个数据对应的超出时间后,确定计算得到的超出时间中的最短时间,并将所确定的最短时间作为润滑油的寿命发送至下位机进行显示;
17.上位机获取润滑油全寿命周期内的粘度数据、水分数据、小颗粒浓度数据、大颗粒浓度数据以及温差数据,并依据粘度数据、水分数据和小颗粒浓度数据将所获取的数据聚类为5类,5类数据按时间序列分别对应油液健康状态优,油液健康状态良,油液健康状态中,油液健康状态差,油液失效五个健康状态,温差数据为同一时间步下油温数据与现场温度数据的差值;
18.将所获取的5类数据以及各类数据对应的状态作为训练样本,对初始神经网络模型进行训练,得到油液健康状态智能评估模型;
19.上位机将实时接收到的粘度数据、水分数据、小颗粒浓度数据、大颗粒浓度数据以及温差数据输入油液健康状态智能评估模型得到当前润滑油的健康状态并发送至下位机进行显示。
20.与现有技术相比,本发明的有益效果在于:利用现场粘度传感器、水分传感器、颗粒度传感器实时采集润滑油的参数,实现在线监测参数变化,并通过神经网络建立油液参数数据变化在时间序列上的关联模型,并通过数据库中样本数据训练模型后,得到输入前n组数据输出n 1组数据的数学模型,反复迭代当预估数据超出油液参数设定阈值为止,通过迭代次数与采集时间间隔得出油液剩余使用寿命,实现实时在线监测的同时进行润滑油寿命预警。
21.可选的,下位机包括相互电连接的stm32f103c8t6主控芯片及串口屏,粘度传感器、水分传感器、颗粒度传感器基于rs485通讯协议与stm32f103c8t6主控芯片连接,stm32f103c8t6主控芯片通过dtu无线传输模块与上位机连接。
22.可选的,水分传感器采用jcw-1624油液水分在线监测传感器,在检测润滑油水分数据的同时检测润滑油的油温数据并发送至下位机;
23.润滑油在线监测及预警系统还包括设置在旁路管道附近的环境温度传感器,环境温度传感器与下位机通信连接,实时检测现场温度数据并将检测到的现场温度数据发送至下位机。
24.可选的,依据粘度数据、水分数据和小颗粒浓度数据将所获取的数据聚类为5类的步骤包括:
25.分别对粘度数据、水分数据和小颗粒浓度数据进行归一化处理,并以归一化处理后的粘度数据、水分数据和小颗粒浓度数据作为几何空间的x、y、z轴建立几何空间坐标;
26.在所建立的几何空间坐标中任选5个聚类中心,针对每一聚类中心以外的每一其他数据,以该数据与各个聚类中心的损失值最小原则进行聚类,得到5个聚类子集;
27.针对每一个聚类子集,利用该聚类子集中数据的平均值更新该聚类子集的聚类中心;
28.针对更新后的聚类中心以外的每一其他数据,以该数据与各个更新后的聚类中心的损失值最小原则进行聚类,得到5个聚类子集,并返回针对每一个聚类子集,利用该聚类子集中数据的平均值更新该聚类子集的聚类中心的步骤,直至达到预定迭代次数,以最小损失值对应的聚类结果作为最终聚类结果。
附图说明
29.此处所说明的附图用来提供对本发明的进一步理解,构成本技术的一部分,并不构成对本发明的限定。在附图中:
30.图1为本发明实施例提供的一种可实现油液参数在线监测与智能评估的新型润滑系统结构图;
31.图2为润滑油在线监测及预警系统结构示意图;
32.图3为本发明实施例提供的一种油液剩余使用寿命预测模型原理图。
具体实施方式
33.为使本发明的目的、技术方案和优点更加清楚明白,下面结合实施方式和附图,对本发明做进一步详细说明。在此,本发明的示意性实施方式及其说明用于解释本发明,但并不作为对本发明的限定。
34.参见图1和图2,本发明实施例提供的一种可实现油液参数在线监测与智能评估的新型润滑系统,润滑油循环回路中通过定量泵1-2将润滑油从油箱1-1中抽取出来,经单向阀1-3后流经压力计1-5与流量计1-6;溢流阀1-4为系统提供安全保障,在管路堵塞时确保系统不会因压力过大损坏元件;电控节流阀依次为:1-11、1-12、1-13、1-14可实现各支路油液流量控制,其依次分别受电信号:1-7、1-8、1-9、1-10驱动,电信号可以通过控制器如plc控制器输出用以控制电控节流阀开度,实现按需供油,全部闭合时系统受溢流阀1-4保护仍可正常运行;油液流经电控节流阀后经各润滑点油液喷嘴1-15、1-16、1-17、1-18至各润滑点,流经各个润滑点的润滑油经润滑油管汇聚后经过第一过滤器1-19过滤由回油管段回流至油箱1-1;
35.润滑油在线监测及预警系统,包括安装在箱体内的下位机、dtu无线传输模块2-11、与润滑系统中回油管段连通的旁路管道及辅助元件组成;dtu无线传输模块2-11利用元件安装架2-14固定在箱体内,旁路管道中在箱体内部分进油口为2-2,出油口为2-16,旁路管道上依次设置有旁路开关阀为2-1,位于箱体内部的油液增压泵2-3和传感器安装用元件2-5,第二过滤器2-17;传感器安装用元件2-5上安装颗粒度传感器2-6、粘度传感器2-7、水分传感器2-8;下位机与颗粒度传感器2-6、粘度传感器2-7以及水分传感器2-8通信连接,下位机与上位机通过dtu无线传输模块2-11通信连接;
36.旁路开关阀2-1打开后润滑系统中的润滑油进入旁路管道,依次流经颗粒度传感器2-6、粘度传感器2-7以及水分传感器2-8,最后经第二过滤器2-17后回流至油箱1-1;
37.粘度传感器2-7检测润滑油的粘度数据并将检测到的粘度数据发送至下位机,水分传感器2-8检测润滑油的水分数据并将检测到的水分数据发送至下位机,颗粒度传感器2-6检测润滑油的大颗粒浓度数据和小颗粒浓度数据并将所检测到的大颗粒浓度数据和小颗粒浓度数据发送至下位机;
38.下位机包括相互电连接的stm32f103c8t6主控芯片2-9、箱体门上的串口屏2-12、电压转换模块2-10以及220v电源接口2-15,220v电源接口2-15与电压转换模块2-10电连接,电压转换模块2-10与各个传感器、stm32f103c8t6主控芯片2-9、dtu无线传输模块2-11及串口屏2-12供电连接,粘度传感器2-7、水分传感器2-8、颗粒度传感器2-6基于rs485通讯协议与stm32f103c8t6主控芯片2-9连接,stm32f103c8t6主控芯片2-9通过dtu无线传输模块2-11与上位机连接,上位机可采用工业控制计算机。stm32f103c8t6主控芯片2-9主要实现提取传感器返还指令中的监测数据,根据传感器开发手册计算实际值并将计算结果分位转换ascii值发送至串口屏2-12。串口屏2-12设有数据实时显示,数据存储,数据变化曲线绘制,预报警判断,报警阈值设定等功能,并分区设定至各个显示界面,实现油液参数的在线智能监测。
39.下位机接收各个传感器发送的粘度数据、水分数据、大颗粒浓度数据和小颗粒浓度数据后在串口屏2-12上进行实时显示,同时将所接收到的各个数据发送至上位机;
40.上位机中内置有油液剩余使用寿命预估模型与油液健康状态智能评估模型;
41.上位机接收到各个数据后,针对接收到的粘度数据、水分数据、大颗粒浓度数据和小颗粒浓度数据中的每一个数据通过以下步骤s1-s3计算每一个数据对应的超出时间:
42.s1,确定n个数据,n个数据包括当前时间步t接收到的数据以及当前时间步t之前连续接收到的n-1个数据,将所确定的n个数据输入至预训练的油液剩余使用寿命预估模型,得到时间步t 1对应的预估数据;
43.s2,利用所得到的时间步t 1对应的预估数据更新确定的n个数据,并将更新后的数据输入至预训练的油液剩余使用寿命预估模型,得到时间步t 2对应的预估数据;
44.s3,参照s2进行迭代计算得到数据值大小超出设定阈值的时间步t m对应的预估数据,并根据时间步的步长和时间步t m计算预估数据的数值大小超出设定阈值的超出时间;
45.上位机计算每一个数据对应的超出时间后,确定计算得到的超出时间中的最短时间,并将所确定的最短时间作为润滑油的寿命发送至下位机进行显示。
46.实施中,可以在进油口2-2进口至油液增压泵2-3出口之间并联一支管路,支管路
上安装截流阀2-4,当旁通支路油压足够时,截流阀2-4打开,油液增压泵2-3不工作;当旁通支路油压不足时,截流阀2-4关闭,油液增压泵2-3运行为油液流通提供动力。
47.位于出油口2-16以及过滤器2-17之间的管道上设置有取样管路,取样管路上安装取样阀2-18,取样阀2-18打开后润滑油流入取样油箱2-19完成现场取样;
48.实施中,水分传感器2-8采用jcw-1624油液水分在线监测传感器,在检测润滑油水分数据的同时检测润滑油的油温数据并发送至下位机;
49.润滑油在线监测及预警系统还包括环境温度传感器2-13,环境温度传感器2-13与下位机通信连接,实时检测现场温度数据并将检测到的现场温度数据发送至下位机。
50.粘度传感器2-7采用jcv-1000型粘度传感器,粘度检测范围为0-1000cp,精度可达0.5cp;采用jcw-1624型水分传感器,水分检测范围为0.05%~5%(
±
0.1%),水分分辨率为100ppm,温度检测范围为5~ 95℃,温度分辨率为0.4℃;颗粒度传感器2-6采用gs-4212型铁磁磨损颗粒传感器,输出为大颗粒浓度与小颗粒浓度;环境温度传感器2-13采用sht20温湿度检测传感器,检测范围为-20℃- 60℃(
±
0.3℃),0%rh-100%rh(
±
3%rh)。
51.实施中,时间步可以理解为数据采样检测的时间节点,比如,时间步分别为2s、4s、6s
……
即分别在第2s、4s、6s
……
进行数据检测,时间步的步长即为相邻两个时间步之间的时间差,如上述举例中时间步的步长则为2s;超出时间即为时间步的步长与迭代计算时间步的数量的乘积,即步长与m的乘积。
52.油液剩余使用寿命预估模型可以利用润滑油全寿命周期内各个数据作为训练集对初始神经网络进行训练得到,比如,n可以取5,即以按时间变化的五组数据为输入,以后一组数据为输出建立前五组数据与后一组数据之间的神经网络模型,经多样本训练得出输入层矩阵与输出层矩阵,以计算得到的新监测数据为输入得出下一次数据变化结果,经反复迭代超出参数设定阈值时停止,并通过迭代次数与步长的乘积得出润滑油剩余使用寿命。
53.实施中,建立油液剩余使用寿命预估模型的核心是确定输入层至第一隐藏层的加权系数矩阵w1以及修正系数矩阵b1,第一隐藏层至第二隐藏层的加权系数矩阵w2以及修正系数矩阵b2,第二隐藏层至输出层的加权系数矩阵w3以及修正系数矩阵b3。参见图3,以粘度数据预测为例,数据库中存在油液全寿命变化周期内油液粘度数据随时间的变化数据,通过归一化对数据预处理,选定训练集样本,以时间序列中t1至t
10
对应粘度数据x1至x
10
为神经网络模型第一组输入,以t
11
对应的粘度数据x
11
为神经网络模型第一组输出,后以t2至t
11
对应的粘度数据为第二组输入,以t
12
对应的粘度数据x
12
为神经网络模型第二组输出,依次得出针对于粘度的剩余使用寿命预测模型的输入与输出样本;模型的第一层隐藏层节点为16,第二层隐藏层节点为10,在以tn至t
n 9
的粘度数据xn至x
n 9
为输入时,tn的粘度值至各隐藏层节点的权重为(ω
11
ω
12
……
ω
116
),t
n 1
至各隐藏层节点的权重为(ω
21
ω
22
……
ω
216
)依次类推即可得出输入层矩阵w1。第一隐藏层的第一节点到第二隐藏层的权重为(θ
11
θ
12
……
θ
110
),第二节点到第二隐藏层的权重为(θ2θ
22
……
θ
210
),依次得出,第十六节点到第二隐藏层的权重为(θ
161
θ
162
……
θ
1610
),以第一隐藏层第一节点到第十六节点到第二隐藏层的权重合并为w2。输出层为单节点,第二隐藏层第一节点至输出层的权重为γ1,第二隐藏层第二节点至输出层的权重为γ2,依次得出,第十节点至输出层的权重为γ
10
,合并为第二隐藏层至输出层权重矩阵w3。模型计算过程如下:
[0054][0055]
(y
11
′y12
′……y116
′
)=(s(y
11
) a1s(y
12
) a2……
s(y
116
) a
16
)
ꢀꢀꢀ
(1-2)
[0056][0057]
(z
11
′z12
′……z110
′
)=(s(z
11
) b1s(z
12
) b2……
s(z
110
) b
10
)
ꢀꢀꢀ
(1-4)
[0058]
(z
11
′z12
′……z110
′
)
·
(γ1γ2……
γ
10
)
t
=k
11
ꢀꢀꢀ
(1-5)
[0059]
x
11
=s(k
11
) c
ꢀꢀꢀ
(1-6)
[0060]
……
[0061][0062]
(y
n1
′yn2
′……yn16
′
)=(s(y
n1
) a1s(y
n2
) a2……
s(y
n16
) a
16
)
ꢀꢀꢀ
(1-8)
[0063][0064]
(z
n1
′zn2
′……zn10
′
)=(s(z
n1
) b1s(z
n2
) b2……
s(z
n10
) b
16
)
ꢀꢀꢀ
(1-10)
[0065]
(z
n1
′zn2
′……zn16
′
)
·
(γ1γ2……
γ
10
)
t
=k
n 10
ꢀꢀꢀ
(1-11)
[0066]
x
n 10
=s(k
n 10
) c
ꢀꢀꢀ
(1-12)
[0067]
上述1-2和1-4为隐藏层节点输出函数,a、b则为偏置系数;模型中输入层与输出层均已知,激活函数s(x)为(1-13),在初始权值已知的情况下可以通过误差计算函数(1-14)得出真实值与预测值的误差e,
[0068][0069][0070]
将误差e对各加权系数求偏导,用得到的偏导值与学习率η的乘积作为权值修订系数δω,以修正ω
11
,θ
11
,γ
11
,a1,b1,c为例:
[0071][0072]
[0073][0074][0075][0076][0077]
其中,
[0078][0079][0080][0081][0082][0083][0084]
其中,
[0085]kn 10
=z
n1
′
·
γ1 z
n2
′
·
γ2
…
z
n16
′
·
γ
10
ꢀꢀꢀ
(1-27)
[0086]zn1
=y
n1
′
·
θ
11
y
n2
′
·
θ
21
…
y
n16
′
·
θ
161
ꢀꢀꢀ
(1-28)
[0087]yn1
=xn·
ω
11
x
n 1
·
ω
21
…
x
n 9
·
ω
101
ꢀꢀꢀ
(1-29)
[0088]
权重矩阵中其余系数w1,w2,w3以及偏置系数矩阵b1,b2,b3与ω
11
,θ
11
,γ
11
修正过程类似。修正后的权重矩阵w1′
,w2′
,w3′
与偏置系数矩阵b1′
,b2′
,b3′
如下
[0089][0090][0091]
w3′
=(γ1′
γ2′……
γ
10
′
)
t
ꢀꢀꢀ
(1-32)
[0092]
b1′
=(a1′
a2′……a16
′
)
t
ꢀꢀꢀ
(1-33)
[0093]
b2′
=(b1′
b2′……b10
′
)
t
ꢀꢀꢀ
(1-34)
[0094]
b3′
=(c
′
)
ꢀꢀꢀ
(1-35)
[0095]
达到迭代次数模型计算停止,得出预测误差最小的输入层权重矩阵w1与偏置系数矩阵b1,隐藏层权重矩阵w2与偏置系数矩阵b2,输出层权重矩阵w3与偏置系数矩阵b3。以权重矩阵与偏置系数矩阵建立网络模型,新输入采集的十组粘度数据样本,预估下一次粘度变化结果,经反复迭代计算当预估粘度值超出设定阈值时停止,以迭代次数与步长的乘积作为粘度超出阈值的超出时间。以相同算法分别建立针对于水分数据、大颗粒浓度数据和小颗粒浓度数据的油液剩余使用寿命预估模型,并分别计算油液水分数据,大颗粒浓度数据和小颗粒浓度数据超出设定阈值的超出时间,对比粘度数据的计算结果,以最短时间作为剩余使用寿命,实现油液剩余使用寿命的智能预测。
[0096]
实施中,上位机进行润滑油使用寿命预估的同时还可以进行润滑油健康状态的评测,具体的,上位机获取润滑油全寿命周期内的粘度数据、水分数据、小颗粒浓度数据、大颗粒浓度数据以及温差数据,并依据粘度数据、水分数据和小颗粒浓度数据将所获取的数据聚类为5类,5类数据分别对应油液健康状态优,油液健康状态良,油液健康状态中,油液健康状态差,油液失效五个健康状态,温差数据为同一时间步下油温数据与现场温度数据的差值;
[0097]
将所获取的5类数据以及各类数据对应的状态作为训练样本,以各参数在线监测数据为神经网络输入,以其对应的油液健康状态为神经网络输出,输入层节点数为5,第一隐藏层的节点数为10,第二隐藏层节点为8,输出层节点数为5,对初始神经网络模型进行训练,得到油液健康状态智能评估模型,具体训练过程可参照前述用于粘度数据的油液剩余使用寿命预估模型训练过程,两者原理相同在此不再赘述;
[0098]
上位机将实时接收到的粘度数据、水分数据、小颗粒浓度数据、大颗粒浓度数据以及温差数据输入油液健康状态智能评估模型得到当前润滑油的健康状态并发送至下位机进行显示。
[0099]
实施中,依据粘度数据、水分数据和小颗粒浓度数据将所获取的数据聚类为5类的步骤包括:
[0100]
分别对粘度数据、水分数据和小颗粒浓度数据进行归一化处理,并以归一化处理后的粘度数据、水分数据和小颗粒浓度数据作为几何空间的x、y、z轴建立几何空间坐标;
[0101]
在所建立的几何空间坐标中任选5个聚类中心,针对每一聚类中心以外的每一其他数据,以该数据与各个聚类中心的损失值最小原则进行聚类,得到5个聚类子集;损失值计算函数可以采用:k=5,ii表示聚类中心,x表示聚类中心以外的其他数据;
[0102]
针对每一个聚类子集,利用该聚类子集中数据的平均值更新该聚类子集的聚类中心;
[0103]
针对更新后的聚类中心以外的每一其他数据,以该数据与各个更新后的聚类中心的损失值最小原则进行聚类,得到5个聚类子集,并返回针对每一个聚类子集,利用该聚类子集中数据的平均值更新该聚类子集的聚类中心的步骤,直至达到预定迭代次数,以最小损失值l对应的聚类结果作为最终聚类结果。
[0104]
上位机将润滑油剩余使用寿命的计算结果与健康状态的评估结果通过dtu模块发送至下位机,下位机中的串口屏中设有显示界面,显示界面中有指示灯与各项数据超出设定阈值的超出时间,最短的超出时间作为剩余使用寿命。指示灯在油液健康状态评估结果为优和良时指示灯亮绿灯,在健康状态评估结果为中和差时指示灯亮黄灯,在健康状态评估结果为油液失效时亮红灯。
[0105]
以上所述仅为本发明的较佳实施例而已,并非用于限定本发明的保护范围。凡在本发明的精神和原则之内所作的任何修改、等同替换、改进等,均包含在本发明的保护范围内。
再多了解一些
本文用于创业者技术爱好者查询,仅供学习研究,如用于商业用途,请联系技术所有人。