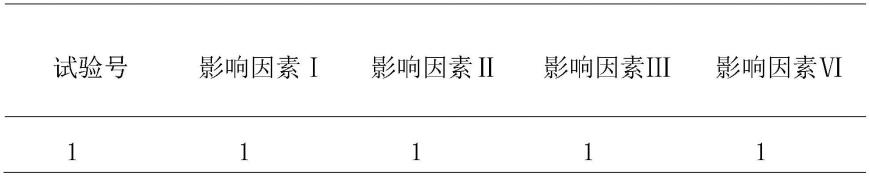
1.本发明涉及材料领域技术,尤其是指一种通过调节冷轧散热控制不锈钢平面度的制造方法。
背景技术:
2.冷轧板带是钢铁企业的重要产品,在钢铁生产总量中的比重越来越高,是生产生活必不可少的原材料,已经被普遍地应用在航空工业、汽车生产业、家电业、电工制造业、精密仪器制造等各行业。现如今我国已经成为世界上冷轧装备产能最大的国家,冷轧带钢的生产规模已经成为衡量一个国家钢铁工业发展水平一个重要的标志。但是近些年,我国处于钢铁的转型期,逐步淘汰落后的产能,同时冷轧带材需求呈现饱和的局面,高质量的带材产品变得越来越有竞争力,越来越受到人们的重视。就企业本身而言,为了提高企业长期的竞争力,在高品质板带材市场占领一席之地,先后增大了研发力度,争取使我国冷轧板带材产品走向国际化、高端化。
3.板形是衡量冷轧板带质量的重要指标,带钢板形的好坏将直接影响带钢质量的高低。常用的板形控制方法可以消除一些常见的非高次项板形缺陷,但还不足以消除局部高次浪形的板形缺陷。当轧制冷轧板时,经常会出现轧辊局部“热点”的现象,这些局部的“热点”是在带钢轧制中,轧辊受到了不对称的轧制负载或者轧辊辊身不同位置受到的温度不均匀导致的。这些局部的“热点”就会使得轧辊产生局部的热凸,因此就会影响板带的质量。控制轧辊局部的热凸度,提高带材的表面质量起到至关重要的作用,尤其是宽带冷轧机的生产中。
4.目前在应用比较广泛的控制板形的方法有轧辊倾斜、支撑辊、工作辊弯辊以及特殊轧机(例如cvc、hc等轧机)。但是当板带产生局部板形问题时,这些板形控制方法只能对这些偏差进行小范围减少,无法解决本质上的问题,因此,有必要研究一种方案以解决上述问题。
技术实现要素:
5.有鉴于此,本发明针对现有技术存在之缺失,其主要目的是提供一种通过调节冷轧散热控制不锈钢平面度的制造方法,其通过改善工作辊局部的对流换热,控制轧辊的温度,极大改善了冷轧不锈钢板带的板型。
6.为实现上述目的,本发明采用如下之技术方案:
7.一种通过调节冷轧散热控制不锈钢平面度的制造方法,包括有以下步骤:
8.(1)对轧机的轧辊进行精磨、抛光,精度控制0.003μm以下;
9.(2)冷轧:采用步骤(1)的轧机对不锈钢板带进行冷轧,在正常冷轧工艺上增加1-3次道次,通过多次冷轧,将冷轧时产生的热量分散;在冷轧过程中,将冷轧速度控制在80m/min-100m/min,喷嘴距离控制为l=26mm,喷嘴到工作辊的距离控制在140mm以内,喷射梁旋转角度为170℃,冷却液喷射速度为25m/s,冷却液的温度控制在20℃,并定期地更换冷却
液,以提高冷却液的冷却效率。
10.作为一种优选方案,所述轧机为二十辊森基米尔轧机,轧辊的外径为40mm。
11.作为一种优选方案,所述步骤(2)中,在一定轧制条件下控制轧制力,其步骤如下:
12.(2.1)根据原料的厚度h,原料公差δ,确定原始板凸度;
13.(2.2)计算轧辊刚性系数kr、热凸度y
t
,根据原始辊型凸度,建立轧制力与板厚关系式:
14.p=kr(δ/h)hi kr(y
t
w)
ꢀꢀꢀ
(1)
15.(1)式中,hi—第i道次轧件厚度;w—原始辊型凸度;
16.(2.3)由成品厚度hn来确定轧制压力pn,在满足各种约束的条件下,按δhn求满足板型良好的轧制压力p
n-1
,如此递推来确定各道次压下量。
17.本发明与现有技术相比具有明显的优点和有益效果,具体而言,由上述技术方案可知:
18.通过将轧辊的精度控制0.003μm以下,并配合对冷轧速度、喷嘴距离、喷嘴到工作辊的距离、喷射梁的旋转角度、冷却液喷射速度和冷却液的温度进行控制,使得不锈钢板带具有良好的板型,可以用于对板型有很高要求的高、精、尖产品,并且,板型抗温性稳定,在经高温烘烤后,其板型变化较小;本发明工艺可以很好地解决国内冷轧板产能过剩以及冷轧薄板对进口的依赖;本发明工艺可扩展冷轧板带的深加工产业链,达到冷轧资源的扩大和减量化应用;以及,本发明工艺生产的产品,可用于汽车制造、电气产品、机车车辆、航空、精密仪表、食品罐头等,减少残余应力对产品的影响。
19.为更清楚地阐述本发明的结构特征和功效,下面结合附图与具体实施例来对本发明进行详细说明。
附图说明
20.图1是本发明之较佳实施例中轧辊温度与轧制速度的变化曲线图;
21.图2是本发明之较佳实施例中喷嘴间距不同时冷却液的速度与温度的变化曲线图;
22.图3是本发明之较佳实施例中喷嘴间距不同时轴向长度与温度的变化曲线图;
23.图4是本发明之较佳实施例中冷却液粘度值与表面换热系数的变化曲线图;
24.图5是本发明之较佳实施例中冷却液粘度值与温度的变化曲线图;
25.图6是本发明之较佳实施例中喷嘴到辊面距离与表面换热系数的变化曲线图;
26.图7是本发明之较佳实施例中喷嘴中心线的角度示意图;
27.图8是本发明之较佳实施例中喷嘴梁角度与表面换热系数的变化曲线图;
28.图9是本发明之较佳实施例中冷却液喷射速度与表面换热系数的变化曲线图;
29.图10是本发明之较佳实施例中冷却液温度与表面换热系数的变化曲线图。
具体实施方式
30.本发明揭示了一种通过调节冷轧散热控制不锈钢平面度的制造方法,包括有以下步骤:
31.(1)对轧机的轧辊进行精磨、抛光,精度控制0.003μm以下;所述轧机为二十辊森基
米尔轧机,轧辊的外径为40mm。
32.(2)冷轧:采用步骤(1)的轧机对不锈钢板带进行冷轧,在正常冷轧工艺上增加1-3次道次,通过多次冷轧,将冷轧时产生的热量分散;在冷轧过程中,将冷轧速度控制在80m/min-100m/min,既控制了热量的产生速率,让轧辊的温度不过高,同时保证一定的生产效率;喷嘴距离控制为l=26mm,喷嘴到工作辊的距离控制在140mm以内,喷射梁旋转角度为170℃,冷却液喷射速度为25m/s,冷却液的温度控制在20℃,并定期地更换冷却液,以提高冷却液的冷却效率。
33.基于轧辊受热膨胀,通过对板型监控而调整下压量及轧制道次以保持板型的平直度,为达到板型良好,所述步骤(2)中,在一定轧制条件下控制轧制力,其步骤如下:
34.(2.1)根据原料的厚度h,原料公差δ,确定原始板凸度;
35.(2.2)计算轧辊刚性系数kr、热凸度y
t
,根据原始辊型凸度,建立轧制力与板厚关系式:
36.p=kr(δ/h)hi kr(y
t
w)
ꢀꢀꢀ
(1)
37.(1)式中,hi—第i道次轧件厚度;w—原始辊型凸度;
38.(2.3)由成品厚度hn来确定轧制压力pn,在满足各种约束的条件下,按δhn求满足板型良好的轧制压力p
n-1
,如此递推来确定各道次压下量。
39.冷轧的速率的大小直接影响冷轧产生的热量,决定了轧辊的温度,并且温度变化剧烈,不易于板型的稳定控制,轧辊温度控制在55℃以下,轧辊热凸度变化较小。如图1所示,轧辊温度均会随着速度的升高而升高,轧制初始速度每提高50m/min,温度就会平均升高5.6℃,将冷轧速度控制在80m/min-100m/min左右,将温度控制在50℃-60℃。
40.喷嘴间距不同时,流动过程中射流之间的交互作用的强烈程度就不同,到达轧辊表面的流量就会有所不同。如图2所示,可以看出当喷嘴距离l=26mm时,由于射流之间的交叉干涉明显强于l=52mm时,因此单位时间内液体到达冲击区的流量变大,冷却效果会好于距离l=52mm。同时随着冷却液速度的升高,喷嘴距离l=26mm比l=52mm的冷却效果更显著。当速度小于20m/s时,喷嘴距离l=26mm比距离l=52mm时,冷却区的平均温度低将近1℃,而当速度大于20m/s时,喷嘴距离为26mm时的冷却效果开始大大强于距离为52mm时,此时冷却区的平均温度相差2℃左右。因此分段冷却控制中喷嘴之间距离对轧辊的温度变化影响显著。
41.由于射流之间的干涉作用,两射流之间壁面射流区和上喷形成区被压缩,射流直接冲击区变大,因此喷嘴距离的不同就会导致轧辊横向方向冷却液喷射的均匀程度,由图3可知,当喷嘴距离l=26mm轧辊横向方向冷却更加均匀,并且温差约为1.1℃。所以当工作辊局部温度需要快速地降低,以此来减少轧辊凸度给板形带来的影响时,喷嘴间距l较小的喷射方案对局部热凸度响应迅速。
42.冷却液的粘度不同,流体微观分子之间的微观分子之间的约束力就会不同,因此就会导致其换热能力差别很大。如图4所示,当冷却液的粘度值从0.001pa.s增加到0.002pa.s时,由于分子间的粘度变大,工作辊表面的平均换热系数明显减小,从7046(w/m2.k)降低到4336(w/m2.k),几乎呈线性降低。但是当冷却液粘度值达到0.002pa.s以后,流体的粘度变大,流体微观分子之间的约束力变的很强,在流速相同的情况下要想发展成为湍流状态变得很困难,此时,冷却液的冷却效率会下降地很慢。
43.如图5所示,粘度值在0.001pa
·
s的基础上,每提高0.0005pa
·
s,相应的喷射区轧辊的温度就会降大约1.3℃。因此定期地检查冷却液的质量,这样才能提高冷却效率,避免对带材生产产生不利的影响。
44.喷嘴到轧辊距离以及喷射梁旋转角度直接影响冷轧系统的热交换。喷嘴到达轧辊表面的距离不同,喷嘴的直喷面积就会有所不同,冷却液到达轧辊表面时的对轧辊的冲击也会有所,不同其距离的大小会影响对轧辊的换热,轧辊表面的换热系数就会有所差异。如图6所示,当距离少于140mm时,工作辊表面的平均换热系数随着距离的增大,变化范围不大;当距离超过140mm-150mm时,液体喷射到轧辊的速度明显减少,对流效果变差,其换热能力明显减小;当距离超过150mm继续增大时,工作辊表面的平均换热系数随着距离的增大缓慢减小。所以喷嘴到工作辊的距离应该控制在140mm以内。
45.如图7所示,把喷嘴中心线与水平线的夹角定义为喷射梁的选择角度。喷射梁旋转的角度影响喷嘴与工作辊直喷的位置,位置不同轧辊表面受到的冲击压力就会不同,其附面层就会有很大差别,因此就会对换热系数产生很大影响。如图8所示,当喷射梁旋转角度165℃时,衰减幅度最大;当喷射梁旋转角度达到170℃时,工作辊表面的平均换热系数达到最大值8294(w/m2.k);当角度大于170℃时,工作辊表面的平均换热系数开始降低。喷嘴倾斜角为160℃和180℃时,工作辊表面的平均换热系数相当,约为7000(w/m2.k)。因此在设计喷射梁旋转角度时把170℃作为最佳的选择。
46.热量交换是通过喷嘴喷射冷却液到轧辊表面来实现的,因此,喷嘴的压力不同喷嘴喷出的液体流速就会不同,压力越大流速越大,单位时间内冷却液的喷射量就会变大,因此冷却液的冷却速度的对冷却液与轧辊之间的换热有很大影响。如图9所示,当冷却液的速度从10m/s增加到25m/s时,随着流速的增大,使得流体的雷诺数增大,单位时间内轧辊表面获得的流量变大,流体的湍流趋势加强,因此,换热能力加强,换热系数随之增大从3634(w/m2.k)增大到7046(w/m2.k);当速度从25m/s增大到30m/s时换热系数变化不大,稳定在7000(w/m2.k)左右;因为当流速继续增加时,流体受到的阻力变大程度大于流速增加的程度,此时增大流速对换热系数的影响逐渐变小。
47.每当冷却液的喷射速度值提高5m/s时,相应的喷射区轧辊的温度就会降大约1.1℃。
48.轧辊工作时的温度不同,因此需要不同温度的冷却液进行冷却,冷却液的温度在很大程度上影响冷却的效率。在一定条件下,冷却液温度越低,其冷却效率越高,对应的换热系数也会越大。如图10所示,当温度从20℃增加到25℃时,由于温度的升高,冷却液的粘度值迅速变大,工作辊表面的平均换热系数变化较大,由7686(w/m2.k)减少到7046(w/m2.k);当温度从26℃增加到29℃时,此时冷却液粘度值变化不明显,工作辊随着冷却液温度的增加缓慢减小;当冷却液温度超过29℃时,随着轧辊与冷却液温度的差值变小,轧辊表面的平均换热系数缓慢减小。因此可以看出在温度低的情况下,减小温度对换热系数的增大比较明显,而在温度较高的情况下,减小温度对换热系数影响逐渐变小。
49.在做实验的时候,多因素,多变量的情况很多,如果把每种因素的每一个变量都通过实验的方法得到了话,总的试验次数将会成幂指数增长。对于面临这种复杂的实验时,正交试验是一个行之有效的方法。从规律中可以看出在小范围的变化中,喷嘴距离轧辊的距离对对流换热系数的影响很小。在生产实际中,喷射梁的倾斜角度一般是固定不变的,只有
冷却液的温度、速度、粘度值和轧辊的温度是变化的,因此对这四个可变量进行正交实验分析。在这四个因素中取三个有代表性规律的实验条件按照l9(34)正交表安排实验:
50.l9(34)正交表
[0051][0052][0053]
把冷却液温度、速度、粘度值和轧辊温度分为三个位级,各因素的位级取值如表所示:
[0054]
各因素的位级取值
[0055][0056]
正交试验表的最右端可以用热流密度值代表试验的性能优劣,表中给出了各个因素位级之和,以及由每个因素的位级和得到的极差。并且把这四个因素的极差由大到小进行排序,如表所示:
[0057]
正交试验表
[0058][0059]
[0060]
当冷却液温度为23℃时,对流换热值比温度为26℃和29℃都要大;冷却速度为25m/s时,对流换热值要明显大于速度为15m/s和20m/s;冷却液粘度值为0.001pa
·
s时,对流换热值要大于粘度为0.001 5pa
·
s和0.002pa
·
s;另外轧辊的温度值变大会大大增强轧辊和冷却液之间的换热系数。因此可以看出在单一因素分析时只能得到每一个因素的最优值,而各因素影响对流换热的大小则不能显示出来。正交试验中每列的极差是对各因素对试验指标的影响大小进行排序,极差大说明该因素活泼,它的变化对结果影响比其他因素大。可以看出四个因素对对流换热的影响排序,影响最大的是轧辊的温度,其次是冷却液的粘度值,最小的是冷却液温度,冷却液的速度影响位于冷却液粘度值和温度之间。其中冷却液的粘度值和轧辊的温度影响对流换热能力几乎相当。
[0061]
在提高换热系数方面,冷却液自身的粘度潜力最大。当轧辊的温度变大时,在其他条件相同的情况下冷却液的冷却效果会有所加强,这样容易使得轧辊尽早进入稳定状态,提高轧制效率。喷射速度对换热系数的影响也是很大的,当喷射速度增大时,单位时间喷射的流量就会变大,冷却效果就会越好。但是受到客观条件的限制喷射速度不能一直增大,冷却液的粘度值也不能无限制的减小,因此当需要调整时需要通过每个因素的互相协调来完成,当冷却液的粘度值确定时可以通过增大速度,加大单位时间的流量来增大对流换热。
[0062]
以上描述了冷却液性质、喷射梁旋转角度、喷嘴与工作辊之间的距离对对流换热系数的影响规律,并得到了各因素的最优值。运用正交试验的方法得出了冷却液温度、冷却液速度、冷却液粘度值和轧辊温度这四个因子对换热系数的影响程度及排序。
[0063]
下面采用以下实施例验证本发明的有益效果:
[0064]
优化工艺前后,平面度数据:(以0.15mm 316li为例)
[0065][0066]
优化工艺前,平面度基本在在0.45-0.75mm,优化工艺后,平面度基本稳定在0.2-0.25mm,板型改善效果良好。
[0067]
冲床制样130mm*70mm,在220℃烘烤45min,测量前后平面度变化差异:(以0.15mm 316li为例)
[0068][0069][0070]
220℃烘烤45min,前后平面度差异基本上小于或等于0.05mm,说明板型稳定,应力比较均匀。
[0071]
以上所述,仅是本发明的较佳实施例而已,并非对本发明的技术范围作任何限制,故凡是依据本发明的技术实质对以上实施例所作的任何细微修改、等同变化与修饰,均仍属于本发明技术方案的范围内。
再多了解一些
本文用于创业者技术爱好者查询,仅供学习研究,如用于商业用途,请联系技术所有人。