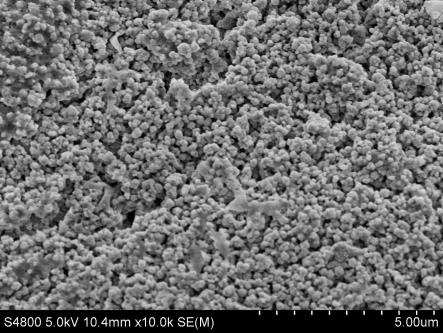
1.本发明属于膜材料的制备领域,具体涉及一种金属基陶瓷复合膜的修补工艺。
背景技术:
2.金属基陶瓷复合膜是由具有高强度、高孔隙率、大孔径的金属支撑体与小孔径的陶瓷膜层经高温烧结制备而成。金属基陶瓷复合膜具备可焊接、耐高温、耐高压、耐酸碱腐蚀、使用寿命长且环保易清洗等优点,在膜过滤分离技术领域占据重要地位。随着石油化工产业的高速发展,金属基陶瓷复合膜的应用领域越加广泛。因而,为了提高金属基陶瓷复合膜的性能和使用寿命,需要在原有技术工艺的基础上,不断改进发展新工艺。
3.金属基陶瓷复合膜的陶瓷涂层与金属基体材料的结合主要为分子力结合,结合强度低,膜层附着力较差,易出现脱落。另外,金属基体与陶瓷粉料两种不同材料的热膨胀系数差异较大且金属基体表层存在缺陷,在高温烧结过程中膜层易开裂,进而影响膜材料的性能和使用寿命。例如,专利cn200510034021.6以有机金属化合物为前驱体,形成金属氧化物溶胶并负载于金属基体表面经热处理制备得到金属基陶瓷复合膜。专利cn02803848.7将金属氧化物与溶剂、添加剂混合得到悬浮液,将悬浮液喷涂于金属基体表面,经热处理后制备得到金属基陶瓷复合膜。上述两种制备技术为金属基陶瓷复合膜较为常见的制备方法,将涂膜液经浸渍、喷涂、刷涂或溶胶凝胶技术与金属基体复合制备得到金属基陶瓷复合膜,制备得到的膜层附着力较差、陶瓷膜层与金属基体的结合强度较低,膜层易脱落。
4.为提高陶瓷膜层的附着力、增加陶瓷膜层与金属基体的结合强度,专利cn200810020318.0在陶瓷层与不锈钢基体间添加一层金属粉末,与陶瓷层共烧。金属粉末即可起到粘结剂的作用又可以修补不锈钢基体上的缺陷同时不影响膜层的过滤精度。该方法通过高温使金属粉末熔融包裹陶瓷粉末,虽可有效提高膜层与金属基体的结合强度,但温度过高导致陶瓷膜层易出现开裂;而降低烧结温度,金属粉末难以熔融完全,陶瓷膜层附着力较低,陶瓷膜层与金属基体结合强度不能有效提升。因此,目前尚无金属基陶瓷复合膜的规模化生产工艺。
技术实现要素:
5.为了实现高性能金属基陶瓷复合膜材料的规模化生产,本发明技术在现有技术的基础上进行技术开发,以解决现有技术在制备过程中存在的主要问题,陶瓷膜层附着力差。众所周知,高温烧结是可以将陶瓷与金属进行烧结的,如热喷涂工艺、共烧结工艺等,在接近熔融状态下是可以实现金属与陶瓷粉末的连接,但是在此温度下的膨胀系数不匹配是关键问题。温度过高,陶瓷膜层易开裂,温度降低,膜层与金属基体结合强度低。本发明技术的解决思路是先通高温过度烧结解决附着力差的问题,再提供后修补工艺实现性能提升。本发明具体是通过提高共烧结温度使得陶瓷膜层与金属基体实现高强度连接,烧结温度比常规烧结温度提高50 ~ 200 ℃,再通过低温修补工艺实现膜层孔径修复与控制,最终获得高性能金属基陶瓷复合膜材料。本发明的基本工艺是在大孔金属基体表面添加一层金属粉
末,得到金属粉末修饰的金属基体,将陶瓷粉末a制备成悬浮液,均匀涂敷于金属粉末修饰的金属基体表面,形成带有陶瓷粉末涂层的胚体,经高温共烧结后得到带有裂纹的高强度金属基陶瓷复合膜材料,再利用平均粒径为陶瓷膜层粉末a平均粒径0.1 ~ 0.8倍的陶瓷粉末b制备成修补陶瓷膜层的浆料,采用填缝隙工艺将前述浆料填充至陶瓷膜的裂缝中,再进行表面清洗后干燥,制备得到裂缝被陶瓷粉末b填充的表面平整、均匀的金属基陶瓷复合膜材料,最后再结合溶胶凝胶技术进行表面修饰经低温烧结制备得到修补的金属基陶瓷复合膜。
6.本发明解决了金属基陶瓷复合膜制备过程中陶瓷膜层与金属基体结合强度低、膜层易出现开裂缺陷等问题。此方法通过结合现有技术研究的基础上,对现有技术进行改进,采用过温共烧技术有效提高金属基体与陶瓷膜层的结合强度,再通过填缝隙工艺对高温过烧后陶瓷膜层的裂纹进行填补,将陶瓷粉末(b)填充在表层裂纹以及表层孔隙中,再表面清洗去除陶瓷膜层表面多余粉料,结合溶胶凝胶技术低温烧结制备得到完整无缺陷的金属基陶瓷复合膜,工艺简单条件可控,可适用于工业化生产。
7.本发明的技术方案是:一种金属基陶瓷复合膜的修补工艺,包括以下步骤:步骤1:将金属粉末与添加剂混合形成悬浮液,均匀涂敷于多孔不锈钢基体表面,干燥后制备得到金属粉末粘结层;步骤2:将陶瓷粉末a与添加剂混合形成悬浮液,均匀涂敷于步骤1中制备得到的带有金属粉末粘结层的基体表面,形成带有陶瓷粉末涂层的胚体;步骤3:将步骤2中制备得到的带有陶瓷粉末涂层的胚体在一定条件下热处理,即可制备得到带有裂纹的金属基陶瓷复合膜材料;步骤4:将陶瓷粉末b与添加剂混合形成修补陶瓷膜层的浆料,采用填缝隙工艺将前述浆料填充至陶瓷膜的裂缝中,再进行表面清洗后干燥,制备得到裂缝被陶瓷粉末b填充的金属基陶瓷复合膜材料;步骤5:以有机化合物或无机金属化合物为前驱体制备涂膜液溶胶,将步骤4制备得到的金属基陶瓷复合膜材料的膜层浸渍于溶胶内,经干燥后热处理制备得到修补的金属基陶瓷复合膜。
8.优选步骤1中所述的金属粉末为不锈钢或镍合金粉末中的一种;所述金属粉末的平均粒径均为1 ~ 50 μm;所述添加剂种类为聚酰亚胺、pva、pvb、甲基纤维素中的一种;所述的悬浮液中金属粉末的质量分数为10 ~ 70 %;所述涂敷方法为喷涂、浸渍或刷涂。本方法结合先前技术人员在金属基体表面添加金属粉末利用金属粉末在高温烧结过程中软化包裹陶瓷粉料,提高粉料间、粉料与基体间的结合力。
9.优选步骤2中所述的陶瓷粉末a为氧化锆、氧化铝、氧化钛、氧化硅或钇稳定氧化锆;所述陶瓷粉末的平均粒径均为0.1 ~ 5 μm;所述添加剂种类与步骤1中一致;所述的悬浮液中陶瓷粉末的质量分数为5 ~ 50 %;步骤2中所述的涂敷方法与步骤1中一致。
10.优选步骤3中所述的热处理操作条件为在真空、还原、惰性气氛条件下,1000 ~ 1500 ℃烧结,保温1 ~ 3 h。本发明采用高温过烧,有利于金属粉末软化与陶瓷膜层粉末烧结,实现金属基体与陶瓷膜层的有效结合。
11.优选步骤4中所述的陶瓷粉末b陶瓷粉末种类与步骤2中一致;所述的添加剂种类
与步骤1中一致;所述的修补陶瓷膜层的浆料中陶瓷粉末b质量分数为1 ~ 20 %。本发明选用平均粒径为陶瓷粉末a平均粒径0.1 ~ 0.8倍的陶瓷粉末b对带有裂纹的金属基陶瓷复合膜材料进行表面裂纹填补及表层修饰,粒径较小的陶瓷粉末在陶瓷膜层表面及缝隙中形成修饰填充层再通过表面清洗去除膜层表面多余粉末,制备得到裂缝被陶瓷粉末b填充的金属基陶瓷复合膜材料。
12.优选步骤4中所述的涂膜方法为刷涂法、过滤法或真空抽吸法。本发明选用刷涂法、过滤法或真空抽吸法,对带有裂纹的金属基陶瓷复合膜材料进行缝隙填充及修饰。在利用刷涂法、过滤法或真空抽吸法进行缝隙填充及表面修饰时,小粒径的陶瓷粉末颗粒在毛细吸力或压力的作用下均匀填充在缝隙中,再将陶瓷膜层表面多余的陶瓷粉末清洗干净,即可得到裂缝被陶瓷粉末b填充的金属基陶瓷复合膜材料。
13.优选步骤5中所述的有机化合物为正丁醇铝、正硅酸四乙酯;所述的无机金属化合物为alcl3·
6h2o、al(no3)3·
6h2o、na2sio3、ti(so4)2或zrocl2;所述的溶胶中有机化合物或无机金属化合物的质量分数为5 ~ 15 %。本发明结合溶胶凝胶技术对裂缝被陶瓷粉末b填充的金属基陶瓷复合膜材料进行表面修饰,同时利用凝胶缩合提高膜层间的结合力。
14.优选步骤5中所述的热处理操作条件为真空、还原、惰性气氛条件下,400 ~ 600 ℃烧结,保温0.5 ~ 1.5 h。本发明将修补后经溶胶凝胶修饰后的膜层采用低温烧结,有利于节约成本同时有效防止因温度过高导致膜层收缩开裂。
15.此方法采用过温共烧技术,利用金属粉末高温熔融浸润陶瓷涂层提高金属基体与陶瓷膜层的结合力,同时金属粉末可修饰金属基体表面存在的缺陷。在过温共烧结后,制备得到带有裂纹的金属基陶瓷复合膜材料,利用平均粒径为陶瓷粉末(a)平均粒径0.1 ~ 0.8倍的陶瓷粉末(b)对带有裂纹的金属基陶瓷复合膜材料进行缝隙填补,粒径较小的陶瓷粉末在陶瓷膜层表面及裂缝中形成修饰填充层,再通过表面清洗去除陶瓷膜层表面多余粉末,得到裂缝被陶瓷粉末b填充的金属基陶瓷复合膜材料。最后利用溶胶凝胶技术再对裂缝被修补填充后金属基陶瓷复合膜材料表面进行修饰,在提高膜层结合力的同时制备得到修补后完整无缺陷的金属基陶瓷复合膜。选择使用粒径更小的陶瓷粉体是为了确保修补后修饰位置的膜层孔径与原膜层的孔径保持一致。由于原膜层陶瓷粉末已经发生过温烧结,其孔径已小于未烧结时粉末堆积的孔径;而修补位置的膜层是依靠溶胶凝胶发生烧结产生的粘结,其本身颗粒未发生烧结,因此孔径与陶瓷粉末的颗粒大小与堆积情况有关,基于此选择孔径更小的粉末。而选择采用溶胶凝胶技术烧结修饰部分的颗粒,是为了降低烧结温度,防止金属基体与陶瓷层在超高温度下热膨胀系数差异生产新的缺陷。此外,裂缝内修饰的陶瓷粉末由于未在高温下烧结,其孔隙率更高,可有效缓解复合膜的金属基体与陶瓷膜层在升降温过程中的热膨胀差异问题。
16.本发明的有益效果如下:本发明制备工艺简单易操作,原材料来源广,可实现金属基陶瓷复合膜的工业化生产。
17.本发明结合前人成熟的技术工艺,在金属基体与陶瓷膜层之间添加金属粉末,通过金属粉末高温熔融作为粘结剂实现金属基体与陶瓷膜层的有效结合。此方法首先采用过温共烧技术可有效提高金属基体与陶瓷膜层的结合力,但在高温烧结的过程中膜层表面易出现开裂、脱落等缺陷。为解决此工艺中存在的问题,本发明在此基础上,选用平均粒径为
陶瓷粉末a平均粒径0.1 ~ 0.8倍的陶瓷粉末b对带有裂纹的金属基陶瓷复合膜层表面裂纹进行填充修补,再通过表面清洗,去除缝隙填补后陶瓷膜层表面多余的粉料,即可得到裂缝被陶瓷粉末b填充且表面平整的金属基陶瓷复合膜材料。
18.本发明将裂纹被陶瓷粉末b填充的金属基陶瓷复合膜材料浸渍于溶胶涂膜浆料中,通过溶胶凝胶技术进行表面修饰同时提高膜层的强度,最后结合低温烧结制备得到修补后完整无缺陷的金属基陶瓷复合膜。本发明利用溶胶凝胶技术一方面可对裂纹填充后的金属基陶瓷复合膜材料进行表面修饰,另一方面可提高膜层强度。裂纹填充修补后的金属基陶瓷复合膜材料经溶胶凝胶表面修饰后采用低温烧结,可有效减少收缩应力防止膜层开裂,进而制备得到修补后完整、无缺陷的金属基陶瓷复合膜。
附图说明
19.图1为实施例1带有裂纹的金属基陶瓷复合膜层表面电镜图。
20.图2为实施例1带有裂纹的金属基陶瓷复合膜层断面电镜图。
21.图3为实施例1修补后膜层表面电镜图。
22.图4为实施例1修补后膜层断面电镜图。
23.图5为对比例1膜层表面开裂电镜图。
具体实施方式
24.实施例1步骤1:将平均粒径均为1 μm的不锈钢粉末与pva混合形成悬浮液,悬浮液中不锈钢粉末的质量分数为10 %,均匀喷涂在不锈钢基体表面,干燥后制备得到不锈钢粉末粘结层;步骤2:将平均粒径为0.1 μm的氧化锆陶瓷粉末与pva混合形成悬浮液,悬浮液中氧化锆陶瓷粉末的质量分数为5 %,均匀喷涂于步骤1中带有不锈钢粉末粘结层的基体表面,形成带有陶瓷粉末涂层的胚体;步骤3:将步骤2中制备得到的带有陶瓷粉末涂层的胚体在真空气氛条件下1300 ℃烧结,保温1 h,即可制备得到带有裂纹的金属基陶瓷复合膜材料;步骤4:将平均粒径为步骤2中所述的氧化锆陶瓷粉末平均粒径0.1倍的氧化铝陶瓷粉末与甲基纤维素混合形成修补陶瓷膜层的浆料,修补陶瓷膜层的浆料中氧化铝陶瓷粉末质量分数为1%,利用真空抽吸的方法将前述浆料填充至陶瓷膜的裂缝中,再进行表面清洗后干燥,制备得到裂缝被氧化铝陶瓷粉末填充的金属基陶瓷复合膜材料;步骤5:以alcl3·
6h2o为前驱体制备涂膜液溶胶,溶胶中alcl3·
6h2o的质量分数为5 %,将步骤4制备得到的裂缝被氧化铝陶瓷粉末填充的金属基陶瓷复合膜材料浸渍于溶胶内,干燥后在真空气氛条件下400 ℃烧结,保温0.5 h,即可制备得到修补的金属基陶瓷复合膜。
25.实施例2步骤1:将平均粒径均为10 μm的镍合金粉末与聚酰亚胺混合形成悬浮液,悬浮液中镍合金粉末的质量分数为20 %,均匀浸渍在不锈钢基体表面,干燥后制备得到镍合金粉末粘结层;
步骤2:将平均粒径为0.5μm的氧化铝陶瓷粉末与聚酰亚胺混合形成悬浮液,悬浮液中氧化铝陶瓷粉末的质量分数为10 %,均匀浸渍于步骤1中制备得到镍合金粉末粘结层的基体表面,形成带有陶瓷粉末涂层的胚体;步骤3:将步骤2中制备得到的带有陶瓷粉末涂层的胚体在还原气氛条件下1250 ℃烧结,保温1.5 h,即可制备得到带有裂纹的金属基陶瓷复合膜材料;步骤4:将平均粒径为步骤2中所述的氧化铝陶瓷粉末平均粒径0.5倍的氧化锆陶瓷粉末与pva混合形成修补陶瓷膜层的浆料,修补陶瓷膜层的浆料中氧化锆陶瓷粉末质量分数为5 %,利用过滤法将前述浆料填充至陶瓷膜的裂缝中,再进行表面清洗后干燥,制备得到裂缝被氧化锆陶瓷粉末填充的金属基陶瓷复合膜材料;步骤5:以na2sio3为前驱体制备涂膜液溶胶,溶胶中na2sio3的质量分数为10 %,将步骤4制备得到的裂缝被氧化锆陶瓷粉末填充的金属基陶瓷复合膜材料浸渍于溶胶内,干燥后在真空气氛条件下500 ℃烧结,保温1 h,即可制备得到修补的金属基陶瓷复合膜。
26.实施例3步骤1:将平均粒径均为50 μm的不锈钢粉末与甲基纤维素混合形成悬浮液,悬浮液中不锈钢粉末的质量分数为70 %,均匀刷涂在不锈钢基体表面,干燥后制备得到不锈钢粉末粘结层;步骤2:将平均粒径为5 μm的氧化钛陶瓷粉末与甲基纤维素混合形成悬浮液,悬浮液中氧化钛陶瓷粉末的质量分数为50 %,均匀刷涂于步骤1中制备得到的带有不锈钢粉末粘结层的基体表面,形成带有陶瓷粉末涂层的胚体;步骤3:将步骤2中制备得到的带有陶瓷粉末涂层的胚体在惰性气氛条件下1500 ℃烧结,保温3 h,即可制备得到带有裂纹的金属基陶瓷复合膜材料;步骤4:将平均粒径为步骤2中所述的氧化钛陶瓷粉末平均粒径0.8倍的钇稳定氧化锆陶瓷粉末与pvb混合形成修补陶瓷膜层的浆料,修补陶瓷膜层的浆料中钇稳定氧化锆陶瓷粉末质量分数为20 %,利用刷涂的方法均匀将前述浆料填充至陶瓷膜的裂缝中,再进行表面清洗后干燥,制备得到裂缝被钇稳定氧化锆陶瓷粉末填充的金属基陶瓷复合膜材料;步骤5:以zrocl2为前驱体制备涂膜液溶胶,溶胶中zrocl2的质量分数为15 %,将步骤4制备得到的裂缝被钇稳定氧化锆陶瓷粉末填充的金属基陶瓷复合膜材料浸渍于溶胶内,干燥后在真空气氛条件下600 ℃烧结,保温1.5 h,即可制备得到修补的金属基陶瓷复合膜。
27.实施例4步骤1:将平均粒径均为20 μm的镍合金粉末与pvb混合形成悬浮液,悬浮液中镍合金粉末的质量分数为30 %,均匀浸渍在不锈钢基体表面,干燥后制备得到镍合金粉末粘结层;步骤2:将平均粒径为1 μm的氧化硅陶瓷粉末与pvb混合形成悬浮液,悬浮液中氧化硅陶瓷粉末的质量分数为25 %,均匀浸渍于步骤1中制备得到带有镍合金粉末粘结层的基体表面,形成带有陶瓷粉末涂层的胚体;步骤3:将步骤2中制备得到的带有陶瓷粉末涂层的胚体在真空气氛条件下1350 ℃烧结,保温2 h,即可制备得到带有裂纹的金属基陶瓷复合膜材料;
步骤4:将平均粒径为步骤2中所述的氧化硅陶瓷粉末平均粒径0.6倍的氧化钇陶瓷粉末与聚酰亚胺混合形成修补陶瓷膜层的浆料,修补陶瓷膜层的浆料中氧化钇陶瓷粉末质量分数为10 %,利用真空抽吸法将前述浆料填充至陶瓷膜的裂缝中,再进行表面清洗后干燥,制备得到裂缝被氧化钇陶瓷粉末填充的金属基陶瓷复合膜材料;步骤5:以正硅酸四乙酯为前驱体制备涂膜液溶胶,溶胶中正硅酸四乙酯的质量分数为8 %,将步骤4制备得到的裂缝被氧化钇陶瓷粉末填充的金属基陶瓷复合膜材料的膜层浸渍于溶胶内,干燥后在还原气氛条件下550 ℃烧结,保温1 h,即可制备修补的金属基陶瓷复合膜。
28.实施例5步骤1:将平均粒径均为5 μm的不锈钢粉末与pva混合形成悬浮液,悬浮液中不锈钢粉末的质量分数为50 %,均匀刷涂在不锈钢基体表面,干燥后制备得到不锈钢粉末粘结层;步骤2:将平均粒径为0.3 μm的氧化锆陶瓷粉末与pva混合形成悬浮液,悬浮液中氧化锆陶瓷粉末的质量分数为40 %,均匀刷涂于步骤1中制备得到带有不锈钢粉末粘结层的基体表面,形成带有陶瓷粉末涂层的胚体;步骤3:将步骤2中制备得到的带有陶瓷粉末涂层的胚体在还原气氛条件下1000 ℃烧结,保温1.2 h,即可制备得到带有裂纹的金属基陶瓷复合膜材料;步骤4:将平均粒径为步骤2中所述的氧化锆陶瓷粉末平均粒径0.5倍的钇稳定氧化锆陶瓷粉末与甲基纤维素混合形成修补陶瓷膜层的浆料,修补陶瓷膜层的浆料中钇稳定氧化锆陶瓷粉末质量分数为15 %,利用刷涂的方法将前述浆料填充至陶瓷膜的裂缝中,再进行表面清洗后干燥,制备得到裂缝被钇稳定氧化锆填充的金属基陶瓷复合膜材料;步骤5:以ti(so4)2为前驱体制备涂膜液溶胶,溶胶中ti(so4)2的质量分数为12 %,将步骤4制备得到的裂缝被钇稳定氧化锆填充的金属基陶瓷复合膜材料的膜层浸渍于溶胶内,干燥后在还原气氛条件下450 ℃烧结,保温0.8 h,即可制备得到修补的金属基陶瓷复合膜。
29.实施例6步骤1:将平均粒径均为30 μm的镍合金粉末与pva混合形成悬浮液,悬浮液中镍合金粉末的质量分数为15 %,均匀喷涂在不锈钢基体表面,干燥后制备得到镍合金粉末粘结层;步骤2:将平均粒径为3 μm的氧化钛陶瓷粉末与pva混合形成悬浮液,悬浮液中氧化钛陶瓷粉末的质量分数为8 %,均匀喷涂于步骤1中制备得到带有镍合金粉末粘结层的基体表面,形成带有陶瓷粉末涂层的胚体;步骤3:将步骤2中制备得到的带有陶瓷粉末涂层的胚体在真空气氛条件下1450 ℃烧结,保温2.5 h,即可制备得到带有裂纹的金属基陶瓷复合膜材料;步骤4:将平均粒径为步骤2中所述的氧化钛陶瓷粉末平均粒径0.7倍的氧化锆陶瓷粉末与pva混合形成修补陶瓷膜层的浆料,修补陶瓷膜层的浆料中氧化锆陶瓷粉末质量分数为10 %,利用过滤法将前述浆料填充至陶瓷膜的裂缝中,再进行表面清洗后干燥,制备得到裂缝被氧化锆粉末填充的金属基陶瓷复合膜材料;步骤5:以正丁醇铝为前驱体制备涂膜液溶胶,将步骤4制备得到的裂缝被氧化锆
粉末填充的金属基陶瓷复合膜材料的膜层浸渍于溶胶内,干燥后,在还原气氛条件下550 ℃烧结,保温1.5 h,即可制备得到修补的金属基陶瓷复合膜。
[0030] 对比例 对比例1本对比例提供一种金属基陶瓷复合膜的修补工艺,其与实施例1基本相同,不同之处在于:步骤3中的烧结温度为900 ~ 1000 ℃。本对比例由于烧结温度较低,膜层孔径较大,膜层与金属基体结合强度较低,膜层在烧结过程中由于热膨胀系数差异易开裂出现脱落。
[0031]
对比例2本对比例提供一种金属基陶瓷复合膜的修补工艺,其与实施例1基本相同,不同之处在于:未进行步骤4中的制备过程。由于未采用填缝隙工艺将修补层浆料填充至陶瓷膜的裂缝中,未修补的带有裂纹的膜层在溶胶凝胶修饰时,溶胶涂膜浆料会通过裂纹渗入基体内部,制备得到的膜层带有裂纹因而影响膜层性能。
[0032]
对比例3本对比例提供一种修补的金属基陶瓷复合膜的制备方法,其与实施例1基本相同,不同之处在于:步骤4中未进行表面清洗。由于没有对裂纹填充后的膜层进行表面清洗,膜层表面粉料颗粒堆积,膜层分布不均匀易开裂脱落。
[0033]
对比例4本对比例提供一种修补的金属基陶瓷复合膜的制备方法,其与实施例1基本相同,不同之处在于:步骤5中的热处理采用高温烧结(800 ~ 1000 ℃)。由于烧结温度较高,膜层收缩应力较大,制备得到的膜层易出现开裂。
[0034]
将上述实施例1-6和对比例1-4样品采用泡点法的孔径分析仪测试孔径测试数据如下表所示:下表为实施例1-6和对比例1-4样品最大孔径、平均孔径数据汇总表。
[0035]
将实施例1-6与对比例1相比,我们可以看出,对比例1由于烧结温度较低,膜层孔径较大,膜层与金属基体结合强度较低,膜层易出现脱落。
[0036]
将实施例1-6与对比例2相比,我们可以看出,对比例2由于未采用填缝隙工艺将修
补层浆料填充至陶瓷膜的裂缝中,未修补的带有裂纹的膜层在溶胶凝胶修饰时,溶胶涂膜浆料会通过裂纹渗入基体内部,制备得到的膜层带有裂纹因而影响膜层性能。
[0037]
将实施例1-6与对比例3相比,我们可以看出,对比例3由于没有对裂纹填充后的膜层进行表面清洗,膜层表面粉料颗粒堆积,膜层分布不均匀易开裂脱落。
[0038]
将实施例1-6与对比例4相比,我们可以看出,对比例4由于烧结温度较高,膜层收缩应力较大,制备得到的膜层易出现开裂。
[0039]
从上述实施例和对比例测试的结果可以得到以下结论。
[0040]
1.本发明基于专利cn101234296a制备技术的基础上,提供一种金属基陶瓷复合膜的修补工艺,对带有裂纹的金属基陶瓷复合膜材料进行修补。通过填缝隙工艺用陶瓷粉末颗粒对膜层裂纹进行填充,表面清洗去除膜层表面多余粉料,结合溶胶凝胶技术低温烧结制备修补后完整无缺陷的金属基陶瓷复合膜。
[0041]
2.本发明采用过温共烧技术,利用金属粉末高温熔融浸润陶瓷涂层提高金属基体与陶瓷膜层的结合力,同时金属粉末可修饰金属基体表面存在的缺陷。过温共烧技术可使金属粉末在高温条件下熔融浸润陶瓷粉末,金属基体与陶瓷膜层结合强度较高。
[0042]
3.本发明通过选用平均粒径为陶瓷膜层粉末平均粒径0.1 ~ 0.8倍的陶瓷粉末对带有裂纹的陶瓷膜层进行填充修补,陶瓷粉末填充在陶瓷膜层的表层裂纹中,并对陶瓷膜层的表层缺陷进行修饰,表面清洗后,形成平整、均匀的表面涂层,为制备完整、无缺陷的金属基陶瓷复合膜提供基础。
[0043]
4.本发明制备工艺简单易操作,在前人制备工艺技术的基础上进行了改进,可实现工业化生产。
再多了解一些
本文用于创业者技术爱好者查询,仅供学习研究,如用于商业用途,请联系技术所有人。