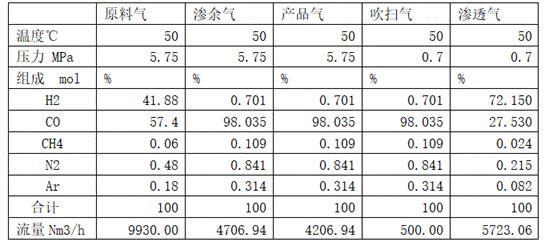
1.本发明涉及煤化工和石油化工的气体分离领域,具体为一种膜分离渗透侧吹扫提纯合成气中一氧化碳的系统。
背景技术:
2.在一些以合成气为原料的化工生产中对气体的组成有严格的要求,比如甲胺生产中要求原料气中的一氧化碳浓度为96—98%(v,下同),同时要求氢气浓度小于2%;甲醇羰基化生产醋酸要求原料气中的一氧化碳浓度大于98%;甲醇氧化羰基化生产碳酸二甲酯也要求原料气体中的一氧化碳大于98%。
3.煤气化生产的粗煤气主要成分是氢气、一氧化碳、二氧化碳、及少量甲烷、氮气、硫化氢、水等杂质,当下游生产需要以一氧化碳为主要原料时,粗煤气无需变换,经过净化和脱除酸性气体后获得主要成分为氢气和一氧化碳的合成气,也含有少量氮气、甲烷等杂质。所以氢气和一氧化碳的分离提纯或调整比例是重要的生产工序。
4.合成气的分离方法主要有深冷法、变压吸附法和膜分离法。深冷分离的特点是处理气量大、分离精度高、投资和占地规模大。变压吸附可以获得高浓度的氢气、一氧化碳等合成气,缺点是操作复杂、当以解析气为产品气时,其压力很低。膜分离投资占地少,操作灵活,渗透气和渗余气的压力均可设定,但是需要保证膜分离两侧具有一定的分压差才能获得好的分离效果。
5.膜分离技术用于氢气和一氧化碳、氮气、甲烷等气体的分离,多用于煤化工和石油化工领域的氢气回收、合成气提纯、和气体的调比。其原理是不同组分的气体通过分离膜的渗透速率不同,在膜两侧分压差的推动力下,进行气体分离。
6.膜分离进行气体分离的技术局限性是当非渗透侧的氢气浓度降低同时渗透侧的氢气浓度升高到一定程度,使气体分离的推动力变得很小,无法进一步降低非渗透侧的氢气浓度,从而使非渗透侧一氧化碳气体的浓度达到极限值不能再升高,可能无法满足生产要求。
7.氢气膜分离器通常结构为原料气和非渗透气在分离膜的高压侧流动,渗透气通过膜在中空纤维膜的低压侧汇集排出。现在已经有双封头结构的膜分离器(cn105879688)增加了渗透侧的气体入口,该膜分离器可以应用于膜分离渗透侧吹扫技术。
技术实现要素:
8.为解决背景技术中描述的问题,克服原用的膜分离技术分离气体不够彻底的局限,本发明提供了一种膜分离渗透侧吹扫技术提纯合成气中一氧化碳的系统,来提高膜分离非渗透侧一氧化碳气的浓度。
9.本发明是这样实现的:一种膜分离渗透侧吹扫提纯合成气中一氧化碳的系统,膜分离器(1)高压侧有原料气入口(16)和渗余气出口(17),低压侧有吹扫气入口(18)和渗透气出口(19);原料气(11)通过原料气入口(16)进入膜分离器(1),在膜分离器两侧压差的推
动下,容易渗透的氢气优先通过分离膜,在渗余气出口(17)得到含氢气量很低而一氧化碳气体含量高的渗余气(12),膜分离器(1)的渗余气出口(17)连接气体分流器(2)进气口,所述气体分流器(2)有出气口一(21)和出气口二(22)两个出气口,渗余气(12)中一部分由出气口一(21)输出作为产品气(13),渗余气(12)中的另一部分由出气口二(22)输出,出气口二(22)连接吹扫气入口(18),所述出气口二(22)和吹扫气入口(18)之间管路上设减压阀(3),渗余气(12)中的另一部分经减压后作为吹扫气(14)进入膜分离器低压侧与渗透气混合后作为低压气(15)经渗透气出口(19)排出。
10.原料气(11)在进入膜分离器(1)之前先经过过滤器,除掉能影响膜分离效果的固体颗粒和液滴,再经过加热器加热到膜分离的合适操作温度,也使气体中的可凝结组分远离饱和露点。
11.所述过滤器为精密过滤器,过滤精度0.1μ。
12.所述加热器加热温度为45
‑‑
75℃。
13.所述膜分离器(1)的原料气入口(16)和吹扫气入口(18)两个入口位置与渗余气出口(17)和渗透气出口(19)两个出口的位置设在膜分离器的不同侧,使膜分离器中气体逆流操作。
14.所述原料气成分不限于氢气和一氧化碳气,也可以是氢气和氮气、甲烷及其它烃类气体的混合气,该系统对所有混合气中某一种或几种组分的分离与提纯均适用。
15.与现有技术相比,本发明的有益效果是:本发明利用了渗透气吹扫技术提高了膜两侧氢气的分压差,从而提高膜分离的推动力,能够获得更高浓度的一氧化碳气体,满足下游生产要求。一氧化碳浓度较高的渗余气作为吹扫气进入到膜分离渗透侧时,在提高渗透气氢气分压差的同时,也降低了渗余气中一氧化碳的分压差,使一氧化碳气更难透过分离膜,从而能够提高一氧化碳气体的浓度。吹扫气用量可以调整,从而在膜分离非渗透侧获得不同浓度的一氧化碳气体,满足不同生产要求。原料气量可以调整,配合吹扫气量的调整可以同时获得浓度和流量都满足要求的合成气产品。膜分离原料气成分不限于氢气和一氧化碳气,也可以是氢气和氮气、甲烷及其它烃类气体的分离,原料气的组成不限,氢气含量从0.1%
‑‑
90%都可以用渗透侧吹扫技术来提高渗余气中一氧化碳或甲烷等的浓度,也适用于所有混合气中某一种或几种组分的分离与提纯均适用,如天然气精制时脱除二氧化碳、脱除硫化氢、各种气体脱水、焦炉气为提高热值脱除氢气和二氧化碳等。膜分离吹扫技术工艺简单,操作灵活,无额外能量消耗,整套装置投资少。该系统不限于氢气/一氧化碳气体的分离与提纯。
附图说明
16.为了更清楚地说明本发明实施方式的技术方案,下面将对实施方式中所需要使用的附图作简单地介绍,应当理解,以下附图仅示出了本发明的某些实施例,因此不应被看作是对范围的限定,对于本领域普通技术人员来讲,在不付出创造性劳动的前提下,还可以根据这些附图获得其他相关的附图。
17.图1为本发明一种膜分离渗透侧吹扫技术提纯合成气中一氧化碳的方法示意图。
18.图2、图3为两种膜分离器结构示意图。
19.图4为对比实例:不带吹扫技术的膜分离分离氢气流程示意图。
20.图中:1、膜分离器;2、气体分流器;3、减压阀;11、原料气;12、渗余气;13、产品气;14、吹扫气;15、低压气;16、原料气入口;17、渗余气出口;18、吹扫气入口;19、渗透气出口;21、出气口一;22、出气口二。
具体实施方式
21.为使本发明实施方式的目的、技术方案和优点更加清楚,下面将结合本发明实施方式中的附图,对本发明实施方式中的技术方案进行清楚、完整地描述,显然,所描述的实施方式是本发明一部分实施方式,而不是全部的实施方式。基于本发明中的实施方式,本领域普通技术人员在没有作出创造性劳动前提下所获得的所有其他实施方式,都属于本发明保护的范围。因此,以下对在附图中提供的本发明的实施方式的详细描述并非旨在限制要求保护的本发明的范围,而是仅仅表示本发明的选定实施方式。基于本发明中的实施方式,本领域普通技术人员在没有作出创造性劳动前提下所获得的所有其他实施方式,都属于本发明保护的范围。
22.如图1所示,一种膜分离渗透侧吹扫提纯合成气中一氧化碳的系统,膜分离器1高压侧有原料气入口16和渗余气出口17,低压侧有吹扫气入口18和渗透气出口19;压力较高、氢气浓度较高的粗合成原料气11通过原料气入口16进入膜分离器1,在膜分离器两侧压差的推动下,容易渗透的氢气优先通过分离膜,在渗余气出口17得到含氢气量很低而一氧化碳气体含量高的渗余气12,膜分离器1的渗余气出口17连接气体分流器2进气口,所述气体分流器2有出气口一21和出气口二22两个出气口,渗余气12中一部分由出气口一21输出作为产品气13,渗余气12中的另一部分由出气口二22输出,出气口二22连接吹扫气入口18,所述出气口二22和吹扫气入口18之间管路上设减压阀3,渗余气12中的另一部分经减压后作为吹扫气14进入膜分离器低压侧与渗透气混合后作为低压气15经渗透气出口19排出。
23.其中,原料气11在进入膜分离器1之前先经过过滤器,除掉能影响膜分离效果的固体颗粒和液滴,再经过加热器加热到膜分离的合适操作温度,也使气体中的可凝结组分远离饱和露点。所述过滤器为精密过滤器,过滤精度0.1μ。所述加热器加热温度为45-75℃。
24.如图2和图3所示,所述膜分离器1的原料气入口16和吹扫气入口18两个入口位置与渗余气出口17和渗透气出口19两个出口的位置设在膜分离器的不同侧,使膜分离器中气体逆流操作。
25.所述原料气成分不限于氢气和一氧化碳气,也可以是氢气和氮气、甲烷及其它烃类气体的混合气,该系统对所有混合气中某一种或几种组分的分离与提纯均适用。
26.初始的产品气13一氧化碳浓度不一定达到生产要求,可以调整吹扫气14的量来调整膜分离的推动力,获得浓度合格的产品气13。
27.由于部分渗余气作为吹扫气14进入膜分离低压侧,使产品气13流量可能达不到下游生产要求,可以调整进入膜分离器的原料气11的气量,相应地需要增加膜面积,同时调节吹扫气14的用量优化膜分离操作,最终获得一氧化碳浓度和流量都合格的产品气13。
28.实施例1:原料气条件:原料气来源:未变换气净化气流量:9122nm3/h(可根据需要增加原料气量);
温度:30℃; 压力:5.75mpag。
29.分离气体要求:1、非渗透气作为产品气,产品气中一氧化碳浓度大于98%;2、产品气流量大于4200nm3/h;产品气压力大于5.5mpag。
30.原料气氢气浓度较高,产品气一氧化碳浓度要求较高,渗透气返回费托合成,对氢气浓度没有严格的要求,而合成气流量有富余,所以从现场实际情况看,具有可以调整膜分离操作的条件。净化气中氮气、甲烷、氩气等杂质也影响产品气的一氧化碳浓度。在本实例中渗透气压力设定为0.6mpa。
31.原料气经预处理后温度设定在50℃,不含有可能存在的其它固体和液体杂质,先进入膜分离器,在非渗透气出口得到的渗余气一氧化碳浓度约为95.31%左右,流量大约4551nm3/h,此时渗余气的一氧化碳浓度不符合要求,渗余气流量大于产品气要求的气量。
32.先取300nm3/h的渗余气作为吹扫气进入膜分离器的吹扫气入口,与膜分离低压侧的渗透气一起从渗透气出口排出界外。在增加吹扫气的流量的同时检测产品气的浓度,当吹扫气为500nm3/h时,产品气中一氧化碳的浓度为97.7%,浓度接近膜分离要求的一氧化碳浓度98%。
33.此时产品气的流量为3943.2nm3/h,未能达到设计要求,再根据产品气流量增加原料气的流量,同时增加膜分离器的投用数量来增加膜面积,当进入膜分离的原料气为9930nm3/h,产品气的流量为4206nm3/h,此时产品气中一氧化碳浓度为98.03%,满足生产要求。需要注意的是在增加膜分离原料气量的同时必须增加膜分离的面积,因为在一定条件下,膜分离装置处理能力与膜面积的选择是对应的线性关系。
34.物料平衡表如下:对比实例2在实例1中如果不采用膜分离渗透侧吹扫技术,用常规的膜分离技术分离合成气,流程示意图如图4。
35.通过调整膜分离的投用面积和进入膜分离的原料气量能得到如下三个结果:当原料气量为9122nm3/h时,如果使产品气的流量达到4218nm3/h,此时产品气中一氧化碳浓度为
97.10%,产品气浓度未能达到要求;当原料气量为9122nm3/h时,如果增加膜面积来使产品气中一氧化碳浓度达到98.12%,此时产品气的流量为3914nm3/h,产品气流量未能达到要求;如果增加原料气的流量到9930nm3/h与实例1的原料气量相等,同时大幅增加膜分离的投用面积,使产品气流量为4220nm3/h,产品气一氧化碳浓度为98.02%,此时膜分离的投用面积为实例1的1.5倍左右。膜分离投资增加较多,可见在本实例1中采用渗透侧吹扫技术能减少膜分离的投资30%以上。
36.实例3:某醋酸生产企业采用焦炭造气得到的合成气条件如下:原料气量流量:16000nm3/h;组成: h2: 10%、co:87.6%、co2:0.6%;n2: 1.6%、o2:0.2%;压力:3.3mpa(a)、温度40℃;甲醇羰基化生产要求合成气的一氧化碳浓度大于97.5%,采用膜分离渗透侧吹扫技术将非渗透中的氢气、二氧化碳和氧气尽量脱除。在吹扫气为400nm3/h时,得到的产品气一氧化碳浓度为97.507%;产品气量为11718nm3/h。如果未经吹扫,则可以得到一氧化碳浓度为96.9%的产品气12200nm3/h。
37.实例3的物料平衡表如下:以上所述仅为本发明的优选实施方式而已,并不用于限制本发明,对于本领域的技术人员来说,本发明可以有各种更改和变化。凡在本发明的精神和原则之内,所作的任何修改、等同替换、改进等,均应包含在本发明的保护范围之内。
再多了解一些
本文用于创业者技术爱好者查询,仅供学习研究,如用于商业用途,请联系技术所有人。