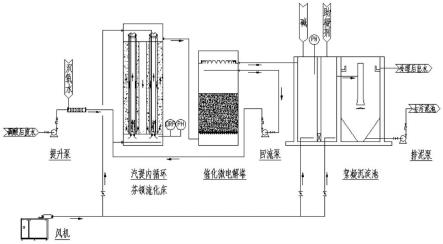
1.本发明提供一种汽提内循环芬顿流化床耦合催化微电解内回流工艺,用于各种高浓度有机废水预处理,属于废水处理技术领域。
背景技术:
2.芬顿氧化能够产生氧化能力强的羟基自由基,使废水中生化抑制性、难降解性有机污染物分解成可生化性较好的小分子有机物,减轻生化系统的处理负荷,确保生化处理系统的稳定高效运行,同时芬顿氧化能够有效破坏有机胺的分子结构,通过羟基自由基的强氧化作用使其分子链断裂,加速释放出氨氮,为后续生物脱氮创造条件,提高生化处理系统的氨氮去除效率;但芬顿对重氮、叠氮、偶氮、硝基氮类有机氮废水等效果较差,无法将其胺基化和氨化,对生化脱氮不利;对部分有机氯、有机磷废水效果也一般;芬顿氧化药剂量投加量大,产生的危废量大。
3.催化微电解在酸性条件下发生电化学反应产生的了初生态的fe
2
和原子h,具有高化学活性,能改变废水中许多有机物的结构和特性,使有机物发生断链、开环等作用;极强的还原作用对重氮、叠氮、偶氮、硝基氮类有机氮废水脱氮,对有机氯废水脱氯,对有机磷废水脱磷效果极好;但由于反应环境为酸性,铁碳填料会溶出消耗,酸度越大,消耗越快;工程应用中为减弱浓差极化、加速电极反应及更新微电解填料表面,一般设置曝气,但也会将fe
2
氧化成fe
3
,减弱了体系的还原能力。
4.芬顿和催化微电解的组合是化工、制药等高难度高浓度废水广泛应用的预处理技术,一般是先催化微电解后芬顿的形式,利用催化微电解产生多余的亚铁离子,减少芬顿的投药量,但催化微电解在前,必然承受酸度更高的环境,凸显了铁碳填料消耗的问题。
5.芬顿流化床是芬顿工艺的一种发展形式,利用流体化床的模式使芬顿法所产生的三价铁大部份得以结晶或沉淀披覆在流体化床的载体填料表面上,结合了同相化学氧化、异相化学氧化(h2o2/feooh)、流体化床结晶及feooh的还原溶解等功能。这项技术将传统的芬顿氧化法作了大幅度的改良,可减少50%的污泥量,同时在载体表面形成的铁氧化物具有异相催化的效果,流化床模式亦促进了反应及传质效率。
6.芬顿流化床的工程应用有几个局限,首先较高流化速度限制了密度较大填料如铁矿类的应用,其次废水流化的动能来源一般采用循环泵,含铁填料流化速度都要在60m/h以上,导致循环泵能耗高,第三为增加实际停留时间,在保证上向流速,设备只能做高,高径比达到3:1~5:1,增加了设备制作成本和一次提升能耗。第四工程应用中只是减少了亚铁盐的投加量,但仍要投加。芬顿流化床多用于低浓度生化性较差废水深度处理,因为所需停留时间较短,一般20~30min,应用于高浓度废水较少,由于停留时间在2h以上,为实现工艺效果的投入和成本都会大大增加。以浙江台州某高浓度医化废水为例,cod约20000~30000mg/l,采用芬顿流化床生化前预处理,处理能力50t/h,水力停留时间2h,塔尺寸3.6m*12.5m,高径比达到3.5:1,采用的循环泵流量600t/h,功率达到30kw.h。
技术实现要素:
7.本发明的目的是克服已有芬顿微电解组合技术的不足,基于汽提内循环芬顿流化床耦合催化微电解内回流工艺,采用汽提内循环芬顿流化床-催化微电解塔-絮凝沉淀工艺流程,适用于几乎所有的高浓度有机废水预处理,特别是需要还原反应破坏分子结构的含重氮、叠氮、偶氮、硝基氮有机氮废水和有机氯废水、有机磷废水等。通过本发明解决了芬顿微电解组合技术在工程应用上的一系列不足:第一采用芬顿流化床采用汽提内循环结构,克服了传统芬顿流化床为实现流化的高能耗投入和大的高径比问题;第二是芬顿在前,微电解在后,芬顿会消耗掉酸度,微电解的ph值上升意味铁碳填料消耗得速度会降低;第三是通过微电解向芬顿的内回流,提供了是芬顿所需的亚铁,减少了亚铁盐的投加;第四内回流的存在,增大了微电解塔内的上向流速,无需曝气即可改善铁碳填料的传质、反应效率、表面更新。
8.汽提内循环结构即是在芬顿流化床设置若干同心导流筒,分内筒和外筒,外筒外部为填料区,内外筒形成的外环和内筒的面积至少1:1,流速不高于0.4m/s,内筒底部与进水区相通,外环筒身侧底部开孔,与填料区相通,外环筒身侧底部开孔面积与内筒面积至少1:1,流速不高于0.4m/s;在每个导流内筒底部设置一组可提升管式曝气器,曝气量约4m3/m2.h(以流化床面积计),曝气充氧的同时利用水气密度差,形成流量巨大的气水混合液,水气比可达到20:1,形成80m3/m2.h的流量,由此产生较大的上升动力,沿导流内筒高速提升,再经过导流外筒高速回流至填料底部将填料流化,再通过整个填料区经筛网板至流化床上部,绝大部分混合液沿芬顿流化床中心筒通道再回流至进水区,从而实现了反复的大比倍循环,中心筒的面积与所有内筒面积之和至少1:1,流速不高于0.4m/s,汽提内循环的少量则作为出水自流至催化微电解塔底部。
9.汽提内循环芬顿流化床可以节约能耗,相比于循环泵的能耗,达到同样的流化效果可以降低75%的能耗。
10.汽提芬顿流化床填料可采用负载羟基氧化铁的活性炭、陶粒、火山岩、沸石等填料,填料的粒径为1~3mm,填料的来源和粒径选择更宽泛。
11.汽提内循环芬顿流化床的高径比可以控制在2.5:1之内。
12.芬顿流化床出水进入催化微电解塔底部,经滤头均布进入铁碳填料区,酸性条件下发生电化学反应产生的初生态的fe
2
和原子h,使有机物发生断链、开环等作用,微电解塔出水堰下方设置回流收集管,通过泵回流至芬顿流化床进水区,回流比为100%以上。
13.由于经过了芬顿流化床反应,废水酸度下降,铁碳填料的消耗速度自然会降低,实际降低了成本和铁碳添加强度。
14.催化微电解至芬顿流化床回流液,含有亚铁离子,芬顿流化床无需额外投加亚铁,节约了药剂。
15.回流比100%,相当于催化微电解塔的上向流速加大1倍,无需曝气即可改善铁碳填料的传质、反应效率、表面更新,同时确保了彻底的还原态,微电解的效能发挥不受影响。
16.出水进入絮凝沉淀池,曝气将剩余亚铁氧化成三价铁,并回调ph值,生成吸附性极强的fe(oh)3胶体,投加pam,促进fe(oh)3及其络合物沉淀分离。
附图说明
17.图1本发明一种汽提内循环芬顿流化床耦合催化微电解内回流用于高浓度有机废水预处理的工艺。
具体实施方式
18.下面通过具体实施方式,并结合附图,对本发明的技术方案作进一步的具体说明。应当强调,本发明的实施并不局限于下面的实施例方式,对本发明所做的任何形式上的变通或改变都在本发明的保护范围以内。
19.高浓度废水调节ph至3~4,通过提升泵提升进入到汽提内循环芬顿流化床,双氧水和原水通过管道混合器混合,亚铁由催化内电解塔回流提供,结合了同相化学氧化(fenton法)、异相化学氧化(h2o2/feooh)、流化床结晶及feooh的还原溶解等功能,在每个导流内筒底部设置一组可提升旋流曝气器,曝气量约4m3/m2.h(以流化床面积计),曝气充氧的同时利用水气密度差,形成流量巨大的气水混合液,水气比可达到20:1,形成80m3/m2.h的流量,由此产生较大的上升动力,沿导流内筒高速提升,再经过导流外筒高速回流至填料底部将填料流化,再通过整个填料区经筛网板至流化床上部,绝大部分混合液沿芬顿流化床中心筒通道再回流至进水区,从而实现了反复的大比倍循环,少量则作为出水自流至催化微电解塔底部。经滤头均布进入铁碳填料区,酸性条件下发生电化学反应产生的初生态的fe
2
和原子h,使有机物发生断链、开环等作用,微电解塔出水堰下方设置回流收集管,通过回流泵至芬顿流化床进水区,回流比为100%以上,提供亚铁离子的同时,使催化微电解塔的上向流速加大1倍以上,无需曝气即可改善铁碳填料的传质、反应效率、表面更新,同时确保了彻底的还原态,微电解的效能不受影响;催化微电解塔出水进入絮凝沉淀池,曝气将剩余亚铁氧化成三价铁,并回调ph值,生成吸附性极强的fe(oh)3胶体,投加pam,促进fe(oh)3及其络合物絮体形成,并在沉淀区沉淀分离;沉淀出水去后续生化处理,底泥排泥泵去污泥池浓缩后脱水处理。
再多了解一些
本文用于创业者技术爱好者查询,仅供学习研究,如用于商业用途,请联系技术所有人。