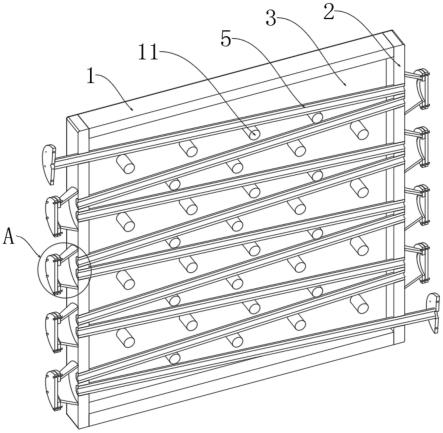
一种v形管式模块化连续反应器
技术领域
1.本发明涉及化工行业工程技术领域,具体涉及一种v形管式模块化连续反应器。
背景技术:
2.精细化工、制药行业很多产品或中间体生产中经常需要用到气固液、固液及气液、液液等反应工艺,比如常见的加氢工艺。而大型化工企业连续化加氢工艺一般采用固定床装置,固定床运行模式均是垂直安装,一般是利用氢气与物料液体在反应器顶部通过复杂的气液分配结构后,自然流经下部装填有固体催化剂床层或是列管内装填的多孔颗粒催化剂孔隙表面时实现气固液传质交换,使氢化液从底部流出,混合物料停留时间与空速和固定床高度相关,而反应效率基本与固定床直径和催化剂有效装填截面积成正比,使用固定床装置的加氢反应工艺一般催化剂使用寿命都较长,可是一旦更换催化剂时,不管是绝热型床层装填模式,还是列管装填模式,受装置本身结构影响,停产周期长,需要耗费大量人力物力和时间拆装,而国内目前中小规模加氢工艺生产特别是精细化工行业,绝大多数仍采用传统高压釜间歇反应装置,另外少数项目装置采用了多台釜式串联或回路反应器等实现连续化加氢反应工艺,但是它们的结构和工作原理决定了物料在其中停留浓度分布不均,新进物料与已持续长时间反应物料之间返混严重,仅适用于少数反应时间较快的产品工艺,更多的加氢产品因为停留时间不足或副反应严重而无法使用。
3.因此,用本发明的一种v形管式模块化连续反应器来解决上述问题很有必要。
技术实现要素:
4.本发明的目的是提供一种v形管式模块化连续反应器,重点解决精细化工行业现有具有较大安全隐患的传统间歇反应模式,以及在釜式串联、回路反应器等连续化反应模式中物料浓度分布不均,新进物料与已持续长时间反应物料之间返混严重的现象;解决部分采用传统管式反应器体积庞大、结构落后、反应效率低下、适用产品较少的弊端。
5.为了实现上述目的,本发明提供如下技术方案:一种v形管式模块化连续反应器,包括壳程,所述壳程两侧均设有管板,所述管板数量设置为两个,所述壳程与两个管板之间共同形成换热腔,所述管板上开设有多个管孔,两个所述管板之间排列有多个反应管,所述反应管设置在换热腔内部,所述反应管倾斜设置,相邻两个所述反应管呈v形排列,所述反应管两端均与相对应的管孔焊接,所述管板两侧均焊接有变径法兰,相邻两个所述反应管与一个变径法兰位置相对应,相邻两个所述反应管相对应的管孔被变径法兰围罩,所述变径法兰远离管板一侧安装有盖板,所述盖板、变径法兰与管板之间共同形成内腔,相邻两个所述反应管依靠内腔折返连通。
6.优选的,所述壳程截面形状设置为矩形,所述管板截面形状设置为矩形。
7.优选的,所述壳程与两侧管板组成反应器模块外壳。
8.优选的,其中一个所述管板远离反应管一侧底部设有进料管,所述进料管与底部的初始反应管相连通。
9.优选的,其中一个所述管板远离反应管一侧顶部设有出料管,所述出料管与顶部的反应管末端相连通。
10.优选的,所述盖板为盲板。
11.优选的,所述盖板位置可安装耐压视镜和传感器模块。
12.优选的,所述壳程前后之间穿过并焊接排列有多个拉杆,所述拉杆由圆柱状高强金属材料制成。
13.优选的,所述反应器可垂直安装。
14.优选的,所述反应器可水平安装。
15.在上述技术方案中,本发明提供的技术效果和优点:
16.1、通过设有v形折返反应管,反应管直径、数量、长度按照装置产能和产品所需工艺停留时间排列设置,并根据反应工艺决定v形折返反应管内的装填物。换热腔内充满换热体以进行反应热交换。比如加氢反应时反应管内装填比表面积较大的颗粒状高活性催化剂,颗粒状催化剂之间又形成了无数不规则物理间隙,等同于无数微型通道,物料由底部进料管进入,在反应管内按一定倾斜角度转换爬升,从出料管排出,液体配合高压输料泵与气体通过前置气液混合器,使料液与气体形成微气泡乳化液态并进入反应管内,在颗粒催化剂堆积的微型通道内表面与催化剂孔隙内部进行气固液传质反应,只需打开一侧管板的变径法兰盖板的情况下,即可暴露出变径内的反应管口,进行内容物的装填、清洗或更换操作,十分快捷方便,该装置反应管内的流体不依靠传统固定床自然高度垂直流动,而是在管腔内以总体下进上出特定通道内以湍流形式排出,在相同单位体积内,此种模块结构比反应管平行排列,两端以u形管、法兰串接,反应管外通常再辅以伴热套管的传统管式反应器模式要节省大量空间、材料,有效反应管长度增加,延长反应行程,大大提高了制造、安装、使用效率,节能效果显著,本发明结构布局合理,结构紧凑,可根据生产现场需要切换安装、运行、维护更换内容物方式,操作方便,可实现固体催化剂的快速装填、拆装,或内构件的清洗,大大缩短停产检修时间,在实现反应器本质安全的基础上,大幅度节约土地、厂房建设、设备投资成本,特别适合于精细化工、制药行业多品种、小批量的生产模式,其独有的拆装方式可以迅速实现装填催化剂和不同产品转换工作,得以实现用输送泵配合前置混合器与反应管进行多种工艺产品的快速反应,与现有技术相比,本发明特有的反应方式大幅度提高了生产效率,降低了投资和生产成本;
17.2、通过使壳程采用矩形,易于反应管与整机模块化排列组装,物料由底部进料管进入,在反应管内按一定排列角度转换混合反应,从出料管排出,盖板可根据需要在不同部位安装耐压视镜及各种传感器,观察到料液在相应反应过程中的实际混合状态,并即时采集、控制反应不同时段中料液的温度、压力、ph值等各种参数,在壳程内排列有金属拉杆用于抵抗换热腔通入换热体后形成的压力不会使矩形壳程膨胀变形。
附图说明
18.为了更清楚地说明本技术实施例或现有技术中的技术方案,下面将对实施例中所需要使用的附图作简单地介绍,显而易见地,下面描述中的附图仅仅是本发明中记载的一些实施例,对于本领域普通技术人员来讲,还可以根据这些附图获得其他的附图。
19.图1为本发明的整体结构示意图;
20.图2为本发明剖视图;
21.图3为本发明图2中a部分结构放大图;
22.图4为本发明壳程立体图;
23.图5为本发明管板立体图;
24.图6为本发明壳程与反应管连接结构示意图;
25.图7为本发明盖板和变径法兰立体图。
26.附图标记说明:
27.1、壳程;2、管板;3、换热腔;4、管孔;5、反应管;6、变径法兰;7、盖板;8、内腔;9、进料管;10、出料管;11、拉杆。
具体实施方式
28.为了使本领域的技术人员更好地理解本发明的技术方案,下面将结合附图对本发明作进一步的详细介绍。
29.本发明提供了如图1-7所示的一种v形管式模块化连续反应器,包括壳程1,壳程1两侧均设有管板2,管板2数量设置为两个,壳程1与两个管板2之间共同形成换热腔3,管板2上开设有多个管孔4,两个管板2之间排列有多个反应管5,反应管5设置在换热腔3内部,反应管5倾斜设置,相邻两个反应管5呈v形横向排列,反应管5两端均与相对应的管孔4焊接,管板2两侧均焊接有变径法兰6,相邻两个反应管5与一个变径法兰6位置相对应,相邻两个反应管5相对应的管孔4被变径法兰6围罩,变径法兰6远离管板2一侧安装有盖板7,盖板7、变径法兰6与管板2之间共同形成内腔8,相邻两个反应管5通过内腔8折返连通,在使用时,反应管5直径、数量、长度按照装置产能和产品所需工艺停留时间排列设置,换热腔3内充满换热体以进行反应热交换,反应管5内可装填比表面积较大的颗粒状高活性催化剂,颗粒状催化剂之间又形成了无数不规则物理间隙,等同于无数微型通道,物料由进料管9进入,在反应管5内按一定角度排列转换混合反应,从出料管10排出,液体配合高压输料泵与气体通过前置气液混合器,使料液与气体形成微气泡乳化液态并进入反应管5内,在颗粒催化剂堆积的微型通道内与催化剂孔隙表面进行气固液传质反应,只需打开一侧管板2的变径法兰6盖板7的情况下,即可暴露出变径的反应管5口,进行清洗内构件或装填、更换催化剂操作,十分快捷方便,该装置反应管5内的流体不依靠传统固定床自然垂直流动在催化剂表面进行气固液交换,而是总体自下而上模式在相同单位体积内,此种模块结构比反应管5平行排列,终端以u形管、法兰连接,反应管5外通常再辅以伴热套管的传统管式反应器模式要节省大量空间、材料,有效反应管5长度增加,延长反应行程,大大提高了制造、安装、使用效率,节能效果显著,本发明结构布局合理,结构紧凑,可根据生产现场需要切换安装、运行、维护更换催化剂方式,操作方便,可实现固体催化剂的快速装填、拆装,或内构件的清洗,大大缩短停产检修时间,在实现反应器本质安全的基础上,大幅度节约土地、厂房建设、设备投资成本,特别适合于精细化工、制药行业多品种、小批量的生产模式,其独有的拆装方式可以迅速实现装填催化剂和不同产品转换工作,得以实现用送料泵配合前置气液混合器、反应管5进行快速反应,与现有技术相比,改变了现有固定床内液体通过复杂的分配器结构,依靠滴流方式与床内气体在催化剂表面完成气液交换化学反应,因此,本发明特有的反应方式大幅度提高了生产效率,降低了投资和生产成本,本反应器根据需要可以选择垂直安装
或者水平安装。
30.如图1-2和4-6所示:壳程1截面形状设置为矩形,管板2截面形状设置为矩形,壳程1采用矩形,易于反应管5与整机模块化排列组装;壳程1与两侧管板2组成反应器模块外壳,便于通过法兰注入换热体;其中一个管板2远离反应管5一侧底部设有进料管9,进料管9与底部的反应管5相连通,其中一个管板2远离反应管5一侧顶部设有出料管10,出料管10与顶部的反应管5相连通,物料由进料管9进入,在反应管5内按一定角度排列转换混合反应,从出料管10排出。
31.如图1-7所示:所述壳程1前后之间穿过并焊接有多个拉杆11,所述拉杆11由圆柱状高强金属材料制成,用于抵抗换热腔3通入换热体后形成的压力使矩形壳程1不会膨胀变形。
32.如图1-3和7所示:盖板7为盲板,使盖板7、变径法兰6与管板2之间共同形成折返内腔8,便于反应。
33.如图1-3和7所示:盖板7在需要位置安装耐压视镜和传感器模块,传感器模块包括温度传感器、压力传感器和ph值传感器,方便的观察到料液在相应反应过程中的实际混合状态,并即时采集、控制反应不同时段中料液的温度、压力、ph值等各种参数。
34.本发明工作原理:
35.参照说明书附图1-7,在使用时,反应管5直径、数量、长度按照装置产能和产品所需工艺停留时间排列设置,换热腔3内充满换热体以进行反应热交换,反应管5内装填比表面积较大的颗粒状高活性催化剂,颗粒状催化剂之间又形成了无数不规则物理间隙,等同于无数微型通道,物料由进料管9进入,在反应管5内按一定角度排列转换混合反应,从出料管10排出,液体配合高压输料泵与气体通过前置气液混合器,使料液与气体形成微气泡乳化液态并进入反应管5内,在颗粒催化剂堆积的微型通道内与催化剂孔隙表面进行气固液传质反应,只需打开一侧管板2的变径法兰6盖板7的情况下,即可暴露出变径的反应管5口,进行清洗内构件或装填、更换催化剂操作,十分快捷方便,该装置反应管5内的流体不依靠传统固定床自然垂直流动在催化剂表面进行气固液交换,而是总体自下而上模式在相同单位体积内,此种模块结构比反应管5平行排列,终端以u形管、法兰连接,反应管5外通常再辅以伴热套管的传统管式反应器模式要节省大量空间、材料,有效反应管5长度增加,延长反应行程,大大提高了制造、安装、使用效率,节能效果显著,本发明结构布局合理,结构紧凑,可根据生产现场需要切换安装、运行、维护更换催化剂方式,操作方便,可实现固体催化剂的快速装填、拆装,或内构件的清洗,大大缩短停产检修时间,在实现反应器本质安全的基础上,大幅度节约土地、厂房建设、设备投资成本,特别适合于精细化工、制药行业多品种、小批量的生产模式,其独有的拆装方式可以迅速实现装填催化剂和不同产品转换工作,得以实现用送料泵配合前置气液混合器、反应管5进行快速反应,与现有技术相比,改变了现有固定床内液体通过复杂的分配器结构,依靠垂直滴流方式与床内气体在催化剂表面完成气液交换化学反应,因此,本发明特有的反应方式大幅度提高了生产效率,降低了投资和生产成本。
36.参照说明书附图1-7,壳程1采用矩形,易于反应管5与整机模块化排列组装,物料由进料管9进入,在反应管5内按一定角度排列转换混合反应,从出料管10排出,盖板7适当部位使用耐压视镜,可以方便的看到料液在相应反应过程中的实际混合状态,并即时采集、
控制反应不同时段中料液的温度、压力、ph值等各种参数,设有拉杆11用于抵抗换热腔3通入换热体后形成的压力使矩形壳程1不会膨胀变形。
37.以上只通过说明的方式描述了本发明的某些示范性实施例,毋庸置疑,对于本领域的普通技术人员,在不偏离本发明的精神和范围的情况下,可以用各种不同的方式对所描述的实施例进行修正。因此,上述附图和描述在本质上是说明性的,不应理解为对本发明权利要求保护范围的限制。
再多了解一些
本文用于创业者技术爱好者查询,仅供学习研究,如用于商业用途,请联系技术所有人。