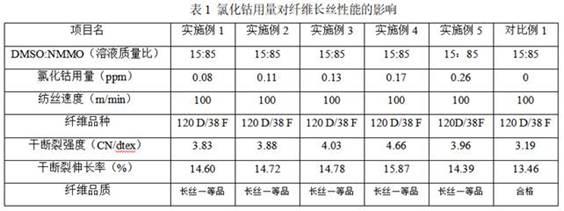
一种nmmo溶剂法菌草再生纤维素纤维及其制备方法
技术领域
1.本发明属于化学纺织新材料领域,具体涉及一种nmmo溶剂法菌草再生纤维素纤维及其制备方法。
背景技术:
2.lyocell纤维是21世纪绿色纤维之一,它以木材原料为主,通过精制所得木浆粕,再以nmmo(n-甲基吗啉-n-氧化物)为溶剂,不经过化学反应直接溶解浆粕成纤维素溶液,再经抽丝工序而得。近年来,lyocell纤维迅速发展,出现了对竹lyocell纤维的研制和开发,但对菌草lyocell纤维的研究报道较少,如何高值化利用菌草并且制备出一种性能优异的菌草再生纤维素纤维成为纺织领域研发的技术问题。
3.纤维素在nmmo中的溶解程度对溶液可纺性和纤维性能均有较大的影响,一般而言,nmmo熔点高,共溶/熔时易使纤维素和nmmo发生降解,随着nmmo中水含量的增加,溶液的熔点下降,但同时含水的nmmo溶解纤维素的能力也下降。因此,如何解决菌草纤维在nmmo中的溶解问题对制备性能优异的nmmo溶剂法菌草再生纤维素纤维具有重大意义。
技术实现要素:
4.针对现有技术中存在的问题和不足,本发明的目的旨在提供一种nmmo溶剂法菌草再生纤维素纤维及其制备方法。
5.为实现发明目的,本发明采用的技术方案如下:本发明第一部分提供一种nmmo溶剂法菌草再生纤维素纤维的制备方法,包括以下步骤:(1)向菌草浆粕中加入dmso/nmmo混合溶剂,并同时加入抗氧化剂和氯化钴混合均匀,得到混合体系;(2)将混合体系进行溶胀、溶解处理后得到菌草纤维胶液,菌草纤维胶液经过滤、脱泡和纺丝处理后得到菌草再生纤维素纤维。
6.进一步地,所述混合体系中氯化钴的含量为0.01~0.5 ppm。
7.进一步地,所述混合体系中菌草浆粕的浓度为3 wt%~5 wt%。
8.进一步地,所述dmso/nmmo混合溶剂由dmso溶液和nmmo溶液质量比按(2~20):(80~98)配比得到。
9.更进一步地,所述dmso/nmmo混合溶剂由dmso溶液和nmmo溶液质量比按(10~20):(80~90)配比得到。
10.进一步地,所述dmso溶液的浓度为85 wt%~99wt%,所述nmmo溶液的浓度为50 wt%~98 wt%。
11.更进一步地,所述dmso溶液的浓度为90 wt%~95wt%,所述nmmo溶液的浓度为75 wt%~98 wt%。
12.进一步地,步骤(2)中所述溶胀的时间为30~120min,溶胀温度为35~50℃。
13.更进一步地,步骤(2)中所述溶胀的时间为50~120 min,溶胀温度为35~45℃。
14.进一步地,步骤(2)中所述溶解的时间为2~5h,溶解温度为80~120℃。
15.更进一步地,进一步地,步骤(2)中所述溶解的时间为3.5~5h,溶解温度为90~115℃。
16.进一步地,步骤(2)中所述纺丝的过程中选取nmmo溶液作凝固浴,所述nmmo溶液的浓度为1 wt%~8wt%。
17.进一步地,步骤(1)中所述抗氧化剂为没食子酸丙酯。
18.进一步地,所述没食子酸丙酯的用量为菌草浆粕的0.01~0.05wt%,优选0.01~0.025wt%。
19.更进一步地,步骤(2)中所述纺丝的过程中选取nmmo溶液作凝固浴,所述nmmo溶液的浓度为1 wt%~6wt%。
20.进一步地,所述凝固浴的温度为15~30℃,优选18~25℃。
21.进一步地,步骤(2)中所述纺丝的速度为60~180 m/min,优选70~150 m/min。
22.进一步地,步骤(2)中所述纺丝过程的上浆量为0.1%~3.5%,优选0.5%~3.0%。
23.进一步地,步骤(2)中所述纺丝过程的纺丝计量泵流量为0.54~0.835 ml/r。
24.本发明第二部分提供一种利用上述方法制备的菌草再生纤维素纤维。
25.与现有技术相比,本发明的有益效果如下:1.本发明选用dmso/nmmo混合溶剂代替传统再生纤维素纤维溶剂体系,并同时加入了抗氧化剂没食子酸丙酯和氯化钴,共同促进了纤维素的溶胀和溶解,制得的再生纤维素纤维的品质可达到一等品标准,其中长丝纤维的干断裂强度3.80~4.70 cn/dtex,干断裂伸长率达15.87%,短丝纤维的干断裂强度达2.03 cn/dtex,干断裂伸长率可超过16.0%。
26.2. 本发明使用的菌草浆粕可由菌草经制浆工艺制得,菌草产量高,价格低,可有限缓解现有再生纤维素纤维生产原料不足的问题,另外,nmmo溶剂法菌草再生纤维素纤维可以直接使用现有的生产设备,大大降低纤维素纤维的生产成本,提高企业经济效益。
27.3. 本发明的溶解条件温和、环境友好无毒,符合国家高效发展战略要求。
具体实施方式
28.以下实施例仅适用于对本发明进行进一步阐述。应该说明的是,本发明所使用的所有技术以及科学术语除另有说明外具有与本发明所属技术领域相同的含义。下列实施例中未注明具体条件的实验方法,均采用本技术领域常规技术,或按照生产厂商所建议的条件;所用试剂或仪器未注明生产厂商者,均为可以通过市购获得的常规产品。
29.为了使得本领域技术人员能够更加清楚地了解本发明的技术方案,以下将结合具体的实施例详细说明本发明的技术方案。
30.为了研究氯化钴用量对所得菌草再生纤维素纤维性能的影响,本发明进行了实施例1~5和对比例1实验,以下实施例1~5和对比例1所得菌草纤维素纤维均为长丝,纺丝设备为连续式纺丝机。
31.实施例1:一种nmmo溶剂法菌草再生纤维素纤维的制备方法,包括以下步骤:(1)采用1.2%乙醇溶液对3 kg菌草浆粕进行杀菌消毒,烘干,备用;
(2)将90 wt%的dmso溶液和96wt%的nmmo溶液按质量比15:85混合,得到混合溶剂,向步骤(1)烘干后的菌草浆粕中加入混合溶剂,并同时加入菌草浆粕0.01wt%的没食子酸丙脂和0.08 ppm氯化钴混合均匀,得到混合体系;(3)将步骤(2)得到的混合体系于35℃下充分溶胀120 min,然后将混合体系升温至100℃继续溶解4.5h,得到菌草纤维胶液;(4)菌草纤维胶液经过滤、脱泡后进行纺丝,纺丝液经凝固浴形成初生丝,再经过牵伸、烘干、上油、制成再生纤维素纤维,最后直接卷绕成型得到菌草再生纤维素纤维;所述凝固浴为5wt%的nmmo水溶液,凝固浴温度为23℃,纺丝速度为100 m/min,上浆量为1.3%,计量泵流量为0.835 ml/r。
32.实施例2:实施例2的内容与实施例1基本相同,其不同之处在于,步骤(2)中氯化钴的添加量为0.11 ppm。
33.实施例3:实施例3的内容与实施例1基本相同,其不同之处在于,步骤(2)中氯化钴的添加量为0.13 ppm。
34.实施例4:实施例4的内容与实施例1基本相同,其不同之处在于,步骤(2)中氯化钴的添加量为0.17 ppm。
35.实施例5:实施例5的内容与实施例1基本相同,其不同之处在于,步骤(2)中氯化钴的添加量为0.26 ppm。
36.对比例1:对比例1的内容与实施例1基本相同,其不同之处在于,步骤(2)中未加入氯化钴。
37.性能测试:对实施例1~5和对比例1所得菌草再生纤维素纤维进行干断裂强度和干断裂伸长率进行测试,结果参见表1,纤维品种120 d/38 f中f表示纺丝喷头孔数,d表示9 km纤维的质量(即纤度)。
38.从表1可以看出,相较于未加入氯化钴的对比例1,溶胀和溶解过程中添加了氯化钴的实施例1~5所得长丝纤维产品的干断裂强度和干断裂伸长率均有明显提升。随着氯化钴用量的增加,所得纤维的干断裂强度和干断裂伸长率呈现先升高后降低的趋势,氯化钴
在0.17 ppm时,溶胀、溶解效果最好,使得整个胶液体系纺制出的纤维强度高、韧性好,当氯化钴用量超过0.17 ppm后,使得胶液聚合度过低,造成纺丝纤维质量有所降低。
39.为了进一步研究氯化钴对制备的菌草再生纤维素纤维短丝性能的影响,以下实施例6~7和对比例2所得菌草再生纤维素纤维均为短丝,纺丝设备为连续式纺丝机。
40.实施例6:一种nmmo溶剂法菌草再生纤维素纤维的制备方法,包括以下步骤:(1)采用1.2%乙醇溶液对3 kg菌草浆粕进行杀菌消毒,烘干,备用;(2)向步骤(1)烘干后的菌草浆粕中加入dmso/nmmo混合溶剂,并同时加入没食子酸丙脂和氯化钴混合均匀,得到混合体系;所述混合溶剂是由90 wt%的dmso溶液和96wt%的nmmo溶液按15:85配比组成;没食子酸丙酯的添加量为菌草浆粕的0.01wt%,所得混合体系中菌草浆粕的浓度为4wt%;氯化钴的添加量为0.09 ppm;(3)将步骤(2)得到的混合体系于35℃下充分溶胀120 min,然后将混合体系升温至100℃继续溶解4.5h,得到菌草纤维胶液;(4)菌草纤维胶液经过滤、脱泡后进行纺丝,得到菌草再生纤维素纤维;所述纺丝过程中凝固浴为5wt%的nmmo水溶液,凝固浴温度为23℃,纺丝速度为60 m/min,上浆量为1.3%,计量泵流量为0.835 ml/r。
41.实施例7:实施例7的内容与实施例6基本相同,其不同之处在于,步骤(2)中氯化钴的添加量为0.10 ppm;对比例2:对比例2的内容与实施例6基本相同,其不同之处在于,步骤(3)中未加入氯化钴。
42.性能测试:对实施例6、7和对比例2所得菌草再生纤维素纤维进行干断裂强度和干断裂伸长率进行测试,结果参见表2,纤维品种1.67d
×
38 mm中mm表示短纤维的长度,d表示9 km纤维的质量(即纤度)。
43.由表2可知,溶胀、溶解过程未添加氯化钴时,制备的纤维短丝强度低,韧性差;溶解过程添加氯化钴后制备的纤维短丝的强度和韧性均有明显提高,当氯化钴的添加量为
0.1 ppm时,再生纤维素纤维短丝的干断裂强度和干断裂伸长率分别为2.03 cn/dtex和15.72%,具备短丝一等品的优良品质。
44.实施例8:实施例8的内容与实施例1基本相同,其不同之处在于:步骤(2)中dmso溶液和nmmo溶液按质量比10:90进行混合,氯化钴的添加量为0.08 ppm。
45.实施例9:实施例9的内容与实施例1基本相同,其不同之处在于:步骤(2)中dmso溶液和nmmo溶液按质量比20:80进行混合。
46.实施例10:实施例10的内容与实施例1基本相同,其不同之处在于:步骤(2)中dmso溶液和nmmo溶液按质量比2.5:97.5进行混合。
47.实施例8~10所得菌草再生纤维素纤维的性能指标参见表3。
48.上述实施例为本发明的具体实施方式,但本发明的实施方式并不受上述实施例的限制,其它任何不超出本发明设计思路组合、改变、修饰、替代、简化,均落入本发明的保护范围之内。
再多了解一些
本文用于创业者技术爱好者查询,仅供学习研究,如用于商业用途,请联系技术所有人。