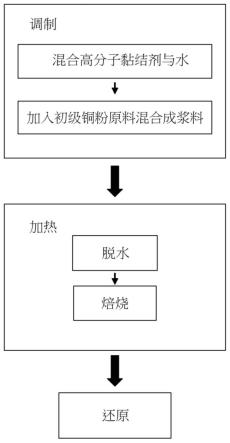
1.本发明是关于一种金属颗粒及金属颗粒的制造方法,特别是关于一种铜粒及铜粒的制造方法。
背景技术:
2.散热领域中热管的使用已经越来越普遍。热管的工作原理是在于,热管的内壁面形成有毛细结构,因此热管内的工作流体能沿毛细结构迅速流动,即时传递热量。热管的毛细结构有多种形式,其中铜粉烧结型的毛细结构具有更强的毛细力、更大的热量传输能力、更好的抗重力效果,最常被用于高功率伺服器、高阶笔记型电脑、及一些工业用电脑领域中。
3.在热管的制造过程中,会将铜粉原料烧结于一管体的内壁面中。铜粉原料的制造方法,主要有水雾化法、电解法、团化法、和球磨法,以制作出低松装密度(apparent density)的铜粉原料,而其中最广为使用的是水雾化法。为了进一步降低松装密度、提高孔隙率,会在水雾化法中进行增氧操作的方法,借此在铜粉原料的表面产生空洞或裂缝。然而,经过增氧操作后所制成的铜粉原料可能有氧化的现象,将会影响烧结后毛细结构的性能以及所制得的热管的可靠度。
4.有鉴于此,提出一种更佳的改善方案,乃为此业界亟待解决的问题。
技术实现要素:
5.本发明的主要目的在于,提出一种铜粒的制造方法以及铜粒,其该制造方法简单、易于量产,且所制得的铜粒具有较大的表面积、更低的松装密度。
6.为达上述目的,本发明所提出的制造方法依序包含下列步骤:
7.将初级铜粉原料、高分子黏结剂、及水混合制成浆料;
8.对该浆料加热制成次级铜粉原料;以及
9.对该次级铜粉原料进行还原反应制成铜粒。
10.为达上述目的,本发明所提出的铜粒包含三个以上的初级铜粉,该等初级铜粉连接成链状。
11.因此,本发明的优点在于,将现有的铜粉以链状形式结合成铜粒,具有较大的表面积、更低的松装密度(例如可达1.0g/cm3至2.5g/cm3)、较佳的毛细力。并且,本发明所提供的铜粒制作方法简单、易于量产,将本发明的铜粒用于制作热管时,还能提升散热效率。此外,本发明的铜粒成分单纯,并不会影响热管的可靠度。
12.进一步而言,如前所述的铜粒的制造方法中,于“将初级铜粉原料、高分子黏结剂、及水混合制成浆料”的步骤中,是先将水加热后,加入所述高分子黏结剂,待所述高分子黏结剂溶解后加入所述初级铜粉原料。
13.进一步而言,如前所述的铜粒的制造方法中,于“将初级铜粉原料、高分子黏结剂、及水混合制成浆料”的步骤中,是将水加热至40℃至70℃。
14.进一步而言,如前所述的铜粒的制造方法中,于“将初级铜粉原料、高分子黏结剂、及水混合制成浆料”的步骤中,所述高分子黏结剂溶解过程中被加热至60℃至90℃后,加入所述初级铜粉原料。
15.进一步而言,如前所述的铜粒的制造方法中,于“将初级铜粉原料、高分子黏结剂、及水混合制成浆料”的步骤中,所述初级铜粉原料、所述高分子黏结剂、及水混合后,加热至65℃至95℃,制成浆料。
16.进一步而言,如前所述的铜粒的制造方法中,于“对该浆料加热制成次级铜粉原料”的步骤中,先将所述浆料加热至脱水。
17.进一步而言,如前所述的铜粒的制造方法中,所述高分子黏结剂包含玉米淀粉、土豆淀粉、小麦淀粉、木薯淀粉、或其组合。
18.进一步而言,如前所述的铜粒的制造方法中,于“对该浆料加热制成次级铜粉原料”的步骤中,加热所述浆料至300℃至600℃,借此烧除所述高分子黏结剂。
19.进一步而言,如前所述的铜粒中,粒径为40目至325目。
附图说明
20.图1为本发明的制造方法的流程图。
21.图2为本发明的铜粒的显微照片。
具体实施方式
22.以下配合附图及本发明的较佳实施例,进一步阐述本发明为达成预定发明目的所采取的技术手段。
23.本发明提出一种铜粒的制造方法以及铜粒。
24.首先请参考图1。该制造方法依序包含调制步骤、加热步骤、及还原步骤。
25.于调制步骤中,是将初级铜粉原料、高分子黏结剂、及水混合制成浆料。初级铜粉原料为现有技术所制得的铜粉。换言之,本发明是以现有的铜粉为原料进行再次加工,以制成具有更低松装密度、更高孔隙率的颗粒。此外,较佳的是选用以水雾化法所制得的铜粉作为初级铜粉原料进行加工。高分子黏结剂可为玉米淀粉、土豆淀粉、小麦淀粉、木薯淀粉,或其组合,例如:高分子黏结剂可为玉米淀粉和土豆淀粉的组合,或者,高分子黏结剂可为土豆淀粉、小麦淀粉、木薯淀粉的组合。
26.于调制步骤中,首先将高分子黏结剂与水充分混合后,再加入初级铜粉原料混合制成浆料。具体而言,是先将水加热后,加入高分子黏结剂至重量百分率为5%至20%之间,待高分子黏结剂溶解后加入初级铜粉原料,至初级铜粉原料的重量百分率为5%至50%之间。于调制步骤中,可将水加热至40℃至70℃后加入高分子黏结剂。另外,也可在高分子黏结剂溶解过程中进一步加热至60℃至90℃,然后再加入初级铜粉原料。最后,可于初级铜粉原料、高分子黏结剂、及水混合后再加热至65℃至95℃,并使混合均匀而不分层,即制得浆料。较佳度,于初级铜粉原料、高分子黏结剂、及水混合的同时进行隔水加热。
27.于加热步骤中,可分为两阶段地加热。第一阶段加热可为将浆料加热至脱水,第二阶段加热可加热至烧除高分子黏结剂而形成次级铜粉原料。第一阶段加热中,可将浆料置于60℃至200℃的烤箱中进行烘干。第二阶段加热中,可将烘干脱水后的浆料置于焙烧炉中
进行焙烧,焙烧炉的温度可为300℃至600℃,焙烧时间可为二至六小时。于焙烧过程中会通入空气,以使高分子黏结剂会因高温而燃烧,借此烧除高分子黏结剂。在烧除高分子黏结剂后即形成次级铜粉原料。
28.由于次级铜粉原料的颗粒表面可能有氧化层,因此后续可再进行还原步骤,以除去氧化层。具体而言,于还原步骤中,是将次级铜粉原料加热至300℃至600℃,并通入氢气及氮气的混合气体,直到所有的氧化层被还原,至此形成本发明的铜粒。
29.后续可再进行除铁、筛分不同等级或粒径大小,经过测试后包装、入库。
30.接着请参考图2,其是以工作距离16.4毫米(mm)、加速电压15.0k伏特(v)、放大倍数100倍的条件下所拍摄的铜粒照片。图2中右下角的两相邻的参考点的距离为50微米(μm)。通过上述制造方法所制成的铜粒,每个铜粒的粒径大小可为40目至325目,且每个铜粒包含了三个以上的初级铜粉。换言之,本发明的铜粒最低可由三个初级铜粉相连结所构成。这些初级铜粉可连接成随机的链状,且可为单一的直链或树枝状、珊瑚状的支链。
31.综上所述,本发明将现有的铜粉以链状形式结合成铜粒,具有较大的表面积、更低的松装密度(例如可达1.0g/cm3至2.5g/cm3)、较佳的毛细力。并且,本发明所提供的铜粒制作方法简单、易于量产,将本发明的铜粒用于制作热管时,还能提升散热效率。此外,本发明的铜粒成分单纯,并不会影响热管的可靠度。以上所述仅是本发明的较佳实施例而已,并非对本发明做任何形式上的限制,虽然本发明已以较佳实施例公开如上,然而并非用以限定本发明,任何本领域技术人员,在不脱离本发明技术方案的范围内,当可利用上述公开的技术内容作出些许更动或修饰为等同变化的等效实施例,但凡是未脱离本发明技术方案的内容,依据本发明的技术实质对以上实施例所作的任何简单修改、等同变化与修饰,均仍属于本发明技术方案的范围内。
再多了解一些
本文用于创业者技术爱好者查询,仅供学习研究,如用于商业用途,请联系技术所有人。