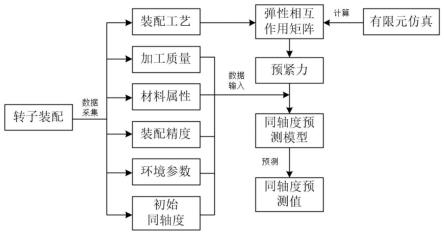
1.本发明属于航空发动机装配领域,涉及一种面向低压转子装配的螺栓拧紧工艺优 化方法。
背景技术:
2.低压转子是航空发动机中重要的组成部分,主要是由带有止口和螺栓连接的多级 盘鼓堆叠而成,螺栓连接是其最常用的紧固连接方式。通过螺栓连接一方面能够保证 盘鼓的配合精度,另一方面能够保证盘鼓之间的紧固连接,在工作时传递扭矩。因此, 这就要求螺栓预紧力尽可能的保证均匀,避免应力集中。但是由于螺栓之间的弹性相 互作用,后拧紧的螺栓会对先拧紧的螺栓产生影响,导致实际预紧力与预期相差甚远。 螺栓组预紧力分布过于离散进一步对航空发动机整机产生影响。螺栓预紧力过大可能 会引起螺纹屈服,降低螺栓连接结构的承载能力,而预紧力太小又会使螺栓连接刚度 降低以至于松脱,导致转子发生严重故障。同时,在螺栓拧紧过程中,每次拧紧都会 令转子发生偏转,所有偏转结果会在空间上累加,使得上下级转子在空间上发生相对 偏转,导致转子同轴度超差。
3.文献“某装载机轮辋螺栓拧紧工艺参数优化”使用有限元和ug软件,对结构复杂 实体切割,将结构划分为网格质量较高的六面体单元和五面体单元。划分完网格之后 对模型上不同的部件分别附加相对应的材料属性,并在不同零件之间设置相应的接触。 最后通过相应的加载曲线curve控制连接螺栓两部分的一维弹簧单元来施加螺栓预紧 力,通过控制加载时间可得出螺栓应力变化曲线。对比不同拧紧顺序下的螺栓拧紧后 的应力均值与方差得出最佳拧紧顺序。但是该文献只针对螺栓拧紧顺序进行了优化, 而实际过程中对装配件影响较大的还有螺栓的拧紧力矩,对此,该文献并没有涉及。 此外,该文献方法也较为复杂,在实际应用过程中具有局限性。
技术实现要素:
4.螺栓连接是航空发动机低压转子各部件连接的主要方式,由于弹性相互作用关系 的影响,容易造成螺栓组预紧力分布不均,虽然能够满足刚度需要,但可能会导致各 部件空间相对位姿发生偏转,容易引起同轴度超差。为解决转子装配同轴度与刚度之 间的优化矛盾问题,本发明提出了面向低压转子装配的螺栓拧紧工艺优化方法,以螺 栓预紧力为优化变量,同轴度与刚度为优化目标,以实际装配过程中已经安装好的螺 栓的拧紧力矩与预紧力均布限制为约束条件,建立同轴度与刚度双目标优化模型;利 用优化算法求解得到后续待安装螺栓初始预紧力非劣解组,实现同轴度与刚度的同步 优化。
5.本发明的技术方案为:
6.所述一种面向低压转子装配的螺栓拧紧工艺优化方法,包括以下步骤:
7.步骤1:建立面向装配过程的低压转子同轴度预测模型c;建立低压转子螺栓连接 刚度模型k;
8.步骤2:构建同轴度与刚度双目标优化模型:
9.低压转子装配后同轴度与刚度双目标优化目标函数为:
[0010][0011]
式中,λ1为同轴度目标的权重参数,λ2为刚度目标的权重参数;c为低压转子装配后 的同轴度;k为低压转子螺栓连接刚度;l为螺栓预紧力向量;li为第i个螺栓的预紧 力;
[0012]
优化变量为:螺栓预紧力向量l;
[0013]
约束条件为:
[0014][0015]
式中,c
max
为螺栓拧紧后允许的最大同轴度;k
min
为螺栓拧紧后允许的最小刚度;l
max
为 单个螺栓最大的预紧力;l
min
为单个螺栓最小的预紧力;
[0016]
步骤3:对步骤2建立的双目标优化模型进行求解,得到螺栓预紧力最优解。
[0017]
进一步的,步骤3中,采用nsga-ii算法对步骤2建立的双目标优化模型进行求 解,得到螺栓预紧力非劣解组,在螺栓预紧力非劣解组中选择最优解。
[0018]
进一步的,步骤2的约束条件中,单个螺栓最小预紧力l
min
根据力矩扳手的最小精 度确定,最大预紧力l
max
根据钢制连接螺栓预紧力公式f≤(0.6~0.8)
×
δs×
a确定,其中 δs为屈服极限,a为螺纹小径横截面积。
[0019]
进一步的,步骤1中,建立所述低压转子同轴度预测模型的过程为:
[0020]
步骤1.1:对低压转子装配过程中,对特定装配工艺下的多螺栓拧紧过程进行数值 模拟,通过拟合预紧力变化值建立弹性相互作用模型,并解算得到当前装配工艺下的 弹性相互作用矩阵[a];
[0021]
步骤1.2:建立基于gru网络的低压转子同轴度预测模型,并对模型进行训练, 得到训练完成的基于gru网络的低压转子同轴度预测模型;
[0022]
其中进行同轴度预测模型训练时的输入包括:装配过程的时间步t
step
、该时间步 内的转子装配影响因素f、该时间步内的同轴度低压转子coa;
[0023]
所述转子装配影响因素f包括装配工艺f
gy
,且装配工艺f
gy
通过步骤1.1得到的 弹性相互作用矩阵[a]转换为装配过程中的螺栓预紧力,并输入同轴度预测模型。
[0024]
进一步的,步骤1.1中,所述弹性相互作用模型为:
[0025]
prlod=a(t
lj
,t
sx
,t
lc
,t
qd
)
[0026]
其中prlod为螺栓组预紧力;a为弹性相互作用矩阵;t
lj
为螺栓拧紧力矩;t
sx
为螺栓 拧紧顺序;t
bs
为螺栓拧紧轮次;t
qd
为螺栓拧紧起点。
[0027]
进一步的,步骤1.1中,根据螺栓拧紧力矩t
lj
、螺栓拧紧顺序t
sx
、螺栓拧紧轮次t
bs
、 螺栓拧紧起点t
qd
,对该装配工艺下的螺栓拧紧过程进行仿真,根据仿真结果,利用公 式
[0028]
[0029][0030]
解算得到当前装配工艺下的弹性相互作用矩阵[a];其中a
ij
表示弹性相互作用矩阵系 数,f
ij
表示螺栓j拧紧后,第i个螺栓的剩余预紧力;δfj表示第j个螺栓拧紧时预紧 力的变化量。
[0031]
进一步的,步骤1.2中,所述装配工艺f
gy
包括螺栓拧紧力矩、拧紧顺序、拧紧轮 次、拧紧起点和盘鼓安装相位;其中螺栓拧紧力矩、拧紧顺序、拧紧轮次、拧紧起点 通过步骤1得到的弹性相互作用矩阵[a]转换为装配过程中的螺栓预紧力,连同盘鼓安 装相位一并输入同轴度预测模型。
[0032]
进一步的,利用螺栓拧紧力矩、拧紧顺序、拧紧轮次、拧紧起点,根据弹性相互 作用公式
[0033]
{f0} [a]{δf}={ff}
[0034]
得到每一加载步之后的各个螺栓预紧力;其中{f0}为每个加载步前螺栓的初始预紧力 (n
×
1);[a]为弹性相互作用矩阵(n
×
n);{δf}为每个加载步螺栓预紧力增量(n
×
1);{ff} 为每个加载步后螺栓的剩余预紧力(n
×
1);n为螺栓组中的螺栓数目;;每次拧紧一个 螺栓为一个加载步。
[0035]
进一步的,转子装配过程中的影响因素还包括加工质量f
jg
、材料属性fd、装配精 度f
jd
和环境参数f
hj
:并采用z-score标准化方法对转子装配过程中的影响因素数据进 行标准化处理,使所有影响因素数据都处于同一量级;
[0036]
所述加工质量f
jg
进行向量形式表达式为:
[0037]fjg
=(q
pm
,q
td
,q
cc
,q
zx
,qy,q
cz
,q
tz
)
[0038]
式中q
pm
为盘鼓上下止口配合平面度;q
td
为盘鼓配合止口处相对于旋转轴跳动度;q
cc
为盘鼓止口配合处表面粗糙度;q
zx
为盘鼓中心轴线直线度;qy为盘鼓外圆与内圆圆 度;q
cz
为盘鼓端面与轴线位置垂直度;q
tz
为盘鼓自身同轴度;
[0039]
所述材料属性fd进行向量形式表达式为:
[0040]fcl
=(e,τ,ρ,μ)
[0041]
式中e为杨氏模量;τ为泊松比;ρ为密度;μ为摩擦系数;
[0042]
所述装配精度f
jd
进行向量形式表达式为:
[0043]fjd
=(paral,intf)
[0044]
式中paral为盘鼓止口上下端面装配平行度;intf为盘鼓止口装配过盈量;
[0045]
所述环境参数f
hj
进行向量形式表达式为:
[0046]fhj
=(t,rh)
[0047]
式中t为进行转子装配时的环境温度;rh进行转子装配时的环境湿度。
[0048]
进一步的,步骤1中,所述连接刚度模型k为:
[0049][0050]
式中,k为螺栓连接刚度;kb为螺栓刚度;kc为被连接件刚度;kd为结合面接触刚 度。
据进行标准化处理,使所有影响因素数据都处于同一量级。
[0068]
三、构建弹性相互作用模型
[0069]
低压风扇转子在装配过程中,螺栓组之间存在着弹性相互作用。装配工艺中的拧 紧力矩、拧紧顺序、拧紧轮次与拧紧起点在模型中不便于输入,因此本发明通过建立 弹性相互作用模型将这些装配工艺统一转化为螺栓预紧力的变化,其过程可以表示为 式2所示。本发明通过建立与转子相同结构的三维模型,使用有限元方法对特定装配 工艺下的螺栓组预紧力变化情况进行仿真,将得到的数据进行处理计算获得弹性相互 作用矩阵,建立弹性相互作用模型。
[0070]
prlod=a(t
lj
,t
sx
,t
lc
,t
qd
)
ꢀꢀꢀꢀꢀꢀꢀꢀꢀꢀꢀꢀꢀꢀꢀꢀ
(2)
[0071]
式中:prlod为螺栓组预紧力;a为弹性相互作用矩阵;t
lj
为螺栓拧紧力矩;t
sx
为 螺栓拧紧顺序;t
bs
为螺栓拧紧轮次;t
qd
为螺栓拧紧起点。
[0072]
四、构建同轴度预测模型
[0073]
基于上述步骤内容构建同轴度预测模型y
tz
:将装配过程包含的加载步数作为模型 的时间步t
step
,以该时间步t内的装配工艺f
gy
、加工质量f
zp
、材料属性f
cl
、装配精 度f
jd
、环境参数f
hj
作为输入,将该时间步内的同轴度coa作为目标输出,输入到建 立的预测模型中进行训练,得到同轴度预测模型。同轴度预测模型的建立如式3所示:
[0074][0075]
式中:y
tz
为转子装配同轴度预测模型;为预测模型的训练参数;t
step
为输入 时间步长度;coa为该时间步内的同轴度;θ为模型训练获得的参数集。
[0076]
五、构建刚度计算模型
[0077]
刚度作为衡量螺栓连接件性能好坏的重要指标之一,尤其对于低压转子这种高速 转动件,刚度越大所能承受的荷载也越大,能够有效提高转子的可靠性。除了螺栓刚 度、被连接件刚度之外,本技术将结合面接触刚度加入螺栓连接刚度计算模型中。
[0078]
螺栓连接刚度主要由螺栓刚度、被连接件刚度和结合面接触刚度三部分串联而成。
[0079][0080]
式中,k为螺栓连接刚度;kb为螺栓刚度;kc为被连接件刚度;kd为结合面接 触刚度。
[0081]
六、构建同轴度与刚度双目标优化模型
[0082]
综合同轴度预测模型与刚度计算模型,低压转子装配后同轴度与刚度双目标优化 目标函数如下所示。
[0083][0084]
式中,λi为第i个目标函数的权重参数;c为低压转子装配后的同轴度;k为低压 转子螺栓连接刚度;l为螺栓预紧力向量;li为第i个螺栓的预紧力。
[0085]
接下来,就以上六个部分作详细描述:
[0086]
一、影响因素统一表达
[0087]
(1)装配工艺
[0088]
转子装配过程中不同的装配工艺参数会引起螺栓预紧力的变化,进而引起同轴度 的变化,该过程中主要的工艺参数包括螺栓拧紧力矩、拧紧顺序、拧紧遍数、拧紧起 点,安装相位,上述五种装配工艺参数进行向量形式表达后如式6所示:
[0089]fgy
=(t
lj
,t
sx
,t
lc
,t
qd
,p
az
)
ꢀꢀꢀꢀꢀꢀꢀꢀꢀꢀꢀꢀꢀꢀꢀꢀꢀꢀꢀ
(6)
[0090]
式中:f
gy
为装配工艺;t
lj
为螺栓拧紧力矩;t
sx
为螺栓拧紧顺序;t
bs
为螺栓拧紧 轮次;t
qd
为螺栓拧紧起点;p
az
为盘鼓安装相位。
[0091]
(2)加工质量
[0092]
由于装配的两级盘鼓的加工质量不同引起的初始同轴度不同,进而导致装配后的 同轴度发生变化。这些加工质量主要包括:平面度、跳动度、粗糙度、直线度、圆度、 垂直度、同轴度,此处所描述的同轴度指的是单级盘鼓自身的同轴度,并非指装配后 的整体同轴度。上述七种加工质量进行向量形式表达后如式7所示:
[0093]fjg
=(q
pm
,q
td
,q
cc
,q
zx
,qy,q
cz
,q
tz
)
ꢀꢀꢀꢀꢀꢀꢀꢀꢀꢀꢀꢀꢀꢀꢀꢀꢀꢀ
(7)
[0094]
式中:f
jg
为加工质量;q
pm
为盘鼓上下止口配合平面度;q
td
为盘鼓配合止口处相 对于旋转轴跳动度;q
cc
为盘鼓止口配合处表面粗糙度;q
zx
为盘鼓中心轴线直线度;qy为盘鼓外圆与内圆圆度;q
cz
为盘鼓端面与轴线位置垂直度;q
tz
为盘鼓自身同轴度。
[0095]
(3)材料属性
[0096]
盘鼓自身的材料属性参数会影响所受摩擦力以及变形程度,进而影响到同轴度的 变化。材料属性主要有:杨氏模量、泊松比、密度、摩擦系数。上述四种材料属性进 行向量形式表达后如式8所示:
[0097]fcl
=(e,τ,ρ,μ)
ꢀꢀꢀꢀꢀꢀꢀꢀꢀꢀꢀꢀꢀꢀꢀꢀꢀꢀꢀꢀꢀ
(8)
[0098]
式中:f
cl
为材料属性;e为杨氏模量;τ为泊松比;ρ为密度;μ为摩擦系数。
[0099]
(4)装配精度
[0100]
当上下级盘鼓之间存在平行度误差时,因存在止口配合,两接触面贴合之后,预 紧力不均与会引起上下级盘鼓偏转,最终影响转子装配后的同轴度。其中的装配精度 参数包括:平行度,过盈量。上述两种装配精度进行向量形式表达后如式9所示:
[0101]fjd
=(paral,intf)
ꢀꢀꢀꢀꢀꢀꢀꢀꢀꢀꢀꢀꢀꢀꢀꢀꢀꢀꢀꢀ
(9)
[0102]
式中:f
jd
为装配精度;paral为盘鼓止口上下端面装配平行度;intf为盘鼓止口 装配过盈量。
[0103]
(5)环境参数
[0104]
装配时的环境参数也会在一定程度上影响装配同轴度。其中主要的环境参数包括: 温度、湿度。将这两种主要参数进行向量形式表达后如10所示:
[0105]fhj
=(t,rh)
ꢀꢀꢀꢀꢀꢀꢀꢀꢀꢀꢀꢀꢀꢀꢀꢀꢀꢀꢀꢀꢀꢀ
(10)
[0106]
式中:f
hj
为环境参数;t为进行转子装配时的环境温度;rh进行转子装配时的 环境湿度。
[0107]
二、数据预处理
[0108]
同轴度影响因素包含零件的装配工艺、加工质量、材料属性等数据,这些数据具 有不同的量纲以及数量级,当数据之间水平相差较大时,会影响后续所建立的预测模 型的准确性和可靠性,因此需要对原始数据进行标准化处理。
[0109]
同轴度影响因素在转子设计与工艺规划时具有设计要求,使其在一个理论范围内 波动变化,并且其分布在一定程度上服从高斯分布,因此可采用z-score标准化方法对 装配数据进行标准处理,其方法如下:
[0110][0111]
式中:x'为标准化后的数据;μ为影响因素序列的均值;σ为影响因素序列的标 准差。
[0112]
三:构建弹性相互作用模型
[0113]
通过在abaqus软件中对螺栓拧紧过程进行仿真实验,并根据螺栓残余预紧力 建立弹性相互作用矩阵。本专利中以8螺栓连接,十字交叉拧紧的低压转子为例建立 弹性相互作用矩阵,螺栓预紧力大小为2500n。
[0114]
螺栓组在加载时的弹性相互作用如式12所示:
[0115]
{f0} [a]{δf}={ff}
ꢀꢀꢀꢀꢀꢀꢀꢀꢀꢀꢀꢀꢀꢀꢀꢀ
(12)
[0116]
式中:{f0}为每个加载步前螺栓的初始预紧力(n
×
1);[a]为弹性相互作用矩阵 (n
×
n);{δf}为每个加载步螺栓预紧力增量(n
×
1);{ff}为每个加载步后螺栓的剩余预 紧力(n
×
1);n为螺栓组中的螺栓数目。
[0117]
上式中的每个矢量表示如下所示:
[0118][0119]
式中:f
i0
,δfi和f
if
分别表示在前一次加载结束时的剩余预紧力,螺栓i的预紧力 增量以及在加载结束后的最终剩余预紧力。
[0120]
弹性相互作用矩阵[a]如式14所示:
[0121][0122][0123]
式中:a
ij
表示弹性相互作用矩阵系数,f
ij
表示螺栓j拧紧后,第i个螺栓的剩余预 紧力;δfj表示第j个螺栓拧紧时预紧力的变化量。
[0124]
在有限元软件中仿真十字交叉加载方式的螺栓预紧力变化如表1所示:
[0125]
表1不同加载步下的螺栓剩余预紧力(n)
[0126][0127]
使用式15计算可以得到弹性相互作用矩阵[a],如下所示:
[0128][0129]
四、构建同轴度预测模型
[0130]
(1)弹性相互作用矩阵计算
[0131]
本实施例中以8螺栓连接,螺栓拧紧力矩为1.5n
·
m进行预紧力变化的计算。首 先通过公式16将拧紧力矩转化为预紧力。
[0132]
t=0.2dffꢀꢀꢀꢀꢀꢀꢀꢀꢀꢀꢀꢀꢀꢀꢀꢀꢀꢀꢀ
(16)
[0133]
式中,t为拧紧力矩;ff为预紧力;d为螺栓外径,本专利采用的是m4螺栓, 外径为4mm,则ff=1875n。
[0134]
使用公式12和前边建立的弹性相互作用矩阵对螺栓预紧力变化进行相应的处理 计算,可以得到在拧紧过程中的实际预紧力,计算过程如下:
[0135]
step1:在拧紧第一颗螺栓时,f0=[0,0,0,0,0,0,0,0]
t
,δf=[1875,0,0,0,0,0,0,0]
t
,则 拧紧第一颗螺栓之后,其他螺栓的预紧力可以通过公式12计算得到,如表2第一列。
[0136]
step2:在拧紧第二颗螺栓时,f0为拧紧第一颗螺栓时的预紧力,即为f0=[1875,78.8,97.5,97.5,0,91.9,91.9,0]
t
,δf=[0,1875,0,0,0,0,0,0]
t
,其他螺栓的预紧 力可以通过公式12计算得到,如表2第二列。
[0137]
step3:以此类推可以计算出所有螺栓拧紧之后的螺栓实际预紧力。如表2所示:
[0138]
表2装配过程中螺栓实际预紧力(n)
[0139][0140]
(2)同轴度预测模型训练
[0141]
将低压风扇转子整个装配过程按照螺栓数目划分为n个加载步,每个加载步内都 包括了该段时间内装配因素、螺栓组预紧力值以及同轴度值。网络训练主要包括预测 模型的前向计算部分和反向调优部分。
[0142]
预测模型前向计算部分:这一步骤主要将该时间段内的装配因素、螺栓组预紧力 和同轴度值作为输入,然后按照gru网络前向计算公式进行计算,经gru网络前向 计算后输出下一时刻转子同轴度预测值。
[0143]
gru网络的前向计算公式如下:
[0144]rt
=σ(wr[s
t-1
,x
t
])
ꢀꢀꢀꢀꢀꢀꢀꢀꢀꢀꢀꢀꢀꢀꢀꢀ
(17)
[0145]zt
=σ(wz[s
t-1
,x
t
])
ꢀꢀꢀꢀꢀꢀꢀꢀꢀꢀꢀꢀ
(18)
[0146]st
=tanh(wh[r
t
*s
t-1
,x
t
])
ꢀꢀꢀꢀꢀꢀꢀꢀꢀ
(19)
[0147]st
=(1-z
t
)*s
t-1
z
t
*s
t
ꢀꢀꢀꢀꢀꢀꢀꢀꢀꢀꢀ
(20)
[0148]yt
=σ(wos
t
)
ꢀꢀꢀꢀꢀꢀꢀꢀꢀꢀꢀꢀꢀꢀꢀꢀꢀꢀꢀꢀꢀꢀ
(21)
[0149]
其中,wr表示重置门的权重,wz表示更新门的权重,wh表示t-1时刻隐藏层信息 s
t-1
作为输入时的权重矩阵,wo表示输出层权重,y
t
表示gru网络t时刻的预测值。
[0150]
由前向计算公式可知wr、wz、wh、wo即是gru网络所需训练学习的权重参数, 前三个参数根据其组成可分割为如下:
[0151]
wr=[w
rx
,w
rs
]wz=[w
zx
,w
zs
]wh=[w
hx
,w
hs
]
ꢀꢀꢀꢀꢀꢀ
(22)
[0152]
假如样本数据在t时刻的实际值为y
t
',使用gru网络所得到的t时刻输出值为y
t
, 则该网络在t时刻的传递损失量(将均方根误差mse作为损失函数)为:
[0153][0154]
因此,网络在整个时间段t内的传递损失量为:
[0155][0156]
而后可求得t时刻网络中的中间误差项如下:
[0157]
δ
y,t
=(y'
t-y
t
)
·
σ'
ꢀꢀꢀꢀꢀꢀꢀꢀꢀꢀꢀꢀꢀꢀꢀꢀꢀꢀ
(25)
[0158]
δ
s,t
=δ
y,t
wo δ
z,t 1wzs
δ
t 1whs
·rt 1
δ
s,t 1wrs
δ
·
s,t 1
·
(1-z
t 1
)
ꢀꢀ
(26)
[0159]
δ
z,t
=δ
t,s
·
(s
t-s
t-1
)
·
σ'
ꢀꢀꢀꢀꢀꢀꢀꢀꢀꢀꢀꢀꢀꢀ
(27)
[0160]
δ
t
=δ
s,t
·zt
·
tanh'
ꢀꢀꢀꢀꢀꢀꢀꢀꢀꢀꢀꢀꢀꢀꢀꢀ
(28)
[0161]
δ
r,t
=s
t-1
·
((δ
s,t
·zt
·
tanh')w
hs
)
·
σ'
ꢀꢀꢀꢀꢀꢀꢀꢀꢀꢀ
(29)
[0162]
由于损失量对权值矩阵的导数即为权重矩阵梯度,各时刻的梯度求和结果便是总 时长内的最终梯度。因此时间段t内各权重参数矩阵wo、w
zx
、w
zs
、w
hx
、w
hs
、w
rx
、 w
rs
的梯度计算公式为:
[0163][0164]
最终,使用上述公式并采用合适的学习率η即可实现gru网络模型各参数的迭代 更新。
[0165]
预测模型反向调优部分:这一部分主要基于误差反向传播原理针对gru网络中 各神经元的权重与偏置迭代更新,然后提高预测模型的准确性。本专利将均方误差当 作这一部分的损失函数,然后使用adam算法对梯度下降进行寻优。
[0166]
adam方法是利用当前梯度的矩计算出一个动态变化的系数τ,然后实现学习率的 动态调整。τ的计算公式如下:
[0167][0168]mt
=p
×mt-1
(1-p)
×gt
ꢀꢀꢀꢀꢀꢀꢀꢀꢀꢀꢀꢀꢀꢀꢀꢀꢀꢀꢀꢀꢀꢀꢀꢀꢀꢀ
(32)
[0169]nt
=q
×nt-1
(1-q)
×gt2
ꢀꢀꢀꢀꢀꢀꢀꢀꢀꢀꢀꢀꢀꢀꢀꢀꢀꢀꢀꢀꢀꢀꢀꢀꢀꢀ
(33)
[0170]
其中,g
t
为该参数当前梯度值;m
t
、n
t
分别表示g
t
的一阶矩估计和二阶矩估计;p、 q均为0到1之间的实数;c为非零常数。
[0171]
(3)同轴度预测模型测试
[0172]
随机选取12组实验样本使用4折交叉验证法训练后的同轴度预测模型进行测试, 测试结果如附图2所示。
[0173]
为了更好地评价同轴度预测模型的预测效果,在此计算了12组测试样本的纳什效 率系数(nsec)值,其计算公式如式34所示。一般情况下,同轴度的预测值和真实 值误差越小,nsec值越接近1。
[0174][0175]
12组测试样本的nsec计算结果如下表3所示。
[0176]
表3测试样本预测值与真实值对比结果
[0177]
[0178][0179]
由图2可以看出12组测试样本中同轴度预测模型测试结果可知同轴度预测值与真 实值之间相差不大,预测准确度相对较好。从表3所示的12组测试样本的nsec值可 以看出预测模型总体上可以实现多螺栓拧紧作用下的低压风扇转子同轴度预测。
[0180]
五、构建刚度计算模型
[0181]
螺栓连接刚度主要由螺栓刚度、被连接件刚度和结合面接触刚度三部分串联而成。
[0182][0183]
式中,k为螺栓连接刚度;kb为螺栓刚度;kc为被连接件刚度;kd为结合面接 触刚度。
[0184]
依据德国(vdi)标准,螺栓刚度一般把螺栓看成的均匀的圆柱进行计算。
[0185][0186]
式中,eb为螺栓的材料弹性模量;d为螺栓的直径;t为被连接件的总厚度。
[0187]
假如被连接件在螺栓压紧下的应力沿着径向呈现出均匀分布,那么受压层的形状 则表现为圆锥体,如图3。
[0188]
被连接件的刚度会随着受压层面积变化,而受压层面积主要是由材料的弹性模量 和厚度影响圆锥角θm决定,联合文献“基于有限元法改进螺栓连接刚度模型”所拟合的 公式,建立弹性模量与厚度引起圆锥角θm变化的关系式,如式(37):
[0189]
kc/emd=-0.058ea/eb 1.309
ꢀꢀꢀꢀꢀꢀꢀꢀꢀꢀꢀꢀ
(37)
[0190]
式中,em表示上下级被连接件材料的等效弹性模量。
[0191]em
=eaeb/(ea eb)
ꢀꢀꢀꢀꢀꢀꢀꢀꢀꢀꢀꢀꢀꢀꢀꢀꢀꢀꢀꢀꢀꢀꢀꢀꢀꢀꢀꢀꢀꢀ
(38)
[0192]
kc/emd=-0.031ea/eb 1.047
ꢀꢀꢀꢀꢀꢀꢀꢀꢀꢀꢀꢀꢀꢀꢀꢀꢀꢀꢀꢀ
(39)
[0193][0194]
被连接件的受压层面积如式(41)所示。
[0195][0196]
式中,dw表示螺栓的夹持外径,dh表示螺纹孔内径。
[0197]
根据胡克定律关系,被连接件的刚度为:
[0198][0199]
考虑到结合面刚度主要会受到接触压强的影响,因此需要在得到结合面的接触压 强之后,才能计算结合面刚度值。对于厚度相同的被连接件,外侧直径dm≥dw ltanθ, 如果
被连接件间不存在垫片,那么接触压强的分布情况可认为是半径r的4次多项式, 其中θ为圆柱体假设的半顶角,则
[0200]
pn(r)=c4r4 c3r3 c3r3 c2r2 c1r c0ꢀꢀꢀꢀꢀꢀꢀꢀ
(43)
[0201]
式中,ci(i=0,1,...,4)为待定系数。
[0202]
根据文献“contact of nominally flat surfaces”可得结合面接触刚度为:
[0203][0204]
式中,fm为施加的预紧力;为施加单位载荷后的压强分布情况。
[0205]
令则
[0206][0207]
联合式(35)-(45),螺栓连接的刚度为:
[0208][0209]
六、构建同轴度与刚度双目标优化模型
[0210]
(1)双目标优化函数
[0211]
综合上述同轴度预测模型与刚度计算模型,低压转子装配后同轴度与刚度双目标 优化目标函数如下式所示。
[0212][0213]
式中,λi为第i个目标函数的权重参数;c为低压转子装配后的同轴度;k为低压 转子螺栓连接刚度;l为螺栓预紧力向量;li为第i个螺栓的预紧力。
[0214]
(2)优化变量
[0215]
螺栓的预紧力并非是可以任意选取的,为了保证转子连接的稳固性并能承受一定 的拉伸、扭转与弯曲,根据一般钢制连接螺栓预紧力公式:
[0216]
f≤(0.6~0.8)
×
δs×aꢀꢀꢀꢀꢀꢀꢀꢀꢀꢀꢀꢀꢀꢀꢀ
(48)
[0217]
式中,δs为屈服极限(本专利中δs=320mpa);a为螺纹小径横截面积。
[0218]
代入到本专利中,通过计算得f
max
=0.8
×
3.14
×
1.82×
320=2604n。
[0219]
考虑到本专利实例验证中力矩扳手的最小精度为1.5n
·
m,通过计算最小预紧力 为1500n,那么螺栓预紧力的取值范围在1500n至2604n之间。
[0220]
(3)约束条件
[0221]
为了避免转子在螺栓拧紧后出现应力集中的问题,单个螺栓最大预紧力与最小预 紧力之间不超过20%。那么多级转子双目标优化约束条件如式(49)所示:
范围内,那么将第j组螺栓预紧力视为父本。
[0243]
第4步:假如下一代螺栓预紧力种群中一共有n组,那么再次重复第2步、第3 步n遍。
[0244]
通过比较两种方法,第一种算法包含的步骤较少,算法具备较高的效率,所以本 专利优化模型的选择算子采用锦标赛法,每一次选择10个个体参与锦标赛。
[0245]
·
交叉算子
[0246]
针对螺栓预紧力,采用线性交叉算子产生下一代螺栓预紧力个体child:
[0247]
child=parent2 0.5(parent
1-parent2)
ꢀꢀꢀꢀꢀꢀ
(53)
[0248]
式中,parent1为第一个螺栓预紧力父本;parent2为第二个螺栓预紧力父本。
[0249]
经过父本螺栓预紧力的线性交叉获得下一代螺栓预紧力,令下一代螺栓预紧力个 体具备遗传的多样性。
[0250]
·
变异算子
[0251]
常见的变异算子主要包括高斯变异算子与自适应变异算子两类。高斯变异算子在 应对无约束规划问题应用较为合适,而自适应变异算法具有更好的适用性。由于转子 间的螺栓预紧力存在约束,为避免螺栓预紧力出现局部最优的情况,同时保证螺栓预 紧力分布均匀,本专利选择自适应变异算子,在螺栓预紧力获得充分变异的基础上, 更加契合低压转子螺栓连接的实际情况。
[0252]
·
算法流程
[0253]
采用nsga
‑ⅱ
算法面向同轴度与刚度的螺栓拧紧工艺优化模型的总体过程如图4。
[0254]
·
基于nsga
‑ⅱ
算法双目标优化仿真结果及分析
[0255]
为了验证本专利所提的同轴度与刚度优化模型的可行性和有效性,利用转子三维 模型进行仿真分析。
[0256]
基于转子三维模型,使用同轴度预测模型得到低压转子装配后的同轴度,利用式 (46)计算可得到转子的螺栓连接刚度,采用nsga
‑ⅱ
算法求解计算,获得螺栓组预 紧力非劣解,每组螺栓预紧力装配后的同轴度与刚度如表4所示。
[0257]
表4同轴度和刚度双目标优化螺栓组预紧力非劣解组
[0258][0259]
为了更加方便的表示同轴度与刚度优化模型非劣解螺栓组中的同轴度和刚度,把 表1中的值映射得到图5。图中,左侧纵坐标表示同轴度,右侧纵坐标表示刚度,横 坐标表示
非劣解组。
[0260]
根据图5可以看出,第一,在转子同轴度极值小于75μm,刚度极值大于1.5
×
108n/m 的约束下,使用本专利的优化模型求解可以得到5组非劣解,对应5组螺栓组预紧力。 第二,第2组螺栓预紧力作用下同轴度精度最高为50.9μm,同时刚度恰好也达到最大 1.93
×
108n/m,选用该组螺栓预紧力,能够令同轴度与刚度都处于最好的状态。
[0261]
综上可知,本专利以同轴度和刚度为优化目标,预紧力为优化变量,螺栓预紧力 均布为约束,建立同轴度与刚度双目标优化模型。根据模型特点,采用nsga
‑ⅱ
算法 求解得到螺栓预紧力非劣解组。依据不同的实际需求,选择合理的初始预紧力。最终 通过仿真实验,证明了双目标优化方法的可行性。
[0262]
尽管上面已经示出和描述了本发明的实施例,可以理解的是,上述实施例是示例 性的,不能理解为对本发明的限制,本领域的普通技术人员在不脱离本发明的原理和 宗旨的情况下在本发明的范围内可以对上述实施例进行变化、修改、替换和变型。
再多了解一些
本文用于创业者技术爱好者查询,仅供学习研究,如用于商业用途,请联系技术所有人。