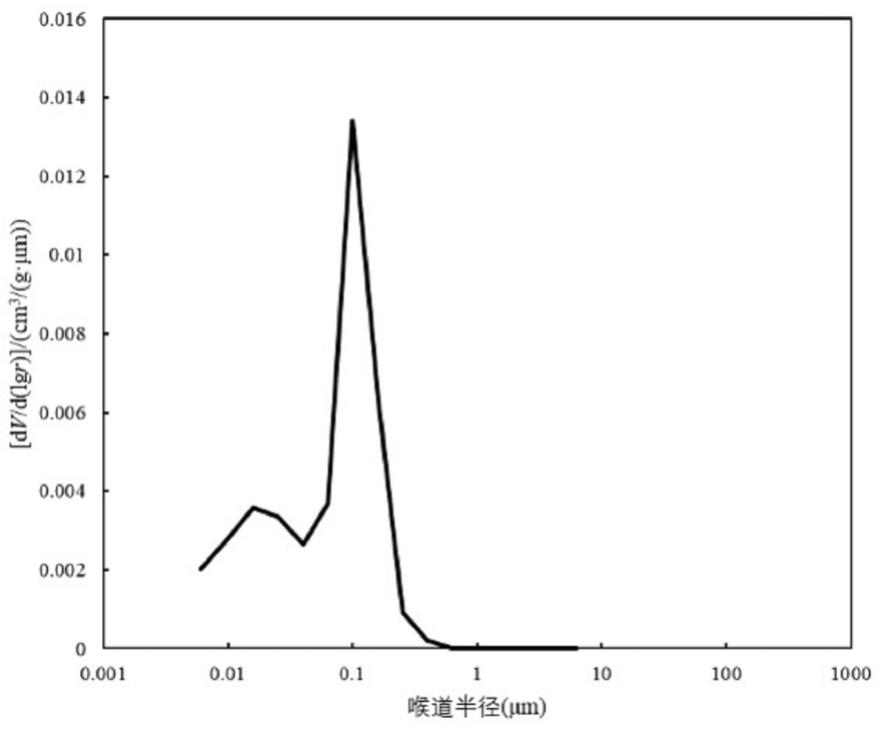
1.本发明涉及油气田开发领域,具体涉及一种微观可视化光刻模型制作方法及其实验流程。
背景技术:
2.微观可视化技术可以直观的观察单相和多相流体在多孔介质中的分布、流动和赋存特征,揭示流体在孔喉空间中的流动机理,这对提高原油采收率,实现资源充分利用有着非常重要的意义。然而,实现这一切的基础在于制作与地下储层孔喉空间相匹配的微观模型。目前,已有的微观可视化模型主要分为:真实岩心模型、填砂微模型和刻蚀模型。
3.真实岩心模型是利用全直径岩样磨成薄片,用玻璃夹住,再用橡胶把模型薄片周围粘结制成。申请号为201910198918.4公布了一种真实砂岩高温高压微观可视化模型,该模型优选一种抗高压耐高温、高透光率的光学玻璃制作了真实砂岩微观可视化模型。但该模型制作周期较长、使用寿命有限,无法重复使用、并且对工艺要求较高,玻璃间密封较差时极有可能出现真“心”假渗流。填砂微观模型是利用石英砂颗粒紧密粘在玻璃片上,嵌入特定的透明橡胶套中。但是该模型孔隙结构与实际岩样差异较大,人为因素较大,且模型是一次性使用,无法重复使用。刻蚀模型是利用孔隙掩膜和吼道掩膜对基片进行刻蚀,形成刻蚀基片,最后刻蚀基片与盖片进行键合,形成微观可视化模型。申请号为202210226097.2的发明专利申请公开了一种三维微观可视化玻璃刻蚀模型及其制备方法,该方法采用干法刻蚀,将孔隙网络结构通过光刻掩膜版成像刻蚀在所述保护胶上,再用显影液使保护胶上的孔隙网络结构图形得以显现;蚀刻所述孔隙网络结构的孔隙图形,然后进一步蚀刻载片玻璃,使得所述孔隙网络结构的孔隙加深至所需深度,形成孔隙网络结构刻蚀模型;将载片玻璃有孔隙网络结构的一面与盖片玻璃键合在一起,形成可视化玻璃刻蚀模型。但是该模型制作工艺复杂,且该模型孔隙网络结构设计主要来自于铸体薄片图像处理,这种方式难以准确抽提喉道及其大小,尤其对于喉道细小的致密砂岩等非常规储层。
4.为了使得实验模型孔隙结构特征与油藏实际孔隙结构特征相近,且能实现制作工艺简单快速以及模型可重复使用的目的。亟需一种微观可视化模型及其制备方法,在以往物理模型的基础上,进一步满足人们对微观实验研究的需求。
技术实现要素:
5.针对上述问题,本发明提供一种微观可视化光刻模型制作方法及其实验流程,其模型孔喉网络结构与实际岩样相近,制作方法简单,且模型可重复使用。
6.本发明采用下述的技术方案:一种微观可视化光刻模型制作方法及其实验流程,包括以下步骤:s1、选取一块长度在7~10cm的圆柱形岩样,并进行洗油和烘干,测量岩样的孔隙度(φ)和渗透率(k)后,将岩样切割成三段;s2、岩样孔隙和喉道大小及其分布:对第ⅰ段岩样进行高压压汞测试,基于高压压
汞实验获取岩样的喉道半径及其分布,并且对第ⅱ段岩样饱和水,测量完全饱和水状态下的核磁共振t2谱曲线,综合高压压汞和核磁共振测试结果获取岩样完整的孔隙和喉道分布;s3、抽提岩样中的孔隙空间:对第ⅲ段岩样进行铸体薄片实验,将铸体薄片图像划分成不同单元,采集各个单元铸体薄片图像,经过降噪、对比度处理后,结合孔隙-骨架间色值(即rgb值)的差异,从图片中抽提出孔隙空间分布,并对每个孔隙进行编号;s4、孔喉空间连通关系划分:根据抽提出的孔喉空间图像,采用分水岭算法连接各个孔隙空间,并对每个喉道进行编号;s5、孔隙和喉道大小赋值:根据获取的完整孔隙和喉道分布曲线,通过拟合分布曲线获取孔隙和喉道半径对应的分布函数,并由计算机产生服从该分布函数的随机数,将产生的随机数根据孔隙和喉道编号赋给相应的孔隙和喉道;s6、模型制作:将步骤s5获取的孔喉网络结构通过光刻掩膜版成像刻蚀在锡纸上,然后将该锡纸粘黏在载玻片上,并借助显微镜观察和清除孔隙和喉道中多余的残胶,确保各个孔隙和喉道间相互连通,最后将载片玻璃有孔喉隙网络结构的一面与盖片玻璃键合在一起,形成可视化玻璃光刻模型;优选地,所述高压压汞实验参照国家标准gb/t 29171-2012《岩石毛管压力曲线的测定》中的压汞法进行;优选地,所述核磁共振实验参照行业标准sy/t 6490-2014《岩样核磁共振参数实验室测量规范》进行;优选地,所述的铸体薄片制作参照行业标准sy/t 5368-2000《岩石薄片鉴定》进行;优选地,步骤2中所述综合高压压汞和核磁共振测试结果获取岩样完整的孔隙和喉道分布包括以下步骤:s21、根据核磁共振t2驰豫时间与孔径间的函数关系(公式1),利用公式(2)~(4)计算获取驰豫率(其中的形状因子为2,高压压汞数据主要将喉道视为长圆柱形),并将核磁共振t2谱曲线转化为孔喉分布曲线;
ꢀꢀꢀꢀꢀꢀꢀꢀꢀꢀꢀꢀꢀꢀꢀꢀꢀꢀꢀꢀꢀꢀꢀꢀꢀꢀ
(1)
ꢀꢀꢀꢀꢀꢀꢀꢀꢀꢀꢀꢀꢀꢀꢀꢀꢀꢀꢀꢀꢀꢀꢀꢀꢀꢀꢀꢀꢀ
(2)
ꢀꢀꢀꢀꢀꢀꢀꢀꢀꢀꢀꢀꢀꢀꢀꢀꢀꢀꢀꢀꢀꢀꢀꢀꢀꢀꢀꢀꢀ
(3)(4)式中,ρ2为表面弛豫率,μm/ms;fs为孔隙形状因子(长圆柱形为2、球形为3);r
nmr
为核磁共振转换后孔喉半径,μm;φ
nmr
为核磁共振获取的孔隙度,%;t
2gm
为驰豫时间的几何平
均值,ms;t
2i
为第i级孔喉对应的驰豫时间;φi为第i级孔喉对应的孔隙度,%;s22、将获取的高压压汞喉道分布曲线和核磁共振孔喉分布曲线按公式(5)处理成标准分布曲线,并将其绘制在同一坐标系下;
ꢀꢀꢀꢀꢀꢀꢀꢀꢀꢀꢀꢀꢀꢀꢀꢀꢀꢀꢀꢀꢀꢀꢀꢀꢀꢀꢀꢀꢀꢀꢀꢀꢀꢀ
(5)式中,r为孔喉半径,μm;对高压压汞和核磁共振,v为单位质量样品的汞的体积和核磁共振t2由小到大时的累计孔隙体积,cm3;s23、在标准化处理的核磁共振孔喉微分分布曲线中减去高压压汞获取的喉道微分分布曲线,获取代表孔隙部分的微分分布曲线,将孔隙部分的微分分布曲线乘以球形孔和管状孔形状因子之比(3/2)则可获取球形孔下孔隙部分的微分分布曲线。
7.本发明的有益效果是:本发明首先通过高压压汞和核磁共振等技术获取了岩样完整的喉道和孔隙大小及其分布特征,并结合孔隙-骨架间色值(即rgb值)的差异采用相关软件从铸体薄片中抽提相应的孔隙空间,在此基础上利用分水岭算法将孤立的孔隙空间连接起来,形成完整的孔喉网络结构。在此基础上,通过拟合孔隙和喉道半径分布曲线获取对应的分布函数,借助计算机产生服从该分布的随机数,并根据孔隙和喉道编号随机赋值。最后,将获取的孔喉网络结构通过光刻掩膜版成像刻蚀在锡纸上,并经过后处理后将载片玻璃有孔喉隙网络结构的一面与盖片玻璃键合在一起,形成最终的可视化玻璃光刻模型。
8.本发明制作工艺简单,且获取的孔喉网络结构与实际岩样相匹配,使得模拟结果更能反映地下实际渗流情况。该模型透光性好,成本低,制作周期短,模型可重复使用,便于设计不同的对比实验。此外该模型可以能够承受油藏条件下的微观驱替实验,满足目前大多数微观渗流实验的要求。
附图说明
9.为了更清楚地说明本发明实施例的技术方案,下面将对实施例的附图作简单地介绍,显而易见地,下面描述中的附图仅仅涉及本发明的一些实施例,而非对本发明的限制。
10.图1为本发明高压压汞喉道分布示意图;图2为本发明核磁共振孔喉分布示意图;图3为本发明基于高压压汞和核磁共振获取的孔隙和喉道大小及其分布示意图;图4为本发明铸体薄片示意图;图5为本发明铸体薄片提取的孔隙空间示意图;图6为本发明基于分水岭算法的孔喉连通关系示意图;图7为本发明制作的光刻模型水驱油实验结果示意图。
具体实施方式
11.为使本发明实施例的目的、技术方案和优点更加清楚,下面将结合本发明实施例的附图,对本发明实施例的技术方案进行清楚、完整地描述。显然,所描述的实施例是本发明的一部分实施例,而不是全部的实施例。基于所描述的本发明的实施例,本领域普通技术
人员在无需创造性劳动的前提下所获得的所有其他实施例,都属于本发明保护的范围。
12.除非另外定义,本公开使用的技术术语或者科学术语应当为本公开所属领域内具有一般技能的人士所理解的通常意义。本公开中使用的“包括”或者“包含”等类似的词语意指出现该词前面的元件或者物件涵盖出现在该词后面列举的元件或者物件及其等同,而不排除其他元件或者物件。“上”、“下”、“左”、“右”等仅用于表示相对位置关系,当被描述对象的绝对位置改变后,则该相对位置关系也可能相应地改变。
13.下面结合附图和实施例对本发明进一步说明。
14.如图1至图7所示,一种微观可视化光刻模型制作方法及其实验流程,包括以下步骤:s1、选取一块长度在7~10cm的圆柱形岩样,并进行洗油和烘干,测量岩样的孔隙度(φ)和渗透率(k)后,将岩样切割成三段;s2、岩样孔隙和喉道大小及其分布:参照国家标准gb/t 29171-2012《岩石毛管压力曲线的测定》中的压汞法中的规定对第ⅰ段岩样(长度为2-3cm)进行高压压汞测试,基于高压压汞实验获取岩样的喉道半径及其分布(图1),并且对第ⅱ段岩样饱和水,按行业标准sy/t 6490-2014《岩样核磁共振参数实验室测量规范》中的要求测量完全饱和水状态下的核磁共振t2谱曲线(图2),综合高压压汞和核磁共振测试结果获取岩样完整的孔隙和喉道分布(图3);s21、根据核磁共振t2驰豫时间与孔径间的函数关系(公式1),利用公式(2)~(4)计算获取驰豫率(其中的形状因子为2,高压压汞数据主要将喉道视为长圆柱形),并将核磁共振t2谱曲线转化为孔喉分布曲线(图2);
ꢀꢀꢀꢀꢀꢀꢀꢀꢀꢀꢀꢀꢀꢀꢀꢀꢀꢀꢀꢀꢀꢀꢀꢀꢀꢀꢀꢀ
(1)
ꢀꢀꢀꢀꢀꢀꢀꢀꢀꢀꢀꢀꢀꢀꢀꢀꢀꢀꢀꢀꢀꢀꢀꢀꢀꢀꢀꢀꢀ
(2)
ꢀꢀꢀꢀꢀꢀꢀꢀꢀꢀꢀꢀꢀꢀꢀꢀꢀꢀꢀꢀꢀꢀꢀꢀꢀꢀꢀꢀꢀ
(3) (4)式中,ρ2为表面弛豫率,μm/ms;fs为孔隙形状因子(长圆柱形为2、球形为3);r
nmr
为核磁共振转换后孔喉半径,μm;φ
nmr
为核磁共振获取的孔隙度,%;t
2gm
为驰豫时间的几何平均值,ms;t
2i
为第i级孔喉对应的驰豫时间;φi为第i级孔喉对应的孔隙度,%;s22、将获取的高压压汞喉道分布曲线和核磁共振孔喉分布曲线按公式(5)处理成标准分布曲线,并将其绘制在同一坐标系下;
ꢀꢀꢀꢀꢀꢀꢀꢀꢀꢀꢀꢀꢀꢀꢀꢀꢀꢀꢀꢀꢀꢀꢀꢀꢀꢀꢀꢀꢀꢀꢀꢀꢀꢀꢀꢀꢀ
(5)式中,r为孔喉半径,μm;对高压压汞和核磁共振,v为单位质量样品的汞的体积和
核磁共振t2由小到大时的累计孔隙体积,cm3;s23、在标准化处理的核磁共振孔喉微分分布曲线中减去高压压汞获取的喉道微分分布曲线,获取代表孔隙部分的微分分布曲线,将孔隙部分的微分分布曲线乘以球形孔和管状孔形状因子之比(3/2)则可获取球形孔下孔隙部分的微分分布曲线。
15.s3、抽提岩样中的孔隙空间:对第ⅲ段岩样进行铸体薄片实验,按行业标准sy/t 5368-2000《岩石薄片鉴定》制作岩样的铸体薄片(图4),将铸体薄片图像划分成不同单元,采集各个单元铸体薄片图像,经过降噪、对比度处理后,结合孔隙-骨架间色值(即rgb值)的差异,从图片中抽提出岩样的孔隙空间分布(图5),并对每个孔隙进行编号;s4、孔喉空间连通关系划分:根据抽提出的孔喉空间图像,采用分水岭算法连接各个孔隙空间,并对每个喉道进行编号(图6);s5、孔隙和喉道大小赋值:根据获取的完整孔隙和喉道分布曲线,通过拟合分布曲线获取孔隙和喉道半径对应的分布函数,并由计算机产生服从该分布函数的随机数,将产生的随机数根据孔隙和喉道编号赋给相应的孔隙和喉道;s6、模型制作:将步骤s5获取的孔喉网络结构通过光刻掩膜版成像刻蚀在锡纸上,然后将该锡纸粘黏在载玻片上,并借助显微镜观察和清除孔隙和喉道中多余的残胶,确保各个孔隙和喉道间相互连通,最后将载片玻璃有孔喉隙网络结构的一面与盖片玻璃键合在一起,形成可视化玻璃光刻模型;使用本发明微观可视化光刻模型可以用于定量研究油水两相在孔喉空间中的运移规律、剩余油赋存规律和三次采油技术优选等一系列涉及储层微观渗流机理方面的实验。本实施例以高温高压岩石微观可视化水驱油实验为例(图7)。实验装置包括渗流模拟系统,与渗流模拟系统相连的微量驱替与计量系统,图像采集与分析系统。实验原理是利用所述微观可视化光刻模型进行水驱油实验,通过显微镜和数据采集器,将驱油过程以图像的形式记录、整理和分析,研究不同阶段下的驱油特征。
16.微观可视化光刻模型水驱油实验步骤依次包括:岩样抽真空-饱和实验水-油驱水建立束缚水饱和度-水驱油实验-结束实验,即将微观可视化光刻模型放入可视化高温高压釜内,首先对微观可视化光刻模型抽真空饱和实验水,然后再以一定的流量进行油驱水以建立束缚水状态,最后进行水驱油实验,利用体式显微镜观察水驱油过程中油水的赋存特征和残余油分布特征,同时采集某一固定区域饱和水状态、束缚水状态和残余油状态下的微观图像,并通过图像统计获取岩样的微观驱替效率。
17.具体步骤如下:s1、微观可视化光刻模型抽真空:将微观可视化光刻模型岩样模型固定在可视化高温高压釜中,利用真空泵对微观模型抽真空;s2、微观可视化光刻模型饱和实验水:向微观可视化光刻模型中注入模拟水,利用体式显微镜观察微观可视化光刻模型中注入水的充填情况,并统计微观可视化光刻模型中的饱和度;s3、油驱水建立束缚水饱和度:向微观可视化光刻模型缓慢加压进行油驱排水至束缚水状态,利用体式显微镜和高速摄像机实时拍摄油驱水过程中油水渗流规律和束缚水状态下油水赋存状态,并统计微观可视化光刻模型中获取岩样的束缚水饱和度;s4、水驱油实验:对微观可视化光刻模型进行水驱油实验,同时观察水驱油过程中
油水渗流规律,实时拍摄水驱油过程油水分布图像,并统计获取对应状态下油水饱和度,计算微观驱油效率直至残余油状态;s5、结束实验。
18.以上所述,仅是本发明的较佳实施例而已,并非对本发明作任何形式上的限制,虽然本发明已以较佳实施例揭露如上,然而并非用以限定本发明,任何熟悉本专业的技术人员,在不脱离本发明技术方案范围内,当可利用上述揭示的技术内容作出些许更动或修饰为等同变化的等效实施例,但凡是未脱离本发明技术方案的内容,依据本发明的技术实质对以上实施例所做的任何简单修改、等同变化与修饰,均仍属于本发明技术方案的范围内。
再多了解一些
本文用于创业者技术爱好者查询,仅供学习研究,如用于商业用途,请联系技术所有人。