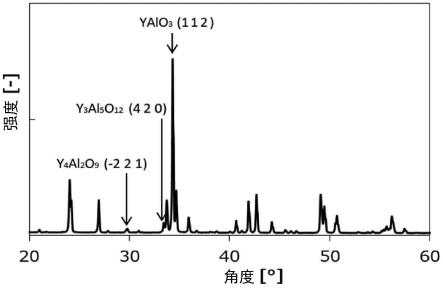
1.本发明涉及成膜用或烧结用粉末。
背景技术:
2.在半导体器件的制造中的蚀刻工序中使用卤素系气体。为了防止由卤素系气体引起的蚀刻装置的腐蚀,蚀刻装置的内部一般通过喷镀膜而涂敷有耐蚀性高的物质。作为这样的高耐蚀性物质之一,已知有包含钇
·
铝
·
石榴石(yag)等钇与铝的复合氧化物的材料。
3.例如在专利文献1中,记载了一种喷镀用粉末,其在测定喷镀用粉末的x射线衍射时,来源于氧化钇的(222)面的x射线衍射峰的强度相对于来源于复合氧化物中的石榴石相的(420)面的x射线衍射峰、来源于复合氧化物中的钙钛矿相的(420)面的x射线衍射峰和来源于复合氧化物中的单斜晶相的(-122)面的x射线衍射峰中的最大峰的强度的比率为20%以下。
4.在专利文献2中,记载了一种喷镀用粉末,其特征在于,其是含有将包含钇及铝的原料粉末进行造粒及烧结而得到的钇-铝复合氧化物造粒-烧结粒子的喷镀用粉末,上述造粒-烧结粒子中的直径为6μm以下的细孔的总容积为0.06~0.25cm3/g。
5.此外,本技术人之前提出了一种成膜用或烧结用粉末,其在x射线衍射测定中观察到立方晶y3al5o
12
的峰和正交晶yalo3的峰,正交晶yalo3的(112)峰相对于立方晶y3al5o
12
的(420)峰的强度比为0.01以上且低于1。根据该粉末,能够容易地形成相对于等离子体蚀刻的耐蚀性高的皮膜或烧结体。
6.现有技术文献
7.专利文献
8.专利文献1:us2006/116274a1
9.专利文献2:us2006/182969a1
10.专利文献3:日本专利第6659073号公报
技术实现要素:
11.然而,喷镀专利文献1及2中记载的粉末而得到的皮膜相对于卤素系等离子体并不具有充分的耐蚀性。
12.在专利文献3中记载的粉末中,以抑制卤素系等离子体耐性低的三方晶al2o3的生成作为主要目的,与钇
·
铝
·
石榴石y3al5o
12
相比较高地控制了y/al比。起因于此,在该文献中记载的粉末中有时观察到氧化钇的峰。然而,在实际的制造工艺上,难以任意地控制氧化钇的含量。其结果是,在包含铝及钇的复合氧化物粉末中有时氧化钇的含量产生不均。例如在氧化钇的含量高的情况下,存在在使用卤素系等离子体的蚀刻条件下蚀刻速率增加等问题。
13.因此,本发明的课题在于提供与上述的现有技术相比相对于等离子体蚀刻的耐蚀性进一步提高的成膜用或烧结用粉末。
14.本发明人对于钇与铝的复合氧化物粉末,对容易制造稳定的制品的组成、及有效地提高相对于使用了卤素系气体的等离子体蚀刻的耐蚀性的组成进行了深入研究。其结果发现:通过采用特定的组成,可有效地提高耐蚀性。
15.本发明是基于上述见识而进行的,提供一种成膜用或烧结用粉末,其在x射线衍射测定中观察到正交晶(也可以称为斜方晶,orthorhombic crystal)yalo3的峰,在x射线衍射测定中观察到的峰中,正交晶yalo3的(112)峰为最大峰。
16.此外,本发明提供将上述成膜用或烧结用粉末通过喷镀法或pvd法进行成膜的皮膜的制造方法、及将成膜用或烧结用粉末通过喷镀法或pvd法进行成膜而成的皮膜。
17.进而,本发明提供一种粉末用于成膜或烧结的用途,所述粉末在x射线衍射测定中观察到正交晶yalo3的峰,在x射线衍射测定中所观察到的峰中,正交晶yalo3的(112)峰为最大峰。
附图说明
18.图1是实施例1中得到的粉末的xrd衍射线图。
19.图2是实施例1中得到的粉末的细孔径分布图。
具体实施方式
20.以下基于其优选的实施方式对本发明进行说明。本发明的成膜用或烧结用粉末(以下也称为“本发明的粉末”)含有包含钇和铝的复合氧化物。
21.(成膜用或烧结用粉末的组成)
22.如果将本发明的粉末供于x射线衍射测定,则观察到来源于正交晶yalo3的衍射峰。观察到所述衍射峰的本发明的粉末在使用了卤素系气体的等离子体蚀刻中显示出高耐蚀性。已知在yalo3中存在立方晶及正交晶这2种相。本发明人发现:使用包含这2种相中作为正交晶的yalo3的粉末而形成的膜及烧结体相对于使用了卤素系气体的等离子体蚀刻极为稳定。
23.从相对于使用了卤素系气体的等离子体蚀刻的耐蚀性变高的方面出发,本发明的粉末优选仅由正交晶yalo3构成。尤其是在不损害耐蚀性的范围内,本发明的粉末不妨含有正交晶yalo3以外的氧化物。在本发明的粉末中包含正交晶yalo3以外的氧化物的情况下,作为该氧化物,例如可列举出立方晶y3al5o
12
、单斜晶y4al2o9、三方晶al2o3及立方晶y2o3等。在本发明的粉末中是否包含立方晶y3al5o
12
、单斜晶y4al2o9、三方晶al2o3及立方晶y2o3可以通过将本发明的粉末供于x射线衍射测定来确认。
24.从提高对于使用了卤素系气体的等离子体蚀刻的耐蚀性的方面考虑,本发明的粉末优选在x射线衍射测定中未观察到氧化铝相的峰、或即使观察到也极小。从该观点出发,在将本发明的粉末供于使用了cukα射线的x射线衍射测定时,除了观察到正交晶yalo3的峰以外还观察到三方晶al2o3的峰的情况下,将正交晶yalo3的(112)峰强度设定为s1,将三方晶al2o3的(104)峰强度设定为s2时,s2相对于s1之比即s2/s1的值优选为低于1。其理由是由于:在由s2/s1的值低于1的粉末得到的皮膜或烧结体中,正交晶yalo3容易作为稳定相而出现,对于使用了卤素系气体的等离子体蚀刻的耐蚀性变高。此外由于:认为如果yalo3为正交晶,则容易得到对于卤素系等离子体而言组成稳定的皮膜或烧结体。从使这些优点变得
进一步显著的观点出发,s2/s1的值优选为0.1以下,更优选为0.01以下,最优选未观察到三方晶al2o3的(104)峰。
25.在将本发明的粉末供于使用了cukα射线的x射线衍射测定时,除了观察到正交晶yalo3的峰以外还观察到立方晶y3al5o
12
的峰或单斜晶y4al2o9的峰的情况下,在将正交晶yalo3的(112)峰强度设定为s1,将立方晶y3al5o
12
的(420)峰强度设定为s3,将单斜晶y4al2o9的(-221)峰强度设定为s4时,s3相对于s1之比即s3/s1的值及s4相对于s1之比即s4/s1的值分别独立地优选为低于1。其理由是由于:在本发明的粉末中,(a)正交晶yalo3容易作为稳定相而出现;(b)正交晶yalo3在钇与铝的复合氧化物中为最高密度,包含其的皮膜或烧结体变成高硬度;即物理蚀刻耐性高;以及(c)与同样地具有高硬度的立方晶y3al5o
12
的单一组成相比,正交晶yalo3为含有更多因卤素系等离子体耐性高而已知的钇成分的组成。
26.从进一步提高对于使用了卤素系气体的等离子体蚀刻的耐蚀性的观点出发,s3/s1及s4/s1的值分别独立地优选为低于0.5,更优选为0.2以下,特别优选为0.1以下,最优选未观察到立方晶y3al5o
12
的(420)峰及单斜晶y4al2o9的(-221)峰。
27.从充分表现出对于卤素系等离子体的耐蚀性的方面出发,本发明的粉末优选不含y2o3、或在包含的情况下为微量。从该观点出发,在将本发明的粉末供于使用了cukα射线的x射线衍射测定时,在将正交晶yalo3的(112)峰强度设定为s1,将立方晶y2o3的(222)峰强度设定为s5时,s5相对于s1之比即s5/s1的值优选为1以下。
28.从更进一步提高对于使用了卤素系气体的等离子体蚀刻的耐蚀性的观点出发,s5/s1的值优选为0.1以下,更优选为0.01以下,最优选未观察到立方晶y2o3的(222)峰。
29.在使用了cukα射线的x射线衍射测定中正交晶yalo3的(112)峰在2θ=34
°
附近被观察到。具体而言在2θ=34.2
°±
0.4
°
的范围内被观察到。
30.此外,在使用了cukα射线的x射线衍射测定中三方晶al2o3的(104)峰通常在2θ=35
°
处被观察到。具体而言在35.2
°±
0.4
°
处被观察到。
31.此外,在使用了cukα射线的x射线衍射测定中立方晶y3al5o
12
的(420)峰通常在2θ=33
°
附近被观察到。具体而言在33.3
°±
0.4
°
的范围内被观察到。
32.进而,在使用了cukα射线的x射线衍射测定中单斜晶y4al2o9的(-221)峰通常在2θ=30
°
附近处被观察到。具体而言在29.6
°±
0.15
°
的范围内被观察到。
33.进而,在使用了cukα射线的x射线衍射测定中立方晶y2o3的(222)峰通常在2θ=29
°
附近处被观察到。具体而言在29.2
°±
0.15
°
的范围内被观察到。
34.本发明的粉末优选的是:在使用了cukα射线的2θ=20
°
~60
°
的扫描范围的x射线衍射测定中观察到的峰中来源于正交晶yalo3的峰为显示出最大峰强度的峰。本发明的粉末特别优选的是:在x射线衍射测定中观察到的峰中正交晶yalo3的(112)峰为显示出最大峰强度的峰。
35.从进一步提高耐蚀性的方面出发,本发明的粉末优选的是:在x射线衍射测定中实质上未观察到来源于yalo3、y3al5o
12
、y4al2o9、al2o3及y2o3以外的成分的峰。在2θ=20
°
~60
°
的扫描范围内,将来源于yalo3、y3al5o
12
、y4al2o9、al2o3及y2o3以外的成分x的峰的强度设定为sx时,sx相对于正交晶yalo3的(112)峰强度s1之比即sx/s1的值优选为0.1以下,更优选为0.01以下。sx/s1的值最优选为0。
36.(微晶尺寸)
37.从所得到的皮膜或烧结体中的正交晶yalo3的结晶性变高、皮膜或烧结体的耐蚀性进一步提高的方面出发,本发明的粉末优选由正交晶yalo3的(112)峰的半值幅求出的微晶尺寸为50nm以上。从该观点出发,上述的微晶尺寸优选为60nm以上,更优选为70nm以上,特别优选为80nm以上。此外,从本发明的粉末的制造容易性或防止由晶粒生长引起的细孔容积的降低的方面出发,上述的微晶尺寸优选为110nm以下,更优选为105nm以下。微晶尺寸通过scherrer式而求出,具体而言可以通过后述的实施例中记载的方法来求出。
38.为了使本发明的粉末具有上述的组成及微晶尺寸,只要在后述的本发明的粉末的优选的制造方法中,调整作为原料的钇源的粉末和铝源的粉末的粒径、或调整原料粉末的烧成温度即可。
39.(细孔容积)
40.从进一步提高使用本发明的粉末而得到的皮膜或烧结体的耐蚀性的观点出发,在使用汞压入法测定的细孔容积相对于细孔径的分布(横轴:细孔径、纵轴:log微分细孔容积)中,优选在细孔径为0.1μm~1μm的范围内观察到至少一个峰。从更进一步有效地提高耐蚀性的观点出发,细孔径为0.1μm~1μm的范围的峰详细而言更优选在细孔径为0.2μm~0.9μm的范围内观察到至少一个,特别优选在细孔径为0.2μm~0.8μm的范围内观察到至少一个。以下,有时将细孔容积的分布中的细孔径为0.1μm~1μm的范围的峰记载为细孔第1峰。
41.从进一步提高耐蚀性的观点出发,本发明的粉末优选的是:在使用汞压入法测定的细孔容积相对于细孔径的分布(横轴:细孔径、纵轴:log微分细孔容积)中,除了在细孔径为0.1μm~1μm的范围内具有至少一个峰以外,在细孔径为5μm~50μm的范围内也具有至少一个峰。从本发明的粉末的制造容易性、和进一步提高皮膜及烧结体的耐蚀性的方面出发,细孔径为5μm~50μm的范围的峰详细而言更优选在细孔径为7μm~35μm的范围内观察到至少一个,特别优选在细孔径为8μm~25μm的范围内观察到至少一个。以下,有时将细孔容积的分布中的细孔径为5μm~50μm的范围的峰记载为细孔第2峰。
42.本发明人发现:如果将本发明的粉末的细孔容积设定为特定的范围,则能够控制所得到的皮膜的表面粗糙度、烧结体的致密性。特别发现:在将本发明的粉末制成颗粒的情况下,将该细孔容积设定为特定的范围是有利的。皮膜的表面粗糙度或烧结体的致密性与对于卤素系等离子体的耐蚀性存在相关。因此,可以通过本发明的粉末的细孔容积来控制皮膜及烧结体的耐蚀性。具体而言,本发明的粉末优选的是:使用汞压入法测定的细孔径为0.1μm~1μm的细孔容积为0.1ml/g以上。细孔径为0.1μm~1μm的细孔容积来源于本发明的粉末中的一次粒子间的空隙。如果该范围的细孔径的细孔容积为0.1ml/g以上,则所得到的皮膜的表面粗糙度降低,此外所得到的烧结体成为致密的烧结体。其理由并不明确,但本发明人推测理由之一是:具有上述的范围的细孔容积的本发明的粉末通过构成颗粒的一次粒子微细、且具有一定以上的细孔容积,从而高效地传播热,从而容易熔融。与此相对,专利文献2中记载的喷镀用粉末如果基于该文献的图1来求出细孔径为0.1μm~1μm的细孔容积,则成为0.05ml/g,变成本发明的细孔容积的范围外即低于0.1ml/g。
43.在本发明的粉末中,细孔径为0.1μm~1μm的细孔容积v1优选为0.05ml/g以上,更优选为0.10ml/g以上,特别优选为0.12ml/g以上。此外,从防止一次粒子间的空隙变得过宽而防止颗粒强度的降低的观点出发,细孔容积v1优选为0.5ml/g以下、特别是0.4ml/g以下、尤其是0.2ml/g以下。
44.在本发明的粉末中,从提高耐蚀性的方面考虑,细孔径为5μm~50μm的细孔容积v2也优选为0.1ml/g以上。细孔径为5μm~50μm的细孔容积来源于本发明的粉末中的二次粒子间的空隙。本发明的粉末中的细孔容积v2更优选为0.15ml/g以上,特别优选为0.20ml/g以上。从确保流动性的方面出发,本发明的粉末的细孔容积v2优选为0.5ml/g以下,更优选为0.4ml/g以下。
45.从进一步提高使用本发明的粉末而得到的皮膜或烧结体的耐蚀性的观点出发,就本发明的粉末而言,使用汞压入法测定的细孔容积v1相对于细孔容积v2之比即v1/v2的值优选为0.3以上,更优选为0.35以上,特别优选为0.4以上。从保证恰当的颗粒密度的方面考虑,v1/v2的值优选为1.0以下、特别优选为0.85以下。
46.为了使本发明的粉末具有上述的细孔容积,只要在后述的本发明的粉末的优选的制造方法中,调整作为原料的钇源的粉末和铝源的粉末的粒径、或调整烧成温度即可。
47.(颗粒粒径)
48.从进一步提高由具有上述的特定的细孔容积或具有上述的特定的组成所带来的耐蚀性的提高效果的方面考虑,本发明的粉末优选为颗粒。从容易得到满足上述的细孔容积分布的本发明的粉末的方面或制成喷镀材料时的流动性变得良好的方面出发,颗粒的平均粒径优选为15μm~100μm,更优选为20μm~80μm,特别优选为20μm~60μm,最优选为20μm~50μm。上述的平均粒径是利用激光衍射
·
散射式粒度分布测定法得到的从小粒径侧起的累积体积成为50%的粒径(d
50
),可以通过后述的实施例中记载的方法来进行测定。
49.(bet比表面积)
50.从在成膜及烧结时起因于粒子适当而容易熔融、容易得到致密的皮膜或烧结体的方面、及起因于体积密度适当而处理时的处理性变得良好的方面考虑,本发明的粉末优选bet比表面积为1.0m2/g~5.0m2/g。从这些观点出发,本发明的粉末的bet比表面积更优选为1.0m2/g~4.4m2/g,进一步优选为1.2m2/g~3.8m2/g,进一步优选为1.4m2/g~3.2m2/g。bet比表面积通过bet1点法而测定,具体而言可以通过后述的实施例中记载的方法来进行测定。
51.〔制造方法〕
52.接着,对本发明的粉末的优选的制造方法进行说明。本制造方法优选具有以下的第1工序~第3工序。以下,对各工序进行详述。
53.·
第1工序:将铝源的粒子与钇源的粒子混合而进行粉碎,得到d
50
为0.05μm~2.0μm的前驱体混合粒子的浆料。
54.·
第2工序:将第1工序中得到的浆料用喷雾干燥器进行造粒而得到造粒物。
55.·
第3工序:将第2工序中得到的造粒物在800℃~1700℃的温度下进行烧成而得到钇与铝的复合氧化物的颗粒。
56.通过具有这些工序的制造方法,能够使正交晶yalo3作为稳定相而生成。其理由是由于:(a)通过将第1工序的氧化铝源的粒子与氧化钇源的粒子混合并进行粉碎而控制混合粒子的d
50
,从而粒子被充分地微细化,成为反应性高的状态,并且维持粒子的分散性,彼此的粒子之间处于充分相邻的状态;以及(b)在第3工序中在与上述的d
50
相关的恰当的温度下进行烧成。
57.〔第1工序〕
58.在本工序中,将铝源的粒子与钇源的粒子混合并进行粉碎,得到规定粒径的浆料。从顺利地得到具有上述的组成及细孔容积或比表面积的粉末的观点出发,前驱体混合粒子的粒径使用激光衍射
·
散射式粒径
·
粒度分布测定器而测定的d
50
优选为0.05μm~2.0μm,更优选为0.1μm~1.0μm。前驱体混合粒子的d
50
可以通过与颗粒的d
50
同样的方法来测定。作为铝源,优选使用选自氧化铝(alumina)、羟基氧化铝(aluminum oxyhydroxide)及氢氧化铝中的1种或2种以上。
59.作为第1工序的步骤,将铝源的粒子和钇源的粒子与液体介质混合,充分地进行搅拌、粉碎,得到前驱体混合粒子的浆料。对液体介质的种类没有特别限制,例如可以使用水或各种有机溶剂。作为铝源,从反应性的方面出发,使用优选微粒子的铝源。尤其是如果成为高比表面积则浆料的粘度上升,因此也可以伴随着铝源的粒子与液体介质的混合,将各种分散剂或粘合剂添加到浆料中。作为分散剂,例如可以使用聚丙烯酸系聚合物、羧酸系共聚物、醋酸、氨等。在铝源的粒子的浆料中添加分散剂的情况下,从所得到的粉末的品质、抑制粘度的上升的方面等出发,相对于氧化铝换算的铝源100质量份优选为0.001质量份~1质量份,更优选为0.01质量份~0.1质量份。
60.本工序中,关于铝源与钇源的混合比率,相对于铝源的铝1摩尔,钇源的钇优选为超过0.8摩尔且1.3摩尔以下,更优选为0.95摩尔~1.05摩尔。
61.对于粉碎,干式粉碎及湿式粉碎中的任一者都可以适用。粉碎可以以1个阶段来实施,或者也可以以2个阶段以上来实施。从成本和工夫的方面出发优选以1个阶段来进行粉碎。优选在粉碎后添加水等液体介质而浆料化。在进行干式粉碎的情况下,例如可以使用磨碎机、喷射磨、球磨机、锤磨机及针磨机等各种干式粉碎机。另一方面,在进行湿式粉碎的情况下,例如可以使用球磨机或珠磨机等各种湿式粉碎机。
62.本工序中的浆料的浓度优选将钇源换算成氧化钇、将铝源换算成氧化铝时的钇源与铝源的合计的浓度设定为50g/l~1500g/l、特别是100g/l~1000g/l。通过将浆料的浓度设定为该范围内,能够抑制能量的过度消耗,此外能够使浆料的粘度变得适宜而使喷雾稳定。
63.〔第2工序〕
64.在本工序中,将第1工序中得到的浆料用喷雾干燥器进行造粒而得到包含钇及铝的造粒物。将喷雾干燥器运转时的雾化器的转速优选设定为5000min-1
~30000min-1
。通过将转速设定为5000min-1
以上,能够充分地进行浆料中的钇源的粒子与氧化铝源的粒子的分散,由此能够得到均匀的造粒物。另一方面,通过将转速设定为30000min-1
以下,变得容易得到具有上述的细孔第2峰的颗粒。从这些观点出发,雾化器的转速进一步优选设定为6000min-1
~25000min-1
。
65.将喷雾干燥器运转时的入口温度优选设定为150℃~300℃。通过将入口温度设定为150℃以上,能够充分地进行固体成分的干燥,变得容易得到残存的水分少的颗粒。另一方面,通过将入口温度设定为300℃以下,能够抑制无用的能量消耗。
66.〔第3工序〕
67.本工序中,将第2工序中得到的造粒物进行烧成而得到钇与铝的复合氧化物的颗粒。该烧成的程度成为控制作为目标的粉末的组成、细孔径为0.1μm~1μm的细孔容积峰及比表面积的因子。详细而言,烧成温度优选为800℃~1600℃。通过将烧成温度设定为800℃
以上,变得容易得到目标组成比率。另一方面,通过将烧成温度设定为1600℃以下,变得容易得到具有作为目标的细孔径分布的第1峰和比表面积的颗粒。从这些观点出发,烧成温度更优选设定为900℃~1550℃,进一步优选设定为1000℃~1550℃。
68.烧成时间以烧成温度为上述的范围内作为条件,优选设定为1小时~48小时。更优选设定为3小时~24小时。烧成的气氛没有特别限制,但根据铝源的种类,需要通过烧成而使其氧化,因此变得需要氧(o2),因此优选在大气中等含氧气氛中进行。
69.如上述那样操作而得到的本发明的粉末被用于喷镀法、物理气相沉积(pvd)法、化学气相沉积(cvd)法、气溶胶沉积(ad)法、冷喷雾法等各种成膜法,例如适宜用于作为喷镀法之一的等离子体喷镀法、pvd法。等离子体喷镀可以是大气压等离子体喷镀,也可以是减压等离子体喷镀。此外,作为pvd法,可列举出离子镀法、溅射法等。作为成为成膜对象的基材,例如使用铝等各种金属、铝合金等各种合金、氧化铝等各种陶瓷、石英等。
70.本发明的粉末也可以适宜作为陶瓷部件的材料来使用。详细而言,如果将本发明的成膜用或烧结用粉末作为例如通过普通的烧结法、压制法、hp法、cip法、hip法、sps法等而制造的陶瓷部件的原料来使用,则能够获得平滑性、耐蚀刻性等优异的陶瓷部件。那样的陶瓷部件例如适宜用于电子材料或其烧成时的夹具、半导体制造装置用构件、使用了等离子体的蚀刻及成膜装置等。需要说明的是,将本发明的成膜用或烧结用粉末进行烧结而制成的烧结体也可以适宜作为离子镀法、真空蒸镀法等pvd法的靶(成膜用材料)来使用。
71.通过使用本发明的粉末,与使用以往已知的钇与铝的复合氧化物的喷镀材料的情况相比,能够得到对于卤素系等离子体的耐蚀性高的喷镀膜。此外,根据本发明的粉末,除了在pvd法等喷镀以外的方法中也同样地能够得到耐蚀性高的膜以外,在制成烧结体的情况下也同样地能够得到耐蚀性高的烧结体。像这样使用本发明的粉末而得到的皮膜或烧结体的耐蚀性高,该皮膜或烧结体对于使用卤素系等离子体的半导体制造装置的构成构件和其涂敷等是有用的。
72.使用本发明的粉末而得到的皮膜及烧结体在使用了卤素系气体的等离子体蚀刻中蚀刻速率低。具体而言,该皮膜及烧结体通过后述的实施例中记载的方法而测定的蚀刻速率优选为3nm/分钟以下,更优选为2nm/分钟以下。
73.在以本发明的粉末作为原料来制造皮膜的情况下,为了提高对于使用了卤素系气体的等离子体蚀刻的耐蚀性,该皮膜优选为表面粗糙度低的皮膜。皮膜的表面粗糙度可以通过后述的实施例中记载的方法来测定。
74.实施例
75.以下,通过实施例对本发明更详细地进行说明。然而本发明的范围并不受所述实施例限制。
76.〔实施例1〕
77.(第1工序)
78.将α-氧化铝6.2kg和氧化钇13.8kg与纯水一起进行湿式搅拌
·
粉碎而制成500g/l的前驱体混合粒子浆料。前驱体混合粒子通过microtrac hra而测定的d
50
为0.4μm。
79.(第2工序)
80.将第1工序中得到的浆料使用喷雾干燥器(大川原加工机(株式会社)制)进行造粒
·
干燥,得到造粒物。喷雾干燥器的操作条件设定为如以下所示的那样。
81.·
浆料供给速度:75ml/min
82.·
雾化器转速:12500rpm
83.·
入口温度:250℃
84.(第3工序)
85.将第2工序中得到的造粒物投入到氧化铝制的容器中,在大气气氛下、电炉中进行烧成而得到造粒颗粒。烧成温度设定为1400℃,烧成时间设定为6小时。颗粒的形状为大致球状。像这样操作,得到作为目标的粉末。
86.〔测定
·
皮膜的形成〕
87.对于实施例1中得到的粉末通过以下叙述的方法进行x射线衍射测定,得到图1中所示的x射线衍射图。基于所得到的x射线衍射图,对于正交晶yalo3的(112)峰、立方晶y3al5o
12
的(420)峰、单斜晶y4al2o9的(-221)峰、三方晶al2o3的(104)峰、及立方晶y2o3的(222)峰算出相对强度。此外,通过以下叙述的方法来测定细孔第1峰、细孔第2峰、细孔容积、微晶尺寸、bet比表面积及颗粒粒径(d
50
)。将这些结果示于以下的表2中。将细孔径分布的测定结果示于图2中。
88.在实施例1中得到的粉末所涉及的2θ=20
°
~60
°
的扫描范围的x射线衍射图中,未观察到来源于yalo3、y3al5o
12
及y4al2o9以外的成分的峰。
89.〔x射线衍射测定〕
90.·
装置:ultimaiv(株式会社rigaku制)
91.·
线源:cukα射线
92.·
管电压:40kv
93.·
管电流:40ma
94.·
扫描速度:2度/min
95.·
步进:0.02度
96.·
扫描范围:2θ=20
°
~60
°
97.〔细孔第1峰、细孔第2峰、0.1μm~1μm的细孔容积、5μm~50μm的细孔容积〕
98.·
装置:autopore iv(micromeritics公司制)
99.·
第1细孔峰:通常如果测定由一次粒子构成的颗粒的细孔径分布则可得到2个峰,将该峰中小径侧的峰设定为第1细孔峰。
100.·
第1细孔峰:将上述的峰中大径侧的峰设定为第2峰。
101.·
0.1μm~1μm的细孔容积:细孔径为0.1μm~1μm的细孔容积的累积值
102.·
5μm~50μm的细孔容积:细孔径为5μm~50μm的细孔容积的累积值
103.〔微晶尺寸测定〕
104.测定基于上述项的x射线衍射测定,由正交晶yalo3的(112)峰的半值幅通过scherrer式而算出。
105.〔bet比表面积测定〕
106.使用mountech公司制全自动比表面积计macsorb model-1201通过bet1点法进行测定。使用气体设定为氮氦混合气体(氮30vol%)。
107.〔颗粒粒径的测定〕
108.使用了microtracbel公司制microtrac d.h.s(hra)version 4.0。在溶解有0.2质
量%六偏磷酸的纯水中投入颗粒直至装置判定为恰当浓度为止,进行测定,得到d
50
的值。
109.〔利用喷镀法的成膜条件〕
110.作为基材,使用了20mm见方的铝合金板。对该基材的表面进行了等离子体喷镀。作为粉末的供给装置,使用了plasma-technik制的twin-system 10-v。作为等离子体喷镀装置,使用了sulzer metco制的f4。以搅拌转速50%、载气流量2.5l/min、供给刻度10%、等离子体气体ar/h2、输出功率35kw、装置-基材间距离150mm的条件,按照膜厚约成为60μm的方式进行了等离子体喷镀。
111.将实施例1中得到的皮膜供于上述的方法的x射线衍射测定,结果s2/s1为0,s3/s1为0.07,s4/s1为0.05。此外,未观察到来源于yalo3、y3al5o
12
、y4al2o9、al2o3及y2o3以外的成分的峰。
112.〔实施例2〕
113.除了将实施例1的第3工序中的烧成温度设定为1500℃以外,与实施例1同样地操作而得到复合氧化物的粉末,与实施例1同样地进行了评价及皮膜的形成。
114.〔实施例3、实施例5〕
115.除了将实施例1的第1工序中的α-氧化铝的量在实施例3中设定为6.5kg、在实施例5中设定为5.9kg以外,与实施例1同样地操作而得到复合氧化物的粉末,与实施例1同样地进行了评价及皮膜的形成。
116.〔实施例4〕
117.除了将实施例3的第3工序中的烧成温度设定为1500℃以外,与实施例3同样地操作而得到复合氧化物的粉末,与实施例3同样地进行了评价及皮膜的形成。
118.〔实施例6〕
119.除了将实施例5的第3工序中的烧成温度设定为1500℃以外,与实施例5同样地操作而得到复合氧化物的粉末,与实施例5同样地进行了评价及皮膜的形成。
120.〔实施例7〕
121.除了将实施例1的第2工序中的雾化器转速设定为20000rpm以外,与实施例1同样地操作而得到复合氧化物的粉末,与实施例1同样地进行了评价及皮膜的形成。
122.〔实施例8〕
123.除了将实施例1的第2工序中的雾化器转速设定为25000rpm以外,与实施例1同样地操作而得到复合氧化物的粉末,与实施例1同样地进行了评价及皮膜的形成。
124.〔实施例9〕
125.将实施例1的第1工序中的铝源变更为羟基氧化铝。羟基氧化铝的使用量以氧化铝换算计设定为6.2kg。此外,将第3工序中的烧成温度设定为1300℃。除了这些点以外,与实施例1同样地操作而得到复合氧化物的粉末,与实施例1同样地进行了评价及皮膜的形成。
126.〔实施例10〕
127.除了将实施例9的第3工序中的烧成温度设定为1200℃以外,与实施例9同样地操作而得到粉末,与实施例9同样地进行了评价及皮膜的形成。
128.〔实施例11〕
129.将实施例1的第1工序中的铝源变更为氢氧化铝。氢氧化铝的使用量以氧化铝换算计设定为6.2kg。除了这点以外,与实施例1同样地操作而得到复合氧化物的粉末,与实施例
1同样地进行了评价及皮膜的形成。
130.〔实施例12〕
131.除了将实施例11的第3工序中的烧成温度设定为1300℃以外,与实施例11同样地操作而得到复合氧化物的粉末,与实施例11同样地进行了评价及皮膜的形成。
132.〔比较例1〕
133.使用专利文献3的实施例1中记载的制造方法而得到复合氧化物的粉末。对于所得到的粉末,进行了与实施例1同样的评价及皮膜的形成。但是,在微晶尺寸的测定中,在本比较例中,不是由正交晶yalo3的(112)峰而是由立方晶y3al5o
12
的(420)峰算出微晶尺寸。
134.〔比较例2〕
135.除了将实施例1的第1工序中的α-氧化铝的量设定为10kg并且未添加氧化钇以外,与实施例1同样地操作而得到α-氧化铝粉末,与实施例1同样地进行了评价及皮膜的形成。但是,在微晶尺寸的测定中,在本比较例中,不是由正交晶yalo3的(112)峰而是由三方晶al2o3的(104)峰算出微晶尺寸。
136.对于实施例及比较例中形成的皮膜通过以下叙述的方法测定了表面粗糙度及蚀刻速率。
137.〔皮膜的表面粗糙度的测定〕
138.通过以下的方法测定了形成有皮膜的铝合金板中的该皮膜的表面粗糙度。
139.使用触针式表面粗糙度测定器(jis b0651:2001),求出算术平均粗糙度(ra)及最大高度粗糙度(rz)(jis b 0601:2001)。作为触针式表面粗糙度测定器,使用了kla-tencor公司制的触针式廓线仪p-7。测定条件设定为评价长度:5mm、测定速度:100μm/s。求出3点的平均值。
140.〔等离子体蚀刻速率的测定〕
141.在形成有皮膜的铝合金板中的该皮膜的一半处粘贴kapton胶带,以皮膜朝上的状态载置于蚀刻装置(samco公司制rie-10nr)的腔室中,进行了等离子体蚀刻。等离子体蚀刻条件设定为如下所述。所使用的蚀刻气体(cf4/o2)与专利文献3中使用的蚀刻气体(cf4/o2/ar)相比卤素系气体较多,为要求更高的卤素系等离子体耐性的条件。
142.蚀刻速率的测定是通过上述的表面粗糙度测定来计测等离子体暴露面与等离子体照射后将胶带剥离后的非暴露面的阶梯差。对每一张皮膜设定为3点测定点,求出3点的平均值。
143.·
气氛气体:cf4/o2=50/5(cc/min)
144.·
高频功率:rf 300w
145.·
压力:10pa
146.·
蚀刻时间:5小时
147.[表1]
[0148]
[0149][0150]
如由表2中所示的结果表明的那样,判定使用各实施例中得到的粉末而得到的皮膜与使用比较例中得到的粉末而得到的皮膜相比,蚀刻速率低,对于使用了卤素系气体的
等离子体蚀刻的耐蚀性高。
[0151]
产业上的可利用性
[0152]
如果使用本发明的成膜用或烧结用粉末,则能够容易地形成对于使用了卤素系气体的等离子体蚀刻的耐蚀性高的皮膜或烧结体。
再多了解一些
本文用于创业者技术爱好者查询,仅供学习研究,如用于商业用途,请联系技术所有人。