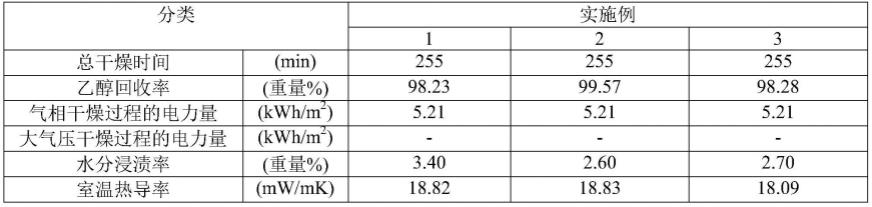
1.相关申请的交叉引用
2.本技术要求2020年11月9日在韩国知识产权局提交的第10-2020-0148448号韩国专利申请的权益,其公开内容通过引用的方式全部并入本文。技术领域
[0003][0004]
本发明涉及一种用于制造气凝胶毡的方法,更具体而言,涉及可改善湿凝胶毡干燥效率的制造气凝胶毡的方法。
背景技术:
[0005]
气凝胶是一种超多孔、高比表面积的材料(≥500m2/g)材料,具有约90.0%至99.9%的孔隙率和1nm至100nm范围内的孔径,并且是具有超轻量、超隔热、超低介电性等优异性质的材料。因此,已经积极开展了对气凝胶材料开发的研究及其作为透明隔热材料、环保高温隔热材料、用于高度集成装置的超低介电薄膜、催化剂和催化剂载体、超级电容器电极和海水淡化电极材料的实际用途的研究。
[0006]
气凝胶的最大优点是,气凝胶具有显示0.300w/m
·
k以下的热导率(低于传统有机隔热材料,如styrofoam)的超级隔热性,并且可以解决有机隔热材料的致命弱点——火灾脆弱性和发生火灾的情况下产生有害气体。
[0007]
通常,气凝胶是通过从如水玻璃和烷氧基硅烷类(teos、tmos、mtms等)等二氧化硅前体制备水凝胶,并在不破坏微观结构的情况下去除水凝胶内的液体成分来制造的。
[0008]
特别是,在纤维中形成疏水性二氧化硅气凝胶的疏水性二氧化硅气凝胶毡是防止湿气腐蚀的功能性隔热材料,广泛应用于建筑或工业领域。通常,这种气凝胶毡是通过硅溶胶溶液制备、凝胶化、熟化、表面改性和干燥步骤制造的。
[0009]
然而,如上所述的典型制造方法的干燥步骤通过超临界干燥进行,这是昂贵的过程,且存在的问题在于,疏水性二氧化硅气凝胶毡内的有机溶剂不能仅通过超临界干燥去除。因此,仅进行超临界干燥的气凝胶毡内残留有机溶剂,并且上述的残留有机溶剂在气凝胶毡使用并暴露于水分时导致水分吸收,这造成气凝胶毡的拒水性能降低,导致气凝胶毡的热导率增加,并导致气凝胶毡的耐久性降低的问题。
[0010]
因此,为解决上述问题,提出了一种在气凝胶毡的超临界干燥之后另外进行大气压干燥过程的方法。在超临界干燥之后另外进行的大气压干燥过程作为在大气压下使用温度为150℃至180℃的空气的热空气干燥过程进行。然而,当制造气凝胶毡时,另外进行的大气压干燥过程导致总干燥时间增加,并且存在的问题在于,热能基本上被消耗以产生热空气,并且本质上需要废气处理设施来处理大气压干燥过程产生的废气。
[0011]
[现有技术文献]
[0012]
[专利文献]
[0013]
(专利文献1)kr10-2012-0070948a
技术实现要素:
[0014]
技术问题
[0015]
本发明的一个方面提供了一种用于制造气凝胶毡的方法,该方法能够在超临界干燥过程之后不进行单独的大气压干燥过程而使气凝胶毡中残留的有机溶剂量最小化。
[0016]
技术方案
[0017]
根据本发明的一个方面,提供一种制造气凝胶毡的方法。
[0018]
(1)本发明提供一种用于制造气凝胶毡的方法,该方法包括:制备包含有机溶剂的湿凝胶毡(s10),将湿凝胶毡引入超临界萃取装置并使用超临界二氧化碳干燥湿凝胶毡(s20),对超临界萃取装置的压力进行减压(s30),和向减压的超临界萃取装置供应气态二氧化碳以干燥湿凝胶毡。
[0019]
(2)在(1)中,本发明提供一种用于制造气凝胶毡的方法,其中,有机溶剂是醇。
[0020]
(3)在(1)或(2)中,本发明提供一种用于制造气凝胶毡的方法,其中,在步骤(s10)中制备的湿凝胶毡是二氧化硅湿凝胶毡。
[0021]
(4)在(1)至(3)中的任一项中,本发明提供一种用于制造气凝胶毡的方法,其中,步骤(s10)包括:制备包含二氧化硅前体和有机溶剂的前体组合物(s1),制备包含有机溶剂、催化剂和表面改性剂的催化剂组合物(s2),将前体组合物和催化剂组合物引入浸渍槽并使毡用基材经过浸渍槽以制备湿凝胶毡(s3),和向湿凝胶毡添加包含表面改性剂的表面改性溶液,并使混合物熟化(s4)。
[0022]
(5)在(4)中,本发明提供一种用于制造气凝胶毡的方法,其中,步骤(s3)中制备的湿凝胶毡是当毡用基材经过浸渍槽时前体组合物和催化剂组合物在毡用基材中浸渍并凝胶化的湿凝胶毡。
[0023]
(6)在(1)至(5)中的任一项中,本发明提供一种用于制造气凝胶毡的方法,其中,步骤(s20)的干燥是干燥湿凝胶毡,并同时萃取有机溶剂。
[0024]
(7)在(6)中,本发明提供一种用于制造气凝胶毡的方法,其中,步骤(s20)中萃取的有机溶剂再循环至制备湿凝胶毡的步骤(s10)。
[0025]
(8)在(1)至(7)的任一项中,本发明提供一种用于制造气凝胶毡的方法,其中,进行步骤(s30)的减压以使超临界萃取装置的压力为10巴至70巴。
[0026]
(9)在(1)至(8)的任一项中,本发明提供一种用于制造气凝胶毡的方法,其中,步骤(s30)的减压包括:进行减压以使超临界萃取装置的压力为50巴至70巴(s31);和进行减压以使超临界萃取装置的压力为10巴至50巴(s32)。
[0027]
(10)在(1)至(9)的任一项中,本发明提供一种用于制造气凝胶毡的方法,其中,在步骤(s40)中供应气态二氧化碳的压力为10巴至70巴。
[0028]
(11)在(1)至(10)的任一项中,本发明提供一种用于制造气凝胶毡的方法,其中,在步骤(s40)中供应气态二氧化碳的温度为60℃以上。
[0029]
(12)在(1)至(11)的任一项中,本发明提供一种用于制造气凝胶毡的方法,其中,步骤(s40)的干燥是干燥湿凝胶毡,并同时萃取有机溶剂。
[0030]
(13)在(12)中,本发明提供一种用于制造气凝胶毡的方法,其中,步骤(s40)中萃取的有机溶剂再循环至制备湿凝胶毡的步骤(s10)。
[0031]
(14)在(1)至(13)的任一项中,本发明提供一种用于制造气凝胶毡的方法,其中,
用于制造气凝胶毡的方法还包括在步骤(s40)的干燥之后将超临界萃取装置的压力减压至大气压(s50)。
[0032]
(15)在(1)至(14)的任一项中,本发明提供一种用于制造气凝胶毡的方法,其中,有机溶剂的回收率为98.00重量%以上。
[0033]
有利效果
[0034]
根据本发明的气凝胶毡的制造方法,在干燥后,可使气凝胶毡的残留的有机溶剂量最小化,从而具有防止残留的有机溶剂导致的物理性质劣化的效果。
[0035]
另外,根据本发明的气凝胶毡的制造方法,可最大化回收有机溶剂,从而具有通过降低气凝胶毡的制造成本来提高生产率的效果。
[0036]
另外,根据本发明的气凝胶毡的制造方法,可以省略大气压干燥过程,从而具有缩短总干燥时间的效果。
[0037]
另外,根据本发明的气凝胶毡的制造方法,可以省略大气压干燥过程,从而具有通过降低大气压干燥的热能消耗来提高生产率的效果。
[0038]
另外,根据本发明的气凝胶毡的制造方法,可以省略大气压干燥过程,从而不需要废气处理设施来处理大气压干燥过程产生的废气。
附图说明
[0039]
图1是示出根据本发明实施例1至3的对于各干燥时间的超临界萃取装置中的压力变化的图;
[0040]
图2是示出根据本发明比较例1至3的对于各干燥时间的超临界萃取装置中的压力变化的图。
具体实施方式
[0041]
在下文中,将更详细地描述本发明以便于理解本发明。
[0042]
应当理解,本发明的说明书和权利要求书中使用的词语或术语不应被解释为仅具有常用词典中定义的含义。将进一步理解,基于发明人可以适当地定义词语或术语的含义以最好地解释发明的原则,词语或术语应被解释为具有与其在相关技术的情况中和本发明的技术思想中的含义一致的含义。
[0043]
本发明提供一种可改善湿凝胶毡的干燥效率的用于制造气凝胶毡的方法。
[0044]
根据本发明的实施方式,气凝胶毡的制造方法可包括:制备包含有机溶剂的湿凝胶毡(s10),将湿凝胶毡引入超临界萃取装置并使用超临界二氧化碳干燥湿凝胶毡(s20),对超临界萃取装置的压力进行减压(s30)和向减压的超临界萃取装置供应气态二氧化碳以干燥湿凝胶毡(s40)。
[0045]
根据本发明的实施方式,制备包含有机溶剂的湿凝胶毡的步骤(s10)是制备湿凝胶毡以制造通过步骤(s20至s40)的后续干燥过程获得的气凝胶毡的步骤,并且可以是制备包含在溶胶溶液、表面改性溶液等中包含的有机溶剂的湿凝胶毡的步骤。
[0046]
根据本发明的实施方式,有机溶剂可以是在制备湿凝胶毡时可使用的有机溶剂,并且作为具体实例可以是极性有机溶剂,作为更具体实例可以是醇。此处,醇可以是选自由一元醇(如甲醇、乙醇、异丙醇和丁醇)和多元醇(如甘油、乙二醇、丙二醇、二乙二醇、二丙二
醇和山梨醇)组成的组中的一种或多种,并且作为具体实例,考虑到与水和与稍后制备的湿凝胶的混溶性,醇可以是选自由具有1至6个碳原子的一元醇(如甲醇、乙醇、异丙醇和丁醇)组成的组中的一种或多种。
[0047]
根据本发明的实施方式,步骤(s10)中制备的湿凝胶毡可以是由二氧化硅前体制备的二氧化硅湿凝胶毡,因此,通过步骤(s20至s40)的后续干燥过程获得的气凝胶毡可以是二氧化硅气凝胶毡。
[0048]
根据本发明的实施方式,步骤(s10)可通过包括二氧化硅溶胶溶液制备步骤、凝胶化步骤、熟化步骤和表面改性步骤来进行。作为具体实例,步骤(s10)可包括:制备包含二氧化硅前体和有机溶剂的前体组合物(s1),制备包含有机溶剂、催化剂和表面改性剂的催化剂组合物(s2),将前体组合物和催化剂组合物引入浸渍槽并使毡用基材经过浸渍槽以制备湿凝胶毡(s3),和向湿凝胶毡添加包含表面改性剂的表面改性溶液并使混合物熟化(s4)。
[0049]
根据本发明的实施方式,步骤(s1)是制备用于制造湿凝胶和气凝胶的前体组合物的步骤,并且可以通过将二氧化硅前体与有机溶剂混合来进行。
[0050]
根据本发明的实施方式,二氧化硅前体是使气凝胶含有二氧化硅的材料,可以是选自由原硅酸四甲基酯(tmos)、原硅酸四乙基酯(teos)、原硅酸甲基三乙基酯、原硅酸二甲基二乙基酯、原硅酸四丙基酯、原硅酸四异丙基酯、原硅酸四丁基酯、原硅酸四仲丁基酯、原硅酸四叔丁基酯、原硅酸四己基酯、原硅酸四环己基酯和原硅酸四(十二烷基)酯组成的组中的一种或多种,另外,可使用上述化合物的预水解产物。当使用预水解产物时,不需要添加酸,可以缩短或省略水解二氧化硅前体的过程,并且可以促进表面改性效果。
[0051]
根据本发明的实施方式,二氧化硅前体可以是预水解的原硅酸四乙基酯(hteos),此处,预水解的原硅酸四乙基酯是具有宽分子量分布的预水解聚硅酸乙基酯低聚物材料,其可根据用户的反应条件容易地应用,这是因为当通过改变预水解程度(水合程度)从原硅酸四乙基酯单体合成低聚物形式时,可调节如凝胶化时间等物理性质,并且其具有优异的最终产品再现性,从而具有保持均一品质的效果。
[0052]
根据本发明的实施方式,步骤(s1)的有机溶剂可以与上述有机溶剂相同。
[0053]
根据本发明的实施方式,步骤(s1)可通过以1.0:0.1至10.0、1.0:0.5至5.0、1.0:1.0至3.0或1.0:1.0至1.5的重量比混合二氧化硅前体和有机溶剂来进行。
[0054]
根据本发明的实施方式,步骤(s2)是制备用于诱导步骤(s1)制备的前体组合物的凝胶化的催化剂组合物的步骤,并且可以通过混合有机溶剂、催化剂和表面改性剂来进行。
[0055]
根据本发明的实施方式,步骤(s20)的有机溶剂可以与上述有机溶剂相同,并且作为具体实例,可以与步骤(s1)中的有机溶剂相同。
[0056]
根据本发明的实施方式,催化剂可以是碱催化剂,且作为具体实例,可以是如氢氧化钠、氢氧化钾等无机碱,或如氢氧化铵等有机碱,作为允许形成使得可诱导二氧化硅前体凝胶化的ph条件的材料。具体而言,有机碱可以是选自由氢氧化铵(nh4oh)、四甲基氢氧化铵(tmah)、四乙基氢氧化铵(teah)、四丙基氢氧化铵(tpah)、四丁基氢氧化铵(tbah)、甲胺、乙胺、异丙胺、单异丙胺、二乙胺、二异丙胺、二丁胺、三甲胺、三乙胺、三异丙胺、三丁胺、胆碱、单乙醇胺、二乙醇胺、2-氨基乙醇、2-(乙氨基)乙醇、2-(甲氨基)乙醇、n-甲基二乙醇胺、二甲氨基乙醇、二乙氨基乙醇、次氮基三乙醇、2-(2-氨基乙氧基)乙醇、1-氨基-2-丙醇、三乙醇胺、单丙醇胺和二丁醇胺组成的组中的一种或多种。
[0057]
根据本发明的实施方式,催化剂组合物中包含的表面改性剂可以是烷基硅烷化合物,作为具体实例,可以是选自由三甲基乙氧基硅烷(tmes)、三甲基硅醇(tms)、三甲基氯硅烷(tmcs)、甲基三甲氧基硅烷(mtms)、甲基三乙氧基硅烷(mtes)、二甲基二乙氧基硅烷(dmdeos)、乙基三乙氧基硅烷和苯基三乙氧基硅烷组成的组中的一种或多种。
[0058]
根据本发明的实施方式,通过在催化剂组合物中包含表面改性剂,表面改性剂可作为共前体参与凝胶化反应,并可使形成的二氧化硅湿凝胶毡疏水化。因为烷基硅烷化合物可以在凝胶化步骤中与二氧化硅前体凝胶化。另外,烷基硅烷化合物可包埋在凝胶中,此时,烷基硅烷化合物可在熟化和表面改性步骤中形成烷基-si-o-si网络,以使二氧化硅湿凝胶毡疏水化。
[0059]
根据本发明的实施方式,步骤(s2)可通过以1.000:0.001至0.100:0.010至1.000、1.00:0.01至0.08:0.01至0.50或1.00:0.02至0.06:0.05至0.30的重量比混合有机溶剂、催化剂和表面改性剂来进行。
[0060]
根据本发明的实施方式,步骤(s3)是用二氧化硅溶胶浸渍毡用基材并通过凝胶化制备湿凝胶毡的步骤,可以通过包括将前体组合物和催化剂组合物引入浸渍槽以制备二氧化硅溶胶、使毡用基材经过浸渍槽以用二氧化硅溶胶浸渍毡用基材以及进行凝胶化的步骤来进行。
[0061]
根据本发明的实施方式,通过混合前体组合物和催化剂组合物制备的二氧化硅溶胶可自身进行凝胶化,此时,当毡用基材经过浸渍槽时,随着用二氧化硅溶胶浸渍毡用基材,可以实现凝胶化。也就是说,在步骤(s3)中制备的湿凝胶毡可以是当毡用基材经过浸渍槽时前体组合物和催化剂组合物在毡用基材中浸渍并凝胶化的湿凝胶毡。
[0062]
根据本发明的实施方式,当在步骤(s3)中毡用基材经过浸渍槽时,二氧化硅溶胶的温度可为室温(23
±
5℃)至50℃、室温至40℃或室温至35℃,并且在该范围内,具有凝胶化稳定进行的效果。
[0063]
根据本发明的实施方式,步骤(s3)中的凝胶化可进行5分钟至1小时、5分钟至30分钟或10分钟至20分钟,并且在此范围内,具有可充分诱导凝胶化的效果。
[0064]
根据本发明的实施方式,毡用基材可根据其用途适当选择,并且作为具体实例,可为无机纤维或有机纤维。作为更具体的实例,毡用基材可以是膜、片材、网、纤维、多孔体、泡沫、无纺布体或其两层以上的层压物,并且必要时可在其表面上形成或图案化表面粗糙度。毡用基材可以是能够通过包括空间或空隙(二氧化硅溶胶可以由其容易地插入毡用基材中)而由于二氧化硅溶胶形成的气凝胶所致进一步改善隔热性能的纤维。
[0065]
根据本发明的实施方式,纤维可以是聚对苯二甲酸乙二醇酯、聚酰胺、聚苯并咪唑、芳香聚酰胺、丙烯酸类树脂、酚醛树脂、聚酯、聚醚醚酮(peek)、聚烯烃(聚乙烯、聚丙烯或聚乙烯-丙烯共聚物等)、纤维素、碳、棉、羊毛、麻、无纺布、玻璃纤维或陶瓷棉,并且作为具体实例,可以是玻璃纤维。
[0066]
根据本发明的实施方式,玻璃纤维可以是玻璃纤维针刺毡,此时,玻璃纤维针刺毡的密度可以为100kg/m3至150kg/m3、110kg/m3至140kg/m3或120kg/m3至140kg/m3。
[0067]
根据本发明的实施方式,步骤(s4)可以是将包含表面改性剂的表面改性溶液添加到湿凝胶毡中并使混合物熟化以制造表面被疏水化以改进拒水性能的气凝胶毡的步骤,此时,可同时进行熟化和表面改性。
[0068]
根据本发明的实施方式,表面改性溶液可包含有机溶剂和表面改性剂,此时,有机溶剂可与上述有机溶剂相同,并且作为具体实例,可与步骤(s1)和步骤(s2)的有机溶剂相同。
[0069]
根据本发明的实施方式,步骤(s4)的表面改性剂可以是烷基硅烷化合物,并且作为具体实例,可以是选自由三甲基乙氧基硅烷(tmes)、三甲基硅醇(tms)、三甲基氯硅烷(tmcs)、甲基三甲氧基硅烷(mtms)、甲基三乙氧基硅烷(mtes)、二甲基二乙氧基硅烷(dmdeos)、乙基三乙氧基硅烷和苯基三乙氧基硅烷组成的组中的一种或多种。
[0070]
根据本发明的实施方式,步骤(s4)可通过以1.00:0.01至0.50、1.0:0.1至0.3或1.0:0.1至0.2的重量比混合有机溶剂和表面改性剂来进行。
[0071]
根据本发明的实施方式,步骤(s4)可在60℃至100℃、70℃至90℃或75℃至85℃进行1小时至10小时、2小时至8小时或3小时至7小时,在此范围内,具有可充分诱导表面改性的效果。
[0072]
根据本发明的实施方式,步骤(s20)是进行超临界干燥以去除溶剂,同时保持熟化二氧化硅湿凝胶的孔隙结构的步骤,可使用超临界二氧化碳进行。二氧化碳(co2)在室温和大气压下呈气态。然而,当温度和压力超过称为超临界点的预定的温度和压力极限时,蒸发过程不会发生,使得二氧化碳处于无法区分气体和液体的临界状态。临界状态的二氧化碳被称为超临界二氧化碳。超临界二氧化碳的分子密度接近液体,但粘度较低,因此具有类似于气体的性质,并且由于扩散快和热导率高,因此具有较高的干燥效率,从而可以缩短干燥过程时间。
[0073]
根据本发明的实施方式,步骤(s20)可通过包括将湿凝胶毡引入作为超临界萃取装置的超临界干燥反应器或超临界萃取器,填充液态二氧化碳,并用二氧化碳置换湿凝胶毡中的有机溶剂的溶剂置换过程来进行。另外,在溶剂置换过程之后,步骤(s20)可通过以恒定升温速率(具体为0.1℃/min至10.0℃/min)将温度升高到40℃至80℃,然后施加二氧化碳变为超临界的压力以上的压力(具体为100巴至170巴的压力)来进行,从而控制二氧化碳处于超临界状态。一般来说,二氧化碳在31℃的温度和73.8巴的压力下会变为超临界。
[0074]
根据本发明的实施方式,步骤(s20)的干燥可以是干燥湿凝胶毡,同时萃取有机溶剂,作为具体实例,可以将有机溶剂与二氧化碳一起萃取,萃取的有机溶剂可以再循环至制备湿凝胶毡的步骤(s10)。如上所述,通过干燥湿凝胶毡以去除有机溶剂,同时重复使用从中萃取的有机溶剂,可以减少在制备湿凝胶毡时引入的额外量的有机溶剂,因此,具有通过防止制造成本增加提高生产率的效果。
[0075]
根据本发明的实施方式,步骤(s20)中使用的二氧化碳可与有机溶剂一起萃取,然后二氧化碳和有机溶剂可彼此分离并回收,从而如上所述再利用有机溶剂。此时,可通过单独的分离器进行分离。另外,可将步骤(s20)中使用的二氧化碳与有机溶剂分离,然后回收以用于下文所述的步骤(s20)和/或步骤(s40)。如上所述,通过重复使用二氧化碳,可以减少在干燥湿凝胶毡时引入的额外量的二氧化碳,因此,具有通过防止制造成本增加来提高生产率的效果。
[0076]
根据本发明的实施方式,为了通过超临界干燥去除湿凝胶毡中的所有有机溶剂,超临界干燥可以进行很长时间,这需要消耗大量能量来持续保持高压和高温,以将二氧化碳保持在超临界状态。因此,从加压开始,步骤(s20)的干燥可进行100至720分钟、120至360
分钟或150至180分钟,在此范围内,湿凝胶毡中的有机溶剂可被有效去除。
[0077]
根据本发明的实施方式,步骤(s30)可以是在完成步骤(s20)的超临界干燥之后,将超临界萃取装置的压力减压以获得湿凝胶毡或气凝胶毡的步骤。
[0078]
根据本发明的实施方式,湿凝胶毡中的大部分有机溶剂通过干燥步骤(s20)被去除并萃取,但当使用气凝胶毡并暴露于水分时,部分有机溶剂可能残留并导致水分吸收,这造成气凝胶毡的拒水性能降低,导致气凝胶毡的热导率增加,并导致气凝胶毡耐久性降低的问题。因此,根据本发明的实施方式,可进行步骤(s30)的减压,使得超临界萃取装置的压力为10巴至70巴、10巴至50巴、10巴至30巴或15巴至25巴,从而有效地进行下述的步骤(s40)的干燥。作为具体实例,步骤(s30)的减压可通过包括下述过程进行:进行减压,使超临界萃取装置的压力为30巴至70巴、40巴至70巴或50巴至70巴(s31),以及进行减压,使超临界萃取装置的压力为10巴至50巴、10巴至40巴、10巴至30巴或15巴至25巴(s32),在这种情况下,具有防止因突然压降而可能出现的安全问题的效果。
[0079]
根据本发明的实施方式,步骤(s40)是在步骤(s20)的干燥之后另外去除并萃取湿凝胶毡中残留的有机溶剂的步骤,并且可以在超临界萃取装置中进行。
[0080]
如上所述,通常,为了另外去除并萃取湿凝胶毡或气凝胶毡中残留的有机溶剂,在如步骤(s20)对湿凝胶毡进行超临界干燥后,另外进行大气压干燥过程。此处,大气压干燥过程作为在大气压下使用温度为150℃至180℃的空气的热空气干燥过程进行。然而,当制造气凝胶毡时,另外进行的大气压干燥过程导致总干燥时间增加,并且存在的问题在于,热能基本上被消耗以产生热空气,并且基本上需要废气处理设施来处理大气压干燥过程产生的废气。
[0081]
然而,在根据本发明的实施方式如步骤(s40)通过向减压的超临界萃取装置供应气态二氧化碳来干燥湿凝胶毡的情况下,可以省略大气压干燥过程,从而在缩短总干燥时间的同时降低大气压干燥的热能消耗以提高生产率,同时,不需要废气处理设施来处理大气压干燥过程产生的废气。
[0082]
根据本发明的实施方式,步骤(s40)的特征在于供应气态二氧化碳,而不是如步骤(s20)的超临界二氧化碳。此时,步骤(s40)中供应气态二氧化碳的压力可以是10巴至70巴、10巴至50巴、10巴至30巴或15巴至25巴。也就是说,供应气态二氧化碳的压力可以与在步骤(s30)中减压的超临界萃取装置的压力相同。同时,供应气态二氧化碳的减压超临界萃取装置的压力不在大气压下单独加压,而是在超临界萃取装置中完成超临界干燥之后根据步骤(s30)减压,因此存在的优势在于,无需单独加压以将超临界萃取装置的压力保持为上述压力。
[0083]
根据本发明的实施方式,步骤(s40)中供应气态二氧化碳的温度可以是60℃以上、60℃至120℃、60℃至100℃、70℃至100℃或70℃至90℃,在该范围内,具有在气相干燥过程的能量最小化的同时最大化去除和萃取残留有机溶剂的效果。
[0084]
根据本发明的实施方式,如在步骤(s20)中那样,步骤(s40)的干燥可以是干燥湿凝胶毡,同时萃取有机溶剂,并且作为具体实例,有机溶剂可以与二氧化碳一起萃取,并且萃取的有机溶剂可再循环至制备湿凝胶毡的步骤(s10)。如上所述,通过使用气态二氧化碳去除有机溶剂以另外干燥湿凝胶毡,同时再利用从中萃取的有机溶剂,可以减少在制备湿凝胶毡时引入的额外量的有机溶剂,因此,具有通过防止制造成本增加来提高生产率的效
果。
[0085]
根据本发明的实施方式,步骤(s40)中使用的二氧化碳可与有机溶剂一起萃取,然后二氧化碳和有机溶剂可彼此分离并回收,从而如上所述再利用有机溶剂。此时,分离可通过单独的分离器进行。另外,步骤(s40)中使用的二氧化碳可与有机溶剂分离,然后回收以用于步骤(s20)和/或步骤(s40)。如上所述,通过重复使用二氧化碳,可以减少在干燥湿凝胶毡时引入的额外量的二氧化碳,因此,具有通过防止制造成本增加来提高生产率的效果。
[0086]
根据本发明的实施方式,从完成步骤(s30)的减压起,步骤(s40)的干燥可进行10至60分钟、20至50分钟或25至40分钟,在此范围内,气凝胶毡中的有机溶剂可被最大化去除。
[0087]
根据本发明的实施方式,用于制造气凝胶毡的方法还可包括在步骤(s40)的干燥之后将超临界萃取装置的压力减压至大气压(s50)。步骤(s50)可以是获得有机溶剂被去除并萃取的气凝胶毡的步骤。
[0088]
根据本发明的实施方式,用于制造气凝胶毡的方法的有机溶剂回收率可以为98.00重量%以上、98.00重量%至100.00重量%、98.20重量%至99.99重量%或98.23重量%至99.57重量%。
[0089]
另外,本发明提供通过所述制造气凝胶毡的方法制造的气凝胶毡。该气凝胶毡可具有均匀的热导率,和由于毡中形成的均匀的热导率而大大改进的整体隔热。
[0090]
根据本发明的实施方式,气凝胶毡包括毡用基材,以及在毡用基材的内部和表面形成的二氧化硅气凝胶,并且水分浸渍率可以为0.1重量%至5.0重量%、1.0重量%至4.0重量%、2.0重量%至3.5重量%或2.6重量%至3.4重量%。
[0091]
根据本发明的实施方式,气凝胶毡包括毡用基材,以及在毡用基材内部和表面形成的二氧化硅气凝胶,并且室温热导率可以为30.00mw/mk以下、10.00mw/mk至30.00mw/mk、15.00mw/mk至20.00mw/mk、18.00mw/mk至19.00mw/mk或18.09mw/mk至18.83mw/mk。
[0092]
根据本发明的实施方式,气凝胶毡可有效地用作用于飞机、船舶、汽车、建筑结构等的隔热材料、保温材料或不燃材料,以及用于隔热和冷却的工厂设施,如各种工业设施的管道和工业炉。
[0093]
在下文中,将详细描述本发明的实施方式,以使本领域技术人员可以容易地实施本发明。然而,本发明可以以许多不同的形式实施,并且不限于本文所述的实施方式。
[0094]
实施例
[0095]
实施例1
[0096]
预水解的原硅酸四乙基酯和乙醇以1:1.1的重量比混合以制备二氧化硅前体组合物。
[0097]
另外,将乙醇、作为碱催化剂的氢氧化钠和作为表面改性剂的三甲基乙氧基硅烷(tmes)以1:0.046:0.14的重量比混合以制备催化剂组合物。
[0098]
此后,将上述制备的二氧化硅前体组合物和催化剂组合物以1:0.941的重量比引入15l浸渍槽并混合以制备二氧化硅溶胶,作为毡用基材,使玻璃纤维针刺毡(密度为130kg/m3)经过浸渍槽,从而在将二氧化硅溶胶的温度保持为室温(23
±
5℃)的情况下被浸渍,然后进行凝胶化以制造凝胶化的湿凝胶毡。此时,凝胶化在10分钟至20分钟之间完成。
[0099]
向凝胶化的湿凝胶毡添加表面改性溶液(乙醇和作为表面改性剂的三甲基乙氧基
硅烷(tmes)以1:0.128的重量比混合),然后在75℃熟化5小时,以制造包含乙醇的湿凝胶毡。
[0100]
此后,将上述制造的包含乙醇的湿凝胶毡放入70l超临界萃取器中,并向其中注入二氧化碳。接下来,用15分钟将超临界萃取器的温度升高至80℃,并将压力施加至170巴以控制二氧化碳处于超临界状态,此后,在包含乙醇的湿凝胶毡上进行超临界干燥。此时,从加压开始,干燥进行165分钟,通过分离器回收与超临界二氧化碳一起萃取的乙醇。
[0101]
超临界干燥完成后,进行减压15分钟,将超临界萃取器的压力减压至60巴,此后再进行另外的减压15分钟,以将超临界萃取器的压力减压至20巴。
[0102]
向压力减压至20巴的超临界萃取器供应并循环温度为80℃的气态二氧化碳,以对具有残留乙醇的湿凝胶毡进行气相干燥。此时,自减压完成起,干燥进行30分钟,并通过分离器回收与超临界二氧化碳一起萃取的乙醇。
[0103]
气相干燥完成后,减压进行15分钟,将超临界萃取器的压力减压至大气压,获得干燥的气凝胶毡。
[0104]
实施例2
[0105]
以与实施例1相同的方式进行相同的操作,不同之处在于,在实施例1中,当使作为毡用基材的玻璃纤维针刺毡经过浸渍槽被浸渍时,将二氧化硅溶胶的温度升高至35℃然后保持,而不是保持为室温。
[0106]
实施例3
[0107]
以与实施例1相同的方式进行相同的操作,不同之处在于,在实施例1中,当制备包含乙醇的湿凝胶毡时,添加表面改性溶液,并在85℃而不是75℃熟化5小时。
[0108]
比较例1至3
[0109]
以与实施例1相同的方式进行相同的操作,不同之处在于,对实施例1中制造的包含乙醇的湿凝胶毡如下进行干燥过程。
[0110]
将实施例1中制造的包含乙醇的湿凝胶毡放入70l超临界萃取器中,并向其中注入二氧化碳。接下来,用15分钟将超临界萃取器的温度升高至80℃,并将压力施加至170巴以控制二氧化碳处于超临界状态,此后,在包含乙醇的湿凝胶毡上进行超临界干燥。此时,从加压开始起,干燥进行165分钟,通过分离器回收与超临界二氧化碳一起萃取的乙醇。
[0111]
超临界干燥完成后,进行减压15分钟,将超临界萃取器的压力减压至60巴,此后再进行另外的减压25分钟,以将超临界萃取器的压力减压至大气压,从而获得具有残留乙醇的超临界干燥的湿凝胶毡。
[0112]
将获得的具有残留乙醇的湿凝胶毡放入干燥器中,并使用利用在大气压下温度为180℃的空气的热空气进行大气压干燥。此时,大气压干燥进行50分钟,并使用单独的废气处理装置排放大气压干燥产生的废气。
[0113]
大气压干燥完成后,获得干燥的气凝胶毡。
[0114]
比较例2至3
[0115]
为了确认在与比较例1相同条件下的再现性,以与比较例1相同的方式分别进行相同的操作。
[0116]
比较例4
[0117]
以与比较例1相同的方式进行相同的操作,不同之处在于,在比较例1中,获得的气
凝胶毡为超临界干燥的湿凝胶毡,而不进行大气压干燥。
[0118]
实验例
[0119]
按照以下方式测量根据实施例1至3和比较例1至4的干燥过程的总干燥时间、乙醇的回收率、气相干燥过程或大气压干燥过程中消耗的电力量、制备的气凝胶毡的水分浸渍率和室温热导率,并显示在表1和表2中。
[0120]
*总干燥时间:将湿凝胶毡放入超临界萃取器后,基于开始加压的时间,将加压、干燥和减压所消耗的总时间相加。
[0121]
*乙醇回收率(重量%):制造气凝胶毡时,计算相对于作为溶剂引入的总乙醇含量的通过干燥过程回收的乙醇含量,并以百分比表示。
[0122]
*气相干燥过程或大气压干燥过程中消耗的电力量(kwh/m2):对于1卷(4m2)湿凝胶毡,测量并示出实施例的气相干燥过程中消耗的电力量和比较例的大气压干燥过程中消耗的电力量。
[0123]
*水分浸渍率(重量%):对于各个实施例和比较例中制造的气凝胶毡,制备三个尺寸为254mm x 254mm的试样(厚度小于100mm),并使试样漂浮在21
±
2℃的蒸馏水上,在试样上放置6.4mm的筛网,以将试样浸入水面下127mm处来浸渍试样。15分钟后,移除筛网,当试样上升至表面时,用夹子将试样取出并垂直悬挂60
±
5秒。此后,各自测量浸渍前后的重量,以确定重量增加率,三个试样的平均值显示为水分浸渍率。
[0124]
*室温热导率(mw/mk):由各个实施例和比较例中制造的气凝胶毡制备尺寸为30cm x 30cm的试样,并使用netzsch co.,ltd的hfm 436lambda设备测量试样的室温(23
±
5℃)热导率。
[0125]
[表1]
[0126][0127]
[表2]
[0128][0129]
如表1和表2所示,在根据本发明的气凝胶毡的制造方法进行干燥过程的实施例1至3的情况下,与在超临界干燥后进行单独的大气压干燥过程的比较例1至3相比,总干燥时间缩短了15分钟(5.6%),同时实现了相同水平的水分浸渍率和室温热导率,乙醇的回收率得到提高,特别是,与比较例1至3的大气压干燥过程中消耗的20.84kwh/m2的平均电力量相比,在气相干燥过程中仅消耗了5.21kwh/m2的电力量,从而证实了电力消耗量减少。
[0130]
同时,在超临界干燥后未进行单独的大气压过程或气相干燥过程的比较例4的情况下,总干燥时间最短,但立即获得超临界干燥的湿凝胶毡作为气凝胶毡,使得乙醇残留在气凝胶毡中,因此,当水分渗透时,水分被乙醇吸收,从而可以确认,由于水分浸渍率的增加,拒水性能降低。
[0131]
从上述结果可以确认,当根据本发明的气凝胶毡的制造方法时,干燥后可以使气凝胶毡的残留有机溶剂量最小化,从而可以防止残留有机溶剂引起的物理性质劣化,可最大化回收有机溶剂,从而可以通过降低气凝胶毡的制造成本来提高生产率,并且可以省略大气压干燥过程,从而降低大气压干燥的热能消耗以提高生产率,同时缩短总干燥时间,同时,无需废气处理设施来处理大气压干燥过程产生的废气。
再多了解一些
本文用于创业者技术爱好者查询,仅供学习研究,如用于商业用途,请联系技术所有人。