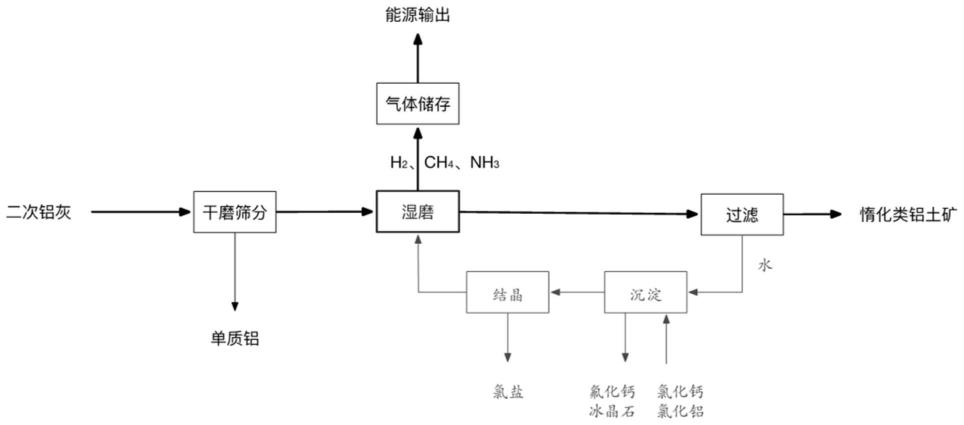
1.本发明涉及资源环境领域,具体涉及一种二次铝灰无害化处理的方法。
背景技术:
2.二次铝灰是铝工业生产过程的必然产物和最终产物,随着国民经济的高速发展,铝制品的需求量快速增长,二次铝灰的产生量也成比例增长,保守估计全国每年产生量在350万吨以上,历年积累更不计其数。二次铝灰中的铝元素除了以氧化铝形态存在外,还以单质铝、碳化铝、氮化铝等形式存在。这些形态的物质活性极高,易在潮湿环境下与水发生反应,生产氢气、甲烷、氨气等易燃性、刺激性有害气体。此外,受上游工艺影响,二次铝灰还含有高达3~5%的氟盐和1~20%的氯盐,已被明确列入《国家危险废物名录》。目前,二次铝灰堆积所造成的环境污染问题已严重制约我国铝工业的持续发展。
3.针对上述行业难题,从二次铝灰中脱除活性组分(单质铝、氮化铝、碳化铝)和毒害组分(氟盐、氯盐),实现二次铝灰的无害化是十分必要的。发明专利(cn201710996711.2)公开了一种铝灰资源化方法,包括如下步骤:将二次铝灰经研磨后过筛,筛后物加入烧碱(naoh)溶液和防沸剂,在常压下进行充分反应至无气泡产生,收集氨气、氢气和甲烷;在高温高压条件下,过滤后将所得滤液进行稀释,冷却稀释后的滤液至室温,析出氢氧化铝晶体;过滤后所得氢氧化铝煅烧失水得氧化铝。“从再生铝二次铝灰中浸出铝的动力学试验研究”(《湿法冶金》2020,39(05),371-375)一文发表了用盐酸从二次铝灰中浸出铝(单质铝、氮化铝、氧化铝)的试验研究,考察了浸出时间、浸出温度、盐酸与铝灰液固体积质量比、盐酸浓度对铝浸出率的影响及不同温度下的浸出动力学。通常情况下,在二次铝灰无害化和资源化过程中需添加酸或碱强化脱除活性组分和毒害组分。
4.二次铝灰中的活性组分在水解过程中会在颗粒表面生成氢氧化铝,阻止水解过程的进一步发生,从而也同时阻止毒害组分从其它组分解离和浸出。现有技术一般采用酸或碱脱除氢氧化铝薄膜,维持水解和浸出过程的进行,但是,这需要在工艺中加入大量的酸或碱,从而导致现有技术存在如下缺陷:其一,酸或碱的加入,无疑导致现在技术的经济运行成本大幅升高;其二,从生命周期评价(lca)的视角看,高耗电原材料酸或碱导致现有技术的环境性能大幅降低;其三,根据物质不灭原理,加入酸或碱后常经中和反应生成盐,导致后续废水处理难度大幅增大;其四,氮化铝水解生成的氨气一般设置吸收塔从混合气分离出来,需要额外增加酸的使用,生成的铵盐溶液需要高耗能的蒸发、结晶工序,完成铵盐的提取,工艺复杂度大大增加,设备投资和运行成本也大大增加。
技术实现要素:
5.本发明的目的就是为了克服上述现有技术存在的缺陷而提供一种无需添加大量酸或碱的二次铝灰无害化处理方法。
6.本发明的目的可以通过以下技术方案来实现:一种二次铝灰无害化处理方法,包括以下步骤:
7.1)基于金属铝易形变和其它组份易破碎的性质,干式研磨操作下金属铝越磨越扁、大,其它组份越磨越小,因此将二次铝灰通过干式研磨和筛分回收大部分单质铝;
8.2)筛分得到的筛下物再进行湿式研磨,筛下物中的活性组分与水发生反应,生成的混合气体进行收集回收,可溶性组分溶于浆相中;
9.3)浆相经过滤分为清液和滤渣,滤渣成为惰化类铝土矿产品;
10.4)清液中氟盐通过沉淀法回收,氯盐通过结晶法回收,水回用于湿式研磨。
11.进一步地,步骤1)所述的干式研磨采用的研磨介质为球磨,直径为0.5~2.0mm,研磨时间为0.5h~2h。
12.进一步地,步骤1)所述的干式研磨过程中添加al(oh)cl2,添加量为二次铝灰质量的0.05~1.00%。
13.进一步地,步骤1)所述的筛分的粒级为0.2~0.4mm。
14.进一步地,步骤2)所述的筛下物中含有活性组分和可溶性组分,其中活性组分包括残余单质铝、氮化铝或碳化铝,可溶性组分包括氯盐或氟盐;
15.活性组分与水发生反应生成的混合气体包括氢气、氨气、甲烷,作为能源使用。
16.进一步地,步骤2)所述的湿式研磨采用的磨介质为球磨,直径0.8~2.2mm,研磨时间为0.5h~2h,研磨后的物料粒径在45μm以下。
17.进一步地,步骤2)所述的湿式研磨过程中添加水,水的添加量为使筛下物与水混合后的固液比为0.05~0.30:1。
18.进一步地,步骤2)所述的湿式研磨过程中添加al(oh)cl2,添加量为筛下物质量的0.05~1.00%。
19.进一步地,步骤3)浆液过滤采用压滤机或吸滤机;
20.当清液中盐分达到6%以上时,向溶液中加入cacl2、alcl3获得氟化钙、冰晶石产品,以蒸发结晶方式提取获得氯盐。
21.与现有技术相比,本发明具有如下有益效果:
22.1)本发明利用干磨条件下单质铝易于变形、其它组分脆性大的特性,通过干磨促使单质铝越磨越大越扁,其它组分越磨越小,再通过筛分提取高值单质铝,从而突破炒灰法等现有技术无法提5%以下单质铝的技术瓶颈。
23.2)本发明在干磨过程中加入微量al(oh)cl2可显著减少解离后的单质铝与其它组分颗粒的复合机率,从而实现以更低能耗达到同等的解离效果。与现有技术相比,添加微量al(oh)cl2后可使解离速率提高30~70%,干磨能耗降低20~40%,设备尺寸减少1/3~2/3。
24.3)本发明采用湿式研磨不断脱除覆盖在活性组分颗粒表面的水解产物氢氧化铝,维持活性组分颗粒表面始终与水接触,可实现持续水解反应,直至活性组分完全水解,毒害组分完全浸出。随着研磨的进行,颗粒还会破碎,粒度越来越小,比表面积大幅增加,从而大幅增加水解和浸出速度和效率。因此,在整个水解和浸出过程中,无需添加酸或碱即可脱除颗粒表面的氢氧化铝覆盖层,与现有技术相比,经济运行成本降低1/3~2/3,环境性能改善1/3~2/3,大幅减少蒸发次数和后续废水处理难度,显著降低了对设备耐腐蚀性能方面的要求。
25.4)本发明在湿磨过程中加入微量al(oh)cl2可显著减少解离后的氢氧化铝覆盖层
与活性组分颗粒表面复合的机会,从而实现以更低能耗达到同等的水解效果。与现有技术相比,添加微量al(oh)cl2后可使水解速率提高30~70%,湿磨能耗降低20~40%,设备尺寸减少1/3~2/3。
26.5)本发明基于活性组分与水反应生成的混合气体组分(h2、ch4、nh3)均为还原性可燃气体的特性,采用直接燃烧方式全部实现混合气体的能源化。与现有技术相比,完全省去了氨吸收的操作单元及相应酸吸收剂,以及后续高能耗的蒸发结晶回收铵盐的复杂工序,大大简化了工艺流程,设备投资可减少20~30%,运行成本可降低20~40%。
27.6)本发明在常温条件下即可完成,勿需升温。与现有技术相比,进一步节约能耗20~40%。
28.7)本发明可以同时实现毒害元素氟、氯元素无害化率、资源化率达到100%,活性组分去除率、资源化和能源化率100%,惰化渣中氧化铝含量可达80%以上,可作为高品质铝土矿出售,即以资源化方式同时实现无害化。与现有技术相比,本发明具有显著的经济效益,可增加200~400元/吨的净收入,由负收益变成正收益。
附图说明
29.图1为本发明的工艺路线图。
具体实施方式
30.下面结合附图和具体实施例对本发明进行详细说明。
31.以下部分是具体实施方式对本发明做进一步说明,但以下实施方式仅仅是对本发明的进一步解释,不代表本发明保护范围仅限于此,凡是以本发明的思路所做的等效替换,均在本发明的保护范围。
32.实施例1
33.如图1所示,一种二次铝灰无害化处理方法,包括以下步骤:
34.1)在二次铝灰中添加1.00wt%的al(oh)cl2,进行干式研磨,研磨介质为直径0.5mm磨球,研磨时间为2h,通过粒级为0.4mm的筛分操作,提取筛上物单质铝颗粒,突破炒灰法等现有技术无法提5%以下单质铝的技术瓶颈,解离速率提高70%,干磨能耗降低40%,设备尺寸减少2/3;
35.2)在筛下物中添加1.00wt%的al(oh)cl2,进行湿式研磨,研磨介质为直径0.8mm的磨球,添加水为使筛下物与水混合后的固液比即铝灰/水固液比为0.30,研磨时间为2h,筛下物中的活性组分(残余单质铝、氮化铝、碳化铝)与水发生反应,生成的混合气体(氢气、氨气、甲烷)进行收集回收,可溶性组分(氯盐、氟盐)溶于浆相中,与现有技术相比,经济运行成本降低2/3,环境性能改善2/3,水解速率提高70%,湿磨能耗降低40%,设备尺寸减少2/3,大幅减少蒸发次数和后续废水处理难度,显著降低了对设备耐腐蚀性能方面的要求;
36.3)混合气体(氢气、氨气、甲烷)作为能源物质对外输出;
37.4)浆相经压滤分为清液和滤渣,滤渣成为惰性类铝土矿产品;
38.5)当清液中盐分达到6wt%以上,即电导率大于93ms/cm时,向溶液中加入cacl2,加入量以摩尔量计为铝灰中氟含量的1/2,搅拌生成的沉淀物过滤获得氟化钙产品,过滤后的液体以mvr蒸发结晶方式提取获得氯盐,水回用于湿磨。
39.本实施例在常温条件下即可完成,勿需升温,与现有技术相比,进一步节约能耗40%,并同时实现毒害元素氟、氯元素无害化率、资源化率达到100%,活性组分去除率、资源化和能源化率100%,惰化渣中氧化铝含量可达80%以上,可作为高品质类铝土矿出售,即以资源化方式同时实现无害化,与现有技术相比,本实施例具有显著的经济效益,可增加400元/吨的净收入,由负收益变成正收益。
40.实施例2
41.在二次铝灰中添加0.60%的al(oh)cl2,进行干式研磨,研磨介质为直径1.2mm磨球,研磨时间为1.2h,通过粒级为0.3mm的筛分操作,提取筛上物单质铝颗粒,突破炒灰法等现有技术无法提5%以下单质铝的技术瓶颈,解离速率提高50%,干磨能耗降低30%,设备尺寸减少1/3;在筛下物中添加0.60%的al(oh)cl2,进行湿式研磨,研磨介质为直径1.5mm的磨球,铝灰/水固液比为0.18,研磨时间为1.2h,筛下物中的活性组分(残余单质铝、氮化铝、碳化铝)与水发生反应,生成的混合气体(氢气、氨气、甲烷)进行收集回收,可溶性组分(氯盐、氟盐)溶于浆相中,与现有技术相比,经济运行成本降低1/3,环境性能改善2/3,水解速率提高50%,湿磨能耗降低30%,设备尺寸减少1/3,大幅减少蒸发次数和后续废水处理难度,显著降低了对设备耐腐蚀性能方面的要求;混合气体(氢气、氨气、甲烷)作为能源物质对外输出;浆相经压滤分为清液和滤渣,滤渣成为惰化类铝土矿产品;当清液中盐分达到6%以上,即电导率大于93ms/cm时,向溶液中加入cacl2,加入量以摩尔量计为铝灰中氟含量的1/2,搅拌生成的沉淀物过滤获得氟化钙产品,过滤后的液体以mvr蒸发结晶方式提取获得氯盐,水可回用于湿磨。本实施例在常温条件下即可完成,勿需升温,与现有技术相比,进一步节约能耗30%,并同时实现毒害元素氟、氯元素无害化率、资源化率达到100%,活性组分去除率、资源化和能源化率100%,惰化渣中氧化铝含量可达80%以上,可作为高品质类铝土矿出售,即以资源化方式同时实现无害化,与现有技术相比,本实施例具有显著的经济效益,可增加300元/吨的净收入,由负收益变成正收益。
42.实施例3
43.在二次铝灰中添加0.05%的al(oh)cl2,进行干式研磨,研磨介质为直径2.0mm磨球,研磨时间为0.5h,通过粒级为0.2mm的筛分操作,提取筛上物单质铝颗粒,突破炒灰法等现有技术无法提5%以下单质铝的技术瓶颈,解离速率提高30%,干磨能耗降低20%,设备尺寸减少1/3;在筛下物中添加0.05%的al(oh)cl2,进行湿式研磨,研磨介质为直径2.2mm的磨球,铝灰/水固液比为0.05,研磨时间为0.5h,筛下物中的活性组分(残余单质铝、氮化铝、碳化铝)与水发生反应,生成的混合气体(氢气、氨气、甲烷)进行收集回收,可溶性组分(氯盐、氟盐)溶于浆相中,与现有技术相比,经济运行成本降低1/3,环境性能改善1/3,水解速率提高30%,湿磨能耗降低20%,设备尺寸减少1/3,大幅减少蒸发次数和后续废水处理难度,显著降低了对设备耐腐蚀性能方面的要求;混合气体(氢气、氨气、甲烷)作为能源物质对外输出;浆相经吸滤分为清液和滤渣,滤渣成为惰化类铝土矿产品;当清液中盐分达到6%以上,即电导率大于93ms/cm时,向溶液中加入alcl3,加入量以摩尔量计为铝灰中氟含量的1/6,搅拌生成的沉淀物过滤获得冰晶石产品,过滤后的液体以mvr蒸发结晶方式提取获得氯盐,水可回用于湿磨。本实施例在常温条件下即可完成,勿需升温,与现有技术相比,进一步节约能耗20%,并同时实现毒害元素氟、氯元素无害化率、资源化率达到100%,活性组分去除率、资源化和能源化率100%,惰化渣中氧化铝含量可达80%以上,可作为高品质
类铝土矿出售,即以资源化方式同时实现无害化,与现有技术相比,本实施例具有显著的经济效益,可增加200元/吨的净收入,由负收益变成正收益。
再多了解一些
本文用于创业者技术爱好者查询,仅供学习研究,如用于商业用途,请联系技术所有人。