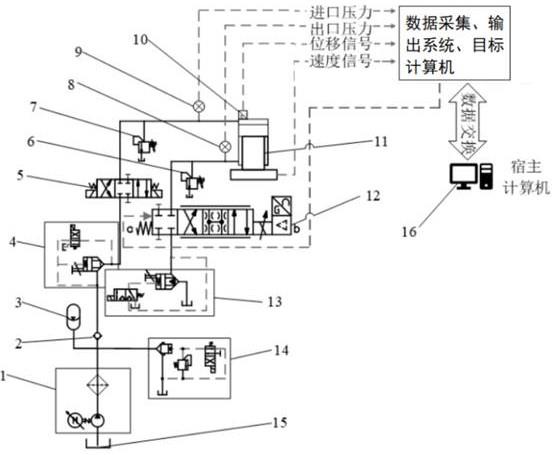
1.本发明属于液压成形装备技术领域,特别涉及大型液压成形装备快降运动曲线的平稳性设计与控制方法。
背景技术:
2.大型液压机活动横梁在下降过程中需快速的完成合模过程,以防止材料温度变化等原因造成成形质量的问题。目前大功率液压成形装备活动横梁快降过程存在速度突变,导致液压系统产生较大的冲击和偏载。针对冲击和偏载问题,国内外学者在液压系统结构、控制算法和运动曲线等方面进行了深入的研究。
3.在液压系统结构优化方面,已有研究学者对插装阀开度调节、增大卸载管路、蓄能器应用以及顶置式缓冲装置的仿真研究,在一定程度上取得了缓解冲击振动的效果。因此,对系统结构的优化研究能够减轻在活动横梁快降过程中的冲击和振动问题,但是传统结构优化方案对液压元件的控制性能要求较高。
4.在控制算法优化方面,已设计预测型多模式控制技术、ts 神经网络控制方案和径向基函数神经网络技术,均得到了相对较好地稳定性控制结果,但是仍然存在一定的跟踪误差,无法适应多变的生产环境。在此基础上,研究学者设计了一种基于smod的自适应反推终端滑模控制器,液压位置伺服控制的仿真验证中提高了系统的鲁棒性。综合分析不同控制算法的方案,实际生产中难以单独引用控制算法完成对活动横梁快降运动的控制过程,无法满足活动横梁快降运动的控制需求。
5.在运动曲线方面,du等在对活动横梁变速下落运动的研究中,首先分析了三次多项式运动轨迹,但是三次曲线对于速度骤变引起的冲击效果应对能力较差,不能彻底改善运动分析过程中产生的冲击问题。其次,利用多岛遗传算法对无冲击最速下降曲线进行优化,得到合理的五次曲线方程,有效地应对了在活动横梁快降中存在的冲击问题。上述研究表明,通过运动曲线的优化能够更好的减缓运动冲击,但是如何在减小冲击的同时提升快降速度、提高生产效率,仍有待进一步研究。
技术实现要素:
6.针对上述现有技术存在的问题,本发明的目地在于提供了大型液压成形装备快降运动曲线的平稳性设计与控制方法。以解决现有大功率液压成形装备活动横梁快降过程存在速度突变,导致液压系统产生较大的冲击和偏载的技术问题。
7.为了实现上述目的,本发明采用如下技术方案:本发明第一方面提供了大型液压成形装备快降运动曲线的平稳性设计结构,包括成形液压机的液压油路及控制系统,所述系统包括:泵组,用于对系统进行供油;单向阀,用于防止油流反向流动;蓄能器,用于储存多余能量,需要时释放能量;
第一插装阀组,用于在主油路中起到开关油路作用;电磁阀,用于控制油路通断;第一溢流阀:用于对回油管路起到溢流保护作用,其一端接在回油路,另一端接在油箱;第二溢流阀,用于对进油管路起到溢流保护作用,其一端接在进油路,另一端接在油箱;第一压力传感器,用于监测回油管路压力变化,其一端接在回油路,另一端接在控制计算机组;第二压力传感器,用于监测进油管路压力变化,其一端接在进油路,另一端接在控制计算机组;内置位移传感器,用于反馈液压缸的行程,其装在液压缸的内部,伸出信号线,接在控制计算机组;液压缸,用于作为液压系统执行机构;高频响电磁阀,用于精准控制回油管路流量,达到对液压缸行程的精准控制;第二插装阀组,用于在回油管路中起到泄压作用,其一端接在回油路,另一端接在油箱;第三插装阀组,用于当第一插装阀组关闭时,泵组未关闭状态下,对泵口进行回油控制,其一端接在进油路,另一端接在油箱;油箱,用于储存系统所需的液压油;控制计算机组,用于对反馈信息进行处理,并做出判断,控制电磁阀的通断,进而控制液压缸的速度。
8.本发明的第二方面提供了基于上述设计结构进行的大型液压成形装备快降运动曲线的平稳性控制方法,包括:s1、液压系统建模:设计成形液压机的液压油路及控制系统,所述系统的开环传递函数为下式(5)所示:(5)其中,;s2、采用五次样条曲线建立目标运动曲线函数,设计运动五次曲线运动模型,应用nsga-ii算法求得最佳活动横梁下降运动曲线;s3、设计自调整模糊 pid 控制器。
9.优选地,步骤s2中,所述设计运动五次曲线运动模型,应用nsga-ii算法求得最佳活动横梁下降运动曲线,具体步骤为:a21、根据设置的条件及参数,列出如下述公式(6)的五次多项式曲线一般表达式和下述公式(7)的优化约束方程组:
(6)(7)其中,a0、a1、a2、a3、a4和a5为多项式系数,t为活动横梁运动总时间,y为活动横梁运动位移,v为活动横梁运动速度,a为活动横梁运动加速度,j为活动横梁运动惯量;式7中,以最短运动时间和最小冲击为优化约束条件;a22、根据运动起点状态和终点状态对五次曲线的优化初始条件进行如下设置:起点条件:y(t0)=y0(m),v(t0)=v0(m/s),a(t0)=a0(m/s2),j(t0)= j0(m/s3);终点条件:y(ts)=ys(m),v(ts)=vs(m/s),a(ts)=as(m/s2),j(ts)=js(m/s3)其中,t0为起点时间,ts为运动终点时间,为需要优化的参数之一;y0、v0、a0为起点处的位移、速度、加速度和加加速度,相对应的ys、vs、as以及js为运动终点处的位移、速度、加速度和加加速度。
10.a23、给出合理的约束条件,优化求解:假设活动横梁在理想极限状态下做自由快降运动,并根据参数数据设置五次曲线优化的状态约束条件,根据已知系统参数初步对最大加速度、最大速度进行求解,相关参数的求解过程如下式(8)所示:(8)
其中,f为油缸活塞杆所受的滑块重力(n),f1为快降时进油口的负压对活塞的拉力(n),f2为快降时出油口处产生的压力反作用力(n),f为活塞杆运动时所受阻力(n),m为滑块质量(kg),a1为活动横梁下落过程中的平均加速度(m/s2),t1为下降时间(s),s为标定下降位移(m),g设为10m/s2,p1为油缸进油口的压强(mpa),a1为进口活塞面积(m2),p2为油缸出油口的压强(mpa),a2为出油口活塞杆底部与油液接触面积(m2),fc为油缸粘性摩擦系数,v1为活塞杆运动速度(m/s)。f3为减速时油缸出油口对活塞杆的最大反作用力(n),f '为减速时油缸所受最大摩擦力(n),a2为活塞杆的最大减加速度(m/s2);其中,p3位油缸出油口所受最大压强(mpa)。
11.优选地,步骤s3中,所述自调整模糊 pid 控制器由pid和模糊逻辑控制器两个模块并联组成,其中以位移误差和误差变化率作为输入,经模糊逻辑控制器输出实时k
p
、kd和ki,以位移误差建立pid模块与模糊逻辑控制器的相互作用。
12.优选地,还包括:amesim和simulink联合仿真对快降运动曲线设计与控制的有效性进行验证,具体步骤包括:在amesim中构建液压系统的仿真模型,同时在simulink中建立设计控制系统,并针对控制方案设置pid对照组进行仿真测试;针对建立的模型、约束条件和已知参数选取相应的求解方案,对曲线模型进行优化;采取nsga-ii算法计算最快速度、最小冲击和最短时间条件的最优解,获得最优解坐标曲线。
13.优选地,还包括:对仿真模拟分析结果的正确性和有效性进行验证。
14.本发明具备如下有益效果:本发明通过分析活动横梁快降时液压系统的动力学特点,提出了基于五次曲线的快降运动规律设计方法,以平均速度最大与冲击最小为约束,应用nsga-ii算法求解最优运动曲线,开发了基于模糊pid的运动曲线跟踪控制策略。通过仿真和实验研究,验证了快降运动曲线设计与控制的有效性,结果表明,活动横梁快降运动过程中的冲击得到了有效缓解,降低幅度达21%,本发明对大型液压装备的研发和平稳性控制具有重要的理论和应用价值。
附图说明
15.为了更清楚地说明本发明实施例中的技术方案,下面将对实施例中所需要使用的附图作简单地介绍,显而易见地,下面描述中的附图仅仅是本发明的一些实施例,对于本领域普通技术人员来讲,在不付出创造性劳动的前提下,还可以根据这些附图获得其他的附图。
16.图1为活动横梁下降运动曲线的运动位移图;图2为本发明设计的成形液压机的液压油路及控制系统的示意图;图3为液压伺服系统位移反馈的方块图;图4为高频响比例伺服阀控液压缸控制系统传递方框图;图5为模糊pid控制器作用的流程图;图6为仿真控制系统的原理图;图7为活动横梁快降运动曲线图;图8为位移跟踪曲线图;图9为跟踪误差曲线图;
图10为pid控制器和模糊pid控制器下运动速度对比图;图11为pid控制器和模糊pid控制器下加速度对比图;图12为pid控制器和模糊pid控制器下出油口压力对比图;图13为位移跟踪实验分析结果中的位移跟踪效果图;图14为位移跟踪实验分析结果中的速度曲线图;图15为位移跟踪实验分析结果中的加速度曲线图。
17.附图标记:1、泵组;2、单向阀;3、蓄能器;4、第一插装阀组;5、电磁阀;6、第一溢流阀;7、第二溢流阀;8、第一压力传感器;9、第二压力传感器;10、内置位移传感器;11、液压缸;12、高频响电磁阀;13、第二插装阀组;14、第三插装阀组;15、油箱;16、控制计算机组。
具体实施方式
18.以下描述中,为了说明而不是为了限定,提出了诸如特定系统结构、技术之类的具体细节,以便透彻理解本发明实施例。然而,本领域的技术人员应当清楚,在没有这些具体细节的其它实施例中也可以实现本发明。在其它情况中,省略对众所周知的系统、装置、电路以及方法的详细说明,以免不必要的细节妨碍本发明的描述。
19.实施例1参照图1,大功率液压成形装备中活动横梁的运动过程基本分为七个阶段,其中t1至t2为快降阶段、t2至t3为减速阶段、t3至t4为工进阶段、t4至t7为压制及保压阶段其次 t7至 t
10
分别为开模、快速回程和减速阶段。由于传统方案的活动横梁运动过程中设置多处减速点,使活动横梁在t4时达到合适的压制速度,但是活动横梁存在较大的惯性,会在速度拐点处产生较大冲击。因此,为了减轻运动冲击,本发明选择难以解决的快降起点至合模阶段的液压系统进行分析。
20.具体地,参照图2,为了在活动横梁快速下降过程中对运动曲线实现精准控制,本发明提供了大型液压成形装备快降运动曲线的平稳性设计结构,包括成形液压机的液压油路及控制系统,该系统包括:泵组1,用于对该系统进行供油;单向阀2,用于防止油流反向流动;蓄能器3,用于储存多余能量,需要时释放能量;第一插装阀组4,用于在主油路中起到开关油路作用;电磁阀5,用于控制油路通断;第一溢流阀6:用于对回油管路起到溢流保护作用,其一端接在回油路,另一端接在油箱15;第二溢流阀7,用于对进油管路起到溢流保护作用,其一端接在进油路,另一端接在油箱15;第一压力传感器8,用于监测回油管路压力变化,其一端接在回油路,另一端接在控制计算机组16;第二压力传感器9,用于监测进油管路压力变化,其一端接在进油路,另一端接在控制计算机组16;内置位移传感器10,用于反馈液压缸11的行程,其装在液压缸11的内部,伸出信号线,接在控制计算机组16;液压缸11,用于作为液压系统执行机构;高频响电磁阀12,用于精准控制回油管路流量,达到对液压缸11行程的精准控制;第二插装阀组13,用于在回油管路中起到泄压作用,其一端接在回油路,另一端接在油箱15;第三插装阀组14,用于当第一插装阀组4关闭时,泵组1未关闭状态下,对泵口进行回油控制,其一端接在进油路,另一端接在油箱15;油箱15,用于储存系统所需的液压油;控制计算机组16,用于对反馈信息进行处理,并做出判断,控制电磁阀5的通断,进而控制液压缸11的速度。这里,本发明在回油路上设置高频响电磁阀12,能够精确控制油路中的流量大小;采用内置位移传感器10的液压缸11由电脑处理位移信号并输出控制信
号,可实现对活动横梁下降过程中速度和压力的实时稳定控制。
21.本发明实施例还提供了基于上述设计结构进行的大型液压成形装备快降运动曲线的平稳性控制方法,包括以下步骤:s1、液压系统建模:基于设计的成形液压机的液压油路及控制系统,分析活动横梁快降时液压系统的动力学特点。
22.具体地,在活动横梁快降过程中无负载力作用,得出上述液压伺服系统的方块图,如图3所示。系统结合相关参数,将常用电液伺服阀近似的二阶振荡系统,其中电液伺服阀的开环传递函数如下式(1)所示:(1)其中,k
sv
为伺服阀的流量增益,g
sv
为k
sv
=1时的伺服阀传递函数,为伺服阀的固有频率,为伺服阀的阻尼比,s取值0.7。
23.根据实况分析,活动横梁快降过程中外负载为0,根据分析可得液压缸位移x
p
对阀的输入指令xv的传递函数为下式(2)所示:(2)其中,kq为流量系数,a
p
为液压缸活塞有效面积,为液压缸固有频率,为液压阻尼比,一般取值0.1~0.2。
24.此外,伺服放大器的电流与输入电压ug近似成比例,采用伺服比例放大器增益ka表示,具体如下式(3)所示:(3)其中,可建立位移传感器增益kf的数学模型,如下式(4)所示:(4)其中,if为反馈电流信号,v;y为液压缸活塞位移,m。
25.最终,通过上述式(1)至式(4),推出高频响比例伺服阀控液压缸控制系统传递方框图,如图4所示。
26.由图4结果可知,系统开环传递函数为下式(5)所示:
(5)其中,。
27.s2、利用五次样条曲线建立目标运动曲线函数,设计运动五次曲线运动模型,求得最佳活动横梁下降运动曲线;具体地,根据设置的条件及参数,列出如下述公式(6)的五次多项式曲线一般表达式和下述公式(7)的优化约束方程组:(6)(7)其中,a0、a1、a2、a3、a4和 a5为多项式系数,t为活动横梁运动总时间,y为活动横梁运动位移,v为活动横梁运动速度,a为活动横梁运动加速度,j为活动横梁运动惯量;式7中,以最短运动时间和最小冲击为优化约束条件。
28.根据图2所示活动横梁下降运动曲线的运动特点可知,在快速下降过程中所设计的五次曲线分为变加速和变减速运动两个阶段。根据运动起点状态和终点状态对五次曲线的优化初始条件进行如下设置:起点条件:y(t0)=y0(m),v(t0)=v0(m/s),a(t0)=a0(m/s2),j(t0)= j0(m/s3);终点条件:y(ts)=ys(m),v(ts)=vs(m/s),a(ts)=as(m/s2),j(ts)=js(m/s3) 。
29.其中,t0为起点时间,ts为运动终点时间,为需要优化的参数之一。y0、v0、a0为起点处的位移、速度、加速度和加加速度,相对应的ys、vs、as以及js为运动终点处的位移、速度、加速度和加加速度。
30.为了实现得到最优解的结果,需要给出合理的约束条件,进行优化求解。具体地,假设活动横梁在理想极限状态下做自由快降运动,并根据参数数据设置五次曲线优化的状态约束条件。根据已知系统参数初步对最大加速度、最大速度进行求解,相关参数的求解过程如下式(8)所示:
(8)其中,f为(液压缸)油缸活塞杆所受的滑块重力(n),f1为快降时进油口的负压对活塞的拉力(n),f2为快降时出油口处产生的压力反作用力(n),f为活塞杆运动时所受阻力(n),m为滑块质量(kg),a1为活动横梁下落过程中的平均加速度(m/s2),t1为下降时间(s),s为标定下降位移(m),g设为10m/s2,p1为油缸进油口的压强(mpa),a1为进口活塞面积(m2),p2为油缸出油口的压强(mpa),a2为出油口活塞杆底部与油液接触面积(m2),fc为油缸粘性摩擦系数,v1为活塞杆运动速度(m/s);f3为减速时油缸出油口对活塞杆的最大反作用力(n),f '为减速时油缸所受最大摩擦力(n),a2为活塞杆的最大减加速度(m/s2);其中,p3位油缸出油口所受最大压强(mpa)。
31.s3、设计自调整模糊pid控制器;为了研究上述运动模型对减小快降冲击、提高位移精度和克服非线性运动效果,本发明设计了自调整模糊pid控制器。其良好自适应特性、结构简单和工作稳定的模糊pid控制器能够弥补pid控制器的不足,能够与系统和运动模型匹配。研究中设计的模糊pid控制器分为pid和模糊逻辑控制器两个模块,如图5所示。其中以位移误差和误差变化率作为输入,经模糊逻辑控制器输出实时k
p
、kd和ki。以位移误差建立pid模块与模糊逻辑控制器的相互作用。
32.已知在研究的系统中模糊控制器直接影响的对象为高频响阀。此时,需要通过模糊pid控制器的特性分辨位移误差和误差变化率与设定模糊控制器输出值的关联。然后,根据相应的控制要求完成对模糊规则设定和输出参数的量化。其中,模糊规则决定这模糊控制器运行的质量,不同的运动情况需要具体设置特定的模糊规则。为了实现搞精度的控制,系统的模糊规则设定,如下表1所示。
33.表1. k
p
、ki、kd模糊规则
实施例2通过仿真和实验对实施例1中的设计方案进行验证。
34.(一)、通过amesim和simulink联合仿真对实施例1中的设计方案进行验证;(1)如下表2所示,为仿真系统的结构。
35.表2.主要液压元件及其参数根据图2液压系统的原理图,在amesim中构建液压系统的仿真模型,具体液压元件型号及仿真参数设定如表2。同时在simulink中建立设计控制系统,控制系统建模如图6所示。并针对控制方案设置pid对照组。通过软件结合,进行仿真测试。
36.此外,结合控制系统设计及活动横梁运动范围参数,最终设定模糊控制器的输入跟踪误差e和误差变化率ec的量化论域为(-0.6,-0.4,-0.2,0,0.2,0.4,0.6)。在实验仿真中得出输出变量比例系数k
p
、积分系数ki和微分系数kd的量化论域。k
p
为(0,5,10,15,20,25,30)。ki为(0,0.09,0.17,0.25,0.33,0.5)。kd为(0,0.05,0.1,0.15,0.20,0.25,0.3)。其次,量化因子是对误差e和误差变化率ec的转化参数,参照油缸行程的设定0.6m,可以得出ke=0.6/0.6,k
ec
=0.6/0.6。
37.(2)曲线优化求解针对建立的模型、约束条件和已知参数选取相应的求解方案,对曲线模型进行优化。经过对现有求解方法的对比分析,本发明实施例采取nsga-ii算法求解方程的最佳解。其中,由活动横梁的运动情况可知,y0=0(m);v0=0(m/s);a0=0(m/s2);t0=0(s);ys=0.6(m);a
max
=6(m/s2)。
38.(3)仿真结果分析根据优化的结果分析,五次曲线运动模型很好的达到了设计要求,得到了满足最快速度、最小冲击和最短时间条件的最优解,最优解坐标曲线如图7所示。
39.在仿真过程中,系统响应对运动曲线优化后的理想五次曲线的跟踪如图8所示,跟踪误差如图9所示。在仿真系统中,在0.8s内,活动横梁位移曲线都存在一定的波动,但其波动误差较小且均在2-10mm内。由图8结果可知,在1.4s后,位移误差逐渐稳定减小。其中,pid控制器作用下的终止误差为3.02mm,模糊pid控制器作用下的终止误差仅为1.7mm。
40.因此,仿真分析有效地体现了五次曲线优化后的模型可以得到很好的系统控制跟踪效果和响应速度,能够满足设计中对系统运行提出的速度和稳定性的要求,且模糊pid的控制精度相对于pid控制器提高了43.7%。
41.参照图10至图12,在仿真过程中,经过优化后的运动模型的振动幅度明显小于传统运动控制方案。其中模糊pid和pid控制器作用下的最大速度波动分别提高了60%和40%,尤其是在1.4秒以后,在相应控制器的作用下,优化后的运动模型速度和加速度均在稳定减小,不存在如传统方案中的终止速度突变现象。
42.其次,由图12结果可知,在活动横快降运动至减速的阶段,传统方案中存在1000bar的压力突变波动,而优化后的模型在0-1.4s内的压力波动最大仅为450bar且无突变性波动,最短波动时间为0.04s。因此,优化后的模型不仅能够有效地减少冲击振动,还能够与传统pid和模糊pid控制器稳定匹配并运行。
43.此外,相对于传统pid控制,模糊pid控制器作用下,活动横梁运动速度波动提升了33.3%,速度精度提升了2.9%。并且由图12结果可知,模糊pid控制器作用下的运动过程,压力波动更小,且在1.6s之后,综合压力值明显小于pid控制器。最重要的是,在终止运动后,pid控制器作用下的压力值为300bar,模糊pid控制器中的压力值仅为230bar,保证了在合模过程中不会因压力过大而产生模具偏移。因此,优化后的运动曲线在模糊pid控制器的配合下,具有高运动精度和低冲击振动的效果。
44.(二)、通过实验对实施例1中的设计方案进行验证;(1)搭建了液压成形装备试验台,同时在实验中设置pid和模糊pid控制系统对照组,分别应用于曲线的运动控制:为了进一步研究验证优化后的运动曲线模型仿真分析的正确性和有效性,本发明搭建了液压成形装备试验台,其液压元件及其相关参数见表2。通过对主缸进行位移控制,完成对理想五次运动曲线的跟踪。液压机还设置了压力传感器和速度传感器等。这些传感器安装在液压机框架及回油路中,用于监控系统的运行状态。此外,控制系统集成在电气柜和控制台中,主要由个人计算机、工控机、采集卡以及输出卡等组成。其中,个人计算机作为主控计算机通过网线与作为目标计算机的工控机进行tcp/ip数据交换。
45.(2)位移跟踪实验分析实验结果如图13至图15所示。其中,t为运动时间,s为活动横梁的位移,v为活动横梁运动速度,a为活动横梁的运动加速度。本发明实施例中实验选用两种控制方案分别匹配运动模型进行验证。
46.由图13至图15结果可知,在两种控制器情况下,活动横梁在0.87s运动时间内都存在振动现象。其中,模糊pid控制器为减少活动横梁振动现象,使整体位移参数均大于理想
位移参数,但是其误差在0-23.15mm内,并逐渐趋于0;pid控制器在此时间内的位移误差范围为0-16.9mm,并逐渐趋向于0。
47.其次,0.8s后在两种控制器作用下的实际位移曲线逐渐趋于平稳,且在1.9s-2s时仍然能够稳定的减少位移误差。最终,pid控制器终止运动时的位移误差为4.02mm(3.775%),模糊pid控制器位移终止误差仅为2.7mm(2.825%)。此处由于仿真模型是较为理想的,不存在结构问题,因此实验误差大于仿真误差约1mm。但是,此模型位移精度实验结果仍比传统方案提高约20%。
48.再有,在0.8s之前速度波动较大,但均收敛于五次运动曲线。且运动速度在1.2s以后,不但能够以较高的速度运动,而且波动明显减少。其中,1.6s以后速度稳定减小,pid控制器位移终止速度误差为14.2%,模糊pid控制器速度误差为10.8%。此外,通过图11的出油口压力检测数据分析,系统中造成振动冲击的压力数值减少了20%。
49.(三)仿真和实验结果分析:(1)系统平稳性提升分析通过仿真和实验分析可知,与传统的活动横梁运动模型相比,优化后的模型以五次多项式运动曲线模型较好的消除了运动过程中的速度突变问题。在活动横梁快降运动的过程中,该运动模型在最大程度上消除了速度突变带来的冲击和振动问题。同时,以工控机simulink realtime平台在模糊pid控制器和高频响阀的配合下能够完成较好的生产应用,为更先进的控制算法的应用打下了基础。
50.(2)控制器应用分析如图13至图15所示,在活动横梁运动过程中,0-0.8s 内,两种控制器作用下的运动都存在一定的波动。但是在模糊 pid 控制器的作用下,位移波动误差相对于pid 控制器减小了 7.25mm,同时为了避免活动横梁启动时由于自身惯性较大产生大范围速度波动,在 0.8s 内模糊 pid 控制器允许运动位移超前,达到减少速度波动的目的。其次,由上述图表可以得出,与pid控制器对比,模糊pid控制器的误差精度更小。其中,终止位移精度提升了1.32mm (44%),速度精度提升了0.06m/s
2 (2.9%)。减少了20%。通过仿真和实验分析可知,模糊pid控制器能够弥补活动横梁下降过程中的非线性冲击振动和存在较大误差的问题。
51.综上,为了解决活动横梁快降过程中的冲击和振动问题,本发明提出了基于五次运动曲线规律的平稳性控制方法,仿真和实验结果均表明运动冲击和振动明显减小,可实现活动横梁无冲击的、可控的非线性运动。最终,活动横梁位移跟踪效率达到97%,振动冲击减缓了21%,有效提升大功率液压成形装备快降的生产质量和使用寿命。因此,本发明方法能够对现有大型液压机的设计和平稳性控制提供有效参考,且经过不断的改进,能够满足更为苛刻的工艺要求,促进高精度和高稳定性能液压机的发展。
52.本发明不局限于上述具体的实施方式,本领域的普通技术人员从上述构思出发,不经过创造性的劳动,所做出的种种变换,均落在本发明的保护范围之内。
再多了解一些
本文用于创业者技术爱好者查询,仅供学习研究,如用于商业用途,请联系技术所有人。