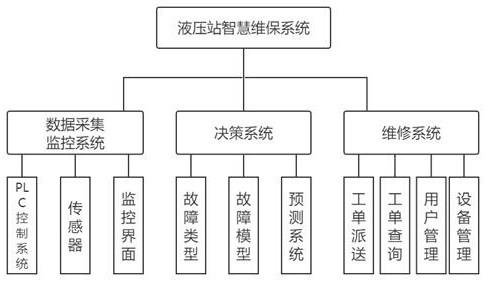
1.本发明涉及一种液压站维修保养系统及流程,特别是涉及一种钢厂液压站智慧维修保养系统及工作流程。
背景技术:
2.液压系统大量存在于冶金钢厂中,是重要的动力源,通常由液压泵组、油箱、过滤器、控温组件等组成,液压油的好坏直接关系到钢厂设备的可靠性和使用寿命。液压用油切忌不同牌号的液压油混合使用,且工作温度要在工艺要求的温度范围。混油会导致油性能下降,产生沉淀物,油温过高加速油品老化变质失效,因此,必须定期换油。目前钢铁厂液压的故障多集中在漏油、跳泵、油温突变、液位突变等方面。主要因素是油品污染导致阀门动作不到位、油品劣化、泵输出压力不稳定、日常慢泄露等,漏油还导致液压站周边环境油腻、脏兮兮,易发生火灾、爆炸等危险。由于液压油属消耗品,且价格较高,目前钢厂普遍存在混油现象,对液压设备的管理大多仍采用点检定修,加多少油、何时加油都凭检修工人经验,存在极大的安全隐患和不规范性。同时,缺少历史数据尤其是故障时的数据参考和维修专家系统指导,导致,故障原因排查慢、维修效率低、工期长。目前维修都是故障维修和定期维修,没有预防维修。换句话说,定期维修是健康体检,故障维修是得病了才找医生,而预防维修是治未病。健康体检的定期维修固然重要,但没有发生故障时的数据,对故障类型判断和维修起不到大作用;得病了才找医生的故障维修是故障问题已出现,已经造成了停车、停产事实,维修是亡羊补牢,维修越快越减少损失。治未病的预防维修是基于数据的故障预测、提前预警、事前预防,利用数据分析及早发现危险隐患,避免和降低出现故障机率,是现代化维修的发展方向。因此,设计一种钢厂液压站智慧维保系统,对液压油的污染度、黏度、油位、油温等参数进行实时在线监测,并在系统平台上布置状态预警模型对故障进行趋势预判,根据人工智能算法对油温等参数进行精准分析,能够对运行状态进行故障提前预判,达到预防性维护的目的。
技术实现要素:
3.本发明的目的在于提供一种钢厂液压站智慧维修保养系统及工作流程,本发明数据采集监控系统是基于plc技术的监控系统,液压油的污染度、黏度、油位、油温等参数通过传感器采集并传给plc,实现在上位机监控界面实时显示、控制等。决策系统是结合智能算法、大数据技术等搭建智能决策平台,利用油液分析数据,按机器学习线性回归算法形成系统故障模型,并利用模型预测系统故障。维修系统是集用户管理、设备管理、维修工单管理、操作日志管理于一体的数据库管理系统,上述系统实现了对液压站设备的维修和保养记录、派单、管理等。
4.本发明的目的是通过以下技术方案实现的:一种钢厂液压站智慧维修保养系统,所述系统包括数据采集监控系统、决策系统和维修系统;数据采集监控系统是由plc控制系统、传感器、监控界面组成;系统中液压油的
污染度、黏度、油位、油温参数通过传感器采集并传给plc,实现在上位机监控界面实时显示、控制;决策系统是结合智能算法、大数据技术等搭建智能决策平台,分析plc采集的数据,形成系统故障模型,并利用预测系统判断故障类型;维修系统是集用户管理、设备管理、工单管理于一体的数据库管理系统;实现对维修人员和液压站设备的维修和保养记录、工单派送和查询管理。
5.一种钢厂液压站智慧维修保养系统工作流程,所述系统工作流程包括以下步骤:温度、压力、液位、流量、颗粒度传感器将液压油温度、压力、油位、流量、污度及黏度参数采集上传到plc,plc系统判断这些参数是否超过工艺允许范围;如果参数超标,则由上位机监控立即报警,同时启动维修系统,下达维修命令;系统依据超标参数特征,判断故障类型,确定维修方案,直至维修结束;如果plc判断数据参数未超过工艺允许范围,则决策系统中的预测系统工作,根据预测模型判断当前数据是否是危险状态,判断系统是否发生故障;若根据预测系统模型判断发生故障,则上位机立即报警,同时启动维修系统,做到危机状态的紧急救治维护;若预测系统模型判断无故障,则表明系统稳定且远离危险,正常工作。
6.所述的一种钢厂液压站智慧维修保养系统及工作流程,所述钢厂液压站智慧维保系统上位机监控界面将液压站各传感器数据实时显示和记录,查询历史数据及趋势;历史数据为决策系统提供训练样本,有利于对液压站整体状况进行分析与评估;监控界面支持访问维修系统,有用户登录界面和设备管理、维修界面;每个设备的故障信息、维保次数及进度,以及维修人员信息等都建立台账,方便查询和访问;上位机界面设置报警界面,在故障时会弹出故障提示,且有指示灯闪烁,以便于维保人员及时发现异常并参与维修。
7.所述的一种钢厂液压站智慧维修保养系统及工作流程,所述钢厂液压站智慧维修保养系统设有人工神经网络模型架构,液压系统通过传感器采集如流量、压力、温度等数据传给plc,在上位机的决策系统进行数据分析,建立一套参数预测系统;预测系统是利用神经网络技术在大量数据基础上训练模型,使模型有较好的泛化性;用训练好的模型用以评估液压站发生故障的概率; 压力、温度、流量、油位、污度、黏度等共计16个液压站采集数据,作为输入层;输出层使用5个不同的神经元分别表示不同的风险等级,故障发生概率定义为风险,风险非常高认为故障发生概率非常高;风险高认为故障发生概率高;风险中等认为故障发生概率中等;风险低认为故障发生概率低;风险非常低认为故障发生概率非常低;在人工神经网络模型中,污度、黏度、油位、油温、压力、流量等这些参数进行加权,用以计算液压站故障发生概率。
8.本发明的优点与效果是:本发明设计开发钢厂液压站智慧维保系统及工作流程,实时监测油品数据并对危险状态实施预警,提前对故障进行趋势预判,达到预防性维护的目的。钢厂液压站智慧维保系统智能实现设备定期维保提醒和维保计划,对正在维保的设备可展示维护保养的进度,每阶段维保后智能更新信息到数据库。智能维保系统能够有效的提升现阶段维保方案的智能化水平,减小故障停机率以及维护不到位的隐患,提高了液压站生产线的经济效益,对我国未来维保及工控行业的智能化发展及无人化运维平台的构建具有重要的意义。
附图说明
9.图1为本发明一种钢厂液压站智慧维保系统组成示意图;
图2为本发明系统工作流程图;图3为本发明监控系统界面图;图4为本发明神经网络模型架构图。
具体实施方式
10.下面结合附图所示实施例对本发明进行详细说明。
11.本发明钢厂液压站智慧维保系统包括数据采集监控系统、决策系统和维修系统三部分。
12.如图1所示,本发明钢厂液压站智慧维保系统包括:1、数据采集监控系统2、决策系统3、维修系统。数据采集监控系统是由plc控制系统、传感器、监控界面组成。液压油的污染度、黏度、油位、油温等参数通过传感器采集并传给plc,实现在上位机监控界面实时显示、控制等。决策系统是结合智能算法、大数据技术等搭建智能决策平台,分析plc采集的数据,形成系统故障模型,并利用预测系统判断故障类型。维修系统是集用户管理、设备管理、工单管理于一体的数据库管理系统。实现对维修人员和液压站设备的维修和保养记录、工单派送和查询管理等。
13.见图2,本发明钢厂液压站智慧维保系统工作流程。具体步骤是温度、压力、液位、流量、颗粒度等传感器将液压油温度、压力、油位、流量、污度及黏度等参数采集上传到plc,plc系统判断这些参数是否超过工艺允许范围。如果参数超标,则由上位机监控立即报警,同时启动维修系统,下达维修命令。系统依据超标参数特征,判断故障类型,确定维修方案,直至维修结束。如果plc判断数据参数未超过工艺允许范围,则决策系统中的预测系统工作,根据预测模型判断当前数据是否是危险状态,判断系统是否发生故障。若根据预测系统模型判断发生故障,则上位机立即报警,同时启动维修系统,做到危机状态的紧急救治维护。若预测系统模型判断无故障,则表明系统稳定且远离危险,正常工作。
14.见图3,本发明钢厂液压站智慧维保系统上位机监控界面。界面将液压站各传感器数据实时显示和记录,可查询历史数据及趋势。历史数据为决策系统提供训练样本,有利于对液压站整体状况进行分析与评估。监控界面支持访问维修系统,有用户登录界面和设备管理、维修界面。每个设备的故障信息、维保次数及进度,以及维修人员信息等都建立台账,方便查询和访问。上位机界面设置报警界面,在故障时会弹出故障提示,且有指示灯闪烁,以便于维保人员及时发现异常并参与维修。
15.见图4,本发明钢厂液压站智慧维保系统人工神经网络模型架构。液压系统通过传感器采集如流量、压力、温度等数据传给plc,在上位机的决策系统进行数据分析,建立一套参数预测系统。预测系统是利用神经网络技术在大量数据基础上训练模型,使模型有较好的泛化性。用训练好的模型用以评估液压站发生故障的概率。 压力、温度、流量、油位、污度、黏度等共计16个液压站采集数据,作为输入层。输出层使用5个不同的神经元分别表示不同的风险等级,故障发生概率定义为风险,风险非常高认为故障发生概率非常高;风险高认为故障发生概率高;风险中等认为故障发生概率中等;风险低认为故障发生概率低;风险非常低认为故障发生概率非常低。在人工神经网络模型中,污度、黏度、油位、油温、压力、流量等这些参数进行加权,用以计算液压站故障发生概率。
再多了解一些
本文用于创业者技术爱好者查询,仅供学习研究,如用于商业用途,请联系技术所有人。