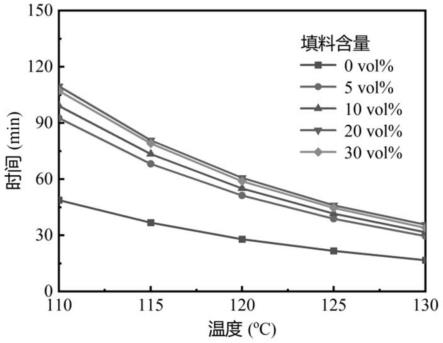
1.本发明属于高电压与绝缘材料技术领域,尤其是涉及一种高导热球形氮化硼复合环氧树脂的固化方法。
背景技术:
2.高导热环氧树脂复合绝缘材料是开发高电压、大容量干式电力设备的基础。填充六方氮化硼的复合环氧树脂具有介电常数低、击穿强度高等优点,但传统片状六方氮化硼复合环氧树脂存在浆料粘度高、导热性能不足等问题。球形氮化硼复合环氧树脂在保持了环氧树脂良好机械和绝缘性能的前提下,有效增强了其导热性能,在电力设备绝缘领域中有着广阔的应用前景。
3.环氧树脂复合材料的绝缘性能、机械特性与固化工艺参数密切相关。在固化过程中,环氧树脂释放大量的固化反应热形成自催化效应。因此,绝缘部件成型过程中会面临温度分布不均匀、内部固化程度不一致产生内应力,导致复合材料出现开裂等现象。深入分析多因素对复合材料固化过程的影响规律,选择合适的固化工艺参数,严格控制固化生产过程,对改善产品质量具有重要意义。
4.固化动力学模型参数包括表观活化能,指前因子和反应级数等,动力学模型分析也即是选择合适的反应模型与“动力学三因子”的求解的过程。表观活化能表示环氧树脂基团之间发生有效碰撞反应所需的能量,其数值大小反映了环氧树脂固化交联的难易程度。但只有选择合适的反应模型,进而才能准确的指导、预测环氧树脂的固化过程,且目前现有技术方案中没有考虑到加入填料的复合环氧树脂的固化工艺。
5.中国专利文献(cn 110197009 a)公开了一种树脂基复合材料固化反应的预测方法。本发明利用树脂基复合材料预浸料的动态差示扫描量热试验数据,对n级固化反应动力学模型和自催化固化反应动力学模型进行非线性拟合,得到树脂基复合材料固化反应动力学模型;再利用所得树脂基复合材料固化反应动力学模型对树脂基复合材料的固化过程进行预测。本发明提供的上述预测方法同时保留了n级固化反应动力学模型和自催化固化反应动力学模型的反应级数,使所得动力学模型能够准确的拟合树脂基复合材料的固化趋势。但该技术方案中没有考虑加入填料的复合环氧树脂的固化工艺的预测优化。
技术实现要素:
6.本发明的目的是提供一种高导热球形氮化硼复合环氧树脂的固化方法,通过选择合适的反应模型,且加入了填料,考虑更全面,进而准确的指导、预测环氧树脂的固化过程,为高导热球形氮化硼复合环氧树脂的制备过程提供了优化固化工艺的方法。
7.为解决上述技术问题,本发明采用的技术方案是,该高导热球形氮化硼复合环氧树脂的固化方法,具体包括以下步骤:
8.s1:选择球形氮化硼复合环氧树脂体系并制备相应的高导热球形氮化硼复合环氧树脂;
9.s2:通过固化度和固化反应热之间的线性函数关系,得到加入填料的动态固化特性关系;
10.s3:通过加入不同含量的填料,通过加入填料的动态固化特性关系,获得固化动力学模型及参数,并得到变化趋势;
11.s4:验证变化趋势的准确性,再根据变化趋势获得高导热球形氮化硼复合环氧树脂在不同填料含量中的最佳固化工艺。
12.采用上述技术方案,将复合环氧树脂的填料参数加入了固化工艺中,阐述了在不同填料含量下的优化固化工艺方法,研究了不同填料含量球形氮化硼复合环氧树脂的固化工艺,建立了不同填料含量球形氮化硼复合环氧树脂的非等温固化动力学模型,获得了填料含量对环氧树脂固化行为的影响规律,获得了不同填料含量的高导热球形氮化硼复合环氧树脂的优化固化工艺,降低固化过程中的内应力,为改善球形氮化硼复合环氧树脂的质量提供全面理论指导。
13.作为本发明的优选技术方案,所述步骤s1中的球形氮化硼复合环氧树脂体系选择双酚a型(cyd-128)环氧树脂作为基体,脂环族树(celloxide 2021p)为活性稀释剂;甲基六氢邻苯二甲酸酐为固化剂,所述填料包括球形氮化硼和/或球形氧化铝;所述步骤s3中加入填料的含量为0~30vol%。球形氮化硼可有效降低浆料粘度,减少环氧树脂内部气泡和界面缺陷,多尺度球形填料可协同提升复合环氧树脂的导热性能,适量的小尺寸颗粒“桥接”大尺寸填料有助于形成导热网络。
14.作为本发明的优选技术方案,所述步骤s2的具体步骤为:采用差示扫描量热仪对环氧-酸酐体系进行动态dsc升温测试并进行监测,得到不同升温速率β下固化度随反应温度的变化规律;从而获得环氧树脂固化度和固化反应热存在线性关系,其关系表达式为:
[0015][0016]
式中,α是t时刻环氧树脂的固化度,q
tol
是该升温速率下环氧树脂总的放热量,q
t
是t时刻固化反应的累积放热量。
[0017]
作为本发明的优选技术方案,所述步骤s3的具体步骤为:
[0018]
s31:通过ozawa-flynn-wall法求解固化过程中不同含量的填料的表观活化能;
[0019]
s32:对不同含量的填料表观活化能利用matlab的非线性最小二乘法拟合实验数据得到lna,m和n,取其平均值,即可得到纯环氧树脂体系的固化动力学模型。
[0020]
作为本发明的优选技术方案,所述步骤s3采用中ozawa-flynn-wall法求解固化过程中的表观活化能,其计算方法表示如式:
[0021][0022]
式中,βi是升温速率,ea为表观活化能,r是普适气体常数(8.314j/mol/k),t
a,i
是对应升温速率下固化a对应的绝对温度,c为常数。
[0023]
作为本发明的优选技术方案,所述步骤s3中的环氧-酸酐体系属于自催化放热反应,固化动力学模型为自催化模型,形式为:
[0024][0025]
式中,m为指前因子,n为反应指数,t为每个交点的温度;r为普适气体常数。
[0026]
作为本发明的优选技术方案,所述步骤s1中的加入的填料的含量为30vol%,脂环族树脂的添加量为67%,所述球形氮化硼复合环氧树脂体系的配方为:双酚a型环氧树脂/脂环族树脂/甲基六氢邻苯二甲酸酐=33/67/95(质量比)。由于脂环族环氧树脂的分子链短,交联密度过高,固化产物脆,韧性差,因此,为保证环氧树脂整体具有良好的柔韧性,选择脂环族树脂的添加量为67%。由于确保环氧树脂与酸酐比例合适对固化产物的力学、电气等性能至关重要,通过对环氧-酸酐体系的动态dsc升温测试,得到不同酸酐含量下的放热峰曲线,当固化反应放热量最大时,即是环氧基与酸酐完全发生交联反应。当固化剂份数为95phr时,固化反应放热量达到最大值。因此,最终确定树脂体系的配方组成为:cyd-128树脂/celloxide 2021p树脂/甲基六氢邻苯二甲酸酐=33/67/95(质量比)。
[0027]
作为本发明的优选技术方案,所述球形氮化硼和球形氧化铝的比例为:0.2~0.5:1;所述球形氮化硼的直径为30~160μm,所述球形氧化铝的直径为10~50μm。
[0028]
与现有技术相比,本发明的高导热球形氮化硼复合环氧树脂的固化方法具有的有益效果是:考虑了添加填料的情况,对固化工艺的优化预测中融入了填料含量,研究了不同填料含量球形氮化硼复合环氧树脂的固化工艺,建立了不同填料含量球形氮化硼复合环氧树脂的非等温固化动力学模型,获得了填料含量对环氧树脂固化行为的影响规律,获得了不同填料含量的高导热球形氮化硼复合环氧树脂的优化固化工艺,降低固化过程中的内应力,为改善球形氮化硼复合环氧树脂的质量提供全面理论指导。
附图说明
[0029]
图1为本发明的高导热球形氮化硼复合环氧树脂的固化方法中10℃/min升温速率下不同填料含量的复合材料的热流曲线;
[0030]
图2为本发明的高导热球形氮化硼复合环氧树脂的固化方法中不同填料含量与固化反应放热量的关系曲线;
[0031]
图3为本发明的高导热球形氮化硼复合环氧树脂的固化方法中纯环氧树脂的固化反应速率实验值与预测值对比;
[0032]
图4为本发明的高导热球形氮化硼复合环氧树脂的固化方法中恒温固化下的实验结果和预测结果对比;
[0033]
图5为本发明的高导热球形氮化硼复合环氧树脂的固化方法中固化特征温度与填料含量的关系;
[0034]
图6为本发明的高导热球形氮化硼复合环氧树脂的固化方法中不同填料含量与温度下所需理论固化时间。
具体实施方式
[0035]
本实施例中的促进剂n,n-二甲基苄胺,固化剂甲基六氢邻苯二甲酸酐,纯度高于99%,均由阿拉丁试剂公司提供;双酚a二缩水甘油醚环氧树脂,牌号为cyd-128,环氧当量为184~194,购买于湖南岳阳巴陵石化公司;脂环族环氧树脂作为活性稀释剂,牌号为
celloxide 2021p,购买上海江杉化学试剂有限公司;自催化固化反应动力学模型进行非线性拟合用软件优选包括origin函数绘图工具。
[0036]
实施例:该高导热球形氮化硼复合环氧树脂的固化方法,具体包括以下步骤:
[0037]
s1:选择球形氮化硼复合环氧树脂体系并制备相应的高导热球形氮化硼复合环氧树脂;
[0038]
所述步骤s1中的球形氮化硼复合环氧树脂体系选择双酚a型(cyd-128)环氧树脂作为基体,脂环族树(celloxide 2021p)为活性稀释剂;甲基六氢邻苯二甲酸酐为固化剂,所述填料包括球形氮化硼和/或球形氧化铝;加入填料的含量为0~30vol%。球形氮化硼可有效降低浆料粘度,减少环氧树脂内部气泡和界面缺陷,多尺度球形填料可协同提升复合环氧树脂的导热性能,适量的小尺寸颗粒“桥接”大尺寸填料有助于形成导热网络;
[0039]
所述步骤s1中的加入的填料的含量为30vol%,脂环族树脂的添加量为67%,所述球形氮化硼复合环氧树脂体系的配方为:双酚a型环氧树脂/脂环族树脂/甲基六氢邻苯二甲酸酐=33/67/95(质量比);当固化剂份数为95phr时,固化反应放热量达到最大值。因此,最终确定树脂体系的配方组成为:cyd-128树脂/celloxide 2021p树脂/甲基六氢邻苯二甲酸酐=33/67/95(质量比);所述球形氮化硼和球形氧化铝的比例为:0.2~0.5:1;所述球形氮化硼的直径为30~160μm,所述球形氧化铝的直径为10~50μm;优选地,填料中球形氮化硼的尺寸为70μm、160μm,球形氧化铝的直径为20μm;20μm的球形氧化铝与70μm的球形氮化硼、160μm的球形氮化硼的配比为0.224:0.374:0.402;
[0040]
s2:通过固化度和固化反应热之间的线性函数关系,得到加入填料的动态固化特性关系;
[0041]
所述步骤s2的具体步骤为:采用差示扫描量热仪对环氧-酸酐体系进行动态dsc升温测试并进行监测,得到不同升温速率β下固化度随反应温度的变化规律;从而获得环氧树脂固化度和固化反应热存在线性关系,其关系表达式为:
[0042][0043]
式中,α是t时刻环氧树脂的固化度,q
tol
是该升温速率下环氧树脂总的放热量,q
t
是t时刻固化反应的累积放热量;
[0044]
s3:通过加入不同含量的填料,通过加入填料的动态固化特性关系,获得固化动力学模型及参数,并得到变化趋势;
[0045]
所述步骤s3的具体步骤为:
[0046]
s31:通过ozawa-flynn-wall法求解固化过程中不同含量的填料的表观活化能;
[0047]
s32:对不同含量的填料表观活化能利用matlab的非线性最小二乘法拟合实验数据得到lna,m和n,取其平均值,即可得到纯环氧树脂体系的固化动力学模型;
[0048]
所述步骤s3采用中ozawa-flynn-wall法求解固化过程中的表观活化能,其计算方法表示如式:
[0049][0050]
式中,βi是升温速率,ea为表观活化能,r是普适气体常数(8.314j/mol/k),t
a,i
是对
应升温速率下固化a对应的绝对温度,c为常数;
[0051]
所述步骤s3中的环氧-酸酐体系属于自催化放热反应,固化动力学模型为自催化模型,形式为:
[0052][0053]
式中,m为指前因子,n为反应指数;t为每个交点的温度;r为普适气体常数;
[0054]
s4:验证变化趋势的准确性,再根据变化趋势获得高导热球形氮化硼复合环氧树脂在不同填料含量中的最佳固化工艺。
[0055]
具体实施例:该高导热球形氮化硼复合环氧树脂的固化方法,具体包括以下步骤:
[0056]
s1:选择球形氮化硼复合环氧树脂体系并制备相应的高导热球形氮化硼复合环氧树脂;
[0057]
所述步骤s1中的球形氮化硼复合环氧树脂体系选择双酚a型(cyd-128)环氧树脂作为基体,脂环族树(celloxide 2021p)为活性稀释剂;甲基六氢邻苯二甲酸酐为固化剂,所述填料包括球形氮化硼和/或球形氧化铝;加入填料的含量为0~30vol%;球形氮化硼可有效降低浆料粘度,减少环氧树脂内部气泡和界面缺陷,多尺度球形填料可协同提升复合环氧树脂的导热性能,适量的小尺寸颗粒“桥接”大尺寸填料有助于形成导热网络;
[0058]
其中,加入的填料的含量分别为0vol%、5vol%、10vol%、20vol%、30vol%,脂环族树脂的添加量为67%,所述球形氮化硼复合环氧树脂体系的配方为:双酚a型环氧树脂/脂环族树脂/甲基六氢邻苯二甲酸酐=33/67/95(质量比);当固化剂份数为95phr时,固化反应放热量达到最大值;因此,最终确定树脂体系的配方组成为:cyd-128树脂/celloxide 2021p树脂/甲基六氢邻苯二甲酸酐=33/67/95(质量比);所述球形氮化硼和球形氧化铝的比例为:0.2~0.5:1;填料中球形氮化硼的尺寸为70μm、160μm,球形氧化铝的直径为20μm;20μm的球形氧化铝与70μm的球形氮化硼、160μm的球形氮化硼的配比为0.224:0.374:0.402;
[0059]
该高导热球形氮化硼复合环氧树脂的制备方法,具体包括以下步骤:
[0060]
(1)制备改性球形氮化硼;
[0061]
所述步骤(1)的具体步骤为:
[0062]
(1-1):称取原材料,所述原材料包括2.0g六方氮化硼片粉末、60g碳酰胺、1wt%粘合剂、0.05g分散剂;所述步骤s11中的六方氮化硼片的纯度高于99%,直径约2μm;碳酰胺的纯度大于99%,粘合剂为1%的聚乙烯醇(pva),其醇解度为98~99mol%;分散剂采用十二烷基苯磺酸钠(sdbs)和纯度为分析纯》90%;
[0063]
(1-2):将2.0g六方氮化硼粉末与60g碳酰胺在24ml去离子水中混合后在行星球磨机上以400rpm的速度球磨24h,再洗涤抽滤后得到球磨产物,即改性氮化硼;
[0064]
(1-3):接着将10g改性氮化硼和0.05g分散剂sdbs溶解在30ml去离子水中,使用真空脱泡机分散均匀,真空脱泡机分散时的转速为2000r/min;获得均匀的氮化硼水溶液,再把配置好的1wt%粘合剂溶液加入氮化硼水溶液中(向氮化硼水溶液中加入5.0g配制好的粘合剂溶液),搅拌均匀备用;
[0065]
(1-4):将氮化硼水溶液加入喷雾干燥机中,在喷雾干燥机中进行球形氮化硼的制备,通过调节浆料中氮化硼的浓度以及雾化器的压力,获得到不同粒径尺寸的球形氮化硼;
所述步骤(1-4)中喷雾干燥机的压力为2.0mpa,干燥的温度为220℃;
[0066]
(1-5):将所述步骤(1-4)中获得的球形氮化硼的颗粒转移到瓷舟中去除有机剂,再转移到管式炉中真空烧结得到球形氮化硼;所述步骤(1-5)中在瓷舟中以600℃空气中预烧结1h,在管式炉中真空烧结的温度为1800℃,真空烧结时间为2h;最后再使用筛网筛出球形氮化硼颗粒。
[0067]
(2):以不同的填料配比和不同的填料直径选择环氧树脂体系,制备高导热球形氮化硼复合环氧树脂;所述步骤s2具体步骤为:
[0068]
(2-1):按质量比33:67:95配制双酚a二缩水甘油醚环氧树脂(cyd-128)、活性稀释剂(celloxide 2021p树脂)和固化剂(甲基六氢邻苯二甲酸酐)促进剂,再加入0.5wt%的n,n-二甲基苄胺作为促进剂,并加入不同体积分数(分别为0vol%、5vol%、10vol%、20vol%、30vol%)的球形氮化硼和球形氧化铝填料,混合搅拌均匀;填料中20μm球形氧化铝与70μm球形氮化硼和160μm的球形氮化硼配比为0.224:0.374:0.402;
[0069]
(2-2):将步骤(2-1)中获得的混合物进行加热固化,所述步骤(2-2)的固化采用分段式固化,首先采用95℃固化30min,再升温至130℃固化2h,再升温至155℃固化1h,获得高导热球形氮化硼复合环氧树脂,获得的高导热球形氮化硼复合环氧树脂在温度为25℃时的导热系数达到了1.84w/(m
·
k);
[0070]
s2:通过固化度和固化反应热之间的线性函数关系,得到加入填料的动态固化特性关系;分别取10mg五种不同含量的填料(0vol%、5vol%、10vol%、20vol%、30vol%)的样品在美国ta仪器的dsc2500型差示扫描量热仪上对动态升温下样品的固化反应进行监测,以10k/min的升温速率达到指定温度后进行恒温,得到不同升温速率β下固化度随反应温度的变化规律,环氧树脂固化度和固化反应热存在线性关系,图1为升温速率为10℃/min时,不同球形氮化硼填充量下复合材料的放热量随温度变化图;从图1中得到规律:随着填充量增加,复合材料固化的起始温度、峰值温度逐渐增大,原因在于球形氮化硼的存在使得环氧树脂基团不能充分碰撞运动,需要更多的热量才能完成交联固化反应;此外在图1中可以看出,随球形氮化硼填充量增加,单位质量复合材料的固化反应热快速下降,这是由于球形氮化硼不参与反应,填料含量升高导致反应物减少;
[0071]
所述步骤s2的具体步骤为:采用差示扫描量热仪对环氧-酸酐体系进行动态dsc升温测试并进行监测,得到不同升温速率β下固化度随反应温度的变化规律;从而获得环氧树脂固化度和固化反应热存在线性关系,其关系表达式为:
[0072][0073]
式中,α是t时刻环氧树脂的固化度,q
tol
是该升温速率下环氧树脂总的放热量,q
t
是t时刻固化反应的累积放热量;将五种不同含量的填料的样品进行动态升温测试并监测,获得了填料含量与固化反应放热量的关系曲线如图2所示;
[0074]
s3:通过加入不同含量的填料,通过加入填料的动态固化特性关系,获得固化动力学模型及参数,并得到变化趋势;
[0075]
所述步骤s3的具体步骤为:
[0076]
s31:通过ozawa-flynn-wall法求解固化过程中不同含量的填料的表观活化能;
[0077]
s32:对不同含量的填料表观活化能利用matlab的非线性最小二乘法拟合实验数
据得到lna,m和n,取其平均值,即可得到纯环氧树脂体系的固化动力学模型;
[0078]
所述步骤s3采用中ozawa-flynn-wall法求解固化过程中的表观活化能,其计算方法表示如式:
[0079][0080]
式中,βi是升温速率,ea为表观活化能,r是普适气体常数(8.314j/mol/k),t
a,i
是对应升温速率下固化a对应的绝对温度;c为常数;根据ozawa-flynn-wall法(ofw法)可推出计算不同填料含量下复合材料的表观活化能,得到不同填料含量下复合材料的模型参数,得到规律如下:当体系固化度逐渐增加,表观活化能有所增大。这是因为在固化初始阶段,单位体积内环氧树脂的活性基团数量多,基团之间的有效碰撞率大,固化反应更容易进行;随着固化反应的进行,环氧树脂分子链开始形成网状结构,体系空间位阻效应增加,可反应的环氧基团逐渐减少,并且导热填料的加入,限制了固化反应过程中链段的运动,活性基团需要更多的动能才能形成有效的碰撞发生交联,因此宏观上表现为表观活化能升高;同时因环氧-酸酐体系属于自催化放热反应,其固化动力学模型为自催化模型,形式为:
[0081][0082]
式中,m为指前因子,n为反应指数;t为每个交点的温度;r为普适气体常数;
[0083]
采用同样的方法计算得到不同球形氮化硼填充量下复合材料的动力学模型参数,如表1所示;从表1中可以看出,填充球形氮化硼后指前因子略微升高,这是由于填料的加入限制了环氧树脂的固化交联;而反应级数n的增加,是因为填料的加入拉长了固化末期所需的时间,也即是固化终止温度向高温方向移动;
[0084]
表1不同填料含量下复合材料的动力学模型参数
[0085][0086]
以纯环氧树脂为例(即0%vol的填料含量),将表观活化能ea=68.40kj/mol代入式中,利用matlab的非线性最小二乘法拟合实验数据得到lnam和n,取其平均值,即可得到纯环氧树脂体系的具体固化动力学模型,如下式所示:
[0087][0088]
同理,可得到不同填料含量的具体固化动力学模型;
[0089]
s4:验证变化趋势的准确性,再根据变化趋势获得高导热球形氮化硼复合环氧树脂在不同填料含量中的最佳固化工艺;为验证动力学模型的准确性,在图3中分别绘制了纯环氧树脂升温速率为3、5、10、15、20k/min时,固化反应速率和温度的曲线;图3中散点为实验数据,曲线为动力学模型预测数据。将实验结果和预测结果对比,两者结果基本吻合(吻
合度大于95%),表明使用自催化模型描述该树脂体系的准确性;本发明对预测结果的曲线与动态dsc试验数据的对比方式没有特殊要求,采用本领域技术人员熟知的即可。在实际生产应用中,往往采用简单易操作的恒温固化工艺;为验证动力学模型在恒温下预测结果的准确性,通过dsc的等温模式测试了纯环氧树脂在110℃和120℃下的固化反应放热曲线;对固化放热曲线进行变换得到固化度与时间的关系,如图4中散点图所示,可以看出动力学模型对恒温固化的预测值与实验值几乎重合,验证了该模型用于预测恒温固化具有相当高的准确性(大于90%);采用同样的方法计算得到不同球形氮化硼填充量下复合材料的动力学模型参数。
[0090]
为简化操作和节省能源,环氧树脂一般在恒定温度下固化,为获得恒温下(升温速率β为0)的固化工艺,在图5中获得了填充不同含量的球形氮化硼时复合材料的固化特征值,并对其进行拟合,其截距即为温度恒定时的固化特征温度;该纵截距展示了不同填料含量下复合材料的近似凝胶温度、固化温度、后处理温度;同时发现随导热填料含量的增加,复合材料所需固化温度随之增加,原因在于导热填料含量增加对环氧树脂分子链运动的限制作用增强;通过固化动力学模型可以有效预测不同填料含量不同温度下的固化度-时间规律,达到考虑全面、高效、高质量和节能的生产过程;由固化动力学模型得到不同球形氮化硼填充量与温度下环氧树脂固化度达到0.99时的理论时间,如图6所示;随着填料含量增加,所需理论时间也逐渐增加。
[0091]
由以上实施例的结果可知,采用恰当的固化温度与时间,是制备高品质复合材料的重要保障;结合图中的固化特征温度与理论固化时间即可得到不同填料填充量下的固化工艺,获得了针对不同填料含量下,高导热球形氮化硼复合环氧树脂的优化固化工艺方法;例如,纯环氧树脂可采用95℃/30min 125℃/1h 145℃/30min阶梯化升温方式进行固化,而球形氮化硼填充量为30vol%时,复合材料则适合采用95℃/30min 130℃/2h 155℃/1h的方式进行固化;该方法的使用对象更加全面,范围覆盖率更高。
[0092]
以上所述的具体实施例,对本发明的目的、技术方案和有益效果进行了进一步详细说明,所应理解的是,以上所述仅为本发明的具体实施例,并不用于限制本发明,凡在本发明的精神和原则之内,所做的任何修改、等同替换、改进等,例如某个部件形状或者材料的改变;均应包含在本发明的保护范围之内。
再多了解一些
本文用于创业者技术爱好者查询,仅供学习研究,如用于商业用途,请联系技术所有人。