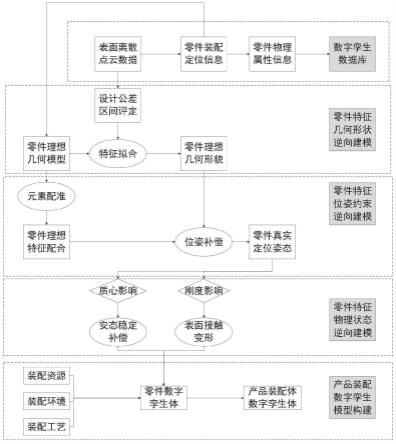
1.本发明属于智能制造领域,特别涉及一种基于数字孪生的多层次信息装配 模型的构建方法。
背景技术:
2.在复杂产品的制造过程中,复杂产品装配是至关重要的环节之一,装配精 度将直接影响后续部件装配及总装的质量和效率。而目前产品数字化建模只考 虑零件制造过程产生的表面几何误差,未包括特征配准约束和物理属性信息, 零件装配结果不仅与其表面特征的几何形状相关,还会受到特征位姿约束和物 理状态的影响。在现有的零件表面特征建模方法中,一般通过三坐标测量仪获 取零件上的离散点云,从而利用多项式方法显式地表示零件的表面形状轮廓。 这种模型仅包括零件表面几何信息,在装配时可视为几何形状匹配问题,无法 反映真实零件装配情况,特别是零件刚度较低发生柔性变形时,单纯几何装配 分析得到的产品累积误差与实际测量结果差距较大,难以指导工作人员装配操 作。
3.现阶段的专利公开以及文献资料显示:1)一种矿井数字孪生模型及其构建 方法(cn201911390383.7)通过构建物理空间矿井应用场景在虚拟空间的数字 孪生模型,实现数字孪生体与物理实体之间信息交互与虚拟监控,该技术在建 模过程中未考虑物理特性及环境因素,因此数字孪生模型的准确度不够高;2) 一种智能制造车间数字孪生模型构建方法与系统(cn202010831244.x)通过在 智能制造车间中配置传感设备,采集制造现场生产数据并进行深度融合与分析, 形成制造车间实时数据库,基于制造车间实时数据库与制造车间语义知识库, 构建出智能车间的数字孪生模型,该技术重在对车间的生产数据等进行实时监 控,忽略了车间本身物理状态因素的影响,易受到环境因素影响,鲁棒性较差; 3)基于飞机结构件数字孪生模型的建模方法(cn202010755020.5)以工艺理论 模型为基准,加工出零件实物提取理论模型尺寸数据对加工完成的零件实物进 行测量,获得到实际零件点位坐标,生成报告运用测量软件将获取的零件关键 尺寸的实测值与理论值进行换算获得差值偏差将通过测量获得到的实际零件点 位坐标生成点云图,再导入建模软件中运用建模软件以生成点云图为基准进行 逆向建模,形成数字孪生模型。该技术没有考虑零件的刚度、硬度等物理量的 影响,因此数字孪生模型无法对实际装配过程进行指导。综上,现有研究成果 和方法在数字孪生模型的建立上普遍存在描述信息片面的问题,没有从多个方 面对现实中的模型进行完善的映射,导致数字模型无法对实际生产发挥指导作 用。
4.本发明在建立数字孪生模型的过程中考虑了现实中的装配零件的形状、位 姿、物理性质三方面信息,解决了描述信息较为片面的问题,相对于现有技术 能够更加完善的对现实中的模型进行映射,因此,能够对实际生产有指导作用。
技术实现要素:
5.为解决上述问题,本发明提出一种基于数字孪生的多层次信息装配模型的 构建方法,将影响后续装配的零件形状、位姿、物理性质考虑在内,生成与真 实物理零件更加相
似的零件数字孪生体,从而构建与真实产品近乎完美映射的 装配数字化模型。首先从真实零件中采集特征的离散点云、配准元素、质心位 置信息,将它们划分为几何形状层、位姿约束层、物理状态层,构造了零件特 征的层次化模型,共同表达面向装配的零件特征完整属性;其次针对不同层次 进行逆向建模,包括基于多项式拟合和离散余弦变换的几何形状建模、基于元 素特征配准的位姿约束建模、基于接触变形的物理状态建模,从而获取包括真 实信息的零件数字孪生体。
6.为实现上述目的,本发明采用的技术方案是:
7.一种基于数字孪生的多层次信息装配模型的构建方法,包括以下步骤:
8.(1)构建零件的层次化信息模型,将虚拟环境中数字模型划分为几何形状 层、位姿约束层、物理状态层三个不同层次,与理想设计模型相叠加共同反映 真实零件当前完整信息状态,从而与真实世界零件相互映射,生成与真实物理 零件更加相似的零件数字孪生体;
9.(2)在零件物理模型上进行信息采集与提取,分别提取零件的几何形状信 息、约束特征信息、物理状态信息并建立相应数据库,以便在后续工作中调用;
10.(3)考虑零件装配特征对其配合约束进行逆向建模,将平面、曲面、轴孔 基础特征进一步分解为点、线、面三类配准元素,以它们的对齐、共线、重合 方式减小装配体自由度,达到零件间固定的目的,基于元素配准的特征位姿求 解方法,得到与该零件装配特征相配合需要进行的坐标变换,并考虑特征几何 误差情况下的位姿变动补偿量,从而将位姿约束信息反映在零件特征上;
11.(4)针对零件物理状态信息进行逆向建模,考虑特征几何误差的装配过程 中零件姿态稳定性,分析零件质心对静力平衡状态的影响,同时根据hertz理论 计算零件接触面的表面变形,并根据其大小确定物理平移和旋转补偿量,从而 将零件物理状态信息融入数字化模型中;
12.(5)将产品装配孪生体分为资源层、工艺层、环境层三个层次,利用上述 方法构造的零件孪生体和采集的装配信息,形成与现实世界物理产品制造-装 配过程相映射的关系,并将其应用于指导实际装配操作。
13.与现有技术相比,本发明具有以下有益效果:
14.本发明将影响后续装配的零件形状、位姿、物理性质考虑在内,解决了描 述信息较为片面的问题,相对于现有技术生成与真实物理零件更加相似的零件 数字孪生体,从而构建与真实产品近乎完美映射的装配数字化模型,进而提升 装配仿真精度,指导实际装配作业。
附图说明
15.图1是产品装配数字孪生模型构建流程图;
16.图2是虚拟世界数字零件信息层模型;
17.图3是现实世界实体零件信息层模型;
18.图4是基于点云信息评定零件质量流程图。
具体实施方案
19.下面结合附图对本发明做进一步的详细说明。此处所说明的附图是本技术 的一部分,用来对本发明进行进一步解释,但并不构成对本发明的限定。
20.图1为产品装配数字孪生模型构建流程图。如图1所示,包括以下步骤:
21.(1)零件孪生体包括真实世界的实物零件和虚拟世界的数字零件两部分, 根据零件信息在装配过程中的表现形式,将虚拟环境中数字模型划分为几何形 状层、位姿约束层、物理状态层三个不同层次。如图2所示,与理想设计模型 相叠加共同反映真实零件当前完整信息状态,从而与真实世界零件相互映射, 共同构成零件孪生体。如图3所示,真实世界实物零件包括零件制造信息、几 何信息和物理信息,涵盖了零件加工成型的整个过程。零件制造信息主要包括 制造工艺和原材料两部分,前者包括切削加工、铸造、锻造、冲压等多种加工 方式,后者包括铝、铝合金、碳钢、碳纤维等材料;零件几何信息由设计图纸 和实际表面轮廓构成,前者包括设计尺寸、设计公差等信息,决定零件整体形 状和功能,后者包括纹理、凹痕、毛刺、擦伤等表面缺陷,由人为或设备原因 引起,可以通过精加工方法消除;零件物理信息包括零件材料属性、力学属性 和运动属性三大块,其中材料属性由密度、杨氏模量、泊松比等本征属性构成; 力学属性由屈服强度、抗拉强度、抗压强度、弯曲强度、剪切强度等集合、材 料刚度和不同受力类型构成;运动属性包括质心位置、速度、加速度、动量等 元素。
22.(2)零件表面轮廓信息是影响其数字化摸型的最直观数据,传统测量手段 利用游标卡尺、量块、r规等工具,仅能获取零件简单特征的尺寸数据,其包 括的信息量无法支撑完整数字模型的构建。现代传感技术的发展使得采集零件 表面离散点的三维坐标数据变为可能,结合计算机技术中的逆向工程对点云数 据进行处理,能够反映出真实零件表面具体形状、零件待装配约束等特征信息 一般来说,非接触式扫描得到的庞大点云数据中掺杂许多噪声点,直接使用它 们进行逆向建摸会导致数字化模型的严重失真,甚至出现与物理零件完全不同 的情况,需要对原始点云数据进行处理,包括多视点云对齐、误差点剔除、点 云滤波、点云精筒等步骤。为了避免点云集的复杂处理步骤,本专利采用接触 式三坐标测量仪对零件各特征面分别进行扫描,得到分布比较规则的零件离散 点云集合。将获取的零件表面轮廓信息存入虚拟环境,形成数字零件的几何形 状层数据库;根据几何理想设计模型标注出约束特征位置,结合该特征处实际 点云形成数字零件的位姿约束层数据库;通过质量质心测试系统、转动惯量测 试仪等设备测算零件物理属性,结合加工制造方法获取零件质量、质心位置、 弹性模量、泊松比等信息,形成数字零件的物理状态层数据库,三者共同构成 零件数字化孪生体的信息基础。
23.(3)零件表面特征点必须全部落在公差设计区间内,因此需要计算各个离 散点偏离理想特征的距离大小,将扫描点云实测误差与设计公差进行比较,评 定零件是否符合设计规范。如图4所示,主要分为以下步骤:
24.1)将零件扫描点云与cad设计模型对齐,利用特征识别软件使二者达到 最接近状态。零件表面理想特征形状比较规则,一般沿特征的边线确定特征坐 标系,采用函数f(x,y,z)=0表示该理想特征面。
25.2)将测量坐标系下的扫描点云数据进行坐标变换,获得零件表面离散点在 零件特征坐标系下的新坐标。若测量坐标系下离散点的点云坐标集合为qm,则 它们在零件特征
坐标系下的新坐标集合q
p
表示为式(1),其中s为测量坐标系 到零件特征坐标系的变换矩阵。
26.s.qm=q
p
ꢀꢀꢀꢀꢀꢀꢀꢀꢀ
(1)
27.3)将变换后的点云新坐标集合q
p
记为{(xi,yi,zi)|1≤i≤n},计算所有点q
p
到零 件理想特征f(x,y,z)=0的距离。对于变换后的离散点在理想特征上寻找距离 点最近的点,如式(2)所示,与该点的距离即为与理想特征的距离。
[0028][0029]
4)判断离散点与理想特征的位置关系,若离散点在理想特征下方,则将 它与理想特征距离记为负值,即:
[0030][0031]
5)零件表面实测误差为离散点与连续特征的最大和最小距离之差,将其与 设计公差t相比较评定该零件是否符合标准。
[0032][0033]
(4)根据零件真实特征信息层次化模型获取拉伸类零件表面线特征的实际 测量离散点云数据,采用最小二乘法对测点进行多项式拟合,从而重构最接近 实际零件表面形状的连续曲线函数。记零件表面线特征扫描获取的离散点云集 合为{qi(xi,zi)},用拟合连续函数f(x)与所有离散点差值的二范数来评价拟合程度 好坏,表示为公式(5)。
[0034][0035]
当f(x)取最小值时,称为离散点云的最小二乘拟合多项式。将拟合曲线与 离散点的二范数平方值将拟合曲线与离散点的二范数平方值记为e,即
[0036][0037]
由于e是多项式系数{a0,a1,
…
,am}的多元函数,求e最小值可通过对ak求偏 导,即
[0038][0039][0040]
当k取0到m中正整数时,式(8)可以用矩阵形式表迖如下:
[0041][0042]
根据零件设计需求设置多项式阶数m,可以计算出多项式系数组合的唯一 解,继而得到最接近真实线特征的几何形状。
[0043]
(5)当零件表面不光滑程度较高,即凸起和凹陷等微小特征较多时,多项 式拟合方法往往具有较大误差,本节利用离散佘弦变换方法实现真实几何线/面 特征的表达。将零件表面形状特征视为信号,根据波长将其分为翘曲度、波纹 度和粗糙度,其中翘曲度占主导作用,波纹度有一定影响,粗糙度可以忽略不 计。
[0044]
将实体零件表面特征的大量点云位置数据集合q记为{(xi,yi,zi)1≤i≤n}(当 该特征为线特征时,q为二维坐标,yi=0),构造表面离散点的偏差位移场 δ(q),它描述了零件特征实际几何形状位置与理想位置间的z方向差值。以平 面轮廓度误差为例,若该特征是类似于(3)中的二维特征,即z仅与x相关, 偏差位移场δ(q)为n元向量,则包括n个元素的线特征离散余弦变换公式为式 (10)。
[0045][0046]
其中,k为阶数,f(i)为第i个离散点的z向偏差位移大小,c(k)如式(11) 所示。
[0047][0048]
根据离散余弦变换性质,其逆变换与正变换具有相同的形式,可以采用式 (12)表示,从而得到线特征的拟合轮廓。
[0049][0050]
(6)零件一般由多个特征构成,其中只有一个或几个特征会与其它零件产 生相互作用关系,而特征间的配合关系是通过特征配准元素确定的,因此准确 识别这些配准元素并与对应元素进行匹配,是零件装配成功的前提。
[0051]
将零件特征按照是否将与其它零件产生配合关系分为装配特征和其它特 征,装配特征主要有平面特征、曲面特征、轴特征、孔特征、销特征、槽特征 等。将装配特征分解为多种元素结构,包括点、线、面三大类特征配准元素, 通过特征配准元素之间的匹配,待装配零件与基准零件产生约束关系,达到相 对自由度为零的状态,即二者固定在一起,完成零件装配过程。
[0052]
零件以配合特征为基准完成装配后,它们的相对位置将保持不变,已知其 中一个
零件位姿信息即可求出另一个零件位姿。由于零件特征一般在各自的零 件特征坐标系中进行描述,而装配过程在世界坐标系中完成,因此需要进行坐 标变换。设某零件孔特征采用轴线元素l和底面元素f表达,二者组成了零件 特征坐标系中的位姿信息c1,包含了轴线向量、底面法向量以及轴线与底面交 点坐标,记为当底面为平面且与轴线垂直时,同 理,待装配的轴特征位姿信息c2记为零件1坐标系与零 件2坐标系到世界坐标系的变换矩阵分别为t
p1-g
和t
p2-g
。
[0053]
基于元素配准方式的特征配合分为以下三个步骤:
[0054]
1)将零件2绕零件1坐标系各轴旋转一定角度,记为r1,使得轴线和平行,即通过二者内积确保方向一致。
[0055]
2)构建两个零件的包围盒,将零件2沿坐标轴平移一定距离,记为t1,使 得轴线和重合,即判断准则为零件1轴线上点a和零件2轴线上 点a和零件2轴线上点b连线ab必与轴线同样平行,即该过程中 约束条件为两零件包围盒不产生干涉。
[0056]
3)将零件2沿轴线平移一定距离,记为t2,使得点和点 重合,从而实现零件1孔特征和零件2轴特征的配合。分步配合矩 阵乘积与整体变换矩阵ts相同,如式(13)所示。
[0057]
t2.t1.r1=tsꢀꢀꢀꢀꢀꢀꢀꢀꢀꢀ
(13)
[0058]
(7)两个零件特征进行装配时,相当于差曲线与直线特征逐渐接近,它们 的间距最小值点处最先接触,该点称之为第一接触点。若差曲线上最小值点存 在两个或两个以上,则与直线特征接触后完成装配;若最小值点只有一个,则 差曲线会发生偏转,直至产生第二个接触点。第二接触点同样也是差曲线的极 小值点,根据偏转方向存在不同的装配状态。值得注意的是,当差曲线进行偏 转时会绕第一接触点“滚动”,即接触位置发生轻微变动。由于特征误差导致的位 姿补偿与零件尺寸相比很小,因此本专利不考虑“滚动”引起的接触点偏移情况, 将第一接触点和第二接触点的连线认为是差曲线与直线特征的接触线。二维真 实表面轮廓匹配的位姿变动补偿量求解方法分为如下三个步骤:
[0059]
1)假设(xk,zk)为差曲线上的点,k=1,2,...,n,首先求差曲线上的极 小值点。将点(xk,zk)与邻点(x
k-1
,z
k-1
),(x
k 1
,z
k 1
)进行比较,若同时满足zk≤z
k-1
和 zk≤z
k 1
,则该点为极小值点。若点(xk,zk)是差曲线端点,即k=1或k=n,若满 足z1≤z2和zn≤z
n-1
,则将端点(x1,z1)和(xn,zn)视为极小值点。
[0060]
2)假设(xi,zi)、(xj,zj)为两个极小值点,获得它们连线的直线方程。将差曲 线上所有测点的x坐标代入两极小值点连线的直线方程中,并与直线方程得到的z值进行比较,若满足式(14),表明差曲线所有点都 位于该直线上方,则这两个
极小值点的组合为可能接触点情况。
[0061][0062]
(8)根据差曲线与直线特征接触点的x坐标确定零件1和零件2上对应实 际接触点位置,保持基准零件固定,则待装配零件可以通过平移和旋转实现二 者的配合。将约束补偿位姿平移量记为它的前两项为0,第三 项大小为差曲线与直线z=0的最短距离;旋转量记为它的第一 项和第三项为0,第二项大小为则式(13)考虑约束补偿项后 变为式(15)
[0063]
rc·
(t2 tc)
·
t1·
r1=t
x
ꢀꢀꢀꢀꢀꢀꢀꢀꢀꢀꢀ
(15)
[0064]
(9)考虑质心位置的零件装配姿态稳定性
[0065]
几何稳定状态的装配形式与实际装配情况并不相符。为了保证物理稳定性, 这里考虑质心位置对装配姿态影响。作出如下两个假设:
[0066]
1)旋转后特征长度和其上离散点x轴坐标均保持不变。
[0067]
2)零件不会发生相对“滑移”,即x轴两端保持固定。
[0068]
对于第一个假设,由于零件旋转补偿角度极小,可以得到x、z轴坐标变 动δx、δz与特征长度变动δl的关系如式(16),补偿角度较小时δx、δl和δz相比 可忽略。对于第二个假设,若零件在x方向出现“滑移”,将导致零件间不能完全
ꢀ“
吻合”,从而造成装配失败。因此本专利认为以上两个假设都是合理的。
[0069][0070]
(10)考虑接触刚度的零件误差表面变形
[0071]
根据hertz理论,将实际零件表面特征的配合看作局部凸体的接触,在压力 p作用下产生半径为r的圆形接触区域,同时在法向上出现大小为3的变形,产 生大小为的应力,它们用公式(17)分别表示如下:
[0072][0073]
其中,r为圆形接触区域中与接触点的距离,满足0≤r≤a,在接触点处(r=0) 接触应力取最大值。ρe为接触点的综合曲率半径,ee为当量弹性模量,二者 由两配合零件的物
理属性决定,表示为式(18)。
[0074][0075]
ρ1和ρ2内分别为零件1和零件2接触点处的曲率半径,e1、μ1和e2、μ2分别为零件 1和零件2的弹性模量和泊松比。
[0076]
在(9)节考虑质心的物理稳定装配状态分析基础上计算接触凸体的变形量, 通过式(19)计算出a和d点的接触变形量,根据两点变形量与a、d点原始 坐标计算出待装配零件的新位姿,刚性平面特征与x轴的夹角由θ2变为θ3。
[0077][0078]
如式(20),和分别为物理平移补偿量和物理旋转补偿量,从而生成新 的位姿矩阵确定最终装配状态,如式(21)。
[0079][0080]rp
·
[rc·
(t2 tc) t
p
]
·
t1·
r1=tsꢀꢀꢀꢀꢀꢀꢀꢀꢀꢀ
(21)
[0081]
以上实施例仅用于说明本发明的技术方案而非对其限制,尽管参照上述实 施例对本发明进行了详细说明,所属领域的普通技术人员依然可以对本发明的 具体实施方案进行修改或者等同替换,而这些并未脱离本发明精神和范围的任 何修改或者等同替换,其均在申请待批的本发明的权利要求保护范围之内。
再多了解一些
本文用于创业者技术爱好者查询,仅供学习研究,如用于商业用途,请联系技术所有人。