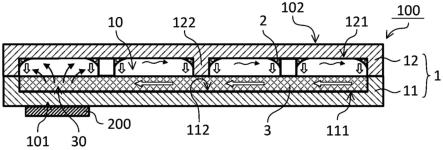
1.本实用新型涉及热传导部件。
背景技术:
2.以往,提出了作为热传导部件的热管。在热管的内部封入有水等工作介质和芯构造体。当热管与发热体接触地配置时,内部的工作介质被发热体加热而气化。气化后的蒸汽在热管的内部向散热侧移动。在散热侧,蒸汽通过散热被冷却而液化。成为液体的工作介质通过毛细管现象而在芯构造体中向发热体侧移动。通过这样的工作介质的移动,热被从发热体侧输送到散热侧。
3.上述的芯构造体例如是通过对金属浆料进行加热而使金属浆料所包含的金属彼此接合而形成的(例如,国际公开2017/056842号)。
4.但是,当供工作介质通过的芯构造体内的流路在散热侧与发热体侧之间中断或变得非常窄时,输送热的工作介质难以在芯构造体内移动。因此,工作介质在芯构造体的内部的移动效率有可能降低。
技术实现要素:
5.鉴于上述状况,本实用新型的目的在于,提供具有工作介质的移动效率较高的芯构造体的热传导部件。
6.为了达成上述目的,本实用新型的一个方式的热传导部件具有:壳体,其在内部具有空间;多孔质的芯构造体;以及工作介质。所述壳体具有第1金属板和第2金属板。所述第1金属板和所述第2金属板对置配置。所述工作介质和所述芯构造体收纳于所述空间。所述芯构造体配置在所述第1金属板上,并且在内部具有供液体状态的所述工作介质通过的流路。所述流路从与在所述第1金属板上配置有所述芯构造体的配置面平行的方向上的所述芯构造体的一端部连接至另一端部。
7.在上述实施方式中,所述芯构造体是多个金属粒的烧结体,所述金属粒的平均粒径为20μm以上且200μm以下。
8.在上述实施方式中,所述金属粒的平均粒径为50μm以上且100μm以下。
9.在上述实施方式中,所述金属粒的材料为铜或铜合金。
10.在上述实施方式中,所述芯构造体还具有多个第1粘合剂部,所述第1粘合剂部将相邻的所述金属粒彼此以小于1μm的间隔连结起来。
11.在上述实施方式中,所述金属粒和所述第1粘合剂部的材料分别相同。
12.在上述实施方式中,所述芯构造体还具有多个第2粘合剂部,所述第2粘合剂部将一部分所述金属粒与所述第1金属板以小于1μm的间隔连结起来。
13.在上述实施方式中,所述金属粒、所述第2粘合剂部以及所述第1金属板的材料分别相同。
14.在上述实施方式中,所述芯构造体的空隙率为20%以上且80%以下。
15.在上述实施方式中,所述空隙率为40%以上且60%以下。
16.为了达成上述目的,本实用新型的一个方式的热传导部件具有:壳体,其在内部具有空间;多孔质的芯构造体;以及工作介质。所述壳体具有第1金属板和第2金属板。所述第1金属板和所述第2金属板对置配置。所述工作介质和所述芯构造体收纳于所述空间。所述芯构造体配置在所述第1金属板上,并且在内部具有供液体状态的所述工作介质通过的流路。所述第1金属板具有能够传递从发热体释放的热的被热部。所述流路从与在所述第1金属板上配置有所述芯构造体的配置面平行的方向上的所述芯构造体的端部连接至所述芯构造体中的从所述配置面的法线方向观察时与所述被热部重叠的部分。
17.在上述实施方式中,所述芯构造体是多个金属粒的烧结体,所述金属粒的平均粒径为20μm以上且200μm以下。
18.在上述实施方式中,所述芯构造体的空隙率为20%以上且80%以下。
19.在上述实施方式中,所述空隙率为40%以上且60%以下。
20.为了达成上述目的,本实用新型的一个方式的热传导部件具有:壳体,其在内部具有空间;多孔质的芯构造体;以及工作介质。所述壳体具有第1金属板和第2金属板。所述第1金属板和所述第2金属板对置配置。所述工作介质和所述芯构造体收纳于所述空间。所述芯构造体是多个金属粒的烧结体,配置在所述第1金属板上。所述金属粒的平均粒径为20μm以上且200μm以下。
21.在上述实施方式中,所述芯构造体的空隙率为20%以上且80%以下。
22.在上述实施方式中,所述空隙率为40%以上且60%以下。
23.根据本实用新型,能够提供具有工作介质的输送效率较高的芯构造体的热传导部件。
24.由以下的本实用新型优选实施方式的详细说明,参照附图,可以更清楚地理解本实用新型的上述及其他特征、要素、步骤、特点和优点。
附图说明
25.图1a是热传导部件的剖视图。
26.图1b是热传导部件的立体图。
27.图1c是热传导部件的分解立体图。
28.图2是芯构造体的内部构造的示意图。
29.图3是用于芯构造体的形成的金属浆料的内部构造的示意图。
30.图4是示出热传导部件的制造工序的流程的流程图。
31.图5a是涂覆步骤的示意图。
32.图5b是烧结步骤的示意图。
33.图5c是密封步骤中的配置步骤的示意图。
34.图5d是密封步骤中的接合步骤的示意图。
35.图6是渗透测量装置的概略图。
36.图7是示出测量金属烧结体的空隙部的连接状态的工序的流程的流程图。
37.图8是示出各个芯构造体的内部的空隙部的连接状态的测量结果的表。
具体实施方式
38.以下,参照附图对本实用新型的实施方式进行说明。图1a至图1c示出热传导部件100的结构例。图1a是热传导部件100的剖视图。图1b是热传导部件100的立体图。图1c是热传导部件100的分解立体图。这里,图1a示出沿着图1b的a-a 线的热传导部件100的截面构造。
39.另外,在本说明书中,关于热传导部件100,将从图1a的上侧和下侧中的一方朝向另一方的方向称为“上下方向”。将上下方向中的从图1a的下侧向上侧的朝向称为“上方”,将从图1a的上侧向下侧的朝向称为“下方”。在图1a以后,将各个结构要素的上方的端部称为“上端部”,将下方的端部称为“下端部”。另外,将各个结构要素的表面中的朝向上方的面称为“上表面”,将朝向下方的面称为“下表面”。但是,这些只是为了说明而使用的名称,并不意味着限定实际的位置关系、方向以及名称。
40.另外,在本说明书中,“烧结”是指将包含金属的粉末或者上述金属的浆料加热至比上述金属的熔点低的温度,从而对上述金属的粒子进行烧固的技术。而且,“烧结体”是指通过烧结而得到的物体。
41.热传导部件100是所谓的蒸气室,利用工作介质2气化和液化的循环来释放发热体200的热。另外,发热体200例如是cpu(central processing unit:中央处理单元)、 mpu(micro processing unit:微处理单元)等运算处理装置以及igbt(绝缘栅双极型晶体管)等功率半导体。
42.热传导部件100具有壳体1、工作介质2以及芯构造体3。
43.壳体1在内部具有空间10。如上所述,热传导部件100具有壳体1。工作介质2 和芯构造体3收纳于上述空间10。
44.壳体1还具有第1金属板11和第2金属板12。第1金属板11和第2金属板12 对置地配置。空间10形成于第1金属板11与第2金属板12之间。壳体1将工作介质2和芯构造体3收纳于第1金属板11与第2金属板12之间。
45.第1金属板11重叠地配置在第2金属板12上。另外,第1金属板11具有凹部 111。凹部111配置于第1金属板11的上表面并向下方凹陷。第2金属板12具有凹部121。凹部121配置于第2金属板12的下表面并向上方凹陷。在从上下方向观察时,凹部111与凹部121重叠。由此,在第1金属板11与第2金属板12之间配置有空间10。在本实施方式中,通过将第1金属板11和第2金属板12的外周缘部相互接合,在壳体1的内部形成密闭的空间10。另外,在本实施方式中,壳体1具有凹部111、121这两者。但是,并不限定于本实施方式的例示,壳体1也可以仅具有凹部111、121中的一方。
46.在第1金属板11的凹部111的底面上配置有芯构造体3。以下,将配置有芯构造体3的面称为“配置面112”。另外,如图1b所示,发热体200以能够进行热传递的方式安装于第1金属板11的下表面的一部分区域。以下,将第1金属板11中的具有该一部分区域的部分称为“被热部101”。在本实施方式中,第1金属板11中的与发热体200接触的部分是被热部101。即,第1金属板11具有能够传递从发热体200 释放的热的被热部101。
47.接着,壳体1还具有多个柱部122。在本实施方式中,第2金属板12具有柱部 122。柱部122从第2金属板12的与第1金属板11对置的面朝向第1金属板11向下方突出。在本实施方式中,柱部122从凹部121的底面向下方突出。柱部122的前端部与芯构造体3接触。由此,柱
部122在第1金属板11与第2金属板12之间对两者进行支承。因此,即使第1金属板11和第2金属板12彼此对置的对置方向的力从外部作用于壳体1,壳体1也不容易发生变形,从而能够抑制空间10由于该壳体1的变形而变窄。另外,并不限定于本实施方式的例示,柱部122的前端部也可以与第1 金属板11接触,例如也可以与凹部111的底面接触。另外,第1金属板11也可以具有柱部122的至少一部分。例如,柱部122的至少一部分也可以从第1金属板11的凹部111的底面朝向第2金属板12向上方突出。
48.在本实施方式中,第1金属板11和第2金属板12的材料均为铜或者铜合金。但是,并不限定于上述的例示,第1金属板11和第2金属板12的材料例如也可以使用铜以外的金属或者包含铜以外的金属的合金。作为铜以外的金属,例如能够采用铝、锌、银、金、镁、锰以及钛等中的任意一种。另外,作为上述的合金,例如能够采用黄铜、不锈钢以及硬铝等。此外,第1金属板11和第2金属板12的材料在本实施方式中相同,但并不限定于该例示,也可以不同。例如,第1金属板11的材料可以是铜或者铜合金,第2金属板12的材料可以是不锈钢。
49.工作介质2在空间10内输送热。如上所述,热传导部件100具有工作介质2。在从上下方向观察时与被热部101重叠的部分处,在液体状态下渗透于芯构造体3 的工作介质2通过从被热部101传递来的热而气化,并在空间10内蒸发。这里,优选密闭的空间10被减压,其内压比大气压低。这样,工作介质2更容易气化。另外,以下,将芯构造体3中的从上下方向观察时与被热部101重叠的上述的部分称为“加热部分30”。
50.气化后的工作介质2在壳体1的远离发热体200的部分被冷却而液化。另外,以下,将壳体1中的气化后的工作介质2被冷却而液化的部分称为“散热部102”。本实施方式的散热部102例如是第2金属板12。
51.在散热部102中液化后的工作介质2朝向芯构造体3移动。工作介质2通过毛细管现象而渗透到芯构造体3的内部,并且回流至芯构造体3的加热部分30。
52.通过上述那样的工作介质2气化和液化的循环,热传导部件100能够将传递至被热部101的热传递至散热部102。此外,热传导部件100通过散热部102向壳体1的外部释放热。
53.在本实施方式中,工作介质2是水,但也可以是水以外的介质。例如,工作介质 2也可以是甲醇和乙醇等醇化合物、氢氟烃等代替氯氟烃、丙烷和异丁烷等烃化合物、二氟甲烷等氟化烃化合物以及乙二醇等中的任意一种。工作介质2能够采用适于热传导部件100的使用环境的介质。
54.接下来,对芯构造体3和用于芯构造体3的形成的金属浆料5进行说明。图2 是芯构造体3的内部构造的示意图。图2示出用包含上下方向的平面假想地切断的芯构造体3的内部构造。另外,图3是用于芯构造体3的形成的金属浆料5的内部构造的示意图。
55.如上所述,热传导部件100具有多孔质的芯构造体3。芯构造体3是金属制的,并且是通过对金属浆料5进行加热处理而形成的。芯构造体3是后述的多个金属粒 31的烧结体。芯构造体3配置在第1金属板11上。液化后的工作介质2能够渗透到芯构造体3的内部。
56.如图2所示,芯构造体3包含多个金属粒31和粘合剂部32。
57.金属粒31在图3所示的金属浆料5中相当于烧结后的金属粒子51,形成芯构造体3的主要的骨架。在本实施方式中,金属粒31是实心的粒子。但是,并不限定于该例示,金属粒31可以是多孔质的,也可以在内部具有成为空隙的孔部。
58.粘合剂部32是图3所示的金属浆料5的粘合剂粒子52通过烧结熔融而凝固的金属
熔融体。熔融前的粘合剂粒子52的粒径例如为0.1μm以上且小于1μm。粘合剂部 32位于多个金属粒31的周围。粘合剂部32包含多个第1粘合剂部321和多个第2 粘合剂部322。
59.第1粘合剂部321将相邻的金属粒31彼此以小于1μm的距离连结起来。芯构造体3具有第1粘合剂部321。这样,能够抑制空隙部33的减少,并且将相邻的金属粒31彼此连结起来。第1粘合剂部321位于相邻的金属粒31之间或者其附近,通过使与它们接触的粘合剂粒子52烧结而形成。如上所述,熔融前的粘合剂粒子52的粒径小于1μm。另外,如后所述,芯构造体3在比较低的温度下烧结。因此,当位于相邻的金属粒31之间的粘合剂粒子52熔融而被烧固时,由第1粘合剂部321连结起来的金属粒31的间隔小于1μm。在芯构造体3中,金属粒31经由第1粘合剂部321 而呈网眼状相连。
60.第2粘合剂部322将一部分金属粒31与第1金属板11以小于1μm的距离连结起来。芯构造体3具有第2粘合剂部322。这样,能够抑制空隙部33的减少,并且将一部分金属粒31与第1金属板11连结起来。即,能够将芯构造体3固定于第1金属板11。另外,上述一部分金属粒31例如是多个金属粒31中的位于以小于1μm的距离与第1金属板11对置的位置的金属粒31。第2粘合剂部322是通过使位于金属粒31与第1金属板11之间或其附近的粘合剂粒子52烧结而形成的。如上所述,熔融前的粘合剂粒子52的粒径小于1μm。另外,芯构造体3在比较低的温度下烧结。因此,当位于金属粒31与第1金属板11之间的粘合剂粒子52熔融而被烧固时,基于第2粘合剂部322的金属粒31与第1金属板11的连结距离小于1μm。
61.在本实施方式中,金属粒31的材料为铜或者铜合金。通过采用热传导性较高的材料,芯构造体3能够将被热部101所释放的热高效地传递至工作介质2。
62.另外,在本实施方式中,金属粒31的材料与粘合剂部32的材料相同。例如,金属粒31和第1粘合剂部321的材料分别相同。这样,与经由不同的金属而连结的情况相比,能够经由第1粘合剂部321容易地将相邻的金属粒31彼此连结起来。因此,能够通过烧结更容易地形成芯构造体3。
63.另外,芯构造体3的材料与第1金属板11相同。例如,金属粒31、第2粘合剂部322以及第1金属板11的材料分别相同。这样,与将不同的金属彼此连结起来的情况相比,能够经由第2粘合剂部322容易地将金属粒31和第1金属板11连结起来。因此,能够容易地将芯构造体3固定在第1金属板11上。
64.接着,芯构造体3在内部具有空隙部33。空隙部33是供液体状态的工作介质2 通过的流路。空隙部33是通过利用第1粘合剂部321将金属粒31连结成网眼状而形成的。在本实施方式中,供工作介质2移动的空隙部33与芯构造体3的外部相连,并且在从上下方向观察时,从芯构造体3的外周缘部的一部分不间断且连续地连接至另一部分。例如,空隙部33从与在第1金属板11上配置有芯构造体3的配置面112 平行的方向上的芯构造体3的一端部连接至另一端部。另外,空隙部33从与在第1 金属板11上配置有芯构造体3的配置面112平行的方向上的芯构造体3的端部连接至芯构造体3中的从配置面112的法线方向观察时与被热部101重叠的加热部分30。
65.本实用新型研究人员发现,通过使金属粒31的平均粒径d50为20μm以上,能够实现这样的结构。另外,本实施方式的平均粒径d50是指根据规定数量的金属粒 31的粒径计算出的体积分布中的中值粒径,换言之是指50%粒径。规定数量例如为 100个以上。另外,金属粒31的粒径能够通过以下的方法求出。例如,根据芯构造体3的截面照片测量各个金属粒
31的面积,并将具有测量出的面积的圆的直径设为该金属粒31的粒径。即,能够求出上述的截面照片所拍摄到的金属粒31的球径作为该金属粒31的粒径。面积的测量例如使用图像解析软件。在图像解析软件中,通过将截面照片的灰度图像二值化,能够划分金属部分与空间而进行各部分的面积计算。另外,在测量时,粘合剂部32的尺寸与金属粒31相比足够小,因此可以忽略。另外,芯构造体3的截面的观察和拍摄的方法只要是能够容易地判别金属粒31和空隙部33 的方法即可,没有特别限定。优选在截面的观察中使用景深较深的扫描型电子显微镜。
66.如果金属粒31的平均粒径d50小于20μm,则空隙部33的连接在芯构造体3的内部中断或极度变窄而工作介质2难以通过。另外,近年来,要求使芯构造体3的厚度变薄,例如有时使其为0.5mm以下的尺寸。因此,如果金属粒31的平均粒径d50 超过200μm,则例如有可能无法利用0.5mm以下的薄型的芯构造体3形成上述的构造。因此,优选金属粒31的平均粒径d50为20μm以上且200μm以下。
67.根据本实施方式的芯构造体3,通过使金属粒31的平均粒径d50为20μm以上且200μm以下,空隙部33实现了从与配置面112平行的方向上的芯构造体3的一端部连接至另一端部,并且从芯构造体3的端部连接至加热部分30的构造。因此,从在从上下方向观察时与散热部102重叠的部分朝向加热部分30的工作介质2能够迅速地移动而不在芯构造体3的内部停止。即,能够提高输送热的工作介质2的移动效率。因此,能够提供具有工作介质的输送效率较高的芯构造体3的热传导部件100。
68.另外,优选金属粒31的平均粒径d50为50μm以上且100μm以下。如果平均粒径d50为50μm以上,则工作介质2在芯构造体3的内部的的移动速度进一步提高。例如,即使芯构造体3的厚度为0.25mm以下,也能够使工作介质2的移动速度比例如网眼形状的芯快。另外,如果平均粒径d50为100μm以下,则即使在薄型的芯构造体3中,也能够更可靠地形成上述的构造。
69.另外,关于金属粒31的平均粒径d50与空隙部33的连续性的连接之间的关系,在后面进行说明。
70.另外,将空隙部33的体积相对于芯构造体3的总体积的比例称为空隙率p。空隙率p的单位是%。空隙率p通过以下的方法来求出。例如,能够通过根据芯构造体 3的截面照片来测量空隙部33的面积并计算空隙部33的面积占整体的比例,从而求出空隙率p。芯构造体3的截面的观察和拍摄的方法只要是能够容易地判别金属粒31 和空隙部33的方法即可,没有特别限定。优选在芯构造体3的截面的观察中使用景深较深的扫描型电子显微镜。
71.另外,空隙率p也可以通过以下的计算来求出。即,将芯构造体3的总体积设为 v0cm3。将芯构造体3所包含的铜的体积设为v1cm3。将芯构造体3所包含的空间的体积设为v2cm3。在该情况下,v0=v1 v2。另外,如果将空隙率设为p,则p=v2/v0= (v0-v1)/v0=1-(v1/v0)。这里,v1=(铜的质量)/(铜的密度)=(芯构造体3 的质量)/(铜的密度)。铜的密度是已知的,为8.96g/cm3。另外,质量的单位为g。芯构造体3的质量和总体积v0能够通过测量或者计算来求出。因此,能够根据p=1
‑ꢀ
(v1/v0)来求出芯构造体3的空隙率p。
72.空隙率p对热传导部件100的热输送性能有很大的影响。例如,被热部101与散热部102的温度差δt是评价热传导部件100的热输送性能的指标,由δt=t1-t2 表示。这里,t1[℃]是在被发热体200加热的被热部101处测量出的温度。t2[℃] 是在放热部102处测量出
的温度,例如是在图1中的第2金属板12的与被热部101 相反的一侧的端部测量出的温度。温度差δt越小,越意味着在芯构造体3的内部充分地确保了工作介质2的流路,在被热部101与散热部102之间实现了高效的热输送。例如,如果温度差δt为5℃以下,则评价为热输送效率较高。
[0073]
优选芯构造体3的空隙率p为20%以上且80%以下。如果是20%≤p≤80%,则热传导部件100能够得到充分的热输送效率,并且能够防止强度的大幅降低,因此能够确保芯构造体3的寿命。与此相对,在空隙率p小于20%的情况下,温度差δt大幅大于5℃,热传导部件100无法得到充分的热输送效率。另外,在空隙率p大于80%的情况下,芯构造体3的强度有可能大幅降低。
[0074]
进一步优选空隙率p为40%以上且60%以下。如果是40%≤p≤60%,则热传导部件100的热输送效率进一步提高,由此容易实现温度差δt≤5℃,进而能够充分地确保芯构造体3的强度。
[0075]
接着,对用于芯构造体3的形成的金属浆料5的详细情况进行说明。如图3所示,金属浆料5包含金属粒子51、粘合剂粒子52以及树脂53。另外,金属粒子51相当于烧结前的金属粒31。
[0076]
树脂53在金属浆料5的加热处理温度下燃烧而消失。树脂53例如能够使用甲基纤维素、乙基纤维素等纤维素树脂、丙烯酸树脂、丁缩醛树脂、醇酸树脂、环氧树脂、酚醛树脂等。优选使用热分解性较高的丙烯酸树脂。
[0077]
金属浆料5还包含树脂53的分散介质(省略图示)。分散介质例如能够使用烃系溶剂、环醚系溶剂、酮系溶剂、醇系化合物、多元醇的酯系溶剂、多元醇的醚系溶剂、萜烯系溶剂以及它们的混合物等。例如优选使用沸点处于200℃附近的丁醇、松油醇。
[0078]
金属浆料5所包含的各成分的配合比只要适当设定为能够得到芯构造体3所期望的空隙率p即可。
[0079]
接下来,对本实施方式的热传导部件100的制造方法进行说明。图4是示出热传导部件100的制造工序的流程的流程图。图5a至图5d是示出热传导部件100的各制造工序的剖视图。图5a是涂覆步骤s110的示意图。图5b是烧结步骤s120的示意图。图5c是密封步骤s130中的配置步骤s131的示意图。图5d是密封步骤s130 中的接合步骤s132的示意图。
[0080]
热传导部件100的制造方法包含涂覆步骤s110、烧结步骤s120以及密封步骤 s130。
[0081]
如图5a所示,在涂覆步骤s110中,将包含多个金属粒子51和树脂53等的金属浆料5涂覆在第1金属板11上。金属浆料5涂覆于第1金属板11的凹部111的底面。优选的是,在涂覆步骤s110中,多个金属粒子51的平均粒径d50为20μm以上且200μm以下。通过使金属浆料5的金属粒子51的平均粒径d50为20μm以上且 200μm以下,能够实现从上下方向观察时与壳体1的外部相连的空隙部33从芯构造体3的端部连接至另一端部而且连接至加热部分30的构造。因此,从在从上下方向观察时与散热部102重叠的部分朝向加热部分30的工作介质2能够迅速地移动而不在芯构造体3的内部停止。即,能够提高输送热的工作介质2的移动效率。因此,通过本实施方式的制造方法,能够制造具有工作介质的移动效率较高的芯构造体3的热传导部件100。
[0082]
另外,优选金属粒子51的平均粒径d50为50μm以上且100μm以下。如果平均粒径d50
为50μm以上,则工作介质2在芯构造体3的内部的的移动速度进一步提高。例如即使芯构造体3的厚度为0.25mm以下,也能够使工作介质2的移动速度例如比网眼形状的芯快。另外,如果平均粒径d50为100μm以下,则即使在薄型的芯构造体3中,也能够更可靠地形成上述的构造。
[0083]
另外,优选的是,在涂覆步骤s110中,多个金属粒子51是通过雾化法制造的粉末。本实施方式的金属粒子51是通过水雾化法制造的粉末。或者,金属粒子51也可以是通过热处理法制造的粉末。在热处理法中,通过在例如惰性气体气氛下对通过其他制造方法制作的粉末进行加热,对其粒子形状、粒子内的金属组织热处理等进行改质。通过雾化法、热处理法制造的金属粒子51的表面例如比通过电解法制造的金属粒子的表面光滑。因此,能够使芯构造体3的空隙部33的内壁更光滑。因此,能够降低在空隙部33内移动的工作介质2相对于空隙部33的内壁的摩擦阻力。即,能够降低工作介质2的流路阻力,因此能够抑制工作介质2的移动速度的降低,从而能够提高工作介质2的热输送效率。但是,并不限定于这些例示,多个金属粒子51也可以是通过雾化法和热处理法以外的制法制作的粉末。例如,金属粒子51也可以是通过电解法制造的粉末。
[0084]
如图5b所示,在烧结步骤s120中,对金属浆料5进行加热,将树脂53烧除并且对金属粒子51进行烧结,由此形成多孔质的芯构造体3。例如,将在涂覆步骤s110 中涂覆在第1金属板11上的金属浆料5与第1金属板11一起放入到加热炉中进行加热。此时的加热温度例如为400℃,加热时间例如为1小时。另外,如上所述,金属浆料5包含金属粒子51、粘合剂粒子52、树脂53以及分散介质。通过金属浆料5 的加热,树脂53与分散介质一起烧除。此外,粘合剂粒子52由于烧结而熔融,形成第1粘合剂部321和第2粘合剂部322。
[0085]
即,一部分粘合剂粒子52的熔融体成为第1粘合剂部321,将相邻的金属粒子51彼此连结起来。另外,另一部分粘合剂粒子52的熔融体成为第2粘合剂部322,将一部分金属粒子51与第1金属板11连结起来。其结果为,形成具有成为工作介质 2的流路的空隙部33的芯构造体3。另外,通过适当地设定金属浆料5的各成分的配合比,芯构造体3成为具有20%以上且80%以下、优选40%以上且60%以下的空隙率p的多孔质。另外,由于金属粒子51的粒径比粘合剂粒子52的粒径大,因此与粘合剂粒子52相比不容易熔融且熔融较慢。因此,金属粒子51几乎不会改变粒子的形状而成为烧结后的金属粒31。即,烧结后的金属粒31的粒径与烧结前的金属粒子51 的粒径相比几乎没有变化。
[0086]
这里,加热炉中的加热温度只要是金属浆料5所包含的粘合剂粒子52熔融的温度以上即可。例如,可知在粘合剂粒子52是小于1μm的铜粒子的情况下,其在400℃以上的温度下熔融。另一方面,铜的熔点约为1085℃。因此,如果将金属浆料5加热至金属粒子51的材料的熔点附近,则金属粒子51也熔融,有可能难以得到多孔质的芯构造体3。因此,优选的是,在烧结步骤s120中,在400℃以上且600℃以下的温度下对金属浆料5进行加热。特别是,在烧结步骤s120中,期望在400℃以上的尽可能低的温度下对金属浆料5进行加热。通过使加热温度低于铜的熔点,能够抑制粒径较大的金属粒子51的熔融,并且能够对粘合剂粒子52进行低温烧结。因此,能够抑制或防止空隙率p的降低,并且能够在短时间内形成多孔质的芯构造体3。
[0087]
在密封步骤s130中,利用第2金属板12将第1金属板11上的芯构造体3与工作介质2一起进行密封。密封步骤s130包含配置步骤s131和接合步骤s132。如图 5c所示,在配置步
骤s131中,在通过烧结步骤s120形成了芯构造体3的第1金属板11上重叠配置第2金属板12。第2金属板12覆盖凹部111内的芯构造体3。如图 5d所示,在接合步骤s132中,在从上下方向观察时比芯构造体3靠外侧的位置,将第1金属板11和第2金属板12接合起来。由此,能够形成壳体1并在壳体1内的空间10中配置芯构造体3。进而,向空间10内注入工作介质2,通过接合将该注入口关闭。由此,能够使空间10密闭而在壳体1内的空间10中密封工作介质2和芯构造体3。
[0088]
接合步骤s132中的第1金属板11和第2金属板12的接合例如通过热压来进行。另外,并不限定于该例示,该接合也可以通过扩散接合、钎焊等来进行。
[0089]
接下来,对金属粒31和金属粒子51的平均粒径d50与空隙部33的连续性的连接之间的关系进行说明。在与芯构造体3的外部相连的空隙部33是从该芯构造体3 的外周缘部的一部分连续地与另一部分相连的流路的情况下,从芯构造体3的外部渗透的工作介质2不会在芯构造体3的内部停止而在芯构造体3内部移动,例如从芯构造体3的散热部102侧的部分向加热部分30迅速地渗透。与此相对,如果与芯构造体3的外部相连的空隙部33在该芯构造体3的内部中断或在中途极端变窄,则工作介质2的渗透有可能在芯构造体3的内部停止。因此,例如,工作介质2从芯构造体 3的散热部102侧的部分向加热部分30的移动延迟。
[0090]
因此,以下,使用各种改变了金属粒子51的平均粒径d50的金属浆料5,通过加热处理形成金属烧结体8,研究了各个金属烧结体8的内部中的空隙部33的连接状态。另外,金属烧结体8是与芯构造体3相同的多孔质。形成金属烧结体8的骨架的金属粒相当于芯构造体3的金属粒31。将在金属烧结体8中相邻的金属粒彼此连结起来的粘合剂部相当于芯构造体3的第1粘合剂部321。金属烧结体8的空隙部相当于芯构造体3的空隙部33。另外,也可以使用形成在第1金属板11上的芯构造体 3来代替金属烧结体8。
[0091]
分别制作使用了平均粒径d50为13μm、15μm、20μm、25μm、50μm、65μm、 100μm、150μm以及200μm的金属粒子51的金属浆料,并通过在非活性气体气氛下进行加热处理而形成i号至ix号的金属烧结体8。另外,金属浆料5的各成分以各自的金属烧结体8的空隙率p为45%的方式配合。各个金属烧结体8的材质和制法与实施方式的芯构造体3相同。另外,各个金属烧结体8是平面形状为长方形状且厚度例如为0.5mm的板状。
[0092]
金属烧结体8内部的空隙部的连接状态使用渗透测量装置500进行测量。图6 是渗透测量装置500的概略图。渗透测量装置500包含治具511、标尺512以及拍摄装置520。
[0093]
治具511以长度方向相对于与铅垂方向垂直的水平方向呈规定角度θ的姿势对金属烧结体8和标尺512进行保持。本实施方式的规定角度为θ=45
°
。治具511能够与金属烧结体8和标尺512一起沿铅垂方向移动。通过调整治具511的铅垂方向位置,金属烧结体8和标尺512能够在维持着上述姿势的状态下沿铅垂方向移动。
[0094]
标尺512与金属烧结体8平行地配置。标尺512例如具有以1mm的长度间隔沿长度方向排列的多个刻度513。以沿着金属烧结体8的标尺512的刻度513为基准,能够测量将金属烧结体8浸渍于工作介质2时的后述的渗透长度l。
[0095]
拍摄装置520对包含整个金属烧结体8和位于金属烧结体8附近的刻度513的动态图像进行拍摄。另外,由于工作介质2渗透的速度比较快,因此动态图像的帧率被设定得较高。拍摄装置520朝向金属烧结体8的表面的法线方向,与金属烧结体8 和标尺512对置配置。优选的是,拍摄装置520能够与治具511一起沿上下方向移动。这样,即使使治具511移
动,也能够将拍摄装置520相对于金属烧结体8的相对位置维持为恒定。
[0096]
使用上述的渗透测量装置500,利用渗透测量装置500测量工作介质2的渗透长度l、渗透速度v以及工作介质2在金属烧结体8的空隙部中的流动fv。
[0097]
渗透长度l是工作介质2通过毛细管现象而在金属烧结体8的内部渗透的长度方向的距离。具体而言,在将金属烧结体8的下端部浸渍于工作介质2的情况下,渗透长度l是从工作介质2的液面至金属烧结体8的内部的工作介质2的渗透范围的上端的距离。在本实施例中,在渗透范围的上端到达金属烧结体8的上端部的情况下评价为〇,在渗透范围的上端未到达金属烧结体8的上端部的情况下评价为
×
。
[0098]
渗透速度v是通过毛细管现象在金属烧结体8的内部浸透的工作介质2的长度方向上的速度。具体而言,渗透速度v是金属烧结体8的内部的工作介质2的渗透范围的上端的长度方向上的每单位时间的移动距离。在芯构造体3的加热部分30蒸发的工作介质2在散热部102被冷却,在液体状态下在芯构造体3内移动。为了降低热传导部件100的被热部101与散热部102的温度差δt,渗透速度v例如为0.5mm/sec 以上即可。因此,在本实施例中,在渗透速度v为0.5mm/sec以上的情况下评价为〇,在渗透速度v为1.5mm/sec以上的情况下评价为
◎
。另一方面,在渗透速度v小于 0.5mm/sec的情况下评价为
×
。
[0099]
根据工作介质2是否实际在空隙部的内部流动来评价金属烧结体8的空隙部的内部的工作介质2的流动fv。流动fv能够通过从拍摄装置520的动态图像放大各个帧的静态图像而在目视确认为金属烧结体8中的工作介质2已经渗透的部分中确认工作介质2是否在空隙部33的内部流动。在本实施例中,将能够确认工作介质2的流动的情况设为〇,将无法确认工作介质2的流动的情况设为
×
。
[0100]
图7是示出测量金属烧结体8的空隙部的连接状态的工序的流程的流程图。
[0101]
首先,在配置于作业台501的水平面上的容器502中充满工作介质2(步骤s201)。另外,在本测量中,使用纯水作为工作介质2。接下来,开始拍摄装置520的拍摄(步骤s202),使治具511向下方移动,将金属烧结体8和标尺512的下端部浸渍于工作介质2(步骤s203)。由此,能够通过拍摄装置520拍摄工作介质2向金属烧结体8 内的渗透状况。当通过目视或者动态图像确认工作介质2的渗透停止时(在步骤s204 中为“是”),停止由拍摄装置520进行的动态图像的拍摄(步骤s205)。
[0102]
接下来,拍摄金属烧结体8的截面照片,测量构成金属烧结体8的金属粒的平均粒径d50和该金属烧结体8的空隙率p(步骤s206)。另外,该平均粒径d50与烧结前的金属浆料5所包含的金属粒子51的平均粒径d50实质上相同。另外,使用 d50=13μm的金属粒子51制作了金属浆料5的i号金属烧结体8的金属粒的10%粒径d10为7μm,90%粒径d90为18μm。使用d50=15μm的金属粒子51制作了金属浆料5的ii号金属烧结体8的金属粒的10%粒径d10为8μm,90%粒径d90为20μm。使用d50=20μm的金属粒子51制作了金属浆料5的iii号金属烧结体8的金属粒的 10%粒径d10为15μm,90%粒径d90为25μm。使用d50=25μm的金属粒子51制作了金属浆料5的iv号金属烧结体8的金属粒的10%粒径d10为20μm,90%粒径d90 为40μm。使用d50=50μm的金属粒子51制作了金属浆料5的v号金属烧结体8的金属粒的10%粒径d10为35μm,90%粒径d90为75μm。使用d50=65μm的金属粒子51制作了金属浆料5的vi号金属烧结体8的金属粒的10%粒径d10为45μm,90%粒径d90为85μm。使用d50=100μm的金属粒子51制作了金属浆料5的vii号金属烧结体8的金属粒的10%粒径d10为80μm,90%粒径d90为120
μm。使用d50=150μm 的金属粒子51制作了金属浆料5的viii号金属烧结体8的金属粒的10%粒径d10 为130μm,90%粒径d90为170μm。使用d50=200μm的金属粒子51制作了金属浆料5的ix号金属烧结体8的金属粒的10%粒径d10为180μm,90%粒径d90为220μm。另外,测量出的空隙率p与作为最初的目标值的45%实质上相同。
[0103]
图8是示出各个芯构造体3的内部的空隙部33的连接状态的测量结果的表。另外,在图8中,透过率k表示在金属烧结体8的空隙部33内移动的工作介质2的透过的容易度,例如能够使用科泽尼-卡曼公式来计算。通常认为,如果透过率k为1
ꢀ×
10-11
mm2以上,则工作介质2良好地渗透。因此,在图8中,在透过率k为1
×ꢀ
10-11
mm2以上的情况下评价为〇,在透过率k小于1
×
10-11
mm2的情况下评价为
×
。
[0104]
如图8的fv的评价所示,能够确认在全部的金属烧结体8中,在目视确认为工作介质2已经渗透的部分工作介质2在空隙部33的内部流动。
[0105]
但是,如图8中的渗透长度l的评价所示,在平均粒径d50为15μm以下的i 号至ii号的金属烧结体8中,工作介质2未渗透至金属烧结体8的上端部。另一方面,在平均粒径d50为20μm以上的iii号至ix号的金属烧结体8中,工作介质2 渗透至金属烧结体8的上端部。
[0106]
另外,在平均粒径d50为15μm以下的i号至ii号的金属烧结体8中,工作介质 2的渗透速度v较慢,小于0.5mm/sec。另一方面,在平均粒径d50为20μm以上的 iii号至ix号的金属烧结体8中,渗透速度v为0.5mm/sec以上。该结果与基于平均粒径d50的透过率k的计算结果良好地匹配。另外,在平均粒径d50为50μm以上的v号至ix号的金属烧结体8中,渗透速度v为1.5mm/sec以上。
[0107]
综上所述,可以认为,在平均粒径d50为20μm以上的iii号至ix号的金属烧结体8中,金属烧结体8的内部的空隙部33在金属烧结体8的长度方向上从下端部不间断地连接至上端部。此外,在平均粒径d50为50μm以上的v号至ix号的金属烧结体8中,显示出良好的渗透速度v,工作介质2容易在空隙部33内移动。
[0108]
但是,薄型的金属烧结体8的形成在金属烧结体8的金属粒的平均粒径d50超过100μm时变得困难,在平均粒径d50低于50μm时变得困难。
[0109]
因此,可以认为,金属烧结体8的金属粒的平均粒径d50优选为20μm以上且 200μm以下,进一步优选为50μm以上且100μm以下。
[0110]
以上,对本实用新型的实施方式进行了说明。另外,上述的实施方式是例示,本领域技术人员应理解在本实用新型的范围内能够对其各结构要素和各处理的组合进行各种变形。
[0111]
本实用新型的热传导部件例如能够用作搭载于电子设备的基板或电子部件的散热用的部件。
再多了解一些
本文用于创业者技术爱好者查询,仅供学习研究,如用于商业用途,请联系技术所有人。