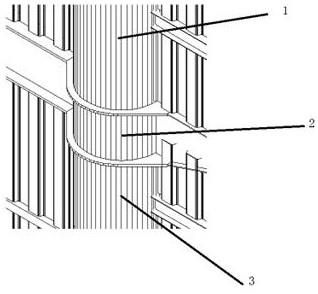
1.本发明涉及海上换流站建造技术领域,尤其为一种换流站上部组块模块化建造工艺。
背景技术:
2.换流站项目上部组块主结构由h型钢主次梁铺板结构及波形板 立柱斜撑组成,内部布设了换流阀组、gis、变压器、控制屏柜等主要电气设备及电气、管系、通风等附属件。实施换流站上部组块模块搭载技术的目的是为了提升搭载效率、压缩搭载周期,降低建造成本,所以在中组模块划分组合时需要解决本体结构强度,模块的整体完整性,模块施工作业和整体搭载的同步性问题。中组模块施工完成后,外形尺寸一般都比较大,且整体重量比较重,对其整体搭载提出了更高的要求,一方面需要解决其吊装过程平稳且无干涉位问题,另一方面又要解决模块落位时与相邻模块结构精确对位问题。对于船舶海工领域产品,国内外生产企业一般都采取先分段壳、舾、涂一体化建造,再结合产品结构特点及其外场搭载场地条件,生产计划,起重设备能力等因素确定在外场预先中组模块建造的大小及方式。船舶海工类产品模块式建造搭载的优势是能通过模块中组完整性施工和搭载作业分场地实施,实现时间上的同步性,压缩搭载场地占用时间,解决船企有限的搭载场地资源问题。除此之外,中组模块化搭载还能将管、电、舾附属件安装作业提前,能大量减少漆后动火问题并有助于高空作业低空化。
技术实现要素:
3.为解决上述问题,本发明旨在提供一种换流站模块划分建造搭载方法。通过模块的合理划分组合(可为同层组合,也可为上下组合),保证模块本体结构吊装搭载时的强度;确保模块地面制作时的整体完整性;实现模块施工和搭载作业的同步性。通过模块施工过程的焊接收缩量加放及质量管控,吊点的设计计算及模型预先理论干涉模拟,解决合拢时结构的精准定位问题并确保模块吊装过程平稳无干涉。
4.一种换流站上部组块模块化建造工艺,所述换流站上部组块为多层钢结构建筑物,包括各层的主次梁平台以及位于该层主次梁平台上的舱壁,其特征在于包括如下步骤:1).将上部组块划分为若干模块:1-1.模块采取正态划分,即主次梁平台上方舱壁划入分段模块内;避免因分段反造翻身引起的结构变形,进而减少后期为满足设备基础平整度而做的火工调整工作;1-2.涉及的设备基座、机、管、电等附属件同区划分,以减少合拢散装件,节约模块搭载时合拢口调整工作量;同时保证本模块上的设备布置均匀分散,能避免模块的重心偏心问题,有利于吊点的对称布设;1-3 .位于第一层主次梁平台下方与之对应的的dsf滑移发运基础胎架接触点位稀少,第一层主次梁平台的模块划分与接触支撑点位相对应,减少新设支撑胎架点位,可减
少施工工作量,达到降低生产成本的目的;1-4.位于第一层的换流阀厅不包含用于顶撑的舱室立柱,阀厅顶盖板分段搭载时底部无支撑顶托;将阀厅顶部分段先形成模块,并在模块四边甲板上方加装导向定位工装,以解决搭载落位无顶撑问题,减少工装使用成本;1-5.上部组块内部安装的换流阀、gis、变压器等主要电气设备,采取将设备的分体先进舱,在舱内再整体组装成设备的方式安装;模块划分时结合模块地面完整性施工构建成舱,并完成搭载工位上的设备安装,来压缩整体搭载周期;2).根据前述步骤1的划分结果建造上部组块模块;3).自下而上将建造的上部组块模块搭载形成所述上部组块:模块与模块之间主次梁h型钢合拢口设置“z”字型错位结构,即h型钢腹板和面板要求错开200mm;为避免后搭载模块合拢时发生落位干涉,必须要求后搭载模块上面板突出腹板,下面板缩进面板。除此以外还要注意合拢口舱壁划分问题。先搭载模块的舱壁不可突出分段断面,必要时做合拢散装处理;一方面在分段模块建造时要注重控制每层平台主次梁轴线开档的装配焊接尺寸精度和整体平整度,另一方面在模块同层组合或上下层组合时控制轴线开档精度或层高尺寸;最后,通过模型模拟确认可能发生干涉的情况,在底部预装支吊架施工作业时预留足够的安装空间来避免搭载干涉情况的发生。
5.所述的一种换流站上部组块模块化建造工艺,其进一步设计在于:在分段模块建造阶段统一要求将主次梁上过度半圆板作散装处理,以便在出现不对筋情况下,做局部微调处理。
6.所述的一种换流站上部组块模块化建造工艺,其进一步设计在于:步骤1)中,划分模块重量控制在起重设备的起重能力范围内,起吊时结构无受力变形,结构强度满足起重受力要求;即在确定模块具体的划分方式后,核算每个模块的重量及重心,然后根据总重量和重心布置吊点,并通过模拟软件进行吊装结构强度校核。
7.本发明的有益效果在于:1)换流站上部组块分段正态划分,即将本层甲板和甲板上方舱壁划入一个分段。既减少了分段搭载前的翻身过程,降低了分段变形风险,又为上下层分段进行模块组合,设备提前进舱安装提供了基础条件,同时还为悬挑附壁式脚手架模块化搭设创造了条件。也即,分段模块正态建造一方面可提高模块完整度,另一方面可简化施工流程,减少脚手架重复搭拆施工成本。
8.2)换流站上部组块第一层和第四层划分甲板片体模块搭载,解决了搭载时下部缺少顶升胎架支撑问题,可节约大量的支撑胎架工装材料及安装拆除施工工作量。项目上涉及此类情况的分段有12个,每个分段以平均设置8个顶升点计算,12个分段可减少直径不小于600mm,壁厚不小于12mm圆管立柱支撑材料1900m及直径不小于220mm,壁厚不小于10mm管材防倾支撑材料4000m。
9.3)换流站上部组块第二层和第三层分段上下组合为框架模块搭载,不仅解决了同层分段模块组合吊装结构强度不足问题,而且提高了封舱设备提前装入率,实现了高空作业低空化目标,做到了模块搭载的完整性。
10.4)换流站上部组块第五层布置了gis、连接变压器及站用变压器等大型设备,起吊组装这些设备需要消耗较长的时间,而使得6、7层搭载计划后延,从而影响项目的交期。将布置有大型设备的分段中组模块化后先行吊装搭载,可实现设备安装及五层周边其它模块搭载的同步性作业,为项目压缩了搭载周期。
11.5)换流站上部组块分段模块在车间建造时,将本分段主立柱对应的反底半圆板加强作散装处理。待搭载时若因累积误差产生上下层主立柱不对筋的情况,可适当微调合拢散装半圆管,使得上下贯通的主立柱板厚方向对接光顺。采用此做法可避免因主立柱对接错位,而需要将立柱焊缝整体去除调整后重新恢复产生的大量施工工时和焊材浪费的问题。
附图说明
12.图1 第一层104 105 106以及110 111 112 108两块甲板片体模块组合。
13.图2 第四层404 405 406/410 411 412甲板片体模块。
14.图3 二三层框架模块及模块完整性预装结构。
15.图4 五层设备层502 503模块组合。图5 五层设备层508 509模块组合。
16.图6为上层立柱、下层立柱以及过渡半圆板结构示意图。
17.图7为图6中所示结构去除过渡半圆板后的上层立柱、下层立柱结构示意图。
具体实施方式
18.以下结合说明书附图以及实施例对本发明进行进一步说明:三峡新能源江苏如东海上换流站属国内首座海上换流站,目前也是世界上最大的海上换流站,共六层。其上部组块换外形轴线尺寸达89mx78mx46m,重量约为20000t。采用模块式建造搭载方式来压缩建造周期,改善施工环境,节约生产成本是十分必要的。本专利所述的换流站模块化建造技术,是结合本体结构特点、本体设备布置、外场搭载场地资源、生产计划安排总结的一种换流站上部组块模块化建造技术。
19.1).将上部组块划分为若干模块,对划分模块的编号规则:编号由三位数组成,第一个数字为层号,后两位数字为模块序号,如104模块,表示第一层的第4个模块。
20.模块采取正态划分,即主次梁平台上方舱壁划入分段模块内;避免因分段反造翻身引起的结构变形,进而减少后期为满足设备基础平整度而做的火工调整工作;涉及的设备基座、机、管、电等附属件同区划分,以减少合拢散装件,节约模块搭载时合拢口调整工作量;同时保证本模块上的设备布置均匀分散,能避免模块的重心偏心问题,有利于吊点的对称布设;位于第一层主次梁平台下方与之对应的的dsf滑移发运基础胎架接触点位稀少,第一层主次梁平台的模块划分与接触支撑点位相对应,减少新设支撑胎架点位,可减少施工工作量,达到降低生产成本的目的;为解决上部组块第一层搭载时,如图1所示,第一层主次梁平台下方与之对应的的dsf滑移发运基础胎架接触点位稀少问题。根据分段划分图,分别将104 105 106及108 110 111 112组成图中所示的两块甲板片体模块。104 105 106片体模块外形尺寸为52x29m,重量为520t,108 110 111 112片体模块外形长宽尺寸为
52x38m,重量为800t。组合为中组模块后,可大量减少单个分段搭载需独立设置工艺顶升胎架带来的施工量及材料成本的增加问题。倘若7个分段单独搭载,每个分段按8个顶升胎架设置,需设置56个胎架。而组合为两个中组模块后,仅需设置13个顶升胎架。同时为了避免后期因施工空间限制而造成顶升胎架拆除困难的问题,巧妙的将顶升胎架底部焊接固定在dsf滑移工装的纵梁上表面。拆除胎架时,仅需修割腾空顶升胎架上部连接点即可。
21.如图2所示,位于第一层的换流阀厅不包含用于顶撑的舱室立柱,阀厅顶盖板分段搭载时底部无支撑顶托;将阀厅顶部分段先形成模块,并在模块四边甲板上方加装导向定位工装4,以解决搭载落位无顶撑问题,减少工装使用成本;为解决换流阀厅未设计舱室立柱,阀厅顶盖板分段搭载时底部无支撑顶托的问题,根据分段划分图,将阀厅顶盖板分段404 405 406,410 411 412形成甲板片体模块。组合后单个中组模块外形尺寸为54x32m,重量为500t。为解决中组模块搭载时下方无胎架支撑问题,创新性在甲板每条边缘高度大于1000m的h型钢上方加装4个导向卡板工装(共12个),搭载时依靠导向工装与相邻接已搭载分段之间的搭接来传递分载本模块自身重量。尤为需要注意是:为预防模块搭载时因分段自重弹性下挠不均,导致导向卡板工装不能同时与邻接分段接触,而产生个别导向卡板工装受力过载的安全风险发生。每个导向卡板设计时要加放足够的结构强度余量,为此,设计的每个导向卡板结构强度需要求满足支撑1/2模块自身重量。运用上述模块方案搭载,可节约下方临时设置支撑胎架引起的施工及材料增加成本。假设6个分段单独搭载,每个分段按8个顶升胎架设置,需设置48个支撑胎架。
22.上部组块内部安装的换流阀、gis、变压器等主要电气设备,采取将设备的分体先进舱,在舱内再整体组装成设备的方式安装;模块划分时结合模块地面完整性施工构建成舱,并完成搭载工位上的设备安装,来压缩整体搭载周期;具体而言 ,如图4-图5所示,为解决第五层gis,连接变压器、站用变压器等大型设备组合安装周期长,会影响后续分段搭载进度推进问题。根据五层大型设备分布图,将分段502 503及508 509组成两个模块,以利于设备独立整体安装。502 503模块外形尺寸为44.1x35.8m,重量为910t,508 509模块外形尺寸为44.5x35.8m,重量为834t。两个中组模块提前在地面中组为模块后先行搭载,不仅为设备提前组装赢得了时间,而且为周边分段模块的连续性搭载创造了条件。实现了设备安装和项目搭载动作的同步性,压缩了总体搭载周期,为确保项目按期交付打下了基础。
23.2).根据前述步骤1的划分结果建造上部组块模块。
24.3).自下而上将建造的上部组块模块搭载形成所述上部组块:通过模型模拟确认可能发生干涉的情况,在底部预装支吊架施工作业时预留足够的安装空间来避免搭载干涉情况的发生。
25.模块与模块之间主次梁h型钢合拢口设置“z”字型错位结构,即h型钢腹板和面板要求错开200mm;为避免后搭载模块合拢时发生落位干涉,必须要求后搭载模块上面板突出腹板,下面板缩进面板。除此以外还要注意合拢口舱壁划分问题。先搭载模块的舱壁不可突出分段断面,必要时做合拢散装处理。
26.一方面在分段模块建造时要注重控制每层平台主次梁轴线开档的装配焊接尺寸精度和整体平整度,另一方面在模块同层组合或上下层组合时控制轴线开档精度或层高尺寸。
27.如图6-图7所示,在分段模块建造阶段统一要求将主次梁上过渡半圆板2作散装处
理,具体而言,上层立柱1下方设置位于下层立柱3上侧过渡半圆板2。以便在出现不对筋情况下,做局部微调处理。
28.步骤1)中,划分模块重量控制在起重设备的起重能力范围内,起吊时结构无受力变形,结构强度满足起重受力要求;即在确定模块具体的划分方式后,核算每个模块的重量及重心,然后根据总重量和重心布置吊点,并通过模拟软件进行吊装结构强度校核。
再多了解一些
本文用于创业者技术爱好者查询,仅供学习研究,如用于商业用途,请联系技术所有人。