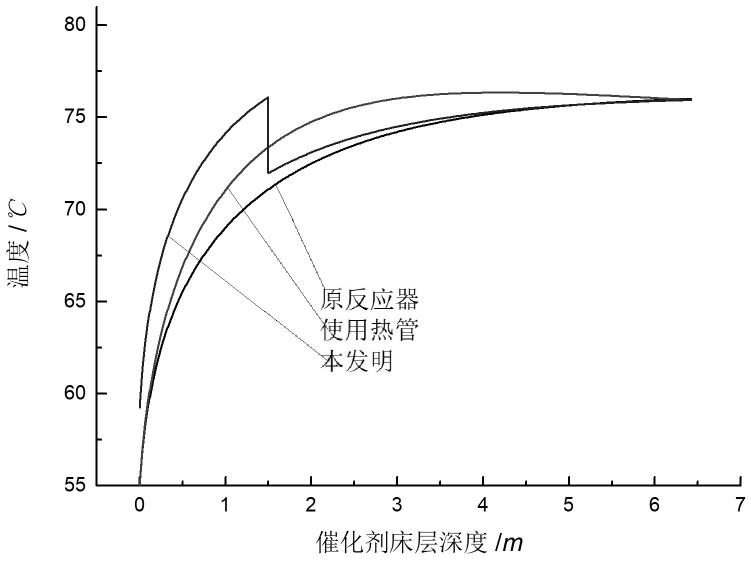
一种可不停工更换催化剂的双酚a反应器及其使用方法
技术领域
1.本发明涉及在有羟基或氧-金属基连接在六元芳环碳原子上化合物的制备技术领域,特别是涉及一种可不停工更换催化剂的双酚a反应器及其使用方法。
背景技术:
2.双酚a是环氧树脂、聚碳酸酯、聚苯醚树脂、聚砜树脂、不饱和聚酯树脂等多种人工合成树脂的原料,还用于增塑剂、阻燃剂、橡胶防老剂、热稳定剂、涂料、农药等。随着国民经济的高速发展,双酚a的应用越来越广泛。
3.双酚a反应器是双酚a生产装置的关键设备,其运行状况直接影响双酚a产量。双酚a合成反应为放热反应(-90kj/mol,[applied catalysis, 1988,37:129-138]),且有平行副反应发生,为了保证转化率与选择性,进料温度不能过高,其最佳进料温度处在双酚a的结晶温度边缘(高校化学工程学报,2004 , 18 (3) :367-370)。
[0004]
双酚a合成过程中,由于催化剂会在使用过程中失活,因此需大量消耗树脂催化剂。通常状况下,一个双酚a反应器内装载百吨上下的催化剂,并需要一年一换甚至半年一换。但双酚a合成催化剂的失活速率,实际上是不同步的,呈现出一种越靠上则失活越快的趋势。(prokop z , hankova l , jerabek k . bisphenol a synthesis
ꢀ–ꢀ
modeling of industrial reactor and catalyst deactivation[j]. reactive & functional polymers, 2004, 60(julsi):77-83.)在更换催化剂的时候,通常反应器底部的催化剂依然能用,但却必须全部更换,从而造成严重的浪费。除此之外,更换催化剂的时候反应器必须停工,不仅使得生产能力下降,而且造成很大的负荷波动(举例来讲,本来后续工序需要处理三个反应器的出料,关了一个后就只能处理两个的,后续的分离、再生等各工序都是为三个反应器的物料设计的,这种情况下就必须调整后续所有工序的参数,等换完还需要再调回来),连带造成后续工序中出现不稳定状况。
[0005]
双酚a析出堵塞催化剂床层是困扰双酚a生产的另一大顽疾,堵塞会造成无法正常生产,频繁开停车不仅减少产量,而且产生大量不合格产品,开停车过程中还容易向环境中排放大量污染物。南通星辰(蓝星)的双酚a装置,因催化剂床层堵塞,多次停车并将尚新鲜的催化剂(5台反应器,每台装催化剂百吨以上)提前报废,损失巨大。天津双孚的双酚a装置,甚至因此而亏损停产。常见的解决方案有提升进料温度,提升进料温度(在最佳进料温度的基础上提升),不仅消耗了更多加热蒸汽,而且会导致反应器下半部分过热,产生更多副产物(一般而言,反应器中需要避免出现高于80℃的地方,如果工艺参数导致有这种地方出现,需采用水套或冷却盘管进行冷却)。另一个常见的解决方案为提升进料中溶剂苯酚的摩尔比,但这不仅降低了生产能力,而且给后续的脱酚步骤带来了更大的负担,使本就容易出故障的薄膜蒸发器等设备故障率更高(如燕山石化的双酚a装置,其薄膜蒸发器屡屡密封失效或是停转,提升机经常卡住不动)。除上述这些之外,cn108774113b 双酚a的生产装置及其生产方法,公开了一种利用热管将一部分反应热从较热的反应器底部转移到较冷的反应器顶部,从而避免反应器堵塞的方法。但在实际使用中发现,这种方法需要使用到2000多
根贯穿整个催化剂床层(6米厚)的铜质热管,不仅很大程度上提升了反应器的成本,而且给反应器内催化剂的装卸带来了很大的难度。除此之外,这些热管由于数量多且细长,非常容易损坏。
[0006]
发明人研究中发现,现有的双酚a合成反应器,其催化剂床层中下段的温度高于常压下丙酮的沸点,且丙酮溶解于苯酚中会大量放热。
技术实现要素:
[0007]
本发明提供一种可不停工更换催化剂的双酚a反应器及其使用方法。
[0008]
解决的技术问题是:1.更换双酚a反应器中的催化剂需使反应器停工,不仅使得生产能力下降,而且造成很大的负荷波动;2.更换双酚a反应器中的催化剂时,会把反应器中仍可使用的催化剂一并更换掉,造成严重的浪费;3.双酚a的反应器的最佳进料温度处在双酚a的结晶温度边缘,导致反应器容易堵塞,但直接提升进料温度易造成反应器后半部分过热。
[0009]
为解决上述技术问题,本发明采用如下技术方案:一种可不停工更换催化剂的双酚a反应器,用于以苯酚和丙酮为原料通过非均相催化反应合成双酚a,包括反应液自上而下流经催化剂床层的固定床反应器,还包括用于临时储存反应液的缓冲罐以及用于临时采出及放回反应液的双向泵;所述固定床反应器内包含上床层与下床层两个相互隔开的催化剂床层,所述上床层与下床层位置的反应器筒体上均带有催化剂加料口以及催化剂卸料口,每个催化剂床层底部分别设置有密封板,两个密封板上均开有反应液采出口;所述双向泵一端与缓冲罐通过管道连通,另一端分别通过管道与两个密封板上的反应液采出口连通,双向泵与上床层之间的管道上设置有上放空阀,双向泵与下床层之间的管道上设置有下放空阀;所述上床层上方设置有液体分布器,下床层上方设置有液体再分布器,反应器的进料管通过一进二出的进料去向三通阀分别与液体分布器及液体再分布器连通,反应器的出料管通过二进一出的采出来源三通阀分别与两个密封板上的反应液采出口连通。
[0010]
进一步,所述双酚a反应器的进料分为新鲜丙酮以及丙酮以外的组分两部分,丙酮以外的组分记作丙外组分;所述双酚a反应器还包括利用采出的反应液汽化新鲜丙酮的丙酮汽化换热器,采出来源三通阀的阀后管道通入采出泵的进液口,采出泵的出液口通过管道与丙酮汽化换热器的热流体入口连通;所述下床层下方还设置有用于在原有的出料管被接入到丙酮汽化换热器后起出料作用的新增出料管,所述新增出料管上端与下床层下方的密封板上的反应液采出口连通,新增出料管上设置有底阀;所述丙酮汽化换热器的热流体出口通过管道与一进二出的采出去向三通阀的入口连通,采出去向三通阀的两根出口管分别与新增出料管位于底阀后的部分以及液体再分布器连通;所述丙酮汽化换热器的冷流体入口与新鲜丙酮的来源管道连通,且冷流体出口通
过管道通入气液混合器的气相入口,所述丙外组分的来源管道与气液混合器的液相入口连通,所述气液混合器的出口与进料去向三通阀的入口通过管道连通。
[0011]
进一步,所述丙酮汽化换热器为列管式换热器,新鲜丙酮经管程流经列管式换热器。
[0012]
进一步,所述丙酮汽化换热器为双管程的换热器,且管程竖直设置。
[0013]
进一步,丙酮汽化换热器的冷流体出口处的流体静压强记作p,丙酮在p下的沸点记作h,所述上床层底部的温度不小于h。
[0014]
进一步,所述丙酮汽化换热器的冷流体出口处的流体静压强为常压,所述气液混合器为文丘里管,所述气液混合器的气相入口设置在文丘里管的喉部。
[0015]
一种可不停工更换催化剂的双酚a反应器的使用方法,用于更换上述的一种可不停工更换催化剂的双酚a反应器中的催化剂,其中,进料去向三通阀切向液体分布器时的状态记作a状态,切向液体再分布器时的状态记作b状态;采出来源三通阀切向上床层时的状态记作a状态,切向下床层时的状态记作b状态;采出去向三通阀切向液体再分布器时的状态记作a状态,切向新增出料管时的状态记作b状态;反应器正常运行状态下,进料去向三通阀、采出来源三通阀以及采出去向三通阀处于a状态,上放空阀、下放空阀关闭,底阀开启,双向泵关闭,采出泵开启;上床层和下床层的催化剂的更换相互独立进行;则更换上床层中的催化剂分为以下步骤:步骤1a:进料去向三通阀、采出来源三通阀以及采出去向三通阀均切到b状态,然后上放空阀打开,双向泵向外抽液;步骤2a:待上床层中反应液抽干,更换上床层中的催化剂;步骤3a:催化剂更换完成,双向泵反向运行,将反应液输回上床层;步骤4a:上放空阀关闭,双向泵关闭,然后进料去向三通阀、采出来源三通阀以及采出去向三通阀均切到a状态;更换下床层中的催化剂分为以下步骤:步骤1b:底阀关闭,采出去向三通阀切到b状态,然后下放空阀打开,双向泵向外抽液;步骤2b:待下床层中反应液抽干,更换下床层中的催化剂;步骤3b:催化剂更换完成,双向泵反向运行,将反应液输回下床层;步骤4a:下放空阀关闭,双向泵关闭,然后采出去向三通阀切到a状态,底阀打开。
[0016]
进一步,所述缓冲罐为保温罐,缓冲罐与固定床反应器之间的各管道、进料去向三通阀的两根出口管、采出来源三通阀的两根入口管、采出去向三通阀的两根出口管、以及新增出料管位于和采出去向三通阀出口管的交叉位置上方的部分均为电伴热管道;在步骤1a、1b、4a以及4b开始之前,先借助电伴热融化管内滞留物料。
[0017]
进一步,步骤2a以及步骤2b中,先沿催化剂卸料口卸出旧催化剂,然后沿催化剂加料口加入经苯酚润湿的新催化剂。
[0018]
进一步,每段催化剂床层中,更换催化剂的时机为该段催化剂床层已经充分失活;每段催化剂床层中,催化剂是否已充分失活采用以下方式判断:刚填充完新鲜催化剂时,经过该段催化剂床层后丙酮的转化率记作m,实际的丙酮转化率记作n,若n/m小于0.6,则认为
该段催化剂床层已充分失活。
[0019]
本发明一种可不停工更换催化剂的双酚a反应器及其使用方法与现有技术相比,具有如下有益效果:本发明中,通过把催化剂床层分成两段,更换催化剂时,只更换其中一段,依靠另一段催化剂床层维持反应器的运转,不需要在更换催化剂时使整个反应器停工,反应器出料的流量不会发生变化,更换结束后再把被更换的催化剂中含有的反应器注回,不会因为需要填充催化剂之间的间隙而导致流量波动,整个更换过程中不会对后续工序造成流量波动;本发明中,由于更换催化剂时只更换其中失活严重的一段,而不是全部更换,不会把尚能使用的另一半催化剂也一并更换,极大减少了催化剂的浪费;本发明中,为实现不停工更换催化剂,反应器存在抽出中部的反应液以及对进料和出料的分流设备,通过在此基础上嫁接一个丙酮汽化换热器,将进料中的新鲜丙酮拆分出来(在被汽化前不跟苯酚以及循环的物料混合),与反应器中段的热反应液在丙酮汽化换热器中进行换热,使新鲜丙酮汽化后携带大量的反应热汇入到进料中,从而显著提升进入催化剂床层的反应液温度,避免较冷的上床层出现结晶堵塞;同时反应器中段的热反应液被冷却后返回下床层,不会像直接提升进料温度那样使下床层因为过热而大量发生副反应;且由于利用的是相变换热,可使得丙酮汽化换热器体积很小,避免设备成本过高(因为苯酚有腐蚀性,设备需要用昂贵的不锈钢制作);本发明中,由于可以利用反应热加热进料,反应器的进料温度可以比传统的反应器低很多(由55℃混合进料,降低到50.6℃的丙外组分加25℃的丙酮),从而显著减少了预热反应器进料的能耗。
附图说明
[0020]
图1为本发明一种可不停工更换催化剂的双酚a反应器的结构示意图;图2为各种不同反应器的催化剂床层温度分布图,为方便比较,本发明中的反应器,其上床层与下床层,视作一个连续的整体(也即上床层的底端的深度,与下床层顶端的深度相同;其中,11-上床层,12-下床层,2-丙酮汽化换热器,3-气液混合器,4-双向泵,5-缓冲罐,61-进料去向三通阀,62-采出来源三通阀,63-采出去向三通阀,71-上放空阀,72-下放空阀,8-底阀。
具体实施方式
[0021]
如图1所示,一种可不停工更换催化剂的双酚a反应器,用于以苯酚和丙酮为原料通过非均相催化反应合成双酚a,包括反应液自上而下流经催化剂床层的固定床反应器,还包括用于临时储存反应液的缓冲罐5以及用于临时采出及放回反应液的双向泵4;固定床反应器内包含上床层11与下床层12两个相互隔开的催化剂床层,上床层11与下床层12位置的反应器筒体上均带有催化剂加料口以及催化剂卸料口,每个催化剂床层底部分别设置有密封板,两个密封板上均开有反应液采出口;这里上床层11与下床层12的厚度可以不等,一般情况下上床层11由于更换更频
繁,因此最好薄一些,在刚更换完催化剂时能够使经过该床层的丙酮转化60%(反应主要在上床层11中进行,其虽然薄,但大部分丙酮是在上床层11中转化的)即可。
[0022]
双向泵4一端与缓冲罐5通过管道连通,另一端分别通过管道与两个密封板上的反应液采出口连通,双向泵4与上床层11之间的管道上设置有上放空阀71,双向泵4与下床层12之间的管道上设置有下放空阀72;上床层11上方设置有液体分布器,下床层12上方设置有液体再分布器,反应器的进料管通过一进二出的进料去向三通阀61分别与液体分布器及液体再分布器连通,反应器的出料管通过二进一出的采出来源三通阀62分别与两个密封板上的反应液采出口连通。
[0023]
也就是说,本实施例中设计了从反应器抽出中部的反应液以及对进料和出料的分流设备,但这部分设备在反应器正常工作的时候是闲置的,因此这里考虑了在这些设备基础上再嫁接一个丙酮汽化换热器2,充分利用上这部分设备来进行进料的预热。后续更换催化剂的操作也是基于嫁接了丙酮汽化换热器2的系统进行的。如果没有嫁接丙酮汽化换热器2,那么后续更换催化剂的操作只需去掉对底阀8以及采出去向三通阀63的操作即可。
[0024]
双酚a反应器的进料分为新鲜丙酮以及丙酮以外的组分两部分,丙酮以外的组分记作丙外组分;注意,双酚a合成采用的原料虽然是苯酚以及丙酮,但由于苯酚与丙酮在反应器中并不能完全反应,因此反应器的进料还包括循环物料,也即反应后的反应液在分离出部分双酚a后,返回到反应器中。反应器的进料,就是由新鲜苯酚、新鲜丙酮以及循环物料混合而成,这里的丙外组分,指的是新鲜丙酮以及循环物料的混合物。循环物料中成分复杂,包括未反应的苯酚丙酮,以及未分离完的双酚a,还含有很多副产物,本文中这些副产物统称为杂质。
[0025]
双酚a反应器还包括利用采出的反应液汽化新鲜丙酮的丙酮汽化换热器2,采出来源三通阀62的阀后管道通入采出泵的进液口,采出泵的出液口通过管道与丙酮汽化换热器2的热流体入口连通;下床层12下方还设置有用于在原有的出料管被接入到丙酮汽化换热器2后起出料作用的新增出料管,新增出料管上端与下床层12下方的密封板上的反应液采出口连通,新增出料管上设置有底阀8;丙酮汽化换热器2的热流体出口通过管道与一进二出的采出去向三通阀63的入口连通,采出去向三通阀63的两根出口管分别与新增出料管位于底阀8后的部分以及液体再分布器连通;丙酮汽化换热器2的冷流体入口与新鲜丙酮的来源管道连通,且冷流体出口通过管道通入气液混合器3的气相入口,丙外组分的来源管道与气液混合器3的液相入口连通,气液混合器3的出口与进料去向三通阀61的入口通过管道连通。
[0026]
这里之所以选择把上床层11底部的反应液引出,而不是把反应器催化剂床层最底部的更热的反应液引出。是因为考虑到如果选用反应热来加热进料使其温度升高的话,可能会导致反应器下半部分过热,导致大量的副产物产生,因此这里把上床层11底部的反应液引出,用新鲜丙酮对其进行冷却后再返回到反应器中,可避免反应器下半部分过热。而之所以利用丙酮来携带反应热,而不是直接让流出反应器的反应液与进料换热,是为了利用相变换热的高换热系数而缩小所需的换热面积,同时还能利用上丙酮的溶解热。这对降低设备成本而言非常有必要,因为换热器需要用昂贵的不锈钢来制作以抵抗苯酚的腐蚀。
[0027]
丙酮汽化换热器2为列管式换热器,新鲜丙酮经管程流经列管式换热器。丙酮汽化换热器2为双管程的换热器,且管程竖直设置。这里之所以选用列管式换热器,是因为列管
式换热器在化工厂容易得到,并且本发明中的所需的换热面积不大,冷热流体的温差也很明显,不需要用到诸如板式换热器之类的特殊换热器。而之所以把新鲜丙酮设置在管程,是因为在实际使用中发现,如果新鲜丙酮设置在壳程的话,会因为强烈的汽化过程而给整个反应器带来剧烈的震动。而之所以选用双管程,是为了方进一步减小换热器体积,降低不锈钢的消耗。这里双管程的换热器最好选用u型管换热器,以减少热应力的影响。这里之所以把换热器竖着放,是因为换热器的换热管内是气液混合物,如果把换热器平放的话,管道上半部分与丙酮液体的接触不佳。
[0028]
丙酮汽化换热器2的冷流体出口处的流体静压强记作p,丙酮在p下的沸点记作h,上床层11底部的温度不小于h。
[0029]
也就是说这里要确保上床层11底部的温度高于丙酮的沸点,从而使丙酮能够汽化。这里温度的控制是依靠控制上床层11以及下床层12的厚度来进行的,具体而言就是先对相同条件下(不引出上床层11底部的反应液,反应液从上到下连续流过整个反应器,别的条件都相同)的常规反应器内的温度分布进行模拟计算,得出催化剂床层深度以及温度的函数关系,然后把高于丙酮的沸点且满足换热所需温差的部分作为下床层12。
[0030]
丙酮汽化换热器2的冷流体出口处的流体静压强为常压,气液混合器3为文丘里管,气液混合器3的气相入口设置在文丘里管的喉部。
[0031]
为确保反应液顺利流过反应器内的催化剂床层,反应器的进料压强是明显高于常压的,一般为三个大气压的绝压。但在三个大气压下,丙酮的沸点将会高于上床层底部反应液的温度,导致丙酮不能汽化。因此本实施例中通过降低新鲜丙酮的静压强,使其容易汽化。但这又带来了一个新的问题,也就是丙酮蒸汽无法汇入到丙外组分中,因此本实施例中采用喉部带有负压的文丘里管作为气液混合器3,丙酮蒸汽汇入到低温的丙外组分后立刻溶解。
[0032]
一种可不停工更换催化剂的双酚a反应器的使用方法,用于更换上述的一种可不停工更换催化剂的双酚a反应器中的催化剂,其中,进料去向三通阀61切向液体分布器时的状态记作a状态,切向液体再分布器时的状态记作b状态;采出来源三通阀62切向上床层11时的状态记作a状态,切向下床层12时的状态记作b状态;采出去向三通阀63切向液体再分布器时的状态记作a状态,切向新增出料管时的状态记作b状态;反应器正常运行状态下,进料去向三通阀61、采出来源三通阀62以及采出去向三通阀63处于a状态,上放空阀71、下放空阀72关闭,底阀8开启,双向泵4关闭,采出泵开启;上床层11和下床层12的催化剂的更换相互独立进行;每段催化剂床层中,更换催化剂的时机为该段催化剂床层已经充分失活。每段催化剂床层中,催化剂是否已充分失活采用以下方式判断:刚填充完新鲜催化剂时,经过该段催化剂床层后丙酮的转化率记作m,实际的丙酮转化率记作n,若n/m小于0.6,则认为该段催化剂床层已充分失活。当然实际使用中这个值可以根据实际情况进行调整,本实施例中的这个值是一个在大部分反应器中都适用的值。
[0033]
则更换上床层11中的催化剂分为以下步骤:步骤1a:进料去向三通阀61、采出来源三通阀62以及采出去向三通阀63均切到b状态,然后上放空阀71打开,双向泵4向外抽液;步骤2a:待上床层11中反应液抽干,更换上床层11中的催化剂;具体如何判断是否
反应液抽干,可以在双向泵4的一个接口上设置一段透明的管道来观察,下同;步骤3a:催化剂更换完成,双向泵4反向运行,将反应液输回上床层11;步骤4a:上放空阀71关闭,双向泵4关闭,然后进料去向三通阀61、采出来源三通阀62以及采出去向三通阀63均切到a状态;更换下床层12中的催化剂分为以下步骤:步骤1b:底阀8关闭,采出去向三通阀63切到b状态,然后下放空阀72打开,双向泵4向外抽液;步骤2b:待下床层12中反应液抽干,更换下床层12中的催化剂;步骤3b:催化剂更换完成,双向泵4反向运行,将反应液输回下床层12;步骤4a:下放空阀72关闭,双向泵4关闭,然后采出去向三通阀63切到a状态,底阀8打开。
[0034]
本文所有的阀门均为与dcs系统电连接的自动阀,双向泵4的开关同样与dcs系统电连接,切阀与切泵的操作在dcs系统中自动进行。
[0035]
缓冲罐5为带有呼吸阀的保温罐,缓冲罐5与固定床反应器之间的各管道、进料去向三通阀61的两根出口管、采出来源三通阀62的两根入口管、采出去向三通阀63的两根出口管、以及新增出料管位于和采出去向三通阀63出口管的交叉位置上方的部分均为电伴热管道;在步骤1a、1b、4a以及4b开始之前,先借助电伴热融化管内滞留物料。
[0036]
这些管道中都涉及到物料滞留(也即管内有物料,但不流动)的情况,一个管道分支使用时,另一个分支内存在物料滞留,滞留的物料会因为冷却而逐渐凝固,导致后续再启用这个分支时无法进行,因此在启用前需要对滞留的物料进行加热融化。一般情况下在管内设置测温装置,把物料加热到76℃即可。在催化剂更换完成后,最好把滞留物料给放空,以免其长时间滞留而变质。
[0037]
步骤2a以及步骤2b中,先沿催化剂卸料口卸出旧催化剂,然后沿催化剂加料口加入经苯酚润湿的新催化剂。
[0038]
苯酚润湿的主要目的是补充被旧催化剂表面带走的反应液。苯酚润湿还有额外一项好处,就是从缓冲罐5打回反应器的反应液是已经反应过的,在进入催化剂颗粒前需要把颗粒里面的苯酚逐渐取代掉才能继续进行反应,不会立即发生反应而造成过热。
[0039]
如图2所示:本实施例中还对比了三种反应器内的温度分布,三种反应器分别记作原反应器、使用热管、本发明,三者的规格如下:原反应器:固定床反应器,反应液自上下而下流经催化剂床层,催化剂床层直径5.1米高6.42米,进料温度55℃,压力三个大气压的绝压,含1.175kg/s的双酚a、9.7625kg/s的苯酚、0.4375 kg/s的丙酮、1.125kg/s的杂质。
[0040]
使用热管:在原反应器的基础上,向催化剂床层中竖直插入热管,热管呈正三角形排列,管心距100mm,热管外径20mm,壁厚1mm,长度与催化剂床层一致,外部加工出螺纹,螺纹夹角45
°
,肋化数8。热管壁材质选用t2-m铜,热管内装填的工质为丙酮,不设吸液芯。
[0041]
本发明:在原反应器的基础上,把原反应器结构改造为本发明中的样式,其中上床层11高
1.5米,下床层12高4.92米;丙酮汽化换热器2规格为:双管程的64根换热管,呈正方形排布,管心距23.812mm;管长2米,外径19.05mm,壁厚1.65mm,材质为304不锈钢,管程压降0.1个大气压;换热器壳内径257.4mm,外径273mm,设置有7块交错排布的折流板;可见,丙酮汽化换热器2很小;注意在设计丙酮气化换热器时,应确保丙酮不完全汽化,还有一部分剩余,否则的话丙酮完全气化后,干燥的丙酮蒸汽与反应液很难换热,多出来的这部分换热面积将被浪费掉。
[0042]
丙外组分:温度50.6℃,压力三个大气压的绝压,含1.175kg/s的双酚a、9.7625kg/s的苯酚、0.0875kg/s的丙酮、1.125kg/s的杂质新鲜丙酮:温度25℃,压力1个大气压的绝压,含0.35kg/s的丙酮。
[0043]
由图2可见,本发明的反应器上床层11的温度高于另外两种反应器,从而更加不易出现结晶堵塞,而最高温度与原反应器相当。
[0044]
根据南通星辰(原反应器就是南通星辰的)的生产数据,反应器中发生结晶堵塞的位置为催化剂床层顶部,将进入催化剂床层的反应液温度从55℃提升到57℃即可避免结晶堵塞,而本发明中进入反应器的反应液温度为59.23℃,成分与原反应器一致,因而不会出现结晶堵塞。
[0045]
除此之外,本发明中的反应器,最终丙酮的转化率相较于另外两种还有轻微的提高(不到1%,但至少没有降低)。
[0046]
当然,本文的设备参数及工艺参数,是为了确保不大改原反应器而设定的,其出料温度与原反应器一致,后续流程不用改造,不一定是最佳设计。举例来讲,如果要新设计反应器,可以把催化剂床层改成两段1.5米高的。
[0047]
以上所述的实施例仅仅是对本发明的优选实施方式进行描述,并非对本发明的范围进行限定,在不脱离本发明设计精神的前提下,本领域普通技术人员对本发明的技术方案作出的各种变形和改进,均应落入本发明权利要求书确定的保护范围内。
再多了解一些
本文用于创业者技术爱好者查询,仅供学习研究,如用于商业用途,请联系技术所有人。