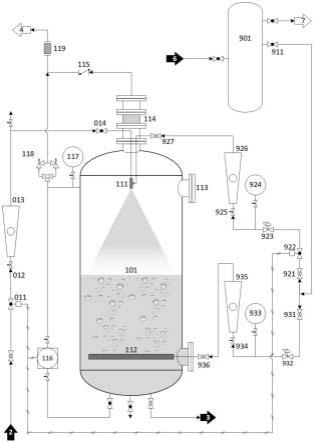
一种制备超纯氢的预处理方法
【技术领域】
1.本发明属于工业制氢中的水电解技术领域,具体涉及一种制备超纯氢的预处理方法。
背景技术:
2.现时用来生产氢气所使用的工业水电解装置工艺流程(基本工艺流程见图1),一般都是把除盐(软化水)从储存罐(101)送进氢液分离器(501),随后注入电解槽(201),在直流电的电解作用下,将水分解成"粗"氢气和"粗"氧气。粗氢和粗氧分别经冷却送入各自的气液分离器(301和501)进行气液分离、之后通过各自的冷却/捕滴/气液分离设备(401和601)除雾和除水。除水后的粗氢进入脱氧装置(701),在催化剂的作用下,粗氢中的小量氧气与氢气发生化合反应生成水。大部份的氢中水在冷凝后被排走。剩余的二氧化炭和微量水分在通过份子筛吸附干燥器(801)时被清除。所产出的氢气是符合gb/t 3634.2-2011对纯氢的技术要求,但逊于gb/t 3634.2-2011对高纯氢和超纯氢的要求。[备注:本说明书提及的"超纯氢"、"高纯氢"和"纯氢"是指符合国家标准gb/t 3634.2-2011规定的超纯氢、高纯氢和纯氢的氢气。(见表1)]
[0003]
主要原因是溶解在除盐水中的各种空气成份(氧、氩、氮、一氧化炭、二氧化炭和甲烷),都会在电解槽水分解的过程中一并释出。如上段所述,氧、二氧化炭和水分在脱氧装置(701)和筛吸附干燥器(801)等后纯化处理过程中被有效清除。而一氧化炭和甲烷,由于其溶质量极低,释放到产品氢的杂质量分别只有0.002ppbv和0.05ppbv,小于超纯氢对一氧化炭和甲烷杂质量的技术要求。余下的氩和氮,由于惰性化学反应的特性,现时普遍的水电解装置是无法清除。依据亨利定律(henry’s law),释放出的氩和氮在产品氢的成份分别可以超出0.24ppmv和9.1ppmv。导致产品氢逊于高纯氢和超纯氢的技术要求。
[0004]
在2019年之前,氢气中的氩和氮杂质,由于它们惰性化学反应的特性,对大部分使用氢气的生产工业都没有多大影响,所以对氢中氩和氮一直都没有特别要求。但由于近年不小新发展的高科技行业在氢气应用方面,对质和量的要求都不断提升,特别是涉及半导体生产的应用,如极紫外光刻(euv lithography)和硅薄膜沉积(silicon thin film deposition)等,而晶圆外延(epitaxy)更开始要求氢中氩不能多于70ppbv。氩和氮,也因为它们惰性化学反应的特性,要把它们从氢气中清除出来,确实是一项极为困难的作业。目前一般都只有采用钯膜扩散或低温吸附的后处理方法去清除。
[0005]
钯膜扩散装置的优异功能是把已达纯氢规格的氢气,进一步提升至高纯氢或超纯氢。当纯氢连同混合在其中的杂质(包括氧、氩、氮、和二氧化炭)进入钯合金膜管束时,氢分子会被钯膜表面吸附、解离、溶解成氢原子、从钯膜的一侧扩散到另一侧、柝出后的氢原子再化合成氢分子并脱附。除氢外,其他气体均不能通过钯膜,从而把纯氢净化达至超纯氢。然而,钯膜扩散方法却存在不小缺点,包括设备成本贵,高能耗,使用寿命和氢脆问题,阐述如下:
[0006]
缺点1.钯本身是一种颇为稀有的贵价金属元素,
[0007]
缺点2.要维持高效透氢率,一般钯膜扩散的工作温度需要提高到300-500℃,
[0008]
缺点3.长时间高温会使钯膜的寿命缩短,
[0009]
缺点4.工作温度失稳(如遇电源波动的情况下)会引起氢脆问题。
[0010]
导致应用此纯化方法的资本、生产和维护成本极为高昂。
[0011]
低温吸附同样是把已达纯氢规格的氢气,进一步提升至高纯氢或超纯氢。目前普遍都是使用双筒罐安排,一吸附一再生轮替运作。筒罐大多采用同轴三层结构。中心筒罐充填分子筛,内夹层浸泡液氮,外夹层为真空隔热层。吸附时,液氮提供-196℃的低温状态进一步提升分子筛的吸附效率。再生时,250℃的反吹促使分子筛把杂质更彻底地脱附。同样,低温吸附方法也存在不小缺点,包括设备制造技术复杂,需要增设额外液氮供辅设施,耗氮、耗电和维护困难,阐述如下:
[0012]
缺点5.同轴三层结构筒罐(或真空夹层筒罐内装液氮热交换器)的制造技术要求高、
[0013]
缺点6.除低温吸附装置外,还需要增设液氮供辅系统,包括液氮槽车停泊及卸载区和卸载设施、液氮真空隔热储槽、真空输液管道和再生加热器、
[0014]
缺点7.多出额外的液氮和用电生产成本、
[0015]
缺点8.焊接部位在-196℃和250℃之间反复切换容易引起应力和疲劳破损。即使是毛发般的微细裂纹,也可以导致真空破坏和产品污杂。查找和修复三层结构筒罐上的裂纹是一项极为艰难,需时和耗费的任务。
[0016]
导致应用此纯化方法的资本、生产和维护成本同样极为高昂。
[0017]
除了前文解述的钯膜扩散和低温吸附的两种后处理纯化方法,专利文献cn106283101和cn101407920也公开了一种对水电解分别制备超纯氢和高纯氢的方法。cn106283101将软化水加热至95-100℃以脱除水中的溶气并通入高纯氧保压。而cn101407920则使用氧气对原料水进行逆流鼓泡反吹。此两种后处理纯化方法也有着各自的缺点,分别为:
[0018]
缺点9.需要增加额外的加热能耗、
[0019]
缺点10.氧鼓泡则使原料水中的溶氧量增加3倍,严重加重对随后脱氧装置的负荷,衰减其性能和使用寿命。
技术实现要素:
[0020]
针对上述4种提升氢气纯度方法的缺点,也就是设备成本贵、能耗高、使用寿命相对短、潜在氢脆隐患、设备制造技术复杂、维护困难、额外增加液氮设施和液氮耗用和额外增加脱氧装置的负荷。本发明提供一种设备成本低、结构坚固简单、没有额外能耗和维护简易的预处理方法:使用氢气雾化及吹脱电解制氢的除盐进水,从而提升产品氢气的质量规格达至符合gb/t 3634.2-2011对超纯氢的技术要求(见图2和图3)。
[0021]
由于目前一般水电解装置所生产出来的氢气,当中的杂质(主要是氧、氩、氮和二氧化炭),都是源自于溶解在除盐水中的各种空气成分。故本发明采取对除盐水进行预处理,解决问题于源头:在除盐水进入电解槽之前,本发明使用小量的氢气(首选采用水电解制程自产的产品氢),通过混合喷嘴在除盐水储存罐的顶部对除盐水进行雾化吹脱和通过曝气管在储存罐底部对除盐水进行鼓泡,给其提供冗余吹脱和微正压屏蔽环境。彻底地把
原先溶解于除盐进水中的氧、氩、氮和二氧化炭脱离排走。
[0022]
随后在电解槽分解成"粗"氢气和"粗"氧气、在各自的气液分离器进行气液分离、在各自的冷却/捕滴/气液分离设备除雾和除水。除水后的粗氢进入脱氧装置化合成水、再经冷凝排水和份子筛吸附干燥,所产出的产品氢是完全符合gb/t 3634.2-2011对超纯氢的技术要求。
[0023]
为决解前述的技术问题,本发明所采用的技术方案展述如下:
[0024]
本发明是对现时普遍用来生产氢气所使用的工业水电解工艺(见图1),包括已投用的现有装置和策划中的流程设计,进行轻度修改,使其产品得以经济地从纯氢提升至超纯氢。
[0025]
主要的工艺修改有八项(见图2和图3):
[0026]
项1.在除盐水储存罐顶部加设法兰连接口(方便维护)用于添加喷咀设施,
[0027]
项2.在上述的接口按装混合喷咀,
[0028]
项3.在除盐水储存罐近底部加设法兰连接口用于添加曝气管,
[0029]
项4.在上述的接口按装曝气管,
[0030]
项5.原接入除盐水储存罐入口的除盐水管道更改为接往混合喷咀入水端口,并加装流量调节阀和流量显示器,
[0031]
项6.从产品氢缓冲罐加设一根管道经三通配件分别接往混合喷咀入气端口和曝气管入气端口,在进入混合喷咀和曝气管前,分别于这两根管道上设置流量调节阀、压力调节阀、压力表和流量显示器。
[0032]
项7.在除盐水储存罐近顶部加设法兰连接口用于添加视镜,位置应方便操作员观察混合喷咀和喷洒状况,
[0033]
项8.在储存罐顶部排气管又混合喷咀的上方加装捕滴器捕捉排气中的过饱和水分并回收至储存罐,以减小除盐水漂移损失。
[0034]
依据亨利定律的实验常数(henry’s law constant),在常温的情况下,溶解在除盐水中的氧、氩、氮和二氧化炭各成分的摩尔分数浓度分别为4.6x10-6
、2.4x10-7
、9.1x10-6
和2.5x10-7
(见数据表2行5)。其中的氩、氮溶质,由于它们惰性化学反应的特性,目前一般水电解装置是完全无法清除,都会在电解槽的阴极侧跟随氢气一并释出,成为产品氢中的氩、氮杂质,其成份分别可以超出0.24ppmv和9.1ppmv。本发明使用氢气:
[0035]
第一对除盐水进行雾化吹脱,使溶解在除盐水中的空气成分(包括氩、氮)扩散到环围的氢气介质中,以及
[0036]
第二对已吹脱完妥的除盐水提供一个微正压的屏蔽环境,防止空气进入储存罐,避免对除盐水造成二次溶气污染。
[0037]
用作对除盐水进行预处理的氢气,首选是来自水电解装置自产的产品氢,装置以外供应的氢气亦可作为一种选择,建议选用符合或高于gb/t 3634.2-2011纯氢规格的氢气。然而,首选自产的产品氢,主要的原因是包括其规格为超纯氢、纯度稳定、不需外购和额外加装氢气供应系统、没有因运输和充装接驳的污染风险。
[0038]
雾化吹脱用氢气使用量,视乎所采用氢气的纯度规格,可以套用随附的数据表为模板计算出来。首先,在行9输入所选定的氢气中的杂质量,然后按步续行往下计算直至全表完成。
[0039]
如选用超纯氢为雾化吹脱用氢气,其使用量对除盐水流量比例(摩尔对摩尔)为9.19x10-4
:1,亦即每100l/h除盐水需使用不小于0.114nm
3h2
/h雾化吹脱用氢气、见数据表2行13和行14。
[0040]
如选用高纯氢为雾化吹脱用氢气,其使用量对除盐水流量比例(摩尔对摩尔)为9.24x10-4
:1,亦即每100l/h除盐水需使用不小于0.115nm
3h2
/h雾化吹脱用氢气、见数据表2行13和行14。
[0041]
如选用纯氢为雾化吹脱用氢气,其使用量对除盐水流量比例(摩尔对摩尔)为9.47x10-4
:1,亦即每100l/h除盐水需使用不小于0.118nm
3h2
/h雾化吹脱用氢气、见数据表2行13和行14。
[0042]
本发明使用氢气通过混合喷咀将除盐进水进行雾化,创造大面积气液传质介面,使传质过程达至充分平衡,实现吹脱效率最大化。混合喷咀的液滴直径要求应该尽量细小。可调范围应为50至200微米,但建议不小于100微米以避免导致过大的漂移损失。混合喷咀的内部结构应选择气流和液流有个别的独立通道,两流只在喷咀外混合撞击,使得个别流量可以独立精准调控。
[0043]
超纯气体生产一旦发生纯度问题事故,往往需要停产数天进行设备检修和管道吹扫。因此,冗余的净化措施普遍都被业界广泛接受甚至要求,尤其是当该气体是应用于半导体行业。因此,本发明在除储存罐近底部加装曝气管鼓泡入氢气,对除盐水提供多一趟冗余吹脱作为以防万一的保险措施,减低因混合喷嘴雾化效能劣化、氢气压力调节阀设定漂移和氢气流量调节阀孔口阻塞等所做成的猝然纯度破坏事故。
[0044]
现时普遍的水电解装置,其储存罐的除盐水补给大多都是采用液位控制、批量补充的模式。在高液位的时段,一般设定为容器水容量的95%以避免满溢,通过液位开关器自动关闭供往储存罐的除盐水液位开关阀。为了节省氢气用量,建议同时把用来雾化吹脱除盐水的氢气一起连锁关闭,在供往混合喷嘴的氢气管道上增设一组液位开关阀和气动控制信号线并连到上述的液位开关器来实现。然而在雾化吹脱用氢气被连锁关闭的情况下,除盐水还是会恒量地从储存罐被抽往气液分离器,为了保证储存罐能维持一个微正压的屏蔽环境,本发明使用不小于除盐水流量的氢气(体积对体积计)通过曝气管鼓泡入除盐水储存罐,填补因除盐水被抽走而产生的空间体积。用100l/h除盐水(相等于约124nm3/h氢气产量)来做举例,鼓泡用氢气为不小于100nl/h(0.1nm3/h)、亦即鼓泡用氢气使用量对除盐水流量(摩尔对摩尔比例)为不小于8.037x10-04
:1。
[0045]
要有效阻止空气藉着扩散运动进入储存罐,屏蔽压力不应小于250n/m2.
[0046]
为更确保空气不能进入除盐水储存罐,本发明在储存罐顶部的排放管、于捕滴器出口和阻火器之间的管道上,设置了单向阀阻止空气扩散入储存罐。单向阀的开启压力亦给除盐水储存罐提供一个稳定的屏蔽微正压,根据上段的要求,单向阀开启压力的规格不应小于250n/m2。
[0047]
除盐水经过上述使用氢气雾化和吹脱后,溶解在其中的氧、氩、氮、一氧化炭、二氧化炭和甲烷浓度,分别剩下1.1x10-07
、6.5x10-09
、1.2x10-07
、1.8x10-12
和1.0x10-07
,单位为摩尔分数mola/mol
h2o
(见表2行15)。进入电解槽后,除盐水在的阴极侧分解成oh-和氢气,全数的氧、氩、氮、一氧化炭、二氧化炭和甲烷亦随着分解出来的氢一并释出,与饱和水分构成产品氢中的主要的杂质。按水电解的化学计量,上例杂质的浓度在分解出来的氢气,分别是
0.11ppmv、0.01ppmv、0.12ppmv、0.000002ppmv和0.10ppmv(见表2行17),已是符合国标对超纯氢的要求。然而,非常微量的氧分子藉着渗透作用会从阳极侧通过隔离膜窜入阴极侧的产品氢,因此,这阶段的氢气还是需要通过催化脱氧、冷凝排水和份子筛吸附干燥,将氧和水份撤底清除,使产品氢完全符合gb/t 3634.2-2011对超纯氢的技术要求。
[0048]
为进一步地解决上述技术问题,本发明提供了一种制备超纯氢的预处理方法,包括下列步骤:
[0049]
a.在除盐水进入电解槽前,除盐水经除盐水管道导入于储存罐顶部;同时,使用氢气经供氢管道导入于储存罐顶部,对除盐水进行雾化和吹脱预处理;
[0050]
b.在除盐水进入电解槽前,通过供氢管道导入氢气到储存罐底部,使用氢气对已完成预处理的除盐水进行鼓泡、冗余吹脱和提供微正压屏蔽;
[0051]
c.对储存罐的排气进行水雾分离,捕捉其中的过饱和水分并回收至储存罐;
[0052]
d.经预处理后获得的除盐水透过随后的水电解装置工艺流程制得产品氢并储存在缓冲罐中。
[0053]
作为制备超纯氢的预处理方法的优选技术方案,在步骤a中所述储存罐顶部设置混合喷咀,其内部结构有个别的独立通道,分别连接所述供氢管道和所述除盐水管道,导入的氢气和除盐水两流只在所述混合喷咀出口处混合和撞击。
[0054]
作为制备超纯氢的预处理方法的优选技术方案,步骤a中所述除盐水通过所述混合喷咀雾化后的液滴直径为不小于100μm。
[0055]
作为制备超纯氢的预处理方法的优选技术方案,在步骤b中所述储存罐底部设置曝气管,鼓泡氢气的体积流量不小于除盐水的体积流量。
[0056]
作为制备超纯氢的预处理方法的优选技术方案,在所述供氢管道上依顺序设置开关阀、压力调节阀、压力表、流量调节阀和流量显示器。
[0057]
作为制备超纯氢的预处理方法的优选技术方案,步骤a中在所述供氢管道上,位于所述开关阀和所述压力调节阀之间,安装液位开关阀,开关设定为当储存罐的液位水平≥95%时关闭。
[0058]
作为制备超纯氢的预处理方法的优选技术方案,在所述储存罐顶部设置排气管,所述排气管上设置捕滴器。
[0059]
作为制备超纯氢的预处理方法的优选技术方案,还包括维持储存罐内一个微正压屏蔽的步骤,所述捕滴器出口的管道上设置单向阀,所述单向阀的开启压力不小于250n/m2。
[0060]
作为制备超纯氢的预处理方法的优选技术方案,所述氢气为纯氢时,氢气使用量与除盐水流量的摩尔比为不小于9.47x10-4
:1;所述氢气为高纯氢时,氢气使用量与除盐水流量的摩尔比为不小于9.24x10-4
:1;所述氢气为超纯氢时,氢气使用量与除盐水流量的摩尔比为不小于9.19x10-4
:1。
[0061]
作为制备超纯氢的预处理方法的优选技术方案,还包括下列步骤:
[0062]
e.经所述供氢管道导入步骤d中的所述产品氢进行步骤a中的雾化和吹脱预处理,和/或进行步骤b中的鼓泡、冗余吹脱和提供微正压屏蔽。
[0063]
本发明亦不选择使用纯氧用作吹脱和保压用途,主要是因为如果使用纯氧,吹脱后溶解于除盐水中的氧浓度,会比吹脱前增加369%达至2.2x10-5 mol
o2
/mol
h2o
(见表5行
15),严重加重对随后脱氧装置的负荷。反之,使用超纯氢吹脱后水中的溶解氧浓度会减小98%降至1.1x10-07 mol
o2
/mol
h2o
(见表2行15),大大减轻对脱氧装置的负荷。使其可以腾出全部的催化能力,集中用来清除通过渗透作用窜越隔离膜,进入阴极侧产品氢的微量氧分子。
【附图说明】
[0064]
下面结合附图和实施例对本发明进一步说明。
[0065]
图1为现时常规的工业水电解流程概述图;
[0066]
图2为本发明(实施例1)与常规水电解装置的总体整合图;
[0067]
图3为本发明(实施例1)的详细流程整改图;
[0068]
图4为本发明修改为不设曝气管(实施例2)与常规水电解装置的总体整合图;
[0069]
图5为本发明修改为不设曝气管(实施例2)的详细流程整改图;
[0070]
图6为本发明修改为外部氢气供应(实施例3)与常规水电解装置的总体整合图;
[0071]
图7为本发明修改为外部氢气供应(实施例3)的详细流程整改图;
[0072]
图8为本本发明修改为外部氢气供应和不设曝气管(实施例4)与常规水电解装置的总体整合图;
[0073]
图9为本本发明修改为外部氢气供应和不设曝气管(实施例4)的详细流程整改图。
[0074]
图中标号的设备名称和接点说明表列于下:
[0075]
[0076]
【具体实施方式】
[0077]
本发明是对现时普遍用来生产氢气所使用的常规工业水电解工艺(见图1)的流程设计或已投用的现有装置,进行的轻度修改(见图2和图3),使其氢气产品得以从纯氢提升至超纯氢。考虑到个别设备和企业的不同状况,提出相应的具体实施方式:
[0078]
实施例1使用水电解装置自产的产品氢作为预处理介质和加装曝气管。
[0079]
实施例2使用水电解装置自产的产品氢作为预处理介质,但没加装曝气管条件。
[0080]
实施例3使用外供的氢气作为预处理介质,但容许加装曝气管。
[0081]
实施例4使用外供的氢气作为预处理介质,没加装曝气管条件。
[0082]
上列的4个实施方法,实施例1是首选。理由是自产自供预处理氢气保证了合理成本和可控纯度,而曝气管亦给除盐水提供了有效的冗余吹脱和正压屏蔽。
[0083]
[实施例1]
[0084]
此实施方式(实施例1)是基于使用水电解装置自产的产品氢作为预处理介质和容许除盐水储存罐(101)加装曝气管(112)。具体施方式为(见图2和图3):
[0085]
在除盐水储存罐(101)顶部加设法兰连接配件(方便维护装拆)用于加装混合喷咀(111)、接入氢气和除盐水。混合喷咀(111)的技术规格要求为:
[0086]
规格1.液滴直径设计点为100微米,可调节范围应为50至200微米。
[0087]
规格2.混合喷咀(111)的气体流量设计点为液体流量的0.0919%(摩尔对摩尔),用100l/h的除盐水流量来做举例,氢气流量设计点为0.114nm3/h,见表2行13和14。
[0088]
原接入除盐水储存罐(101)的除盐水管道更改为接往混合喷咀(111)的入水端口。若原设计没有设置除盐水流量调节阀(012)和流量显示器(013),应在除盐水供应管道上又混合喷咀(111)的上游给予补装以方便精准操控。
[0089]
从产品氢缓冲罐(901)气体出口开关阀(911)加设一根管道,经三通管件分别接往混合喷咀(111)入气端口和曝气管(112)入气端口,在进入混合喷咀(111)和曝气管(112)前,分别于这两根管道上设置开关阀(921,931)、压力调节阀(923,932)、压力表(924,933)、流量调节阀(925,934)、流量显示器(926,935)和开关阀(927,936),以方便分别准确地调控用作雾化吹脱和屏蔽鼓气除盐水的氢气流量。此部分的技术设计参数为;
[0090]
参数1.从产品氢缓冲罐(901)供往上述三通的管件和阀门的氢气流量设计点应为液体流的0.1723%(摩尔对摩尔比例),用100l/h的除盐水流量来做举例,氢气流量设计点为0.214nm3/h。
[0091]
参数2.由三通供往混合喷咀(111)的管径、流量调节阀(925)、压力调节阀(923)和流量显示器(926)的氢气流量设计点应为液体流的0.0919%(摩尔对摩尔比例),用100l/h的除盐水流量来做举例,氢气流量设计点为0.114nm3/h,见表2行13和14。
[0092]
参数3.由三通供往曝气管(112)的管径、流量调节阀(934)、压力调节阀(932)和流量显示器(935)的氢气流量设计点应为液体流的0.08037%(体积比例),用100l/h的除盐水流量来做举例,氢气综合流量设计点为0.10nm3/h。
[0093]
在开关阀(921)和压力调节阀(923)之间加设液位开关阀(922)和一路气动控制信号线并连到液位显示及开关器(116)。在储存罐(101)液位高(设定为储存罐的液位水平≥95%以避免满溢)的时段,连锁关闭液位开关阀(922)以节省雾化吹脱用的氢气用量。同样,液位开关阀(922)的氢气流量设计点应为液体流的0.0919%(摩尔对摩尔比例),用100l/h的除盐水流量来做举例,氢气流量设计点为0.114nm3/h,见表2行13和14。
[0094]
在除盐水储存罐(101)近顶部加设法兰连接口用于添加视镜(113),位置应方便操作员视察喷咀(111)和喷洒状况。在除盐水储存罐(101)顶部排气管又喷咀的上方加装捕滴器(114)捕捉排气中的过饱和水分并回收至储存罐(101),以减小除盐水漂移损失。
[0095]
在除盐水储存罐(101)的捕滴器出口的管道上加装单向阀(115)以防止空气窜入和给除盐水储存罐(101)提供稳定的屏蔽压力。
[0096]
由于储存罐(101)导入了氢气,罐体顶部应加装压力表(117)和压力安全阀组合(118)方便监察罐内压力,在压力调节阀(923、932)和单向阀(115)发生故障的情况下,保护容器免受过压。
[0097]
除盐水储存罐(101)和压力安全阀组合(118)的排气应通过管道收集并连接到室外高位处,通过阻火器(119)安全排放。
[0098]
[实施例2]
[0099]
此实施方式(实施例2)是基于使用水电解装置自产的产品氢作为预处理介质,但除盐水储存罐(101)没有加装曝气管(112)的条件。具体施方式为(见图4和图5):
[0100]
在除盐水储存罐(101)顶部加设法兰连接配件(方便维护装拆)用于加装混合喷咀
(111)、接入氢气和除盐水。混合喷咀(111)的技术规格要求为:
[0101]
规格1.液滴直径设计点为100微米,可调节范围应为50至200微米。
[0102]
规格2.混合喷咀(111)的气体流量设计点为液体流的0.0919%(摩尔对摩尔比例),用100l/h的除盐水流量来做举例,氢气流量设计点为0.114nm3/h,见表2行13和14。
[0103]
原接入除盐水储存罐(101)的除盐水管道更改为接往混合喷咀(111)的入水端口。若原设计没有设置除盐水流量调节阀(012)和流量显示器(013),应在除盐水供应管道上又混合喷咀(111)的上游给予补装以方便精准操控。
[0104]
从产品氢缓冲罐(901)气体出口开关阀(911)加设一根管道接往混合喷咀(111)入气端口,在进入混合喷咀(111)前,设置开关阀(921)、压力调节阀(923)、压力表(924)、流量调节阀(925)、流量显示器(926)和开关阀(927),以方便准确地调控用作雾化吹脱除盐水流量的氢气流量。此部分的管径、阀件和流量显示器的氢气流量设计点应为液体流的0.0919%(摩尔对摩尔比例),用100l/h的除盐水流量来做举例,氢气流量设计点为0.114nm3/h,见表2行13和14。
[0105]
注意,此实施方式(实施例2)在开关阀(921)和压力调节阀(923)之间是不设液位开关阀,以保证在储存罐(101)液位高的时段,氢气仍然持续输入储存罐(101),保证储存罐(101)能维持一个微正压的屏蔽环境。
[0106]
在除盐水储存罐(101)近顶部加设法兰连接口用于添加视镜(113),位置应方便操作员视察喷咀(111)和喷洒状况。在除盐水储存罐(101)顶部排气管又喷咀的上方加装捕滴器(114)捕捉排气中的过饱和水分并回收至储存罐(101),以减小除盐水漂移损失。
[0107]
在除盐水储存罐(101)的捕滴器出口的管道上加装单向阀(115)以防止空气窜入和给除盐水储存罐(101)提供稳定的屏蔽压力。
[0108]
由于储存罐(101)导入了氢气,罐体顶部应加装压力表(117)和压力安全阀组合(118)方便监察罐内压力,在压力调节阀(923、932)和单向阀(115)发生故障的情况下,保护容器免受过压。
[0109]
除盐水储存罐(101)和压力安全阀组合(118)的排气应通过管道收集并连接到室外高位处,通过阻火器(119)安全排放。
[0110]
在没有加装曝气管(112)的条件下,建议调升计划巡检和计划维护的频率来替代装曝气管(112)提供的冗余吹脱效能,以降低发生纯度事故的机率。
[0111]
[实施例3]
[0112]
此实施方式(实施例3)是基于使用外供的氢气作为预处理介质,而除盐水储存罐(101)容许加装曝气管(112)。具体施方式为(见图6和图7):
[0113]
在除盐水储存罐(101)顶部加设法兰连接配件(方便维护装拆)用于加装混合喷咀(111)、接入氢气和除盐水。混合喷咀(111)的技术规格要求为:
[0114]
规格1.液滴直径设计点为100微米,可调节范围应为50至200微米。
[0115]
规格2.通过混合喷嘴(111)用作雾化吹脱的外供氢气,其使用量可以套用前附的数据表为模板计算出来。首先,在行9输入所选定的氢气中的杂质量,然后按步续行往下计算直至全表完成。
[0116]
如选用超纯氢为雾化吹脱用氢气,其使用量对除盐水流量比例(摩尔对摩尔)为9.19x10-4
:1,亦即每100l/h除盐水需使用不小于0.114nm
3h2
/h雾化吹脱用氢气、见数据表2
行13和行14。
[0117]
如选用高纯氢为雾化吹脱用氢气,其使用量对除盐水流量比例(摩尔对摩尔)为9.24x10-4
:1,亦即每100l/h除盐水需使用不小于0.115nm
3h2
/h雾化吹脱用氢气、见数据表2行13和行14。
[0118]
如选用纯氢为雾化吹脱用氢气,其使用量对除盐水流量比例(摩尔对摩尔)为9.47x10-4
:1,亦即每100l/h除盐水需使用不小于0.118nm
3h2
/h雾化吹脱用氢气、见数据表2行13和行14。
[0119]
原接入除盐水储存罐(101)的除盐水管道更改为接往混合喷咀(111)的入水端口。若原设计没有设置除盐水流量调节阀(012)和流量显示器(013),应在除盐水供应管道上又混合喷咀(111)的上游给予补装以方便精准操控。
[0120]
于外部氢气供应点加装充装接头(912),一端用于跟外部氢气供应软管接驳,另一端装开关阀(913)、管道经三通管件分别接往混合喷咀(111)入气端口和曝气管(112)入气端口,在进入混合喷咀(111)和曝气管(112)前,分别于这两根管道上设置开关阀(921,931)、压力调节阀(923,932)、压力表(924,933)、流量调节阀(925,934)、流量显示器(926,935)和开关阀(927,936),以方便分别准确地调控用作雾化吹脱和屏蔽鼓气除盐水的氢气流量。此部分的技术设计参数为;
[0121]
参数1.装充装接头(912)、上述的三通管件及其间的管道和开关阀(913)的氢气流量设计点应为液体流量的0.1723%(当外供氢为超纯氢规格)、0.1728%(当外供氢为高纯氢规格)和0.1751%(当外供氢为纯氢规格),用100l/h的除盐水流量来做举例,相对的氢气流量设计点分别为0.214nm3/h、0.215nm3/h和0.218nm3/h。
[0122]
参数2.由三通供往混合喷咀(111)的管径、流量调节阀(925)、压力调节阀(923)和流量显示器(926)的氢气流量设计点应为液体流的0.0919%(当外供氢为超纯氢规格)、0.0924%(当外供氢为高纯氢规格)和0.0947%(当外供氢为纯氢规格)。用100l/h的除盐水流量来做举例,相对的氢气流量设计点分别为0.114nm3/h、0.115nm3/h和0.118nm3/h,见表2、3和4行13和14。
[0123]
参数3.由三通供往曝气管(112)的管径、流量调节阀(934)、压力调节阀(932)和流量显示器(935)的氢气综合流量设计点应为液体流的0.0804%(体积比例),用100l/h的除盐水流量来做举例,氢气综合流量设计点为0.10nm3/h。
[0124]
在开关阀(921)和压力调节阀(923)之间加设液位开关阀(922)和一路气动控制信号线并连到液位显示及开关器(116)。在储存罐(101)液位高(设定为储存罐的液位水平≥95%以避免满溢)的时段,连锁关闭液位开关阀(922)以节省雾化吹脱用的氢气用量。同样,液位开关阀(922)的氢气流量设计点应为液体流的0.0919%(当外供氢为超纯氢规格)、0.0924%(当外供氢为高纯氢规格)和0.0947%(当外供氢为纯氢规格)。用100l/h的除盐水流量来做举例,相对的氢气流量设计点分别为0.114nm3/h、0.115nm3/h和0.118nm3/h,见表2、3和4行13和14。
[0125]
在除盐水储存罐(101)近顶部加设法兰连接口用于添加视镜(113),位置应方便操作员视察喷咀(111)和喷洒状况。在除盐水储存罐(101)顶部排气管又喷咀的上方加装捕滴器(114)捕捉排气中的过饱和水分并回收至储存罐(101),以减小除盐水漂移损失。
[0126]
在除盐水储存罐(101)的捕滴器出口的管道上加装单向阀(115)以防止空气窜入
和给除盐水储存罐(101)提供稳定的屏蔽压力。
[0127]
由于储存罐(101)导入了氢气,罐体顶部应加装压力表(117)和压力安全阀组合(118)方便监察罐内压力,在压力调节阀(923、932)和单向阀(115)发生故障的情况下,保护容器免受过压。
[0128]
除盐水储存罐(101)和压力安全阀组合(118)的排气应通过管道收集并连接到室外高位处,通过阻火器(119)安全排放。
[0129]
[实施例4]
[0130]
此实施方式(实施例4)是基于使用外供的氢气作为预处理介质,和除盐水储存罐(101)没有加装曝气管(112)的条件。具体施方式为(见图8和图9):
[0131]
在除盐水储存罐(101)顶部加设法兰连接配件(方便维护装拆)用于加装混合喷咀(111)、接入氢气和除盐水。混合喷咀(111)的技术规格要求为:
[0132]
规格1.液滴直径设计点为100微米,可调节范围应为50至200微米。
[0133]
规格2.通过混合喷嘴(111)用作雾化吹脱的外供氢气,其使用量可以套用前附的数据表为模板计算出来。首先,在行9输入所选定的替代氢气中的杂质量,然后按步续行往下计算直至全表完成。
[0134]
如选用超纯氢为雾化吹脱用氢气,其使用量对除盐水流量比例(摩尔对摩尔)为9.19x10-4
:1,亦即每100l/h除盐水需使用不小于0.114nm
3h2
/h雾化吹脱用氢气、见数据表2行13和行14。
[0135]
如选用高纯氢为雾化吹脱用氢气,其使用量对除盐水流量比例(摩尔对摩尔)为9.24x10-4
:1,亦即每100l/h除盐水需使用不小于0.115nm
3h2
/h雾化吹脱用氢气、见数据表2行13和行14。
[0136]
如选用纯氢为雾化吹脱用氢气,其使用量对除盐水流量比例(摩尔对摩尔)为9.47x10-4
:1,亦即每100l/h除盐水需使用不小于0.118nm
3h2
/h雾化吹脱用氢气、见数据表2行13和行14。
[0137]
原接入除盐水储存罐(101)的除盐水管道更改为接往混合喷咀(111)的入水端口。若原设计没有设置除盐水流量调节阀(012)和流量显示器(013),应在除盐水供应管道上又混合喷咀(111)的上游给予补装以方便精准操控。
[0138]
于外部氢气供应点加装充装接头(912),一端用于跟外部氢气供应软管接驳,另一端装开关阀(913)、从开关阀(913)加设一根管道接往混合喷咀(111)入气端口,在进入混合喷咀(111)前,设置开关阀(921)、压力调节阀(923)、压力表(924)、流量调节阀(925)、流量显示器(926)和开关阀(927),以方便准确地调控用作雾化吹脱除盐水流量的氢气流量。此部分的管径、阀件、流量显示器的氢气流量设计点跟混合喷咀(111)相同。
[0139]
注意,此实施方式(实施例4)在开关阀(921)和压力调节阀(923)之间是不设液位开关阀,以保证在储存罐(101)液位高的时段,氢气仍然持续输入储存罐(101),保证储存罐(101)能维持一个微正压的屏蔽环境。
[0140]
在除盐水储存罐(101)近顶部加设法兰连接口用于添加视镜(113),位置应方便操作员视察喷咀(111)和喷洒状况。在除盐水储存罐(101)顶部排气管又喷咀的上方加装捕滴器(114)捕捉排气中的过饱和水分并回收至储存罐(101),以减小除盐水漂移损失。
[0141]
在除盐水储存罐(101)的捕滴器出口的管道上加装单向阀(115)以防止空气窜入
和给除盐水储存罐(101)提供稳定的屏蔽压力。
[0142]
由于储存罐(101)导入了氢气,罐体顶部应加装压力表(117)和压力安全阀组合(118)方便监察罐内压力,在压力调节阀(923、932)和单向阀(115)发生故障的情况下,保护容器免受过压。
[0143]
除盐水储存罐(101)和压力安全阀组合(118)的排气应通过管道收集并连接到室外高位处,通过阻火器(119)安全排放。
[0144]
在没有加装曝气管(112)的条件下,建议调升计划巡检和计划维护的频率来替代装曝气管(112)提供的冗余吹脱效能,以降低发生纯度事故的机率。
[0145]
与本发明相关的数据如下列各表所示:
[0146]
表1 gb/t 3634.2-2011中纯氢、高纯氢和超纯氢的技术要求
[0147][0148]
表2参数、气体溶解和吹脱气(超纯氢)用量数据表
[0149][0150]
备注:mola中的"a"是指空气中的各成分,即氮、氧、氩和二氧化炭。
[0151]
表3参数、气体溶解和吹脱气(高纯氢)用量数据表
[0152][0153]
备注*:mola中的"a"是指空气中的各成分,即氮、氧、氩和二氧化炭。
[0154]
表4参数、气体溶解和吹脱气(纯氢)用量数据表
[0155][0156]
备注*:mola中的"a"是指空气中的各成分,即氮、氧、氩和二氧化炭。
[0157]
表5参数、气体溶解和吹脱气(纯氧)用量数据表
[0158][0159]
备注*:mola中的"a"是指空气中的各成分,即氮、氧、氩和二氧化炭。
再多了解一些
本文用于创业者技术爱好者查询,仅供学习研究,如用于商业用途,请联系技术所有人。