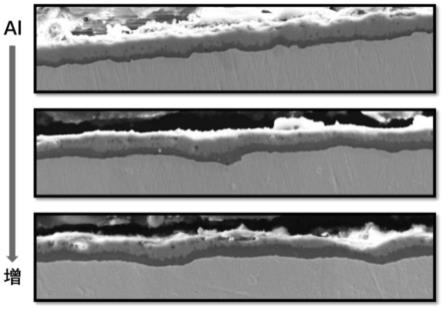
1.本发明涉及高温合金领域,尤其是涉及一种高温抗氧化高强镍基合金及其制备方法。
背景技术:
2.为了提高航空发动机的推力,需要在航空发动机蜗轮部件的转子和静子配合处的机匣内壁上设计成蜂窝密封结构,此蜂窝结构是采用厚度仅为几十微米的箔材制成,与一般条形高温合金的四级晶粒尺寸相当,而具备蜂窝结构的条形高温合金是制备发动机机匣内壁上的蜂窝结构的基础。考虑到航空发动机的使用工况,要求具备蜂窝结构的条形高温合金应在较高温度下(1000-1100℃)仍保持优异的抗氧化性能,同时还需要兼顾高温合金的强度。而现有具备蜂窝结构的条形高温合金是采用高a1含量(最高al含量为8%)以及辅加稀土y元素来提高高温合金的抗氧化性能和强度,但是在实际的应用过程中发现当合金中al含量较高时,其氧化物夹杂的形成倾向极强,且含al的氧化夹杂硬度很高,而这种夹杂一旦存在,在最终高温合金箔材的轧制过程中将形成微型的纵向裂纹,从而影响产品的表面质量、加工塑性以及力学性能。
技术实现要素:
3.针对现有技术中条形蜂窝用高温合金采用高a1含量来提高高温合金抗氧化性能导致的氧化物夹杂的形成倾向极强的问题,本发明提供一种高温抗氧化高强镍基合金及其制备方法,能够使得高温合金中氧化物夹杂含量降低,同时本技术得到的高温合金还具有优异的高温持久性能和冷热加工性能,可在高达1100℃的条件下仍保持完整致密的表面氧化膜。
4.本发明的目的一是提供的一种高温抗氧化高强镍基合金,采用如下的技术方案:一种高温抗氧化高强镍基合金,按重量百分比计,所述合金的化学成分为c:0.03~0.05%、cr:15.5~16.5%、fe:3.1~4.0%、al:4.1~4.7%、mn:0.10~0.25%、y:0.002~0.010%、zr:0.01~0.03%、b:0.001~0.005、余量为ni及不可避免的杂质。
5.优选的,按重量百分比计,所述合金的化学成分为c:0.03~0.05%、cr:15.5~16.5%、fe:3.1~4.0%、al:4.2~4.6%、mn:0.10~0.25%、y:0.002~0.006%、zr:0.01~0.03%、b:0.001~0.005、余量为ni及不可避免的杂质。
6.进一步优选的,按重量百分比计,所述合金的化学成分为c:0.037~0.05%、cr:16.2~16.5%、fe:3.55~4.0%、al:4.2~4.66%、mn:0.15~0.25%、y:0.002~0.006%、zr:0.01~0.03%、b:0.003~0.005、余量为ni及不可避免的杂质。
7.通过采用上述技术方案,本技术通过调整c、al、zr、b、y、mn的含量发现c、al、zr、b、y、mn的含量对合金性能的影响比较大。主要有,c元素含量直接决定了合金中碳化物的数量,而由于碳化物对晶界的钉扎作用,其数量、大小和分布对合金热变形过程中的动态再结晶和随后退火过程中的静态再结晶行为有重要的影响,当碳含量太低的情况下,晶界钉扎
不充分,合金主要通过动态回复软化,不利于再结晶形核而影响了动态再结晶的充分进行,而过多的碳化物易在单向冷变形的过程中形成条带状分布,影响合金的加工和服役性能(拉伸性能、持久性能)。所以将c含量控制在0.03-0.05%的范围内时,有效保证了合金的力学性能。
8.al、cr、y三种元素的配合使用,随着al元素含量的提高,单位面积氧化增重(氧化膜增厚)有所增加,由于合金的抗氧化性能通常是采用一定温度下100h内单位面积平均氧化增重来表征,所以al含量增加时,合金的抗氧化性能是增强的,同时氧化膜增厚后能够更加有效的阻碍cr元素向外扩散,使得cr的氧化膜厚度反而变小,即抑制了cr元素的挥发,保证了合金的高温力学性能,同时随着y元素含量的增加,会加速氧离子向内扩散,使氧化膜向内弯曲,而弯曲的氧化膜与基体的结合强度更高,从而改善氧化膜的粘附性。
9.且随着al元素含量的增加,第二相(γ'相)析出量和析出速度显著提高,第二相的析出有助于提高合金的高温性能,当γ'相的质量分数升高后,γ'相的回溶温度也随之升高(回溶温度是指γ'相重新溶于基体中的温度),尤其当al含量高于5%时,γ'相在温度为950℃以上时将会大量析出,从而严重降低合金的热加工性能,导致锻造开坯的火次变形量也降低,锻造的次数也会增加,反而会使得加工成本增加,同时很容易在边角或局部温度比较低时应变速率比较大时容易开裂,并在热轧后期温度下降较多时极易开裂,所以当al含量控制在4.1-4.7%的范围内时,可以在均匀化、中间退火等升降温的过程中避免第二相的析出,从而避免应变时效裂纹的产生,同时终锻终扎温度可以低至920℃,方便后期的加工。
10.zr、b、mn元素的添加有助于提高合金的塑性,但是当zr、b、mn元素的添加量超过期限后,合金的塑性反而降低,持久寿命也会有所降低。
11.本发明的目的二是提供一种高温抗氧化高强镍基合金的制备方法,包括如下步骤:(1)按重量百分比将石墨、金属铬、硼铁、金属锰、镍板原料加入真空感应炉中进行真空精炼,精炼后依次加入金属铝、金属锆和金属钇搅拌均匀,再浇注形成自耗电极棒;(2)将步骤(1)得到的自耗电极棒进行电渣重熔后得到铸锭;(3)将步骤(2)得到的铸锭进行均匀化热处理;(4)锻坯的制备:将步骤(3)处理后的铸锭进行锻造开坯,制备得到锻坯。
12.优选的,所述步骤(1)中的精炼温度为1480-1490℃,精炼20-25min。
13.优选的,所述步骤(2)中的电渣重熔所采用的电渣按重量百分比包括caf2:50-65%、cao:15-25%、al2o3:10-25%。
14.优选的,所述步骤(2)中的电渣重熔的熔炼速度为0.4-2kg/min,熔炼电流为3000-4500a,侧向电流100-450a。
15.优选的,所述步骤(2)中的抽锭速度为4-6mm/min,冷却水量:3-5档;其中一档水流量为8-10l/min。
16.优选的,所述步骤(3)中的均匀化热处理温度为1140-1180℃,均匀化热处理时间为20-40h。
17.优选的,所述步骤(4)中的锻造温度为1000-1200℃,每火次变形量为30-70%。
18.通过采用上述技术方案,将电渣重熔的熔炼速度限定为0.4-2kg/min、熔炼电流限定为3000-4500a,侧向电流100-450a时,有助于保证铸态组织以及锻造成品的退火组织,降
低一次碳化物的偏析情况。
19.本技术有效控制精炼阶段的温度和精炼时间以及抽锭速度和冷却水量,进而可以有效控制合金在精炼以及电渣重熔阶段的有害元素o和s的含量,从而在源头上有效减少能够形成氧化物夹杂的原料,从而使得本技术上述制备方法得到的合金中的a类(硫化物夹杂物)、b类(氧化铝类夹杂物)、c类(硅酸盐类夹杂物)的粗系和细系的级数均为0级,ds类(圆形球状夹杂物)的级数为为0级,d类(球状氧化物类夹杂物)的细系为0.5级,粗系为0级,从而有效保证合金在后续能够轧制成箔材。
20.本技术的锻造是在1200℃到1000℃的范围内进行锻造,而将每火次变形量限定在30-70%的范围内时,锻造制得的锻坯的平均晶粒度在3-6级,也能够有效保证每火次锻造的效率,尤其是当锻造的每火次变形量在40-50%的范围内时可以有效降低变形的火次,不仅提高了生产效率,同时制得的锻坯的平均晶粒度比较高(平均晶粒度达到4-5级),当每火次变形量低于30%时,合金再结晶的能量不够,从而会导致最终合金产品的塑性不够,而当每火次变形量高于70%时,也会使合金的塑性和强度都降低,因此只要保证合金的每火次锻造变形量在30-70%之间时,都可有效保证锻坯的完整性、力学性能和塑性。
21.综上所述,本发明具有以下有益效果:本技术通过调整c、al、zr、b、y、mn元素的含量范围,不仅可以保证合金的力学性能,同时还能够保证合金在高温下的持久性能以及抗氧化性能,同时本技术在制备过程中合理控制精炼温度、精炼时间以及电渣冶炼阶段的工艺参数,有效降低合金中的有害元素,使得最终产品中的氧化夹杂物控制在很低的水平,为后续合金轧制成箔材提供了有效的保障。
附图说明
22.图1是氧化膜截面的形貌随合金中al元素含量变化的电镜图。
23.图2是氧化膜截面的形貌随合金中y元素含量变化的电镜图。
24.图3是不同c含量合金经过相同变形量的热锻加工后的组织状态。
25.图4是不同c含量合金经过相同变形量的热锻加工及退火后的组织状态。
具体实施方式
26.以下结合附图对本发明作进一步详细说明。
27.实施例1-5采用同一个制备方法,所得到的高温合金的成分如表1所示,工艺如下:实施例1-5一种高温抗氧化高强镍基合金的制备方法,包括如下步骤:(1)真空感应熔炼,根据合金成分要求,将石墨、金属铬、硼铁、金属锰以及镍板加入真空感应炉中进入熔化,控制真空度为5pa,熔化后控制精炼温度在1480℃的条件下精炼20min,精炼结束后依次向真空感应炉中加入金属铝、金属锆和金属钇,搅拌均匀后浇铸成直径为电渣锭结晶器直径的0.6倍的自耗电极棒;精炼20min后合金中氧元素含量为0.0007;(2)电渣重熔,将步骤(1)得到的自耗电极棒加入电渣锭结晶器中,然后加入电渣进行熔炼,熔炼速度为0.4kg/min,熔炼电流为3000a,侧向电流100a,电渣熔化后电渣的厚
度为电渣锭结晶器直径的0.4倍,待自耗电极棒熔化后,冷却凝固得到电渣重熔铸锭,抽锭速度为6mm/min,冷却水量3档;其中电渣锭结晶器的直径为150mm,所用电渣按重量百分比计:caf2:50%、cao:25%、al2o3:25%;同时还检测了抽速和冷却水量对于合金中o和s含量的影响,具体如下表所示(3)将步骤(2)得到的铸锭进行均匀化热处理,在均匀化热处理温度为1145
±
5℃的条件下处理20h;(4)锻坯的制备,将步骤(3)得到的铸锭进行在1200℃的条件下进行锻造开坯,在锻造的过程中,当温度小于1000℃时停止锻造,制备得到锻坯,每火次锻造变形量超过30%。
28.实施例6与实施例3的不同之处在于,实施例6中al元素含量为4.36%,其余组分含量与实施例3的相同。
29.实施例7与实施例3的不同之处在于,实施例7中al元素含量为4.66%,其余组分含量与实施例3的相同。
30.实施例8与实施例3的不同之处在于,实施例8中y元素含量为0.008%,其余组分含量与实施例3的相同。
31.表1为实施例1-8所得合金的元素含量表,单位wt%成分实施例1实施例2实施例3实施例4实施例5实施例6实施例7实施例8c0.030.030.0370.050.050.0370.0370.037cr15.515.516.216.516.516.216.216.2fe3.13.13.554.04.03.553.553.55al4.14.24.44.64.74.364.664.4mn0.100.100.150.250.250.150.150.15y0.0020.0020.0040.0060.010.0040.0040.008zr0.010.010.020.030.030.020.020.02b0.0010.0010.0030.0050.0050.0030.0030.003ni余量余量余量余量余量余量余量余量实施例9与实施例3的不同之处在于,步骤(1)中的精炼温度为1490℃,其余条件及步骤均与实施例3中的相同,精炼后合金中氧元素的含量0.0008。
32.实施例10与实施例3的不同之处在于,步骤(1)中的精炼时间为25min,其余条件及步骤均与实施例3中的相同,精炼后合金中氧元素的含量0.0007。
33.实施例11与实施例3的不同之处在于,步骤(2)中的均匀化热处理温度为1175
±
5℃,均匀化热处理时间为40h,其余条件及步骤均与实施例3中的相同。
34.实施例12与实施例3的不同之处在于,步骤(2)中的电渣重熔的熔炼速度为1kg/min,熔炼电流为4000a、侧向电流为300a,所用电渣按重量百分比计:caf2:65%、cao:15%、al2o3:20%。
35.实施例13与实施例3的不同之处在于,步骤(2)中的电渣重熔的熔炼速度为2kg/min,熔炼电流为4500a、侧向电流为450a,所用电渣按重量百分比计:caf2:65%、cao:25%、al2o3:10%,其余条件及步骤均与实施例3中的相同。
36.实施例14与实施例3的不同之处在于,步骤(2)中的抽锭速度为4mm/min,其余条件及步骤均与实施例3中的相同。
37.实施例15与实施例3的不同之处在于,步骤(2)中的抽锭速度为5mm/min,其余条件及步骤均与实施例3中的相同。
38.实施例16与实施例3的不同之处在于,步骤(2)中的水量为4档,其余条件及步骤均与实施例3中的相同。
39.实施例17与实施例3的不同之处在于,步骤(2)中的水量为5档,其余条件及步骤均与实施例3中的相同。
40.实施例14-17中抽锭速度和水量对o和s含量的影响对比例1与实施例3的不同之处在于,a1元素的含量为3.96%,其余元素含量与实施例3相同。
41.对比例2与实施例3的不同之处在于,a1元素的含量为5.19%,其余元素含量如表2所示。
42.对比例3与实施例3的不同之处在于,c元素的含量为0.021%,其余元素含量如表2所示。
43.对比例4
与实施例3的不同之处在于,c元素的含量为0.055%,其余元素含量如表2所示。
44.对比例5与实施例3的不同之处在于,c元素的含量为0.1%,其余元素含量如表2所示。
45.对比例6与实施例3的不同之处在于,y元素的含量为0.02%,其余元素含量如表2所示。
46.对比例7与实施例3的不同之处在于,zr元素的含量为0%,其余元素含量如表2所示。
47.对比例8与实施例3的不同之处在于,zr元素的含量为0.06%,其余元素含量如表2所示。
48.对比例9与实施例3的不同之处在于,b元素的含量为0%,其余元素含量如表2所示。
49.对比例10与实施例3的不同之处在于,mn元素的含量为0%,其余元素含量如表2所示。
50.表2对比例1-10所得合金的元素含量表,单位wt%成分实施例3对比例1对比例2对比例3对比例4对比例5c0.0360.0360.0360.0210.0550.1cr16.216.216.216.216.216.2fe3.553.553.553.553.553.55al4.43.965.194.44.44.4mn0.150.150.150.150.150.15y0.0040.0040.0040.0040.0040.004zr0.020.020.020.020.020.02b0.0030.0030.0030.0030.0030.003ni余量余量余量余量余量余量续表2续表2注:上述实施例和制备例中的余量中包括ni和不可避免的杂质。
51.性能检测对实施例和对比例得到的合金进行抗氧化性能以及力学性能检测,其中抗氧化性能试验是将热处理后的试样加工成小片,在1100℃条件下测试不同时间段的氧化情况,然后通过称重测试其氧化增重情况,其判定根据gb/t13303-9《钢的抗氧化性能测定方法》及hb5258-2000《钢及高温合金抗氧化性能测定试验方法》,本技术中采用增重法进行试验并通过观察氧化膜的截面形貌,测试氧化膜厚度。
52.力学性能的检测是将热处理后的试样加工成圆棒,然后分别进行了室温拉伸、1100℃高温拉伸和980℃/22mpa条件下的持久寿命等力学性能测试试验,检测依据gb/t228.1-2010《金属材料拉伸试验第一部分:室温试验方法》和gb/t228.2-2015《金属材料拉伸试验第一部分:高温试验方法》、gb/t2039-2012《金属材料单轴拉伸蠕变试验方法》进行检测。
53.表3合金室温力学性能检测结果表
表4本技术合金在1100℃下的力学性能检测结果表
表5各合金在980℃/22mpa的条件下的高温持久性能检测结果表
由于c、fe、mn、zr、b的含量对合金抗氧化性能的影响不是很大,所以本技术对实施例1-8和对比例1-2得到的合金的抗氧化性能做进一步的说明,抗氧化性试验检测结果如表6所示。
54.表6合金在1100℃下氧化100h的检测结果表
(1)al和y元素对合金性能影响的分析:从表3中可以看出,当a1元素含量低于本技术限定的最小值4.1%时,对比例1得到的合金的室温抗拉强度明显降低,而当al元素含量高于4.7%时,对比例2中的断后伸长率和断面收缩率相比于实施例3均降低,说明当al元素含量超过4.7%后,合金的室温塑性会明显下降,反而会影响合金的冷加工性能。
55.从表4-5中可以看出,在1100℃的条件下,al元素含量对合金的高温拉伸性能影响不明显,但是对高温合金的持久寿命有显著影响,随着al元素含量的增加,高温合金的持久断裂时间有效增加。但当al元素含量超过4.7%时,对比例2(al元素含量为5.19%)中的合金的室温塑性急剧下降,当al元素含量比较低时(al元素含量为3.96%),合金的持久性能比较差,因此,当合金中al元素的含量控制在4.1-4.7%时,不仅可有效保证合金的高温持久性能也能保证合金的室温塑性。
56.从表6中可以看出,如图1和图2所示,实施例1-5中随着al、y元素含量的增加,单位面积氧化增重呈逐渐下降的趋势,其主要原因是表面形成的氧化铝增加了该合金氧化膜的连续致密程度,且稀土元素改善了氧化膜的粘附性,使得表面完整的氧化膜阻隔了空气中氧的渗入,有效地阻止了合金的继续氧化。此外,y元素的添加加速了氧离子向内扩散,使氧化膜向内弯曲,增加氧化膜与基体的结合强度,所以本技术实施例1-8中的单位面积氧化增重均小于对比例1-2中的单位面积氧化增重,说明本技术实施例得到的合金的抗氧化性能更好。
57.从对比例1与实施例3的对比中可以看出,当al元素含量比较低时,生成的铝的氧化膜不易连续,对于氧元素的阻碍作用相对较低,则空气中的氧容易渗入并与合金基体发生氧化反应,使得其单位面积上的氧化增重持续增加。
58.从表3中可以看出,y元素含量的增加,可以使得合金的室温力学性能进一步提升,但是从对比例6(y元素含量为0.02%)中可以看出,当y元素含量进行提升后,合金的室温力学性能并没有进一步提升,且塑性还大大降低。
59.从表4-5中可以看到,y元素对合金的高温力学性能影响不大,但当y元素的含量超过0.01%时,室温塑性大大降低,且高温的持久性能也大大降低,说明y元素的含量限定在0.002-0.01%的范围内时,不仅可以有效保证合金的塑性,同时还能与al元素配合提高合金的抗氧化性能。
60.(2)c元素对合金性能的影响:从表3和表4中可以看出,随着c含量的增加,合金的室温强度和高温强度均逐步提高,但塑性逐步下降,另外从表5中看出看出,当c含量超过本技术的最高值0.05%后,对比例4-5的合金的断裂时间明显下降,原因是,结合图3和图4,c含量太低时,晶界钉扎不充分,合金主要通过动态回复软化,不利于再结晶形核而影响了动态再结晶的充分进行,而c含量达到0.055%后,锻造加工后碳化物出现条带状分布现象,且在退火处理后条带状分布的碳化物也没有明显变化,从而对合金的力学性能产生不利影响,因此将c元素的含量控制在0.03-0.05%的范围内。
61.(3)zr、b和mn元素含量对合金性能的影响分析:
从表3-5中可以看出,当zr元素的含量为0时,对合金的室温力学性能和高温力学性能影响不是很大,但是从对比例7中看出,合金的室温塑性、高温塑性、高温持久性都下降了,而当zr元素的含量为0.06%,超出本技术限定的范围后,合金的室温力学性能上升,但高温的持久性大大降低,因此将zr的含量限定在0.01-0.03%的范围内时,有助于保持合金的力学性能、塑性以及高温持久性。
62.b和mn元素含量为0时,合金的室温塑性、高温塑性和高温持久性都明显下降。
63.本具体实施方式的实施例均为本发明的较佳实施例,并非依此限制本发明的保护范围,故:凡依本发明的结构、形状、原理所做的等效变化,均应涵盖于本发明的保护范围之内。
再多了解一些
本文用于创业者技术爱好者查询,仅供学习研究,如用于商业用途,请联系技术所有人。