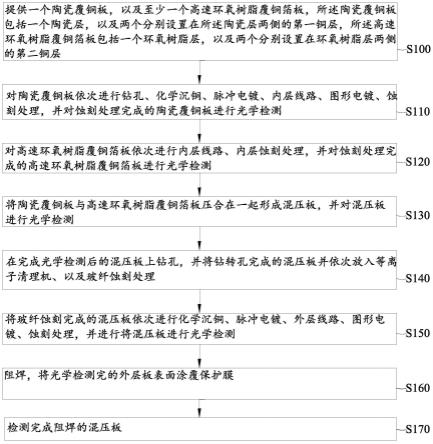
1.本发明属于pcb板制作技术领域,特别是一种制作陶瓷混压正凹蚀板的方法。
背景技术:
2.正凹蚀,是将多层芯板经压合、钻孔,钻孔后将孔壁上的环氧树脂和玻璃纤维丝蚀刻到一定深度,使内层线路铜层完全裸露出来,然后经孔壁金属化,使内层线路铜层与孔壁镀铜层形成三维连接,以满足高可靠性电气连接的一类印制电路板。随着航天、军工技术的快速推进,设计师对产品性能和可靠性的要求越来越高。并且现目前航天、军工产品,其常常用于极热、极寒、高压等恶劣环境下,电子部件必须满足可靠性的要求,正凹蚀工艺已形成主流研发项目。
3.如中国专利一种正凹蚀pcb的制作方法,专利号为cn201811502710.9,其通过在生产板上先钻出一个辅助孔并对其金属化后,作为电镀时的导电层,而后再钻出连接孔,并通过电镀把连接孔内的内层线路铜层进行径向加厚而裸露凸出于孔壁,从而使后期电镀的孔壁铜层与凸出的内层线路铜层之间形成三维连接。目前为了提升pcb板的可靠性高、以及使用寿命,通过陶瓷覆铜板与高速环氧树脂覆铜箔板压合加工形成pcb板,但该正凹蚀pcb的制作方法,无法适用于陶瓷覆铜板与高速环氧树脂覆铜箔板之间的连接。
技术实现要素:
4.有鉴于此,本发明提供了一种制作陶瓷混压正凹蚀板的方法,以满足工业需求。
5.一种制作陶瓷混压正凹蚀板的方法包括如下步骤:
6.步骤s100:提供一个陶瓷覆铜板,以及至少一个高速环氧树脂覆铜箔板,所述陶瓷覆铜板包括一个陶瓷层,以及两个分别设置在所述陶瓷层两侧的第一铜层,所述高速环氧树脂覆铜箔板包括一个环氧树脂层,以及两个分别设置在环氧树脂层两侧的第二铜层;
7.步骤s110:对陶瓷覆铜板依次进行钻孔、化学沉铜、脉冲电镀、内层线路、图形电镀、蚀刻处理,并对蚀刻处理完成的陶瓷覆铜板进行光学检测;
8.步骤s120:对高速环氧树脂覆铜箔板依次进行内层线路、内层蚀刻处理,并对蚀刻处理完成的高速环氧树脂覆铜箔板进行光学检测;
9.步骤s130:将陶瓷覆铜板与高速环氧树脂覆铜箔板压合在一起形成混压板,并对混压板进行光学检测;
10.步骤s140:在完成光学检测后的混压板上钻孔,并将钻孔完成的混压板并依次放入等离子清理机、以及玻纤蚀刻处理;
11.步骤s150:将玻纤蚀刻完成的混压板依次进行化学沉铜、脉冲电镀、外层线路、图形电镀、蚀刻处理,并进行将混压板进行光学检测;
12.步骤s160:阻焊,将光学检测完的外层板表面涂覆保护膜。
13.进一步地,所述制作陶瓷混压正凹蚀板的方法还包括步骤s170:检测完成阻焊的混压板。
14.进一步地,完成步骤s110、完成步骤s140分别测量陶瓷覆铜板、以及高速环氧树脂覆铜箔板的涨缩。
15.进一步地,在步骤s130中,所述陶瓷覆铜板与高速环氧树脂覆铜箔板之间通过pp层粘合。
16.进一步地,在步骤s150中玻纤蚀刻为通过氟化氢铵、硫酸混合溶液进行蚀刻。
17.进一步地,在步骤s140中等离子清理机将由氧气、氮气和四氟化碳组成的混合气体通过高电压电离形成等离子气体,然后通过等离子气体轰击混压板的孔壁,对板料孔壁进行清洁、改性、光刻胶灰化。
18.与现有技术相比,本发明提供的制作陶瓷混压正凹蚀板的方法中通过对陶瓷覆铜板、高速环氧树脂覆铜箔板形成的混压板依次进行离子清理机、以及玻纤蚀刻处理,提升混压板的质量。制作陶瓷混压正凹蚀板的方法中先将陶瓷覆铜板依次进行钻孔、化学沉铜、脉冲电镀、内层线路、图形电镀、蚀刻处理,并对蚀刻处理完成的陶瓷覆铜板进行光学检测。对高速环氧树脂覆铜箔板依次进行内层线路、蚀刻处理,并对蚀刻处理完成的高速环氧树脂覆铜箔板进行光学检测。将陶瓷覆铜板与高速环氧树脂覆铜箔板压合在一起形成混压板,并对混压板进行光学检测。在完成光学检测后的混压板上钻孔,并将钻孔完成的混压板并依次放入等离子清理机、以及玻纤蚀刻处理,将玻纤蚀刻完成的混压板依次进行化学沉铜、脉冲电镀、外层线路、图形电镀、蚀刻处理,并进行将混压板进行光学检测。其中等离子清理机、以及处理将混压板的孔壁树脂进行咬蚀一定深度,使内层铜凸显出来,树脂除去后通过孔壁玻纤需通过玻纤蚀刻处理将进行咬蚀从而使孔壁粗糙度满足要求,且混压板中孔内的各个铜层之间在化学沉铜的过程中,将铜层形成三维链接,从而加强了可靠性性能。该制作陶瓷混压正凹蚀板的方法实现了陶瓷覆铜板与高速环氧树脂覆铜箔板之间的压合,可靠性高,可进行高密度组装、使用寿命长。
附图说明
19.图1为本发明提供的制作陶瓷混压正凹蚀板的方法的流程示意图。
20.图2为本发明提供的制作陶瓷混压正凹蚀板的方法中混压板的剖面结构示意图。
具体实施方式
21.以下对本发明的具体实施例进行进一步详细说明。应当理解的是,此处对本发明实施例的说明并不用于限定本发明的保护范围。
22.如图1至图2所示,其为本发明提供的制作陶瓷混压正凹蚀板的方法的流程示意图。
23.一种制作陶瓷混压正凹蚀板的方法包括如下步骤:
24.步骤s100:提供一个陶瓷覆铜板10,以及至少一个高速环氧树脂覆铜箔板20,所述陶瓷覆铜板10包括一个陶瓷层11,以及两个分别设置在所述陶瓷层11两侧的第一铜层12,所述高速环氧树脂覆铜箔板20包括一个环氧树脂层21,以及两个分别设置在环氧树脂层21两侧的第二铜层22;
25.步骤s110:对陶瓷覆铜板10依次进行钻孔、化学沉铜、脉冲电镀、内层线路、图形电镀、蚀刻处理,并对蚀刻处理完成的陶瓷覆铜板10进行光学检测,钻孔为用钻头在陶瓷覆铜
板10上加工出孔;
26.步骤s120:对高速环氧树脂覆铜箔板20依次进行内层线路、蚀刻处理,并对蚀刻处理完成的高速环氧树脂覆铜箔板20进行光学检测,蚀刻为腐蚀外层板铜面并保留外层线路保护层覆盖的铜面形成内层线路;
27.步骤s130:将陶瓷覆铜板10与高速环氧树脂覆铜箔板20压合在一起形成混压板,并对混压板进行光学检测;
28.步骤s140:在混压板上钻孔,并将转孔完成的混压板并依次放入等离子清理机、以及玻纤蚀刻处理;
29.步骤s150:将玻纤蚀刻完成的混压板依次进行化学沉铜、脉冲电镀、外层线路、图形电镀、蚀刻处理,并进行将混压板进行光学检测,化学沉铜为在混压板的孔内的各个铜层之间沉积一层铜,脉冲电镀,外层线路为在混压板外层制作外层线路保护层,图形电镀,蚀刻为腐蚀外层板铜面并保留外层线路保护层覆盖的铜面形成外层线路;
30.步骤s160:阻焊,将光学检测完的混合板表面涂覆保护膜;
31.步骤s170:检测完成阻焊的混压板。
32.如图2所示,为本发明中制作陶瓷混压正凹蚀板的方法中混压板的剖面结构,其所述陶瓷覆铜板10包括一个陶瓷层11,以及两个分别设置在所述陶瓷层11两侧的第一铜层12,所述高速环氧树脂覆铜箔板20包括一个环氧树脂层21,以及两个分别设置在环氧树脂层21两侧的第二铜层22。陶瓷覆铜板10是由陶瓷基材、键合粘接层及导电层而构成,高速环氧树脂覆铜箔为环氧树脂将玻璃纤维织胶合起来制成板状,并在板的侧壁上覆以铜箔,陶瓷覆铜板10、高速环氧树脂覆铜箔20为一种现有技术,在此不再赘述。
33.在步骤s110中,化学沉铜为在陶瓷覆铜板10的孔内的各个铜层之间沉积一层铜,脉冲电镀为陶瓷覆铜板10的孔壁上镀上预设厚度阈值的铜层,内层线路为在陶瓷覆铜板10的第一铜层12上制作内层线路保护层,图形电镀为将内层线路保护层覆盖区域加大铜厚,内层蚀刻为腐蚀陶瓷覆铜板10的第一铜层12并保留内层线路保护层覆盖的铜面形成内层线路。
34.在步骤s120中,内层线路为在高速环氧树脂覆铜箔板20的第二铜层22上制作内层线路保护层、内层蚀刻为腐蚀高速环氧树脂覆铜箔板20的第二铜层22并保留内层线路保护层覆盖的铜面形成内层线路。
35.在步骤s130中,陶瓷覆铜板10与高速环氧树脂覆铜箔板20压合在一起,压合为将陶瓷覆铜板10与高速环氧树脂覆铜箔板20在预设的压合温度阈值以及压力阈值下粘合形成。且陶瓷覆铜板10与高速环氧树脂覆铜箔板20之间通过pp层30粘合,其pp层30为聚丙烯制成,pp层30为一种现有技术。
36.在步骤s140中,混压板通过等离子清理机、以及玻纤蚀刻依次处理,等离子清理机为采用等离子气体轰击混压板的孔壁,等离子清理机将由氧气、氮气和四氟化碳组成的混合气体通过高电压电离形成等离子气体,然后通过等离子气体轰击混压板的孔壁,对板料孔壁进行清洁、改性、光刻胶灰化。在本实施例中,离子清理机清理时间为5min至13min,以保证了混压板中陶瓷覆铜板10、以及高速环氧树脂覆铜箔板20的孔壁除胶效果。
37.混压板容置于等离子清理机内进行除胶,混压板在除胶时间将孔壁树脂进行咬蚀一定深度,使内层铜凸显出来,树脂除去后孔壁玻纤需通过氟化氢铵、硫酸配比药水进行咬
蚀,从而使孔壁粗糙度满足要求,并在步骤s150中在混压板中孔内的各个铜层之间在化学沉铜的过程中,将铜层形成三维链接,加强了可靠性性能。其中玻纤蚀刻为通过氟化氢铵、硫酸混合溶液进行蚀刻,玻纤蚀刻的温度为25
±
2℃,时间为150
±
10s,以使玻纤蚀刻的效果稳定,且满足孔壁粗糙度要求。
38.在完成步骤s110、完成步骤s140后皆通过三元设备分别检测陶瓷覆铜板10、以及高速环氧树脂覆铜箔板20的涨缩,即为测试所述陶瓷覆铜板10、所述高速环氧树脂覆铜箔板20在加工处理过程中是否发生变形,以保证所述陶瓷覆铜板10、所述高速环氧树脂覆铜箔板20的成型质量。其中三元设备为通过三维取点来进行测量的一种仪器,市场上也有叫三坐标测量机,三元设备主要原理是:将被测物体置于三次元测量空间,可获得被测物体上各测点的坐标位置,根据这些点的空间坐标值,经计算求出被测物体的几何尺寸,形状和位置,三元设备为一种现有技术,在此不再赘述。
39.在步骤s150中,混压板依次进行化学沉铜、脉冲电镀、外层线路、图形电镀、蚀刻处理。化学沉铜为在混压板的孔内的各个铜层之间沉积一层铜,脉冲电镀为混压板的孔壁上镀上预设厚度阈值的铜层,外层线路为在混压板中所述陶瓷覆铜板10中可与空气接触的第一铜层12上、或高速环氧树脂覆铜箔板20中可与空气接触的第二铜层22上制作外层线路保护层,图形电镀为将外层线路保护层覆盖区域加大铜厚,蚀刻为混压板保留外层线路保护层覆盖的铜面形成外层线路。在步骤s110、以及步骤s150中,化学沉铜的沉铜厚度皆为0.5um,以使成型后的陶瓷覆铜板10、以及混压板的孔壁的结构稳定。
40.在步骤s160中,在混压板上涂覆保护膜,以防止混压板表面传输过程中损坏。
41.在步骤s170中,将完成阻焊处理的混压板进行检测,以保证该混压板的质量。步骤s110、完成步骤s140后皆通过三元设备检测,以及步骤s170中对完成阻焊处理的混压板进行检测,保证了混压板在加工过程中的产品质量。
42.与现有技术相比,本发明提供的制作陶瓷混压正凹蚀板的方法中通过对陶瓷覆铜板10、高速环氧树脂覆铜箔板20形成的混压板依次进行离子清理机、以及玻纤蚀刻处理,提升混压板的质量。制作陶瓷混压正凹蚀板的方法中先将陶瓷覆铜板10依次进行钻孔、化学沉铜、脉冲电镀、内层线路、图形电镀、蚀刻处理,并对蚀刻处理完成的陶瓷覆铜板10进行光学检测。对高速环氧树脂覆铜箔板20依次进行内层线路、蚀刻处理,并对蚀刻处理完成的高速环氧树脂覆铜箔板20进行光学检测。将陶瓷覆铜板10与高速环氧树脂覆铜箔板20压合在一起形成混压板,并对混压板进行光学检测。在完成光学检测后的混压板上钻孔,并将钻孔完成的混压板并依次放入等离子清理机、以及玻纤蚀刻处理,将玻纤蚀刻完成的混压板依次进行化学沉铜、脉冲电镀、外层线路、图形电镀、蚀刻处理,并进行将混压板进行光学检测。其中等离子清理机、以及处理将混压板的孔壁树脂进行咬蚀一定深度,使内层铜凸显出来,树脂除去后通过孔壁玻纤需通过玻纤蚀刻处理将进行咬蚀从而使孔壁粗糙度满足要求,且混压板中孔内的各个铜层之间在化学沉铜的过程中,将铜层形成三维链接,从而加强了可靠性性能。该制作陶瓷混压正凹蚀板的方法实现了陶瓷覆铜板与高速环氧树脂覆铜箔板之间的压合,可靠性高,可进行高密度组装、使用寿命长。
43.以上仅为本发明的较佳实施例,并不用于局限本发明的保护范围,任何在本发明精神内的修改、等同替换或改进等,都涵盖在本发明的权利要求范围内。
再多了解一些
本文用于创业者技术爱好者查询,仅供学习研究,如用于商业用途,请联系技术所有人。