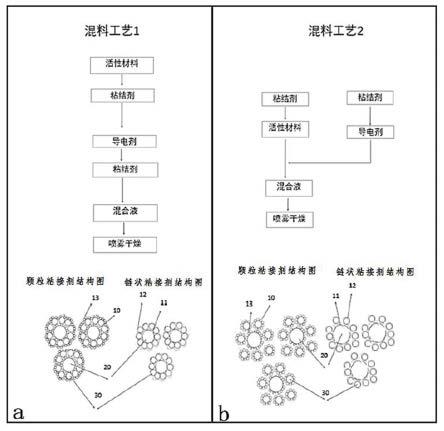
1.本发明属于电极制备技术领域,具体涉及一种制备电极用的复合材料及其制备方法、电极及其制备方法。
背景技术:
2.传统电池的制备工艺一般是将原材料,包括活性材料、粘结剂、导电剂和溶剂等按照一定的工艺流程逐步加入到匀浆罐体中,经过高速搅拌约12h后将这些原材料混合均匀成具有一定流动性和粘度的浆料,再将浆料分别涂覆在集流体的单双面上,然后经过烘干,再碾压分切成需要的极片,这种匀浆、涂布、碾压分切工艺流程时间长,能耗大,且针对于正极材料一般nmp作为溶剂,这款溶剂成本高,且污染环境,需要做回收处理等附加设备等问题,再加上这种工艺下的极片面密度低,压实密度小,已经不能满足新能源车厂对电池能量密度的需求。
3.另外,电池的电极制备也可用于电容的电极制备。因此,电极制备方法的改进,对电池和电容的生产都具有意义。
技术实现要素:
4.基于现有技术的缺陷,本发明采用将原材料预制成复合材料,然后将复合材料经过一步成型技术制备成电极,此工艺制备的电极省去了大型匀浆、涂布、烘干和碾压工序,只需要经过2到3步简单工艺即可实现高压实密度、高面密度、高导电率、强粘接力的电极,这种电极制备工序简单,设备成本低,生产效率高。
5.本发明所提供的技术方案如下:一种制备电极用的复合材料,包括以下重量百分含量的各组分:40%~99%的活性材料、0%~15%的导电剂(不包含零)、0.1~20%的粘结剂和0%~25%的溶剂(不包含零),其中,所述粘结剂为温度大于或等于120℃时具有粘接效果的粘结材料。
6.上述技术方案中:复合材料中的颗粒表面覆盖一层粘结剂,该粘结剂在常温下没有粘接效果,在高于120℃温度下具备较强的粘接性,常温下散装的粉体材料在转移过程中不会粘在一起影响成膜效果,热压情况下容易形成三维立体结构的自支撑膜,从而可避免基于液相涂覆工艺所需要的大型匀浆、涂布、烘干和碾压工序。
7.上述技术方案中:溶剂含量≤25%,溶剂含量超出25%,粉体容易结块,不利于下一工序的成膜分散均匀性;粉体的粒度d50≤20μm,粉体粒度超出20μm,同样会影响下一工序的成膜均匀性;粉体的振实密度在0.3~2.0g/cm3之间。
8.上述技术方案中:电极为电池电极,或电容电极。
9.具体的,所述制备电极用的复合材料为全干或半干粉体。
10.具体的,所述粘结剂为含氟类粘结剂、丁苯橡胶类粘结剂、聚丙烯酸类粘结剂或聚氨酯类粘结剂。
11.优选的,所述粘结剂包含但不限于:聚偏二氟乙烯乳液或者颗粒;聚四氟乙烯乳液或者颗粒;聚丙烯酰胺乳液或者颗粒;聚丙烯腈乳液或者颗粒;聚甲基丙烯酸甲酯或者颗粒;聚丁苯橡胶乳液。
12.具体的,所述活性材料选自可嵌锂离子或钠离子的钛酸锂、硬碳、石墨、活性炭、si基材料、sn基、 sb基、 pb基、磷或磷化物材料中的任意一种或多种的混合;或者,所述活性材料选自可嵌锂离子或钠离子的层状结构氧化物、橄榄石磷酸盐、尖晶石结构、无机配合物或有机钠盐化合物中的任意一种或多种的混合。
13.具体的,所述导电剂选自0维导电剂、1维导电剂、2维导电剂或3维导电剂中的任意一种或多种的混合。
14.0维导电剂可例如炭黑、乙炔黑、科琴黑等。
15.1维导电剂可例如碳纳米纤维、单壁纳米管等、多壁纳米管等。
16.2维导电剂主要是mxene可例如石墨烯、碳钛化合物、钛氮化合物等。
17.3维导电剂可例如鳞片石墨导电剂、球形导电石墨等。
18.具体的,所述溶剂选自去离子水、n-甲基吡咯烷酮、乙醇或丙酮中的任意一种或多种的混合。
19.本发明还提供了上述制备电极用的复合材料的制备方法,其特征在于,包括以下步骤:按照配方的量,将活性材料、导电剂、粘结剂和溶剂加入到分散容器中,在50-70℃下分散,让粘结剂包覆在颗粒表面,然后将分散均匀后的浆料采用喷雾干燥的方式挥发溶剂,剩下散状粉料,即为分散均匀的制备电极用的复合材料。
20.上述技术方案中,根据活性材料、导电剂、粘结剂和溶剂的添加顺序不一样,形成的复合材料的结构有不同的情况,并有各自的优点。
21.具体的,按照活性材料、部分粘结剂、导电剂和剩下的粘结剂的顺序依次混料。
22.基于上述技术方案,可形成层层包覆的层状结构的复合材料,在保证粘接的情况下有利于导电网络的最大化利用。
23.具体的,按照将部分粘结剂与活性材料混合得到第一混合料,将剩下的粘结剂与导电剂混合得到第二混合料,再将第一混合料和第二混合料混合的顺序混料。
24.基于上述技术方案,在保证导电性的同时增强颗粒间的结构稳定性,便于成膜。
25.本发明还提供了一种电极的制备方法,至少包括以下步骤:1)采用温度为120-180℃的碾压对辊将本发明所提供的所述的制备电极用的复合材料成型为三维立体的自支撑膜;2)在集流体箔的至少一面上复合上所述的三维立体的自支撑膜,得到所述的电极。
26.具体的,包括以下步骤:1)分别采用温度为120-180℃的碾压对辊将本发明所提供的所述的制备电极用的复合材料成型为三维立体的自支撑膜,得到第一自支撑膜和第二自支撑膜;2)采用温度为150-170℃的碾压对辊将所述第一自支撑膜和第二自支撑膜分别复合到集流体箔的两个表面上,得到所述的电极。
27.基于上述技术方案,电极的制备工艺流程从喷雾开始到成品电极完成,工序流程紧凑,即可适用于小型产线,也可以应用于大型产线。
28.具体的,包括以下步骤:1)采用温度为150-180℃的碾压对辊将本发明所提供的所述的制备电极用的复合材料成型到集流体箔的一面上,在集流体箔的一面上形成三维立体的自支撑膜;2)采用温度为150-180℃的碾压对辊将本发明所提供的所述的制备电极用的复合材料成型到集流体箔的另一面上,在集流体箔的另一面上形成三维立体的自支撑膜,得到所述的电极。
29.本发明还提供了根据上述制备方法制备得到的电极。
附图说明
30.图1是本发明所提供的混料工艺的原理图。
31.图2是本发明所提供的一个电极制备工艺流程图。
32.图3是本发明所提供的另一个电极制备工艺流程图。
具体实施方式
33.以下对本发明的原理和特征进行描述,所举实施例只用于解释本发明,并非用于限定本发明的范围。
34.实施例1如图1的a部分所示的混料工艺1,按照活性材料、部分粘结剂、导电剂和剩下的粘结剂的顺序依次混料。所形成的复合材料的结构是中间为活性材料20,活性材料20周围包覆一层颗粒状10(例如采用聚丙烯酸类乳液所形成的)或者链状结构11(采用pvdf乳液所形成的)的粘结剂,再将导电剂30包覆在粘结剂10或者11的外层,最后再将粘结剂12或者13包覆在导电剂30的外城,其中粘结剂10与13相同,粘结剂11与12相同;采用混料工艺1形成的这样形成层层包覆的层状结构的复合材料,在保证粘接的情况下有利于导电网络的最大化利用。
35.实施例2如图1的b部分所示的混料工艺2,按照将部分粘结剂与活性材料混合得到第一混合料,将剩下的粘结剂与导电剂混合得到第二混合料,再将第一混合料和第二混合料混合的顺序混料。所形成的复合材料的结构是先将链状粘结剂11和颗粒状粘结剂13分别包覆在活性材料20的表面,同时将链状粘结剂12和颗粒状粘结剂10分别包覆在导电剂30的表面,然后再将粘结剂包覆完好的导电剂包覆在粘结剂包覆完好的活性材料表面,采用这种结构的复合材料优点是在保证导电性的同时增强颗粒间的结构稳定性,便于成膜。
36.实施例3如图2所示,将喷雾干燥出来的复合材料经过管道c48存储到料槽c41中,然后将料槽c41中的复合材料均匀的传送到平台c46上,然后传送给温度在120-180℃之间的碾压对辊c42间,形成三维立体的自支撑膜c48,上下2个独立的自支撑膜进入温度在150-170℃间的对辊c47中,分别复合在集流体箔c43的a/b面上,制备出电极c44,电极c44通过高温隧道炉进行烘干,将剩余的溶剂烘烤出去后,电极就可以进去组装工序;此电极的制备工艺流程
从喷雾开始到成品电极完成,工序流程紧凑,即可适用于小型产线,也可以应用于大型产线。
37.实施例4如图3所示,将喷雾干燥出来的复合材料经过管道c48存储到料槽c41中,然后将料槽c41中的复合材料均匀的喷洒到集流体箔c43,然后经过150-180℃的对辊c42将复合材料c40复合到集流体箔c43上,形成单面涂覆的电极c49,经过2个导向辊c45进入第二个料槽c41,将从喷雾管槽c48中喷出来的复合材料c40喷洒到单面电极c49上,再次经过150-180℃的对辊c47形成双面电极c44,经过红外高温隧道炉烘烤后进入组装工序。
38.实施例5将原材料活性材料活性炭、粘结剂球形聚丙烯腈乳液、导电剂炭黑和溶剂去离子水,按照配方活性材料:粘结剂:导电剂=80:10:10的配方分散均匀,固含量为40%,分散工艺如下:采用研磨分散机,将活性炭加入到研磨机中,然后加入85%重量的粘结剂,加热至55℃,进行研磨2h,然后一次性加入导电剂super_p li,进行研磨1h后,加入剩余的15%粘结剂乳液,研磨2h后,加入溶剂调整固含量到40%,然后进行喷雾干燥,干燥完成后的复合材料为散状颗粒,在常温下无粘接性;此时散装颗粒的溶剂含量为5.3%,振实密度为0.46g/cm3,d50为8.3μm;将此散装复合材料采用热压160
±
2℃下采用电极制备工艺流程2(图3)直接复合在铝箔上,然后经过长度为5米的红外烘箱后,得到活性炭电极,此电极的双面面密度为230g/m2,碳膜厚度为0.280mm,压实密度为0.82 g/cm3,于此同时测试的极片剥离强度为0.08kgf/cm,此电极的电导率为0.004s/cm。
39.将上述极片组装成3000f电容结构相同的电容,卷芯直径为56.0
±
0.1mm,经过烘烤注液后,测试容量、esr和耐久性测试,测试数据见表1。
40.实施例6将原材料活性材料活性炭、粘结剂球形聚丙烯腈乳液、导电剂炭黑和溶剂去离子水,按照配方活性材料:粘结剂:导电剂=80:10:10的配方分散均匀,固含量为40%,分散工艺如下:采用行星式搅拌机,先将活性材料加入到85%粘结剂乳液中,加热至55℃,高速搅拌5h后,加入所需要的导电剂,搅拌3h,然后加入15%剩余的粘结剂乳液,搅拌4h后,加入溶剂调整固含量到40%,然后采用挤压式涂布机进行涂覆,涂覆双面面密度为140g/m2;然后采用热压方式进行碾压,碾压碳膜厚度为0.233mm,压实密度为0.6 g/cm3;测试的极片剥离强度为0.03 kgf/cm,电极的电导率为0.001s/cm。
41.将上述极片组装成3000f电容结构相同的电容,卷芯直径为56.0
±
0.1mm,经过烘烤注液后,测试容量、esr和耐久性测试,测试数据见表1。
42.实施例7将原材料活性材料活性炭、粘结剂链状聚四氟乙烯乳液、导电剂super_p li和溶剂去离子水,按照配方活性材料:粘结剂:导电剂=80:10:10的配方分散均匀,固含量为40%,分散工艺如下:采用研磨分散机1,将活性炭一次性加入到85%的聚四氟乙烯乳液中,研磨2h,在第二台研磨分散机2中将所需要的导电剂super_p li添加到剩余的15%聚四氟乙烯乳液中,加热至55℃,分散2h后,将导电剂 聚四氟乙烯乳液添加到研磨分散机1中,分散2h后形成均匀分散的混合液,将混合液固含量调制40%固含量后进行喷雾干燥,形成复合材料;复合材料
的溶剂含量为8.6%,阵实密度0.48g/cm3,d50为8.2μm;将此复合材料采用电极制备工艺流程1(图2),对辊c42温度为150
±
2℃下形成三维立体的自支撑膜,上下2条的自支撑膜竞经过对辊c47,温度为155
±
2℃下制备成电极c44,经过红外隧道烘烤后测试涂覆双面面密度为256g/m2,碳膜厚度为0.301mm,压实密度为0.85 g/cm3,极片剥离强度为0.086kgf/cm,电导率为0.0036s/cm。
43.将上述极片组装成3000f电容结构相同的电容,卷芯直径为56.0
±
0.1mm,经过烘烤注液后,测试容量、esr和耐久性测试,测试数据见表1:表1 将以上活性材料、导电剂、粘结剂和溶剂经过图1中的两种不同的混料方式进行分散,从混料工艺1(图1中a部分)和混料工艺2(图1中b部分)可发现,不同的物料添加顺序,各成分间的接触方式不同,但最外一层的物料均为粘结剂,最外一层为粘结剂的原因是为了后面工序的成膜;分散方式可采用研磨、行星式搅拌、气流方式进行分散;一种复合材料及其电极的制备方法中,其中的电极是将半干或全干的复合材料在热压环境下形成三维立体结构的柔性膜, 成膜的工艺流程见图2、3;成膜后的极片可采用目前锂离子电池或者钠离子电池的组装工艺进行组装,或者,采用目前电容的组装工艺进行组装。
44.以上所述仅为本发明的较佳实施例,并不用以限制本发明,凡在本发明的精神和原则之内,所作的任何修改、等同替换、改进等,均应包含在本发明的保护范围之内。
再多了解一些
本文用于创业者技术爱好者查询,仅供学习研究,如用于商业用途,请联系技术所有人。