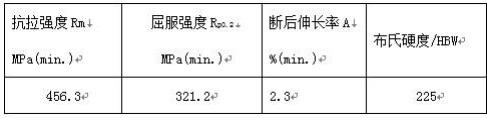
1.本发明属于蠕墨铸铁技术领域,具体涉及一种铸造蠕墨制动盘的生产工艺。
背景技术:
2.铸铁中的蠕虫状石墨在20世纪四五十年代发现球墨铸铁时就已发现,但由于获得困难及对其性能认识不足,直到70年代蠕铁才开始应用于工业生产中,比球铁的应用晚了近30年。我国在七八十年代,研究和应用蠕铁曾风靡一时,后渐转入沉寂。直到21世纪初,随着蠕铁在汽车缸体、缸盖上的应用成功,研究与应用又渐多了起来,且与adi、高韧性球铁并称“新铁器时代”的象征。蠕墨铸铁的强度和韧性高于灰口铸铁,但不如球墨铸铁:铸造性与灰口铸铁相当。蠕墨铸铁的耐磨性较好,它适用于制造重型机床床身、机座、活塞环、液压件等。蠕墨铸铁的导热性比球墨铸铁要高得多,几乎接近于灰口铸铁,它的高温强度、热疲劳性能大大优于灰口铸铁,适用于制造承受交变热负荷的零件,如钢锭模、结晶器、排气管和气缸盖等。蠕墨铸铁的减振能力优于球墨铸铁。目前人们采用球化剂作蠕化剂,加入不足量的球化剂,使其球化不良而成蠕铁。这种方法极难控制获得满意的蠕化率。20世纪70年代有工厂采用这方法生产蠕铁,使用冲天炉熔炼,事先测定铁液中的含s量,控制好铁液温度和出液量,根据镁和稀土的吸收率确定最终的蠕化剂加入量,可得到合格的蠕铁。另一种方法是先把铁液处理成球铁,测定其mg残和re残,再兑入一定量的灰铁铁液,最终成为蠕铁。这种方法同样难以控制。铁水蠕化处理常用的方法有包底冲入法和出铁槽冲入法。中国专利cn2018112265891公开了一种蠕墨铸铁全液压转向器体壳铸件的铸造工艺,其将蠕化剂加入铁水包底,采用堤坝式包底冲入法包底冲入法。就是将蠕化剂先加到铁水包内,再出铁水,使蠕化剂在铁水流的冲击作用下熔解到铁水中,达到蠕化的目的,生产的球铁铸件的质量不稳定,这种方法要求蠕化剂含有镁,自身有起爆能力。出铁槽冲入法这种方法是在出铁过程中,将蠕化剂随铁水流加入到出铁槽中,使蠕化剂充分熔解到铁液中,使铁水蠕化。本领域技术人员亟待开发出一种铸造蠕墨制动盘的生产工艺以满足现有的应用市场和性能需求。
技术实现要素:
3.有鉴于此,本发明提供一种铸造蠕墨制动盘的生产工艺。
4.一种铸造蠕墨制动盘的生产工艺,包括常规的备砂、造砂型和炉料熔炼、蠕化孕育、浇注冷却、开箱、铸件清理、二次蠕化热处理步骤;其中浇注铁水中的化学成分质量百分比为:c3.4-3.8%、si1.8-2.4%、mn0.4-0.8%、p≤0.08%、s≤0.08%、cr≤0.3%、cu0.2-0.6%、mg0.01-0.03%、sn0.03-0.07%、fe为余量。
5.进一步的,炉料熔炼步骤包括配置炉料和熔炼,熔炼为往感应电炉中加入废钢和回炉铁,待电炉升温至1180~1240℃加入固定碳含量为82~88%的粒度10~30mm石墨球增碳剂。
6.进一步的,炉料配置质量百分比为:回炉铁33~37%、废钢60~62%;熔炼采用中频
感应电炉进行铁液熔炼,熔炼温度为1470~1530℃。
7.进一步的,所述蠕化、孕育处理为向炉料中的铁水依次喂入蠕化丝和孕育丝,其中孕育丝的加入量为铁液总质量的0.1~0.3wt%,孕育丝的线径13.0mm、线重170g/m的sica包芯线,其中孕育丝含si55wt%、ca28wt%,蠕化丝成分为镁3.8-4.3wt%、镧2.8-3.3wt%、钙2.8-3.3wt%、钛3.8-4.3wt%、硅44-46wt%、铝《0.8wt%、铁余量,线重170~185g/m,直径8-10mm圆形丝;喂丝速度:4-7m/s、喂蠕化丝长度30~34m,主机旋转速度14m/min,旋转角度0~180
°
,导线管角度30
°
。
8.进一步的,所述浇注工序中,当达到1360℃~1380℃时,即可进行浇注,浇注的同时采用0.1%-0.15%质量分数的钡硅孕育剂进行二次瞬时孕育,然后撒入除渣覆盖剂,迅速扒净铁液表面的渣子,最后覆盖草木灰进行浇注,所述硅钡孕育剂的成分硅≥65wt%,钡2.0-6.0wt%、钙:1.0~2.0wt%、铝1.0-2.0wt%,硅钡孕育剂粒度为0.2~0.8mm。
9.进一步的,还包括自然冷却、铸件清理后进行二次蠕化热处理步骤为随炉加热至790~820℃下保温90~120min,25℃/min速率降温至700~720℃保温40~60min后,25℃/min速率降温至室温。
10.本发明的有益效果:本发明公开了一种铸造蠕墨制动盘的生产工艺,蠕化处理后的铁液,进行二次孕育处理,可以减小稀土镁引起的白口倾向,改善石墨形态和抑制铸件中形成自由渗碳体组织;孕育包芯丝的加入可以改善组织,增加共晶团数,延缓蠕化衰退。随后进行二次蠕化热处理,可以使使碳化物熔断,进行保温,使碳化物部分溶入,冷却后细小的蠕状碳化物均匀分布,得到粒状珠光体组织。
11.本发明相比现有技术具有如下优点:本发明通过通过调整合金材料的化学成分含量配方,保证产品的机械性能、外观精度,喂丝法有控制精确、改善劳动环境的优点,以往使用工艺不稳定的冲入法时,mg的吸收率波动大,对蠕墨铸铁来说往往有处理过头的现象,本发明由于蠕墨铸铁对于金属基体割裂作用有良好改善,与灰口铸铁件相比较,具有机械强度高、耐热疲劳性能好、抗氧化、塑性强、导热性能优良、使用寿命长、应用范围广等特点。蠕墨铸铁具较高的力学性能、导热性和优良的耐热疲劳性能,是制造制动盘盘体的理想材料,制动盘具有稳定的磨擦系数、低而稳定的磨损率、较高的使用寿命及良好的制动性能,解决了以往制动盘导热性差、高温强度差、高耐磨性差和抗疲劳强度低,易开裂、易涨裂的缺点,特别适应于载重汽车制动盘的制造,可以大幅度提高制动安全性和使用寿命。
具体实施方式
12.实施例1一种铸造蠕墨制动盘的生产工艺,包括以下步骤:第一步、备砂、造砂型,落砂后的旧砂经s997磁选分离机3000gs下磁选后进入振动筛筛分,冷却后由带式输送机送入混砂机上方的旧砂斗中;购入的新砂经一系列输送系统进入新砂斗,经由翻斗加料机加入旧砂系统中。旧砂经给料机进入hm285-160混砂机的主料秤中称量;煤粉、粘土粉经螺旋给料机先后进入混砂机的辅料秤中称量;所需水分则经混砂机给水装置自动定量。以上各料按设定的配比称量后,加入混砂机中混制,得到合格型砂方可排放。合格的型砂排放至圆盘卸砂斗
中,经输送机送往垂直分型造型机disa131b供造型线使用;第二步、炉料熔炼炉:料熔炼步骤包括配置炉料和熔炼,由带电子秤、吸铁盘的起重机配料、配好的炉料(回炉铁、废钢)由起重机送到振动加料车,由加料车向电炉加料进行熔炼;熔炼为往感应电炉中加入废钢和回炉铁,待电炉升温至1240℃加入固定碳含量为88%的粒度30mm石墨球增碳剂,炉料配置质量百分比为:回炉铁37wt%、废钢62wt%、1wt%石墨球增碳剂;熔炼采用中频感应电炉进行铁液熔炼,熔炼温度为1530℃;第三步、蠕化孕育:蠕化、孕育处理为向炉料中的铁水依次喂入蠕化丝和孕育丝,其中孕育丝的加入量为铁液总质量的0.3wt%,孕育丝的线径13.0mm、线重170g/m的sica包芯线,其中孕育丝含si55wt%、ca28wt%,蠕化丝成分为镁4.3wt%、镧3.3wt%、钙3.3wt%、钛4.3wt%、硅46wt%、铝《0.8wt%、铁余量,线重185g/m,直径10mm圆形丝;wx-58f喂丝机的喂丝速度:7m/s、喂蠕化丝长度34m,主机旋转速度14m/min,旋转角度0~180
°
,导线管角度30
°
;第四步、浇注:浇注工序中,当达到1380℃时,即可进行浇注,由叉车、起重机将铁液运至浇注机辊道,采用机械浇注方式,浇注的同时采用0.15%质量分数的钡硅孕育剂进行二次瞬时孕育,所述硅钡孕育剂的成分硅≥65wt%,钡2.0-6.0wt%、钙:1.0~2.0wt%、铝1.0-2.0wt%,硅钡孕育剂粒度为0.8mm,然后撒入信阳金辉jh-2除渣覆盖剂,迅速扒净铁液表面的渣子,最后覆盖草木灰进行浇注,浇注铁水中的化学成分质量百分比为:c3.8%、si2.4%、mn0.8%、p≤0.08%、s≤0.08%、cr≤0.3%、cu0.6%、mg0.03%、sn0.07%、fe为余量;第五步、冷却、开箱、铸件清理:自然冷却至室温后开箱,落砂通过滚筒的旋转,将其中的砂型与铸件一起滚动、跌落、相互撞击,实现砂型和铸件的分离;铸件的清理铸件铸型、缸盖铸件从砂箱脱出后,冷却一段时间,由机械手抓取送往清理工部。首先在落砂机上进行铸件清砂,通过液压浇冒口去除浇冒口,打掉飞边,进行抛丸处理,先是抛丸机抛丸,然后是人工对铸件的飞边、毛刺、浇口气针的残留进行打磨清理;第六步、二次蠕化热处理步骤:二次蠕化热处理步骤为随炉加热至790℃下保温9min,25℃/min速率降温至700℃保温40min后,25℃/min速率降温至室温。
13.产品极限偏差中孔直径 0.1mm、底面厚度
±
0.2mm、内孔深度
±
0.2mm,制动面厚度
±
0.1mm、制动面跳动0.1mm、螺栓孔位置度0.25mm,蠕化率为大于90%;珠光体数量大于60%。
14.对实施例1的制动盘进行物理力学性能的检测,检测结果如表1所示.表1实施例1的制动盘的物理力学性能测试结果实施例2一种铸造蠕墨制动盘的生产工艺,包括以下步骤:第一步、备砂、造砂型,落砂后的旧砂经s997磁选分离机3000gs下磁选后进入振动筛筛分,冷却后由带式输送机送入混砂机上方的旧砂斗中;购入的新砂经一系列输送系统进入新砂斗,经由翻斗加料机加入旧砂系统中。旧砂经给料机进入hm285-160混砂机的主料秤中称量;煤粉、粘土粉经螺旋给料机先后进入混砂机的辅料秤中称量;所需水分则经混砂机给水装置自动定量。以上各料按设定的配比称量后,加入混砂机中混制,得到合格型砂方可排放。合格的型砂排放至圆盘卸砂斗
中,经输送机送往垂直分型造型机disa131b供造型线使用;第二步、炉料熔炼炉:料熔炼步骤包括配置炉料和熔炼,由带电子秤、吸铁盘的起重机配料、配好的炉料(回炉铁、废钢)由起重机送到振动加料车,由加料车向电炉加料进行熔炼;熔炼为往感应电炉中加入废钢和回炉铁,待电炉升温至1180℃加入固定碳含量为82%的粒度10mm石墨球增碳剂,炉料配置质量百分比为:回炉铁33wt%、废钢60wt%、0.9wt%石墨球增碳剂、生铁6.1wt%;熔炼采用中频感应电炉进行铁液熔炼,熔炼温度为1470℃;第三步、蠕化孕育:蠕化、孕育处理为向炉料中的铁水依次喂入蠕化丝和孕育丝,其中孕育丝的加入量为铁液总质量的0.1wt%,孕育丝的线径13.0mm、线重170g/m的sica包芯线,其中孕育丝含si55wt%、ca28wt%,蠕化丝成分为镁3.8wt%、镧2.8wt%、钙2.8wt%、钛3.8wt%、硅44-46wt%、铝《0.8wt%、铁余量,线重170g/m,直径8mm圆形丝;wx-58f喂丝机的喂丝速度:4m/s、喂蠕化丝长度30m,主机旋转速度14m/min,旋转角度0~180
°
,导线管角度30
°
;第四步、浇注:浇注工序中,当达到1360℃时,即可进行浇注,由叉车、起重机将铁液运至浇注机辊道,采用机械浇注方式,浇注的同时采用0.1%质量分数的钡硅孕育剂进行二次瞬时孕育,所述硅钡孕育剂的成分硅≥65wt%,钡2.0-6.0wt%、钙:1.0~2.0wt%、铝1.0-2.0wt%,硅钡孕育剂粒度为0.2mm,然后撒入石川f2除渣覆盖剂,迅速扒净铁液表面的渣子,最后覆盖草木灰进行浇注,中浇注铁水中的化学成分质量百分比为:c3.4%、si1.8%、mn0.4%、p≤0.08%、s≤0.08%、cr≤0.3%、cu0.2%、mg0.01-0.03%、sn0.03%、fe为余量;第五步、冷却、开箱、铸件清理:自然冷却至室温后开箱,落砂通过滚筒的旋转,将其中的砂型与铸件一起滚动、跌落、相互撞击,实现砂型和铸件的分离;铸件的清理铸件铸型、缸盖铸件从砂箱脱出后,冷却一段时间,由机械手抓取送往清理工部。首先在落砂机上进行铸件清砂,通过液压浇冒口去除浇冒口,打掉飞边,进行抛丸处理,先是抛丸机抛丸,然后是人工对铸件的飞边、毛刺、浇口气针的残留进行打磨清理;第六步、二次蠕化热处理步骤:二次蠕化热处理步骤为随炉加热至790℃下保温90min,25℃/min速率降温至700℃保温40min后,25℃/min速率降温至室温。
15.产品极限偏差中孔直径 0.1mm、底面厚度
±
0.2mm、内孔深度
±
0.2mm,制动面厚度
±
0.1mm、制动面跳动0.1mm、螺栓孔位置度0.25mm,蠕化率为大于90%;珠光体数量大于60%。
16.对实施例2的制动盘进行物理力学性能的检测,检测结果如表2所示表2实施例2的制动盘的物理力学性能测试结果注:试验方法化学成份在试块或本体试样上钻屑取样,钻头直径8mm,转速200r/min,一块试样上取4个点,铁屑混匀后按gb/t223.3-1988钢铁及合金化学分析方法二安替比林甲烷磷钼酸重量法测定磷量测定磷含量、gb/t223.4-2008钢铁及合金锰含量的测定电位滴定或可视滴定法测定锰含量、gb/t223.5-2008钢铁酸溶硅和全硅含量的测定还原型硅钼酸盐分光光度法测定硅含量、gb/t223.69-2008钢铁及合金碳含量的测定管式炉内燃烧后气体容量法测定碳含量、gb/t223.72-2008钢铁及合金硫含量的测定重量法测定硫含量。抗拉强度抗拉试棒按gb/t9439-2010灰铸铁件制备,采用单铸试棒,试棒长300mm,直径30,须
用浇注铸件的同一批铁水浇注。按gb/t228.1-2021金属材料拉伸试验第1部分:室温试验方法的规定进行,在we-100液压万能拉伸机上进行;硬度按gb/t231.3-2022金属材料布氏硬度试验第3部分:标准硬度块的标定的规定进行,采用布氏硬度计测量;金相组织按gb/t26656-2011蠕墨铸铁金相检验的规定进行。
再多了解一些
本文用于创业者技术爱好者查询,仅供学习研究,如用于商业用途,请联系技术所有人。