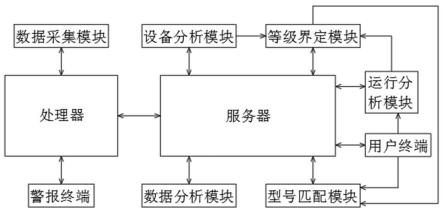
1.本发明属于化工生产领域,涉及设备智能控制技术,具体是一种化工生产用设备智能化控制系统及控制方法。
背景技术:
2.化工是运用化学方法改变物质组成、结构或合成新物质的技术,也就是化学工艺,所得产品被称为化学品或化工产品。起初,生产这类产品的是手工作坊,后来演变为工厂,并逐渐形成了一个特定的生产行业即化学工业。人类与化工的关系十分密切,有些化工产品在人类发展历史中,起着划时代的重要作用,它们的生产和应用,甚至代表着人类文明的一定历史阶段。
3.在化工生产中,需要对化工生产设备进行生产监测,特别利用催化剂得到粗品产物的化工生产设备,但是由于设备、运行状态等多重因素影响下,导致化工生产设备的化工生产不尽相同,因此采用统一的生产监测标准已无法适用当下化工生产设备的生产情况,为此,我们提出一种化工生产用设备智能化控制系统及控制方法。
技术实现要素:
4.针对现有技术存在的不足,本发明目的是提供一种化工生产用设备智能化控制系统及控制方法。
5.本发明所要解决的技术问题为:如何基于多重因素设定相应的生产监测标准并对化工生产设备进行生产监测。
6.本发明的目的可以通过以下技术方案实现:一种化工生产用设备智能化控制系统,包括设备内部设置的处理器,所述处理器连接有数据采集模块、警报终端和服务器,所述服务器连接有设备分析模块、等级界定模块、运行分析模块、用户终端、型号匹配模块以及数据分析模块,所述用户终端用于工作人员输入化工生产设备的型号和设备信息,型号匹配模块依据型号用于匹配得到化工生产设备的标准运行数据,所述服务器将标准运行数据发送至运行分析模块、设备信息发送至设备分析模块;所述数据采集模块用于采集化工生产设备在运行期间的实时运行数据并发送至运行分析模块;所述运行分析模块用于对化工生产设备的运行状况进行分析,得到化工生产设备的运行偏差等级发送至等级界定模块;所述设备分析模块用于对化工生产设备进行设备分析,得到化工生产设备的设备使用等级发送至等级界定模块;所述等级界定模块用于对化工生产设备的数据差异包进行界定,得到化工生产设备的数据差异包发送至数据分析模块;同时,所述数据采集模块用于采集化工生产设备中催化剂的初始重量值、以及反应后粗品产物和催化剂实时重量值发送至数据分析模块;所述数据分析模块用于对化工生产设备分离工作的分离数据进行分析,生成工作
正常信号或工作异常信号。
7.进一步地,设备信息为化工生产设备的设备名称、设备出厂时间、故障次数以及每次故障的故障时间;标准运行数据为化工生产设备的标准温度值、标准真空度、标准湿度值、标准分贝值和标准振幅值;实时运行数据为化工生产设备的实时温度值、实时真空度、实时湿度值、实时分贝值和实时振幅值;数据差异包为化工生产设备中催化剂反应前后的预估重量差值范围、以及粗品产物的预估重量值范围。
8.进一步地,所述运行分析模块的分析过程具体如下:在化工生产设备的运行期间内设定若干个时间点,采集化工生产设备在若干个时间点时的实时温度值、实时真空度、实时湿度值、实时分贝值和实时振幅值;计算化工生产设备在若干个时间点时的实时运行数据与标准运行数据的数据差值,得到化工生产设备在若干个时间点时的温度点差值、真空点差值、湿度点差值、分贝点差值和振幅点差值;统计化工生产设备在运行期间内时间点的数量并记为时间点数;若干个时间点时的温度点差值相加求和除以时间点数得到化工生产设备在运行期间的温度偏差值;同理,得到化工生产设备在运行期间的真空偏差值、湿度偏差值、分贝偏差值和振幅偏差值;计算化工生产设备的运行偏差值,运行偏差值比对运行偏差阈值得到化工生产设备的运行偏差等级。
9.进一步地,所述设备分析模块的设备分析过程具体如下:获取化工生产设备的设备出厂时间和故障次数,利用服务器的当前时间减去设备出厂时间得到化工生产设备的使用时长;而后获取化工生产设备每次故障的故障时间,计算化工生产设备的相邻故障间隔时长,相邻故障间隔时长相加求和除以故障次数得到化工生产设备的故障间隔时长;计算得到化工生产设备的设备使用值,设备使用值比对设备使用阈值得到化工生产设备的设备使用等级。
10.进一步地,所述等级界定模块的界定过程具体如下:依据设备使用等级设定对应化工生产设备的第一界定值,依据运行偏差等级设定化工生产设备对应的第二界定值;为第一界定值和第二界定值分配相应的权重系数,计算得到化工生产设备的等级界定值,依据等级界定值得到对应的界定等级;通过界定等级得到化工生产设备对应的数据差异包。
11.进一步地,界定等级包括第一界定等级、第二界定等级和第三界定等级,第一界定等级、第二界定等级和第三界定等级的级别依次递减。
12.进一步地,所述数据分析模块的分析过程具体如下:获取化工生产设备中粗品产物反应前催化剂的初始重量值、反应后催化剂的实时重量值和粗品产物的实时重量值;
若催化剂的实时重量值大于初始重量值,则生成工作异常信号;若催化剂的实时重量值小于等于初始重量值,则计算得到化工生产设备中催化剂反应前后的实时重量差值;而后获取催化剂反应前后的预估重量差值范围、以及粗品产物的预估重量值范围;若催化剂反应前后的实时重量差值处于催化剂反应前后的预估重量差值范围,且粗品产物的实时重量值处于粗品产物的预估重量值范围,则生成工作正常信号;若催化剂反应前后的实时重量差值未处于催化剂反应前后的预估重量差值范围或粗品产物的实时重量值未处于粗品产物的预估重量值范围,则生成工作异常信号。
13.进一步地,所述数据分析模块将工作正常信号或工作异常信号将反馈至服务器;若服务器接收到工作正常信号,则不进行任何操作;若服务器接收到工作异常信号,则将工作异常信号发送中处理器,处理器依据工作异常信号生成警报指令加载至警报终端,警报终端接收到警报指令后进行警报工作。
14.一种化工生产用设备智能化控制系统的控制方法,控制方法具体如下:步骤s101,用户终端输入化工生产设备的型号和设备信息,型号匹配模块依据型号匹配得到化工生产设备的标准运行数据,数据采集模块采集化工生产设备在运行期间的实时运行数据;步骤s102,利用运行分析模块对化工生产设备的运行状况进行分析,得到化工生产设备的运行偏差等级发送至等级界定模块;步骤s103,设备分析模块对化工生产设备进行设备分析,得到化工生产设备的设备使用等级发送至等级界定模块;步骤s104,等级界定模块结合设备使用等级和运行偏差等级对化工生产设备的数据差异包进行界定,得到化工生产设备的数据差异包发送至数据分析模块;步骤s105,数据采集模块采集化工生产设备中催化剂的初始重量值、以及反应后粗品产物和催化剂实时重量值并发送至数据分析模块;步骤s106,利用数据分析模块对化工生产设备分离工作的分离数据进行分析,生成工作正常信号或工作异常信号。
15.与现有技术相比,本发明的有益效果是:本发明中的型号匹配模块依据型号匹配得到化工生产设备的标准运行数据,通过运行分析模块对化工生产设备的运行状况进行分析,得到化工生产设备的运行偏差等级,设备分析模块对化工生产设备进行设备分析,得到化工生产设备的设备使用等级,运行偏差等级和设备使用等级发送至等级界定模块,等级界定模块对化工生产设备的数据差异包进行界定,得到化工生产设备的数据差异包发送至数据分析模块,数据分析模块对化工生产设备分离工作的分离数据进行分析,生成工作正常信号或工作异常信号,本发明结多设备、设备运行等多重因素为化工生产设备设定相应的生产监测标准,并在此生产监测标准下对化工生产设备催化剂和粗品产物的分离工作进行生产监测。
附图说明
16.为了便于本领域技术人员理解,下面结合附图对本发明作进一步的说明。
17.图1为本发明的整体系统框图;图2为本发明的工作流程图。
具体实施方式
18.下面将结合实施例对本发明的技术方案进行清楚、完整地描述,显然,所描述的实施例仅仅是本发明一部分实施例,而不是全部的实施例。基于本发明中的实施例,本领域普通技术人员在没有做出创造性劳动前提下所获得的所有其它实施例,都属于本发明保护的范围。
19.在一实施例中,请参阅图1所示,现提供一种化工生产用设备智能化控制系统,该化工生产用设备用于分离化工生产中的粗品产物和催化剂,包括设备内部设置的处理器,所述处理器连接有数据采集模块、警报终端和服务器,所述服务器连接有设备分析模块、等级界定模块、运行分析模块、用户终端、型号匹配模块以及数据分析模块;所述用户终端用于化工生产的工作人员输入个人信息后注册登录系统,并将个人信息发送至服务器内存储;需要具体说明的是,个人信息包括工作人员的姓名、实名认证的手机号码等;在本实施例中,在工作人员注册登录后,所述用户终端用于工作人员输入化工生产设备u的型号和设备信息,并将化工生产设备的型号和设备信息发送至服务器,u=1,2,
……
,z,z为正整数,所述服务器将化工生产设备的型号发送至型号匹配模块,所述型号匹配模块依据型号用于匹配得到化工生产设备的标准运行数据,并将标准运行数据发送至服务器,所述服务器将标准运行数据发送至运行分析模块;需要具体说明的是,设备信息为化工生产设备的设备名称、设备出厂时间、故障次数以及每次故障的故障时间等;标准运行数据为化工生产设备的标准温度值、标准真空度、标准湿度值、标准分贝值、标准振幅值等;其中,所述数据采集模块用于采集化工生产设备在运行期间的实时运行数据,并将实时运行数据发送至处理器,所述处理器将实时运行数据发送至服务器,所述服务器将实时运行数据发送至运行分析模块;需要具体说明的是,实时运行数据为化工生产设备的实时温度值、实时真空度、实时湿度值、实时分贝值、实时振幅值等;所述运行分析模块用于对化工生产设备的运行状况进行分析,分析过程具体如下:步骤p1:在化工生产设备的运行期间内设定若干个时间点,采集化工生产设备在若干个时间点时的实时温度值、实时真空度、实时湿度值、实时分贝值和实时振幅值;步骤p2:计算化工生产设备在若干个时间点时的实时运行数据与标准运行数据的数据差值(即计算若干个时间点时实时温度值与标准温度值的差值、实时真空度与标准真空度的差值、实时湿度值与标准湿度值的差值、实时分贝值与标准分贝值的差值、实时振幅值与标准振幅值的差值),从而得到化工生产设备在若干个时间点时的温度点差值、真空点差值、湿度点差值、分贝点差值和振幅点差值;步骤p3:统计化工生产设备在运行期间内时间点的数量并记为时间点数;步骤p4:若干个时间点时的温度点差值相加求和除以时间点数得到化工生产设备
在运行期间的温度偏差值wdpu;同理,得到化工生产设备在运行期间的真空偏差值zkpu、湿度偏差值sdpu、分贝偏差值fbpu和振幅偏差值zdpu;步骤p5:通过公式ypu=wdpu
×
b1 zkpu
×
b2 sdpu
×
b3 fbpu
×
b4 zdpu
×
b5计算得到化工生产设备的运行偏差值ypu;式中,b1、b2、b3、b4和b5均为固定数值的权重系数,且b1、b2、b3、b4和b5的取值均大于零;步骤p6:若ypu<y1,则化工生产设备的运行偏差等级为第三偏差等级;若y1≤ypu<y2,则化工生产设备的运行偏差等级为第二偏差等级;若y2≤ypu,则化工生产设备的运行偏差等级为第一偏差等级;其中,x1和x2均为固定数值的运行偏差阈值,且y1<y2;可理解的是,第一偏差等级的级别高于第二偏差等级的级别,第二偏差等级的级别高于第三偏差等级的级别;所述运行分析模块将化工生产设备的运行偏差等级反馈至服务器,所述服务器将化工生产设备的运行偏差等级发送至等级界定模块;所述服务器将设备信息发送至设备分析模块,所述设备分析模块用于对化工生产设备进行设备分析,设备分析过程具体如下:步骤s1:获取化工生产设备的设备出厂时间,利用服务器的当前时间减去设备出厂时间得到化工生产设备的使用时长tsu;步骤s2:获取化工生产设备的故障次数,并将故障次数标记为gcu;步骤s3:获取化工生产设备每次故障的故障时间,计算化工生产设备的相邻故障间隔时长,相邻故障间隔时长相加求和除以故障次数得到化工生产设备的故障间隔时长tjgu;步骤s4:通过公式ssu=tsu
×
a1 gcu
×
a2 tjgu
×
a3计算得到化工生产设备的设备使用值ssu;式中,a1、a2和a3均为固定数值的权重系数,且a1、a2和a3的取值;步骤s5:若ssu<x1,则化工生产设备的设备使用等级为第三使用等级;若x1≤ssu<x2,则化工生产设备的设备使用等级为第二使用等级;若x2≤ssu,则化工生产设备的设备使用等级为第一使用等级;其中,x1和x2均为固定数值的设备使用阈值,且x1<x2;可理解的是,第一使用等级的级别高于第二使用等级的级别,第二使用等级的级别高于第三使用等级的级别;所述设备分析模块将化工生产设备的设备使用等级反馈至服务器,所述服务器将化工生产设备的设备使用等级发送至等级界定模块;所述等级界定模块结合设备使用等级和运行偏差等级用于对化工生产设备的数据差异包进行界定,界定过程具体如下:依据设备使用等级设定对应化工生产设备的第一界定值,依据运行偏差等级设定化工生产设备对应的第二界定值,具体为:若为第一使用等级则第一界定值为α1,若为第二使用等级则第一界定值为α2,若为第三使用等级则第一界定值为α3,若为第一偏差等级则第二界定值为β1,若为第二偏差等级则第二界定值为β2,若为第三偏差等级则第二界定值为β3;其中,α1>α2>α3,β1>β2
>β3,α1、α2、α3、β1、β2和β3均为大于零的固定数值;为第一界定值和第二界定值分配相应的权重系数,计算得到化工生产设备的等级界定值,依据等级界定值得到对应的界定等级;通过界定等级得到化工生产设备对应的数据差异包;需要具体说明的是,界定等级包括第一界定等级、第二界定等级和第三界定等级,第一界定等级、第二界定等级和第三界定等级的级别依次递减,数据差异包为化工生产设备中催化剂反应前后的预估重量差值范围、以及粗品产物的预估重量值范围,可理解的是,不同界定等级使得催化剂反应前后的预估重量差值范围、以及粗品产物的预估重量值范围也不同;举例说明:若等级界定值为10,不同界定等级对应等级界定值的取值范围分别为[0,15)、[15,30)、[30,45)
……
、[0,n)、[n,m],即可通过等级界定值得到化工生产设备对应的界定等级,最后通过界定等级得到相应的数据差异包;所述等级界定模块将化工生产设备的数据差异包反馈至服务器,所述服务器将化工生产设备的数据差异包发送至数据分析模块;同时,所述数据采集模块用于采集化工生产设备中催化剂的初始重量值、以及反应后粗品产物和催化剂实时重量值,并将催化剂的初始重量值、以及反应后粗品产物和催化剂实时重量值发送至处理器,所述处理器将催化剂的初始重量值、以及反应后粗品产物和催化剂实时重量值发送至服务器,所述服务器将催化剂的初始重量值、以及反应后粗品产物和催化剂实时重量值发送至数据分析模块;所述数据分析模块用于对化工生产设备分离工作的分离数据进行分析,分析过程具体如下:步骤q1:获取化工生产设备中粗品产物反应前催化剂的初始重量值qczu;获取化工生产设备中反应后催化剂的实时重量值hczu和粗品产物的实时重量值cwzu;步骤q2:若催化剂的实时重量值大于初始重量值,则生成工作异常信号;若催化剂的实时重量值小于等于初始重量值,则通过公式szcu=hczu-qczu计算得到化工生产设备中催化剂反应前后的实时重量差值szcu;步骤q4:获取催化剂反应前后的预估重量差值范围、以及粗品产物的预估重量值范围;步骤q5:若催化剂反应前后的实时重量差值处于催化剂反应前后的预估重量差值范围,且粗品产物的实时重量值处于粗品产物的预估重量值范围,则生成工作正常信号;若催化剂反应前后的实时重量差值未处于催化剂反应前后的预估重量差值范围或粗品产物的实时重量值未处于粗品产物的预估重量值范围,则生成工作异常信号;所述数据分析模块将工作正常信号或工作异常信号将反馈至服务器;若服务器接收到工作正常信号,则不进行任何操作;若服务器接收到工作异常信号,则将工作异常信号发送中处理器,处理器依据工作异常信号生成警报指令加载至警报终端,警报终端接收到警报指令后进行警报工作;在具体实施时,警报终端具体为安装在化工生产设备上的警报器、声光警报器等。
[0020]
在另一实施例中,请参阅图2所示,提出一种化工生产用设备智能化控制方法,控制方法具体如下:
步骤s101,工作人员通过用户终端输入化工生产设备u的型号和设备信息,并将化工生产设备的型号和设备信息发送至服务器,服务器将化工生产设备的型号发送至型号匹配模块,型号匹配模块依据型号匹配得到化工生产设备的标准运行数据,并将标准运行数据发送至服务器,服务器将标准运行数据发送至运行分析模块,同时,通过数据采集模块采集化工生产设备在运行期间的实时运行数据,并将实时运行数据发送至处理器,处理器将实时运行数据发送至服务器,服务器将实时运行数据发送至运行分析模块;步骤s102,利用运行分析模块对化工生产设备的运行状况进行分析,在化工生产设备的运行期间内设定若干个时间点,并采集化工生产设备在若干个时间点时的实时温度值、实时真空度、实时湿度值、实时分贝值和实时振幅值,计算化工生产设备在若干个时间点时的实时运行数据与标准运行数据的数据差值,得到化工生产设备在若干个时间点时的温度点差值、真空点差值、湿度点差值、分贝点差值和振幅点差值,统计化工生产设备在运行期间内时间点的数量并记为时间点数,若干个时间点时的温度点差值相加求和除以时间点数得到化工生产设备在运行期间的温度偏差值wdpu,同理,得到化工生产设备在运行期间的真空偏差值zkpu、湿度偏差值sdpu、分贝偏差值fbpu和振幅偏差值zdpu,通过公式ypu=wdpu
×
b1 zkpu
×
b2 sdpu
×
b3 fbpu
×
b4 zdpu
×
b5计算得到化工生产设备的运行偏差值ypu,若ypu<y1,则化工生产设备的运行偏差等级为第三偏差等级,若y1≤ypu<y2,则化工生产设备的运行偏差等级为第二偏差等级,若y2≤ypu,则化工生产设备的运行偏差等级为第一偏差等级,运行分析模块将化工生产设备的运行偏差等级反馈至服务器,所述服务器将化工生产设备的运行偏差等级发送至等级界定模块;步骤s103,服务器将设备信息发送至设备分析模块,通过设备分析模块对化工生产设备进行设备分析,获取化工生产设备的设备出厂时间,利用服务器的当前时间减去设备出厂时间得到化工生产设备的使用时长tsu,而后获取化工生产设备的故障次数gcu,最后获取化工生产设备每次故障的故障时间,计算化工生产设备的相邻故障间隔时长,相邻故障间隔时长相加求和除以故障次数得到化工生产设备的故障间隔时长tjgu,通过公式ssu=tsu
×
a1 gcu
×
a2 tjgu
×
a3计算得到化工生产设备的设备使用值ssu,若ssu<x1,则化工生产设备的设备使用等级为第三使用等级,若x1≤ssu<x2,则化工生产设备的设备使用等级为第二使用等级,若x2≤ssu,则化工生产设备的设备使用等级为第一使用等级,设备分析模块将化工生产设备的设备使用等级反馈至服务器,服务器将化工生产设备的设备使用等级发送至等级界定模块;步骤s104,等级界定模块结合设备使用等级和运行偏差等级对化工生产设备的数据差异包进行界定,依据设备使用等级设定对应化工生产设备的第一界定值,依据运行偏差等级设定化工生产设备对应的第二界定值,为第一界定值和第二界定值分配相应的权重系数,计算得到化工生产设备的等级界定值,依据等级界定值得到对应的界定等级,通过界定等级得到化工生产设备对应的数据差异包,等级界定模块将化工生产设备的数据差异包反馈至服务器,服务器将化工生产设备的数据差异包发送至数据分析模块;步骤s105,最后数据采集模块用于采集化工生产设备中催化剂的初始重量值、以及反应后粗品产物和催化剂实时重量值,并将催化剂的初始重量值、以及反应后粗品产物和催化剂实时重量值发送至处理器,处理器将催化剂的初始重量值、以及反应后粗品产物和催化剂实时重量值发送至服务器,服务器将催化剂的初始重量值、以及反应后粗品产物
和催化剂实时重量值发送至数据分析模块;步骤s106,利用数据分析模块对化工生产设备分离工作的分离数据进行分析,获取化工生产设备中粗品产物反应前催化剂的初始重量值qczu,获取化工生产设备中反应后催化剂的实时重量值hczu和粗品产物的实时重量值cwzu,若催化剂的实时重量值大于初始重量值,则生成工作异常信号,若催化剂的实时重量值小于等于初始重量值,则通过公式szcu=hczu-qczu计算得到化工生产设备中催化剂反应前后的实时重量差值szcu,获取催化剂反应前后的预估重量差值范围、以及粗品产物的预估重量值范围,若催化剂反应前后的实时重量差值处于催化剂反应前后的预估重量差值范围,且粗品产物的实时重量值处于粗品产物的预估重量值范围,则生成工作正常信号,若催化剂反应前后的实时重量差值未处于催化剂反应前后的预估重量差值范围或粗品产物的实时重量值未处于粗品产物的预估重量值范围,则生成工作异常信号,数据分析模块将工作正常信号或工作异常信号将反馈至服务器,若服务器接收到工作正常信号,则不进行任何操作,若服务器接收到工作异常信号,则将工作异常信号发送中处理器,处理器依据工作异常信号生成警报指令加载至警报终端,警报终端接收到警报指令后进行警报工作。
[0021]
上述公式均是去量纲取其数值计算,公式是由采集大量数据进行软件模拟得到最近真实情况的一个公式,公式中的预设参数由本领域的技术人员根据实际情况进行设置,权重系数和比例系数的大小是为了将各个参数进行量化得到的一个具体的数值,便于后续比较,关于权重系数和比例系数的大小,只要不影响参数与量化后数值的比例关系即可。
[0022]
以上公开的本发明优选实施例只是用于帮助阐述本发明。优选实施例并没有详尽叙述所有的细节,也不限制该发明仅为的具体实施方式。显然,根据本说明书的内容,可作很多的修改和变化。本说明书选取并具体描述这些实施例,是为了更好地解释本发明的原理和实际应用,从而使所属技术领域技术人员能很好地理解和利用本发明。本发明仅受权利要求书及其全部范围和等效物的限制。
再多了解一些
本文用于创业者技术爱好者查询,仅供学习研究,如用于商业用途,请联系技术所有人。