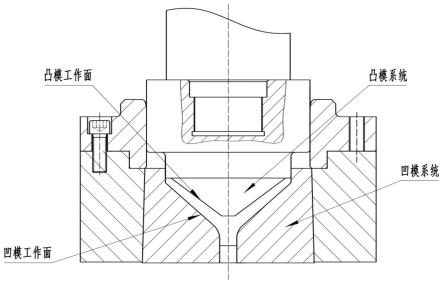
1.本发明涉及金属材料技术领域,特别是对于聚能侵彻弹药型罩用材料的内部质量检验,尤其涉及一种强塑变形铜材料内部微缺陷暴露的实验方法。
背景技术:
2.国外对药型罩材料、组织(晶粒度、形貌、分布、晶粒取向等)、几何尺寸精度和毁伤效能之间的关系作了大量而深入的研究。结果表明,在药型罩结构参数与装药装配相同条件下,晶粒尺寸与均匀性、织构(晶粒取向)和其它内在组织参数对侵彻能力影响明显,而材料内部气孔、疏松等缺陷是影响侵彻深度指标跳差的核心关键。
3.目前,用于制造聚能侵彻弹药型罩的金属材料主要有:钽、铜、镍、铁等纯金属材料,以及钽钨、钽铜等合金材料,其中铜具有密度高(8.93g/cm3)、塑性好(室温断后伸长率达到50%)、声速大(4.7km/s)、熔点高(1083℃),同时材料成形性能好(塑性成形极限达到95%)、储藏丰富、价格相对便宜,能够满足常规武器战斗部的低成本制造与高性能发展需求。但国内现有制备铜材的熔铸、挤压、轧制、无损探伤检测等技术与装备相对落后,导致铜材的品质不高、质量一致性不好。如某公司生产tu1铜材,采用普通熔炼炉 木炭覆盖剂,铸锭中氧(o)、磷(p)等元素含量经常超标,再通过挤压、拉拔、轧制等大塑性变形后,铸锭中的气孔、疏松等部分缺陷发生焊合、变形,在后续常规抽检中很难发现,导致用户产品报废率达到50%;又如某公司生产tu00铜材,采用真空熔炼炉生产的规格200mm以内的铜锭中氧含量超标一倍以上(经常降低二至三个等级使用),规格为(245-360)mm铸锭中疏松、气孔多,而且缺陷在用户入厂验收过程难以发现,在产品生产和综合性能使用过程中废品率非常高,并且给聚能侵彻弹药型罩服役性能的不稳定性埋下了严重隐患。
4.为了进一步挖掘或发挥铜材的潜力,从药型罩连续射流长度与侵彻威力之间的关联性,以及金属材料的强塑变理论和塑性力学出发,铜材内部缺陷越少,在高爆压、高爆速、瞬态下金属侵彻体拉伸长度就越长,能显著提升战斗部的侵彻毁伤效能(铜材射流长度理论值达到20倍药型罩口径以上,国内现阶段水平是13~15倍口径,且跳差20%以上)。国内现有铜材出厂或入厂验收方式:一是化学成分、密度、高倍或低倍组织、力学性能、氢脆检测,从同一批材料中随机抽取一个或几个试样,不足之处是试样尺寸小,覆盖范围太小,且未考虑塑性变形下金属内部质量;二是超声波探伤检测,对缺陷的识别灵敏度0.5mm以上(gb/t 3310-2010),对微小的气孔、疏松等缺陷很难发现,并存在漏探等问题;三是冲压制耳检测,主要获得铜材轧制横向、纵向织构强度因子。对于聚能侵彻弹药型罩用铜材,要求任何部位都不能有气孔、疏松、夹渣等缺陷,必须通过有效的检测方法最大程度发现缺陷,若在原材料入厂验收、产品加工制造过程发现,可以剔除不合格品,确保药型罩产品制造零缺陷原则。
技术实现要素:
5.本发明解决的技术问题在于提供一种强塑变形铜材料内部微缺陷暴露的实验方
法。
6.本发明是通过下列技术方案实现:
7.一种强塑变形铜材料内部微缺陷暴露的实验方法,经过下列工艺步骤实现:
8.(1)模具制造:采用模具为两层组合式金属模具,由凹模、凸模组成;
9.模具材料为钢,硬度hrc58~63,冲击吸收功80~100j,工作面粗糙度达到ra0.4μm;
10.(2)坯料准备:采用锯切 车削加工方法,将铜材制备成设计要求的坯料,坯料高度与直径比为1~2,坯料外径和端面的粗糙度达到ra0.8μm;
11.(3)缺陷暴露实验:将金属模具安装于10000kn液压机上,将铜坯料放入金属模具中,液压机上滑块带动凸模工作,对坯料进行挤压扩径变形,使坯料端面、径向受到张应力作用,扩径率为30~75%;
12.(4)微缺陷分析与确认:对步骤(3)中坯件端面与外径表面进行微缺陷分析与确认;首先采用目测观察坯件端面是否有可见的缺陷;其次采用10倍放大镜观察;最后采用放大50~1000倍金相显微镜或电镜观察试样端面。
13.优选的,所述步骤(1)中模具设计为铜坯料在模具中受到挤压力同时铜坯料一端与模具锥面之间有足够的间隙(图2所示);具体的坯料一端与模具锥面之间有足够的间隙,是指当扩径率达到最大值75%时,挤压坯件外径至少还有15mm高度未贴合模具锥面(图2所示),保证坯料外径上有足够面积只受到张应力,有利于坯料外径表面缺陷的充分暴露。
14.所述步骤(1)中模具制造工艺为依次进行双重淬火、阶梯控温回火、深冷处理工艺;双重淬火为(1080℃~1150℃)
×
(2h~5h)(油冷,温度60℃) (980℃~1030℃)
×
(2h~4h)(油冷,温度60℃);阶梯控温回火为(550℃~600℃)
×
(2h~4h)(空冷,室温) (500℃~550℃)
×
(4h~6h)(空冷,室温) (450℃~500℃)
×
(6h~8h)(空冷,室温);深冷处理为(-135℃~-196℃)
×
(8h~12h),深冷介质为液氮。
15.所述步骤(2)中坯料,一般一次实验样本量为(15~20)件。
16.所述步骤(2)中铜棒材,可以是tu00、tu1、t2等纯铜材料,也可以是h90、h68、h62等铜合金材料。
17.所述步骤(2)中坯料高度与直径比为1~2,在坯料直径不大于35mm时,坯料高度与直径比为1;在坯料直径为35mm到70mm时,坯料高度与直径比不大于1.5;在坯料直径大于70mm时,坯料高度与直径比不大于2。
18.所述步骤(3)中扩径率在(30~75)%之间,在坯料直径不大于35mm时,扩径率在(30~40)%之间;在坯料直径为35mm到70mm时,扩径率在(40~55)%之间;在坯料直径大于70mm时,扩径率在(55~75)%之间。
19.具体的,一种强塑变形铜材料内部微缺陷暴露的实验方法,经过下列工艺步骤实现:
20.(1)模具设计制造:
21.铜材的强度低、变形抗力小,缺陷暴露实验模具系统设计为两层组合式金属模具,其中凹模、凸模工作部分结构如图1所示,铜坯料在金属模具中受到挤压力,同时坯料一端与模具锥面之间有足够的间隙,坯料端面、径向在无约束作用下受到张应力,坯料中微缺陷就会拉伸、扩展、开裂等暴露出来;
22.模具材料为优质冷作模具钢(7cr7mo2v2si,代号为ld),通过双重淬火 阶梯控温回火 深冷处理工艺,硬度hrc58~63,冲击吸收功80~100j,通过车削 抛光模具工作面的粗糙度达到ra0.4μm。
23.(2)坯料准备:采用锯切 车削加工方法,将铜材制备成设计要求的坯料,坯料高度与直径比为1~2,为降低表面质量对缺陷暴露实验结果的影响,坯料外径和端面的粗糙度达到ra0.8μm,如图2所示。
24.(3)缺陷暴露实验:首先将金属模具(图1)安装于10000kn液压机上,其次将铜坯料放入金属模具中,液压机上滑块带动凸模工作,对坯料进行挤压扩径变形,使坯料端面、径向受到张应力作用,扩径率在(30~75)%之间(扩径率xd=(d
u-d)/d
×
100%,d
u-挤压后坯料的外径,d-挤压前坯料的外径)。
25.(4)微缺陷分析与确认:对步骤(3)中坯件端面与外径表面进行微缺陷分析与确认,首先采用目测观察坯件端面是否有可见的缺陷(如裂纹、开口等),其次采用放大镜(放大10倍)观察坯件端面是否有缺陷,最后在目测、放大镜都没有发现有缺陷的位置取样,采用金相显微镜或电镜(放大50~1000倍)观察试样端面是否有缺陷,确定缺陷为严重缺陷或一般缺陷,评价铜材的质量。
26.有益效果
27.1、本发明包括模具设计制造、坯料制备、缺陷暴露实验、微缺陷分析与确认,首先使铜坯料在金属模具中受到挤压力,同时坯料一端与模具锥面之间有一定的间隙,在挤压力作用下坯料径向受到张应力,铜坯料端面、径向在无约束作用下发生塑性变形,其次通过目测或现代材料分析方法能快速有效发现铜材料的微缺陷。
28.2、本发明方法具有以下明显优势:本发明通过局部无约束塑性变形方式检测材料内部质量,首次提出采用挤压成形暴露铜材内部微缺陷,设计制造一定形状结构的金属模具,使铜坯料的外径、端面等局部只受到张应力作用,使得坯料中微缺陷暴露出来,并通过多种方法配合快速有效检测一定扩径率下的端面上是否有缺陷。本发明克服了化学成分、高倍或低倍组织、力学性能、氢脆检测、超声波探伤检测等难以发现内部微小缺陷难题,同时具有实验样本数量可调、工艺稳定性好、效率高等优点。
29.(1)易于发现内部缺陷。克服了传统检测方法难以发现疏松、气孔等微小缺陷,并且在张应力作用下可以扩展、放大缺陷,缺陷放大1~3倍,尤其是一些闭合缺陷易于发现。
30.(2)适用范围广。可以检测不同牌号、规格的材料,有效发现裂纹、疏松、气孔、夹渣等不同缺陷。
31.(3)工艺稳定性好、可信度高。可以有效控制铜坯料的扩径率,保证工艺稳定性,结合现代材料分析方法,确定缺陷的可信度达到100%。
附图说明
32.图1金属模具系统
33.图2铜坯料端面与模具间隙示意图
34.图3坯料几何尺寸
35.图4扩径实验后坯件结构图
36.图5坯料与扩径后坯件
37.图6表面缺陷宏观照片
38.图7表面开裂微观照片
39.图8扩径后坯件端面、外径直边段宏观照片
40.图9气孔、疏松微观照片
具体实施方式
41.下面通过具体实施例对本发明进行描述,有必要在此指出的是,所述实施例只用于对本方法进行进一步说明,不能理解为对本发明保护范围的限制,该领域的技术人员可以根据本发明的技术方案做出一些非本质的改进和调整。
42.实施例1
43.一种强塑变形铜材料内部微缺陷暴露的实验方法,它具体包括以下步骤:
44.(1)模具设计制造:铜材的强度低、变形抗力小,缺陷暴露实验模具系统设计为两层组合式金属模具,其中凹模、凸模工作部分结构如图1所示,铜坯料在金属模具中受到挤压力,同时坯料一端与模具锥面之间有足够的间隙,坯料端面、径向在无约束作用下受到张应力,坯料中微缺陷就会拉伸、扩展、开裂等暴露出来;模具材料为优质冷作模具钢(7cr7mo2v2si,代号为ld),通过“双重淬火 阶梯控温回火 深冷处理工艺”实现材料强度与韧性匹配,即双重淬火为1120℃
×
3h(油冷,温度60℃) 1000℃
×
2h(油冷,温度60℃),阶梯控温回火为580℃
×
3h(空冷,室温) 530℃
×
5h(空冷,室温) 480℃
×
8h(空冷,室温),深冷处理为(-135℃~-196℃)
×
10h,深冷介质为液氮。经检测,凸模、凹模表明硬度hrc61.2(5个不同部位平均值),冲击吸收功92j(3个试样平均值),通过车削 抛光模具工作部分表面粗糙度ra0.12μm~ra0.33μm。
45.(2)坯料准备:选用某公司tu00、直径为65mm的挤压 拉拔铜材(杂质元素如表1所示,杂质元素、力学性能、晶粒度、氢脆等检测结果都合格),采用锯切 车削加工方法将铜材制备成坯料高度与直径比为1.2(外径为64.2mm、高度为77.04mm),共计20件,经标准试块比对,坯料外径和端面的粗糙度在ra0.4μm至ra0.8μm之间,如图2所示。
46.表1铜材的杂质元素含量(
×
10-6
)
[0047][0048][0049]
(3)缺陷暴露实验:首先将金属模具(图1)安装于10000kn液压机上,调试好模具闭合高度;其次将铜坯料放入金属模具中,液压机上滑块带动凸模工作,对坯料进行挤压扩径变形,使坯料端面、径向受到张应力作用;最后通过控制液压机上滑块的下行高度,实现坯料的扩径挤压变形(图3)。通过测量挤压后坯料外径为95.2mm~96.1mm、直边段高度为24.6mm~25.2mm(图4),代入扩径率xd=(d
u-d)/d
×
100%,经计算xd=48.44%~49.68%。
[0050]
(4)微缺陷分析与确认:对步骤(3)中坯件端面进行微缺陷分析与确认,采用目测观察坯件端面、外径直边段位置,发现2件有开裂、开口缺陷(图5);采用10倍放大镜观察坯件端面、外径直边段,发现1件有开裂缺陷(图6);在目测和低倍放大镜下17个坯件端面未发现缺陷,每个坯件上取1个试样(坯件表面如图7所示,试样长
×
宽
×
厚,15mm
×
15mm
×
6mm),
经放大100~1000倍观察,发现有2个试样有气孔、疏松等缺陷(图8)。
[0051]
由上述的20个坯料挤压扩径试验结果得出,目测和低倍放大镜观察3件出现开裂,占比15%;从17件未开裂坯件端面取样17个,发现有2个试样有气孔,占比为10%;综合分析20个坯料中发现5个有缺陷,其中3个为严重缺陷,2个为一般缺陷,判定该批材料不合格。进一步将该批材料随机抽取一根材料,按照某标准药型罩制造工艺规范进行加工与验收,制备出20件药型罩,随机抽取7件药型罩进行装药与装配,静态侵彻试验中3发侵彻深度指标异常(分别为260mm、310mm、385mm),与标准侵彻深度值(550mm)之间的跳差30%~52.7%。
[0052]
实施例2
[0053]
一种强塑变形铜材料内部微缺陷暴露的实验方法,它具体包括以下步骤:
[0054]
(1)模具设计制造:铜材的强度低、变形抗力小,缺陷暴露实验模具系统设计为两层组合式金属模具,其中凹模、凸模工作部分结构如图1所示,铜坯料在金属模具中受到挤压力,同时坯料一端与模具锥面之间有足够的间隙,坯料端面、径向在无约束作用下受到张应力,坯料中微缺陷就会拉伸、扩展、开裂等暴露出来;模具材料为优质冷作模具钢(7cr7mo2v2si,代号为ld),通过双重淬火 阶梯控温回火 深冷处理工艺,即双重淬火为1150℃
×
4h(油冷,温度60℃) 980℃
×
4h(油冷,温度60℃),阶梯控温回火为600℃
×
3h(空冷,室温) 550℃
×
4h(空冷,室温) 500℃
×
6h(空冷,室温),深冷处理为(-135℃~-196℃)
×
12h,深冷介质为液氮。经检测,凸模、凹模表明硬度hrc62.4(5个不同部位平均值),冲击吸收功88j(3个试样平均值),通过车削 抛光模具工作部分表面粗糙度ra0.15μm~ra0.28μm。
[0055]
(2)坯料准备:选用某公司tu1、直径为90mm的挤压铜材(杂质元素如表2所示,杂质元素、力学性能、晶粒度、氢脆等检测结果都合格),采用锯切 车削加工方法将铜材制备成坯料高度与直径比为1.8(外径为89.2mm、高度为160.56mm),共计20件,经标准试块比对,坯料外径和端面的粗糙度在ra0.4μm至ra0.8μm之间,如图2所示。
[0056]
表2铜材的杂质元素含量(
×
10-6
)
[0057]
牌号pbisbasfenisnsopbzn总和tu110101081065181097103
[0058]
(3)缺陷暴露实验:缺陷暴露实验:首先将金属模具(图1)安装于10000kn液压机上,调试好模具闭合高度;其次将铜坯料放入金属模具中,液压机上滑块带动凸模工作,对坯料进行挤压扩径变形,使坯料端面、径向受到张应力作用;最后通过控制液压机上滑块的下行高度,实现坯料得扩径挤压变形(图3)。通过测量挤压后坯料外径为151.1mm~153.4mm、直边段高度为42.3mm~44.6mm(图4),代入扩径率xd=(du-d)/d
×
100%,经计算xd=69.39%~71.97%。
[0059]
(4)微缺陷分析与确认:对步骤(3)中坯件端面进行微缺陷分析与确认,采用目测观察坯件端面、外径直边段位置,发现2件有开裂缺陷(图5);采用10倍放大镜观察坯件端面、外径直边段,发现3件有开裂缺陷(图6);在目测和低倍放大镜下15个坯件端面未发现缺陷,每个坯件上取1个试样(坯件表面如图7所示,试样长
×
宽
×
厚,15mm
×
15mm
×
6mm),经放大100~1000倍观察,发现有3个试样有气孔、疏松等缺陷(图8)。
[0060]
由上述的试样结果得出,20个坯料通过挤压扩径试验,直接观察5件出现开裂,占比25%;从15件未开裂坯件端面取样15个,发现有3个试样有气孔,占比为15%;综合分析20
个坯料中发现8个有缺陷,其中5个为严重缺陷,3个为一般缺陷,判定该批材料不合格。进一步将该批材料随机抽取一根材料,按照某标准药型罩制造工艺规范进行加工与验收,制备出20件药型罩,随机抽取7件药型罩进行装药与装配,静态侵彻试验中4发侵彻深度指标异常(分别为430mm、510mm、470mm、500mm),与标准侵彻深度值(800mm)之间的跳差36%~46.3%。
[0061]
实施例3
[0062]
一种强塑变形铜材料内部微缺陷暴露的实验方法,它具体包括以下步骤:
[0063]
(1)模具设计制造:铜材的强度低、变形抗力小,缺陷暴露实验模具系统设计为两层组合式金属模具,其中凹模、凸模工作部分结构如图1所示,铜坯料在金属模具中受到挤压力,同时坯料一端与模具锥面之间有足够的间隙,坯料端面、径向在无约束作用下受到张应力,坯料中微缺陷就会拉伸、扩展、开裂等暴露出来;模具材料为优质冷作模具钢(7cr7mo2v2si,代号为ld),通过双重淬火 阶梯控温回火 深冷处理工艺,即双重淬火为1080℃
×
5h(油冷,温度60℃) 1030℃
×
3h(油冷,温度60℃),阶梯控温回火为560℃
×
4h(空冷,室温) 530℃
×
6h(空冷,室温) 480℃
×
7h(空冷,室温),深冷处理为(-135℃~-196℃)
×
10h,深冷介质为液氮。经检测,凸模、凹模表明硬度hrc59.1(5个不同部位平均值),冲击吸收功96j(3个试样平均值),通过车削 抛光模具工作部分表面粗糙度ra0.12μm~ra0.23μm。
[0064]
(2)坯料准备:选用某公司h90、直径为35mm的拉拔铜材(化学成分如表3所示,化学成分、力学性能、晶粒度等检测结果都合格),采用锯切 车削加工方法将铜材制备成坯料高度与直径比为1(外径为34.4mm、高度为34.4mm),共计15件,经标准试块比对,坯料外径和端面的粗糙度在ra0.4μm至ra0.8μm之间,如图2所示。
[0065]
表3铜材的化学成分(%)
[0066]
牌号cufepbzn杂质h9089.420.050.0510.180.3
[0067]
(3)缺陷暴露实验:缺陷暴露实验:首先将金属模具(图1)安装于10000kn液压机上,调试好模具闭合高度;其次将铜坯料放入金属模具中,液压机上滑块带动凸模工作,对坯料进行挤压扩径变形,使坯料端面、径向受到张应力作用;最后通过控制液压机上滑块的下行高度,实现坯料得扩径挤压变形(图3)。通过测量挤压后坯料外径为45.8mm~47.1mm、直边段高度为15.3mm~17.2mm(图4),代入扩径率xd=(du-d)/d
×
100%,经计算xd=33.14%~36.92%。
[0068]
(4)微缺陷分析与确认:对步骤(3)中坯件端面进行微缺陷分析与确认,采用目测观察坯件端面、外径直边段位置,未发现有开裂缺陷;采用10倍放大镜观察坯件端面、外径直边段,未发现有开裂缺陷;在15个坯件端面取样15个试样(试样长
×
宽
×
厚,15mm
×
15mm
×
6mm),经放大100~1000倍观察,未发现有气孔、疏松等缺陷。
[0069]
由上述的试样结果得出,15个坯料通过挤压扩径试验,未发现有开裂、气孔等缺陷,判定该批材料合格。进一步将该批材料随机抽取一根材料,按照某标准药型罩制造工艺规范进行加工与验收,制备出20件药型罩,随机抽取7件药型罩进行装药与装配,静态侵彻试验中7发侵彻深度满足设计指标要求(设计值为800mm),分别为810mm、855mm、830mm、890mm、903mm、910mm、880mm,最大深度值与最小深度值之间的跳差约12.3%。
[0070]
综合上述3个实施例,通过缺陷暴露实验,使铜坯料在金属模具中受到径向张应力,铜坯料端面、径向在无约束作用下发生塑性变形,若是坯料内部有气孔、疏松、缩孔等微缺陷,在张应力作用下快速扩展形成裂纹、十字叉等缺陷。只要在坯件端面发现有开裂、十字叉等缺陷,用同一批铜料制备成药型罩样品的综合使用性能试验,侵彻性能跳差达到50%,可以直接表明性能不稳定是由材料内部缺陷引起的。
再多了解一些
本文用于创业者技术爱好者查询,仅供学习研究,如用于商业用途,请联系技术所有人。