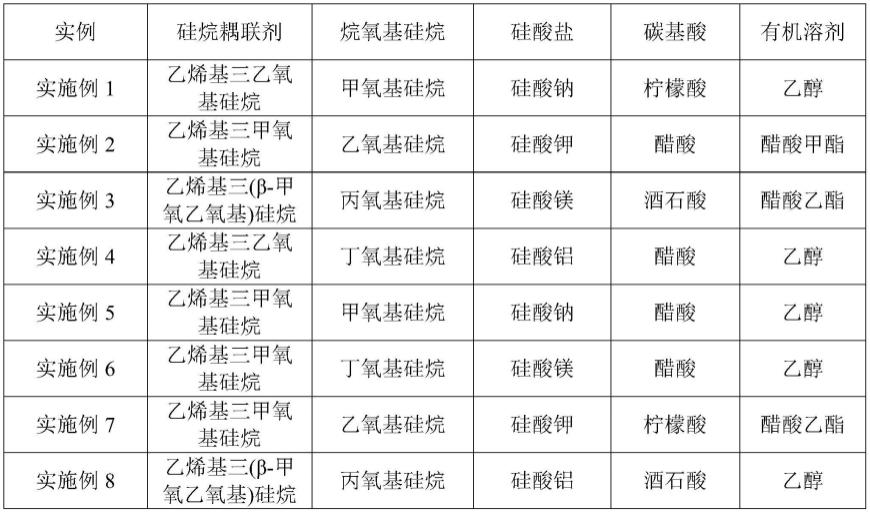
1.本发明属于绝缘涂料技术领域,具体涉及一种新能源汽车用无取向硅钢片无铬环保绝缘涂料。
背景技术:
2.环保与能源问题对汽车工业的可持续发展提出了严峻的挑战。在不可再生资源日益紧张的情况下,发展新能源汽车可以减少国家石油资源消耗,削减车辆运行阶段大气污染物的排放,对调整能源结构、改善城市空气质量,保障人群健康均有重要意义。新能源汽车是低碳经济的必然选择,代表汽车产业的发展趋势。
3.无取向硅钢是汽车驱动电机的核心材料之一。新能源汽车驱动电机最大转速由每分钟几千转提高到几万转甚至高达20万转,工作频率由50hz提高到数百数千赫兹,这就要求材料在高频下必须具有低铁损;驱动电机启动、加速时要有高的扭矩,即材料必须具有高的磁感应强度;还要满足驱动电机反复启动和刹车要求,即材料应具有高强度。因此,新能源汽车用无取向硅钢的硬核指标为“高磁感、高频低铁损、高强度”。研究表明,普通无取向硅钢铁损值在400hz下较工频下增加20倍以上,因此普通无取向硅钢难以用于新能源汽车。因此需要生产新能源汽车用的高强度无取向硅钢片,同时硅钢片用绝缘涂层也要满足高强度需求。
4.由于无取向硅钢在制作电机铁芯的加工过程中,需要经历分条、冲压、铆接、退火、发蓝等一系列过程,故该绝缘层除了具有优良的绝缘性能外,还应该具有优良的附着性,保证在加工过程中涂层不脱落;优良的耐腐蚀性,使硅钢表面不易锈蚀;优良的冲压性,以保护冲压模具,延长模具使用寿命;优良的焊接性,允许叠片铁芯以合理的速度进行焊接而不产生过多的气孔。
5.由于制造新能源汽车用电机转子和定子的无取向硅钢片尺寸各异,并且需要满足高频率高强度的使用需求,因此对无取向硅钢片的表面涂层厚度要求也不同,涂层厚度从0.1-4μm之间变化较大。但不论涂层厚度多少,都要求涂层具有优良的绝缘性,附着性,耐腐蚀性,冲片性和焊接性,以满足新能源汽车用无取向硅钢片的各种应用需求。
6.专利申请号201510589941.8开发了一种无铬的无取向硅钢用涂料,组分为有机硅树脂,磷酸二氢铝,磷酸二氢锌,二氧化硅胶体,丙二醇。在钢板表面形成约1.5μm厚的涂层,涂层具有良好的表面状态,和高附着性、高绝缘性、高耐蚀性、耐高温和高焊接性。但该涂层没有考虑涂层的冲片性能,并且该涂层不适用涂层厚度为0.1-1μm的无取向硅钢片。专利申请号200910053706.3公布了一种无取向硅钢用无铬绝缘涂料,涂料组分有:金属磷酸二氢盐,树脂,金属有机酸盐,有机溶剂。涂布后涂层具有良好的绝缘性、耐蚀性和附着性,并改善了绝缘涂层表面发粘的现象。但该涂层仅考虑了涂敷量为1.8g/m2的情形,未考虑改变涂层厚度对冲片性、焊接性的影响。专利申请号201310407312.x公开了一种含有有机着色剂的无取向硅钢,使涂层的颜色加深,该涂层是含铬的涂料,并且没有考虑涂层的冲片性和焊接性。专利201010551455.1公开了一种环保半无机无取向硅钢绝缘涂料,含有聚氨酯-丙烯
酸酯-环氧乙烷树脂,磷酸二氢铝,钼酸锌,胶体二氧化硅,非离子表面活性剂。涂层厚度约为1.5μm,涂布后涂层具有优良的外观,附着性,防潮性和耐腐蚀性。但没有考虑涂层的冲片性和焊接性问题,也不适用涂层厚度为0.1-1μm的无取向硅钢片。申请号201010189174.9公布了一种环保无取向硅钢用的绝缘涂料,涂料中化学组成包括:硼酸,异丙醇镁,聚氨酯-丙烯酸酯-环氧乙烷树脂,磷酸二氢铝,乙酸锌,胶体二氧化硅。涂层厚度约为1.5μm,该涂层具有良好的耐腐性、焊接性、附着性。但没有考虑涂层的冲片性能,并且该涂料不适用涂层厚度为0.1-1μm的无取向硅钢片。申请号200910194759.7公开了一种半无机型环保无取向硅钢绝缘涂料,包含异丙醇镁,聚氨酯-丙烯酸酯-环氧乙烷树脂,磷酸二氢铝,乙酸锌,胶体二氧化硅,非离子表面活性剂。涂层厚度约为1.5μm,该涂层具有良好的耐腐性、焊接性、附着性。但没有考虑涂层的冲片性能,并且该涂料也不适用涂层厚度为0.1-1μm的无取向硅钢片。申请号201010241799.5公开了一种无铬环保型无取向硅钢绝缘涂料,组分包括:乙二醇,硼酸,聚氨酯-丙烯酸酯-环氧乙烷树脂,磷酸二氢铝,乙酸锌,胶体二氧化硅。涂层厚度约为1.5μm,该涂层具有良好的耐腐性、可焊接性、附着性。但没有考虑涂层的冲片性能,并且该涂料也不适用涂层厚度为0.1-1μm的无取向硅钢片。申请号201710424754.3提出了一种无取向硅钢环保绝缘涂料的制备方法。主要是提供了树脂的制备方法,制备的绝缘涂料可改善涂层的耐热性能,稳定性和遮盖力问题。没有考虑涂层的冲片性和焊接性。申请号201210550722.5公布了一种无取向硅钢用半无机环保绝缘涂料,涂料组分为磷酸二氢铝,磷酸二氢锰,磷酸二氢锌,氧化锌,氧化镁,硼酸,树脂,有机溶剂,有机助剂。涂层厚度为0.5-5μm,涂层后涂层具有优良的绝缘性,附着性,耐热性和耐腐蚀性,但没有考虑涂层的冲片性和焊接性。申请号201210492590.5公开了一种无铬半有机绝缘涂料,成分为:金属磷酸二氢盐,水溶性环氧树脂分散体,氨基树脂或三聚氰胺和双氰胺。涂层涂布量为1.0-1.5g/m2,涂布后涂层具有优良的附着性,冲片性和绝缘性,但涂层耐腐蚀性较差,锈蚀面积为20-40%,并且没有考虑涂层的焊接性。申请号201910173714.5公开了一种无取向硅钢用无铬半有机绝缘涂层涂料,包括金属磷酸二氢盐,水溶性树脂,含锌的氧化物和/或含锌的硝酸盐。该涂层具有优异的耐腐蚀性、耐热性和附着性。没有考虑涂层的冲片性和焊接性。申请号201910551775.0公开了一种用于特大型发电机的无取向硅钢用无铬绝缘涂料,组分包括二氧化钛,硫酸钡,硅溶胶,钛酸酯偶联剂,有机溶剂,其他助剂。该涂层厚度达到4-7μm,需满足大型发电机制造所需的极厚涂层电工钢。未考虑涂层的冲片性和焊接性。申请号201210204406.2公开了一种用于无取向硅钢的环保绝缘涂料,包含:水性环氧树脂,磷酸二氢铝,锌系化合物,铜系化合物,钴系化合物,镍系化合物,硅溶胶,表面活性剂。该涂液稳定性好,涂料涂布后,涂层均匀,具有良好的绝缘性能。但没有考虑涂层的冲片性和焊接性。
7.由于涂层厚度大于2μm时,涂层附着性和焊接性都将大幅度降低。而涂层厚度小于0.3μm时,涂层的绝缘性和冲片性都会大幅度降低。因此上述涂料均不满足不同涂层厚度下(0.1-4μm),新能源汽车用无取向硅钢片的高强度、高附着性、高绝缘性需求。
技术实现要素:
8.本发明的目的在于提供一种适用于新能源汽车用无取向硅钢片的无铬环保绝缘涂料,在涂层厚度0.1~4μm范围内,钢板表面质量优良,涂层具有良好的附着性、绝缘性、耐腐蚀性,以及优良的冲片性和焊接性能。
9.为了解决上述技术问题,本发明提供以下技术方案:
10.提供一种适用于新能源汽车用无取向硅钢片的无铬环保绝缘涂料,包含如下质量百分比含量的各组分:硅烷偶联剂为1~15%,烷氧基硅烷:0.5~8%,氧化锆胶体:2~10%,硅酸盐:0.1~3%,碳基酸:0.3~2%,有机溶剂,2~12%,余量为水。
11.按上述方案,所述烷氧基硅烷,选用甲氧基硅烷、乙氧基硅烷、丙氧基硅烷、丁氧基硅烷中的至少一种。
12.按上述方案,所述硅烷偶联剂,选用乙烯基三乙氧基硅烷、乙烯基三甲氧基硅烷、乙烯基三(β-甲氧乙氧基)硅烷中的至少一种。
13.烷氧基硅烷中烷氧基基团在水中发生水解,形成硅羟基基团:
[0014]-si-or h2o
→‑
si-oh roh
ꢀꢀꢀꢀꢀꢀꢀꢀꢀꢀꢀꢀꢀꢀꢀꢀꢀ
(1)
[0015]
硅羟基基团与金属羟基基团发生脱水缩合反应形成si-o-me键(me代表金属):
[0016]-si-oh me-oh
→‑
si-o-me h2o
ꢀꢀꢀꢀꢀꢀꢀꢀꢀꢀꢀꢀꢀ
(2)
[0017]
硅羟基基团发生自身脱水缩合反应,形成si-o-si键,从而在金属表面上形成三维网络结构:
[0018]-si-oh si-oh
→‑
si-o-si- h2o
ꢀꢀꢀꢀꢀꢀꢀꢀꢀꢀꢀꢀꢀꢀꢀ
(3)
[0019]
si-o-me与si-o-si的密度越大,硅烷与金属的附着力越好;三维网络越密集,硅烷对金属的防腐蚀能力越高。但反应(2)和(3)在水环境下,都会发生逆向水解,导致金属失去硅烷膜的覆盖,发生腐蚀。
[0020]
硅烷偶联剂的分子结构式一般为y-r-si(or)3(式中y—有机官能基,sior—硅烷氧基)。硅烷氧基对无机物具有反应性,有机官能基对有机物具有反应性或相容性。当硅烷偶联剂介于无机和有机界面之间,可形成有机基体-硅烷偶联剂-无机基体的结合层,有利于提高涂层的附着性。
[0021]
加入氧化锆胶体,可以提高硅烷膜三维网状的结构密度,并提高硅烷膜、金属界面层的结合强度。有利于在金属表面形成以si-o-si键为主体的网状膜,并与金属离子之间存在价键。氧化锆胶体在钢板表面形成由fe与zr的氧化物、氢氧化物所构成的复合膜层。
[0022]
按上述方案,烷氧基硅烷与硅烷偶联剂含量的比值为0.5~2.0,有利于涂层的焊接性能。
[0023]
按上述方案,所述硅酸盐,选自金属为mg、k、al或na的硅酸盐中的至少一种。
[0024]
硅酸盐粘结力强,可以由溶液自发转化为凝胶,可强化涂层的密度和硬度。硅酸盐与上述硅烷偶联剂溶液混合后发生了水解缩合反应,形成硅衍生物的溶胶凝胶。比如,硅酸钠与乙烯基三乙氧基硅烷混合后,乙烯基三乙氧基硅烷由于水解,形成乙烯基硅醇和乙醇,乙烯基硅醇与硅酸钠水解产生的硅羟基发生缩合,最终形成中间是si-o-si,外层是未水解的疏水-oc2h5,不参与反应的-ch=ch2,和少量的-oh基团的硅-聚合物,从而在表面形成了庞大的三维网络,强化了涂层的机械性能。硅酸盐含量不可过高,因为硅酸盐的溶解度较低,含量过高,不利于涂料的稳定性。含量过低,将不足以形成硅衍生物的溶胶凝胶,无法强化涂层的机械性能。
[0025]
按上述方案,所述碳基酸,选用柠檬酸、醋酸、酒石酸中的至少一种。
[0026]
碳基酸可调节硅烷偶联剂的聚合度,也可调节涂液的ph值至4-6。碳基酸含量不可过高,过高会降低硅烷偶联剂的聚合度,过低又不能调节涂料的硅烷偶联剂的聚合度,影响
涂料的稳定性。此外当碳基酸过高时,ph值低于4,容易对钢板造成腐蚀,当碳基酸过低时,ph值高于6,也不利于涂料的稳定。
[0027]
按上述方案,所述有机溶剂为乙醇、醋酸乙酯或醋酸甲酯。有机溶剂的加入有利于涂层的涂布性能,使涂层外观优良。
[0028]
按上述方案,所述涂料的固含量为10~28%,有利于涂层的涂布性能。若固含量过低,影响涂层的绝缘性;若过高,影响涂层的涂布效果。
[0029]
提供一种适用于新能源汽车用无取向硅钢片的无铬环保绝缘涂层,由上述无铬环保绝缘涂液涂布在所述无取向硅钢片表面制备得到。
[0030]
按上述方案,所述无铬环保绝缘涂层的厚度为0.1~4μm。
[0031]
按上述方案,所述无铬环保绝缘涂层制备工艺为:
[0032]
将所述无铬环保绝缘涂料涂布到所述无取向硅钢片上,在板温为150~350℃下加热干燥,如果板温低于150℃,绝缘膜中会有水分残留,若板温高于350℃,涂层会出现过烧发黑的现象。
[0033]
优选地,干燥时间为40~100s。
[0034]
按上述方案,在涂层厚度0.1-4μm范围内,涂层附着性为a级,层间电阻大于30ω
·
cm2/片,钢板叠片系数大于96.0%;涂层耐腐蚀性好,经盐雾实验,腐蚀面积不超过2%;涂层冲片性能优良,毛刺达到50μm的冲片次数可达到180万次-300万次;涂层焊接性优良,焊接气泡<7个的最大焊接速度可达到100cm/min。
[0035]
本发明提供一种适用于新能源汽车用无取向硅钢片的无铬环保绝缘涂料,通过硅烷耦联剂、烷氧基硅烷、氧化锆胶体、硅酸盐和碳基酸协同配合得到与基底紧密结合的三维网状膜层,具体为:
[0036]
烷氧基硅烷在水中水解,一部分自身脱水缩合反应形成si-o-si键,从而在金属表面上形成三维网络结构;一部分与金属羟基缩合得到si-o-me键,提高与基底的结合力;其中si-o-me与si-o-si的密度越大,硅烷与金属的附着力越好;三维网络越密集,硅烷对金属的防腐蚀能力越高,但是在水环境中,si-o-me与si-o-si均会发生逆向水解,导致金属失去硅烷膜的覆盖,发生腐蚀。
[0037]
本发明通过硅烷偶联剂、碳基酸、硅酸盐和氧化锆胶体共同提高三维网络结构的致密性。一方面,硅烷偶联剂同时含有有机官能团和硅烷氧基,可以同时对无机物和有机物有反应性。硅烷偶联剂介于无机基体和有机网状结构之间,可形成有机基体-硅烷偶联剂-无机基体的结合层,有利于提高涂层的附着性。同时,碳基酸的加入可以调节硅烷偶联剂的聚合度,有利于硅烷偶联剂发挥作用。而硅酸盐因本身粘结力强,可以由溶液自发转化为凝胶,可强化涂层的密度和硬度。其还可与硅烷偶联剂、烷氧基硅烷发生水解缩合反应,形成硅衍生物的溶胶凝胶,从而在表面形成了庞大的三维网络,有利于在金属基体表面形成以si-o-si键为主体的网状膜,强化了涂层的冲片性和焊接性。另一方面,氧化锆胶体可与金属基体之间形成共价键,在钢板表面形成由fe与zr的氧化物、氢氧化物所构成的复合膜层,可以提高硅烷膜三维网状的结构密度,强化了涂层的冲片性和焊接性,并提高硅烷膜、金属界面层的结合强度。本发明通过硅烷耦联剂、烷氧基硅烷、氧化锆胶体、硅酸盐和碳基酸协同配合,所得膜层结构致密,与金属基体结合力强,在涂层厚度0.1-4μm范围内,均具有良好的冲片性和焊接性。此外,有机溶剂有利于涂层的涂布性能,使涂层外观优良。
[0038]
本发明的有益效果如下:
[0039]
本发明提供一种无铬环保绝缘涂料,硅烷耦联剂、烷氧基硅烷、氧化锆胶体、硅酸盐和碳基酸协同配合,可形成以有机高分子化合物为主和以氧化锆胶体为辅的复合成膜物,所得膜层结构致密,与金属基体结合力强;应用于新能源汽车电机用无取向硅钢时,在涂层厚度0.1-4μm范围内,均具有优良的耐腐蚀性、冲片性和焊接性,同时钢板表面质量优良,涂层附着性为a级,绝缘电阻可达到30ω
·
cm2/片以上,叠片系数大于0.96,可满足新能源汽车用无取向硅钢高强度、高附着性、高绝缘性的需求。
具体实施方式
[0040]
下面通过具体实施例进一步对本发明进行解释说明。
[0041]
实施例1-8
[0042]
提供一种新能源汽车用无取向硅钢的无铬环保绝缘涂料,包括以下组分:硅烷耦联剂,烷氧基硅烷,氧化锆胶体,硅酸盐,碳基酸,有机溶剂,余量为去离子水。
[0043]
其中,各组分具体物质类型和配比分别如表1和表2所示。
[0044]
表1实施例1-8和对比例1-3组分具体物质类型
[0045][0046][0047]
表2实施例1-8和对比例1-3组分配比
[0048][0049]
其中,表中质量百分比剩余量为纯水。
[0050]
对0.5mm的无取向硅钢片,涂布实施例1-8和对比例1-3所得的绝缘涂层后,经板温350℃下退火60s,涂层厚度如表2所示,钢板性能如表3所示。
[0051]
表3.实施例1-8和对比例1-3涂覆绝缘涂层后钢板性能
[0052][0053]
耐腐蚀性测试:盐雾试验,gb/t13448-2006,gb/t1766-1995,8小时。
[0054]
焊接性测试:氩气保护焊,焊接电流120a,电极th-w,加压100kg/cm2。
[0055]
从表2和表3中可以看出,在实施例1~8中,按本发明所配制的绝缘涂液涂布在0.5mm的无取向硅钢上,经350℃烘干后,涂层厚度为0.1-4μm,钢板表面质量优良,涂层附着性为a级,层间电阻普遍大于30ω
·
cm2/片,钢板叠片系数大于96.0%。涂层耐腐蚀性好,经盐雾实验,腐蚀面积不超过2%。涂层冲片性能优良,毛刺达到50μm的冲片次数可达到180万次-300万次。涂层焊接性优良,焊接气泡<7个的最大焊接速度可达到100cm/min。
[0056]
对比例1中,硅烷耦联剂含量过低,烷氧基硅烷含量过高,烷氧基硅烷和硅烷耦合剂比例大于2,并且氧化锆胶体含量过低,导致表面涂层外观性不好,涂层绝缘性差,绝缘电阻为1.5ω
·
cm2/片,涂层易脱落,附着性为d级,钢板叠片系数小于96.0%,涂层冲片性较差,毛刺达到50μm的冲片次数仅为90万次。焊接性差,焊接气泡<7个的最大焊接速度仅为
15cm/min。
[0057]
对比例2中,烷氧基硅烷和硅烷耦合剂比例小于0.5,氧化锆胶体含量过低,涂料的固含量较低,涂料涂敷烘干后,涂层附着性差,涂层绝缘电阻低,仅为1.3ω
·
cm2/片。涂层焊接性差,焊接气泡<7个的最大焊接速度仅为10cm/min。
[0058]
对比例3中,氧化锆胶体和硅酸盐含量过高,碳基酸含量过低,涂料涂敷烘干后,涂层附着性差,涂层绝缘电阻低于10ω
·
cm2/片,钢板叠片系数小于96.0%,涂层的冲片性差,毛刺达到50μm的冲片次数仅为80万次。
[0059]
以上仅为本发明的较佳实施例而已,并不用以限制本发明,凡在本发明的精神和原则之内,所作的任何修改、等同替换、改进等,均应包含在本发明的保护范围之内。
再多了解一些
本文用于企业家、创业者技术爱好者查询,结果仅供参考。