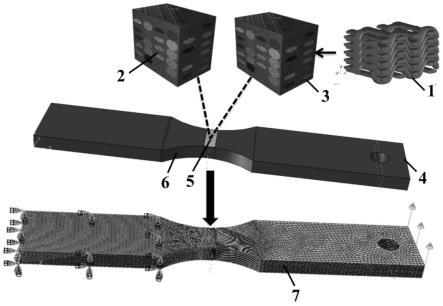
一种2.5d机织复合材料振动疲劳损伤的多尺度模拟方法
技术领域
1.本发明属于复合材料虚拟仿真技术领域,涉及一种2.5d机织复合材料振动疲劳损伤的多尺度模拟方法。
背景技术:
2.以低密度、高比强度、高比刚度和良好的耐久性的树脂基复合材料代替金属材料,是实现发动机减重增效的重要技术途径,已成为新一代航空发动机的主流趋势。2.5d机织复合材料由于独特的层间联锁结构,克服了层板复合材料层间性能薄弱和抗冲击性能差的缺点。此外,2.5d机织复合材料还具备制备成本低、可设计性强等优点,比普通的3d编织复合材料具有更好的工艺性。显著的优点使得2.5d机织复合材料成为制备发动机叶片的理想选择。航空发动机叶片服役在严苛的振动疲劳环境中,典型的一个案例是发动机叶片轴颈处于弯曲振动疲劳加载的工况下。众所周知振动疲劳是比普通疲劳更加恶劣的工况条件,因此在对2.5d机织复合材料叶片进行结构设计、分析时必须充分考虑材料在振动疲劳工况下的安全性,这对工程可用的2.5d机织复合材料振动疲劳损伤预测模型提出了迫切需求。
3.2.5d机织复合材料是一种新兴的发动机叶片用材料,其振动疲劳行为方面的研究还非常有限,现存的关于2.5d机织复合材料振动疲劳的数值模拟方法大都采用宏观尺度的有限元模型,即不考虑2.5d机织复合材料内部纱线的微观结构特征,而是将整个结构中的材料当作一种均匀的各向异性材料,并采用力学试验测得的材料9个工程常数定义材料的宏观模量和泊松比。2.5d机织复合材料是一种具有明显纱线三维空间结构的非均质材料,其损伤行为的表征与描述必须聚焦到单胞尺度,因此对2.5d机织复合材料振动疲劳损伤的预测必须基于单胞模型,但如果整个结构的模型都细化到单胞尺度,计算量将非常庞大,为了兼顾高预测精度和工程应用对低计算成本、高计算效率的需求,建立2.5d机织复合材料振动疲劳损伤模拟的多尺度模型是目前唯一可行的技术途径。目前2.5d机织复合材料的多尺度模型大都集中在静态载荷下材料内部损伤演化规律的模拟方面,尚缺少专门用于预测2.5d机织复合材料振动疲劳加载过程中内部微观损伤状态的多尺度模拟方法。此外,现存的2.5d机织复合材料多尺度模拟方法大都基于全局模型-子模型的思想,具体实施方法是在宏观模型和子模型上对应位置定义界面,在宏观模型的数值计算过程中,将该界面处的数据按照指定步长保存,根据需要去掉外部载荷或者保留部分外部载荷,或者对载荷进行放大后,将数据传递到细观尺度的子模型中再进行一次计算,可见采用全局模型-子模型的方法需要进行两次计算分析,操作繁琐。另外,为了保证全局模型和子模型的匹配,还需要对宏观有限元模型计算得到的界面数据进行人为放大,放大因子的选择往往高度依赖工程师的经验,因此这种便捷性差、操作繁琐的方法在实际工程中的应用非常有限。
4.2.5d机织复合材料叶片轴颈在振动疲劳工况下的安全性和可靠性设计是目前业界非常关注的一个工程问题,上述工况可简化为一个2.5d机织复合材料悬臂梁弯曲加载条件的共振疲劳试验,工程实际由此对兼顾高预测精度和高计算效率的2.5d机织复合材料振动疲劳损伤的多尺度模拟方法产生迫切需求。。
技术实现要素:
5.本发明的目的是:提出一种2.5d机织复合材料振动疲劳损伤的多尺度模拟方法,对2.5d机织复合材料在任意载荷水平下的一阶弯曲振动疲劳加载过程中材料内部的损伤状态进行快速、准确地预测。
6.为解决此技术问题,本发明的技术方案是:
7.提供一种2.5d机织复合材料振动疲劳损伤的多尺度模拟方法,
8.通过将单胞有限元模型嵌入2.5d机织复合材料振动疲劳试验件宏观有限元模型工作段最小截面处,将宏观有限元模型上单胞模型嵌入区域的材料设置为一种具有极小弹性模量的各向同性材料,利用“嵌入式”约束将单胞有限元模型的节点约束于宏观有限元模型的单元网格中,组合得到多尺度模型,基于固定周期跳跃的疲劳加载模拟方法设置数值模拟的分析步,结合专门针对2.5d机织复合材料振动疲劳损伤模拟提出的失效准则和材料性能退化规则,在cae软件中开展有限元模型的数值计算,实现2.5d机织复合材料振动疲劳损伤的多尺度模拟;具体包含步骤如下:
9.步骤一、建立单胞有限元模型:
10.根据2.5d机织预制体的编织结构,建立2.5d机织复合材料的单胞有限元模型,并分别为单胞有限元模型中的基体和纱线设置材料参数;标记单胞模型的长、宽方向及其尺寸,其中单胞模型的长、宽方向取决于振动疲劳试验件中真实的纱线分布;
11.具体方法如下:若振动疲劳试验件长度方向是经纱延展方向,则单胞模型中的经纱延展方向为单胞模型的长度方向,纬纱延展方向为单胞模型的宽度方向;若振动疲劳试验件长度方向是纬纱延展方向,则单胞模型中的纬纱延展方向为单胞模型的长度方向,经纱延展方向为单胞模型的宽度方向;
12.步骤二、建立划分了单胞模型嵌入区域和其它区域的振动疲劳试验件的宏观有限元模型:
13.首先,在软件中建立振动疲劳试验件的宏观有限元模型。然后,根据单胞模型的宽度w和振动疲劳试验件工作段区域的最小宽度w,计算拟嵌入单胞有限元模型的个数n,
14.其次,以振动疲劳试验件工作段中心为单胞模型嵌入区域的中心,以单胞模型的长度作为单胞模型嵌入区域的长度,以n个单胞模型的总宽度(n﹡w)作为单胞模型嵌入区域的宽度,由此确定振动疲劳试验件宏观有限元模型上的单胞模型嵌入区域,并从宏观模型中将这部分切割成独立的部分。
15.将单胞模型嵌入区域定义为各向同性材料,材料弹性模量设置为极小值(0.001mpa),泊松比设置为0.3。宏观有限元模型上其它区域定义为正交各向异性材料,设置材料局部坐标系,按照试验测得的2.5d机织复合材料宏观尺度的9个材料工程常数(即e1,e2,e3,v
12
,v
13
,v
23
,g
12
,g
13
,g
23
)为其它区域的材料定义不同方向的弹性模量和泊松比。
16.步骤三、多尺度模型的组合:
17.将n个单胞有限元模型嵌入2.5d机织复合材料振动疲劳试验件宏观有限元模型上的单胞模型嵌入区域,然后利用嵌入式约束(embedded region),将单胞有限元模型的节点约束到振动疲劳试验件宏观有限元模型的单元网格中;
18.步骤四、设置组合后的多尺度有限元模型的约束和载荷条件
19.对组合后的振动疲劳试验件的多尺度有限元模型设置如下约束和载荷条件:多尺
度模型无中心孔一侧的端面到中间工作段之间区域的上、下表面设置固支约束(约束节点的平动和转动自由度);多尺度模型有中心孔一侧端面的上方边线施加位移型载荷,位移方向垂直于试验件宏观有限元模型的上表面并朝上,位移的具体数值取决于真实振动疲劳加载时试验件自由端的振幅;
20.步骤五、定义单胞有限元模型中基体和纱线的失效准则以及损伤后的力学性能退化规则
21.针对固定周次跳跃的疲劳加载模拟方法,为了模拟每经历固定循环周次n0=106的损伤,专门提出了如下基体和纱线的失效准则。
22.基体的失效准则定义为:基体的von mises应力(或叫冯米思应力)大于0.8倍的基体拉伸强度;纱线的失效准则定义为:纱线中横向应力或纱线厚度方向应力大于0.8倍的纱线横向拉伸强度;
23.在满足失效准则后,对基体和纱线进行材料力学性能退化,退化规则是:若纱线的应力水平满足失效准则,则将纱线的横向模量降为极小值(0.001mpa);若基体的应力水平满足失效准则,将基体的弹性模量降为极小值(0.001mpa);
24.步骤六、为有限元模型设置模拟疲劳加载的分析步和数值计算参数
25.按照固定周期跳跃的疲劳加载模拟方法的思想,在软件中为有限元模型设置模拟疲劳加载的分析步;
26.步骤七、基于多尺度模型数值计算的振动疲劳损伤模拟
27.根据步骤五定义的单胞内纱线和基体的失效准则和力学性能退化规则,编写子程序,并在子程序中定义损伤状态变量(statev)作为失效准则的表征量,在软件中进行有限元模型和子程序的关联设置,利用软件对上述建立的多尺度有限元模型进行数值计算。从多尺度模型的数值计算结果中单独调取内嵌的单胞有限元模型的模拟结果,逐增量步地查看单胞有限元模型中的纱线和基体的损伤状态变量(statev)云图,获得每经历固定循环周次n0=106的振动疲劳加载过程中2.5d机织复合材料试验件工作段区域材料内部微观损伤状态的演变规律。
28.步骤二所述n具体计算方法为:令试验件工作段最小宽度w与单胞模型的宽度w相除,取结果的整数部分作为n。
29.步骤六具体方法如下:在软件中定义一个“tabular”类型的载荷谱,定义“加载-卸载”循环模块,其中循环模块的个数n等于拟模拟的疲劳加载循环次数n除以固定循环周次n0;然后,在软件中定义一个时间长度为1的通用静态分析步,将当前分析步的计算增量步设置为固定值1/n,并将当前分析步的加载谱类型设置为上述定义的“tabular”类型的载荷谱。
30.该方法适用于模拟发动机叶片轴颈振动工况的,基于悬臂梁弯曲的2.5d机织复合材料一阶共振疲劳加载过程中的材料内部微观损伤状态的预测。
31.该方法适用于一侧开中心孔(开孔的目的是加配重块用)的2.5d机织复合材料哑铃型试样的振动疲劳损伤模拟。
32.所述振动疲劳加载为应力比为r=-1的周期性正弦疲劳载荷谱。
33.所述2.5d机织复合材料为采用树脂传递模塑成型工艺(rtm)制备的树脂基复合材料。
34.该模拟方法适用于室温干态条件下2.5d机织复合材料的振动疲劳损伤行为的预测。
35.该方法基于固定周期跳跃的疲劳加载模拟方法,适用于固定跳跃周次n0=106的情形,其它情形也可参照使用,但采用的失效准则需要做调整。
36.本发明的有益效果是:
37.本发明方法通过将2.5d机织复合材料的单胞有限元模型嵌入振动疲劳试验件宏观有限元模型工作段最小截面处,将宏观有限元模型上单胞模型嵌入区域的材料设置为一种具有极小弹性模量的各向同性材料,宏观有限元模型其它区域的材料根据材料力学测试获得的2.5d机织复合材料宏观尺度上的9个材料工程常数进行参数设置,随后利用“嵌入式”约束将单胞有限元模型的节点约束于宏观有限元模型的单元网格中,进一步基于固定周期跳跃的疲劳加载模拟方法,结合专门针对2.5d机织复合材料振动疲劳损伤模拟提出的单胞内纱线和基体的失效准则及其力学性能退化规则,实现对模拟发动机叶片轴颈振动工况的,2.5d机织复合材料悬臂梁一阶弯曲振动疲劳加载过程中材料内部纱线、基体微观损伤状态及其演变规律的多尺度模拟。
38.(1)弯曲加载下的振动疲劳是发动机叶片轴颈的典型工况,本发明提出的方法可预测任意应力水平下2.5d机织复合材料在一阶弯曲振动疲劳加载过程中的损伤萌生、损伤演化和最终的损伤状态,可帮助设计师确定发动机用2.5d机织复合材料叶片结构的设计许用值;
39.(2)根据结构特点,对试验件工作段高应力区域采用考虑内部纱线结构的单胞有限元模型进行精细化模拟,其它区域采用基于材料均匀化假设的宏观有限元模型模拟,相比于对整个试验件都采用宏观有限元模型进行模拟的预测方法具有更高的预测精度,并且可以预测材料内部纱线、基体的微观损伤状态;
40.(3)较之需要开展两次数值计算的基于全局模型-子模型的多尺度模拟方法,本发明所述方法只需对多尺度模型开展一次数值计算,无需设置全局模型和子模型之间的数据传递,具有简单、快捷、便于工程应用等优点;
41.(4)在建模策略方面,本方法创新性地在宏观有限元模型上划分出单胞嵌入区域,并将这个区域的材料设置为一种具有极小弹性模量的各向同性材料,然后将单胞有限元模型嵌入该区域,并采用嵌入式约束(embedded region)将单胞有限元模型的节点约束到宏观有限元模型的单元网格中,相比将宏观有限元模型待嵌入单胞区域切除后嵌入单胞有限元模型,然后直接绑定宏观模型和单胞模型接触面的方法,本方法可有效避免降低由于模型在几何上不连续而引起的应力集中,可保证载荷和变形在两个尺度的有限元模型之间有效传递,从而获得高精度的单胞模型内部应力场的模拟结果。
42.(5)所述方法具有通用性和拓展性,可拓展到其它更加复杂工况,以及具有更复杂结构形式的2.5d机织复合材料结构振动疲劳行为的模拟。
附图说明
43.图1为振动疲劳试验件构型和尺寸结构图;
44.图2为多尺度模型的建模方案示意图;
45.图3(a)~(c)为模拟得到的振动疲劳加载次数分别为1
×
106、5
×
106、1
×
107时单
胞模型内部损伤状态的云图;
46.图4(a)~(c)为振动疲劳加载次数分别为1
×
106、5
×
106、1
×
107时真实试验件工作段内部损伤状态的ct检测结果;
47.图5为本发明的2.5d机织复合材料振动疲劳损伤的多尺度模拟方法流程图。
48.其中,1为2.5d机织复合材料的单胞编织构型;2为拟嵌入的第一个2.5d机织复合材料的单胞有限元模型;3为拟嵌入的第二个2.5d机织复合材料的单胞有限元模型;4为振动疲劳试验件的几何模型;5为宏观有限元模型上单胞有限元模型嵌入区域;6为宏观有限元模型上其它区域;7为组合得到的2.5d机织复合材料振动疲劳试验件的多尺度模型。
具体实施方式
49.为使本发明实施例的目的、技术方案和优点更加清楚,下面将结合本发明实施例中的附图,对本发明实施例中的技术方案进行清楚、完整地描述。下面将详细描述本发明实施例的各个方面的特征。在各个附图和下面的描述中,没有示出公知的结构和技术,以避免对本发明造成不必要的模糊。
50.图5为本发明方法的流程图,该方法将2.5d机织复合材料的单胞有限元模型嵌入振动疲劳试验件宏观有限元模型工作段最小截面处,将宏观有限元模型上单胞模型嵌入区域的材料设置为一种具有极小弹性模量的各向同性材料,随后利用“嵌入式”约束将单胞有限元模型的节点约束于宏观有限元模型的单元网格中;进一步基于固定周期跳跃的疲劳加载模拟方法,结合专门针对2.5d机织复合材料振动疲劳损伤模拟提出的失效准则和材料性能退化规则,在cae软件内进行数值计算,实现对2.5d机织复合材料振动疲劳加载过程中材料内部纱线、基体微观损伤状态的多尺度模拟。
51.为此,首先根据预制体的纱线结构建立2.5d机织复合材料的单胞有限元模型,随后根据试验件尺寸和单胞模型的尺寸确定拟嵌入单胞有限元模型的数量,并由此确定宏观有限元模型上单胞模型嵌入的区域,将该单胞模型嵌入区域划分为一个独立的部分;并将单胞模型嵌入区域的材料设置为一个具有极小弹性模量的宏观各向同性材料,宏观有限元模型其它区域的材料则根据材料力学测试获得的2.5d机织复合材料宏观尺度上的9个材料工程常数进行参数设置,随后将单胞有限元模型移动到宏观有限元模型的单胞模型嵌入区域,并利用软件嵌入式约束(embedded region)功能,将单胞模型的节点约束到宏观有限元模型的单元网格中;
52.进一步根据固定周期跳跃的疲劳加载模拟方法,在软件中进行分析步和计算增量步的设置,并对组合得到的多尺度有限元模型设置模拟真实试验加载工况的约束和载荷条件,随后结合基于试验结果分析的、专门针对2.5d机织复合材料振动疲劳损伤模拟提出的单胞内纱线和基体大的失效准则和力学性能退化规则编写子程序。
53.在子程序中定义损伤状态变量,并且在cae软件中对有限元模型和子程序进行关联设置在cae软件中对多尺度模型提交计算,完成数值计算后,从整个多尺度模型的数值计算结果中单独调取单胞有限元模型的结果,逐增量步地查看单胞有限元模型中损伤状态变量的云图,获得振动疲劳试验过程中不同循环次数下试验件工作段材料内部损伤状态的预测结果。
54.该方法兼具计算成本低和预测精度高的优点,可有效预测2.5d机织复合材料振动
疲劳加载过程中材料内部的微观损伤状态以及损伤演化规律。
55.下面将结合附图和2.5d机织复合材料试验件悬臂梁一阶弯曲振动疲劳加载过程中损伤行为模拟的实施例对本发明技术方案作进一步地详述:
56.1、试验件和振动疲劳试验加载的描述
57.(a)振动疲劳试验件构型和尺度
58.2.5d机织复合材料振动疲劳试验件的构型和具体尺寸如图1,其中试验件的长度方向为2.5d机织复合材料的经纱方向。图1中的尺寸参数如下:长度l=110mm,宽度b=20mm,工作段最窄截面处宽度w=20mm,工作段圆弧半径r=20mm,配重块装配用圆孔直径d=6mm。
59.(b)2.5d机织预制体描述
60.2.5d机织预制体由经纱、纬纱、衬经纱组成,纱线规格为t800-6k*2。纬纱的密度为6根/cm,层数为6。经纱的密度为4根/cm,层数为5。衬经纱的密度为4根/cm,层数为5。t800碳纤维是一种横观各向同性材料,定义材料力学性能所需的全部6个工程常数为:(纤维纵向的弹性模量)ef=295gpa,(纤维横向的模量)e
t
=10gpa,(纤维纵横剪切模量)g
ft
=5gpa,(纤维横向剪切模量)g
tt
=5gpa,(纤维纵横泊松比)v
ft
=0.3,(纤维横向泊松比)v
tt
=0.4。
61.(c)2.5d机织复合材料描述
62.用于切割成振动疲劳试验件的2.5d机织复合材料板子通过rtm工艺成型得到,采用的树脂为一种双马树脂(ec230r)。板子名义厚度为4mm,纤维体积含量为56%。利用力学测试获得表征2.5d机织复合材料宏观基本力学性能的9个材料工程常数,分别为:(经纱方向模量)e1=66.1gpa,(纬纱方向模量)e2=59.2gpa,(厚度方向模量)e3=8.11gpa,(面内纵横剪切模量)g
12
=4.84gpa,(层间剪切模量)g
13
=2.88gpa,(面内横向剪切模量)g
23
=3.23gpa,(纵横泊松比)v
12
=0.085,(纵厚泊松比)v
13
=0.51,(横厚泊松比)v
23
=0.42。根据静态拉伸性能的测试结果,2.5d机织复合材料的经向拉伸强度x
t
为691mpa。基体ec230r的弹性模量em=4.5gpa,泊松比vm=0.3,基体拉伸强度σm=119mpa。纱线的纵向拉伸强度xf=1900mpa,纱线横向是由基体将纤维粘结在一起,因此纱线的横向拉伸强度yf在数值上等于基体拉伸强度σm,即yf=119mpa。(补充描述各个模量含义)
63.(d)2.5d机织复合材料振动疲劳试验描述
64.基于悬臂梁弯曲的加载方案,对2.5d机织复合材料试验件开展一阶弯曲振动疲劳试验,载荷谱为周期性的正弦波,采用的应力比为r=-1。通过控制振动疲劳试验件上表面的应变,结合应力标定结果,控制振动疲劳试验的应力水平,本实施例中振动疲劳试验中的应力水平选为2.5d机织复合材料的经向拉伸强度x
t
的0.28倍,此时试验件自由端的振幅为4mm,疲劳加载的循环次数共计107次。
65.2、多尺度模型的建立和数值计算
66.根据上一节所述的本实施例中振动疲劳试验件和振动疲劳试验加载方式的描述,按照以下步骤建立2.5d机织复合材料振动疲劳损伤预测的多尺度模型,并开展数值计算,得到在振动疲劳加载过程中材料内部损伤状态的预测结果。
67.(1)步骤一,根据2.5d机织复合材料的单胞编织构型1、组分材料参数以及振动疲劳试验件的名义厚度,利用软件建立2.5d机织树脂基复合材料的全厚度单胞几何模型,根据前面所述的纱线和基体组分各自的材料基本力学性能参数,在软件中为单胞
模型中的纱线设置6个材料工程常数,分别为:ef=295gpa,e
t
=10gpa,g
ft
=5gpa,g
tt
=5gpa,v
ft
=0.3,v
tt
=0.4;同时为单胞模型中的基体设置材料的弹性模量和泊松比,分别为em=4.5gpa和vm=0.3。设置单胞3个方向的网格尺寸和单元类型。在本实施例中3个方向的网格个数均为50个,单元类型设置为完全积分的8节点六面体单元(c3d8),完成单胞有限元模型的建模后,导出模型的input文件,该input文件中存储着2.5d机织树脂基复合材料单胞有限元模型的全部信息,包括局部坐标系、纱线和基体力学参数、纱线的几何与空间分布等。
68.(2)步骤二,建立划分了单胞模型嵌入区域和其它区域的振动疲劳试验件的宏观有限元模型
69.首先,按照振动疲劳试验件的几何构型和尺寸,在软件中建立振动疲劳试验件的几何模型4。然后,根据单胞模型的宽度w和振动疲劳试验件工作段区域的最小截面宽度w,计算拟嵌入单胞有限元模型的个数n,具体计算方法为:令试验件工作段最小截面宽度w与单胞模型的宽度w相除,取结果的整数部分作为n。接下来,以振动疲劳试验件工作段中心为单胞模型嵌入区域的中心,以单胞模型的长度作为单胞模型嵌入区域的长度,以n个单胞模型的总宽度(n﹡w)作为单胞模型嵌入区域的宽度,由此确定振动疲劳试验件宏观有限元模型上的单胞模型嵌入区域,并从宏观模型中将这部分切割成独立的部分。在本实例中拟嵌入单胞模型的个数为2个,根据前面所述方法确定了宏观有限元模型上的单胞模型嵌入区域5,由此对宏观有限元模型进行不同区域的分割,使单胞模型嵌入区域5形成一个独立的部分。
70.在软件中为宏观模型上单胞模型嵌入区域5和其它区域6设置不同的材料力学性能参数,其中将单胞模型嵌入区域5的材料定义为各向同性材料,材料弹性模量e设置为极小值(0.001mpa),泊松比v设置为0.3。宏观模型其它区域6的材料定义为正交各向异性材料,设置材料局部坐标系,并按照试验测得的2.5d机织复合材料宏观尺度上的9个材料工程常数(即e1,e2,e3,v
12
,v
13
,v
23
,g
12
,g
13
,g
23
)为其它区域6的材料设置不同方向的材料弹性模量和泊松比。对宏观模型进行网格划分,并定义单元类型为c3d8。
71.(3)步骤三,多尺度模型的组合
72.将步骤一得到的单胞有限元模型的input文件导入软件,得到
73.在软件界面下显示的2.5d机织复合材料的单胞有限元模型,在软件的装配模块下导入2个单胞有限元模型2,3,以及步骤二得到的划分了单胞模型嵌入区域和其它区域的振动疲劳试验件的宏观有限元模型。将两个单胞模型的长度方向旋转到与试验件宏观模型的长度方向一致,并将2个单胞模型并排到一起,然后将其平移到宏观有限元模型上的单胞嵌入区域5,使2个单胞模型与单胞嵌入区域5完全重合。随后,切换到软件的接触模块下,利用软件的嵌入式约束(embedded region)功能,将2个单胞有限元模型2,3的所有节点约束到振动疲劳试验件的宏观有限元模型的单元网格中,得到组合后的多尺度有限元模型7。
74.(4)步骤四,设置组合后的多尺度有限元模型的约束和载荷条件
75.切换到软件的加载模块,对组合后的多尺度有限元模型7设置如下约
束条件和载荷条件:多尺度模型无中心孔一侧的端面到中间工作段之间区域的上、下表面设置固支约束(约束节点的平动和转动自由度);多尺度模型有中心孔一侧端面的上方边线施加位移型载荷,位移的方向为垂直于试验件多尺度有限元模型的上表面并朝上,对本实施例,由于振动疲劳试验中控制的试验件自由端的振幅为4mm,因此模拟中位移载荷的数值设置为4mm;
76.(5)步骤五,定义单胞有限元模型中基体和纱线的失效准则以及损伤后的力学性能退化规则。
77.针对固定周次跳跃的疲劳加载模拟方法,为了模拟每经历固定循环周次n0=106的损伤状态,专门提出了如下单胞模型内基体和纱线的失效准则。基体的失效准则定义为:基体的von mises应力(或叫冯米思应力)大于0.8倍的基体拉伸强度σm;纱线的失效准则定义为:纱线中横向应力(在软件界面下显示为s22)或纱线厚度方向应力(在软件界面下显示为s33)大于0.8倍的纱线横向拉伸强度yf;在满足失效准则后,对基体和纱线进行材料力学性能退化,退化规则是:若纱线的应力水平满足失效准则,则将纱线的横向模量e
tt
降为极小值(0.001mpa);若基体的应力水平满足失效准则,则将基体的弹性模量em降为极小值(0.001mpa);之所以采用0.8倍的基体拉伸强度和纱线横向拉伸强度作为失效准则中的强度阈值是考虑106的疲劳循环次数跳跃造成的累积损伤。
78.(6)步骤六,为有限元模型设置模拟疲劳加载的分析步和数值计算参数
79.按照固定周期跳跃的疲劳加载模拟方法的思想,在软件中为有限元模型设置模拟疲劳加载的分析步,针对本实施例,具体方法如下:在软件中定义一个“tabular”类型的载荷谱,设置“加载-卸载”循环模块(加载设置为参数1,卸载设置为参数0),其中循环模块的个数n等于拟模拟的疲劳加载循环次数n(107)除以固定跳跃循环周次n0(106),因此循环模块的个数n=10;然后,在软件中定义一个时间长度为1的通用静态分析步,将当前分析步的计算增量步设置为固定值1/n(即0.1),并将当前分析步的加载谱类型设置为上述定义的“tabular”类型的载荷谱。
80.(7)步骤七,基于多尺度模型数值计算的振动疲劳损伤模拟。
81.根据步骤五定义的失效准则和材料性能退化规则,编写umat子程序,在umat子程序中分别定义2.5d机织复合材料中纱线和基体的本构、失效准则、指示失效准则是否满足的损伤状态变量(statev)、纱线和基体失效后的退化规则等。其中,损伤状态变量(statev)是确保损伤状态在不同分析步之间传递的关键参数,也是表征内部纱线和基体损伤程度的量化指标。在软件中进行多尺度有限元模型和umat子程序的关联设置,利用软件对上述建立的多尺度有限元模型进行数值计算。从整个多尺度模型的计算结果中单独调取内嵌的单胞有限元模型的结果,逐增量步地查看单胞模型中损伤状态变量(statev)的云图,在软件界面下损伤状态变量(statev)显示为符号sdv设置当sdv大于1时云图显示为灰色,单胞模型上显示出的灰色区域的大小、位置和分布即为2.5d机织复合材料振动疲劳试验件工作段区域单胞内基体和纱线的损伤状态,根据步骤六的分析步设置,增量步每增加一步,代表模拟的振动疲劳循环加载次数向前跳跃了固定循环周次n0=106,通过逐增量步地查看单胞内sdv的云图,可以对每累计106次疲劳循环加载的2.5d机织复合材料振动疲劳试验件工作段处材料内部的损伤状态进行模拟仿真;利用配备了12核
cpu,内存为8gb的计算机进行多尺度模型的数值计算,计算时间约79min,图3(a)~3(c)分别展示了2.5d机织复合材料振动疲劳试验件分别累计经历了1
×
106、5
×
106、1
×
107次循环后工作段处材料内部损伤状态的模拟结果,其中灰色区域代表已经失效的材料。可见随着循环次数的增加,单胞内部的损伤区域逐渐变大。此外根据sdv指示的损伤因子的数值,可知随着振动疲劳循环次数的增加,单胞内部的损伤程度也越来越严重。图4(a)~4(c)分别展示了2.5d机织复合材料振动疲劳试验件分别累计经历1
×
106、5
×
106、1
×
107次循环后真实试验件工作段处损伤状态的ct检测结果。可见,数值模拟得到的损伤状态和对应的累计循环次数下真实试验件内部损伤的ct检测结果基本吻合,说明了本发明提出的模拟方法具有较高的预测精度。此外,真实的物理试验大约耗时19小时,而基于本发明提出的多尺度模拟方法的数值计算仅耗时约79分钟,数值模拟可以给出与真实试验基本吻合的损伤状态,并且可量化损伤程度,可见本发明提出的一种2.5d机织复合材料振动疲劳损伤的多尺度模拟方法具有高效、快捷的优点,在实际工程设计中具有可观的应用前景。
再多了解一些
本文用于企业家、创业者技术爱好者查询,结果仅供参考。