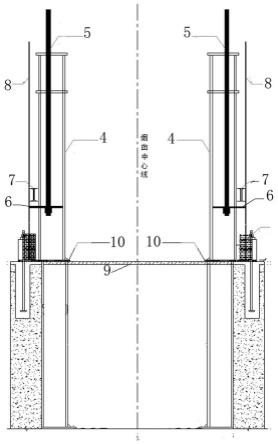
1.本发明涉及钢内筒烟囱施工方法,具体而言,涉及一种钢内筒烟囱液压提升施工方法。
背景技术:
2.中煤蒙大60万吨/年煤制甲醇项目热电装置烟囱总高度为180m,是一个套筒烟囱,外筒为钢筋混凝土筒壁,顶标高为175m;内筒为等直径自立式钢内筒,顶标高为180m,内直径为4100mm。钢内筒(0.0m-170.0m)及内筒底座采用q235b钢,烟道接口附件及加劲肋材质为q235b,钢内筒上部10m及顶部外露爬梯等均采用不锈钢。其中混凝土外壁未考虑钢内筒安装荷载,烟囱钢内筒工程系铆工、电焊工、油漆工、起重工等多工种交叉作业,工序繁杂、工程量大、工期紧张的综合性特殊施工项目,具有高、难、险、紧的施工特点,寻求一套技术上可行、经济上节约、工序上安排合理的钢内筒施工方法迫在眉睫。
技术实现要素:
3.本发明的目的是提供一种能够降低高空作业风险、提高施工效率的钢内筒烟囱液压提升施工方法。
4.为实现上述目的,本发明采用的技术方案是:一种钢内筒烟囱液压提升施工方法,包括步骤:步骤一,制作安装支撑平台利用钢内筒混凝土基础制作钢内筒的支撑平台,所述支撑平台包括支撑平台立柱和固定连接在支撑平台立柱顶端的顶板;支撑平台立柱沿混凝土基础板均布并焊接牢固;步骤二,液压提升装置的制作和安装液压提升装置包括胀圈和提升支架系统;胀圈胀紧于钢内筒;所述提升支架系统包括提升架、提升杆、托架和千斤顶,所述提升架顶部安装千斤顶,提升杆竖直连接于千斤顶上,提升架侧面中部留有竖向的滑道,托架滑动安装在滑道内并与提升杆底部相连接;提升时,由千斤顶拉动提升杆,提升杆拉动托架,托架托动胀圈,胀圈带动钢内筒移动;步骤三,围板装置制作安装所述围板装置包括用于水平运输的小车,和用于垂直提升的配置有手拉葫芦的弧形单轨梁;通过该围板装置将钢内筒部件运输并吊装就位;步骤四,筒壁提升带板组对筒壁安装前在钢内筒支撑平台顶板上画出壁板的安装位置线,沿画线四周每个立柱顶板设一垫块;采用倒装法施工,首先安装顶层的第一节钢内筒,按照排板依次将第一节钢内筒壁板用围板装置吊装就位并焊接,安装完成后通过液压提升装置进行提升,然后安装第二节钢内筒并组对和焊接两圈壁板之间的环缝;按照上述方法依次安装全部钢内筒壁板;
步骤五,工装拆除 钢内筒提升完毕后,拆除支撑平台,将裙座与底部筒体焊接完成,拆除液压提升装置。
5.进一步地,步骤一中,支撑平台立柱间预留两个施工进出通道,其它支撑平台立柱间用槽钢连接起来使其成为整体。
6.进一步地,步骤二中,所述胀圈分为两件,每片胀圈的弧长小于半个钢内筒的弧长,两扇胀圈的缺口之间放置胀紧千斤顶,胀紧千斤顶顶紧胀圈缺口的端面,使胀圈胀紧在钢内筒内壁上。
7.进一步地,步骤二中,第一节钢内筒安装及提升时,在围板装置的手拉葫芦的配合下,按照排板依次将壁板吊装就位,一边吊装,一边点焊纵缝,待该层壁板全部吊装组对完成以后,在内侧沿焊缝自上而下间隔点弧型板;钢内筒内部加膨胀圈顶紧后,方可施焊。
8.进一步地,步骤二中,最后组对的一节钢板的纵缝及上部环缝焊接后,将胀圈落下并开启液压提升装置,使钢内筒升高160~200mm,拆除垫块。
9.进一步地,在烟囱各层钢结构平台的平台主梁上安装导向轮,以保证钢内筒垂直提升运行。
10.进一步地,在钢内筒提升高度未达到30m时,每提升一段后用吊坠在钢内筒0
°
和90
°
方向测量垂直度,如果不符合要求,用单个提升装置微调,将其调控在规范要求之内;当钢内筒提升高度超过30m,在30m的钢梁处0
°
、90
°
、180
°
、270
°
方向划定四个点,当钢内筒第一次通过该点时测量数据并记录,以后每次提升钢内筒时以前次数据为基础计算垂直度是否超标。
11.进一步地,在提升支架外运过程中将0-20.0m钢内筒与钢爬梯钢柱用槽钢连接,槽钢设置方式为竖直方向每2.5m/层,每层6根。
12.根据本发明所述方法,先施工裙座底板部分,利用钢内筒裙座钢板作为钢内筒支撑平台;在液压提升系统不工作时,可以安全承载钢内筒全部荷载。同时由于在施工过程中垫高已经安装完成的钢内筒段,便于施工人员及机具进出已经安装完成的钢内筒段。钢内筒提升方法选择倒装提升法,减少了高空作业,提高了施工质量;使用围板装置解决了烟囱内作业空间狭小的问题,优化了施工工序;提升设备工装利用烟囱的加强柱大大的降低了摊销费用,同时又保证了工期;钢内筒提升过程中的垂直导向措施优化增加了稳定性,降低了提升风险。
附图说明
13.图1为支撑平台布置示意图;图2为提升装置布置图;图3为围板装置构造图;图4为钢制导向轮布置图;图5为导向装置构造图;图6为支撑稳固示意图。
14.图中,1-钢内筒混凝土基础,2-支撑平台,3-裙座底板,4-提升架,5-提升杆,6-托架,7-胀圈,8-钢内筒,9-柱顶板,10-提升支架底板,11-烟囱外壁,12-弧形单轨梁,13-手拉
葫芦,14-运输小车,15-平台支架,16-平台梁,17-导向轮,18-混凝土筒壁,19-连接板,20-筋板,21-槽钢。
具体实施方式
15.本发明一种典型的实施方式提供的钢内筒烟囱液压提升施工方法,包括步骤:步骤一,制作安装支撑平台利用钢内筒混凝土基础制作钢内筒的支撑平台,所述支撑平台包括支撑平台立柱和固定连接在支撑平台立柱顶端的顶板;支撑平台立柱沿混凝土基础板均布并焊接牢固;支撑平台的作用是在液压提升系统不工作时,可以安全承载钢内筒全部荷载;同时由于在施工过程中垫高已经安装完成的钢内筒段,便于施工人员及机具进出已经安装完成的钢内筒段。
16.步骤二,液压提升装置的制作和安装液压提升装置包括胀圈和提升支架系统;胀圈胀紧于钢内筒;所述提升支架系统包括提升架、提升杆、托架和千斤顶,所述提升架顶部安装千斤顶,提升杆竖直连接于千斤顶上,提升架侧面中部留有竖向的滑道,托架滑动安装在滑道内并与提升杆底部相连接;提升时,由千斤顶拉动提升杆,提升杆拉动托架,托架托动胀圈,胀圈带动钢内筒移动。
17.利用钢内筒基础内部混凝土筏板基础,安装基础内支撑柱及液压提升设备。在液压设备垂直拉升作用下,通过牵引系统带动钢内筒垂直运行,使已经焊接完成的钢内筒分2米每段垂直向上提升。
18.步骤三,围板装置制作安装所述围板装置包括用于水平运输的小车,和用于垂直提升的配置有手拉葫芦的弧形单轨梁;通过该围板装置将钢内筒部件运输并吊装就位。烟囱内钢内筒部件采用上述围板装置进行水平运输和垂直运输步骤四,筒壁提升带板组对筒壁安装前在钢内筒支撑平台顶板上画出壁板的安装位置线,沿画线四周每个立柱顶板设一垫块;采用倒装法施工,首先安装顶层的第一节钢内筒,按照排板依次将第一节钢内筒壁板用围板装置吊装就位并焊接,安装完成后通过液压提升装置进行提升,然后安装第二节钢内筒并组对和焊接两圈壁板之间的环缝;按照上述方法依次安装全部钢内筒壁板。
19.步骤五,工装拆除 钢内筒提升完毕后,拆除支撑平台,将裙座与底部筒体焊接完成,拆除液压提升装置。
20.以申请人施工的某煤制甲醇项目为例,热电装置烟囱总高度为180m,是一个套筒烟囱,外筒为钢筋混凝土筒壁,顶标高为175m;内筒为等直径自立式钢内筒,顶标高为180m,内直径为4100mm。其施工工艺流程为:施工准备
→
基部支撑平台安装
→
提升设备支架安装
→
提升设备安装调试
→
围板装置安装
→
筒壁提升带板组对
→
导向装置安装
→
工装拆除。
21.施工前准备施工所需要的材料已经到场并检验合格,场地经过平整并清除所有障碍,现场具
备开工条件。
22.基部支撑平台安装1
ꢀꢀ
支撑平台校核计算钢内筒支承平台承载的钢内筒筒身及附件最大重量为301t,无缝钢管φ219*8(20#)的截面面积为a=89.98cm
²
,q235(δ≤16mm)抗压设计强度f=215n/mm
²
,立柱个数n=16故计算钢柱实际承受强度为f’=g/(na)=301
×
10
×
1000n/(16
×
5303)mm
²
=35.48n/mm
²
安全系数n=f/f’=215/35.48=6.05,满足使用要求。
[0023]2ꢀꢀ
支撑平台制作安装根据设计图纸加工钢内筒裙座底板3,基础环板采用半自动火焰切割机加工,螺栓孔采用机械加工。基础环板和地脚螺栓安装完毕后用水平尺校正底板,并地脚螺栓灌浆完毕。
[0024]
用高度为500mm无缝钢管φ219*8(20#) 做支撑平台立柱,共计16个,支撑平台顶板采用钢板δ=20mm(300
×
300)。其沿原基础板均布并焊接牢固,支撑平台立柱间预留两个施工进出通道,其它支撑立柱间用槽钢[8连接起来使其成为整体以增加稳定性。图1为支撑平台布置示意图。
[0025]
提升设备安装1
ꢀꢀ
提升设备支架安装如图2所示,液压提升装置的制作包括胀圈制作、提升支架系统制作。
[0026]
①ꢀ
胀圈制作和安装:将滚压成弧型的钢板焊接成圆,用胀圈胀紧钢内筒,减少钢内筒的变形,提高钢内筒的钢性,便于下一代钢板的焊接。提升胀圈采用槽钢[25a(q235b),滚压成型,弧度和钢内筒的内壁弧度相同,一根槽钢正面滚压,一根槽钢反面滚压,然后对扣,焊接成弧度与钢内筒内径弧度相同的口字型工件。整个胀圈分为两件,每片胀圈的弧长小于半个钢内筒的弧长,两扇胀圈的缺口,能放下两台胀紧千斤顶。千斤顶,顶胀圈的两头的端面,使胀圈紧紧胀紧在钢内筒内壁上,保证钢内筒的圆度与刚度,便于下一带板的拼装焊接。
[0027]
②ꢀ
提升支架系统制作和安装提升支架系统由6根提升架连接组成。提升支架应均匀布置在钢内筒内壁,尽量靠近壁板,以减少支架的弯距。为节约摊销费用,结合钢内筒加强柱的做法,提升架是由钢板δ=52mm和δ=30mm拼装组成,中间留有滑道,滑道里装有托板式托架。提升架上端焊有装千斤顶的一个平台,平台分两层,上层装千斤顶,下层装下夹头。底部有一块钢板用于提升架和底部支柱。提升架中一根直径为70mm的提升杆,用于提升托架,从而带动钢内筒的提升。中央控制台置于钢内筒中心,由高压橡胶软管连接各油缸的上下油孔。使用时逐个进行空载试验,检查油缸往复动作,提升杆步进,上、下卡头是否可靠,提升杆与托架的运动,以及中央控制台和油管是否正常工作。提升时千斤顶拉动提升杆,提升杆拉动托架,托架托动胀圈,胀圈带动钢内筒。
[0028]2ꢀꢀ
提升设备调试液压提升动力来自中央控制台,其中包括电机、油泵、油箱、换向阀、安全阀、压力表、按钮盘、配油器、截止阀等。高压油经软管送至双作用油泵,通过换向阀实现油缸的往复
动作。活塞杆是空心的,中间穿一提升杆。在油缸的上、下各有一个单向卡头,在油缸往复运动时,可自动完成提升杆的步进式工作。提升杆拉动托架,用托板提动胀圈,使筒体提升,实现倒装工艺要求。
[0029]
围板装置制作安装如图3所示,围板装置包括用于水平运输的小车,和用于垂直提升的配置有手拉葫芦的弧形单轨梁。
[0030]
根据土建施工预留洞口尺寸5200
×
4850mm,每带板板宽2000mm,选择1.8m
×
12000m的轨道,2t卷扬机作牵引,轨道选用h250
×
250
×9×
14,共计22m,轨道底部用24mm钢板满铺。
[0031]
壁板单重最大重量为1.82t故选择2个2t手拉葫芦作为垂直起吊工具,用来围壁板工作。根据《单轨、悬挂吊车梁通用图集》hg21542-3选择跨度为6m,对应吊车梁为i25(q235b),吊车梁、手拉葫芦、壁板总重量约为6t,选择安全系数为6,吊车梁支柱选择5根,抗压设计强度f=215n/mm
²
故计算得承载截面面积a=6
×
10
×
1000
×
6/(5
×
215)=334mm
²
选择无缝钢管φ219
×
6 材质为20#,其截面面积为 415mm
²
,可满足使用要求。为保证支柱的稳定性,将无缝钢管用槽钢[16连接,并与混凝土壁连接,防止侧移。
[0032]
筒壁提升带板组对1
ꢀꢀ
第一节钢内筒安装及提升每节钢内筒由2~3块钢板组成,第一节钢板安装前应在钢内筒支撑平台顶板上画出壁板的安装位置线,沿画线四周每个立柱顶板设一垫块。垫块采用槽钢[14a,长150mm。垫块与底板点焊,在其上表面画出安装线,在画线两侧点焊挡板。倒装法施工,首先安装顶层壁板。在手拉葫芦的配合下,按照排板依次将壁板吊装就位,一边吊装,一边点焊纵缝(留出有安装余量的一道纵缝不点焊)。对口间隙应符合设计要求,待该层壁板全部吊装组对完成以后,在内侧沿焊缝自上而下每500mm左右点焊一块弧型板。整圈对口时,注意周长先预留85mm,每条纵缝上加设3块弧形板,且内部加膨胀圈顶紧后,方可施焊;留下一条纵缝先不焊,等其它纵缝焊完后围尺测量其收缩值,符合要求后再焊接。以后的周长预留值按此进行。壁板纵缝先焊外侧,内侧清根后施焊。除活口以外的其他纵缝全部焊完后,应拉尺测量壁板周长。周长的实际尺寸应该是理论尺寸加最后活口焊接收缩量,加下部环缝焊接收缩量。要围尺检查上下口的周长是否符合要求,上下口用倒链收紧,内纵缝磨平后,上口用钢膨胀圈校圆,焊接最后活口。
[0033]
第一圈壁板提升时提升装置应由专人控制,同步运行。提升过程中应密切注意提升是否平稳正常。发现异常情况,应立即停止提升,查明原因,消除隐患后重新开始提升。提升到约200mm左右高度时,暂停。检查设备是否同步运行,提升高度是否一致,受力是否均衡,胀圈有无变形,立柱有无异常等。如无问题,可继续提升。
[0034]2ꢀꢀ
第二节及其它节钢内筒安装钢内筒第一节安装之后,即可安装第二节钢板,方法同第一节钢板,并留出一道活口先不焊,当外侧的其它立缝全部焊完后,在活口处用倒链拉紧到达调整与上圈壁板焊口错边量的目的,然后焊接该道活口。
[0035]
组对和焊接两圈壁板之间的环缝。环缝焊接时,活口两侧应留出长约1米的环缝暂
不焊接,待活口组焊完毕后再焊。每圈壁板的活口应相互对称错开180
°
。在第三节钢板吊装的同时,在钢内筒内组对和安装胀圈。调整提升设备,然后提升,提升时,用中央控制台按钮盘按上升钮,完成提升,再按下降钮,使油缸活塞复位。第二步提升同第一步操作。一步步提升直至使第1节钢板高出下层壁板30~50mm,在下层壁板内外侧错开设计要求的对口间隙相同。当上下壁板不等厚时,应保证内侧平齐。用提升机构调整环缝间隙,其方法是依间隙大小逐个支架进行调整。调整时关闭油泵,释放下卡头,手动拧开油缸下回路,每500mm左右点焊一块矩形板,以防止环缝的焊接变形,纵缝内侧自上而下每500mm左右点焊弧形板。第2节安装后,将胀圈落下与底部连接,方法与第1节相同。
[0036]
如此循环按上述方法和步骤安装第3、4节,直至最后所有节段安装结束。每节提升前应将上节壁板上的焊疤打磨清理干净。如上下两节不同板厚的钢板对接处坡口除上述要求外,在外表面应加工一斜坡,最后一节钢板的纵缝及上部环缝焊接后,将胀圈落下与底部连接,开启提升机,使钢内筒升高160~200mm,拆除垫块,在第1节钢板安装线内、外设挡板,使钢板就位。钢内筒的环向及纵向焊缝,由数名焊工均匀对称分布于钢内筒内外,采用分段退焊法,沿同一方向同时施焊。
[0037]3ꢀꢀ
钢内筒提升后的垂直度调整在钢内筒提升高度未达到30m时,每提升一段后用吊坠在钢内筒0
°
和90
°
方向测量垂直度,如果不符合要求,用单个提升装置微调,将其调控在规范要求之内;当钢内筒提升高度超过30m,在30m的钢梁处0
°
、90
°
、180
°
、270
°
方向划定四个点,当钢内筒第一次通过该点时测量数据并记录。以后每次提升钢内筒时以第前次数据为基础计算垂直度是否超标,调整方式如上;需要说明的是由于钢内筒高度越高其摆动幅度越大,在判定其整体中心线是否垂直相对困难,为此我们结合gb50205的相关规定,在测量时四个方向同时测量并测量五次,选择在30mm处定点测量,取其平均值,可减少摆动幅度对测量引起的偏差;垂直度控制范围为l/1000,且不大于30mm,l为每两节筒高。
[0038]
垂直导向装置安装如图4、5所示,为保证钢内筒提升过程中筒体的垂直上升,在烟囱各层钢结构平台上30m平台上安装4套钢制导向轮。导向轮直径200mm*厚度30mm,与平台主梁焊接安装,对称布置,以保证钢内筒在此段垂直提升运行。
[0039]
工装拆除全部钢内筒提升完成,经检查各项指标均满足要求后,将钢套筒提升200mm静止不动,开始拆除基部支撑平台(h型钢、平台钢板、支撑材料等),将内筒基础板打磨后,支撑钢套筒的千斤顶回落使钢套筒完全回落到内筒基础板上,然后按照图纸要求,将基础板和钢套筒连接成整体(最后一带板上预留2m
×
2m洞口,并将预留洞加强,用于运出提升装置部件)。到此,液压提升结束。
[0040]
提升系统的拆除之前钢内筒筒身加强(除加强柱外)必须施工完毕、止晃点安装完毕。提升结束后,所有提升杆均呈不受力状态,此时,割除胀圈、割除各支撑架的支撑体系,将整个系统解体,将提升系统各部件由小到大运出钢内囱外。
[0041]
提升系统中长度为5m的提升支架共计6根,单重为3.03t。长度大、作业空间小、外运难度难度大,为防止支架外运时与钢内筒碰撞导致危险发生,在提升支架外运过程中将
钢内筒0-20.0m与钢爬梯钢柱用槽钢21连接、竖直方向每2.5m/层,每层6根。支撑稳固见图6。
再多了解一些
本文用于企业家、创业者技术爱好者查询,结果仅供参考。