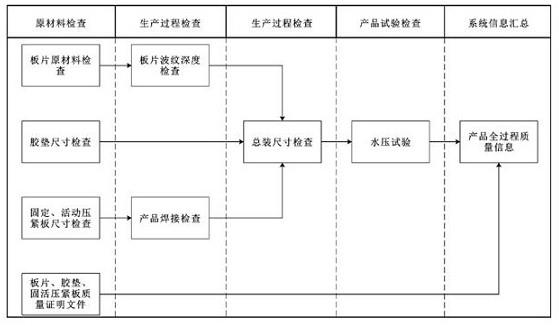
1.本发明涉及可拆式板式热交换器质量管理领域,具体的说是一种基于标准化的板式热交换器全过程质量管理追溯系统及方法。
背景技术:
2.传统的质量管理方式是一种离散的、静态的管理方式,随着产品的生产过程,质量管理人员对产品进行质量检查,并填写纸质记录单后收集汇总,再分析问题,这种方式很难发现制造过程中隐藏的质量问题,也就很难从根本上提高制造过程质量。
3.本发明旨在将各个质量控制环节实现线上记录、电子化流转,系统通过对板式热交换器在生产过程中产生的质量数据进行实时的数据收集、数据清洗,最终实现板式热交换器产品全过程质量信息的大数据分析,并形成质量诊断专家库。用来提升板式热交换器质量控制过程,增强产品竞争力。
技术实现要素:
4.本发明的目的是针对传统的质量管理方式离散、混乱、低效并难以发现隐藏质量问题的缺点,提供了一种基于标准化的板式热交换器全过程质量管理追溯系统及方法,解决了目前板式热交换器从原材料购买、产品制造生产、产品出厂试验中发生的产品质量资料管理混乱,质检数据汇总繁琐,产品质量资料无法快速进行追溯的问题。
5.为达到上述目的,本发明所采取的技术方案为:一种基于标准化的板式热交换器全过程质量管理追溯系统,采用b/s开发模式开发系统整体框架并设计系统各个模块,开发工具选择java、jsp、javascript、html语言设计编写前后端程序,实现系统算法与逻辑,后台数据库选用sql server 2012,分析实际质检过程,合理设计数据库结构,包括相互间信号连接的系统信息录入模块、原材料检查模块、生产过程检查模块、产品试验检查模块和系统信息汇总五个模块,系统信息录入模块用于在系统中录入完整的数据,为质量管理提供准确的数字化依据;原材料检查模块包括板片原材料检查、胶垫尺寸检查、压紧板尺寸检查、质量证明文件上传,用于获取产品生产过程中的原材料数据,包括板片批号、板片字头号、胶垫批号等;生产过程检查模块包括板片波纹深度检查、产品焊接检查,用于获取产品在生产过程中,产品部件的质检数据信息,主要获取方式为移动终端录入方式;产品试验检查模块包括水压试验检查,用于产品完工后,获取产品出厂前的试压数据信息,主要获取方式为手机端录入。
6.一种基于标准化的板式热交换器全过程质量管理追溯方法,采用上述的基于标准化的板式热交换器全过程质量管理追溯系统,包括以下步骤:步骤一、系统信息录入:质量管理人员在办公系统中,收到产品的生产任务通知单,质量管理人员在pc端中打开质量管理追溯系统的“质量信息录入”页面,将此台产品的产品编号、工号、图号、产品名称以及客户要求的温度、压力、材质等关键信息录入系统,此台产品的质量管理过程开始在系统中流转进行;
步骤二、原材料检查:质量检查人员根据步骤一所录入产品信息,对采购的板片原材料、胶垫原材料、压紧板尺寸依次进行质量检查,然后进行质量证明文件上传;步骤三、生产过程检查:生产过程质量检查人员收到产品生产任务通知单,在该台产品的板片压型冲裁完成后,进行板片波纹深度检查;车间焊工完成产品焊接后,进行产品焊接检查并将焊接检验信息录入系统;在产品完成生产组装后,质量检查人员对该台产品进行总装尺寸检查并将检验信息录入系统;步骤四、产品试验检查:当产品完成总装尺寸检查后,质量管理人员在车间打压区进行产品的打压试验,在完成打压试验后,质量管理人员在移动端登录质量管理追溯系统,打开“水压试验检查”页面,找到该产品的水压试验检查待检记录单,在其中录入水温、设计压力、试验压力、保压时间等数据并提交,系统自动记录质量检查人员与提交时间,水压试验检查记录通过“产品编号”关联至该台产品下;步骤五、系统信息汇总:质量管理追溯系统通过上述质量检查环节之间的关联关系,在该产品的全部质量检查过程均完成后,系统实时自动完成该产品的全过程质量信息汇总,该台产品出厂后,若发生产品产生质量问题,在系统中通过查询产品编号,便可快速查询出此台产品的各个质量检查环节过程中的质量数据,并可以快速查出此台产品所使用的物料及其数据,并且质量管理追溯系统提供针对客户的查询模块,客户通过扫描产品标牌上的二维码,即可查询到该台产品的产品合格证等质量证明文件。
7.优选的,所述步骤二的板片原材料检查过程包括质量检查人员在移动端打开质量管理追溯系统,进入“过程检查”中的“板片原材料检查”页面,首先录入该批板片原材料的字头号、材料、批号等数据,然后使用测量工具,对板片原材料进行检查,在移动端系统中录入板片原材料厚度、长度、对角差等数据,提交后,系统自动记录质量检查人员身份信息及提交时间,该批板片原材料通过“板片字头号”关联至板片波纹深度检查记录下。
8.优选的,所述步骤二的胶垫原材料检查过程包括质量检查人员使用pc端登录系统,在“胶垫尺寸检查”页面中,质量检查人员首先录入该批胶垫的型号、材料、批号、厂家代号、硬度厚度标准值范围等数据,然后使用测量测厚仪、硬度计对胶垫进行质量检查,在系统中录入胶垫硬度、厚度等数据并提交,系统可通过硬度、厚度标准值范围判断数据是否超限,若超限,则将数据标红显示,系统可自动记录质量检查人员信息与提交时间,该批胶垫原材料通过胶垫的型号、材质、批号、厂家代号关联至总装尺寸检查记录下。
9.优选的,所述步骤二的压紧板尺寸检查过程包括质量检查人员在移动端打开质量管理追溯系统,进入“过程检查”中的“压紧板检查”页面,首先录入压紧板的图号、压板材料、批号等数据,然后使用测量工具,对压紧板进行尺寸检查,并在移动端系统中录入压紧板尺寸数据,提交后,系统自动记录质量检查人员身份信息及提交时间,该批压紧板通过“压紧板板号”关联至总装尺寸检查记录下。
10.优选的,所述步骤二的质量证明文件检查过程包括质量检查人员在进行板片原材料检查和胶垫原材料检查并确认物料质量证明无误后,使用pc端登录系统,打开“质量文件上传”页面,上传确认无误的物料质量证明文件,其中,板片质量证明文件通过“板片字头号”关联至板片波纹深度检查记录下,胶垫质量证明文件通过“胶垫型号-胶垫材质-胶垫批号-胶垫厂家代号”、压紧板通过“压紧板板号”,统一关联至总装尺寸检查记录下。
11.优选的,所述步骤三的板片波纹深度检查过程包括生产过程质量检查人员收到产
品的生产任务通知单,在该台产品的板片压型冲裁完成后,进行板片波纹深度检查,打开“板片波纹深度检查表”页面,录入板片的型号、板型、材料、图号等信息,然后使用数显千分尺进行板片波纹深度检查,系统通过数显千分尺自动获取板片波纹数据,检查完成后提交,系统自动记录质量检查人员身份信息及提交时间,板片原材料检查记录已通过“字头号”关联至板片波纹深度检查记录下,板片波纹深度检查通过“预制工号”、“胶垫型号”关联至产品编号下。
12.优选的,所述步骤三的产品焊接检查过程包括车间焊工在施焊完成后,在移动端中打开质量管理追溯系统,打开“焊接检查(施焊)”页面,找到产品的焊接待检记录,在该条待检记录中录入母材规格、母材材质、焊接位置、焊接方法等数据后提交,系统自动记录焊接人员与时间;焊工完成焊接检查(施焊)后,该条记录自动进入“焊接检查(审核)”中,质量检查人员需对其进行审核,质量检查人员在移动端打开质量管理追溯系统,打开“焊接检查(审核)”页面,找到该产品的焊接检查记录,经审核无误后提交,系统自动记录审核人员姓名与审核时间,产品焊接检查记录通过“产品编号”关联至该台产品下。
13.优选的,所述步骤三的总装尺寸检查过程包括质量管理人员在质量管理追溯系统中录入产品的主要信息后,系统中自动生成产品的总装尺寸检查待检记录单,质量检查人员对该台产品进行总装尺寸检查,首先质量检查人员在移动端打开“总装尺寸检查”页面,找到该产品的总装尺寸检查待检记录单,在该条待检记录单中录入胶垫材质、胶垫批号、胶垫厂家代号、压紧板板号等数据并提交,系统自动记录人员信息与提交时间,然后,质量检查人员进入移动端“总装尺寸检查2”页面,找到该产品的待检记录单,使用检查工具检查产品组装后的主要尺寸并在系统中提交,系统自动记录质量检查人员与提交时间,总装尺寸检查记录结束,通过“产品编号”关联至该台产品下。
14.本发明与现有技术相比具有以下优点:1、本发明将所有质检业务过程转为手机终端填写,线上记录,线上流转汇总,所有质检环节中提交到系统中的质检数据均实时关联至该台产品下,在系统中可以实时的看到该产品的质检数据及生产进度,并且支持在线打印质量文件,省去了人工手写纸质记录单与数据整理的时间,极大地提高了工作效率。
15.2、本发明通过产品编号,可清晰的在平台里追溯此产品所涉及的原材料、生产过程、产品试验信息,充分实现了产品质量信息的可追溯性,有效提高了板式热交换器质量精细化管理水平及质量控制过程。
16.3、本发明系统中各个模块能够实现在移动终端打开浏览器后稳定运行,数据库结构设计安全可靠,能够实现数据的共享和安全存取,便于各环节操作人员实行实时数据上传和共享,稳定可靠。
附图说明
17.图1为本发明系统模块图;图2为本发明实体关系图。
具体实施方式
18.下面结合具体实施例对本发明做进一步详细的说明。
19.如图1所示,一种基于标准化的板式热交换器全过程质量管理追溯系统,采用b/s开发模式,开发系统整体框架,设计系统各个模块,能够在浏览器中稳定运行;开发工具选择java、jsp、javascript、html语言,设计编写前后端程序,实现系统算法与逻辑,后台数据库选用sql server 2012,分析实际质检过程,合理设计数据库结构,实现数据的共享和安全存取,包括相互间信号连接的系统信息录入模块、原材料检查模块、生产过程检查模块、产品试验检查模块及系统信息汇总五个模块,系统信息录入模块用于在系统中录入完整的数据,为质量管理提供准确的数字化依据;原材料检查模块包括板片原材料检查、胶垫尺寸检查、压紧板尺寸检查、质量证明文件上传,用于获取产品生产过程中的原材料数据,包括板片批号、板片字头号、胶垫批号等;生产过程检查模块包括板片波纹深度检查、产品焊接检查,用于获取产品在生产过程中,产品部件的质检数据信息,主要获取方式为移动终端录入方式;产品试验检查模块包括水压试验检查,用于产品完工后,获取产品出厂前的试压数据信息,主要获取方式为手机端录入。
20.如图2所示,一种基于标准化的板式热交换器全过程质量管理追溯方法,包括以下步骤:步骤一、系统信息录入:质量管理人员在办公系统中,收到产品的生产任务通知单,质量管理人员在pc端中打开质量管理追溯系统的“质量信息录入”页面中,将此台产品的产品编号、工号、图号、产品名称以及客户要求的温度、压力、材质等关键信息录入系统,此台产品的质量管理过程开始在系统中流转进行;步骤二、原材料检查:质量检查人员根据步骤一所录入产品信息,对采购的板片原材料、胶垫原材料、压紧板尺寸依次进行质量检查,然后进行质量证明文件检查;板片原材料检查过程包括质量检查人员在移动端打开质量管理追溯系统,进入“过程检查”中的“板片原材料检查”页面,首先录入该批板片原材料的字头号、材料、批号等数据,然后使用测量工具,对板片原材料进行检查,在移动端系统中录入板片原材料厚度、长度、对角差等数据,提交后,系统自动记录质量检查人员身份信息及提交时间,该批板片原材料通过“板片字头号”关联至板片波纹深度检查记录下;胶垫原材料检查过程包括质量检查人员使用pc端登录系统,在“胶垫尺寸检查”页面中,质量检查人员首先录入该批胶垫的型号、材料、批号、厂家代号、硬度厚度标准值范围等数据,然后使用测量测厚仪硬度计对胶垫进行质量检查,在系统中录入胶垫硬度厚度等数据并提交,系统可通过硬度厚度标准值范围判断数据是否超限,若超限,则将数据标红显示,系统可自动记录质量检查人员信息与提交时间,该批胶垫原材料通过胶垫的型号、材质、批号、厂家代号关联至总装尺寸检查记录下;压紧板尺寸检查过程包括质量检查人员在移动端打开质量管理追溯系统,进入“过程检查”中的“压紧板检查”页面,首先录入压紧板的图号、压板材料、批号等数据,然后使用测量工具,对压紧板进行尺寸检查,并在移动端系统中录入压紧板尺寸数据,提交后,系统自动记录质量检查人员身份信息及提交时间,该批压紧板通过“压紧板板号”关联至总装尺寸检查记录下;质量证明文件检查过程包括质量检查人员在进行板片原材料检查和胶垫原材料检查并确认物料质量证明无误后,使用pc端登录系统,打开“质量文件上传”页面,上传确认无误的物料质量证明文件,其中,板片质量证明文件通过“板片字头号”关联至板片波纹深
度检查记录下,胶垫质量证明文件通过“胶垫型号-胶垫材质-胶垫批号-胶垫厂家代号”、压紧板通过“固定(活动)压紧板板号”,统一关联至总装尺寸检查记录下;步骤三、生产过程检查:生产过程质量检查人员收到产品生产任务通知单,在该台产品的板片压型冲裁完成后,进行板片波纹深度检查;车间焊工完成产品焊接后,进行产品焊接检查并将焊接检验信息录入系统;在产品完成生产组装后,质量检查人员对该台产品进行总装尺寸检查并将检验信息录入系统;板片波纹深度检查过程包括生产过程质量检查人员收到产品的生产任务通知单,在该台产品的板片压型冲裁完成后,进行板片波纹深度检查,打开“板片波纹深度检查表”页面,录入板片的型号、板型、材料、图号等信息,然后使用数显千分尺进行板片波纹深度检查,系统通过数显千分尺自动获取板片波纹数据,检查完成后提交,系统自动记录质量检查人员身份信息及提交时间,板片原材料检查记录已通过“字头号”关联至板片波纹深度检查记录下,板片波纹深度检查通过“预制工号”、“胶垫型号”关联至产品编号下;产品焊接检查过程包括车间焊工在施焊完成后,在移动端中打开质量管理追溯系统,打开“焊接检查(施焊)”页面,找到产品的焊接待检记录,在该条待检记录中录入母材规格、母材材质、焊接位置、焊接方法等数据后提交,系统自动记录焊接人员与时间;焊工完成焊接检查(施焊)后,该条记录自动进入“焊接检查(审核)”中,质量检查人员需对其进行审核,质量检查人员在移动端打开质量管理追溯系统,打开“焊接检查(审核)”页面,找到该产品的焊接检查记录,经审核无误后提交,系统自动记录审核人员姓名与审核时间,产品焊接检查记录通过“产品编号”关联至该台产品下;总装尺寸检查过程包括质量管理人员在质量管理追溯系统中录入产品的主要信息后,系统中自动生成产品的总装尺寸检查待检记录单,因总装尺寸检查过程需录入数据信息较多,不便一次性录入全部数据,故在移动端中分为“总装尺寸检查”与“总装尺寸检查2”两部分,在产品完成生产与组装后,质量检查人员对该台产品进行总装尺寸检查,首先质量检查人员在移动端打开“总装尺寸检查”页面,找到该产品的总装尺寸检查待检记录单,在该条待检记录单中录入胶垫材质、胶垫批号、胶垫厂家代号、压紧板板号等数据并提交,系统自动记录人员信息与提交时间,然后,质量检查人员进入移动端“总装尺寸检查2”页面,找到该产品的待检记录单,使用检查工具检查产品组装后的主要尺寸并在系统中提交,系统自动记录质量检查人员与提交时间,总装尺寸检查记录结束,通过“产品编号”关联至该台产品下;步骤四、产品试验检查:当产品完成总装尺寸检查后,质量管理人员在车间打压区进行产品的打压试验,在完成打压试验后,质量管理人员在移动端登录质量管理追溯系统,打开“水压试验检查”页面,找到该产品的水压试验检查待检记录单,在其中录入水温、设计压力、试验压力、保压时间等数据并提交,系统自动记录质量检查人员与提交时间,水压试验检查记录通过“产品编号”关联至该台产品下;步骤五、系统信息汇总:质量管理追溯系统通过上述质量检查环节之间的关联关系,在该产品的全部质量检查过程均完成后,系统实时自动完成该产品的全过程质量信息汇总,该台产品出厂后,若产品产生质量问题,在系统中通过查询产品编号,便可快速查询出此台产品的各个质量检查环节过程中的质量数据,并可以快速查出此台产品所使用的物料及其数据,并且质量管理追溯系统提供针对客户的查询模块,客户通过扫描产品标牌上
的二维码,即可查询到该台产品的产品合格证等质量证明文件;以上的仅是本发明的优选实例。应当指出对于本领域的普通技术人员来说,在本发明所提供的技术启示下,作为质量管理领域的公知常识,还可以做出其它等同变型和改进,也应视为本发明的保护范围。
再多了解一些
本文用于企业家、创业者技术爱好者查询,结果仅供参考。