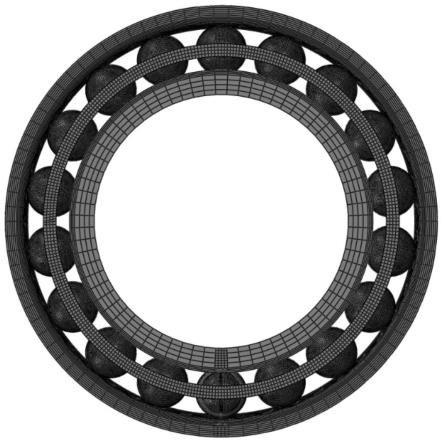
1.本发明涉及机床用角接触球轴承动态性能研究领域,特别提供一种评价机床用角接触球轴承动态性能的有限元分析方法。
背景技术:
2.轴承作为机床的重要零部件,其性能直接影响机床加工精度、刚度和可靠性,并且对机床的主轴系统以及主机的性能有着举足轻重的影响。近年来机床主轴轴承正朝着高转速、高精度和长寿命方向发展,这对机床轴承的结构动态性能和材料的疲劳性能提出了更高要求。因此,研究机床轴承在使役条件下的动态响应,对评价机床轴承的加工精度、刚度和材料疲劳性能具有重要意义。
3.在使役环境下,机床轴承的主要失效模式是滚动接触疲劳导致内、外圈滚道内产生剥离和裂纹,进而使得轴承精度下降。为了研究轴承材料滚动接触疲劳的失效机制,提高轴承的使用寿命,急需一种能够计算轴承在高转速下滚道内接触应力的分析方法,因此,本发明提出一种评价机床用角接触球轴承动态性能的有限元分析方法。
技术实现要素:
4.本发明的目的在于提供一种评价机床用角接触球轴承动态性能的有限元分析方法。此方法能够帮助我们计算机床用角接触球轴承在高转速下的接触应力和动态位移响应,进而用于评价轴承材料的滚动接触疲劳失效机制,改进其生产工艺,提高机床轴承的使用精度和寿命。
5.本发明主要通过下述技术方案实现:一种评价机床用角接触球轴承动态性能的有限元分析方法,包括以下步骤:
6.步骤一、依据国家标准《gb/t292-2007》滚动轴承角接触球轴承外形尺寸,建立角接触球轴承的内圈、外圈、滚动体和保持架的三维实体模型:
7.首先,采用机械设计软件solidworks创建轴承三维实体模型,模型的建立是依据国家标准中规定的轴承尺寸参数和选定的轴承型号,在solidworks的零件模块中分别建立轴承的内圈、外圈和保持架的三维实体模型,而轴承滚动体模型则采用阵列的方式生成。然后,将solidworks零件模块中所建立的轴承各部件导入到装配模块中,完成轴承各零件的装配。最后,导出格式为step的文件,用于模型在有限元软件中的导入和网格划分。
8.步骤二、将导出的轴承模型文件导入到有限元分析软件abaqus中,完成轴承模型的网格划分:
9.轴承各部件的网格划分均在有限元分析软件abaqus中完成。首先,由于轴承内、外圈滚道和滚动体的接触面积非常小,近似于线接触,所以滚道内的网格和滚动体的网格都需要细化处理。其次,由于网格细化处理会导致计算量的显著增加,所以内、外圈和滚动体的网格还需要进行过渡处理,以降低网格数量,提高计算效率;
10.1)轴承内圈模型网格的划分和处理方式如下:首先,将内圈沿径向均匀切分为72
份模型,每一份模型所占角度为5
°
,切分后只保留其中一份,删除其余部分,同时,对切分后保留部分再次进行切分,主要切分部位位于内圈滚道外侧,切分后的模型如图1(a)所示,切分后的模型具有过渡形貌。然后,对切分后的模型进行网格划分,选取单元类型为c3d8r,切分后内圈最小网格尺寸为0.25mm,最大网格尺寸为2mm,网格划分结果如图1(b)所示;最后,将生成的网格部件导入装配模块,在装配模块中对部件进行阵列,生成完整轴承内圈网格模型。此外,为了得到更精确的应力结果,对内圈与滚动体接触应力最大位置的网格进行再细化处理,此时,网格再划分部分的模型所占角度为2.5
°
,模型切分方式不变,最小网格尺寸为0.03mm;
11.2)轴承外圈模型网格的切分方式与内圈相同,首先,将外圈沿径向均匀切分为90份模型,每一份模型所占角度为4
°
(目的是保证最小网格尺寸与内圈一致),切分后只保留其中一份,删除其余部分,同时,对切分后保留部分再次进行切分,主要切分部位位于内圈滚道外侧,切分后的模型如图2(a)所示,切分后的模型具有过渡形貌。然后,对切分后的模型进行网格划分,选取单元类型为c3d8r,切分后外圈最小网格尺寸为0.25mm,最大网格尺寸为2mm,网格划分结果如图2(b)所示;最后,生成的网格部件导入装配模块,在装配模块中对部件进行阵列,生成完整轴承外圈网格模型。此外,为了得到更精准的应力结果,对外圈与滚动体接触应力最大位置的网格进行再细化处理,此时,网格再划分部分的模型所占角度为2
°
,模型切分方式不变,最小网格尺寸为0.03mm;
12.3)滚动体的网格划分同样需要考虑模型整体的计算效率,因此,在滚动体与内、外圈滚道的接触位置,沿轴承径向对滚动体进行切分,并将与滚道接触位置的网格细化,滚动体的切分方式如图3(a)所示,同时,根据轴承转动过程中滚动体的运动轨迹,选取滚动进入稳态后与外圈接触的滚动体,对其网格进一步细化,使其最小尺寸为0.03mm,与内、外圈滚道的网格尺寸一致,滚动体的细化网格如图3(b)所示;
13.4)轴承保持架与滚动体间相互接触,保证滚动体在滚动过程中形态稳定,但其相互间的接触应力较小,因此网格不做细化处理,网格尺寸设定为0.2mm。
14.步骤三、轴承各部件间的接触设置和模型的输入参数:
15.轴承各部件间的接触类型选取显示通用接触,接触界面的法向设定为
‘
硬’接触,切向设定为静-动指数衰减的摩擦接触,其中静摩擦系数设定为0.02,动摩擦系数设定为0.01,衰减系数设定为0.01;
16.为了满足轴承的加载和约束条件,在轴承中心点位置分别建立两个参考点,其中,参考点1与轴承内圈耦合,参考点2与轴承保持架耦合,耦合类型为连续分布耦合;
17.依据轴承各部件的材质,分别赋予对应的材料参数。
18.步骤四、依据轴承的使役工况,完成轴承模型的约束和加载设定:
19.在轴承的台架试验中,轴承外圈固定,内圈施加垂向和轴向的载荷并高速转动。因此,在仿真分析中选用显示动态分析并建立两个分析步:分析步1)中,在轴承内圈的参考点1施加轴承所受的垂向和轴向载荷以及重力载荷,分析步2)中,在参考点1上施加轴承的转速,同时,在两个分析步中固定与载荷和转动方向无关的自由度。
20.进一步,在所述步骤一中,角接触球轴承的接触角角度是15
°
,外圈外径d=68mm,内圈内径d=40mm,滚动体数量为18粒。
21.进一步,在所述步骤二中,轴承内、外圈网格模型的生成是在abaqus的装配模块
中,对内、外圈的网格部件阵列后,利用网格节点的合并功能合并节点后得到,同时,局部细化的网格模型,也需要导入装配模块,对相同位置的网格节点进行合并。
22.进一步,在所述步骤三中,参考点与内圈和保持架的耦合类型只能选取为连续分布耦合,这是因为要保证耦合节点间可以发生相对变形,而运动耦合会限制节点相对变形,从而使结构刚度增大,模拟结果产生较大误差。
23.所述材料参数为:内、外圈为轴承钢材料,其密度为7.8g/cm3,弹性模量是206gpa,泊松比是0.3。滚动体为陶瓷材料,其密度为3.2g/cm3,弹性模量是320gpa,泊松比是0.26。保持架为尼龙材质,其密度为1.35g/cm3,弹性模量是28.3gpa,泊松比是0.35。
24.进一步,在所述步骤四中,轴承垂向和轴向载荷的加载幅值类型选取为光滑型,转速的幅值类型也为光滑型,这种加载方式可以降低惯性力冲击导致的结果振荡,使得动态结果能够快速趋于稳定。
25.本发明的有益效果是:
26.本发明提出一种评价机床用角接触球轴承动态性能的有限元分析方法。此方法依据国家标准提供的机床用角接触球轴承的外形和尺寸,准确建立三维实体模型,并将此模型导入商用有限元分析软件,开展有限元仿真计算。针对机床轴承内、外圈与滚动体的接触面积小,对网格尺寸和计算精度要求高的问题,此方法提出了一种内、外圈和滚动体模型的切分方法,利用此切分方法,能够划分出高质量、高精度的有限元分析网格,并且此方法能够合理控制整体模型的网格数量,减少显示动态的计算时间,提高计算精度和效率。最后,此方法可以准确计算出机床轴承在高转速下的动态位移响应,以及滚动体与接触界面间的接触应力,利用此方法的计算结果可以快速评价机床轴承在使役条件下的动态性能,分析轴承滚道内滚动接触疲劳的失效机理,为改进轴承的生产工艺,提高机床的整体性能提供帮助。
附图说明
27.图1轴承内圈切分方式和网格划分示意图(a、切分方式,b、网格划分方式);
28.图2轴承外圈切分方式和网格划分示意图(a、切分方式,b、网格划分方式);
29.图3滚动体切分方式和网格划分示意图(a、切分方式,b、网格划分方式);
30.图4轴承整体网格划分示意图。
具体实施方式
31.下面结合附图对本发明的技术方案作具体的介绍和说明,一种评价机床用角接触球轴承动态性能的有限元分析方法,具体内容如下:
32.一、依据国家标准《gb/t292-2007》滚动轴承角接触球轴承外形尺寸,建立角接触球轴承的内圈、外圈、滚动体和保持架的三维实体模型:
33.首先,采用机械设计软件solidworks创建轴承三维实体模型,模型的建立是依据国家标准中规定的轴承尺寸参数和选定的轴承型号,在solidworks的零件模块中分别建立轴承的内圈、外圈和保持架的三维实体模型,而轴承滚动体模型则采用阵列的方式生成。然后,将solidworks零件模块中所建立的轴承各部件导入到装配模块中,完成轴承各零件的装配。最后,导出格式为step的文件,用于模型在有限元软件中的导入和网格划分。
34.二、将导出的轴承模型文件导入到有限元分析软件abaqus中,完成轴承模型的网格划分:
35.轴承各部件的网格划分均在有限元分析软件abaqus中完成。滚道内的网格和滚动体的网格都需要细化处理,轴承内、外圈和滚动体的网格也需要进行过渡处理,具体如下:
36.1)轴承内圈模型网格的划分和处理方式如下:首先,将内圈沿径向均匀切分为72份模型,每一份模型所占角度为5
°
,切分后只保留其中一份,删除其余部分,同时,对切分后保留部分再次进行切分,主要切分部位位于内圈滚道外侧,切分后的模型如图1(a)所示,切分后的模型具有过渡形貌。然后,对切分后的模型进行网格划分,选取单元类型为c3d8r,切分后内圈最小网格尺寸为0.25mm,最大网格尺寸为2mm,网格划分结果如图1(b)所示;最后,将生成的网格部件导入装配模块,在装配模块中对部件进行阵列,生成完整轴承内圈网格模型。此外,为了得到更精确的应力结果,对内圈与滚动体接触应力最大位置的网格进行再细化处理,此时,网格再划分部分的模型所占角度为2.5
°
,模型切分方式不变,最小网格尺寸为0.03mm;
37.2)轴承外圈模型网格的切分方式与内圈相同,首先,将外圈沿径向均匀切分为90份模型,每一份模型所占角度为4
°
(目的是保证最小网格尺寸与内圈一致),切分后只保留其中一份,删除其余部分,同时,对切分后保留部分再次进行切分,主要切分部位位于内圈滚道外侧,切分后的模型如图2(a)所示,切分后的模型具有过渡形貌。然后,对切分后的模型进行网格划分,选取单元类型为c3d8r,切分后外圈最小网格尺寸为0.25mm,最大网格尺寸为2mm,网格划分结果如图2(b)所示;最后,将生成的网格部件导入装配模块,在装配模块中对部件进行阵列,生成完整轴承外圈网格模型。此外,为了得到更精准的应力结果,对外圈与滚动体接触应力最大位置的网格进行再细化处理,此时,网格再划分部分的模型所占角度为2
°
,模型切分方式不变,最小网格尺寸为0.03mm;
38.3)滚动体的网格划分同样需要考虑模型整体的计算效率,因此,在滚动体与内、外圈滚道的接触位置,沿轴承径向对滚动体进行切分,并将与滚道接触位置的网格细化,滚动体的切分方式如图3(a)所示,同时,根据轴承转动过程中滚动体的运动轨迹,选取滚动进入稳态后与外圈接触的滚动体,对其网格进一步细化,使其最小尺寸为0.03mm,与内、外圈滚道的网格尺寸一致,滚动体的细化网格如图3(b)所示;
39.4)轴承保持架与滚动体间相互接触,保证滚动体在滚动过程中形态稳定,但其相互间的接触应力较小,因此网格不做细化处理,网格尺寸设定为0.2mm。
40.三、轴承各部件间的接触设置和模型的输入参数:
41.轴承各部件间的接触类型选取显示通用接触,接触界面的法向设定为
‘
硬’接触,切向设定为静-动指数衰减的摩擦接触,其中静摩擦系数设定为0.02,动摩擦系数设定为0.01,衰减系数设定为0.01;
42.为了满足轴承的加载和约束条件,在轴承中心点位置分别建立两个参考点,其中,参考点1与轴承内圈耦合,参考点2与轴承保持架耦合,耦合类型为连续分布耦合;
43.依据轴承各部件的材质,分别赋予对应的材料参数,其中内、外圈为轴承钢材料,其密度为7.8g/cm3,弹性模量是206gpa,泊松比是0.3。滚动体为陶瓷材料,其密度为3.2g/cm3,弹性模量是320gpa,泊松比是0.26。保持架为尼龙材质,其密度为1.35g/cm3,弹性模量是28.3gpa,泊松比是0.35。
44.四、依据轴承的使役工况,完成轴承模型的约束和加载设定:
45.在轴承的台架试验中,轴承外圈固定,内圈施加垂向和轴向的载荷并高速转动。因此,在仿真分析中选用显示动态分析并建立两个分析步:分析步1)中,在轴承内圈的参考点1施加轴承所受的垂向和轴向载荷以及重力载荷,分析步2)中,在参考点1上施加轴承的转速,同时,在两个分析步中固定与载荷和转动方向无关的自由度。
46.上述实施例只为说明本发明的技术构思及特点,其目的在于让熟悉此项技术的人士能够了解本发明的内容并据以实施,并不能以此限制本发明的保护范围。凡根据本发明精神实质所作的等效变化或修饰,都应涵盖在本发明的保护范围之内。
再多了解一些
本文用于企业家、创业者技术爱好者查询,结果仅供参考。