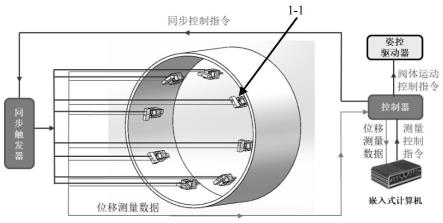
1.本发明属于传感测控技术领域,特别涉及多通道非接触式姿轨控推力矢量系统极性测试装置及方法。
背景技术:
2.姿轨控推力系统主要用于运载火箭末级和各类航天器的姿态控制,实现机动飞行任务。姿轨控推力系统中,燃气阀通过调节燃气发生器产生高温燃气的启闭及流量来控制推力大小,多个燃气阀同步工作产生不同方向推力从而实现对飞行器的轨道与姿态控制。姿轨控推力系统极性是航天器的关键特性。姿轨控推力系统极性错误会使航天器性能严重下降,甚至导致任务失败,姿轨控推力系统极性测试装置是验证推力系统极性正确性的有效手段。
3.姿轨控推力矢量系统通过相对于航天器发动机主轴线径向排列的推力器,使航天器的姿态和轨道发生变化。通常采用成对的转向推力器,每对推力器径向排列在航天器发动机壳体的相对侧。推力器中的针形阀可以是液压、气压或者机电式,沿喷管喉部轴向移动。随着针形阀靠近喷管喉部,喉部通道尺寸减小;针形阀远离喉部,喉部通道面积增大。通过改变和控制针形阀的轴向运动和不同的轴向位置可以实现喷管喉部大小的连续可变,进而实现不同的推力等级。通过比对实际测量姿轨控推力系统运动状态与航天器控制系统发出的姿轨控推力矢量系统控制动作指令的一致性,确定姿轨控推力系统极性是否正确。
4.现有姿轨控推力矢量系统极性测量通过目视、听声音、手触摸等方法判断,这些方法尽管简单并形成了相应规范和协议,但是仍然存在产生误判、漏判等风险,以及存在测试方法不完善的问题。为克服人工测量效率低以及可靠性不高的问题,研究人员提出了利用压力、流量或电磁等不同类型传感器实现自动极性测量的方法。专利文献公开的一种推进系统及其极性数字化测试方法公开号cn109884458a,通过流量传感器与推力器喷管内部接通,基于流量传感器测得的气体最大流量判断姿轨控推力系统极性是否和控制指令一致。该方法在测量过程中需给所有推力器充入氮气,装置较复杂,使用不方便。专利文献公开的一种全闭环航天器姿控极性测试方法cn107703905b,利用气压敏感装置测量喷管内气压,通过综合气压敏感装置产生的信号、各喷管处气球动作进行判读,最终确定姿控系统极性的正确性。该极性测试方法仍然通过采集喷管内气压信号实现极性测量,使用不便。专利文献公开的基于一种卫星姿态控制系统的极性测试装置cn111580492a,用于在地面测试卫星姿态控制系统的极性测量,该装置可显著提高测试效率。该装置的构成包括工作台、机械臂以及控制设备。极性测试时,控制设备通过机械臂改变待测卫星姿态状态,控制设备根据控制信号对应的极性测量值范围以及采集到的卫星姿态控制系统的极性测量值,分析卫星姿态控制系统极性测试结果。该装置需机械臂模拟改变卫星姿态,不适用于姿轨控推力系统极性测试。作者为魏京芳,李宏安,郑文松,李鹏发表于《火箭推进》2005年第003期(31(3):50-53)的“末修姿控系统极性检测仪设计”通过测试仪内部与电磁阀线圈串联的取样电阻网络,获得电磁阀通电或断电时产生的动态电流变化信号,经过信号分析得到末修姿控动
力系统按控制时序的工作情况。该方法实际测量的是电磁阀的吸合或关闭时的电流变化,不能直接测量阀芯的运动特性。专利文献公开的基于漏磁原理的非接触式动力系统极性测试装置授权公告号cn105629095b,基于漏磁原理进行动力系统极性测试。该装置利用磁场传感器采集磁场瞬态变化信号,通过提取信号中的特征信号判断对应姿控喷管电磁阀的动作特征,与控制系统发出的动力系统姿控喷管电磁阀控制动作指令进行一致性比对,若采集的姿控喷管电磁阀的动作特征与弹上控制系统发出的动力系统姿控喷管电磁阀的控制动作指令比对一致,则认为系统极性正确。该装置基于漏磁原理识别对应电磁阀通电和断电过程实现极性测试,没有获取阀芯运动过程中的位置变化量。专利文献公开的一种基于三轴陀螺仪的智能极性测试系统及方法公开号cn111983504a,基于接收不同象限机组内已知的各姿态发动机电磁阀开启产生的磁场强度及角度,输出x轴、y轴和z轴的不同数据。采用人工神经网络根据采集数据计算各个象限机组不同位置方向的电磁阀磁场特征量并制定判据,根据判据判断电磁阀相对空间位置,实现电磁阀极性测试。该方法受电磁噪声影响较大,需要配合增益滤波电路才可以使用,系统复杂度要比较高,并且不能获取阀芯运动过程状态变化。
技术实现要素:
5.本发明的目的是提供一种非接触测量方式实时同步测量多通道姿轨控发动机姿控喷管针形阀位移,从而有效准确获得喷管针形阀极性特性的测试装置。
6.为解决上述技术问题,本发明采用如下技术方案:一种多通道非接触式姿轨控推力矢量系统极性测试装置,极性测试装置包括至少一个姿轨控推力矢量极性测试系统,姿轨控推力矢量极性测试系统包括推力器喷管、阀体和姿轨控伺服驱动器,还包括光电位移传感器、嵌入式计算机、控制器、测试工装、同步控制电路和极性测试软件;测试工装包括光电位移传感器姿态调整装置和推力器喷管联结调整装置;同步控制电路包括多路位移信号同步触发控制器和极性状态指示灯控制器;极性测试软件包括位移数据采集模块、数据处理模块和测量结果显示模块。
7.在上述多通道非接触式姿轨控推力矢量系统极性测试装置中,测试工装包括手持部分、夹紧部分和测试工装定位环;手持部分包括第一半支撑、第二半支撑、极性状态指示灯和测试工装固定衬套,第一半支撑与第二半支撑通过测试工装固定衬套固定连接形成手柄,极性状态指示灯设置在手柄上;夹紧部分包括手动螺旋锁紧机构和夹爪转臂,手动螺旋锁紧机构设置于手柄内部与夹爪转臂活动连接;光电位移传感器固定在测试工装固定衬套上,光电位移传感器测量轴线和测试工装定位环轴线重合;测试工装定位环设置于手柄与推力器喷管之间,使光电位移传感器测量轴线和阀体运动方向共线;夹爪转臂与推力器喷管活动连接。
8.多通道非接触式姿轨控推力矢量系统极性测试装置的测试方法,利用光电位移传感器测量推力器喷管内阀体相对于推力器喷管外圆端面的偏移量,根据偏移量大小确定阀体极性;包括以下步骤:
9.步骤1、利用测试工装将光电位移传感器固联在推力器喷管端面,调节光电位移传感器的姿态,使光电位移传感器测量轴线与推力器喷管中阀体运动方向共线;
10.步骤2、极性测试装置上电,启动极性测试软件,极性测试软件启动后,嵌入式计算
机分别与多路位移信号同步触发控制器和姿轨控伺服驱动器建立通信;
11.步骤3、点击极性测试软件中启动测量按钮,极性测试软件首先向多路位移信号同步触发控制器发送启动位移测量控制信号,触发多路光电位移传感器同步启动位移测量,然后向姿轨控伺服驱动器发送启动阀体运动的控制信号;
12.步骤4、极性测试软件同步接受多路位移测量信号,在软件界面上实时显示多个推力器中阀体的位移测量信号;
13.步骤5、极性测试软件根据极性测试结果,控制测试工装上极性状态指示灯显示对应极性状态,并将测试结果以文件形式存于嵌入式计算机中。
14.在上述多通道非接触式姿轨控推力矢量系统极性测试装置的测试方法中,步骤1的实现包括:
15.步骤1.1、通过测试工装将光电位移传感器和推力器喷管固联;
16.两个半支撑固定形成操作手柄,手柄上装有极性状态显示灯,通过测试工装芯套将手持部分、夹紧部分和光电位移传感器进行整合,实现定位、夹紧和测量一体化;采用对角大力钳结构,手柄作为整个极性测试装置的支撑用于手持安装测试工装,同时作为辅助定心施加轴向力的推杆,使得测试工装通过测试工装定位环与推力器喷管自动对中;手动螺旋锁紧机构利用夹爪转臂将测试工装固联到推力器喷管;
17.步骤1.2、利用测试工装芯套固定光电位移传感器,使得光电位移传感器测量轴线和测试工装定位环轴线重合;
18.步骤1.3、通过调整测试工装定位环实现光电位移传感器测量轴线与推力器喷管中阀体运动方向共线。
19.在上述多通道非接触式姿轨控推力矢量系统极性测试装置的测试方法中,多个推力矢量系统进行极性测量,重复步骤1操作,将多个光电位移传感器与推力器喷管联结,并使得对应的光电位移传感器测量轴线和推力器喷管中阀体运动方向共线。
20.在上述多通道非接触式姿轨控推力矢量系统极性测试装置的测试方法中,步骤2的实现包括:
21.步骤2.1、嵌入式计算机与姿轨控伺服驱动器通过can总线建立通信,并向姿轨控伺服驱动器发送指令控制阀体运动;
22.步骤2.2、极性测试软件与多路位移信号同步触发控制器通过串口建立通信,并向多路位移信号同步触发控制器发送指令,同步触发多路光电位移传感器同步测量阀体位移。
23.在上述多通道非接触式姿轨控推力矢量系统极性测试装置的测试方法中,步骤5的实现包括:
24.步骤5.1、极性测试软件同步接受控制器实时发送各光电位移传感器检测的偏移量测量信号,并对测量信号进行分析、处理、显示和存储;
25.步骤5.2、极性测试软件依据每个光电位移传感器返回的阀体位移值显示极性状态,同时控制测试工装上极性状态指示灯显示相应的极性状态;显示的极性状态和控制信号一致,则极性正常。
26.与现有技术相比,本发明的有益效果:
27.(1)本发明设计创新一种非接触式姿轨控推力矢量系统极性测量装置。该装置结
构稳定、紧凑,可以适用于现场操作空间狭小的测试环境。测试工装采用对角大力钳结构,利用固定芯套将测试工装手持部分、固定部分和测量传感器进行整合,实现安装过程中自定位、夹紧一体化。
28.(2)本发明可以对多个推力矢量系统的阀体位移信号进行同步测量。该装置通过自行设计的高精度同步控制器可以同步触发多路光电位移传感器同步启动位移测量,同步精度优于0.1ms。高精度同步测量使得该装置不仅可以检验单个推力矢量系统的极性是否符合控制指令要求,还可以检验同一时刻多个推力矢量系统的极性状态分布是否符合规定要求。
29.(3)本发明可以实现对推力矢量系统阀体运动过程检测。该装置利用光电位移传感器实时测量推力矢量系统阀体位移检测推理矢量系统极性,使得该装置不仅可以检测推力矢量系统阀体的最终极性状态,还可以以图形的形式直观反映推力矢量系统阀体的运动过程。
30.(4)本发明装置测试环境适应强。同基于喷管内气压测试极性的装置相比,由于该装置结构紧凑、测量时间短、采用测量阀体位移的方式检测极性,使得该装置不仅可以用于推力矢量系统出厂时极性检测,还可以用于系统总装联测的单元测试。
附图说明
31.图1为本发明一个实施例姿轨控推力矢量系统极性测试装置原理图,其中:1-1为光电位移传感器;
32.图2为本发明一个实施例单个姿轨控推力矢量极性测试原理图,其中2-1为测试工装,2-2为推力器喷管外圆端面,2-3为推力器喷管,2-4为阀体,2-5为光电位移传感器测量轴线;
33.图3为本发明一个实施例单个姿轨控推力矢量极性测试工装结构,其中3-1为第一半支撑,3-1
′
为第二半支撑,3-2手动螺旋锁紧机构,3-3为极性状态指示灯,3-4为测试工装固定衬套,3-5测试工装定位环,3-6为夹爪转臂,1-1为光电位移传感器,2-3为推力器喷管,2-4为阀体;
34.图4为本发明一个实施例极性状态指示灯驱动电路图。
具体实施方式
35.下面将结合本发明实施例对本发明实施例中的技术方案进行清楚、完整地描述,显然,所描述的实施例仅仅是本发明一部分实施例,而不是全部的实施例。基于本发明中的实施例,本领域普通技术人员在没有作出创造性劳动的前提下所获得的所有其他实施例,都属于本发明保护的范围。
36.需要说明的是,在不冲突的情况下,本发明中的实施例及实施例中的特征可以相互组合。
37.下面结合具体实施例对本发明作进一步说明,但不作为本发明的限定。
38.本实施例提供一种多通道非接触式姿轨控推力矢量系统极性测试装置及测试方法,通过光电位移传感器测量推力器喷管内阀体相对于喷管喉部的实时位移,根据所测得的阀体相对位移判断姿轨控推力矢量系统极性是否和控制指令一致,从而实现姿轨控推力
矢量系统极性测量,本装置可以对姿轨控推力矢量系统中多个推力器喷管阀体极性进行同步测量,进而对多个推力器喷管阀体的极性分布是否和控制指令一致进行测量。
39.本实施例是通过以下技术方案来实现的,一种多通道非接触式姿轨控推力矢量系统极性测试装置,包括至少一个姿轨控推力矢量极性测试系统,通过光电位移传感器测量喷管内阀体动态位移实现极性测量。姿轨控推力矢量极性测试系统包括推力器喷管、阀体、姿轨控伺服驱动器、光电位移传感器、嵌入式计算机、控制器、测试工装、同步控制电路、极性测试软件。光电位移传感器实现非接触获取阀体位移信号,测试工装包括光电位移传感器姿态调整装置、推力器喷管联结调整装置;同步控制电路包括多路位移信号同步触发控制器和极性状态指示灯控制器;极性测试软件包括位移数据采集模块、数据处理模块和测量结果显示模块。
40.多通道非接触式姿轨控推力矢量系统极性测试装置的测试方法具体包括以下步骤:
41.s1,光电位移传感器固定在测试工装中,调节光电位移传感器的姿态,使光电位移传感器测量轴线和推力器喷管中阀体运动方向共线。
42.s2,极性测试装置上电,启动极性测试软件,极性测试软件启动后,嵌入式计算机分别与多路位移信号同步触发控制器和姿控伺服驱动器建立通信。
43.s3,点击极性测试软件中启动测量按钮,极性测试软件首先向多路位移信号同步触发控制器发送启动位移测量控制信号,触发多路光电位移传感器同步启动测量,然后向姿控伺服驱动器发送启动阀体运动的控制信号。
44.s4,极性测试软件同步接受多路位移信号,在软件界面上实时显示多个推力器中阀体的位移信号。
45.s5,极性测试软件根据极性测试结果,控制测试工装上极性状态指示灯显示对应极性状态,并将测试结果以文件形式存在计算机中,供事后查阅。
46.并且,通过步骤s1实现光电位移传感和推力器喷管可靠联结,并使得光电位移传感器测量轴线和推力器喷管中阀体运动方向共线。测试工装是为联结光电位移传感器和推力器喷管而专门设计制作的一个联结件。测试工装的结构如图3所示。测试工装通过两个半支撑固定形成操作手柄,利用测试工装固定衬套将手持部分、夹紧部分和测量传感器进行整合,实现定位、夹紧和测量一体化。由于现场可操作空间小,设计利用矩形对角最大空间特点,采用对角大力钳结构设计,手持部分既作为整个测试装置的支撑,又作为辅助定心施加轴向力的推杆,十字形架构结构稳定、紧凑,所有安装及测量工作均在限定空间完成。通过旋转测试工装上手动螺旋锁紧机构的手柄,可控制夹爪转臂的开合,实现仪器在测量工位的圆锥外壁锁紧动作。手柄上装有极性状态指示灯,根据设置方式显示阀体运动状态,尾部通过设置的出线口将极性状态指示灯信号线引出。
47.并且,如果有多个推力矢量系统需要进行极性测量,重复s1操作,将多个光电位移传感器和推力器喷管联结,并使得对应的光电位移传感器测量轴线和推力器喷管中阀体运动方向共线。
48.并且,步骤s2中极性测试装置上电后,嵌入式计算机和推力器喷管中姿轨控伺服驱动器通过can总线建立通信,在后续极性测试中通过向姿轨控伺服驱动器发送指令控制阀体运动。极性测试软件和多路位移信号同步触发控制器通过串口通信建立通信,在后续
极性测试中,通过向多路位移信号同步触发控制器发送指令同步触发多路光电位移传感器同步测量阀体位移。当数据通信正常时,测试工装上的极性状态显示灯红绿交替闪烁,否则极性状态显示灯常亮,表示通信中断,排除错误。
49.并且,步骤s3中点击极性测试软件界面启动测量按钮,极性测试软件向多路位移信号同步触发控制器发送启动位移测量控制信号,然后向姿轨控伺服驱动器发送启动阀体运动的控制信号。多路位移信号同步触发控制器接收到启动位移测量信号后触发光电位移传感器启动位移测量。
50.并且,步骤s4中极性测试软件同步接受多路光电位移传感器获取的阀体实时位移信号,在软件界面实时显示多路位移信号值,可以直观显示每个阀体的运动过程。
51.多通道非接触式姿轨控推力矢量系统极性测试装置极性测试原理如图1所示。每个光电位移传感器1-1测量对应通道的姿轨控推力矢量系统极性。极性测试软件发送启动测量指令给控制器,控制器发送同步测量指令给多路位移信号同步触发控制器,同步触发多个光电位移传感器开始测量阀体位移。控制器同步发送阀体运动控制指令给姿轨控伺服驱动器,驱动阀体按指令方式运动。光电位移传感器的测量数据同步传输给控制器,控制器将测量数据打上时间戳后,传输给嵌入式计算机,极性测量软件完成数据经处理后,将每个通道的实时位移最终的极性状态显示在软件界面上,同时极性测量软件根据极性状态控制测试工装上的极性状态指示灯显示对应的状态。
52.单个姿轨控推力矢量极性测试系统极性测试原理如图2所示。图2中左边圆柱体为测试工装2-1,通过测试工装2-1将光电位移传感器1-1和推力器喷管2-3固联。光电位移传感器1-1光电位移传感器测量轴线2-5和推力器喷管2-3中阀体2-4运动方向共线。当阀体2-4沿光电位移传感器测量轴线2-5运动时,光电位移传感器1-1实时检测阀体2-4相对于推力器喷管2-3推力器喷管外圆端面2-2的偏移量l,根据偏移量l大小确定阀体2-4极性。
53.图3给出了对应于图2中测试工装的整体结构及测试工装固联在推力器喷管上的情形。测试工装包括手持部分、夹紧部分和测试工装定位环3-5;手持部分包括第一半支撑3-1、第二半支撑3-1
′
、极性状态指示灯3-3和测试工装固定衬套3-4,第一半支撑3-1与第二半支撑3-1
′
通过测试工装固定衬套3-4固定连接形成手柄,极性状态指示灯3-3设置在手柄上;夹紧部分包括手动螺旋锁紧机构3-2和夹爪转臂3-6,手动螺旋锁紧机构3-2设置于手柄内部与夹爪转臂3-6活动连接;光电位移传感器1-1固定在测试工装固定衬套3-4上,光电位移传感器1-1测量轴线和测试工装定位环3-5轴线重合;测试工装定位环3-5设置于手柄与推力器喷管2-3之间,使光电位移传感器1-1测量轴线和阀体2-4运动方向共线;夹爪转臂3-6与推力器喷管2-3活动连接。第一半支撑3-1和第二半支撑3-1
′
作为整个极性测试装置的支撑用于手持安装测试工装,两个半支撑同时作为在狭小空间内辅助定心施加轴向力的推杆,使得测试工装2-1通过测试工装定位环3-5与推力器喷管2-3自动对中。手动螺旋锁紧机构3-2利用夹爪转臂3-6将测试工装固联到推力器喷管2-3上。测试工装固定衬套3-4用于固定光电位移传感器1-1,并使得光电位移传感器测量轴线2-5和测试工装定位环3-5轴线重合。测试工装定位环3-5实现光电位移传感器测量轴线2-5和阀体2-4运动方向共线。整个测试工装结构紧凑,便于使用。测试工装上的极性状态指示灯3-3受极性测试软件控制,显示对应通道的极性状态。
54.极性测试装置电子部分实现多路位移测量信号同步采集、多路测量信号传输、阀
芯运动控制指令发送、测试数据显示以及阀芯极性状态光电直观显示。电子部分同步控制器接收嵌入式计算机发送的启动测量指令后,将启动指令转发给同步触发器。多路位移信号同步触发控制器以固定的频率同步触发多个光电位移传感器工作,光电位移传感器测量数据发送给控制器。在触发传感器工作同时,多路位移信号同步触发控制器采用can通讯方式发送阀体控制指令给姿轨控伺服驱动器,控制阀体运动。控制器实时接收每一个光电位移传感器测量值,然后实时发送给嵌入式计算机极性测试软件,极性测试软件对测量值分析、处理、显示和存储。控制器依据实时测量的阀体位移控制阀体极性状态显示灯闪烁。极性状态指示灯驱动电路如图4所示。
55.具体实施时,多通道非接触式姿轨控推力矢量系统极性测试装置的测试方法如下:
56.1)通过逆时针拧松测试工装上手动螺旋锁紧机构调节旋钮,使夹爪转臂头部松开,将测试工装两半支撑作为手柄,手握手柄,沿推力器喷管轴线方向施加一定推力,将测试工装推入推力器喷管,稳住手柄,顺时针平稳拧紧旋钮,将测试工装的夹爪转臂与推力器喷管固联;反之为测试工装拆卸过程。
57.2)极性测试装置接通电源,启动极性测试软件,极性测试装置进入等待测量状态。这时,测试工装上的极性状态指示灯交替闪烁。极性测试软件启动后,会自动根据检测极性测试软件和多路位移信号同步触发控制器以及姿轨控伺服驱动器通讯是否正常。如通讯中断,则需检测通信线缆联结及多路位移信号同步触发控制器供电是否正常。如异常,根据软件界面提示,排查错误,直至通讯建立正常。
58.3)通过姿轨控伺服驱动器将推力器喷管内阀体驱动至阀体移动行程中点位置,点击极性测试软件界面上“原点校准”按钮,将该位置设置为光电位移传感器测量位移的零位,即处于该位置处阀体对应的输出位移量为零。
59.4)点击“开始测量”按钮,启动极性测量,分别发送光电位移传感器同步触发信号和阀体运动控制信号。在极性测量过程中,极性测试软件依据每个光电位移传感器返回的阀体位移值显示极性状态,同时控制测试工装上极性状态指示灯显示相应的极性状态。如果显示的极性状态和控制信号一致,则极性正常。
60.5)测量过程中,“开始测量”按钮会变成“停止测量”。当测量结束时,点击“停止测量”按钮。点击“停止按钮”后,极性测量过程的所有位移测量数据以文件的形式存储在本地硬盘,供事后数据分析显示。
61.实施例1:
62.根据本实施例所设计制作的姿轨控推力矢量系统极性测试装置,对4路姿轨控推力矢量极性测试系统进行了极性测试实验。实验过程和测试结果如下:
63.(1)将四个测试工装固联到对应的姿轨控推力矢量系统推力器喷管,确保测试工装标号和姿轨控推力矢量系统推力器喷管标号一一对应。
64.(2)启动极性测试软件,首先进行点击“原点校准”按钮,进行阀体零位设置。然后点击“开始测量”启动极性测量,此时测试工装上所有指示灯为黄色,示意所有阀体处在行程中间位置。接着控制阀体开始移动,此时2号、4号通道指示灯为绿色,1号、3号通道指示灯为红色,显示的极性状态和控制装置一致。最后使阀体反方向移动,此时2号、4号通道变为红色,1号、3号变为绿色,显示的极性状态和控制装置一致.表1给出了四路位移信号状态测
试结果。
65.表1.四路位移信号状态测试结果
[0066][0067]
综上所述,针对现有姿轨控推力矢量系统极性测试装置结构复杂,难以同步在线测量多个推力矢量系统极性的问题,本实施例提供了多通道非接触式姿轨控推力矢量系统极性测试装置及方法,通过设计的测试工装实现光电位移传感器测量轴线和推力矢量系统位移方向自动对中,同步获取多路光电位移传感器测量阀体的实时位移,进而依据阀体位移确定推力矢量系统极性状态。该装置不仅可以验证推力矢量系统极性是否和控制指令一致,同时可以记录阀体运动过程,从而可以检测阀体运动性能。
[0068]
以上仅为本发明较佳的实施例,并非因此限制本发明的实施方式及保护范围,对于本领域技术人员而言,应当能够意识到凡运用本发明说明书内容所作出的等同替换和显而易见的变化所得到的方案,均应当包含在本发明的保护范围内。
再多了解一些
本文用于企业家、创业者技术爱好者查询,结果仅供参考。