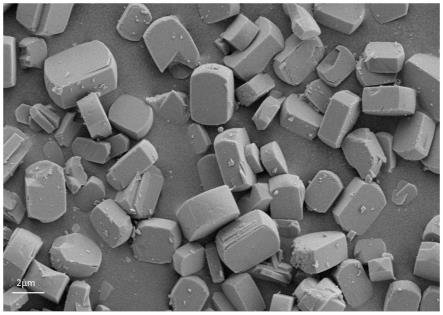
1.本发明涉及催化剂领域,具体地说涉及一种煤层气部分氧化制甲醇催化剂及其制备方法与应用。
背景技术:
2.煤层气是一种产于煤层中的、与煤共伴生的以甲烷为主要成分的天然气资源。煤矿开采过程普遍存在煤层气(主要为甲烷浓度低于30%(体积百分比)的低浓度煤层气)利用率不高、直接排空等问题。这造成了大量资源的浪费,同时加剧了温室效应和环境压力,不符合当下“碳达峰、碳中和”的战略目标。虽然甲烷在大气中的寿命比二氧化碳短得多,但出现的问题是,甲烷是一种比二氧化碳更有效的温室气体,其危害性约为二氧化碳的 28-36倍。此外,观测到的地球温度的持续上升也会显著导致全球甲烷排放的增加,从而进一步加剧气候问题。因此,有必要将甲烷转化为一种有用的、更环保的化学物质,而不是仅仅燃烧生成二氧化碳。甲醇是一种用途极多的化学平台原料,便于运输,可以用于制氢向更清洁的能源进行转化,具有很高的经济价值。利用催化技术,采用低浓度煤层气在低温下制甲醇可有效的提高煤矿中煤层气的经济效益同时减少对环境的污染。
3.以沸石为载体负载活性金属的催化剂的开发是获得高活性甲烷制甲醇反应催化剂的重要技术手段。现阶段国内外的研究主要集中在商业沸石催化剂的开发,但目前商业沸石价格高昂,且在低温下煤层气甲烷部分氧化制甲醇的甲烷转化率不高,甲醇选择性并不理想且易于失活。
4.因此,为了提高低温低浓度下甲烷制甲醇的效率,采用铜铁活性金属封装在以凹凸棒石衍生的类沸石结构中的催化剂来模拟自然界中生物酶中的铜铁活性位点,以获得较高的甲烷转化率和甲醇选择性和长时间的催化寿命。
技术实现要素:
5.本发明所要解决的技术问题是提供一种煤层气部分氧化制甲醇催化剂及其制备方法与应用。所述催化剂为一种具有高活性高选择性高稳定性的煤层气部分氧化制甲醇催化剂。
6.为了解决上述技术问题,本发明采用如下技术方案:一种煤层气部分氧化制甲醇催化剂,包括活性金属和封装活性金属的凹凸棒石基沸石载体,所述活性金属包括铜和铁;其中,以催化剂总重量计,铜的含量为1~5wt%,铁的含量为1~5wt%。例如,以催化剂总重量计,铜的含量1wt%、1.1wt%、1.2wt%、1.3wt%、1.4wt%、1.5wt%、1.6wt%、1.7wt%、1.8wt%、 1.9wt%、2wt%、2.1wt%、2.2wt%、2.3wt%、2.4wt%、2.5wt%、2.6wt%、2.7wt%、2.8wt%、 2.9wt%、3wt%、3.1wt%、3.2wt%、3.3wt%、3.4wt%、3.5wt%、3.6wt%、3.7wt%、3.8wt%、 3.9wt%、4wt%、4.1wt%、4.2wt%、4.3wt%、4.4wt%、4.5wt%、4.6wt%、4.7wt%、4.8wt%、 4.9wt%或5wt%。
7.例如,以催化剂总重量计,铁的含量1wt%、1.1wt%、1.2wt%、1.3wt%、1.4wt%、
1.5wt%、 1.6wt%、1.7wt%、1.8wt%、1.9wt%、2wt%、2.1wt%、2.2wt%、2.3wt%、2.4wt%、2.5wt%、 2.6wt%、2.7wt%、2.8wt%、2.9wt%、3wt%、3.1wt%、3.2wt%、3.3wt%、3.4wt%、3.5wt%、 3.6wt%、3.7wt%、3.8wt%、3.9wt%、4wt%、4.1wt%、4.2wt%、4.3wt%、4.4wt%、4.5wt%、 4.6wt%、4.7wt%、4.8wt%、4.9wt%或5wt%。
8.凹凸棒石基沸石分子筛作为载体。铜和铁金属封装在载体上。
9.进一步地,所述催化剂由活性金属和封装活性金属的凹凸棒石基沸石载体组成,所述活性金属为铜和铁。
10.进一步地,余量为凹凸棒石基沸石载体。
11.进一步地,活性金属铜和铁是封装包裹在凹凸棒石基沸石载体骨架内。
12.进一步地,所制备的催化剂中铜和铁活性组分是封装包裹在凹凸棒石基硅铝源合成的具有mfi拓扑结构的微孔沸石载体骨架内。
13.过渡金属铜和铁在低温下部分氧化甲烷制甲醇中都具有较好的活性。铁能够快速活化甲烷,断裂一个碳氢键,形成甲基自由基,与铜促进产生的羟基自由基迅速结合,形成甲醇。
14.凹凸棒石粘土是一种具有链层状结构的含水富镁铝硅酸盐粘土矿物,是天然的硅源、铝源。以凹凸棒石为硅铝源合成沸石分子筛,不但可以保留凹凸棒石的高水热稳定性,而且可以进一步对它的表面形貌和性能、孔道结构进行优化、裁剪。将活性金属铜铁封装在其骨架中,可以提供类似生物酶的配位环境来提高催化剂对甲烷转化的活性和对甲醇的选择性,同时因为活性金属在骨架中,不易因为积碳等原因失活,因此具有很高的使用寿命。
15.进一步地,铜的含量为1~5wt%,铁的含量为1~5wt%。
16.本发明还提供上述煤层气部分氧化制甲醇催化剂在催化煤层气部分氧化制甲醇中的应用。
17.进一步地,如上任一项所述的催化剂在催化煤层气部分氧化制甲醇中的应用,催化剂应用于煤层气部分氧化制甲醇,反应条件为:催化剂用量0.1~0.5g,煤层气中甲烷浓度为3~30%,气体进料空速为960~6000ml
·
h-1
·gcat-1
,水蒸气空速为1440~9000ml
·
h-1
·gcat-1
,反应温度为180℃~260℃。
18.进一步地,针对低浓度(甲烷浓度低于30体积%)(特别是爆炸范围(爆炸范围是甲烷浓度高于15体积%))煤层气,能够实现煤层气部分氧化制甲醇,煤层气中甲烷转化率大于 70%、甲醇选择性高于80%,使用寿命高于200h。
19.进一步地,催化低温煤层气制甲醇的反应条件为:催化剂用量0.1~0.5g,进料中甲烷浓度为3%~30%(体积百分比),气体进料空速为960~6000ml
·
h-1
·gcat-1
,反应温度为50~280℃。在实施本发明的过程中,发明人发现,此反应条件下,可以实现甲烷转化率超过70%,甲醇的选择性高于80%,使用寿命高于200h。
20.本发明还提供上述煤层气部分氧化制甲醇催化剂的制备方法,包括以下步骤:以经无机酸处理后的凹凸棒石为硅铝源,洗涤、离心、干燥、研磨后通过溶胶凝胶法将铜、铁活性金属负载在硅铝源上,再将负载后硅铝源干燥、研磨、煅烧后在碱性条件下加入模板剂充分混合后再水热结晶,制得所述铜-铁@凹凸棒石基沸石分子筛催化剂。
21.在本发明的一个实施方案中,上述煤层气部分氧化制甲醇催化剂的制备方法,包括如下步骤:(1)将凹凸棒石黏土与无机酸混合,酸化处理后获得硅铝源;(2)通过溶胶凝胶
法将活性金属前体盐负载在所述的硅铝源上,进行干燥、研磨和煅烧,得到负载金属后的凹凸棒石基载体硅铝源;(3)将负载金属后的凹凸棒石基载体硅铝源与模板剂在碱性条件下混合,再进行水热结晶处理,然后再经离心、洗涤、干燥、研磨和煅烧后得所述催化剂。
22.进一步地,步骤(1)中,所述的无机酸为盐酸和/或硫酸,所述无机酸的浓度为3.5~7mol/l。
23.进一步地,步骤(1)中,所述的酸化处理为在120~180℃条件下水热处理12~18h。
24.进一步地,步骤(2)中,所述活性金属前体盐为铜的前驱体盐和铁的前驱体盐。
25.进一步地,步骤(2)中,所述的溶胶凝胶法包括加入螯合剂,所述活性金属前体盐中的金属离子与螯合剂摩尔比为1:1~2。所述螯合剂为柠檬酸。
26.进一步地,步骤(2)中,所述煅烧为以2~4℃/min的升温速率从室温升至500~700℃,然后恒温4~8h。
27.进一步地,步骤(3)中,碱性条件的ph为10~12。
28.进一步地,步骤(3)中,所述碱性条件通过氢氧化钠水溶液形成。
29.进一步地,步骤(3)中,所述混合的时间为4~8h。
30.进一步地,步骤(3)中,负载金属后的凹凸棒石基载体硅铝源与模板剂质量比为 1:0.125~0.25。例如,负载金属后的凹凸棒石基载体硅铝源与模板剂质量比为1:0.125、1:0.15、 1:0.175、1:0.2、1:0.225或1:0.25。
31.进一步地,步骤(3)中,所述的水热结晶处理为在120~180℃下水热结晶老化12~18h。
32.进一步地,步骤(3)中,所述的活性金属前体盐中的金属离子与螯合剂摩尔比为1:1~2。
33.进一步地,步骤(3)中,所述的模板剂为四丙基氢氧化铵。
34.进一步地,所述铜的前驱体盐为三水合硝酸铜,铁的前驱体盐为九水合硝酸铁。
35.进一步地,所述的催化剂,其具体制备过程为:凹凸棒石与无机酸酸混合后经超声震荡均匀后放置于聚四氟乙烯内衬的水热反应釜中进行水热老化处理,充分过滤洗涤体系中杂原子后,即得凹凸棒石衍生硅铝源。将硅铝源加入到含有柠檬酸的铜、铁金属的凝胶体系中,然后搅拌均匀,经老化、蒸发、洗涤过滤、干燥、研磨筛分处理后在空气气氛中进行煅烧,将煅烧后粉末在碱性条件充分混合一段时间,再加入模板剂,放入水热釜水热结晶老化合成铜-铁@凹凸棒石基沸石分子筛。再经洗涤、离心、干燥、研磨后在空气气氛下进行煅烧。
36.进一步地,凹凸棒石硅铝源合成条件为无机酸为盐酸、硫酸或混合,浓度为3.5~7mol/l,在120~180℃条件下水热处理12~18h。
37.进一步地,封装活性金属形成沸石分子筛的合成条件为在ph=10~12、在氢氧化钠水溶液中混合时间为4~8h,硅铝源与模板剂摩尔比为1:0.05~0.33的条件下,在120~180℃下水热结晶老化12~18h。
38.进一步地,所述的负载金属离子与螯合剂摩尔比为1:1~2。
39.进一步地,老化处理为在60~120℃条件下,先搅拌5~8h,再静置10~15h。
40.进一步地,煅烧处理为以2~4℃/min的升温速率从室温升至500~700℃,然后恒温4~8 h。
41.进一步地,搅拌均匀为在30~60℃水浴条件下磁力搅拌4~6h。
42.进一步地,蒸发处理为在95~105℃条件下,将水蒸发去除。
43.进一步地,洗涤过滤处理为用去离子水洗涤过滤3~6次。
44.进一步地,干燥处理为在常压、100~105℃条件下干燥8~12h。
45.进一步地,研磨筛分处理为用研钵将干燥后的固体研碎,并筛分出直径为0.18~0.25mm 的颗粒。
46.本发明的有益效果体现在:
47.1.本发明铜-铁@凹凸棒石基沸石分子筛催化剂应用在催化煤层气制甲醇时,可实现甲烷转化率超过70%,甲醇选择性达到80%,使用寿命≥200h,且具有高活性、高稳定性、价格低廉的优点,满足煤层气制甲醇的工业化要求。
48.2.本发明铜-铁@凹凸棒石基沸石分子筛催化剂利用凹凸棒石基载体作为封装骨架来模拟生物酶中的配位环境,将铜铁活性位点封装在其中模拟实现自然界中生物酶对甲烷部分氧化制甲醇的高活性及高选择性。
49.3.本发明相对于其他铜铁负载沸石催化剂,利用高热稳定性的凹凸棒石为硅源合成有序介孔分子筛作载体,降低了催化剂的生产成本。
50.4.本发明应用于煤层气制甲醇反应中,可明显降低反应所需要的温度,在低浓度时同样具有较好的转化率,具有很好的工业化前景。
附图说明
51.图1为实施例1制得的催化剂的粉末x射线衍射图案,即封装1wt%cu和1wt%fe的催化剂的粉末x射线衍射图案,证实了确有mfi结构,且观察不到cufe的信号;
52.图2为实施例1制得的催化剂的扫描电镜图像,即封装1wt%cu和1wt%fe的催化剂的扫描电镜图像,可以观察到表面较为光滑;
53.图3为实施例1制得的催化剂的透射电镜图像,即封装1wt%cu和1wt%fe的催化剂的透射电镜图像,可以观察到内部具有活性金属黑色颗粒。
具体实施方式
54.下面结合实施例和附图对本发明作进一步描述。但以下的实施例仅限于解释本发明,本发明的保护范围应包括权利要求的全部内容,而且通过以下实施例的叙述,本领域的技术人员是可以完全实现本发明权利要求的全部内容。
55.下列实施例所使用的部分试剂及仪器如下:
56.凹凸棒石黏土1000目,来自江苏盱眙
57.管式炉合肥科晶otf-1200x型)
58.烘箱(上海博迅bzf-50型)
59.磁力搅拌器(北京大龙兴创ms-h-pro型)
60.微型固定床反应器(上海岩征yzupbr型)
61.以下实施例所使用的各种原料,如未作特别说明,均为本领域公知的市售产品。所述方法如无特殊说明均为常规方法。
62.实施例1
63.本实施例制备的铜-铁@凹凸棒石基沸石分子筛催化剂中的活性成分铜(cu)含量
为1 wt%,铁(fe)的含量为1wt%,剩余组分为凹凸棒石基沸石分子筛载体,制备方法如下:称取20g凹凸棒石黏土通过超声震荡均匀分散在120ml 3.5mol/l盐酸溶液中形成悬浊液i,将悬浊液i移入200ml聚四氟乙烯内衬的水热釜中,在180℃下处理12h后冷却至室温,使用去离子水过滤洗涤至中性后,在100℃烘箱中干燥12h,使用研钵碾碎后即得凹凸棒石基硅铝源。称取0.1939g三水合硝酸铜(cu(no3)2·
3h2o)、0.3689g九水合硝酸铁 (fe(no3)3·
9h2o)完全溶解于25ml去离子水中,形成溶液i;称取0.7686g柠檬酸完全溶解于25ml去离子水中,形成溶液ii,将溶液ii缓慢倒入溶液i,搅拌形成溶胶后,加入5g 凹凸棒石基硅铝源,30℃搅拌4h均匀后,经60℃水浴老化8h、95℃蒸发4h、洗涤过滤3 次、105℃干燥8h、研磨筛分处理后得到直径0.18mm的负载活性金属的凹凸棒石基硅铝源粉末。将所得粉末放在管式炉中,通入空气气氛,从室温以4℃/min的升温速率升至700℃,恒温煅烧4h后冷却至室温,所得粉末均匀分散在20ml去离子水中形成悬浊液ii;称取2.5 g四丙基氢氧化铵溶液(tpaoh,浓度为25wt%)在40℃下加入10ml去离子水中形成溶液ⅲ。将悬浊液ii逐滴移入溶液ⅲ中,充分搅拌后,逐滴加入0.1mol/l氢氧化钠溶液调节 ph至11后搅拌8h形成悬浊液iii。将悬浊液iii移入200ml聚四氟乙烯内衬的水热釜中,在120℃下水热结晶18h后冷却至室温,离心、水洗、乙醇洗至中性,在105℃烘箱中干燥12h,研磨后在700℃下流动空气氛围中煅烧4h移除模板剂后,即得铜-铁@凹凸棒石基沸石分子筛催化剂,编号1#。
64.在甲烷浓度为3%(体积浓度,余为氮气),反应温度为200℃,甲烷进料为8ml/min,水蒸汽进料为12ml/min,催化剂的用量为0.3g的反应条件下,在微型固定床反应器上对其催化性能进行了测试。先通入氮气吹扫设备30分钟,再将固定床反应器升温至反应温度,通入ch4后再通过泵将水泵入固定床中的预热混合室,形成水蒸气与甲烷混合气通入反应管,并通过gc装置检测反应后产物。其甲烷转化率为85.7%,甲醇选择性为83.7%,使用寿命高于200h。
65.图1为实施例1制得的催化剂的粉末x射线衍射图案,即封装1wt%cu和1wt%fe的催化剂的粉末x射线衍射图案,证实了催化剂确有mfi拓扑结构,且观察不到cufe的信号。
66.图2为实施例1制得的催化剂的扫描电镜图像,即封装1wt%cu和1wt%fe的催化剂的扫描电镜图像,可以观察到催化剂表面较为光滑。图3为实施例1制得的催化剂的透射电镜图像,即封装1wt%cu和1wt%fe的催化剂的透射电镜图像,可以观察到催化剂内部具有活性金属黑色颗粒。图2和图3表明活性金属铜和铁是封装包裹在凹凸棒石基沸石载体骨架内。
67.实施例2
68.本实施例制备的铜-铁@凹凸棒石基沸石分子筛催化剂中的活性成分铜(cu)含量为5 wt%,铁(fe)的含量为5wt%,剩余组分为凹凸棒石基沸石分子筛载体,制备方法如下:称取20g凹凸棒石黏土通过超声震荡均匀分散在120ml 7mol/l硫酸溶液中形成悬浊液i,将悬浊液i移入200ml聚四氟乙烯内衬的水热釜中,在120℃下处理12h后冷却至室温,使用去离子水过滤洗涤至中性后,在105℃烘箱中干燥12h,使用研钵碾碎后即得凹凸棒石基硅铝源。称取1.056g三水合硝酸铜(cu(no3)2·
3h2o)、2.0093g九水合硝酸铁 (fe(no3)3·
9h2o)完全溶解于25ml去离子水中,形成溶液i;称取2.0903g柠檬酸完全溶解于25ml去离子水中,形成溶液ⅱ,将溶液ⅱ缓慢倒入溶液i,不断搅拌形成溶胶后,加入5g凹凸棒石基硅铝源,50℃搅拌6h均匀后,经80℃水浴老化6h、105℃蒸发4h、洗涤过滤6次、105℃干燥8h、研磨筛分
处理后得到0.2mm直径的负载活性金属的凹凸棒石基硅铝源粉末。将所得粉末放在管式炉中,通入空气气氛,从室温以2℃/min的升温速率升至500℃,恒温煅烧8h后冷却至室温,所得粉末均匀分散在20ml去离子水中形成悬浊液 ii;称取5g四丙基氢氧化铵溶液(tpaoh,浓度为25wt%)在40℃下加入10ml去离子水中形成溶液ⅲ。将悬浊液ii逐滴移入溶液ⅲ中,充分搅拌后,逐滴加入0.1mol/l氢氧化钠溶液调节ph至12后搅拌6h形成悬浊液iii。将悬浊液iii移入200ml聚四氟乙烯内衬的水热釜中,在180℃下水热结晶18h后冷却至室温,离心、水洗、乙醇洗至中性,在105℃烘箱中干燥12h,研磨后在700℃下流动空气氛围中煅烧4h移除模板剂后,即得铜-铁@凹凸棒石基沸石分子筛催化剂,编号2#。
69.在甲烷浓度为3%(体积浓度,余为氮气),反应温度为180℃,甲烷进料为6ml/min,水蒸汽进料为9ml/min,催化剂的用量为0.1g的反应条件下,在微型固定床反应器上对其催化性能进行了测试。先通入氮气吹扫设备30分钟,再将固定床反应器升温至反应温度,通入 ch4后再通过泵将水泵入固定床中的预热混合室,形成水蒸气与甲烷混合气通入反应管,并通过gc装置检测反应后产物。其甲烷转化率为78.7%,甲醇选择性为88.5%,使用寿命高于200h。
70.实施例3
71.本实施例制备的铜-铁@凹凸棒石基沸石分子筛催化剂中的活性成分铜(cu)含量为5 wt%,铁(fe)的含量为1wt%,剩余组分为凹凸棒石基沸石分子筛载体,制备方法如下:称取20g凹凸棒石黏土通过超声震荡均匀分散在120ml 3.5mol/l盐酸和3.5mol/l硫酸混合后溶液中形成悬浊液i,将悬浊液i移入200ml聚四氟乙烯内衬的水热釜中,在180℃下处理18h后冷却至室温,使用去离子水过滤洗涤至中性后,在105℃烘箱中干燥12h,使用研钵碾碎后即得凹凸棒石基硅铝源。称取1.011g三水合硝酸铜(cu(no3)2·
3h2o)、0.3847 g九水合硝酸铁(fe(no3)3·
9h2o)完全溶解于25ml去离子水中,形成溶液i;称取1.2007g 柠檬酸完全溶解于25ml去离子水中,形成溶液ⅱ,将溶液ⅱ缓慢倒入溶液i,不断搅拌形成溶胶后,加入5g凹凸棒石基硅铝源,30℃搅拌4h均匀后,经70℃水浴老化6h、100℃蒸发4h、洗涤过滤6次、100℃干燥8h、研磨筛分处理后得到0.25mm直径的负载活性金属的凹凸棒石基硅铝源粉末。将所得粉末放在管式炉中,通入空气气氛,从室温以3℃/min 的升温速率升至700℃,恒温煅烧4h后冷却至室温,所得粉末均匀分散在20ml去离子水中形成悬浊液ii;称取2.5g四丙基氢氧化铵溶液(tpaoh,浓度为25wt%)在40℃下加入25ml去离子水中形成溶液ⅲ。将悬浊液ii逐滴移入溶液ⅲ中,充分搅拌后,逐滴加入 0.1mol/l氢氧化钠溶液调节ph至10后搅拌4h形成悬浊液iii。将悬浊液iii移入200ml 聚四氟乙烯内衬的水热釜中,在180℃下水热结晶12h后冷却至室温,离心、水洗、乙醇洗至中性,在105℃烘箱中干燥12h,研磨后在700℃下流动空气氛围中煅烧4h移除模板剂后,即得铜-铁@凹凸棒石基沸石分子筛催化剂,编号3#。
72.在甲烷浓度为30%(体积浓度,余为氮气),反应温度为260℃,甲烷进料为10ml/min,水蒸汽进料为15ml/min,催化剂的用量为0.5g的反应条件下,在微型固定床反应器上对其催化性能进行了测试。先通入氮气吹扫设备30分钟,再将固定床反应器升温至反应温度,通入ch4后再通过泵将水泵入固定床中的预热混合室,形成水蒸气与甲烷混合气通入反应管,并通过gc装置检测反应后产物。其甲烷转化率为72.3%,甲醇选择性为84.1%,使用寿命高于200h。
73.实施例4
74.本实施例制备的铜-铁@凹凸棒石基沸石分子筛催化剂中的活性成分铜(cu)含量为1 wt%,铁(fe)的含量为5wt%,剩余组分为凹凸棒石基沸石分子筛载体,制备方法如下:称取20g凹凸棒石黏土通过超声震荡均匀分散在120ml 3.5mol/l盐酸溶液中形成悬浊液 i,将悬浊液i移入200ml聚四氟乙烯内衬的水热釜中,在180℃下处理18h后冷却至室温,使用去离子水过滤洗涤至中性后,在105℃烘箱中干燥12h,使用研钵碾碎后即得凹凸棒石基硅铝源。称取0.2022g三水合硝酸铜(cu(no3)2·
3h2o)、1.9327g九水合硝酸铁 (fe(no3)3·
9h2o)完全溶解于25ml去离子水中,形成悬浊液i;称取2.1105g柠檬酸完全溶解于25ml去离子水中,形成溶液ⅱ,将溶液ⅱ缓慢倒入悬浊液i,不断搅拌形成溶胶后,加入5g凹凸棒石基硅铝源,30℃搅拌6h均匀后,经60℃水浴老化6h、100℃蒸发4h、洗涤过滤3次、105℃干燥12h、研磨筛分处理后得到0.25mm直径的负载活性金属的凹凸棒石基硅铝源粉末。将所得粉末放在管式炉中,通入空气气氛,从室温以3℃/min的升温速率升至700℃,恒温煅烧4h后冷却至室温,所得粉末均匀分散在20ml去离子水中形成悬浊液ii;称取5g四丙基氢氧化铵溶液(tpaoh,浓度为25wt%)在40℃下加入10ml 去离子水中形成溶液ⅲ。将悬浊液ii逐滴移入溶液ⅲ中,充分搅拌后,逐滴加入0.1mol/l氢氧化钠溶液调节ph至11搅拌4h后形成悬浊液iii。将悬浊液iii移入200ml聚四氟乙烯内衬的水热釜中,在180℃下水热结晶12h后冷却至室温,离心、水洗、乙醇洗至中性,在 105℃烘箱中干燥12h,研磨后在700℃下流动空气氛围中煅烧6h移除模板剂后,即得铜
‑ꢀ
铁@凹凸棒石基沸石分子筛催化剂,编号4#。
75.在甲烷浓度为20%(体积浓度,余为氮气),反应温度为240℃,甲烷进料为6ml/min,水蒸汽进料为9ml/min,催化剂的用量为0.1g的反应条件下,在微型固定床反应器上对其催化性能进行了测试。先通入氮气吹扫设备30分钟,再将固定床反应器升温至反应温度,通入 ch4后再通过泵将水泵入固定床中的预热混合室,形成水蒸气与甲烷混合气通入反应管,并通过gc装置检测反应后产物。其甲烷转化率为80.4%,甲醇选择性为86.5%,使用寿命高于200h。
76.实施例5
77.对来自不同公司的煤层气进行了催化反应测试
78.取上述1#~4#催化剂0.1g~0.5g置于固定床反应器中,反应时通入不同公司的煤层气,反应温度为180℃~260℃。具体的反应条件及结果见表1(煤层气从各公司购买甲烷浓度为 25%(体积浓度,余为氮气))
79.表1
[0080][0081]
应当理解本文所述的例子和实施方式仅为了说明,并不用于限制本发明,本领域技术人员可根据它做出各种修改或变化,凡在本发明的精神和原则之内,所作的任何修改、等同替换、改进等,均应包含在本发明的保护范围之内。
再多了解一些
本文用于企业家、创业者技术爱好者查询,结果仅供参考。