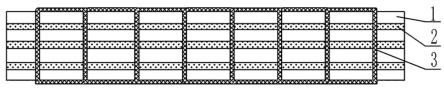
1.本发明属于热管理材料及其制备技术领域,具体是一种金刚石碳纤维多层编织复合材料极其制备方法。
背景技术:
2.随着电子技术的迅速发展,军民领域电子设备热控系统中元器件的功率越来越高,热管理变得尤为重要,甚至成为大功率电子器件发展的瓶颈。然而,目前通用的金属(al,cu)、陶瓷(sic,aln)、金属基复合材料(cu/mo,al/sic)等越来越难以满足大功率电子器件散热的需求。因此,开发新一代高导热材料来保证大功率电子设备热控系统的稳定工作成为热管理材料领域的研发重点。
3.不同于金属依靠外围电子进行传热,金刚石依靠声子传热,其室温下热导率最高可达2000 w/(m
·
k),是铜的5倍。同时,金刚石具有极好的绝缘性,低的热膨胀系数和密度,使得金刚石成为大功率电子设备最佳的热管理应用材料。目前,金刚石在热管理材料上的应用主要有三种形式:cvd金刚石膜单独使用;cvd金刚石膜与金属焊接形成复合散热片;金刚石粉/颗粒与铜、铝等金属形成复合材料。金刚石单独作为散热材料面临如下问题:金刚石厚膜生长周期长,深加工困难,成本高;金刚石膜硬而脆,韧性差,易断裂。金刚石膜与金属焊接存在的问题是:金刚石化学惰性高,与金属材料浸润差,很难形成良好的界面结合;金刚石与金属热膨胀系数差异大,热冲击会引起变形失调。金刚石粉/颗粒与铜、铝等金属复合则面临界面热阻高、复合热导率较小的问题。
4.碳纤维具有抗拉强度高、热膨胀系数小(甚至可为负值-1.5
×
10-6
/℃)、比重轻等一系列优异性能。若将金刚石与碳纤维复合,则有望将金刚石的超高导热优点及碳纤维的高强、高韧优势综合。尽管碳纤维和金刚石同属碳材料,然而二者结构不同,复合困难,使得目前尚未研制出二者的复合材料。本发明通过材料的结构功能一体化设计,制备获得高导热、高强度、高韧性、低密度的金刚石碳纤维复合热管理材料,满足大功率电子器件的散热需求。
技术实现要素:
5.针对现有热管理材料无法满足大功率电子器件日益增加的散热需求,本发明提供了一种金刚石碳纤维多层编织复合材料。
6.本发明是通过如下技术方案实现的:一种金刚石碳纤维多层编织复合材料,是由依次交替排列的金刚石膜片和碳纤维-固化粘结剂复合片沿上下方向叠置而成的叠层结构,且其顶层和底层均为金刚石膜片;碳纤维-固化粘结剂复合片为固化粘结剂填充碳纤维间隙形成的片结构;叠层结构上设置有贯穿其上下的通孔阵列,通过通孔阵列穿设绑捆有碳纤维束,各层之间通过固化粘结剂及碳纤维束共同连接固定。
7.作为优选的技术方案,金刚石膜片为采用cvd法制备的自支撑金刚石膜片,其热导
率≥1200 w/(m
·
k),平整度≤0.1 mm,平行度≤0.1 mm,粗糙度ra≤0.05 mm。
8.作为优选的技术方案,金刚石膜片的厚度为0.3 mm~1 mm,碳纤维-固化粘结剂复合片的厚度为0.1 mm~0.3 mm,碳纤维束的直径为0.05 mm~0.2 mm,通孔的直径为0.5 mm~1 mm、间距为3 mm~20 mm。
9.作为优选的技术方案,固化粘结剂为钡酚醛树脂、环氧树脂或改性环氧树脂固化而成。
10.作为优选的技术方案,固化粘结剂中包含有金刚石微粉,金刚石微粉的粒径为200 nm~2 μm。
11.进一步的,本发明还提供了上述金刚石碳纤维多层编织复合材料的制备方法,以解决金刚石难以膜形式沉积于碳纤维表面、二者连接和复合困难的问题。该制备方法包括如下步骤:1)金刚石膜片处理:根据对金刚石膜片的尺寸要求,选择合适直径及厚度的金刚石膜片,对金刚石膜片进行厚度修整和表面光滑处理,然后切割成设定的形状,最后对金刚石膜片进行打孔,形成孔阵列;2)粘结剂调配:粘结剂有两种调配方式,第一种调配方式是将树脂和稀释剂调配均匀,得到第一种粘结剂;第二种调配方式是将金刚石微粉、树脂和稀释剂调配均匀,得到第二种粘结剂;3)多层膜片平铺:在定位夹具中依次交替平铺金刚石膜片和浸润了粘结剂的碳纤维,直至复合厚度达到要求,得到复合层结构,其中各层金刚石膜片上的孔阵列对齐后整体形成通孔阵列;4)固定多层膜片:将碳纤维束穿过复合层结构上的通孔阵列,使碳纤维束通过所有的通孔,将多层膜片连接固定,排出金刚石膜片之间富余的粘结剂及弥散于粘结剂内的气泡;5)固化处理:在复合层结构的最顶层金刚石膜片上放置重物,保持多层膜片处于压紧状态,对整体进行加热使粘结剂固化转变为固化粘结剂;6)后处理:去除重物和定位夹具,对复合层结构的侧面进行打磨和超声清洗,最终获得所述的金刚石碳纤维多层编织复合材料。
12.作为优选的技术方案,步骤1)中,金刚石膜片厚度修整和表面光滑处理时采用机械研磨、化学抛光和激光处理;金刚石膜片切割时采用激光切割机或金刚石线锯;金刚石膜片打孔是采用激光打标机。
13.作为优选的技术方案,步骤2)中,第一种粘结剂中树脂和稀释剂的调配比例是1:1~1:5;第二种粘结剂中树脂和稀释剂的调配比例是1:1~1:5,金刚石微粉在树脂和稀释剂整体中的比例为5-30 g/100 g。
14.作为优选的技术方案,树脂采用钡酚醛树脂、环氧树脂或改性环氧树脂,稀释剂采用无水乙醇,金刚石微粉的粒径为200 nm~2 μm。
15.作为优选的技术方案,步骤5)中,加热固化的温度为200
ꢀ°
c~300
ꢀ°
c,保温时间为3~8 h。
16.与现有技术相比,本发明的有益效果如下:1)金刚石具有优异的散热性能,碳纤维具有高抗拉强度和高韧性,本发明利用钡
酚醛树脂、环氧树脂、改性环氧树脂等作为粘合剂,碳纤维束作为织线,将金刚石膜片和碳纤维两种性能优异的碳材料编织结合起来,实现二者的性能互补,制备出的金刚石碳纤维多层编织复合材料,该材料能够兼有金刚石的高热导率和碳纤维的高抗拉强度和高韧性,可作为高导热、高强度、高韧性、低密度的热管理材料,有效抵抗机械冲击和热冲击。
17.2)本发明的复合材料面内具有较高的热导率,本发明采用金刚石膜片作为复合材料,多片金刚石膜片的存在可在水平方向作为高效散热通道,把接触的热量快速传走,使得水平方向具有较高的热导率;考虑到固化粘结剂的热导率不高及界面热阻的存在使得法向热导率受影响的问题,本发明可根据应用需求在固化粘结剂中加入金刚石微粉用于增加法向热导率;本发明复合材料尤其适合作为航空航天、核工业等领域热控系统中的散热托架。
18.3)由于碳纤维为编织材料,粘结剂可完全渗透,因此粘结剂可实现对碳纤维的高强度粘合,金刚石膜片则表面粗糙度低,加上自身的惰性,导致固化粘结剂对其粘合度不高,因此,本发明通过碳纤维束捆绑金刚石层和碳纤维层保证碳纤维和金刚石的结合性,其结合性优于碳纤维和金刚石之间粘合,在双重作用下,可保证金刚石层和碳纤维层在使用过程中不发生开裂。
19.4)本发明复合材料由两种材料通过固化粘结剂粘合形成,两种材料的形状、厚度均可调,因此复合材料整体的形状和厚度可根据热控系统空间进行灵活调整,热导率可根据成本及实际需求进行调控。
附图说明
20.本技术的示意性附图只是用于对本技术的进一步理解,并不构成对本技术的不当限定。
21.图1为实施例1中金刚石膜片加工孔阵列后的俯视示意图。
22.图2为实施例1中金刚石碳纤维多层编织复合材料俯视示意图。
23.图3为图2中的a-a剖视图。
24.图中:1-金刚石膜片、2-碳纤维-固化粘结剂复合片、3-碳纤维束。
具体实施方式
25.下面将结合参考附图及实施例,对本发明作进一步说明,但不局限于以下实施例。本领域普通人员在没有做出创造性劳动前提下获得的所有其他实施例,均属于本发明的保护范围。
26.实施例1一种金刚石碳纤维多层编织复合材料,是由依次交替排列的金刚石膜片1和碳纤维-固化粘结剂复合片2沿上下方向叠置而成的叠层结构,且其顶层和底层均为金刚石膜片1;碳纤维-固化粘结剂复合片2为固化粘结剂填充碳纤维间隙形成的片结构;叠层结构上设置有贯穿其上下的通孔阵列,通过通孔阵列穿设绑捆有碳纤维束3,各层之间通过固化粘结剂及碳纤维束3共同连接固定,如图2和图3所示。其中,金刚石膜片1的长、宽、厚为30 mm
×
20 mm
×
1 mm,金刚石膜片1的层数为4层;碳纤维-固化粘结剂复合片2的长、宽、厚为30 mm
×
20 mm
×
0.3 mm,碳纤维-固化粘结剂复合片2的层数为3层;碳纤维束3的直径为0.1 mm;通孔的直径为1 mm、间距为3 mm。
27.上述金刚石碳纤维多层编织复合材料的制备方法,包括如下步骤:1)选择直径为52 mm、厚度为1.2 mm、抗拉强度为1000 mpa、热导率为1200 w/(m
·
k)的cvd自支撑金刚石膜,采用激光修面机对cvd自支撑金刚石膜进行厚度修整和表面光滑处理,厚度修整时激光功率为1000 w,沿厚度方向修整速度为0.02 μm/d,表面光滑处理时激光功率为450 w,修面处理后cvd自支撑金刚石膜的厚度为1 mm,表面平整度为0.1 mm,平行度为0.1 mm,粗糙度为0.05 mm;设计金刚石膜片1的尺寸为30 mm
×
20 mm的矩形块,采用激光切割机对上述cvd自支撑金刚石膜进行切割,激光功率为12 w、频率为6 hz,得到金刚石膜片1;使用激光打标机对金刚石膜片1进行打孔处理,孔呈8
×
5矩形阵列,孔直径为1 mm、间距为3 mm,如图1所示;2)选用环氧树脂和无水乙醇按1:3比例进行均匀调配,得到粘结剂;将抗拉强度为5000 mpa、弹性模量为230 gpa的12 k碳纤维片及碳纤维束3均置于粘结剂中浸润5分钟,取出后在空气中放置30分钟;3)在定位夹具中依次交替平铺金刚石膜片1和浸润了粘结剂的碳纤维,其中金刚石膜片1平铺4层、碳纤维平铺3层,得到复合层结构;将浸润了粘结剂的碳纤维束3穿过复合层结构上的通孔阵列,使碳纤维束3通过所有的通孔,并绑扎固定;随后在顶层金刚石膜片1表面放置一质量为0.5 kg的重物,以排出金刚石膜片1之间富余的粘结剂及弥散于粘结剂内的气泡,在此状态下进行加热固化,缓慢升温至260
ꢀ°
c,保温6小时;4)移走定位夹具及重物,对复合层结构的四个侧面进行打磨和超声清洗,去除侧面的固化粘结剂及碳纤维外漏的端部,打磨采用320#~800#的sic金刚砂纸,超声清洗选用丙酮,清洗时间为15分钟,最终制备获得所述的金刚石碳纤维多层编织复合材料,如图2和图3所示。
28.通过上述步骤制备的金刚石碳纤维多层编织复合材料面内热导率约1100 w/(m
·
k),抗拉强度约为2500 mpa,同金刚石抗拉强度相比提高了2.5倍。
29.实施例2一种金刚石碳纤维多层编织复合材料,是由依次交替排列的金刚石膜片1和碳纤维-固化粘结剂复合片2沿上下方向叠置而成的叠层结构,且其顶层和底层均为金刚石膜片1;碳纤维-固化粘结剂复合片2为固化粘结剂填充碳纤维间隙形成的片结构;叠层结构上设置有贯穿其上下的通孔阵列,通过通孔阵列穿设绑捆有碳纤维束3,各层之间通过固化粘结剂及碳纤维束3共同连接固定。其中,金刚石膜片1为圆形片结构,其直径为φ20 mm、厚度为0.8 mm,金刚石膜片1的层数为5层;碳纤维-固化粘结剂复合片2为圆形片结构,其直径为φ20 mm、厚度为0.2 mm,碳纤维-固化粘结剂复合片2的层数为4层;碳纤维束3的直径为0.1 mm;通孔的直径为1 mm。
30.上述金刚石碳纤维多层编织复合材料的制备方法,包括如下步骤:1)选择直径为50 mm、厚度为1 mm、抗拉强度为600 mpa、热导率为1400 w/(m
·
k)的cvd自支撑金刚石膜,采用激光修面机对cvd自支撑金刚石膜进行厚度修整和表面光滑处理,厚度修整时激光功率为850 w,沿厚度方向修整速度为0.02 μm/d,表面光滑处理时激光功率为350 w,修面处理后cvd自支撑金刚石膜的厚度为0.8 mm,表面平整度为0.05 mm,平行度为0.05 mm,粗糙度为0.01 mm;设计金刚石膜片1的尺寸为φ20 mm的圆形片结构,采用激光切割机对上述cvd自支撑金刚石膜进行切割,激光功率为10 w、频率为8 hz,得到金刚
石膜片1;使用激光打标机对金刚石膜片1进行打孔处理,呈数量分布为3-6-9的环形阵列,孔直径1 mm;2)选用钡酚醛树脂和无水乙醇按1:5比例进行均匀调配,同时加入粒径为200 nm的金刚石微粉,金刚石微粉的加入量在改性环氧树脂和无水乙醇整体中的比例为5 g/100g,得到粘结剂;将抗拉强度为4500 mpa、弹性模量为230 gpa的12 k碳纤维片及碳纤维束3均置于粘结剂中浸润3分钟,取出后在空气中放置20分钟;3)在定位夹具中依次交替平铺金刚石膜片1和浸润了粘结剂的碳纤维片,其中金刚石膜片1平铺5层、碳纤维片平铺4层,得到复合层结构;将浸润了粘结剂的碳纤维束3穿过复合层结构上的通孔阵列,使碳纤维束3通过所有的通孔,并绑扎固定;随后在顶层金刚石膜片1表面放置一质量为0.6 kg的重物,以排出金刚石膜片1之间富余的粘结剂及弥散于粘结剂内的气泡,在此状态下进行加热固化,缓慢升温至300
ꢀ°
c,保温8小时;4)移走定位夹具及重物,对复合层结构的四个侧面进行打磨和超声清洗,去除侧面的固化粘结剂及碳纤维外漏的端部,打磨采用320#~800#的sic金刚砂纸,超声清洗选用丙酮,清洗时间为15分钟,最终制备获得所述的金刚石碳纤维多层编织复合材料。
31.通过上述步骤制备的金刚石碳纤维多层编织复合材料面内热导率约为1250 w/(m
·
k),法向热导率约为850 w/(m
·
k),抗拉强度约为1700 mpa,同金刚石抗拉强度相比提高了2.8倍。
32.实施例3一种金刚石碳纤维多层编织复合材料,是由依次交替排列的金刚石膜片1和碳纤维-固化粘结剂复合片2沿上下方向叠置而成的叠层结构,且其顶层和底层均为金刚石膜片1;碳纤维-固化粘结剂复合片2为固化粘结剂填充碳纤维间隙形成的片结构;叠层结构上设置有贯穿其上下的通孔阵列,通过通孔阵列穿设绑捆有碳纤维束3,各层之间通过固化粘结剂及碳纤维束3共同连接固定。其中,金刚石膜片1的长、宽、厚为15 mm
×
15 mm
×
0.5 mm,金刚石膜片1的层数为6层;碳纤维-固化粘结剂复合片2的长、宽、厚为15 mm
×
15 mm
×
0.2 mm,碳纤维-固化粘结剂复合片2的层数为5层;碳纤维束3的直径为0.15 mm;通孔的直径为0.8 mm、间距为4 mm。
33.上述金刚石碳纤维多层编织复合材料的制备方法,包括如下步骤:1)选择直径为55 mm、厚度为0.7 mm、抗拉强度为450 mpa、热导率为1800 w/(m
·
k)的cvd自支撑金刚石膜,采用激光修面机对cvd自支撑金刚石膜进行厚度修整和表面光滑处理,厚度修整时激光功率为900 w,沿厚度方向修整速度为0.02 μm/d,表面光滑处理时激光功率为400 w,修面处理后cvd自支撑金刚石膜的厚度为0.5 mm,表面平整度为0.08 mm,平行度为0.08 mm,粗糙度为0.03 mm;设计金刚石膜片1的尺寸为15 mm
×
15 mm的矩形块,采用激光切割机对上述cvd自支撑金刚石膜进行切割,激光功率为11 w、频率为7 hz,得到金刚石膜片1;使用激光打标机对金刚石膜片1进行打孔处理,孔呈3
×
3矩形阵列,孔直径为0.8 mm、间距为4 mm;2)选用改性环氧树脂和无水乙醇按1:1比例进行均匀调配,同时加入粒径为2 μm的金刚石微粉,金刚石微粉的加入量在改性环氧树脂和无水乙醇整体中的比例为30 g/100 g,得到粘结剂;将抗拉强度为4000 mpa、弹性模量为200 gpa的12 k碳纤维片及碳纤维束3均置于粘结剂中浸润1分钟,取出后在空气中放置10分钟;
3)在定位夹具中依次交替平铺金刚石膜片1和浸润了粘结剂的碳纤维片,其中金刚石膜片1平铺6层、碳纤维片平铺5层,得到复合层结构;将浸润了粘结剂的碳纤维束3穿过复合层结构上的通孔阵列,使碳纤维束3通过所有的通孔,并绑扎固定;随后在顶层金刚石膜片1表面放置一质量为1 kg的重物,以排出金刚石膜片1之间富余的粘结剂及弥散于粘结剂内的气泡,在此状态下进行加热固化,缓慢升温至200
ꢀ°
c,保温3小时;4)移走定位夹具及重物,对复合层结构的四个侧面进行打磨和超声清洗,去除侧面的固化粘结剂及碳纤维外漏的端部,打磨采用320#~800#的sic金刚砂纸,超声清洗选用丙酮,清洗时间为15分钟,最终制备获得所述的金刚石碳纤维多层编织复合材料。
34.通过上述步骤制备的金刚石碳纤维多层编织复合材料面内热导率约为1600 w/(m
·
k),法向热导率约为1300 w/(m
·
k),抗拉强度约为1400 mpa,同金刚石抗拉强度相比提高了约3.1倍。
35.实施例4一种金刚石碳纤维多层编织复合材料,是由依次交替排列的金刚石膜片1和碳纤维-固化粘结剂复合片2沿上下方向叠置而成的叠层结构,且其顶层和底层均为金刚石膜片1;碳纤维-固化粘结剂复合片2为固化粘结剂填充碳纤维间隙形成的片结构;叠层结构上设置有贯穿其上下的通孔阵列,通过通孔阵列穿设绑捆有碳纤维束3,各层之间通过固化粘结剂及碳纤维束3共同连接固定。其中,金刚石膜片1的长、宽、厚为30 mm
×
20 mm
×
0.3 mm,金刚石膜片1的层数为10层;碳纤维-固化粘结剂复合片2的长、宽、厚为30 mm
×
20 mm
×
0.1 mm,碳纤维-固化粘结剂复合片2的层数为9层;碳纤维束3的直径为0.05 mm;通孔的直径为0.5 mm、间距为5 mm。
36.上述金刚石碳纤维多层编织复合材料的制备方法,包括如下步骤:1)选择直径为50 mm、厚度为0.8 mm、抗拉强度为500 mpa、热导率为2000 w/(m
·
k)的cvd自支撑金刚石膜,采用激光修面机对cvd自支撑金刚石膜进行厚度修整和表面光滑处理,厚度修整时激光功率为850 w,沿厚度方向修整速度为0.02 μm/d,表面光滑处理时激光功率为350 w,修面处理后cvd自支撑金刚石膜的厚度为0.3 mm,表面平整度为0.05 mm,平行度为0.05 mm,粗糙度为0.01 mm;设计金刚石膜片1的尺寸为30 mm
×
20 mm的矩形块,采用激光切割机对上述cvd自支撑金刚石膜进行切割,激光功率为10 w、频率为8 hz,得到金刚石膜片1;使用激光打标机对金刚石膜片1进行打孔处理,孔呈6
×
4矩形阵列,孔直径为0.5 mm、间距为5 mm;2)选用改性环氧树脂和无水乙醇按1:2比例进行均匀调配,同时加入粒径为1 μm的金刚石微粉,金刚石微粉的加入量在改性环氧树脂和无水乙醇整体中的比例为10 g/100g,得到粘结剂;将抗拉强度为4000 mpa、弹性模量为200 gpa的12 k碳纤维片及碳纤维束3均置于粘结剂中浸润5分钟,取出后在空气中放置15分钟;3)在定位夹具中依次交替平铺金刚石膜片1和浸润了粘结剂的碳纤维片,其中金刚石膜片1平铺10层、碳纤维片平铺9层,得到复合层结构;将浸润了粘结剂的碳纤维束3穿过复合层结构上的通孔阵列,使碳纤维束3通过所有的通孔,并绑扎固定;随后在顶层金刚石膜片1表面放置一质量为1.5 kg的重物,以排出金刚石膜片1之间富余的粘结剂及弥散于粘结剂内的气泡,在此状态下进行加热固化,缓慢升温至240
ꢀ°
c,保温5小时;4)移走定位夹具及重物,对复合层结构的四个侧面进行打磨和超声清洗,去除侧
面的固化粘结剂及碳纤维外漏的端部,打磨采用320#~800#的sic金刚砂纸,超声清洗选用丙酮,清洗时间为15分钟,最终制备获得所述的金刚石碳纤维多层编织复合材料。
37.通过上述步骤制备的金刚石碳纤维多层编织复合材料面内热导率约为1800 w/(m
·
k),法向热导率约为1400 w/(m
·
k),抗拉强度约为1700 mpa,同金刚石抗拉强度相比提高了3.6倍。
再多了解一些
本文用于企业家、创业者技术爱好者查询,结果仅供参考。