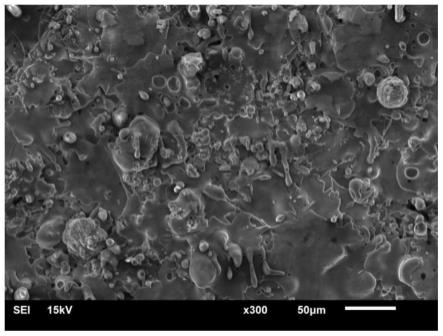
一种tft工艺用耐腐蚀挡板表面涂层的制备方法及涂层
技术领域
1.本技术涉及显示器领域,特别涉及一种tft工艺用耐腐蚀挡板表面涂层的 制备方法及tft工艺用耐腐蚀挡板的表面涂层。
背景技术:
2.led、oled显示器的tft制作中,tft薄膜可能产生黑点、短路等缺陷,影 响led、oled显示器的显示质量。
技术实现要素:
3.基于上述问题,本技术提供一种tft工艺用耐腐蚀挡板表面涂层的制备方 法,该方法制备出的表面涂层降低了tft薄膜黑点、短路等缺陷,提高了led、 oled显示器的显示质量。
4.一种tft工艺用耐腐蚀挡板表面涂层的制备方法,包括以下步骤:
5.⑴
粉末制备:
6.①
取复合陶瓷粉体原料,混合形成浆料;
7.②
在
①
形成的浆料中加入粘结剂,混合形成造粒浆料;
8.③
将
②
形成的造粒浆料在喷雾造粒机中喷雾造粒形成基本为球形的复合 陶瓷喷雾粒子;
9.⑵
前处理:对挡板元件基体前处理;
10.⑶
等离子喷涂:等离子喷涂复合陶瓷喷雾粒子形成复合陶瓷层。
11.可选地,所述等离子喷涂中,在等离子喷涂复合陶瓷喷雾粒子形成复合陶 瓷层前,还包括等离子喷涂梯度材料粉末形成梯度涂层。
12.可选地,所述复合陶瓷粉体含量为tio2:8~12wt%;0≤ceo2《1,余量为 al2o3。
13.可选地,所述等离子喷涂梯度材料为nicraly。
14.可选地,所述nicraly中,ni 67wt%;cr 22wt%;al 0~10wt%;y 0~1wt% 其中,al、y均》0。
15.可选地,所述喷雾造粒中,烘干室温度维持在250~300℃左右,喷雾造粒 机进风温度为250~300℃,出风温度为100~120℃,雾化器频率25hz。
16.可选地,所述喷砂采用的是不锈钢砂丸,尺寸为400~600μm,喷丸压力 为3~5kg。
17.可选地,所述梯度涂层制备中的等离子喷涂工艺参数为喷涂电流:300~ 400a;喷涂距离90~110mm;氢气流量:140~180plmm/h;喷枪移速:300~ 500mm/s。
18.可选地,所述复合陶瓷层制备中的等离子喷涂工艺参数为喷涂电流:450~ 550a;喷涂距离90~110mm;氢气流量:160~200l/h;喷枪移速:300~500mm/s。
19.可选地,所述等离子喷涂其采用的惰性保护气体为氩气,气体流量为 2000l/h。
20.可选地,所述的等离子喷涂采用的是外送粉大气等离子器。
21.可选地,所述
⑶
中,等离子喷涂前,挡板元件基体预热至120℃左右。
22.本技术还提供一种tft工艺用耐腐蚀挡板的表面涂层。
23.一种tft工艺用耐腐蚀挡板的表面涂层,该tft工艺用耐腐蚀挡板表面涂 层包括经等离子喷涂复合陶瓷喷雾粒子形成的复合陶瓷层。
24.可选地,所述tft工艺用耐腐蚀挡板表面涂层还包括经等离子喷涂梯度材 料粉末形成的梯度涂层。
25.发明原理及有益效果:
26.本技术发明人在对黑点、短路等缺陷进行分析研究中发现,部分黑点、短 路等缺陷产生的原因在于:在led、oled显示器tft制作过程中,为了便于模 组断的软板键合或降低外围导引线的阻抗,在tft薄膜中会溅射一种金属钼或 其氧化物moox,在此过程中这种材料会不断地飞溅至腔体内的挡板上并沉积。 当沉积物累积到一定厚度时会导致沉积膜与挡板之间的粘结力降低,严重的会 导致沉积膜脱落,污染腔体,进而产生黑点、短路等缺陷,影响led、oled显 示器的显示质量。
27.因此,本技术发明人为了提高沉积膜与挡板的附着力,减少沉积膜的脱落, 提出对腔体内裸露于工艺环境中的挡板进行等离子喷涂涂层制备,确保工艺环 境满足显示屏制程工艺要求,提升产品质量,减少了黑点、短路等缺陷的发生。
28.本技术发明人还发现:针对金属mo及其氧化物(moox)的沉积膜通常使用 hno3/h2so4/hf等酸液进行浸泡清洗。在浸泡过程中所使用的酸液易挥发,危险 性较大,尤其是氢氟酸具有较强的腐蚀性,会对挡板造成较大的腐蚀损伤。因 此,本技术发明人在挡板表面制备一层氧化铝基复合陶瓷涂层,不仅可以为沉 积膜提供较为粗糙的附着表面,还能提高挡板的耐腐蚀性能,避免对部件本体 造成较大损害,从而延长部件的使用寿命,降低成本。
29.本技术发明人运用喷雾造粒机书制备的复合陶瓷粉末,具有良好的球形度, 具有良好的流动性,便于等离子喷涂设备进行送粉。
30.本技术对耐腐蚀挡板元件表面涂层的制备工艺具有工艺操作简单,可控性 好,可以在短时间内对电子元件表面进行涂层制备,减少更换新电子元件的费 用,提高电子元件的使用寿命的特点。并且制备的涂层与挡板基体结合良好, 表现为明显的机械结合,并且涂层中组织致密,孔隙率小,能够明显改善挡板 元件再清洗过程中的耐腐蚀性能。另外,本技术表面涂层(复合陶瓷层)为沉 积物提供了便于附着的粗糙表面,减少沉积膜的脱落,提高腔体的使用寿命, 降低投入成本。其中氧化铈的添加,使其成分混合均匀,球形度较好,复合粉 末的流动性好。本专利中引入梯度涂层主要是因为挡板基体与陶瓷涂层间线膨 胀系数相差较大,将陶瓷层直接喷涂至挡板上容易产生开裂、剥落的现象,影 响挡板元件的使用性能。梯度涂层的引入一方面缓解了不同材料之间的热膨胀 系数差异,减少涂层因残余应力而导致的开裂和剥落;另一方面,也为陶瓷层 的附着提供了粗糙表面,提高与基体之间的结合强度。
附图说明
31.图1复合陶瓷喷雾粒子粉末显微形貌图;
32.图2为实施例1-3tft工艺用耐腐蚀挡板的整体结构示意图;
33.图3为实施例1的复合陶瓷层的表面形貌图;
34.图4为实施例2的复合陶瓷层的表面形貌图;
35.图5为实施例3的复合陶瓷层的表面形貌图;
36.图6为施例3的复合陶瓷层的截面形貌图;
37.图7为实施例4-6tft工艺用耐腐蚀挡板的整体结构示意图图;
38.图8为tft工艺用设备结构示意图。
39.具体实施方式
40.下面将结合附图对本技术作进一步说明。
41.实施例1
42.一种tft工艺用耐腐蚀挡板表面涂层制备工艺,包括以下步骤:
43.⑴
粉末制备:
44.①
取粉体原料(粉体原料中,al2o
3 90wt%;tio210wt%)和去离子水(去离子 水作为分散剂,去离子水:粉体原料重量比=13:5),机械混合1h形成浆料;
45.②
在
①
形成的浆料中加入pva作为粘结剂(pva即聚乙烯醇,pva质量为 浆料质量的3wt%),机械混合2h形成造粒浆料。
46.③
将
②
形成的造粒浆料在喷雾造粒机中喷雾造粒形成复合陶瓷喷雾粒子: 喷雾造粒过程烘干室温度维持在250℃左右,喷雾造粒机进风温度为250℃, 出风温度为117℃,雾化器频率25hz。
47.造粒形成的复合陶瓷喷雾粒子粉末显微形貌图如图1,经喷雾造粒后的复 合陶瓷粉末球形度好,具有良好的流动性,便于后续等离子喷涂涂层制备过程 中粉体材料的送粉过程的进行。
48.⑵
前处理:对挡板元件基体进行喷砂处理,然后用无水酒精对挡板元件基 体进行超声波清洗,去除表面油污和杂质。前处理中,喷砂处理采用的是不锈 钢砂丸,尺寸为400~600μm,喷丸压力为4kg;超声波清洗机频率40hz,清 洗时间20min;
49.⑶
等离子喷涂:复合陶瓷喷雾粒子经等离子焰流熔化送至
⑵
处理后的挡板 元件基体表面,采用外送粉等离子器制备涂层。在挡板元件基体表面等离子喷 涂喷涂复合陶瓷喷雾粒子形成复合陶瓷层。等离子喷涂前,
⑵
处理后的挡板元 件基体预热至120℃左右。
50.等离子喷涂中,等离子喷涂复合陶瓷层过程的参数如下:
[0051][0052]
本实施例形成的tft工艺用耐腐蚀挡板如图2,该tft工艺用耐腐蚀挡板 包括挡板元件基体1和等离子喷涂形成的复合陶瓷层3,其中,复合陶瓷层3 设置在挡板元件基体1的上表面上。复合陶瓷层3为由复合陶瓷喷雾粒子形成 的复合陶瓷层。复合陶瓷喷雾粒子由al2o3粒子、tio2粒子和pva经喷雾形成。
[0053]
本实施例的复合陶瓷层3的表面形貌如图3,从图3可以看出,面层熔融 情况较好,存在大面积的完全熔融区域,能够有效改善基体材料的耐腐蚀性能; 完全熔融区夹杂着部
分未熔融颗粒,起到提高涂层强度,阻碍裂纹扩展的作用。
[0054]
实施例2
[0055]
一种tft工艺用耐腐蚀挡板表面涂层制备工艺,包括以下步骤:
[0056]
⑴
粉末制备:
[0057]
①
取粉体原料(粉体原料中,al2o
3 90wt%;tio210wt%)和去离子水(去离子 水作为分散剂,去离子水:粉体原料重量比=13:5),机械混合1h形成浆料;
[0058]
②
在
①
形成的浆料中加入pva作为粘结剂(pva即聚乙烯醇,pva质量为 浆料质量的3wt%),机械混合2h形成造粒浆料。
[0059]
③
将
②
形成的造粒浆料在喷雾造粒机中喷雾造粒形成复合陶瓷喷雾粒子: 喷雾造粒过程烘干室温度维持在250℃左右,喷雾造粒机进风温度为250℃, 出风温度为117℃,雾化器频率25hz。
[0060]
⑵
前处理:对挡板元件基体进行喷砂处理,然后用无水酒精对挡板元件基 体进行超声波清洗,去除表面油污和杂质。前处理中,喷砂处理采用的是不锈 钢砂丸,尺寸为400~600μm,喷丸压力为4kg;超声波清洗机频率40hz,清 洗时间20min;
[0061]
⑶
等离子喷涂:复合陶瓷喷雾粒子经等离子焰流熔化送至
⑵
处理后的挡板 元件基体表面,采用外送粉等离子器制备涂层。在挡板元件基体表面等离子喷 涂喷涂复合陶瓷喷雾粒子形成复合陶瓷层。等离子喷涂前,
⑵
处理后的挡板元 件基体预热至120℃左右。
[0062]
等离子喷涂中,等离子喷涂复合陶瓷层过程的参数如下:
[0063][0064]
本实施例形成的tft工艺用耐腐蚀挡板如图2,该tft工艺用耐腐蚀挡板 包括挡板元件基体1和等离子喷涂形成的复合陶瓷层3,其中,复合陶瓷层3 设置在挡板元件基体1的上表面上。复合陶瓷层3为由复合陶瓷喷雾粒子形成 的复合陶瓷层。复合陶瓷喷雾粒子由al2o3粒子、tio2粒子和pva经喷雾形成。
[0065]
本实施例的复合陶瓷层3的表面形貌如图4,从图4可以看出,面层熔融 情况较好,存在大面积的完全熔融区域,能够有效改善基体材料的耐腐蚀性能; 完全熔融区夹杂着部分未熔融颗粒,起到提高涂层强度,阻碍裂纹扩展的作用。
[0066]
实施例3
[0067]
一种tft工艺用耐腐蚀挡板表面涂层制备工艺,包括以下步骤:
[0068]
⑴
粉末制备:
[0069]
①
取粉体原料(粉体原料中,al2o
3 89.8wt%;tio
2 10wt%;ceo
2 0.2wt%)和去 离子水(去离子水作为分散剂,去离子水:粉体原料重量比=13:5),机械混 合1h形成浆料;
[0070]
②
在
①
形成的浆料中加入pva作为粘结剂(pva即聚乙烯醇,pva质量为 浆料质量的3wt%),机械混合2h形成造粒浆料。
[0071]
③
将
②
形成的造粒浆料在喷雾造粒机中喷雾造粒形成复合陶瓷喷雾粒子: 喷雾造粒过程烘干室温度维持在250℃左右,喷雾造粒机进风温度为250℃, 出风温度为117℃,
雾化器频率25hz。
[0072]
⑵
前处理:对挡板元件基体进行喷砂处理,然后用无水酒精对挡板元件基 体进行超声波清洗,去除表面油污和杂质。前处理中,喷砂处理采用的是不锈 钢砂丸,尺寸为400~600μm,喷丸压力为4kg;超声波清洗机频率40hz,清 洗时间20min;
[0073]
⑶
等离子喷涂:复合陶瓷喷雾粒子经等离子焰流熔化送至
⑵
处理后的挡板 元件基体表面,采用外送粉等离子器制备涂层。在挡板元件基体表面等离子喷 涂喷涂复合陶瓷喷雾粒子形成复合陶瓷层。等离子喷涂前,
⑵
处理后的挡板元 件基体预热至120℃左右。
[0074]
等离子喷涂中,等离子喷涂复合陶瓷层过程的参数如下:
[0075][0076]
本实施例形成的tft工艺用耐腐蚀挡板如图2,该tft工艺用耐腐蚀挡板 包括挡板元件基体1和等离子喷涂形成的复合陶瓷层3,其中,复合陶瓷层3 设置在挡板元件基体1的上表面上。复合陶瓷层3为由复合陶瓷喷雾粒子形成 的复合陶瓷层。复合陶瓷喷雾粒子由al2o3粒子、tio2粒子、ceo2粒子和pva 经喷雾形成。
[0077]
本实施例的复合陶瓷层3的表面形貌如图5,从图中可知,面层熔融情况 较好,存在大面积的完全熔融区域,能够有效改善基体材料的耐腐蚀性能;完 全熔融区夹杂着部分未熔融颗粒,起到提高涂层强度,阻碍裂纹扩展的作用。
[0078]
实施例4
[0079]
一种tft工艺用耐腐蚀挡板表面涂层的制备方法,所述方法包括:
[0080]
⑴
粉末制备:
[0081]
①
取粉体原料(粉体原料中,al2o
3 90wt%;tio210wt%)和去离子水(去离子 水作为分散剂,去离子水:粉体原料重量比=13:5),机械混合1h形成浆料;
[0082]
②
在
①
形成的浆料中加入pva作为粘结剂(pva即聚乙烯醇,pva质量为 浆料质量的3wt%),机械混合2h形成造粒浆料。
[0083]
③
将
②
形成的造粒浆料在喷雾造粒机中喷雾造粒形成复合陶瓷喷雾粒子: 喷雾造粒过程烘干室温度维持在250℃左右,喷雾造粒机进风温度为250℃, 出风温度为117℃,雾化器频率25hz。
[0084]
⑵
前处理:将挡板元件基体表面喷丸处理,进行粗化;将粗化后的挡板元 件基体用压缩空气除尘,然后使用无水乙醇进行超声波清洗并干燥。喷砂处理 采用的是不锈钢砂丸,尺寸为400~600μm,喷丸压力为4kg。超声波清洗机 频率40hz,清洗时间20min。
[0085]
⑶
等离子喷涂:nicraly金属粉末(ni 67wt%,cr 22wt%,al 10wt%,y 1wt%)和复合陶瓷喷雾粒子经等离子焰流熔化送至
⑵
处理后的挡板元件基 体表面,采用外送粉等离子器制备涂层。等离子喷涂时,先在挡板元件基体的 表面上等离子喷涂nicraly金属粉末形成梯度涂层(梯度涂层厚度约50μm), 然后在梯度涂层的表面上等离子喷涂复合陶瓷喷雾粒子形成复合陶瓷层(复合 陶瓷层厚度100-200μm)。等离子喷涂前,
⑵
处理后的挡板元件基体预热至 120℃左右。
[0086]
等离子喷涂中,等离子喷涂梯度涂层过程的参数如下:
[0087][0088]
等离子喷涂中,等离子喷涂复合陶瓷层过程的参数如下:
[0089][0090]
本实施例形成的tft工艺用耐腐蚀挡板如图9,该tft工艺用耐腐蚀挡板 包括挡板元件基体1、梯度涂层2和等离子喷涂形成的复合陶瓷层3,其中, 梯度涂层2设置在挡板元件基体1的上表面上,复合陶瓷层3设置在梯度涂层 2的上表面上。
[0091]
进一步地,复合陶瓷层3为由复合陶瓷喷雾粒子形成的复合陶瓷层。
[0092]
进一步地,复合陶瓷喷雾粒子由al2o3粒子、tio2粒子和pva经喷雾形成。
[0093]
进一步地,梯度涂层2为nicraly粘结层。
[0094]
进一步地,梯度涂层2厚度约50μm,复合陶瓷层3厚度100-200μm。
[0095]
本实施例形成的形成的复合陶瓷层3表面形貌如图3,梯度涂层2表面形 貌如图7。
[0096]
实施例5
[0097]
一种tft工艺用耐腐蚀挡板表面涂层的制备方法,所述方法包括:
[0098]
⑴
粉末制备:
[0099]
①
取粉体原料(粉体原料中,al2o
3 90wt%;tio210wt%)和去离子水(去离子 水作为分散剂,去离子水:粉体原料重量比=13:5),机械混合1h形成浆料;
[0100]
②
在
①
形成的浆料中加入pva作为粘结剂(pva即聚乙烯醇,pva质量为 浆料质量的3wt%),机械混合2h形成造粒浆料。
[0101]
③
将
②
形成的造粒浆料在喷雾造粒机中喷雾造粒形成复合陶瓷喷雾粒子: 喷雾造粒过程烘干室温度维持在250℃左右,喷雾造粒机进风温度为250℃, 出风温度为117℃,雾化器频率25hz。
[0102]
⑵
前处理:将挡板元件基体表面喷丸处理,进行粗化;将粗化后的挡板元 件基体用压缩空气除尘,然后使用无水乙醇进行超声波清洗并干燥。喷砂处理 采用的是不锈钢砂丸,尺寸为400~600μm,喷丸压力为4kg。超声波清洗机 频率40hz,清洗时间20min。
[0103]
⑶
等离子喷涂:nicraly金属粉末(ni 67wt%,cr 22wt%,al 10wt%, y 1wt%)和复合陶瓷喷雾粒子经等离子焰流熔化送至
⑵
处理后的挡板元件基 体表面,采用外送粉等离子器制备涂层。等离子喷涂时,先在挡板元件基体的 表面上等离子喷涂nicraly金属粉末形成梯度涂层(梯度涂层厚度约50μm), 然后在梯度涂层的表面上等离子喷涂复合陶瓷喷雾粒子形成复合陶瓷层(复合 陶瓷层厚度100-200μm)。等离子喷涂前,
⑵
处理后的挡板元件基体预热至120℃左右。
[0104]
等离子喷涂中,等离子喷涂梯度涂层过程的参数如下:
[0105][0106]
等离子喷涂中,等离子喷涂复合陶瓷层过程的参数如下:
[0107][0108]
本实施例形成的tft工艺用耐腐蚀挡板如图9,该tft工艺用耐腐蚀挡板 包括挡板元件基体1、梯度涂层2和等离子喷涂形成的复合陶瓷层3,其中, 梯度涂层2设置在挡板元件基体1的上表面上,复合陶瓷层3设置在梯度涂层 2的上表面上。
[0109]
进一步地,复合陶瓷层3为由复合陶瓷喷雾粒子形成的复合陶瓷层。
[0110]
进一步地,复合陶瓷喷雾粒子由al2o3粒子、tio2粒子和pva经喷雾形成。
[0111]
进一步地,梯度涂层2为nicraly粘结层。
[0112]
本实施例形成的形成的复合陶瓷层3表面形貌如图4,梯度涂层2表面形 貌如图7。
[0113]
实施例6
[0114]
一种tft工艺用耐腐蚀挡板表面涂层的制备方法,所述方法包括:
[0115]
⑴
粉末制备:
[0116]
①
取粉体原料(粉体原料中,al2o
3 89.8wt%;tio
2 10wt%;ceo
2 0.2wt%)和去 离子水(去离子水作为分散剂,去离子水:粉体原料重量比=13:5),机械混 合1h形成浆料;
[0117]
②
在
①
形成的浆料中加入pva作为粘结剂(pva即聚乙烯醇,pva质量为 浆料质量的3wt%),机械混合2h形成造粒浆料。
[0118]
③
将
②
形成的造粒浆料在喷雾造粒机中喷雾造粒形成复合陶瓷喷雾粒子: 喷雾造粒过程烘干室温度维持在250℃左右,喷雾造粒机进风温度为250℃, 出风温度为117℃,雾化器频率25hz。
[0119]
⑵
前处理:将挡板元件基体表面喷丸处理,进行粗化;将粗化后的挡板元 件基体用压缩空气除尘,然后使用无水乙醇进行超声波清洗并干燥。喷砂处理 采用的是不锈钢砂丸,尺寸为400~600μm,喷丸压力为4kg。超声波清洗机 频率40hz,清洗时间20min。
[0120]
⑶
等离子喷涂:nicraly金属粉末(ni 67wt%,cr 22wt%,al 10wt%, y 1wt%)和复合陶瓷喷雾粒子经等离子焰流熔化送至
⑵
处理后的挡板元件基 体表面,采用外送粉等离子器制备涂层。等离子喷涂时,先在挡板元件基体的 表面上等离子喷涂nicraly金属粉末形成梯度涂层(梯度涂层厚度约50μm), 然后在梯度涂层的表面上等离子喷涂复合陶瓷喷雾粒子形成复合陶瓷层(复合 陶瓷层厚度100-200μm)。等离子喷涂前,
⑵
处理后的挡板元件基体预热至 120℃左右。
[0121]
等离子喷涂中,等离子喷涂梯度涂层过程的参数如下:
[0122][0123]
等离子喷涂中,等离子喷涂复合陶瓷层过程的参数如下:
[0124][0125]
本实施例形成的tft工艺用耐腐蚀挡板如图9,该tft工艺用耐腐蚀挡板 包括挡板元件基体1、梯度涂层2和等离子喷涂形成的复合陶瓷层3,其中, 梯度涂层2设置在挡板元件基体1的上表面上,复合陶瓷层3设置在梯度涂层 2的上表面上。
[0126]
进一步地,复合陶瓷层3为由复合陶瓷喷雾粒子形成的复合陶瓷层。
[0127]
进一步地,复合陶瓷喷雾粒子由al2o3粒子、tio2粒子、ceo2粒子和pva 经喷雾形成。
[0128]
进一步地,梯度涂层2为nicraly粘结层。
[0129]
进一步地,梯度涂层2厚度约50μm,复合陶瓷层3厚度100-200μm。
[0130]
进一步地,梯度涂层2厚度约50μm,复合陶瓷层3厚度100-200μm。
[0131]
本实施例的复合陶瓷层3的表面形貌如图5,复合陶瓷层3和梯度涂层2 截面形貌形貌如图6,从图5-6可以看出,面层熔融情况较好,存在大面积的 完全熔融区域,能够有效改善基体材料的耐腐蚀性能;完全熔融区夹杂着部分 未熔融颗粒,起到提高涂层强度,阻碍裂纹扩展的作用。
[0132]
实施例7
[0133]
将实施例1-6制备的tft工艺用耐腐蚀挡板进行性能检测,检测结果如下:
[0134][0135][0136]
基于上述实施例1-6任一的tft工艺用耐腐蚀挡板,本技术还提供一种tft 工艺用设备。
[0137]
如图9,一种tft工艺用设备,该tft工艺用设备包括tft工艺用设备本 体,该tft工艺用设备本体设置有工作腔体4,该tft工艺用设备本体还设置 有tft工艺用耐腐蚀挡板5,该tft工艺用耐腐蚀挡板5为实施例1-6任一的 tft工艺用耐腐蚀挡板。
[0138]
进一步地,tft工艺用设备为tft工艺用磁控溅射镀膜设备。
[0139]
tft工艺用设备为tft工艺用化学气相沉积设备。
[0140]
以上所述仅为本技术的优选实施例而已,并不用于限制本技术,对于本领 域的技术人员来说,本技术可以有各种更改和变化。凡在本技术的精神和原则 之内,所作的任何修改、等同替换、改进等,均应包含在本技术的保护范围之 内。
再多了解一些
本文用于企业家、创业者技术爱好者查询,结果仅供参考。