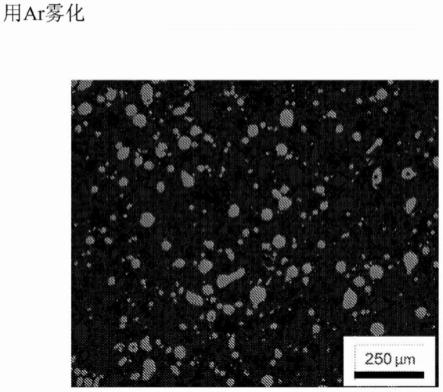
用于增材制造的金属粉末
1.本发明涉及用于制造钢部件的金属粉末,特别是其用于增材制造的用途。本发明还涉及用于制造所述金属粉末的方法。
2.fetib2钢因其优异的高弹性模量e、低密度和高抗拉强度而备受关注。然而,这样的钢板难以以良好的产量通过常规路线生产,这限制了它们的使用。
3.因此,本发明的目的是通过提供fetib2粉末来弥补这样的缺点,所述fetib2粉末在保持良好的使用特性的同时可以通过增材制造方法有效地用于制造部件。
4.为此目的,本发明的第一个主题包括用于增材制造的金属粉末,以重量含量表示,所述金属粉末的组成包含以下元素:
5.0.01%≤c≤0.2%
6.2.5%≤ti≤10%
7.(0.45xti)-1.35%≤b≤(0.45xti) 0.70%
8.s≤0.03%
9.p≤0.04%
10.n≤0.05%
11.o≤0.05%
12.并且任选地包含:
13.si≤1.5%
14.mn≤3%
15.al≤1.5%
16.ni≤1%
17.mo≤1%
18.cr≤3%
19.cu≤1%
20.nb≤0.1%
21.v≤0.5%
22.并且包含tib2的析出物并任选地包含fe2b的析出物,余量为fe和由加工产生的不可避免的杂质,金属粉末的平均圆度为至少0.70。
23.根据本发明的金属粉末还可以具有单独或组合考虑的在权利要求2至9中的任一项中列出的任选特征。
24.本发明的第二个主题包括用于制造用于增材制造的金属粉末的方法,所述方法包括:
[0025]-使元素和/或金属合金在高于液相线温度至少50℃的温度下熔融,以获得熔融组合物,所述熔融组合物以重量含量表示包含0.01%≤c≤0.2%、2.5%≤ti≤10%、(0.45
×
ti)-1.35%≤b≤(0.45
×
ti) 0.70%、s≤0.03%、p≤0.04%、n≤0.05%、o≤0.05%,并且任选地包含si≤1.5%、mn≤3%、al≤1.5%、ni≤1%、mo≤1%、cr≤3%、cu≤1%、nb≤0.1%、v≤0.5%,余量为fe和由加工产生的不可避免的杂质,以及
[0026]-用加压氩气使所述熔融组合物通过喷嘴雾化。
[0027]
根据本发明的方法还可以具有单独或组合考虑的在权利要求11至13中的任一项中列出的任选特征。
[0028]
本发明的第三个主题包括金属部件,所述金属部件通过使用根据本发明的金属粉末的增材制造工艺制造或通过根据本发明的方法获得。
[0029]
参照以下附图通过阅读以下描述将更好地理解本发明,该描述仅仅是为了解释的目的而提供并且决不旨在为限制性的:
[0030]-图1,图1是通过用氮气雾化获得的本发明之外的粉末的显微照片,
[0031]-图2,图2是通过用氩气雾化获得的根据本发明的粉末的显微照片。
[0032]
根据本发明的粉末具有特定的组成,当用于制造部件时,使组成平衡以获得良好的特性。
[0033]
由于当碳含量大于0.20%时,抗冷裂性和haz(热影响区)中的韧性降低,因此碳含量由于可焊性而受到限制。当碳含量等于或小于0.050重量%时,特别改善了电阻可焊性。
[0034]
由于钢的钛含量,优选限制碳含量以避免液态金属中tic和/或ti(c,n)的一次析出。最大碳含量必须优选限制为0.1%,甚至更好地限制为0.080%,以便主要在凝固期间或在固相中产生tic和/或ti(c,n)析出物。
[0035]
硅是任选的,但当添加时,由于固溶硬化,硅有效地促进提高抗拉强度。然而,过量添加硅导致形成难以去除的附着氧化物。为保持良好的表面特性,硅含量必须不超过1.5重量%。
[0036]
锰元素是任选的。然而,在等于或大于0.06%的量下,锰提高淬透性,并有助于固溶硬化,因此提高了抗拉强度。锰与存在的任何硫结合,从而降低热开裂的风险。但是,高于3重量%的锰含量,在凝固期间形成锰的有害偏析的风险更大。
[0037]
铝元素是任选的。然而,在等于或大于0.005%的量下,铝是用于使钢脱氧的非常有效的元素。但是,高于1.5重量%的含量,发生氧化铝的过量的一次析出,导致加工问题。
[0038]
在大于0.030%的量下,硫倾向于以有害的锰硫化物的形式过度大量析出。
[0039]
磷是已知在晶界处偏析的元素。其含量必须不超过0.040%以保持足够的热延性,从而避免开裂。
[0040]
任选地,可以添加镍、铜或钼,这些元素提高了钢的抗拉强度。出于经济原因,这些添加被限制为1重量%。
[0041]
任选地,可以添加铬以提高抗拉强度。其还允许析出更大量的碳化物。然而,其含量被限制为3重量%以制造较便宜的钢。将优选选择等于或小于0.080%的铬含量。这是因为过量添加铬导致更多的碳化物析出。
[0042]
同样任选地,可以分别以等于或小于0.1%和等于或小于0.5%的量添加铌和钒,以便以细小析出的碳氮化物的形式获得互补硬化。
[0043]
钛和硼在根据本发明的粉末中起重要作用。
[0044]
钛以2.5%至10%的量存在。当钛的重量含量小于2.5%时,tib2析出不以足够的量发生。这是因为析出的tib2的体积分数小于5%,从而阻止了弹性模量的显著变化,弹性模量保持小于220gpa。当钛的重量含量大于10%时,在液态金属中发生粗的一次tib2析出并且在产品中引起问题。此外,液相点升高,使得再也无法达到50℃的最低过热,使得不可
能进行粉末制造。
[0045]
fetib2共晶析出在凝固时发生。析出的共晶性质给予形成的显微组织有利于机械特性的特定细度和均匀性。当tib2共晶析出物的量大于5体积%时,在轧制方向上测量的钢的弹性模量可以超过约220gpa。高于10体积%的tib2析出物,模量可以超过约240gpa,从而使得能够设计明显减轻的结构。在包含诸如铬或钼的合金元素的钢的情况下,该量可以增加到15体积%以超过约250gpa。这是因为当这些元素存在时,在共晶析出的情况下可以获得的tib2的最大量增加。
[0046]
如上所述,钛必须以足以引起内生的tib2形成的量存在。
[0047]
根据本发明,钛也可以通过在环境温度下以基于tib2计算的相对于硼的亚化学计量比溶解在基体中而存在。为得到这样的亚共晶钢,钛含量优选使得:2.5%≤ti≤4.6%。当钛的重量含量低于4.6%时,tib2析出以析出的体积分数低于10%的方式发生。弹性模量则为220gpa至约240gpa。
[0048]
根据本发明,钛也可以通过在环境温度下以基于tib2计算的相对于硼的超化学计量比溶解在基体中而存在。为得到这样的过共晶钢,钛含量优选使得:4.6%≤ti≤10%。当钛的重量含量等于或大于4.6%时,tib2析出以析出的体积分数等于或大于10%的方式发生。弹性模量则等于或大于约240gpa。
[0049]
以钢的钛和硼的百分比表示的重量含量为使得:
[0050]
(0.45
×
ti)-1.35%≤b≤(0.45
×
ti) 0.70%
[0051]
这可以等价地表示为:
[0052]-1.35≤b-(0.45
×
ti)≤0.70
[0053]
如果钛和硼的重量含量为使得:
[0054]
οb-(0.45
×
ti)》0.70,则存在过量的fe2b析出,这使延性劣化,
[0055]
ο-1.35《b-(0.45
×
ti),则没有足够的tib2析出。
[0056]
在本发明的框架内,这里的“游离ti”是指不以析出物的形式结合的ti的含量。游离ti含量可以评估为游离ti=ti-2.215
×
b,b表示粉末中的b含量。根据这样的游离ti的值,粉末的显微组织将不同,现在将对粉末的显微组织进行描述。
[0057]
根据本发明的第一实施方案,钛的量为至少3.2%,钛和硼的重量含量为使得
[0058]
(0.45
×
ti)-1.35≤b≤(0.45
×
ti)-0.43
[0059]
在该组成域中,游离ti含量高于0.95%,并且无论温度如何(低于t液相线),粉末的显微组织主要为铁素体。“主要为铁素体”,必须理解粉末的组织由铁素体、析出物(尤其是tib2析出物)和至多10%的奥氏体组成。结果,与现有技术的钢相比,粉末的热硬度显著降低,使得热成型性大大提高。
[0060]
根据本发明的第二实施方案,钛和硼的含量为使得:
[0061]-0.35≤b-(0.45
×
ti)《-0.22
[0062]
当量b-(0.45
×
ti)等于或大于-0.35且小于-0.22时,游离ti的量为0.5%至0.8%。该量证明特别适合于获得仅由tib2组成的析出,而没有fe2b的析出。溶解在基体中的钛的量非常低,这意指从生产率的角度来看,钛的添加特别有效。
[0063]
根据本发明的第三实施方案,钛和硼的含量为使得:
[0064]-0.22≤b-(0.45
×
ti)≤0.70
[0065]
在该范围内,游离ti的含量小于0.5%。析出以两种连续共晶体的形式发生:首先是fetib2,然后是fe2b,根据合金的硼含量,fe2b的这种第二内生析出以较大量或较少量发生。以fe2b形式析出的量可以高达8体积%。该第二析出也根据共晶方案发生,使得可以获得细的均匀的分布,从而确保机械特性的良好均匀性。
[0066]
fe2b的析出结束了tib2的析出,其最大量与共晶有关。fe2b起着与tib2类似的作用。它增加了弹性模量并降低了密度。因此,可以通过改变fe2b析出相对于tib2析出的补充量来细微调整机械特性。这是一种特别可以用于在钢中获得大于250gpa的弹性模量和产品的抗拉强度的增加的方法。当钢包含等于或大于4体积%的量的fe2b时,弹性模量增加超过5gpa。当fe2b的量大于7.5体积%时,弹性模量增加超过10gpa。
[0067]
根据本发明的金属粉末的形态特别良好。
[0068]
实际上,根据本发明的金属粉末的平均圆度的最小值为0.70,优选为至少0.75。平均圆度被定义为b/l,其中l是颗粒投影的最长尺寸,b是颗粒投影的最小尺寸。圆度是粉末颗粒的形状接近数学上完美的圆(其圆度为1.0)的形状的程度的量度。由于这种高圆度,金属粉末是高度可流动的。因此,使增材制造更容易,并且打印的部件致密且坚硬。
[0069]
在一个优选实施方案中,根据本发明的金属粉末的平均球形度spht也得到改善,最小值为0.75,优选为至少0.80。
[0070]
平均球形度可以通过camsizer测量并且在iso 9276-6中定义为4πa/p2,其中a是由颗粒投影覆盖的测量面积,p是颗粒投影的测量周长/周界长。值为1.0表示完美的球体。
[0071]
优选地,如根据iso13320:2009或astm b822-17通过激光衍射测量的,至少75%的金属粉末颗粒具有在15μm至170μm范围内的尺寸。
[0072]
所述粉末可以例如通过首先混合作为原材料的纯元素和/或铁合金并使其熔融来获得。或者,所述粉末可以通过使预合金化组合物熔融来获得。
[0073]
通常优选纯元素以避免具有过多的来自铁合金的杂质,因为这些杂质可能会降低结晶。然而,在本发明的情况下,已经观察到来自铁合金的杂质对本发明的实现无害。
[0074]
本领域技术人员知晓如何混合不同的铁合金和纯元素以达到目标组成。
[0075]
一旦通过以适当比例混合纯元素和/或铁合金获得了组合物,将组合物在高于其液相线温度至少100℃的温度下加热并保持在该温度下以使所有原材料熔融并使熔体均匀化。由于这种过热,熔融组合物的粘度降低帮助获得具有良好特性的粉末。即便如此,由于表面张力随温度增加,优选不将组合物在高于其液相线温度超过450℃的温度下加热。
[0076]
优选地,将组合物在高于其液相线温度至少100℃的温度下加热。更优选地,将组合物在高于其液相线温度300℃至400℃的温度下加热。
[0077]
然后通过在中等压力下迫使熔融金属流通过孔口、喷嘴并通过用气体(气体雾化)或水(水雾化)的射流撞击熔融金属流而使熔融组合物雾化成细的金属液滴。在气体雾化的情况下,就在金属流离开喷嘴之前将气体引入到金属流中,用于在夹带的气体膨胀(由于加热)并离开至大收集容积(雾化塔)时产生湍流。后者充满气体以促进熔融金属射流的进一步湍流。金属液滴在其在雾化塔中落下期间冷却。优选气体雾化,因为其有利于产生具有高程度的圆度和少量附属物(satellite)的粉末颗粒。
[0078]
雾化气体为氩气。它比其他气体(例如氦气)更慢地增加熔体粘度,这促进较小的颗粒尺寸的形成。氩气还控制化学成分的纯度,避免不希望的杂质,并在粉末的良好形态方
面起关键作用,如将在实施例中证明的。
[0079]
气体压力是重要的,因为其直接影响金属粉末的颗粒尺寸分布和显微组织。特别地,压力越高,冷却速率越高。因此,将气体压力设定为10巴至30巴以优化颗粒尺寸分布并有利于微米/纳米晶相的形成。优选地,将气体压力设定为14巴至18巴以促进其尺寸与增材制造技术最兼容的颗粒的形成。
[0080]
喷嘴直径对熔融金属流量有直接影响,因此对颗粒尺寸分布和冷却速率有直接影响。最大喷嘴直径通常限制为4mm以限制平均颗粒尺寸的增加和冷却速率的降低。喷嘴直径优选为2mm至3mm,以更准确地控制颗粒尺寸分布并有利于特定显微组织的形成。
[0081]
气体与金属的比率,定义为气体流量(以kg/小时计)与金属流量(以kg/小时计)之间的比率,优选保持为1.5至7,更优选为3至4。其帮助调节冷却速率并因此进一步促进特定显微组织的形成。
[0082]
根据本发明的一种变体,如果发生吸湿,则将通过雾化获得的金属粉末干燥以进一步改善其流动性。干燥优选在100℃下在真空室中进行。
[0083]
通过雾化获得的金属粉末可以照这样使用,或者可以进行筛分以保留其尺寸更适合增材制造技术的颗粒以供以后使用。例如,在通过粉末床融合的增材制造的情况下,优选20μm至63μm的范围。在通过激光金属沉积或直接金属沉积的增材制造的情况下,优选45μm至150μm的范围。
[0084]
由根据本发明的金属粉末制成的部件可以通过以下增材制造技术获得:例如粉末床融合(lpbf)、直接金属激光烧结(dmls)、电子束熔融(ebm)、选择性热烧结(shs)、选择性激光烧结(sls)、激光金属沉积(lmd)、直接金属沉积(dmd)、直接金属激光熔融(dmlm)、直接金属打印(dmp)、激光熔覆(lc)、粘合剂喷射(bj)。由根据本发明的金属粉末制成的涂层也可以通过诸如冷喷涂、热喷涂、超音速火焰喷涂(high velocity oxygen fuel)的制造技术获得。
实施例
[0085]
在下文中呈现的以下实施例和测试在本质上是非限制性的,并且必须仅出于说明的目的而被考虑。它们将说明本发明的有利特征、发明人在大量实验之后选择的参数的重要性,并进一步确立根据本发明的金属粉末可以实现的特性。
[0086]
根据表1的金属组合物首先通过以适当比例混合铁合金和纯元素并使其熔融或者通过使预合金化组合物熔融来获得。添加元素的以重量百分比计的组成汇总在表1中。
[0087]
表1
–
熔体组成
[0088]
样品ctibmnalsivspnonicrcuc1030.0445.881.68<0.0010.3260.4390.2200.0060.002<0.001<0.001<0.001<0.001<0.001c1570.0215.991.960.1860.1150.0690.0470.0020.009<0.001<0.0010.0440.0330.053c300.0225.481.730.0800.0210.06200.0070.00630.0050.0010.0150.0830.02c1040.09210.353.89<0.0010.5021.0120.2990.0180.004<0.001<0.001<0.001<0.001<0.001c290.0225.481.730.0800.0210.06200.0070.00630.0050.0010.0150.0830.02c140.0225.481.730.0800.0210.06200.0070.00630.0050.0010.0150.0830.02c260.0194.811.990.1890.0460.06800.0010.0090<0.001<0.0010.0450.0330.05
[0089]
将这些金属组合物加热,然后在汇总于表2中的工艺条件下用氩气或氮气进行气体雾化。
[0090]
表2-雾化参数
[0091]
对于所有试验,雾化器bluepower au3000的常见输入参数是:
[0092][0093][0094]
rt意指室温
[0095]
然后将获得的金属粉末在100℃下在真空下干燥0.5天至1天,并进行筛分以根据它们的尺寸分离为三种级分f1至f3。
[0096]
分析粉末的元素组成,以重量百分比计,并将主要元素汇总在表3中。所有其他元素含量均在本发明范围内。
[0097]
表3-粉末组成
[0098]
样品tibtib2fe2bc1035.341.73是否c1575.842.05是否c305.341.72是否c1048.283.13是否c295.371.70是否c145.301.71是否
c264.992.04是是
[0099]
确定粉末的f1级分(收集尺寸为1μm至19μm的粉末颗粒)的形态并汇总在表4中。
[0100]
表4-f1级分形态
[0101][0102]
*:根据本发明的样品;加下划线的值:在本发明之外
[0103]
确定粉末的f2级分(收集尺寸为20μm至63μm的粉末颗粒)的形态并汇总在表5中。
[0104]
表5
–
f2级分形态
[0105][0106]
*:根据本发明的样品;加下划线的值:在本发明之外
[0107]
确定粉末的f3级分(收集尺寸高于64μm的粉末颗粒)的形态并汇总在表6中。
[0108]
表6
–
f3级分形态
[0109][0110]
*:根据本发明的样品;加下划线的值:在本发明之外
[0111]
从实施例清楚地看出,与参考例相比,根据本发明的粉末的所有级分都呈现出改善的形态,尤其是改善的平均圆度。
[0112]
这通过如图1和图2所示的显微照片证实,其中示于图2中的根据本发明的粉末的改善的形态是清楚可见的。
再多了解一些
本文用于企业家、创业者技术爱好者查询,结果仅供参考。